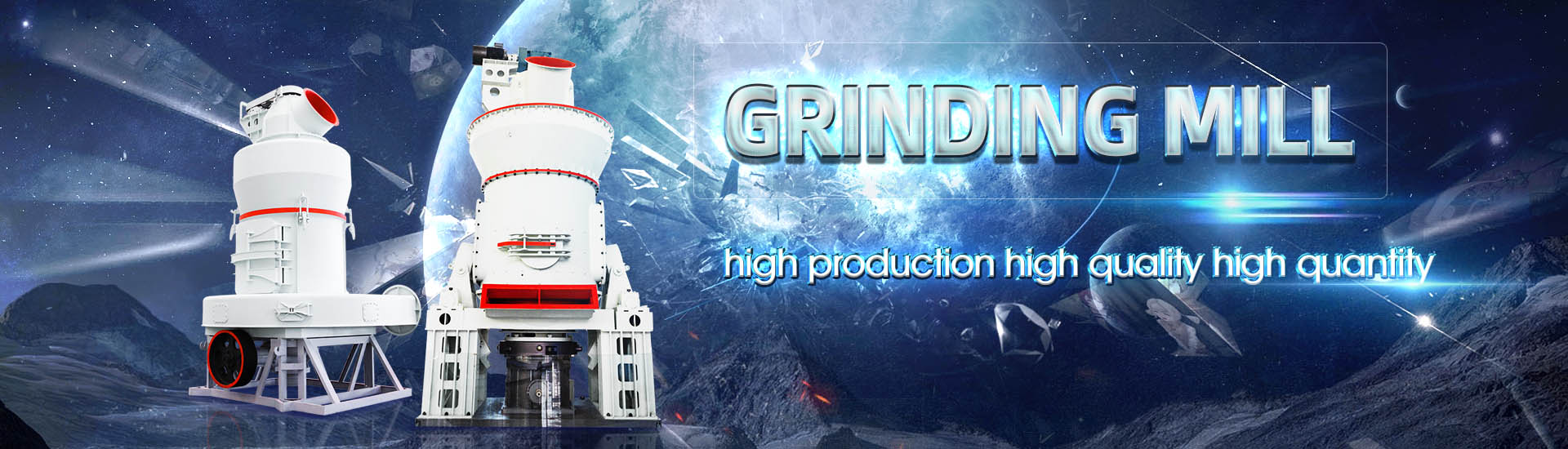
Steel slag powder wet grinding magnetic separation line process control
.jpg)
An airfluidized magnetic separator and its separation
2024年3月1日 In order to address the issue of magnetic agglomeration leading to poor magnetic separation efficiency and low activity enhancement, resulting in limited utilization of steel slag fine powder material, this study proposes a 2024年3月1日 Primary magnetic separation tests on a steel slag fine powder material demonstrate that the air fluidized dry magnetic separator effectively separates inert minerals (PDF) An airfluidized magnetic separator and its separation In universities and research institutes, the technique used for efficient recycling of iron mainly include dry magnetic separation of bulk slag, wet stage grinding and magnetic separation, wet DRY MAGNETIC SEPARATION TECHNOLOGY FOR THE RECOVERY Generally, the steel slag (steel furnace and ladle furnace slags) contains an appreciable amount of magnetic substances such as metallic iron and magnetic iron oxide, and thus, they can be WET MAGNETIC SEPARATION OF IRON FROM FINEGRAINED
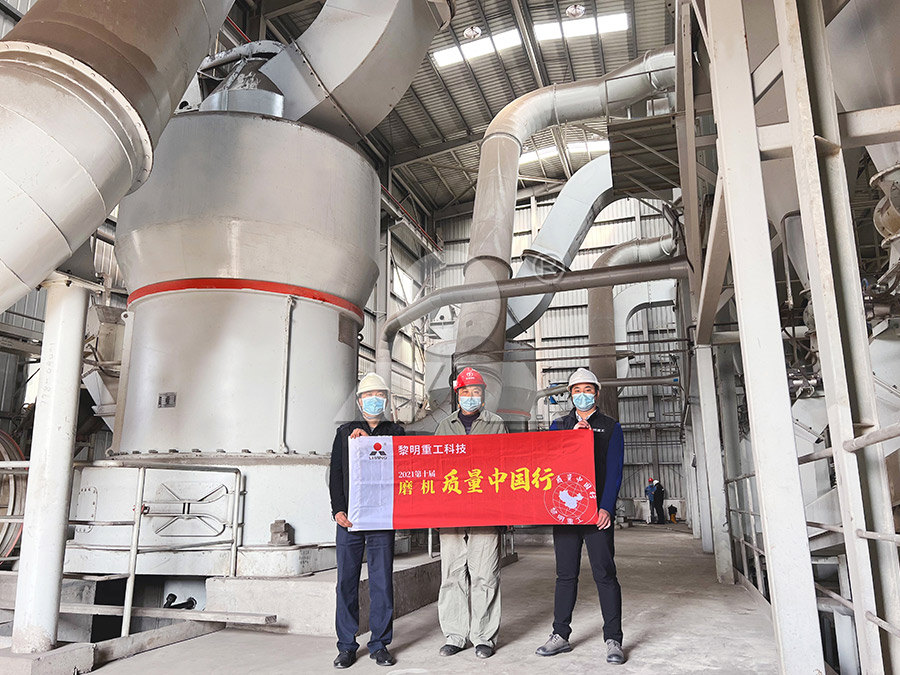
Recovery of high grade iron compounds from LD slag by
2014年1月10日 The combination of Low and High Intensity Magnetic Separation (LIMS and HIMS) of ground LD slag at 63 μm in wet process may recover ferromagnetic particles (iron 2024年7月29日 This study reveals the magnetic separation characteristics of the equipment for inert minerals in steel slag powder and provides a solution for obtaining steel slag powder that Magnetic separation characteristics of steel slag powder in a 2017年2月1日 To improve the efficiency of iron recovery from steel slag and reduce the wearandtear on facilities, a new method was proposed by adding a secondary screen sizer to the Optimization of magnetic separation process for iron recovery 2024年7月1日 Steel slag can separate inert minerals by the mineral separation method and prevent the hydration of active minerals caused by wet magnetic separation In order to solve [PDF] Magnetic separation characteristics of steel slag powder in a
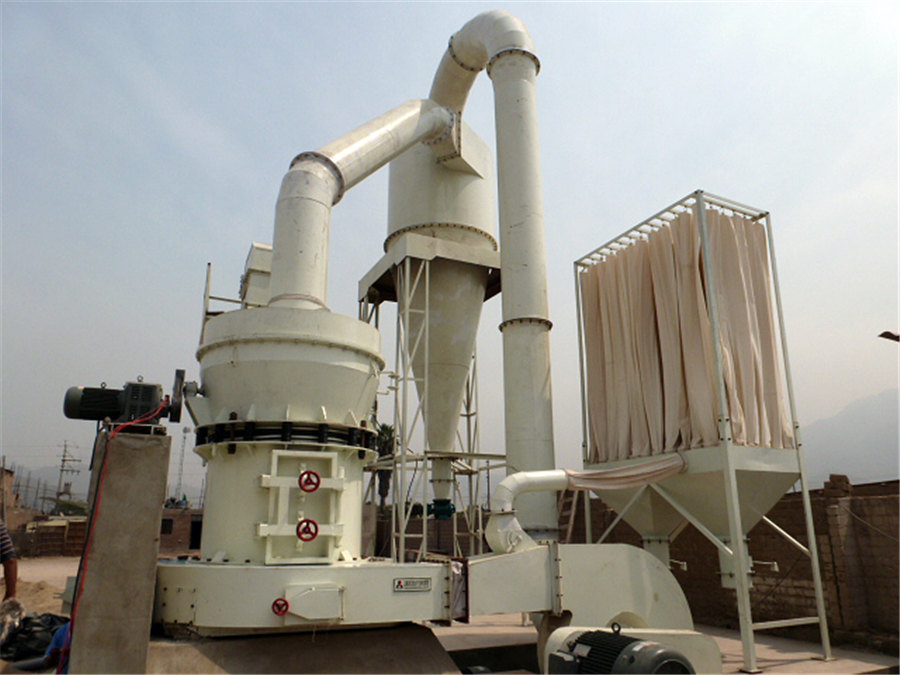
Optimization of magnetic separation process for iron recovery
T he ways for magnetic separation of slag usually va ry with cooling methods of liquid steel slag and its chemical/mineralogical composition Mostly , steel slag magnetic separation process Carbon dioxide sequestration using steel slag—modeling and experimental investigation Smitha Gopinath, Anurag Mehra, in Carbon Dioxide Sequestration in Cementitious Construction Materials, 2018 41 Introduction Steel slag is an industrial waste that is generated during the production of steel In the production of steel, oxides of metal impurities in the iron combine Steel Slag an overview ScienceDirect Topicschemical/mineralogical composition Mostly , steel slag magnetic separation process includes crushing/ grinding, screening and magnetic separation':", In order to liberate metallic iro n and other ferrous min erals fr om steel slag, size reduction pretreatment Received 10 May 2016 ; Received in revised for m 2 August 2016 ; Accepted 1 August Optimization of magnetic separation process for iron recovery 2024年7月29日 The mineral dry separation method is a technique for the comprehensive utilization of steel slag In this process, two products, ie, steel slag powder with high activity (reaches 75% of the cementitious activity of pure cement) and inert mineral material, are obtained by crushing and separating steel slag 12,13 If wet magnetic separation is adopted, the active Magnetic separation characteristics of steel slag powder in a
.jpg)
Superconducting magnetic separation of ground steel slag powder
2017年3月1日 Request PDF Superconducting magnetic separation of ground steel slag powder for recovery of resources Steel slag has been considered as an industrial waste A huge amount of slag is produced 2022年3月10日 Magnetic separation is an effective method to recover iron from steel slag However, the ultrafine tailings generated from steel slag become a new issue for utilizationCarbonation Curing on Magnetically Separated Steel Slag for the 2022年3月10日 Magnetic separation is an effective method to recover iron from steel slag However, the ultrafine tailings generated from steel slag become a new issue for utilization The dry separation processes generates steel slag powder, which has hydration activity and can be used as cement filler However, wet separation processes produce steel slag mud, which has Carbonation Curing on Magnetically Separated Steel Slag for the dry magnetic separation of bulk slag, wet stage grinding and magnetic separation, wet magnetic separation for full grain level, finegrained level flotation, and gravity separation [79] The wet separation and electromagnetic separation technologies suffer from high power and water consumption, whereas by contrast, dry permanentDRY MAGNETIC SEPARATION TECHNOLOGY FOR THE
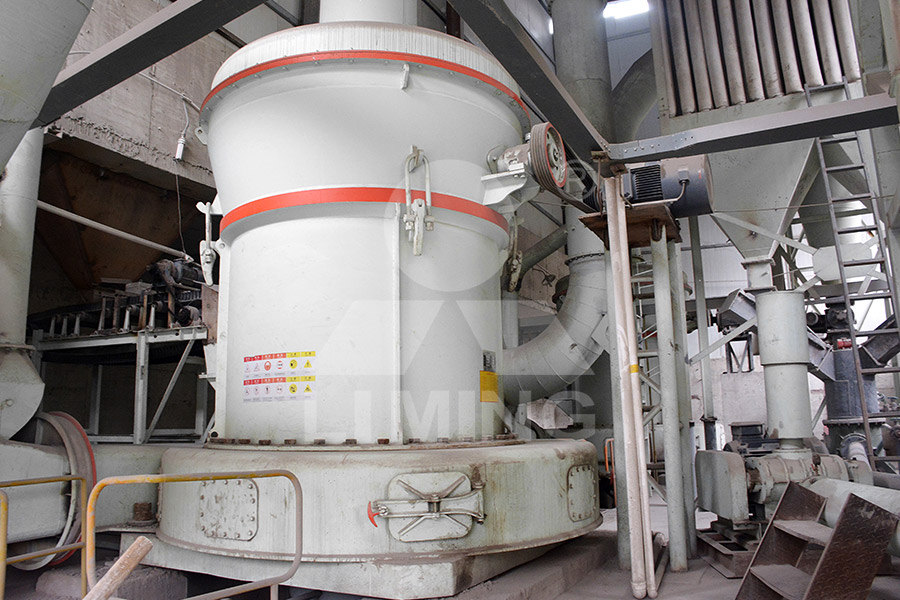
Steel Slag Magnetic Separation Line FTM Mac
Main Equipment of Steel Slag Magnetic Separation Plant There are two stages of the steel slag magnetic separation line; respectively they are grinding and screening With the main equipment of ball mill and magnetic separator, the steel slag magnetic separation line has advantages of fluent craft flow, high production efficiency and good 2018年8月1日 Steel slag is the main waste product in the steelmaking process Because of its chemical composition and technical properties, it can be reused as raw material in steel plants and can serve as a Steel slag in China: Treatment, recycling, and management2024年10月10日 Steel slag is a byproduct of steelmaking process The producing of steel slag in China is proximately 100 million tons, but the utilization ratio of comprehensive resources is the lower This paper described the production and composition characteristics of steel slag, reviewed current situation and progress of resource utilization and stabilization of steel slag Steel slag The Research Progress of Steel Slag Utilization and Stabilization recycling of iron primarily includes dry magnetic separation of bulk slag, wet stage grinding and magnetic separation, wet magnetic separation for full grain level, finegrained level flotation, and gravity separation [12] Usually, the wet magnetic separation method is used to separate the metallic iron particles form the slag powder [13]SEPARATION OF THE MAGNETIC FRACTION FROM THE SLAGS
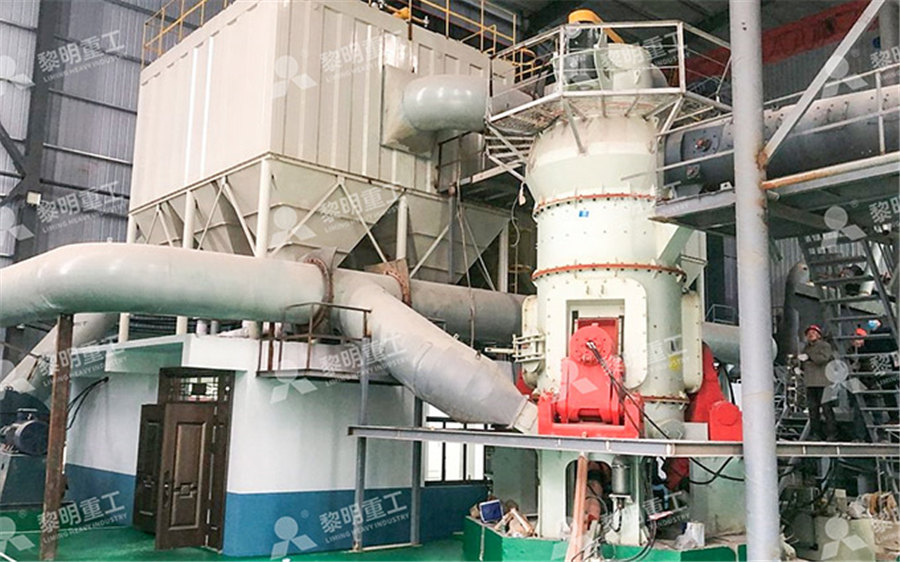
Optimization of magnetic separation process for iron recovery
2017年2月1日 To improve the efficiency of iron recovery from steel slag and reduce the wearandtear on facilities, a new method was proposed by adding a secondary screen sizer to the magnetic separation 2012年6月1日 Basic kinetic and energy models of the grinding process are described and the most commonly used control strategies are analyzed and discussed +1 Figures uploaded by Vladimir MonovGrinding in Ball Mills: Modeling and Process Control2016年10月28日 The converter steel slag cannot be widely used in building materials for its poor grindability In this paper, the grinding characteristics of untreated and pretreated (ie, magnetic separation) steel slag were compared Additionally, the grinding property of pretreated steel slag was also studied after adding grinding aids The results show that the residues (ie, oversize Comparison of Grinding Characteristics of Converter Steel Slag 2017年2月1日 To improve the efficiency of iron recovery from steel slag and reduce the wearandtear on facilities, a new method was proposed by adding a secondary screen sizer to the magnetic separation process according to grain size distribution of magnetic iron (MFe) in the slag The final recycling efficiency was evaluated by calculating the percentage of recycled M Optimization of magnetic separation process for iron recovery
.jpg)
Steel Slag Grinding Plant CHAENG
The steel slag after pretreatment is screened by a vibrating feed screen to remove large slag steel, and then enters the crushing magnetic separation system, where the steel slag is crushed and purified by a rod mill The purified steel slag tailings has an iron content of less than 2% and a fineness of less than 10mmBased on this, a steel slag grading grindingmagnetic separation utilization technique suitable for highaltitude areas is proposed, which is beneficial for improving the added value and XRD patterns of LD slag treated by magnetic separationdry magnetic separation of bulk slag, wet stage grinding and magnetic separation, wet magnetic separation for full grain level, finegrained level flotation, and gravity separation [79] The wet separation and electromagnetic separation technologies suffer from high power and water consumption, whereas by contrast, dry permanentDRY MAGNETIC SEPARATION TECHNOLOGY FOR THE DOI: 101016/jjmrt202301186 Corpus ID: ; Efficient separation of iron elements from steel slag based on magnetic separation process @article{Liu2023EfficientSO, title={Efficient separation of iron elements from steel slag based on magnetic separation process}, author={Xin Liu and Dazhi Wang and Zhiwei Li and Wei Ouyang and Yanping Bao and Chao Gu}, Efficient separation of iron elements from steel slag based on magnetic
.jpg)
Steel Slag Ball Mill Quality Ball Bill Supplier Provide Best Price
The steel slag material with the size up to the standard is sent to the steel slag ball mill, and then the material is ground to the required fineness by the steel slag ball mill Magnetic separation The steel slag after grinding is sent to magnetic separator for separation This process can separate the metal iron from the steel slag powder 2023年5月15日 Steel slag is the main solid waste generated in the steelmaking process, accounting for 15 to 20% of crude steel output [1]China's crude steel output in 2021 was 1035 billion tons [2], more than half of the global crude steel output (19505 billion tons) [3], and the steel slag output exceeded 120 million tonsIn contrast, the comprehensive utilization rate of Comprehensive utilization of steel slag: A review ScienceDirectFig 1 Dry magnetic separation process Fig2 Fine grinding + low intensity magnetic separation + screening process Results and Discussion Phase compositionThe phase composition of thesteel slag was tested by XRD, and the resulted were shown in Fig 1 From Fig 1, the main phases in the slag were tricalcium silicate (C3S),Dry Magnetic Separation Recovery Iron from Steel Slag Powder2013年1月1日 The combination of Low and High Intensity Magnetic Separation (LIMS and HIMS) of ground LD slag at 63 μm in wet process may recover ferromagnetic particles (iron oxides) at LIMS and paramagnetic Recovery of high grade iron compounds from LD slag
.jpg)
HighTitanium Slag Preparation Process by Carbothermic
reduction of ilmenite, followed by wet grinding and magnetic separation of slag from iron, was conducted to produce UGS with lowgrade ores This study aims to investigate the effect of Na 2CO 3 on the semimolten reduction of ilmenite and the separation behavior of slag from iron Finally, we developed a novel and low energy2023年2月1日 The multistage wet weak magnetic separation method is suitable for steel slag, with a best magnetic separation intensity of 100 mT in the laboratory range and a single magnetic separation time of Efficient separation of iron elements from steel slag based on magnetic 2021年9月24日 During steel production, the impurities in the hot metal react with the fluxes forming the steel slag Chemical constituents of this steel slag (SS) are relevant to iron/steelmaking or blended cement manufacture Harmful impurities present in it, however, limit its recycling to these applications Japan, Europe, and the US consume a significant amount of BOF Steel Slag: Critical Assessment and Integrated Approach for 2024年10月1日 The main components of EAF slag are Fe x O, Fe, CaO, SiO 2, MgO, and MnOThe EAF slag contains more iron, but it is mainly dominated by RO phase, which is difficult to be recovered by magnetic separation, resulting in low utilization of iron in slag (Liu et al, 2023, Zhang et al, 2019)The traditional view that EAF slag and converter slag are similar in nature, Separation and extraction of iron resources from hazardous
.jpg)
XRD patterns of LD slag treated by magnetic separation
In addition to this, the metals like Al, Fe, Zn, Pb, Ni, Ta, Ag and Au have also recovered from LD slag, with the application of different separation methods like The converter steel slag cannot be widely used in building materials for its poor grindability In this paper, the grinding characteristics of untreated and pretreated (ie, magnetic separation Specific surface areas (SSA) of steel slag under different grinding 2024年1月31日 Slag grinding exhibits complex nonlinear dynamics that challenge control Li X, Jia C, et al Tracking control of slag powder production process based on adaptive dynamic programming Acta Automatica Sinica 2016; 24: 1542–1551 Modeling of heat transfer for a wet multiplate clutch based on empirical data Show details Hide Intelligent process control system for predicting operating 55 known as the distribution function [45, 46]) describes the distribution of fragment sizes obtained after a breakage of particles of size xjThus, b1j, b2j, , bnj are the mass fractions of particles in size classes 1, 2, , n after a breakage of particles in size class j The mechanism of breakage is illustrated in [23] by a diagram shown in Fig 3Grinding in Ball Mills: Modeling and Process Control Sciendo
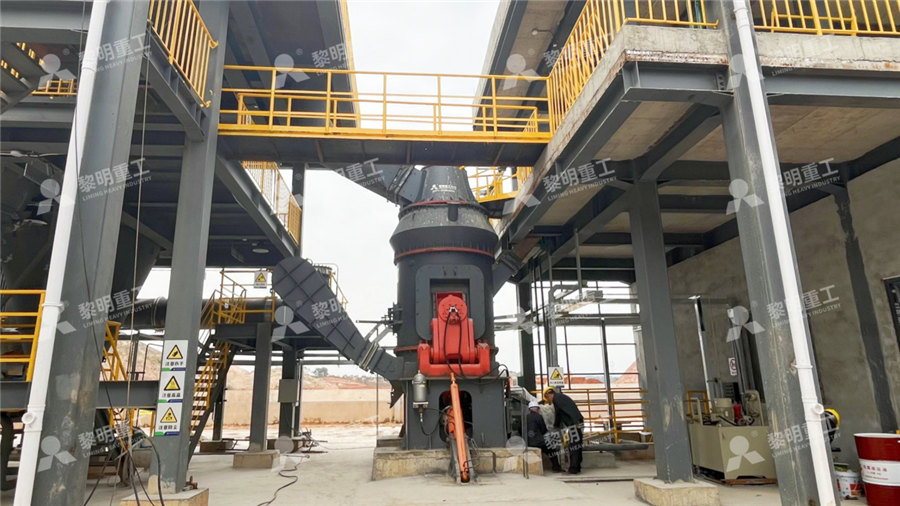
Current Development of Slag Valorisation in China
2014年2月19日 Drumgranulation process is a new process for molten steel slag granulation It is an improved version of the HK process, which was originally used for BF slag granulation []A kind of heat resistant alloy steel was used as material of the drum, and the cooling ability for the drum was enhanced in order to fit the high temperature of molten BOF slagSeparation and extraction of iron resources from hazardous electric arc furnace (EAF) steel slag: Aggregation of Ferich layers, magnetic separation, powder characterization Process Safety and Environmental Protection ( IF 69) Pub Date : , DOI: 101016/jpsep202408064Separation and extraction of iron resources from hazardous 2023年11月23日 This study aims at investigating the mechanical and electromagnetic interference (EMI) shielding properties of cementitious composites with combined utilization of recycled carbon fiber (rCF) and steel slag Different dosage of raw steel slag (SS) and wetgrinding steel slag (WSS) as replacement of cement were introduced to the cementitious Simultaneously enhanced mechanical and electromagnetic 2012年1月1日 [9] Yu KX, Zhou Z, Song BY Beneficiation process design of steel slags products by magnetic separation and its production practice Metal mine Res (in Chinese) 2010; 1:1767 [10] Li K, Huang JB Line construction demonstration of steel slag recycling project of Beng steel group Shanxi Metal Res (in Chinese) 2010; 5:324 [11] Liu SZAn Overview of Utilization of Steel Slag ScienceDirect
.jpg)
Comprehensive utilization of steel slag: A review Request PDF
2023年3月1日 Request PDF Comprehensive utilization of steel slag: A review Steel slag, the main solid waste in the steelmaking process, is produced more than 120 million tons annually in China Most of 2006年3月1日 Download Citation Effect of fine steel slag powder on the early hydration process of Portland cement Hydration heat evolution, nonevaporative water, setting time and SEM tests were performed Effect of fine steel slag powder on the early hydration process of 2024年11月12日 Ferronickel, produced from the thermal upgrading of nickeliferous ores, is one of the feed materials for stainless steel production However, traditional hightemperature smelting processes for producing ferronickel are facing increasing pressure due to environmental concerns and decreasing ore grades The pyrometallurgical processing of lowgrade laterites, aimed at A Review of Direct Reduction–Magnetic Separation Process for 2014年1月10日 The grinding of steel slag and magnetic separation are necessary for a better separation of a high grade iron compounds which can be directly recycled in converter steel mill Even, milling at about 50 μm is not sufficient to release complete carrier iron and calcium due to the small size of the crystallitesRecovery of high grade iron compounds from LD slag by enhanced magnetic
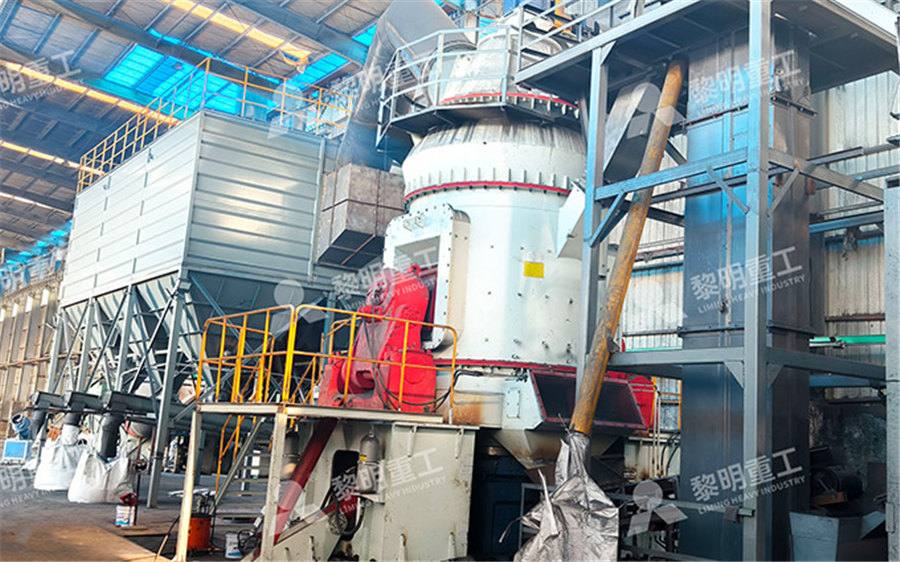
Superconducting magnetic separation of ground steel slag powder
Superconducting magnetic separation of ground steel slag powder for recovery of resources As Fig 2 Magnetic separation rate of steel slag (Velocity of flow=02 m/s) Fig 3 SEM images of steel slag, (a) before magnetic separation, (b) captured at 60 T, (c) passed at 60 T The collected portion of the slag was ranged from 8120%