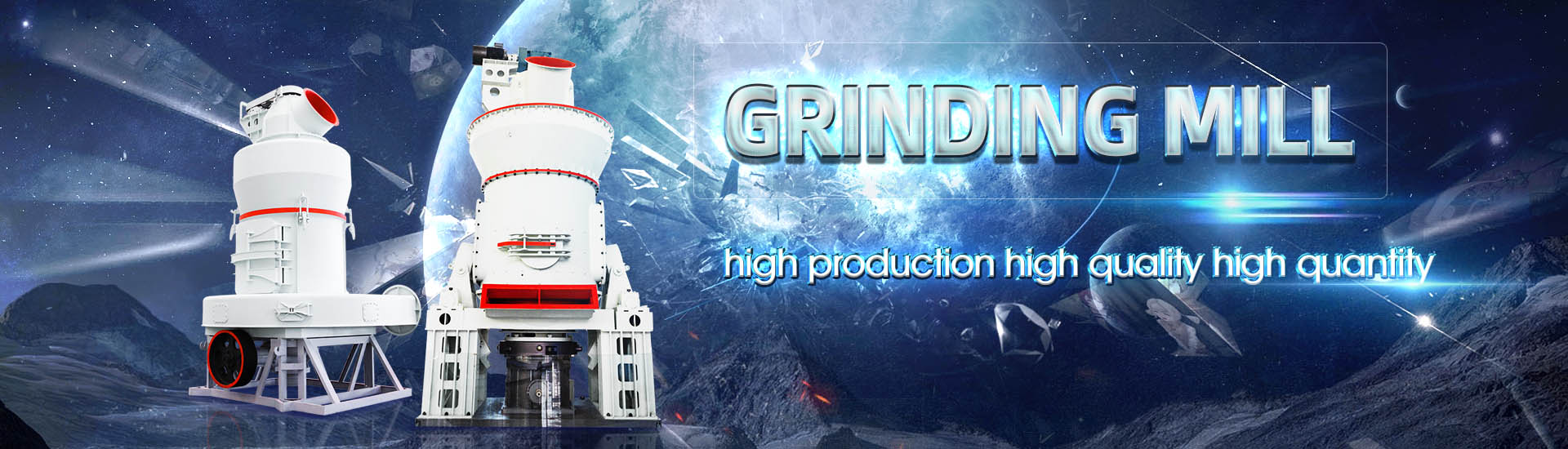
Reason for fast speed of ore mill
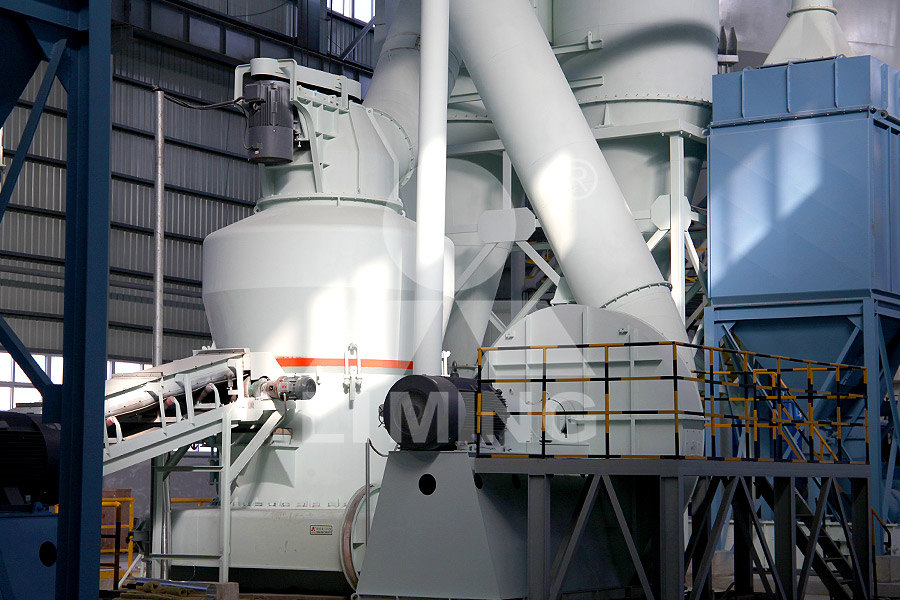
Mill Speed an overview ScienceDirect Topics
2011年8月1日 Milling speed is one of the most important milling parameters that controls the milling process because it provides the mill with the energy required for (1) powder particles and grainsize refining (topdown approach), (2) solidstate reaction, (3) solidstate reduction, (4) 2024年5月14日 Predictability, precision and speed: Robotics ensure consistent, optimal liner exchange so operators can maximise mill availability and grinding efficiency throughout the Higher performing liners + fast relining = higher throughputTo get rid of pulp and rocks in the charge, a mill grindout (no ore feed) of 10 to 20 minutes is also performed before mill inspection or relining The complete grindout is required to obtain the Optimization of mill performance by using1983年1月1日 Some of the possible advantages are: o Quicker control of product size or circulating load o Power savings due to more efficient grinding o Better control of processes Mill Speed as a Manipulated Variable for Ball Mill Grinding Control
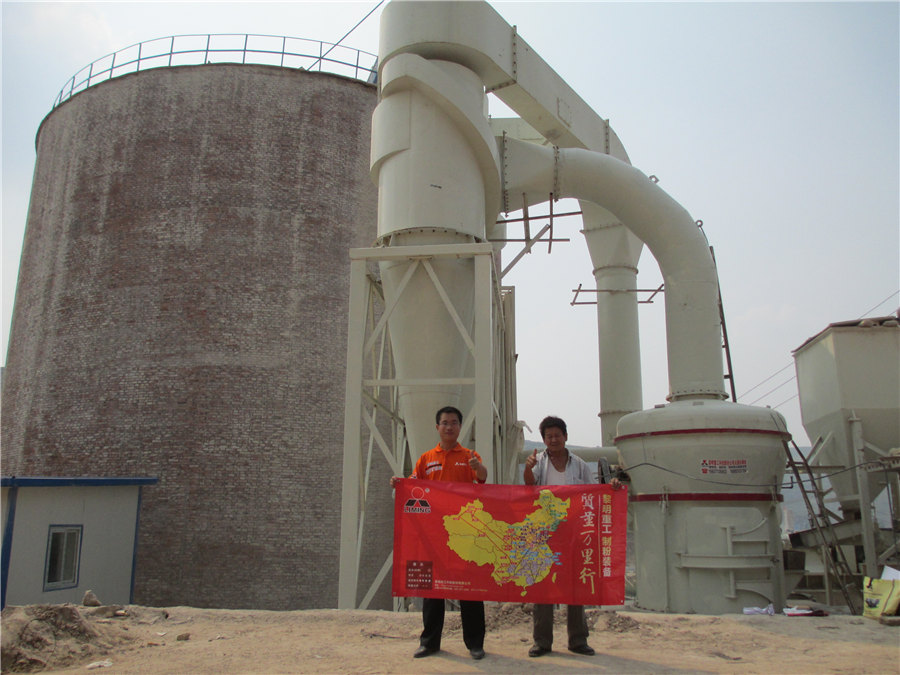
Factors affecting ores grinding performance in ball mills
Milling time and speed are two important factors that affect ore grinding performance in ball mills The longer the milling time, the more fines will be processed, which will lead to a lower grind SemiAutogenous Grinding mills can be optimized for maximum ore throughput or maximum grinding energy efficiency In both cases, precise control of the mill weight is critical Model SAG Mill Optimization using Model Predictive Control Andritz2020年10月13日 The results of the analyses clearly show that using a sieve of +180µm and its bottom180µm, the best time for grinding 05kg of Itakpe iron ore with 3kg of grinding media THE EFFECTS OF PROCESS VARIABLES ON THE GRINDING OF The results of the analyses clearly shows that using a sieve of +180µm and its bottom 180µm, the best time for grinding 05kg of Itakpe iron ore with 3kg of grinding media and a mill speed THE EFFECTS OF PROCESS VARIABLES ON THE GRINDING OF
.jpg)
Operational parameters affecting the vertical roller mill
2017年4月1日 The control of the circulating load is achieved by adjusting the pressure drop over the mill comprising out of the gas flow and the solid loading inside the mill Higher classifier An investigation of these 'milling curves' on a 26x16ft (DxL) SAG mill operated at speeds of 60% to 75% of critical speed and fillings between 20% and 45% is presented SAG mills areMILLING CURVES AS A TOOL FOR CHARACTERISING SAG MILL 2017年3月20日 Ball mill process parameters for five ground samples with ball load J = 050, particle filling U = 053, mill speed N c = 71% and mill factor F c = 069 Shape and size factors equation and Physicochemical Problems of Mineral Processing 2017年2月21日 911 Metallurgist is a trusted resource for practical insights, solutions, and support in mineral processing engineering, helping industry professionals succeed with proven expertise Ore Sampling Methods: Good ProperOre Sampling Methods: Good Proper 911Metallurgist
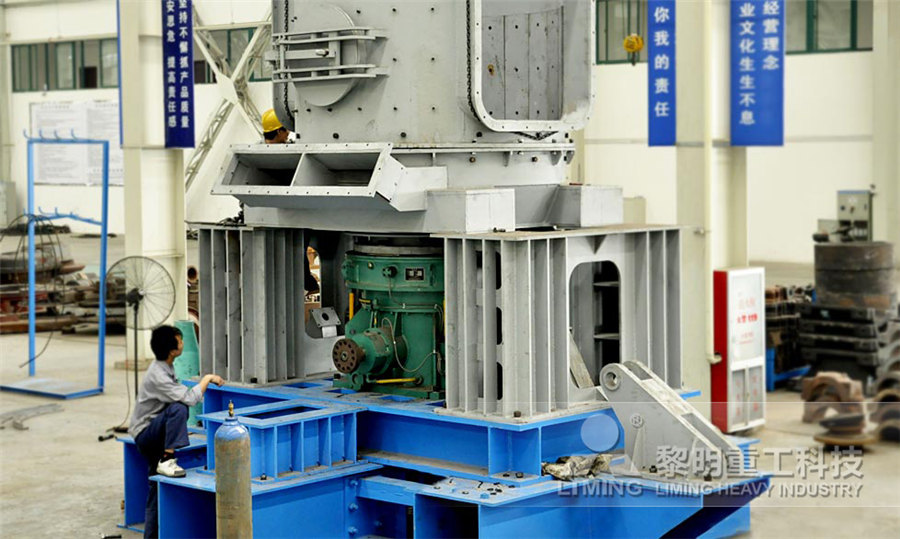
Ore mill, Ore grinding mill All industrial manufacturers
Rotational speed: 150 rpm 740 rpm Output: 200 kg/h 186,000 kg/h Motor power: 22 kW 1,250 kW of the pulp from the discharge end The overflow type ball mill is a new type of ball mill equipment with simple structure and selfflow discharge of ore It is often used to grind fine 2024年5月17日 A SAG (SemiAutogenous Grinding) mill is a giant rotating cylinder filled with grinding media and the ore being reduced As the mill rotates, the grinding media lifts and the impact crushes the feed material SAG mill control refers to the practice of managing the mill load, which is the amount of material inside the mill at any given timeA guide to SAG Mill management2020年7月2日 PDF A comprehensive investigation was conducted to delineate the effect of ball size distribution, mill speed, and grinding of ore to liberate valuable mineral particles(PDF) Effects of Ball Size Distribution and Mill Speed and Their The rod mill is another type of grinding mill used in the copper ore mining process This machine uses steel rods as the grinding media instead of balls, which are commonly used in ball mills The rods grind the ore by tumbling within the mill, similar to the action of a rotating drumUnderstanding the SAG Mill in Copper Ore Mining Process
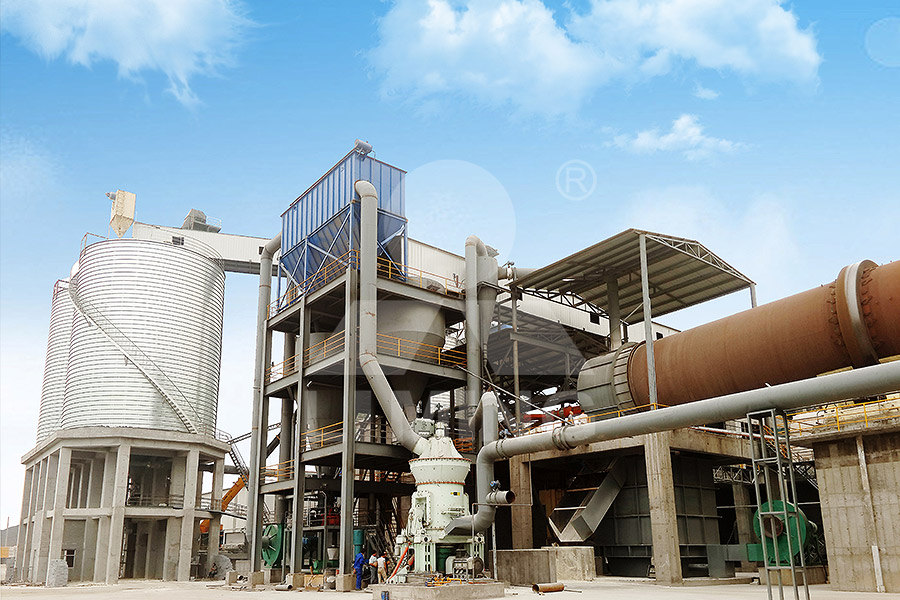
Monitoring the fill level of a ball mill using vibration sensing and
2019年10月19日 Ball mills are extensively used in the size reduction process of different ores and minerals The fill level inside a ball mill is a crucial parameter which needs to be monitored regularly for optimal operation of the ball mill In this paper, a vibration monitoringbased method is proposed and tested for estimating the fill level inside a laboratoryscale ball mill A vibration 1983年1月1日 Values of mill speed, fresh ore feedrate, The reason for this is that the mill speed almost immediately offsets the effect which the ore hardness disturbance Slow Slow Slow Fast ucyc lone feed ++ + 3 pumping rate Fast Fast Fast Fast feed water +++ addition rate Slow Slow Slow Fast u4 mill speed +Med Med Slow Slow Us Mill Speed as a Manipulated Variable for Ball Mill Grinding Controlfines, the roller mill must have the right roll surface, roll speed ratio, and roll gap for your application Roll surface Typically, the roll surface is corrugated rather than smooth to achieve efficient size reduction, as shown in Figure 3 Thousands of different corrugation configurations are available to suit your material hardnessRoller mills: Precisely reducing particle size with greater efficiencyCritical speed is defined as the point at which the centrifugal force applied to the grinding mill charge is equal to the force of gravity At critical speed, the grinding mill charge clings to the mill inner surface and does not tumble Most ball mills operate at approximately 75% critical speed, as this is determined to be the optimum speedBall Mill (Ball Mills Explained) saVRee saVRee
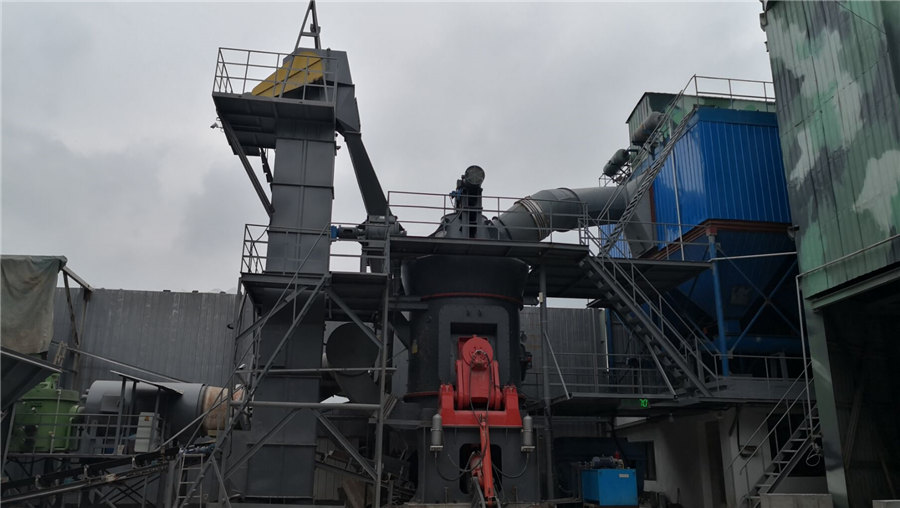
Effects of slurry filling and mill speed on the net power draw of a
Effects of slurry filling and mill speed on the net power draw of a tumbling ball mill François K Mulengaa,⇑, Michael H Moysb a Department of Electrical and Mining Engineering, University of South Africa, Florida Campus, Private Bag X6, Johannesburg 1710, South Africa bSchool of Chemical and Metallurgical Engineering, University of the Witwatersrand, Private Bag X3, Wits I mean, setting up Resonant Pulverizer+Resonant Redstone Furnace with maximum speed upgrade for every single ore seems to be a good idea But, it will drain like 25k RF/t For fast processing I use Ender IO SAG Mill and Alloy Smelter and just scale out [Infinity] Fast Ore Processing : r/feedthebeast Reddit(01 Apr 2024): Some aspects on grindability of feldspar ore using ball mill, Particulate Science and Technology , DOI: 101080/2023 To link to this article: https://doior g/10 Some Aspects on Grindability of Feldspar Ore Using increase of mill speed and optimum speed was not reached in the range of chosen mill speed fractions Again the rate of breakage was plotted as a function of particle size, the optimum size was 08 mm when milling at 30% critical speed As for 20% and 30% optimum size was not reached The selection function parameters estimated atEFFECTS OF MILL ROTATIONAL SPEED ON THE BATCH GRINDING
.jpg)
Optimisation of a SAG mill though trajectory and power milling
Mill filling is an important operational parameter in a SAG mill circuit and by its control and optimisation it can produce significant improvements in production capacity and energy efficiency However, it is industry practice to report mill load as the total output given by load cells, or kPa for systems based on lubrication bearing back pressure, rather than the actual percent total mill an estimate of the dynamic states of the mill by means of MHE and passes this information to the NMPC controller for determining optimized values for mill speed and feed The grade and hardness of the ore supplied to the mill often vary considerably In addition, equipment wear and drift will introduce uncertainty into the process managementWhite paper, September 2015 SmartMill™: Exceed your Lowspeed mills operate at around 6001200 revolutions per minute (RPM), while highspeed mills typically operate at around 3000 RPM or higher While there are definite benefits to using a highspeed ball mill over a lowspeed mill, it's important to note that not all products are best suited for highspeed millingHow does the speed of ball mill affect productivityexhibits many of these aspects Maintaining the SAG mill weight at the optimum value is critical for achieving maximum grind rate efficiency and mill production (Powell, MS, van der Westhuizen, AP, Mainza, AN 2009) However, SAG mill weight is difficult to control as the dynamic response changes as the mill approaches maximum capacitySAG Mill Optimization using Model Predictive Control Andritz
.jpg)
Grinding Mills and Their Types – IspatGuru
2015年4月9日 Typically this type of mill can deliver a product with a fineness of less than 01 mm Testing of material is needed before hand to determine the suitability of the ore for processing in an autogenous mill The rod mill (Fig 1) is a tumbling mill which is having a large percentage of its volume (30 % to 40 %) loaded with steel rods2017年5月8日 The critical speed of a mill has already been discussed and it has been shown there, by equation from the point of view of motion of charge, not independent variables For this reason the functions ∅4(d/D) and ∅7(f) Also in some cases, though rather rarely, large pieces of ore are used as a grinding mediumGrinding Mill Power 911Metallurgist2024年11月21日 The advantage of the grid type ball mill is that the ore discharge speed is fast, it can reduce the overcrushing of ore, and at the same time it can increase the output per unit volume 1 Large row of ore mouth Ball Mill Is Indispensable For Lithium Ore ProcessingThe best ore doubling method depends on what you are looking for early game The AA Crusher wins on speed but has no extra output, making it less optimal early game The EU Crusher is the cheapest but is also slow The EIO SAG Mill is by far the most efficient, especially when including grinding balls, but is also by far the most expensiveA comparison of the popular early game ore doubling, smelting,
.jpg)
Simulating the Impact of Ore Competence Variability
2019年9月24日 There are numerous examples in the literature, some of which are quantifying the effect of Mine to Mill Grundstrom et al, 2001;Hart et al, 2001;Scott et al, 2002;Burger et al, 2006;Jankovic et al 2023年10月27日 The ball mill is a rotating cylindrical vessel with grinding media inside, which is responsible for breaking the ore particles Grinding media play an important role in the comminution of mineral A Review of the Grinding Media in Ball Mills for Mineral Processing2020年7月23日 The results revealed that stirrer speed, grinding time, and feed size played crucial role on the performance of stirred mill Mathematical correlations were developed for predicting product size Optimization of stirred mill parameters for fine grinding of PGE 2023年7月10日 The present literature review explores the energyefficient ultrafine grinding of particles using stirred mills The review provides an overview of the different techniques for size reduction and the impact of energy requirements on the choice of stirred mills It also discusses the factors, including the design, operating parameters, and feed material properties, EnergyEfficient Advanced Ultrafine Grinding of Particles Using
.jpg)
Roller Mill SpringerLink
2023年7月4日 The Raymond mill is mediumspeed fine grinding equipment According to the number of rollers, it can be divided into three rollers (3R), four rollers (4R The Raymond mill is mainly used to grind coal, nonmetallic ore, glass, ceramics, cement, gypsum, pesticide, chemical fertilizer, and other materials The product particle size increase of mill speed and optimum speed was not reached in the range of chosen mill speed fractions Again the rate of breakage was plotted as a function of particle size, the optimum size was 08 mm when milling at 30% critical speed As for 20% and 30% optimum size was not reached The selection function parameters estimated atEFFECTS OF MILL ROTATIONAL SPEED ON THE BATCH GRINDING 2017年1月1日 An increase of over 10% in mill throughput was achieved by removing the ball scats from a single stage SAG mill These scats are non spherical ball fragments resulting from uneven wear of balls (PDF) Performance optimization of an industrial ball mill for 2023年10月1日 To determine the ball mill work index of the samples (Table 1), around 10 to 17 kg of ore was required for the particle size crushed to −335 mm (Amtech, 2006) The 700 cm 3 ore sample weight is fed to the Bond mill at a −335 mm size rangeEstimation methodology for Bond ball mill work index experiment
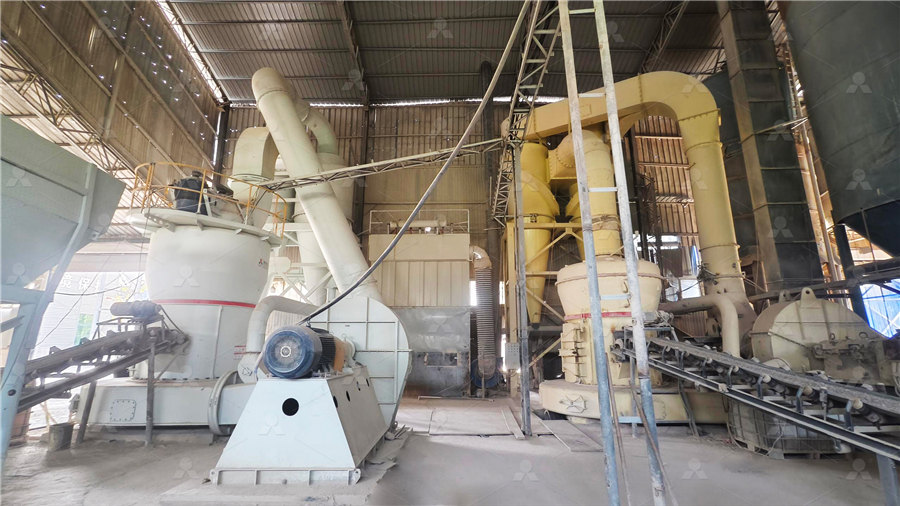
(PDF) Variability Study of Bond Work Index and
2021年6月17日 PDF It is a wellknown fact that the value of the Bond work index (wi) for a given ore varies along with the grinding size In this study, a Find, read and cite all the research you need on 2017年7月26日 Soft ore Work Index 13 = 100,000/90,000 = 11 kwh/t Hard ore Work Index 16 = 100,000/65,000 = 154 kwh/t For the purposes of this example, we will hypothesize that the the crushing index of the hard ore with the increased energy input of 154 kw/t reduces the ball mill feed size to 6,500 micrometersHow Ball Mill Ore Feed Size Affects Tonnage Capacity2016年2月1日 The purpose of this study is to understand how ore loss and dilution affect the mine call factor, with the aim of subsequently improving the quality of ore mined and fed to the millMonitoring ore loss and dilution for minetomill 2019年4月19日 At new ore locations, power system stiffness doesn’t seem to be growing as fast as large mill sizes High starting current (usually of low power factor) drawn through the utility system,ant transformers, and plant distribution networks causes voltage dipsElectric Drives for Large Ore Grinding Mills 911Metallurgist
.jpg)
Size reduction performance evaluation of HPGR/ball mill and
2022年12月15日 It can be concluded that the HPGRStirred mill combination was a more energyefficient grinding circuit than the HPGRBall mill combination for PGE bearing chromite ore2020年1月30日 The highest nickel extraction percentage of 889% was obtained from the leaching of saprolite ore at 95°C, stirring speed of 400 rpm, particle size distribution of80+100 mesh, solid to liquid Effect of Agitation Speed and Leaching Time for Nickel Recovery Figure 3: Effect of Feed Size on Autogenous Mill Tonnage A similar graph for the variablespeed semiautogenous mill is shown in Figure 4 below, where differences in mill tonnage from 1200 tph to over 2000 tph within a 24 hour period are accounted for by feed size changes 0 10 20 30 40 50 60 Weight % in Fraction 0 400 800 1200 1600 2000 2400 The Importance of Primary Crushing in Mill Feed Size OptimizationOne reason is the dry inbed grinding principle Results of extensive test works with two types of magnetite iron ores in a Loesche VRM are presented here Within these test works, mill parameters like grinding pressure, separator speed and dam ring height were varied, following a factorial design of the experimentsResearch of iron ore grinding in a verticalrollermill
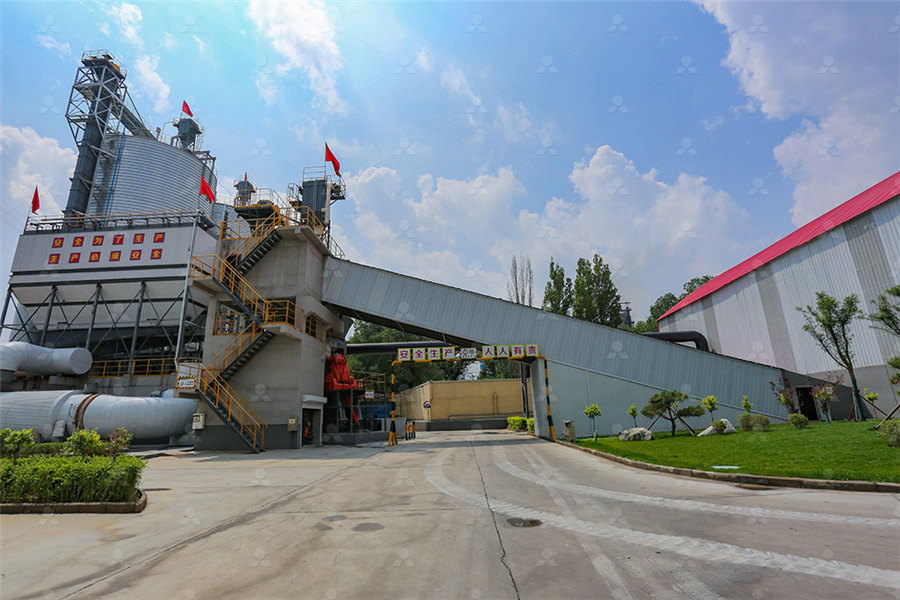
Effect of mechanochemical activation parameters on vanadium
2024年9月15日 The particle size reduced effectively with an increase in surface area without a notable agglomeration at rotational speed 140 rpm as depicted in Fig 9 d similar to work done by Ref [13], on the effect of planetary ball milling speed on the powder formed at varying speed of 100 rpm, 200 rpm and 300 rpm on the microstructure and lattice destruction, they found out 2021年1月11日 inside the mill such as increased load, liner shape, mill speed or friction, that causes the cascading ore and steel (in this case 10% steel was used) to hit the shell more than 30o before the vertical diameter will cause reduced Choosing a SAG Mill to Achieve Design Performance