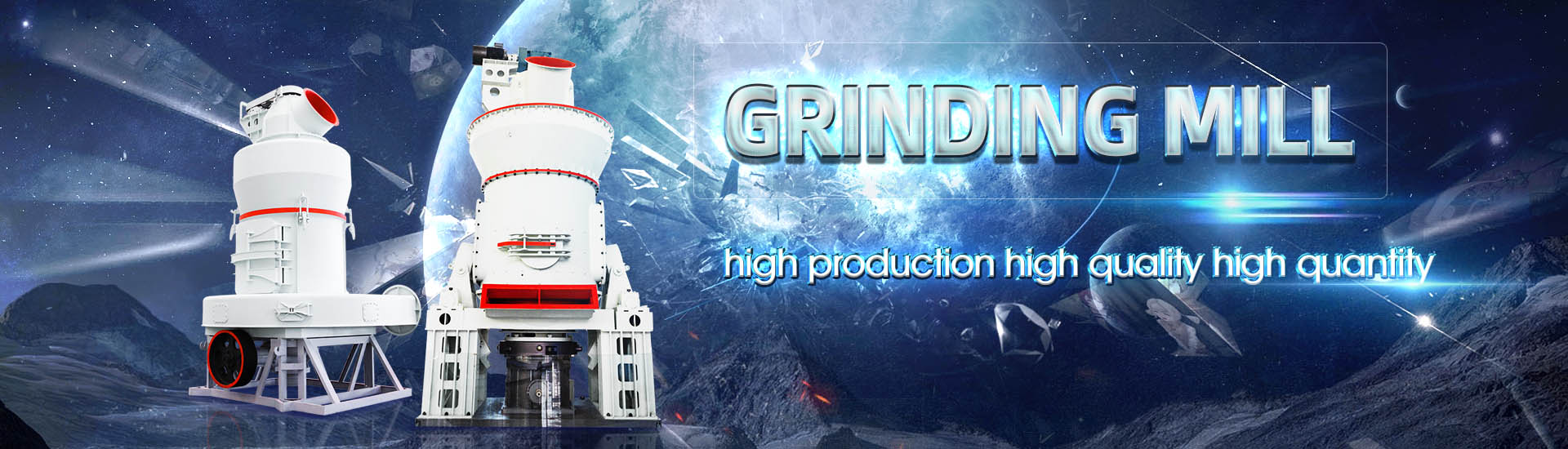
How much is a highefficiency ore grinding machine
.jpg)
Our Dynamic HPGR Technology for Mineral Grinding
With low energy consumption, low maintenance requirements, excellent throughput capacity and high availability, Enduron® high pressure grinding rolls (HPGR) are a proven way to improve the efficiency of aggregate and mineral Optimise your results with a high pressure grinding roll, the most energyefficient way to process mining ores Suitable for industries including iron ore, precious metals, base metals and other, FLS High Pressure Grinding Rolls – Efficient grinding• Very high intensity attrition grinding mechanism, suited to fines grinding • Small media size, essential to increase grinding efficiency for fines • The use of inert grinding media This can Fine Grinding as Enabling Technology – The IsaMillAlthough 60% of total energy is estimated to be consumed in mining equipment, this category covers a very wide variety of different equipment Comminution, consuming close to 40% of total energy contains a single piece of MINING ENERGY CONSUMPTION 2021 CEEC
.jpg)
Helping to reduce mining industry carbon emissions: A stepby
2022年3月30日 High Pressure Grinding Rolls (HPGR) circuits have the potential to reduce the Mining Industry’s CO 2 emissions by up to 345 megatonnes/year, or 435% when compared 2019年8月7日 As a single HPGR unit only uses 08 25 kWh per tonne of material, they not only saving you money but freeing up capacity for downstream milling The high pressure of Why HPGRs are revolutionising mill circuits WeirHPGRs (high pressure grinding rolls) have been developed within the last decades for energy efficient processing of a wide variety of ores Special interest has been raised by projects Quantification of HPGR energy efficiency effects on downstream Metso HIGmill™ is an advanced and energyefficient fine and ultrafine grinding solution that relies on proven technology The mill takes advantage of gravitational forces and GrindForce™ rotor technology to produce a finer grind HIGmill high intensity grinding mill Metso

Energy efficiency of stateoftheart grinding processes
2018年1月1日 Another study identified that grinding machines had a share of 28% on installed CNC machine tools in the EU27 in 2009 [4] When considering the energetic performance of a production system in general and a grinding machine in particular, it is necessary to differentiate between efficiency and effectiveness2022年12月8日 CNC grinders combine a highspeed grinding operation with precision and an excellent surface finish Here is our guide on what to know when buying these machinesCNC Grinding Machine Buyers Guide: Types, Price, June 2022; ARCHIVE Proceedings of the Institution of Mechanical Engineers Part C Journal of Mechanical Engineering Science 19891996 (vols 203210) 236(2):1107(PDF) A comprehensive review on the grinding process: 2023年2月24日 Many grinding machines now have builtin automatic wheel changers and dressing units, which allow for several gradations of grinding in one clamping The greatest benefit of continuous dress creep feed grinding (CDCF) may be in undoing the traditional elongated process of milling, heat treatment, deburring and finishing by combining those applications into Milling vs Grinding: For Deep Cuts, Grinding Might Be Better
.jpg)
Towards Sustainable Grinding of DifficulttoCut Alloys—A
2024年3月11日 31 Development of Grinding Techniques Grinding is the most commonly used technology in abrasive machining and one of the most critical technologies for precision manufacturing difficulttocut alloys such as superalloys [2, 15, 31] and titanium alloys [32, 33] with high strengthIt is meaningful to study and improve the sustainability of grinding technology2020年6月29日 Gratio The Gratio is the ratio of the amount of stock removed versus the amount of wear on the wheel, measured in cubic inches per minute This ratio will vary from 10 to 50 in very rough grinding, and up to 250 to 500 in finish grindingChapter 17: Grinding Methods and Machines American Machinist2017年10月26日 The following are factors that have been investigated and applied in conventional ball milling in order to maximize grinding efficiency: 911 Metallurgist Flotation Machines: HighPerformance Turner (1979) has demonstrated an overall increase in capacity of almost 800 percent by ball addition to an ore of extreme Factors Affecting Ball Mill Grinding Efficiency2021年4月16日 Grinding hand tools A die grinder is a highspeed rotary tool that is typically powered by compressed air The tool has a smalldiameter abrasive bit that rotates to get the job done Check out Choosing the Right Air Die Grinder for more information and some recommended models Angle grinders are also abrasive hand tools Unlike die grinders, Intro to Grinding Methods, Machines and Tools
.jpg)
Breaking down energy consumption in industrial grinding mills
2017年1月17日 Other process activities, such as spraying the ore with water for dust control or the fact that runofmine ore moisture is approximately 2%5% are not generally considered (Bleiwas, 2012a)2022年8月31日 In addition, the sphalerite had a more prominent effect on the grinding characteristics of the ore The grinding speed of ore and its component minerals decreased exponentially with the grinding time, and the instantaneous grinding speed of 0 min was negatively correlated with the feed sizesGrinding Modeling and Energy Efficiency in Ore/Raw Material 2022年6月24日 Grinding is a manufacturing process which significantly contributes in producing high precision and durable components required in numerous An experimental investigation of the effects of workpiece and grinding parameters on minimum quantity lubrication—MQL grinding Int J Machine Tools Manufacture 2009; 49(12–13): 924 A comprehensive review on the grinding process: Advancements 2016年3月21日 where R represents the ratio: % Pb in crude ore/% Cu in crude ore Formula (32) is very convenient for milling calculations on ores of this type Example: An ore contains 5% lead and 1% copper The ratio of perfect Common Basic Formulas for Mineral Processing
.jpg)
Factors affecting ores grinding performance in ball mills
The effect of milling time and speed on ore grinding performance Milling time and speed are two important factors that affect ore grinding performance in ball mills The longer the milling time, the more fines will be processed, which will lead to a lower grind efficiency2021年11月27日 Because of the high material removal rate creepfeed grinding can deliver in challenging materials, grinding might not be just the last step in the process—it might be the process Read More Automation 29 Sep 20237 Key Factors in Choosing a Grinding Wheel Modern Machine 2024年10月17日 How much does an ore crushing machine cost? Finding a highyield, reliable small ore crusher is a key concern for customers regarding cost The price of ore grinding machines varies due to multiple factors, including production capacity requirements, material characteristics, equipment configuration, and brand and service The price range varies from What types of ore crusher are there and how much does one costThe Grinding Laws and Machines Grinding is an essential process in the mining industry, and it involves breaking down large pieces of ore into smaller fragments The grinding laws are fundamental principles that guide the design and operation of grinding machines These laws include Kick's law, Bond's law, and Rittinger's lawUnderstanding the SAG Mill in Copper Ore Mining Process
.jpg)
(PDF) Grinding Media in Ball MillsA Review ResearchGate
2023年4月23日 high speeds of about 90%, causing breakage o f large ore particles wh ilst reducing the mill’s energy efficiency The num ber of cataracting media increases as mill speed increases [ 62 ] 2019年3月7日 Here, b s is set as 200 μm according to the average measurement value of conditioned diamond wheel with D213 μm abrasive size, θ is set as 353° in view of the abrasive grain shape [], C is the grain density on wheel surface and is 1093/mm 2 for D213 μm wheel based on the experimental measurement The calculated maximum undeformed chip High Efficiency Precision Grinding of Microstructured SiC 2024年10月5日 Highspeed grinding (HSG) is an advanced technology for precision machining of difficulttocut materials in aerospace and other fields, which could solve surface burns, defects and improve surface integrity by increasing the linear speed of the grinding wheel The advantages of HSG have been preliminarily confirmed and the equipment has been built for Highspeed grinding: from mechanism to machine tool2021年11月23日 This is a small grinder operated with electric power It can be easily carried anywhere Grinding can be done by holding it in hand It is used for cleaning heavy welding jobs On one end of the motor shaft, a grinding wheel is fitted and on the other end, a handle or switch for operating the machine is fixed according to our convenience14 Types of Grinding Machines [Working, Diagram PDF] The

What is Grinding: Definition, Process, Types
2024年1月23日 HighPrecision Grinding Machines: These machines are designed for intricate and precise grinding tasks They often include advanced features like CNC (Computer Numerical Control) systems Prices for such 2022年2月16日 A 5axis grinding machine is a cutter grinder commonly used to shape and sharpen milling cutters and other tool bits 5axis tool ensuring optimal stability during severe grinding It provides both high precision and Grinding Machine Types How it works Phillips 1993年1月1日 An efficient grinding process, especially HEDG and creep feed grinding processes; can only be operational if using a high performance grinding machine with a proper grinding wheel and an adequate (PDF) High Efficiency Deep Grinding ResearchGate2017年11月2日 Many scientists contributed to the analysis of temperatures in grinding leading up to presentday understanding This paper draws together important developments from various papers and aims to identify an improved general approach to thermal analysis with wide applicability including for conventional fine grinding, creep feed grinding, and high efficiency Temperatures in Grinding—A Review ASME Digital Collection
.jpg)
Energy efficiency of stateoftheart grinding processes
2018年1月1日 Dependence of specific energy consumption í µí± í µí± (left) and energetic process efficiency í µí¼ í µí¼ í µí± í µí± (right) on cutting speed and specific material removal 2023年10月17日 3 Ultrafine Powder Grinding Mill Ultrafine powder mill (threering / fourring mediumspeed micropowder mill) feed particle size ≤25 mm, production capacity 0545 t/h, production fineness 1503500 mesh,it is a highefficiency and lowconsumption ultrafine powder processing equipment that successfully replaces the traditional jet mill and complex process How to choose a suitable ore powder grinding mill?Creepfeed grinding (CFG) was a grinding process which was invented in Germany in the late 1950s by Edmund and Gerhard Lang Normal grinding is used primarily to finish surfaces, but CFG is used for high rates of material removal, competing with milling and turning as a manufacturing process choice CFG has grinding depth up to 6 mm (0236 inches) and Grinding (abrasive cutting) Wikipedia2019年6月21日 Nextgeneration grinding technologies in particular offer vast scope for improvement, and machines such as highpressure grinding rolls (HPGRs) and vertical stirred mills that were introduced 30 Grinding down energy consumption in comminution
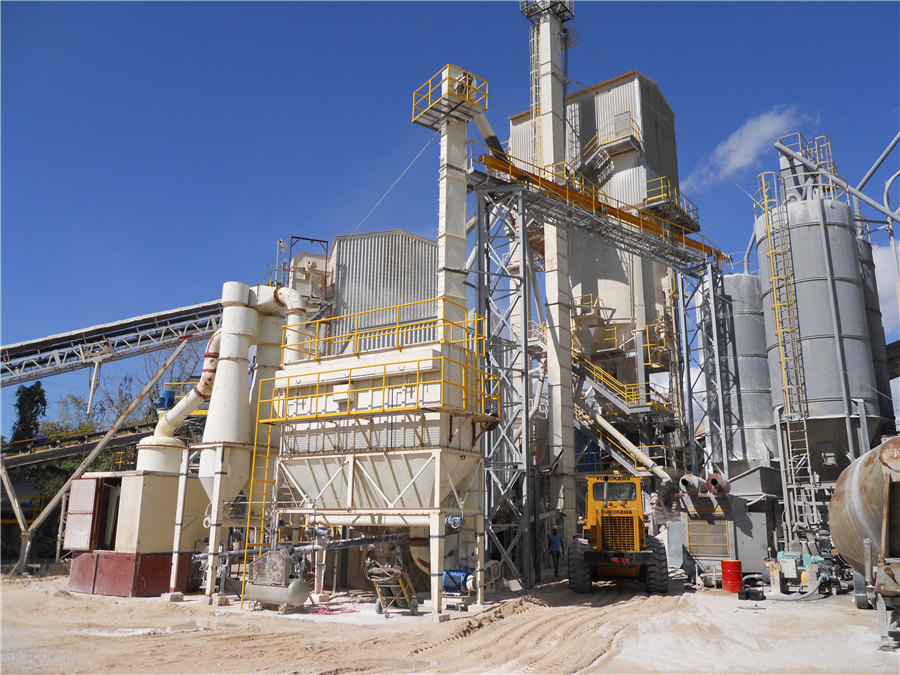
Application of sustainable techniques in grinding process for
2024年3月11日 Grinding is a machining process that entails the meticulous removal of material from a workpiece through the utilization of abrasive grains []This method, executed by grinding machines, is pivotal for achieving stringent tolerances, refining surface finishes, and sculpting specific shapes or profiles []Abrasive materials like aluminium oxide, silicon carbide, diamond, 911 Metallurgist can enter the scene and see what you have become blind to We can fix issues in ways you never thought possible Our fresh eyes will open new opportunities for your plant Each mineral processing plant has varied ore types, mining equipment, (crusher, ball mill, flotation, tailings), and management (operating) philosophyThe evaluation and prioritization of variables Metallurgists Mineral Processing Engineers 911Metallurgist2016年6月20日 Efficiency The amount of loading influences screening efficiency In practice it is impossible to reach 100% efficiency Maximum efficiency is about 95% In most of the cases 90% is achieved and the screen Ore, Rock Aggregate Screening (Complete Guide)2022年11月28日 Therefore, before grinding, the workpiece is usually removed by other cutting methods to remove most of the machining allowance, leaving only 01~1mm or less of the grinding allowance With the development of high What is Grinding Process How It Works Different
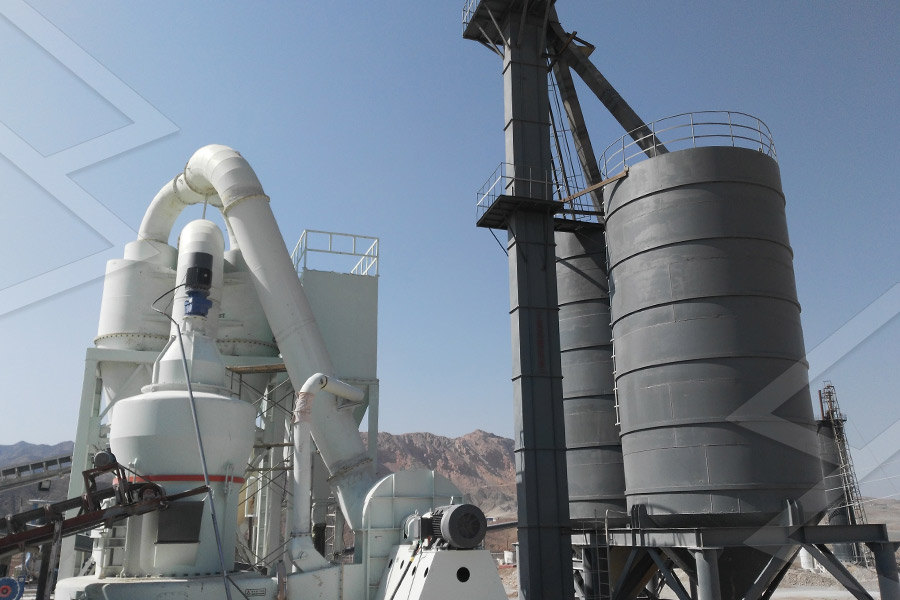
Ball Rod Mill Density – How Water Impacts Grinding
2015年8月6日 If the rate of flow is too great the ore will not get the opportunity to be ground before all the fine material has been washed away Soon there will only be the large and intermediate size of feed left in the mill Mill slurry characteristics affect grinding efficiency because of their influence on slurry rheology2001年1月1日 Regimes of deep grinding range from creep grinding conducted at low workspeeds to High Efficiency Deep Grinding (HEDG) at fast workspeeds RS Hahn, On the nature of the grinding process, Proceedings 3rd Machine Tool Design and Research Conference, 1962, pp 129–154Thermal analysis of high efficiency deep grinding ScienceDirectIt is able to reduce the ore from size 2070mm to below 3mm High crushing efficiency, low energy consumption Ores output from HPGR are with high ratio of fine particle, and the internal of the ore will have a lot of micro cracks More fine particle and micro cracks will help to highly reduce the ore grinding cost(HPGR) high pressure grinding rolls/rollers for cement, oresFor example, a 5% incremental improvement in energy efficiency across comminution could result in greenhouse gas emissions reductions of more than 30M tonnes of CO2e2 Primary energy, that is—energy that is combusted directly to drive mobile equipment or generate electricity—was also explored in this study by analysing different ways in which mine sites may generate or MINING ENERGY CONSUMPTION 2021 CEEC (Coalition for Eco
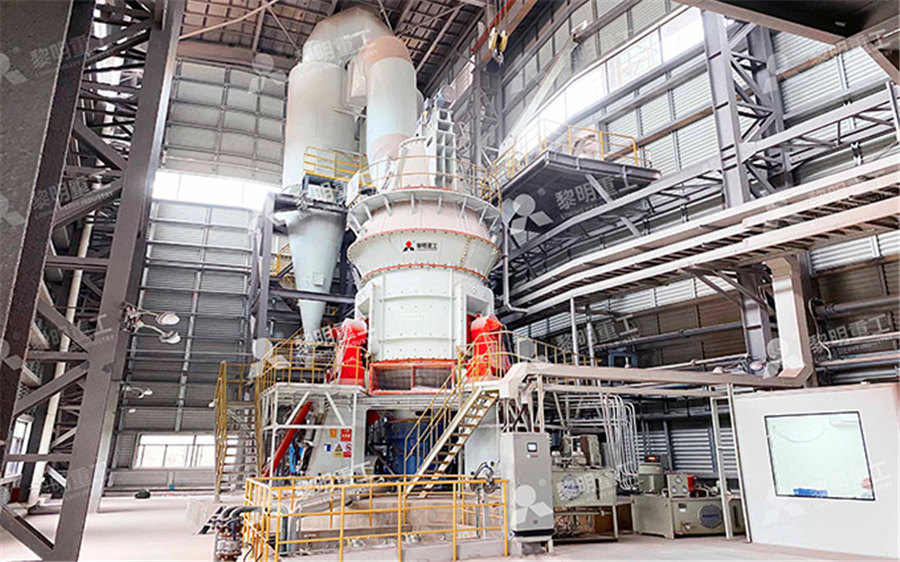
How to Measure Grinding Efficiency 911Metallurgist
2018年4月20日 Efficiency factor Wioc ÷ Wi 121; Grinding Efficiency in % 826; Ball mill feed micrometers 1300; Ball mill product micrometers 115; Ball mill ratio of reduction 113; Power per metric tonne motor input Kw 92; Calculated operating work index Wio 1575; On basis motor output 42 x 0956 + 92 x 0947 = 1273 Kw/tonne 1575 x 1273 ÷ 134 14年1月1日 Superb grinding machines now produce optical quality finishes due to developments in process control and machine design It is the same for extremely high removal ratesPrinciples of Modern Grinding Technology ResearchGate2019年10月8日 The crushing and grinding operations are an important part of the processing of mineral resources, and it is also operation with high investment and high energy consumption In the case of metal mines, equipment investment in crushing operations accounts for 65% to 70% of the total plant value, power consumption is about 50% to 65%, and steel consumption is as Crushing and Grinding Process JXSC Machine2021年8月20日 This can happen in more aggressive grinding or when grinding certain metals that tend to stick to the grinding wheel In these applications, scrubber nozzles might need to be implemented Scrubber nozzles are typically highpressure (5001,000 psi), lowflow rate devices that are targeted after the grinding zone to remove chips from the wheel structure5 Grinding Considerations for Improving Surface Finish