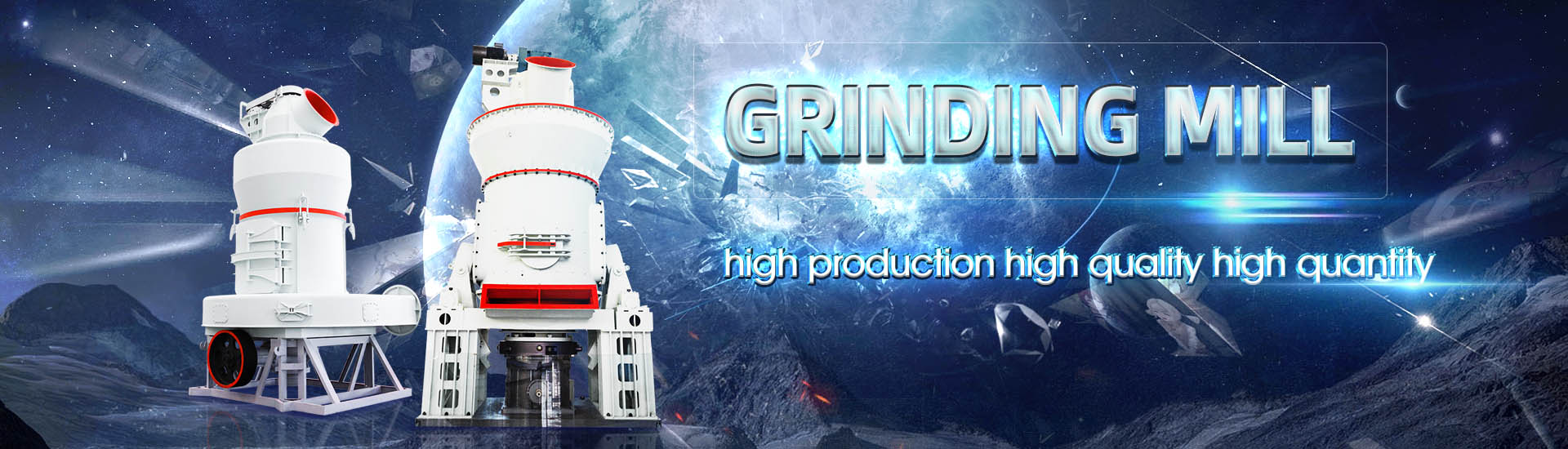
How to reduce the power consumption of ball mill
.jpg)
Ball Mill Design/Power Calculation 911Metallurgist
2015年6月19日 The ball mill motor power requirement calculated above as 1400 HP is the power that must be applied at the mill drive in order to grind the This paper will focus on the ball mill grinding process, its tools and optimisation possibilities (see Figure 1) The ball mill comminution process has a high electrical energy consumption, BALL MILLS Ball mill optimisation Holzinger Consulting2017年8月15日 Reducing the instantaneous power demands is an effective approach to reduce energy consumption, which can be achieved by energyoriented component design Energy consumption in machining: Classification, prediction, and 2001年8月1日 In this paper, we analyse the effect of changes in particle size and shape distribution (for both balls and rocks), lifter pattern and profile, and fill level on power draw and Charge behaviour and power consumption in ball mills: sensitivity
.jpg)
How to reduce the energy consumption of ball mill
2021年6月2日 These two methods can effectively reduce the energy consumption of ball mill 2 Reduce the feed particle size The larger the grinding particle size of the ball mill, the greater2020年2月26日 Owing to the lack of effective energy consumption models of ball mills in the ceramic industry, a calculation model to forecast energy consumption of ceramic ball mills Calculation method and its application for energy consumption of 2023年8月21日 The main way to improve the performance of ball mills is to optimize the operating modes of the electric drive and mill equipment, to ensure stable operation of the ball Improvement of methods to ensure energy efficiency of ball mills 2017年10月25日 Ball Mill Breakage Efficiency Consider a ball mill circuit processing material of a given feed size and at a given throughput rate to a target product size, the latter which once How to Improve Ball Mill Performance 911Metallurgist
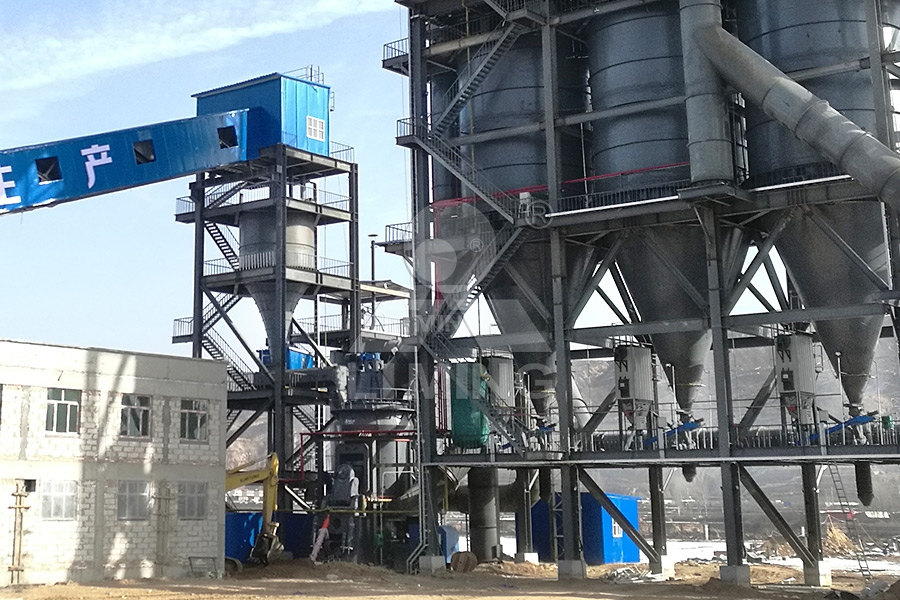
How to improve ball mill output quality and reduce power consumption
2020年3月19日 The power consumption of raw meal and cement ball mills accounts for about 23% of the power consumption of cement plants and about 13% of the cost of cement Therefore, in order to reduce power consumption, reduce costs, and improve economic efficiency, it is necessary to significantly increase the mill output2001年8月1日 Discrete element method (DEM) modelling has been used to systematically study the effects of changes in mill operating parameters and particle properties on the charge shape and power draw of a 5m ball mill Specifically, changes in charge fill level, lifter shape (either by design or wear) and lifter pattern are analysed The effects of changes to the properties of the Charge behaviour and power consumption in ball mills: 2023年5月12日 The main issue of improvement is to reduce the power consumption of a balltube mill with crosslongitudinal movement of the load A comparative analysis and the possibility of using the known methods for calculating the power consumption of the drive of a balltube mill with crosslongitudinal movement of grinding bodies is givenPower Calculation of BallTube Mill Drives in the Construction 2017年7月26日 We will consider an ore with a ball mill work index varying between 16 and 13, feeding into a single stage ball mill operation with one million kilowatts per day consumed power For the particular mill configuration, a performance graph, Fig (21), has been constructed according to Bond’s methodsHow Ball Mill Ore Feed Size Affects Tonnage Capacity

Energy consumption model for milling processes considering
2019年11月14日 With the modern manufacturing industry evolving and advancing and amid a more energy conscious society, high energy demand in manufacturing—particularly in machining—has drawn more and more attention Accurate energy consumption modelling is critical to the improvement of energy efficiency in machining In the existing energy models of 2022年3月15日 Power consumption management and simulation of optimized operational conditions of ball mills using the Morrell Power model: A case study March 2022 DOI: 1017794/rgn2022211(PDF) Power consumption management and simulation of 2013年7月15日 The sample was received crushed appropriately for the ball mill test Ball Mill Grindability Test was conducted by standard practice using 100mesh (150 pm) closing screens The ball mill work index is shown below BM Wi (kWhr/st) = 1797 ; Bond Work Index FormulaEquation 911MetallurgistThe required power consumption of a grinding mill based on the calculations shown above can be estimated thanks to this free Excel calculator : Calculation Tool Grinding Mill Power Calculation Warning : this calculator is provided to illustrate the concepts mentioned in this webpage, it is not intended for detail design Grinding power : step by step calculation PowderProcess
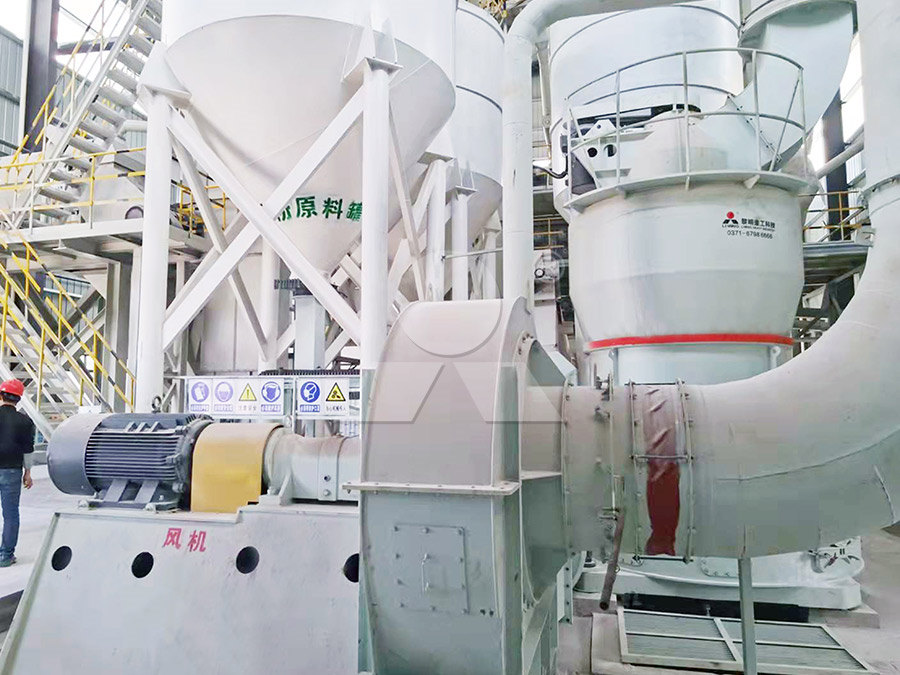
(PDF) Energy Efficient Ball Mill Circuit – Equipment Sizing
2013年7月15日 A powerbased method is first utilised to determ ine the required ball mill power consumption to achieve the required product P80 used to reduce the selected ball mill size and power2018年12月13日 To investigate the power of ball mill with differing lifter shapes, a series of Discrete Element Method (DEM) simulations were performed on a ball millEffect of Lifter Shapes on the Mill Power in a Ball Mill2021年6月2日 Therefore, reasonable ball size ratio can not only reduce the steel consumption of ball mill, but also effectively improve the grinding efficiency 5 control grinding concentrationHow to effectively reduce the energy consumption of 2021年6月2日 In order to reduce the power consumption of the ball mill, the feed particle size of grinding can be reduced Therefore, the product particle size of crushing is required to be small, How to reduce the energy consumption of ball mill
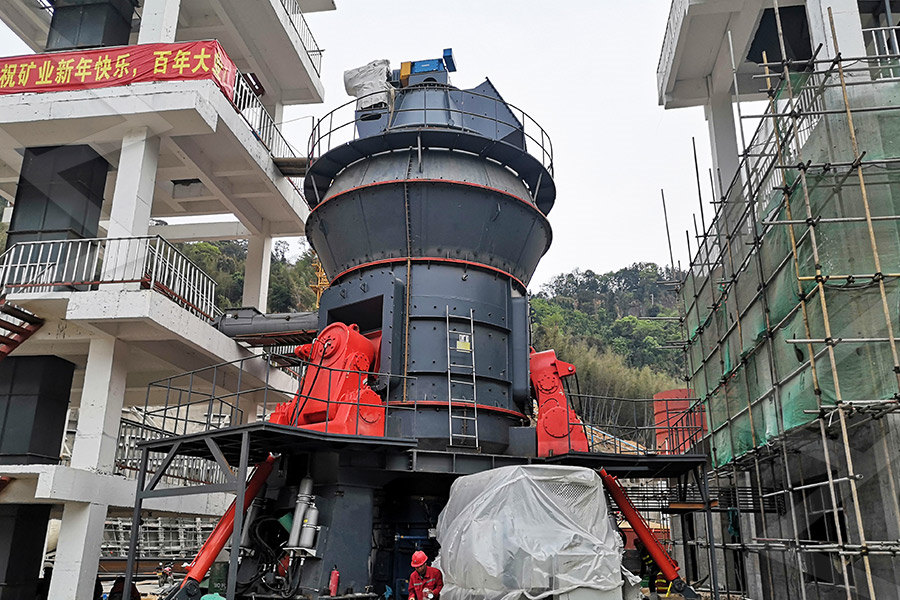
Ball Mill Capacity and Power Consumption Relationship to Mill
2020年11月16日 where v = peripheral speed of the mill in feet per minute If the observed capacity of a mill at speed n1 is = T1 tph, the capacity T2 of the same mill at speed n2 should be The acceleration factor of the ball or rod mass is a function of the peripheral speed of the mill Thus P = f4(F) = f1(D²)f5(υ) Indicating that υ = πDn, and2 More crushing and less grinding to reduce the feed size into mill The larger feed size, the more work that the ball mill needs to do on the ore To achieve the specified grinding fineness, the workload of ball mill will be increased inevitably, and then, the energy consumption and power consumption will be increased accordingly10 Ways to Improve the Grinding Efficiency of Your Ball Mill2017年10月26日 The following are factors that have been investigated and applied in conventional ball milling in order to maximize grinding efficiency: a) Mill Geometry and Speed – Bond (1954) observed grinding efficiency to be a function of ball mill diameter, and established empirical relationships for recommended media size and mill speed that take this factor into Factors Affecting Ball Mill Grinding Efficiency2024年6月14日 Improving the efficiency of a ball mill involves several factors, HighEfficiency Motors: Use energyefficient motors and drives to reduce power consumption 7How to increase the efficiency of a ball mill LinkedIn
.jpg)
Ball Mill Design/Power Calculation LinkedIn
2016年12月12日 If P is less than 80% passing 70 microns, power consumption will be Ball Mill Power Calculation Example A wet grinding ball mill in closed circuit is to be fed 100 TPH of a material with a work 2013年5月14日 And practices prove that the unit energy consumption of wet ball mill can reduce to some degree after adopting the rubber scaleboard, it usually can reduce 10% What's more, the service life of the rubber scaleboard is 2 or 3 times longer than the alloy scaleboardThe most remarkable thing is that besides reducing energy consumption, the rubber scaleboard can also How to Reduce the Energy Consumption of Ball Mill from 2019年4月22日 2 More crushing and less grinding to reduce the feed size into mill The larger feed size, the more work that the ball mill needs to do on the oreTen Ways to Improve the Grinding Efficiency of Your Ball Mill2022年5月9日 Modeling of energy consumption factors for an industrial cement vertical roller mill by SHAPXGBoost: a "conscious lab" approachModeling of energy consumption factors for an industrial cement
}@~3SRDG`IA1KP_ICWAA.jpg)
OPTIMIZATION OF CEMENT GRINDING OPERATION IN BALL MILLS
run factor Consistent quality and maximum output with lower specific power consumption results in lower operating costs per unit of production Optimization can also reduce the cost of liners and grinding media The cost of optimization is minimal since 2020年3月21日 Under the condition that the ball mill speed is constant, the filling rate is large, the steel ball hits the material many times, the grinding area is large, the grinding effect is strong, but the power consumption is also large, and the Top 10 tips to improve the grinding efficiency of ball 2015年10月23日 Grinding of cement to a lower Blaine value will reduce the specific power consumption A comparison of typical specific energy consumption of Cemex ® mill with conventional multicompartment ball mill EnergyEfficient Technologies in Cement Grinding2021年6月29日 Nowadays, ball mills are widely used in cement plants to grind clinker and gypsum to produce cement The research focuses on the mill speed as well as air classifier speed effect on the two Effects of Mill Speed and Air Classifier Speed on Performance of
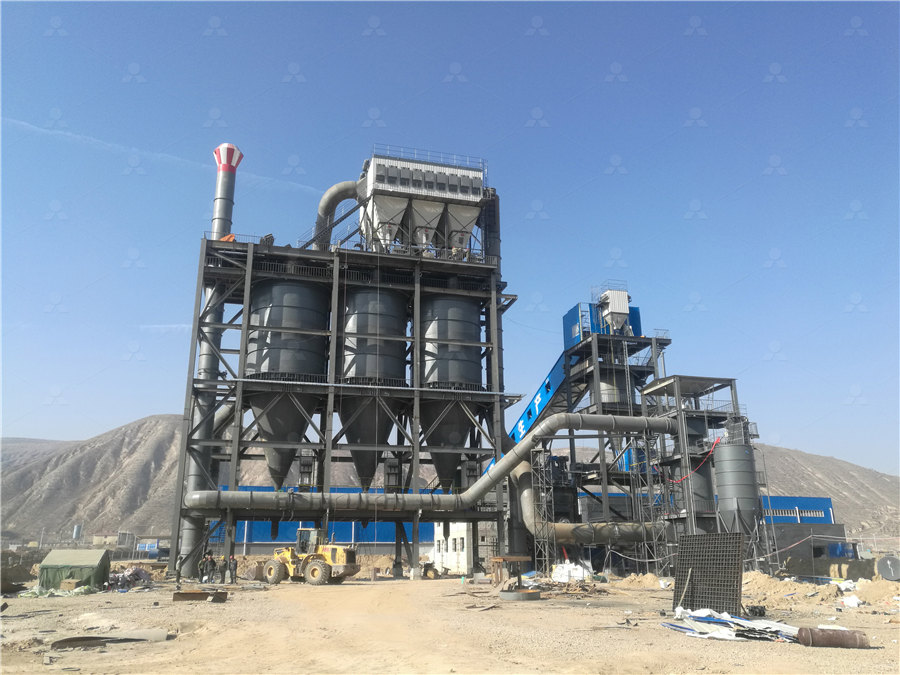
Modeling of power consumption of ball mill Request PDF
2016年1月1日 Request PDF Modeling of power consumption of ball mill It was established that, addition of boron reduces thermal stability TiH1,9 more, than on 3000C; 2014年10月20日 The ball mill is the most common ore grinding technology today, and probably more than 50% of the total world energy consumption for ore grinding is consumed in ball millsEffect of circulating load and classification efficiency on HPGR The performance of the cement ball mill in cement grinding system directly affects the output capacity and cement quality of the cement plant clinker discharged from the cement kiln must be pretreated to reduce its particle size so as to increase the output and reduce the power consumption of the ball millHow to Improve Cement Ball Mill Performance2021年1月19日 Our paper presents the hammer mill working process optimization problem destined for milling energetic biomass (MiscanthusGiganteus and Salix Viminalis)(PDF) Optimization Issues of a Hammer Mill Working Process
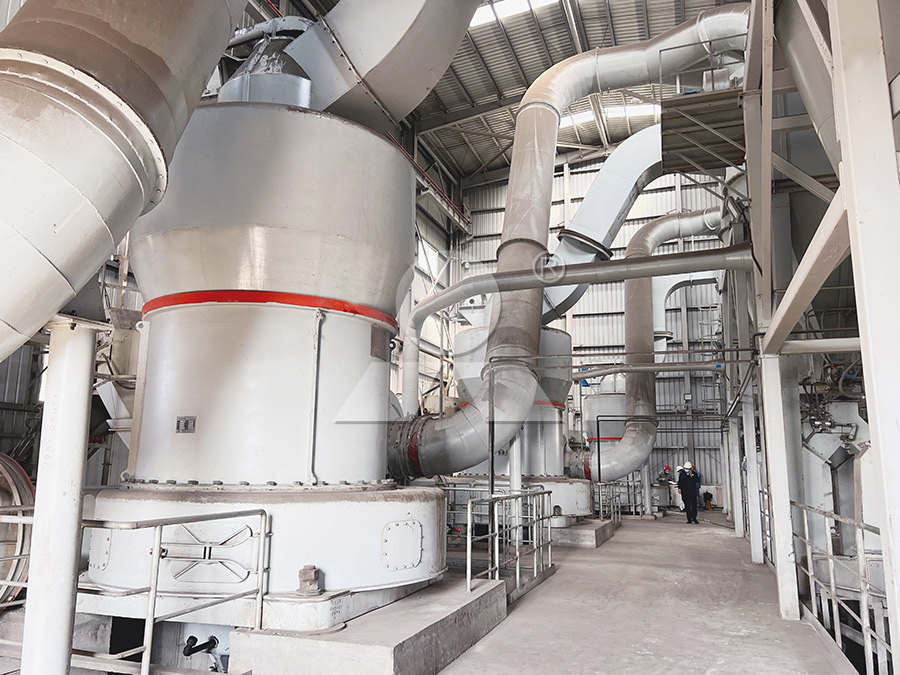
Variables in Ball Mill Operation Paul O Abbe
Ball mill operation is often regarded as something of a mystery for several reasons Ball milling is not an art If we reduce this to ½” then there will be 24x24x24 or 13,824 pieces of media An 8 fold increase The first issue to resolve then is how large, or small, 2015年10月9日 Calculating a grinding circuit’s circulating loads based on Screen Analysis of its slurries Compared to %Solids or Density based Circulating load equations, a more precise method of determining grinding circuit tonnages uses the screen size distributions of the pulps instead of the dilution ratiosPulp samples collected around the ball mill or rod mill and Ball Mill Circulating Load Formula 911Metallurgist2017年4月22日 When the volume of ball charge is reduced, within certain limits, the power consumption per unit of ball charge is increased, because the center of gravity of the charge is further from the axis of the mill; but as the mass of balls is more active and circulates more freely, the crushing efficiency is increased proportionately to the increase in power consumption per Ball Milling 911Metallurgist2020年5月1日 The main aim of this study is to improve the processing capacity of the largescale ball mill Taking a Φ549 × 883 m ball mill as the research object, the reason for the low processing capacity of the ball mill was explored via process mineralogy, physicochemical analysis, workshop process investigation, and the power consumption methodEnhancing the capacity of largescale ball mill through process
.jpg)
Improvements in New Existing Cement Grinding
Factors affecting ball mill performance 4 Ball mill improvements case Every 100 cm²/g increase in cement fineness increases the mill power consumption by 12 kWh/t for a closed circuit mill 23 kWh/t for an flyash pozzolana for It requires significant power to rotate the mill and cause the balls inside to impact and grind the material effectively Detailed Explanation: 4 Key Factors Influencing Ball Mill Power Consumption 1 Mechanism of Energy Consumption Ball mills operate by rotating a cylindrical shell partially filled with grinding media (usually balls)How much power does a ball mill use? 4 Key Factors to Consider2017年2月13日 On the class of work for which it is especially suitable the power consumption of a rod mill is about threequarters that of a ball mill with the production of less undersize The rod and liner consumption is also about 75% of that of a ball mill, and rods cost less than balls because they are more easily manufacturedBall Mills 911Metallurgist2021年1月1日 India is the world's second largest producer of cement and produces more than 8 per cent of global capacity Due to the rapidly growing demand in various sectors such as defense, housing, commercial and industrial construction, government initiative such as smart cities PMAY, cement production in India is expected to touch 550–600 million tones per Review on vertical roller mill in cement industry its performance
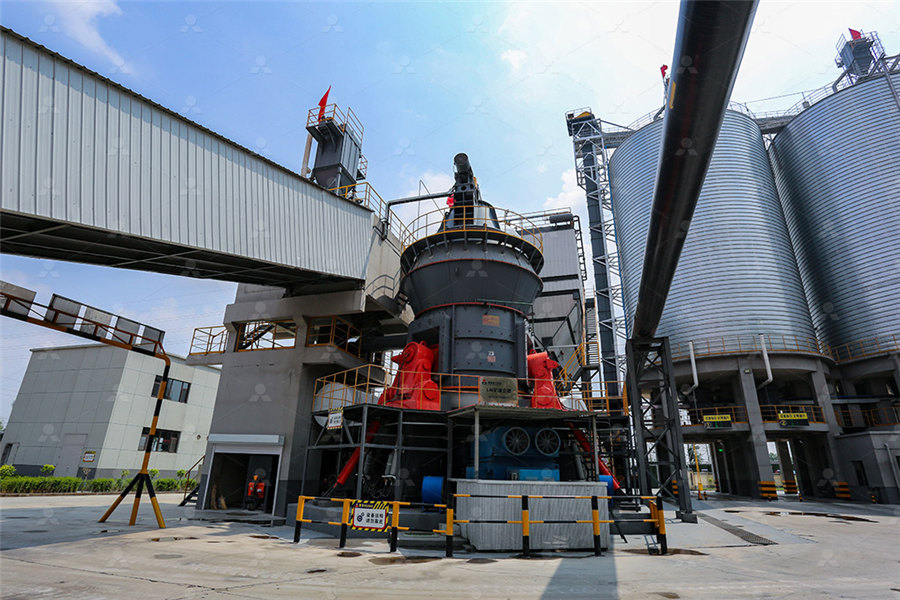
9 ways tell you how to improve ball mill efficiency
2021年7月5日 Ball mill is the key machine in the grinding stage,how toimprove the grinding area is large, the grinding effect is strong, but the power consumption is also large, and the filling rate is too high, which will easily cause the steel ball to move Changes have taken place to reduce the impact on largeparticle materials 4 2020年6月23日 The potential to make full use of the available power in a ball mill through conversion from overflow to grate discharge often results in the mill being able to process more tonnes per hour or achieve a more suitable product size to increase the overall production, and hence revenue, from an operationConverting a ball mill from overflow to grate discharge Metso2017年5月1日 When a ball mill works at a relatively high speed, its net power consumption can be determined, as indicated in Table 1, where m is the mass of the charge, φ is the fill level, ψ is the rotation rate (constant fraction of the critical speed), ρ is the density of the granular pile, V is the internal volume of the ball mill, D is the internal diameter of the ball mill, and d j is the Effect of lifters and mill speed on particle behaviour, torque, and Nowadays, in the field of cement grinding system of the world cement industry, the major cement grinding equipments include loop flow ball mill, roller press, ball mill semifinishing system, and vertical mill system, in which ball mill and vertical mill are 2 major cement grinding systems in Cement Manufacturing PlantsPower Consumption of Cement Manufacturing Plant