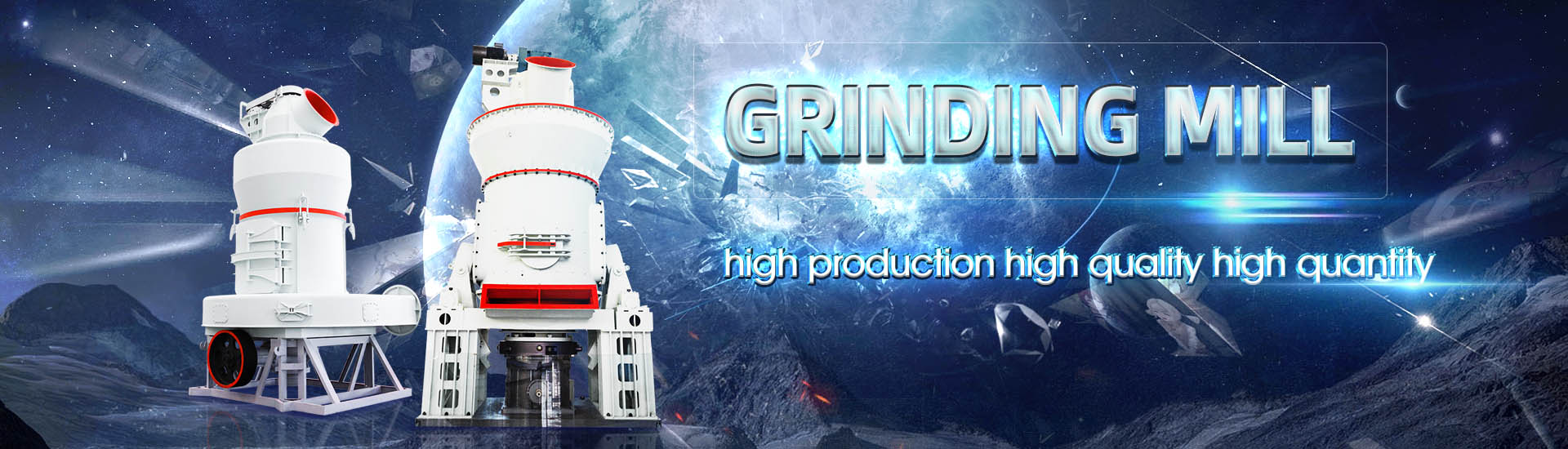
Ball mill agglomeration
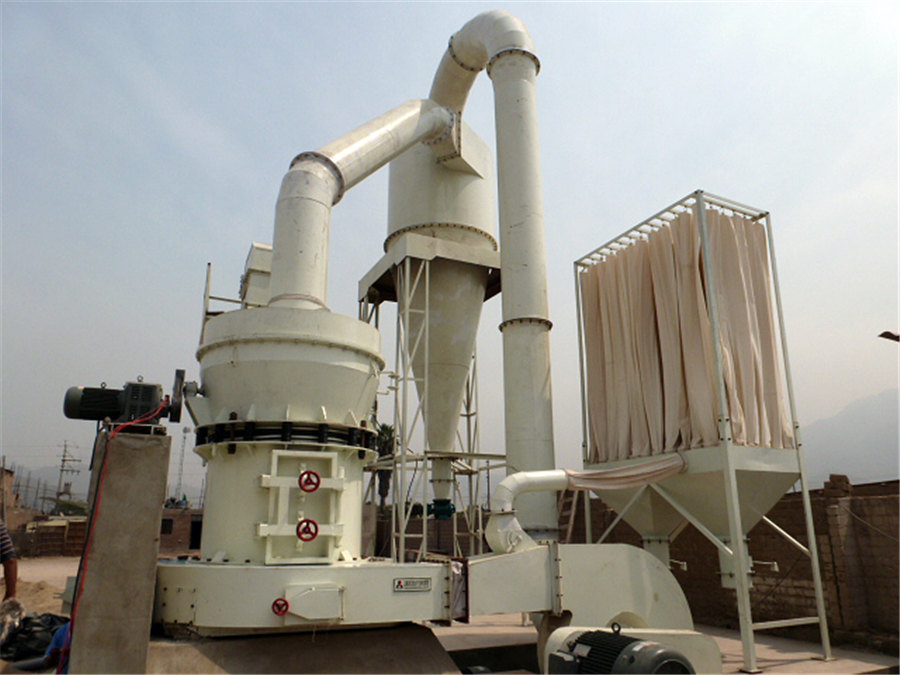
Evaluation of particle size reduction and agglomeration in dry
2020年5月15日 This study investigates particle size reduction and interparticle agglomeration in clear and milky quartz ground in a planetary ball mill for up to 32 h Particle size distribution 2009年9月15日 A Population Balance approach is used to model breakage and agglomeration phenomena during grinding of fine powders in ball milling devices A suitable fitting procedure Modelling breakage and reagglomeration during fine dry grinding 2003年2月19日 The complex behavior of LaH2 during ball milling was investigated in this study, with its mechanical, chemical, and morphological changes explored The relationship between On agglomeration phenomena in ball mills Semantic Scholar2021年10月21日 This work has investigated the effect of variation of the millball parameters on the particle sizes in mechanical activationassisted leaching and proved the limitation of the Effect of Ball Mill Parameters’ Variation on the Particles of a
.jpg)
On agglomeration phenomena in ball mills: Application to the
2003年2月1日 Composites of poly (vinyl acetate) filled with calcium carbonate (CaCO3) have been synthesized in a ball mill The different steps in fragmentation and agglomeration The low energy ball milling process was effective in synthesizingporous and agglomerated Alpowders consisting of 60 120nm sized spherical nanoparticles on average A lower milling Synthesis and Characterization of Agglomerated Coarse Al 2024年5月23日 Ball milling has emerged as a versatile and effective technique to synthesize and modify nanostructured Mgbased hydrides with enhanced hydrogen storage properties This review provides a comprehensive summary Ball Milling Innovations Advance MgBased Hydrogen 2020年3月17日 The objective of this study was to investigate the soft agglomerates behaviour of Mo powder and orthogonal tests were carried out to evaluate the dispersion of agglomerated Study of the Agglomeration Behaviour of SurfaceModified
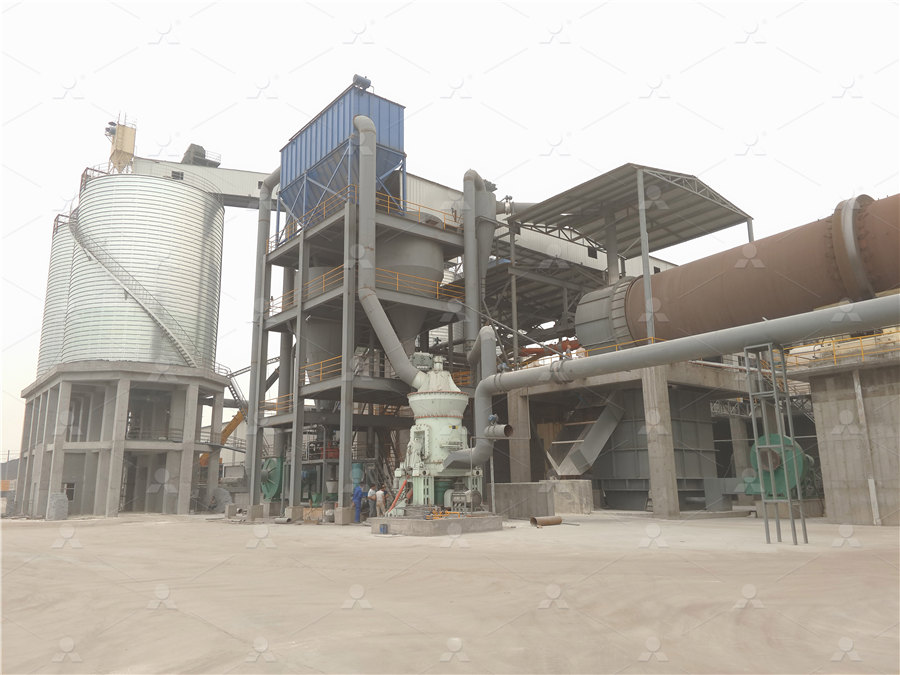
EVERY COMPONENT OF BALL MILL DETAILED
Fine Grinding and Mill Cooling PROBLEM Insufficient mill cooling lead to material agglomeration on balls and liners The grinding is not any more done by balls against material but by material against material SOLUTION Adapted 2020年4月1日 This study investigates particle size reduction and interparticle agglomeration in clear and milky quartz ground in a planetary ball mill for up to 32 hEvaluation of particle size reduction and agglomeration in dry 2020年1月15日 Mechanical milling is a promising route for production of submicron and nano sized silicon powders, but it is challenging to predict and control the product properties In this study a metallurgical grade silicon quality was milled in a planetary ball mill and the properties of the powder were investigated as a function of grinding time, grinding bead size (20 mm, 2 mm, Silicon Powder Properties Produced in a Planetary Ball Mill as a Ball mills are used often in scientific work to reduce the particle size, eliminate agglomeration, change the shape of particles, provide for mechanical alloying, mixing, A planetary ball mill consists of at least one grinding jar which is arranged eccentrically on a socalled sun wheelBall mill Wikipedia
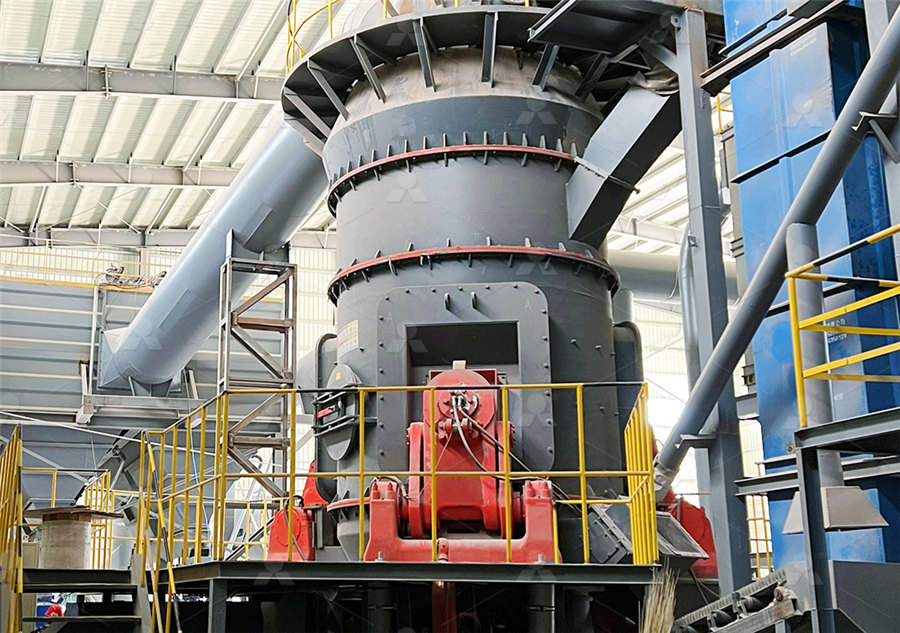
Recent Developments on the Synthesis of Nanocomposite
2022年9月16日 This review is focused on the topical developments in the synthesis of nanocomposites using the simplest topdown approach, mechanochemical milling, and the related aspects of the interfacial interactions Milling constraints include time duration of milling, ball size, the balltosample content proportion, rotation speed, and energy that took part in a vital part I've been conducting ball mill operation to reduce the size of NanoTitania (TiO2) particles Machine used: FRITSCH Planetary Ball Mill PULVERISETTE 7 with Sintered Corundum Cups and Corundum ballsHow can I reduce agglomeration of particles due to ball mill 2023年5月15日 During ball milling, solids constantly undergo stress, aggregation, and agglomeration, which allows the material to interact and experience various chemical reactions under mechanical forces [15]In a highenergy mill, the material to be milled is placed in a hollow cylindrical container and a milling medium, ie, balls generally made of stainless steel, Ballmilling: A sustainable and green approach for starch of the ball mill would be of great interest Accordingly, the aim of this paper is to identify which dimensionless numbers must be kept constant in order to reproduce the results obtained in a laboratory ball mill at the industrial scale Such scaling criteria are provided by an exhaustive dimensional analysis applied to the ball millInvestigating grinding mechanisms and scaling criteria in a ball mill
.jpg)
Ball milling as a mechanochemical technology for fabrication of
2020年9月1日 The tumbler ball mill contains a cylinder with milling balls in which an axial rotation causes these balls to roll down and impact against the powder (Fig 2 b) Conditioning of biochar at low temperatures before ball milling would minimize such agglomeration of biochar nanoparticles, 2019年2月15日 Then the ball mill and the air classifier were modelled by using perfect mixing approach and Whiten’s equation respectively –NH2, –OH, –SO3–) prevent the agglomeration by causing the propensity to adsorb on electrostatic surfaces formed by the breakage of the covalent bonds of AlO, SiO, and CaO [10] Klimpel and Effects of grinding aids on model parameters of a cement ball mill The initial powders were ground via a highenergy planetary ball mill with a balltopowder weight ratio of 3:1 for 1 h The rotating speed was kept at 200 rpm The stainless steel vial with the capacity of 1 L and the stainless steel balls (10 mm Effects of ball milling on powder particle boundaries Grinding Aid Effectiveness in Cement Ball Mill Web: bulawali : bulawali@gmail, ali@bulawali LinkedIn: Ali Bulawali The introduction of the grinding aid (GA) has been started more than 50 year ago, to facilitate `Grinding Aid Effectiveness in Cement Ball Mill
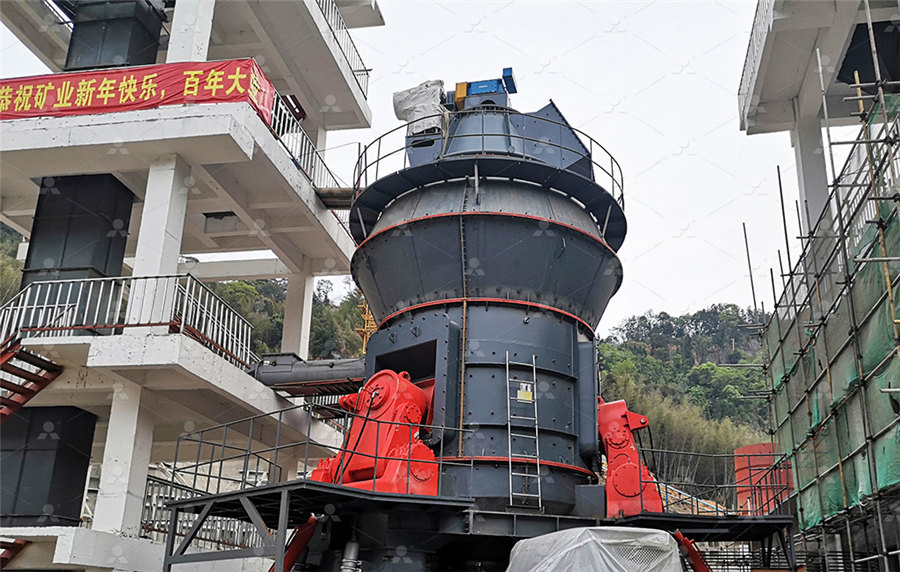
Modelling breakage and agglomeration during fine dry grinding in ball
2009年9月1日 Modelling of grinding of fine powders in ball milling devices is addressed The model quantitatively describes breakage and agglomeration phenomena by considering two populations, ie primary Process Training Ball Mill To improve the grinding and separating capacity (avoidance of capacity losses by preventing agglomeration) grinding aids are used, especially when producing cements of higher fineness (> 3500 cm 2 /g)Process Training Ball Mill INFINITY FOR CEMENT EQUIPMENT2020年7月2日 A comprehensive investigation was conducted to delineate the effect of ball size distribution, mill speed, and their interactions on power draw, charge motion, and balls segregation in a (PDF) Effects of Ball Size Distribution and Mill Speed and Their 2023年1月12日 In this study, silica nanoparticles (SiO2 NPs) were fabricated using a handmade ball mill as a novel, simple, rapid, costeffective, and green approach The sol–gel method was also used to produce these NPs as a comparative method The SiO2 NPs produced by both methods were characterized using highresolution transmission electron microscopy Facile, fast, and green preparation of highpurity and quality silica

Silicon Powder Properties Produced in a Planetary Ball Mill as a
2020年10月1日 The current study investigates the type of ratio for ball mill jars listed in Table 3 and [63,80,168,181,183] Different balltojar ratios can affect the milling kinetics, the size, and 2018年7月4日 Yttriareinforced copper matrix composites were prepared by dry ball milling (DBM) and wet ball milling (WBM), respectively, followed by spark plasma sintering (SPS) It is to determine which milling process is better for fabricating Cu–Y2O3 composites It is found that Cu–Y2O3 composites synthesized by DBM exhibit better densification, mechanical and Dry ball milling and wet ball milling for fabricating copper–yttria 2012年6月1日 way (normalized breakage) and that no agglomeration processes take place during A ball mill is a type of grinder widely utilized in the process of mechanochemical catalytic degradationGrinding in Ball Mills: Modeling and Process ControlFor any closed circuit ball mill system there is an optimum circulating load for maximum output and minimum kWh/t Increasing circulating load is desirable as a means to reduce the inmill fineness and thus reduce negative influences of fine particle agglomeration However, the increase in total mill throughput has negative consequences of Mike Sumner and Keith Marsay, Grace, examine ball mill
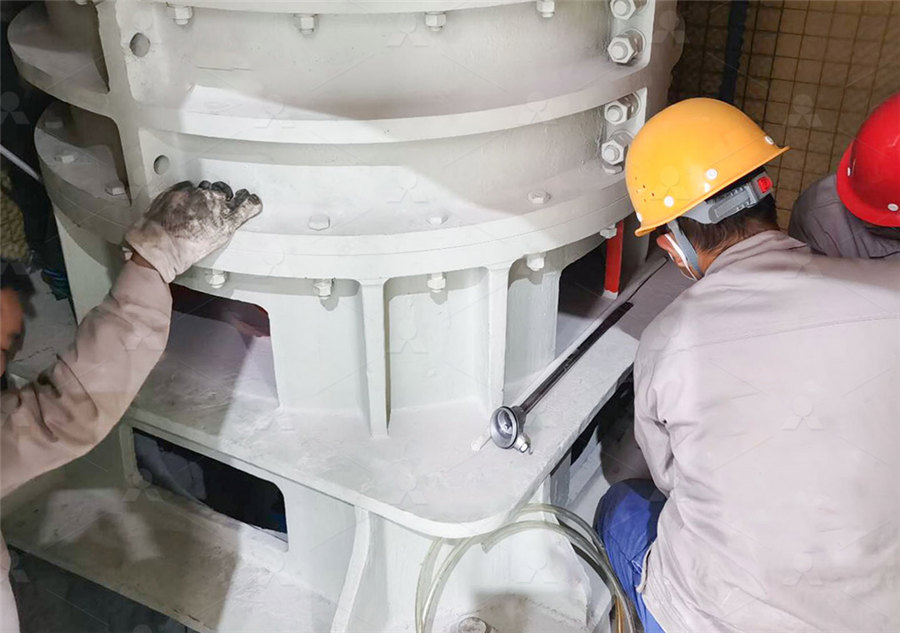
Simulation of the breakage of bonded agglomerates in a ball mill
2013年3月1日 Numerically investigated agglomerate breakage in batch ball mill Parametric investigation of milling behavior Range from little breakage to complete breakage with variation in bond strength Duplicate experimental trends with rotation rate and grinding media diameter Breakage occurs near the mill shell, a key result for more efficient mill designIn this module, the readers will learn the working principle and applications of Ballmill technique in nanomaterials synthesis The basic principle of a ball mill is drawbacks of ballmilling include long processing times, no control over particle morphology, possibilities of particle agglomeration, residual strain in the crystallized Ballmilling – Nanoscience and Nanotechnology I INFLIBNET DOI: 101016/JPOWTEC201506050 Corpus ID: ; The onset of particle agglomeration during the dry ultrafine grinding of limestone in a planetary ball mill @article{Guzzo2015TheOO, title={The onset of particle agglomeration during the dry ultrafine grinding of limestone in a planetary ball mill}, author={Pedro L Guzzo and Alan AA Tino and J{\'u}lia Borges dos The onset of particle agglomeration during the dry ultrafine Adaptable Ball Mill Design Super Orion (Classic version) up to 1400 kW Super Orion Compact Line (SOCL) up to 355 kW Wear protection and contamination Steel linings and balls Ceramic linings and ballsAlpine SO Super Orion Ball Mill Hosokawa Micron Powder Systems
.jpg)
Dry grinding in planetary ball mills: Evaluation of a ResearchGate
2017年11月1日 Planetary ball mills at laboratory scale are widely used for grinding and alloying processes However, in contrast to other mill types, no applicable mechanistic model exists to describe the 2015年11月1日 The size distribution of limestone particles ground in a planetary ball mill with different grinding times and revolution speeds together with particle morphology analysis carried out by electron microscopy showed that the onset of the agglomeration process took place when the specific surface area of ultrafine particles reached a value of approximately 4000 cm 2 /gThe onset of particle agglomeration during the dry ultrafine 2024年1月28日 2 Liners: An abrasionresistant material such as manganese steel or rubber typically lines the inner surface of the cylindrical shell to protect it from wear due to the grinding action 3 Balls: They place steel or ceramic balls, typically used as grinding media in a ball mill, inside the shell and rotate them with it 4 Feed and Discharge: Entering the hollow shell at the Ball mill: Principles, construction, working, uses, merits, and 2020年12月1日 Request PDF Fabrication of homogeneous nanosized nickel powders using a planetary ball mill: Applications to multilayer ceramic capacitors (MLCCs) Given the increasing demand for multilayer Fabrication of homogeneous nanosized nickel powders using a
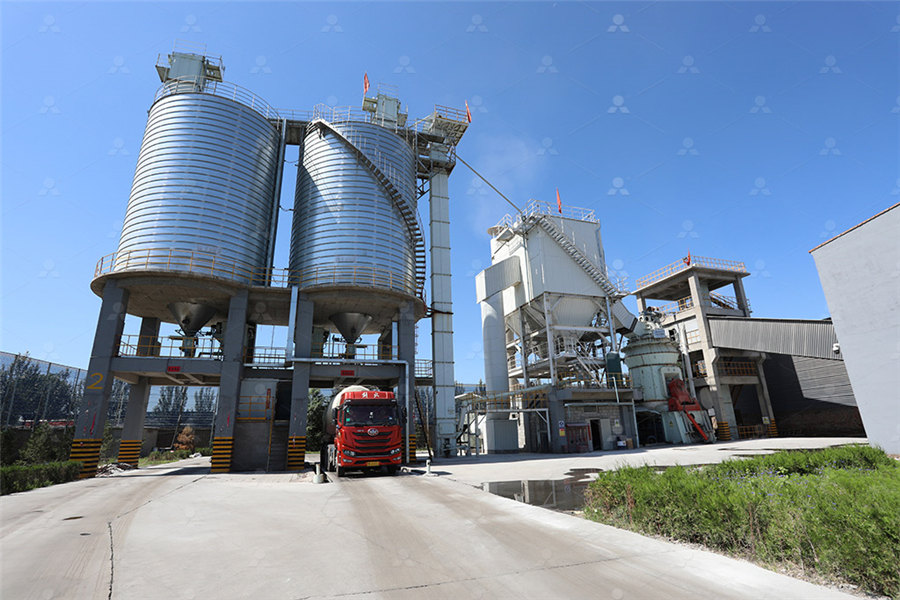
HighEnergy Ball Milling Parameters in Production of
2017年8月24日 In Spex ball mill, the maximum temperature was 200 °C It was Agglomeration of the powder was reported to increase with increase in milling speed and more PCA (ethanol) was required to prevent agglomeration Let’s consider a mass of material M in a ball mill that after breakage needs to be divided, by using x i screens, into i + 1 narrow size classes Normally, for a size class i bounded between two successive screens x i and x i +1 containing a mass fraction m i (t) at time t, it is assumed that breakage follows a firstorder lawThat is, the rate of breakage of size i is proportional to the Identification of Optimal Mill Operating Parameters during 2024年6月7日 Ball milling, as a costeffective and ecofriendly approach, has been popular in materials synthesis to solve problems involving toxic reagents, high temperatures, or high pressure, which has the potential for largescale Recent Advances in BallMilled Materials and Their 2022年12月1日 Results of studying preparation of activated finely dispersed alphaalumina by dry milling in a ball mill are presented The αAl2O3 refinement mechanism is considered It is shown that the powder material obtained has Research in the Area of Preparing Activated Alumina

Homogeneous nanoparticle dispersion prepared with impurity
2013年8月1日 Homogeneous nanoparticle dispersion prepared with impurityfree dispersant by the ball mill technique Author links open overlay panel Lingyun Zhou a b, Hui Zhang a, Hui Zhang a, Zhong Zhang various dispersants must be added to prevent the agglomeration and precipitation of nanoparticles as a result of electrostatic, steric, and 2022年9月19日 Further prolonging the milling duration led to agglomeration, which increased the size of the biochar nanoparticles The thermogravimetric analysis The biochar powder was then ground into NBC in a ball mill using a SPEX 8000D (Metuchen, NJ, USA) highenergy ball mill with two 65 mL vials This process was conducted at ambient HighEnergy Ball Milling for High Productivity of Nanobiochar2023年1月20日 Nevertheless, there is almost no intensive review of the studies in ball millingactivated ZVI composites For instance, Sitotaw et al mainly introduced the research progress of ball milling technology for the efficient production of bioethanol from lignocellulosic biomass (Sitotaw et al, 2021)Visentin et al reviewed the main synthesis methods and production New insights into ballmilled zerovalent iron composites for Compaction / Granulation / Agglomeration; Industries Chemical; Cosmetics; Food; Mineral; Pharmaceutical; Plastics; Battery Materials; Services Aftermarket OEM Quality Parts; Service Maintenance; Alpine® SO Ball Mill brochure brochure: Alpine® Spiral Jet Mill 50 AS Demo video Demo video: Hosokawa Alpine AFG Fluidied Bed Jet MillHosokawa Alpine Ball Mill and Classifier
.jpg)
The onset of particle agglomeration during the dry ultrafine
2015年6月20日 This study investigates structural and morphological changes in limestone particles ground in a planetary ball mill The grinding tests were carried out as a function of the revolution speed (100 Previous Post Next Post Contents1 Ball charge optimization2 1 How to use the BP21 2 Description of the main indicators used in this BP2101 The residue on 2mm/4mm before partition wall2102 Material filling level and ball charge expansion211 Cement mill specific power 1st compartment 212 Raw mill specific power 1st compartment Ball charge Ball charge optimization INFINITY FOR CEMENT EQUIPMENT2011年7月1日 Request PDF Ballmill grinding kinetics of master alloys for steel powder metallurgy applications Agglomeration of fine particles can be overcome with the use of a process control agentBallmill grinding kinetics of master alloys for steel powder 2023年11月28日 The highenergy ball mill processing can be divided in three main groups according to the mechanisms involved and/or the purpose envisaged: Mechanophysical conditioning, Mechanochemical synthesis and mix processes In the first group, dissimilar or similar materials can be processedMaterials Processing Using HighEnergy Ball Milling Across