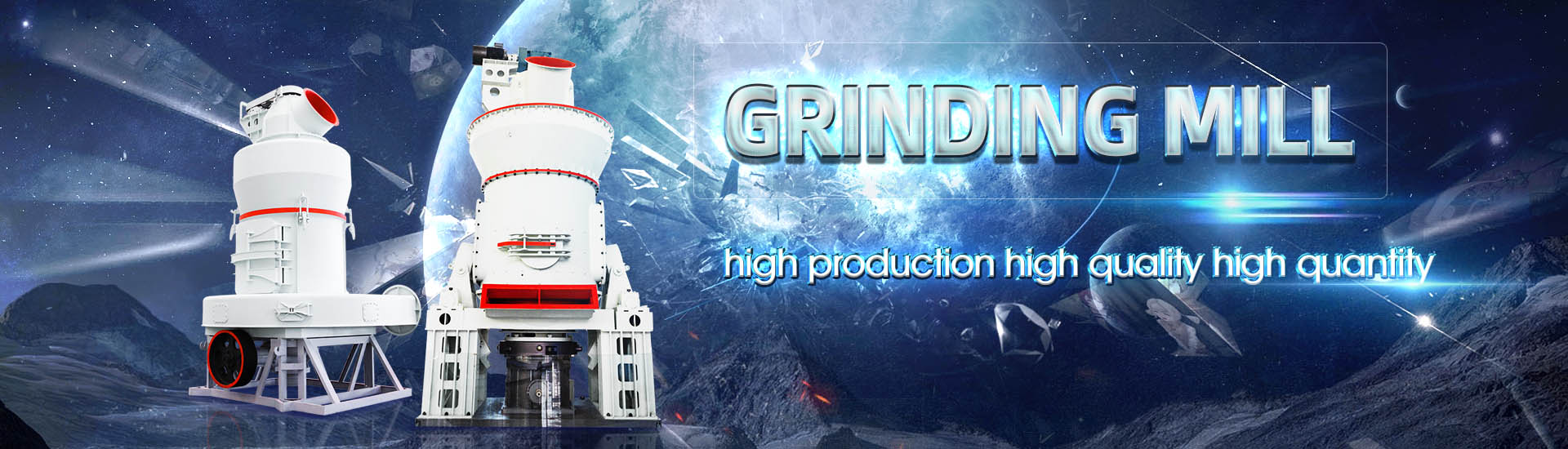
Feeding particle size 400mm ore grinding machine
.jpg)
Fine Grinders, Hammer Mills, and More for Particle Size
The “M” Series fine grinders are designed to grind dry, freeflowing material down to 400 mesh with extremely tight particle size distribution This highly efficient machine ensures easy access to all internal areas and is perfect for heat Common feeding devices include rotary feeders (for granular feed with an average particle size from 1⁄4 to 3⁄4 inch) and vibratory feeders (for powder feed with an average size up to about Roller mills: Precisely reducing particle size with greater efficiency2018年2月7日 A pendulum feeder/ plunger ore feeder is a mining auxiliary equipment of mineral transport machinery It is suitable for shortmoment Plunger Ore Feeder Pendulum Feeder JXSC Machine2023年11月13日 Choosing the right feeder depends on the material characteristics, feed size, required feed rate, and specific application needs Proper selection and maintenance of feeders can enhance the efficiency and How to Select the Best Feeder for Your Ore Processing
.jpg)
HighPressure Grinding Roller Presses for Minerals Processing
In order to achieve proper interparticle comminution, all feed particles should be smaller than the operating gap between the rollers This also ensures low wear The maximum feed size to be 2023年7月10日 Compression, impact, shear, and attrition are the four mechanisms that contribute to reductions in particle size The type of grinding machine required depends on parameters such as the feed size (F 80), EnergyEfficient Advanced Ultrafine Grinding of The Prater FullScreen Hammermill utilizes a specially shaped grinding chamber designed with distinct grindandrelease zones Coarse raw product is fed into the chamber, using a rotary Hammermills Particle Size Reduction Equipment Prater IndustriesEnduron® high pressure grinding rolls (HPGR) can handle a wide variety of ores and particle sizes from fine pellet feed all the way up to coarse grinding of 75mm magnetite iron ore When Our Dynamic HPGR Technology for Mineral Grinding Weir
.jpg)
Research on Grinding Characteristics and Comparison
2022年10月26日 The particle size composition of grinding products will significantly affect the technical and economic indexes of subsequent separation operations The polymetallic complex ores from Tongkeng and Gaofeng are 2023年8月30日 Mineral particle size is an important parameter in the mineral beneficiation process In industrial processes, the grinding process produces pulp with qualified particle size for subsequent Hierarchical Intelligent Control Method for Mineral 2021年11月8日 Illite ore industrial grinding mill machine can grind illite into powder up to 3000 mesh In addition, because of its small particle size, large specific surface area, and unique Zeng bond structure, illite powder can be Illite Ore Industrial Grinding Mill Machine SBM 2023年10月17日 3 Ultrafine Powder Grinding Mill Ultrafine powder mill (threering / fourring mediumspeed micropowder mill) feed particle size ≤25 mm, production capacity 0545 t/h, production fineness 1503500 mesh,it is a highefficiency and lowconsumption ultrafine powder processing equipment that successfully replaces the traditional jet mill and complex process How to choose a suitable ore powder grinding mill?
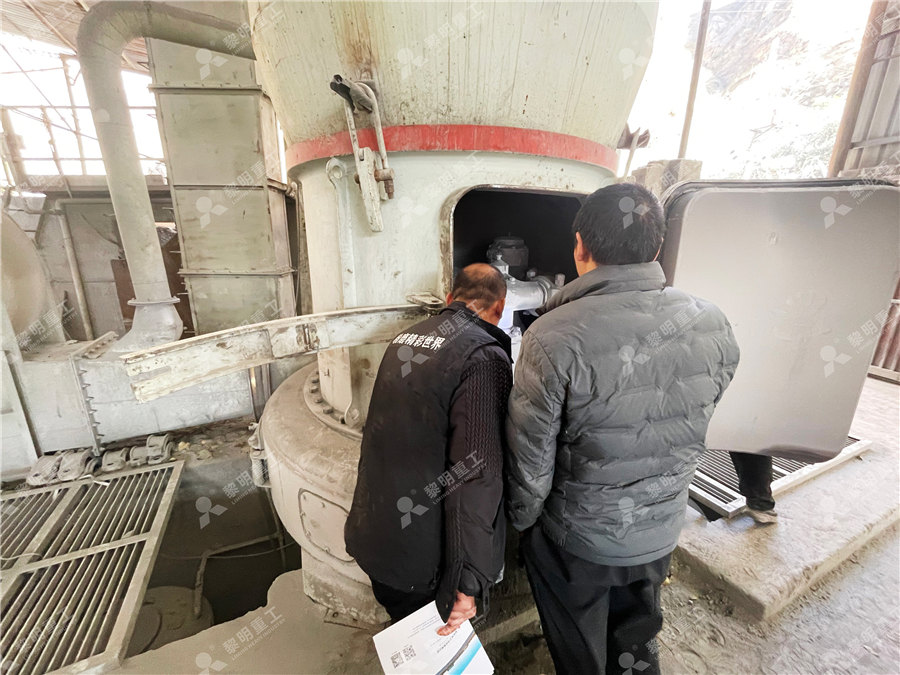
Investigation on Iron Ore Grinding based on Particle Size Distribution
2020年5月28日 The feed samples of X, Y, and Z iron ores were ground in the BBM (ball mill refers to a BBM of size 300 mm × 300 mm with smooth liners) to identify the PSD, BWI, and RT of each ore Grinding experiments were conducted according to Bond’s standard test procedure []For each iron ore sample, the RT taken to produce 250% circulating load in the BBM was 2024年4月19日 Atrition crushing is great for the production of very fine particle sizes and it is commonly used in mineral processing and mining for grinding ore Shear Crushing : Shear crushing takes a shearing force and applies it to the material, which results in the formation of cracks on the weak planesTypes of Crushers Explained: Everything You Need to Know JXSC2020年9月22日 Grinding machine has been widely used in gold mines in South Africa since 1905 At that time, the grinding machine used river pebble as the grinding medium, which was essentially a gravel mill Later, in order to improve the production capacity of the mill, cast iron balls were used as the medium, so normal gravel mills were evolved into ball mills and rod millsGrinding Machines: Types and Selection Principles Mining Download scientific diagram Particle size distributions for feed and product materials for feed sizes 0/300 mm, 100/300 mm and 100/400 mm Feed material distributions drawn in solid lines Particle size distributions for feed and product materials for feed
.jpg)
Grinding SpringerLink
2022年2月28日 An investigation conducted on magnetite ore grinding with a dry HPGR machine to reduce the particle size from 50 mm to 90 µm has revealed that using two stages HPGR closed circuit with an air classifier can reduce energy consumption by 46% compared to a circuit in which there is a tertiary crushing with a wet ball millparticle size fraction shall be fully mixed into 500 g/bag for subsequent grinding test Table 3 Particle size distribution of two types of ores sample Particle Size/mm Tongkeng Ore Gaofeng Ore Optimization of Polymetallic Complex Ores ResearchGateKeywords Particle size distribution (PSD) Retention time Comminution Characterization studies 1 Introduction Ball mills are progressively used to grind the ores for particle size reduction and to liberate valuable minerals from the ores The (PDF) Estimation of Grinding Time for Desired Particle Size 2019年2月25日 You are accessing a machinereadable page In −023 + 0075 mm was chosen as the requirement grade for cassiterite in cassiteritepolymetallic sulfide ore, ie, the grinding particle size a of cassiterite was 023 Grinding Optimization of CassiteritePolymetallic
.jpg)
SIZE REDUCTION BY GRINDING METHODS By ResearchGate
5 Ball mills are used for wet grinding iron ore, gold/copper ore, nickel ore and other ores, as well as lime/limestone for flue gas desulphurisation systems, coal and other raw materials2020年10月20日 One of the feed ore properties which can affect the grinding charge of an AG mill is particle size distribution Bergstedt and Fagremo (1977) studied the effect of feed size distribution on the performance of an AG during a series of pilot plant tests They reported that the ideal feed ore to an AG mill should have 10–15 wt% materials coarser than 100 mm Bouajila The performance improvement of a fullscale autogenous mill by setting 2023年8月30日 Mineral particle size is an important parameter in the mineral beneficiation process In industrial processes, the grinding process produces pulp with qualified particle size for subsequent flotation processes In this paper, a hierarchical intelligent control method for mineral particle size based on machine learning is proposed In the machine learning layer, artificial Hierarchical Intelligent Control Method for Mineral Particle Size 2023年7月10日 principal grinding methods used in mineral ore processing, reducing the particle size from 500 mm to sub15 µ m through ultrafine grinding [ 23 ] Energies 2023 , 16 , x FO R P EER RE VIEW 5 of 41(PDF) EnergyEfficient Advanced Ultrafine Grinding of Particles
.jpg)
Research on Grinding Law and Grinding Parameters Optimization
2022年10月13日 Grinding plays an important role in mining, construction, metallurgy, chemical, coal and other basic industries In terms of beneficiation, grinding is the most energy consuming operation So, reasonable grinding conditions according to the properties of ores is the key to obtain good grinding results and reduce energy consumption and resource waste In this 2022年7月10日 A Hybrid PBMDEM Model of HighPressure Grinding Rolls Applied to Iron Ore Pellet Feed Pressing sizes fed to the machine Particle size distributions from samples of the feed and (PDF) A Hybrid PBMDEM Model of HighPressure GrindingOre Grinding Wu Caibin1 and Xu Kuangdi2 1School of Resources and Environmental Engineering, Jiangxi University of Science and Technology, Ganzhou, China 2Chinese Academy of Engineering, Beijing, China Ore grinding is a process to further reduce and disperse the ore particle size In the mineral processing industry, ore grinding is the particle Ore Grinding Methods and Process of Ore GrindingThe purpose of the primary crusher is to reduce the ROM ore to a size amenable for feeding the secondary crusher or the SAG mill grinding circuit The dimensions defined by those particle sizes are: Gape: The distance between the jaws at the feed opening; Closed side set K = machine characteristic constant: L min = closed side setting AMIT 135: Lesson 5 Crushing – Mining Mill Operator Training
.jpg)
CLUM Ultrafine Vertical Grinding Mill
CLUM series of ultrafine gypsum powder vertical grinding mills are a new type of ultrafine industrial ore grinding equipment that integrates grinding, grading, powder collection and conveying +年1月1日 (2) Various working parameters of grinding mill, including fraction of critical speed for grinding mill, filling rate for grinding mill, grinding concentration, grinding cycle load, etc (3) And grinding material properties, including ore grindability, feeding particle size, etc Huge energy and steel consumption in ore grinding process greatly affect the subsequent separation Ore Grinding SpringerLink2021年6月23日 The grinding product particle size is the most crucial operational index of mineral grinding processes The size and consistency of the product directly affects the subsequent dressing and sintering(PDF) OptimalSetting for Ore and Water Feeding in Grinding 2024年6月11日 In this study, the evolution behavior of the particle size distribution during the grinding process was examined with fractal theory According to the distribution index k of the Rosin–Rammler–Benne model, the relationship between the fractal dimension D of the fractal theory and the distribution index k is discussed The fractal dimension D was used to evaluate Effect of Solid Concentration on Particle Size Distribution and
.jpg)
Grinding and grading equipment in beneficiation JXSC Mining
2021年8月13日 In over 20 years of grinding equipment design and manufacturing, our jxsc has adopts advanced controllable feeding and discharging technology, combined with the actual grinding material, should be equipped with a suitable grinding body, and the traditional surface contact is changed to line contact, so that the discharge particle size is more uniform and the 2019年10月8日 1 Crushing and grinding improvement The ore size reduction process involves two steps: crushing and grinding The grinding process is the final operation of making the mineral to dissociate from the monomer and making the particle size meet the selection requirements Grinding is a highefficiency and lowefficiency operationCrushing and Grinding Process JXSC Machineparticle size with reduced specific energy consumption [12, 13] Unlike tumbling mills, which require steel balls as grinding media to act as an energy transfer medium, in HPGR the direct transfer of energy from the rolls to the particle bed leads to interparticle breakage [14, 15] The past research works by various researchers havePotential of HighPressure Grinding Roll (HPGR) for Size 2020年5月28日 In the iron and steel industry, the production of narrow particle size distribution (PSD) for pellet feed making with acceptable liberation of valuables from the iron ore is very difficultInvestigation on Iron Ore Grinding based on Particle Size Distribution
.jpg)
What Factors Will Influence Ball Mill Grinding Efficiency?
2021年3月26日 Ball mill grinding efficiency is influenced by many factors: ore grindability, feed size, grinding product size, ball mill diameter and length, ball mill working speed, liner type, steel ball loading system, grinding concentration, return sand ratio in closedcircuit grinding and feed rate (Ball mill) To improve the ball mill grinding efficiency, you must first understand the 2013年8月3日 In Grinding, selecting (calculate) the correct or optimum ball size that allows for the best and optimum/ideal or target grind size to be achieved by your ball mill is an important thing for a Mineral Processing Engineer AKA Calculate and Select Ball Mill Ball Size for Optimum Ball mills are progressively used to grind the ores for particle size reduction and to liberate valuable minerals from the ores The grinding of ore is a highly energyintensive process [1–4] In this process, the size of the particle obtained depends on the energy consumption of the ball mill The major challenge encountered in theEstimation of Grinding Time for Desired Particle Size DistributionAs reliable feeding machine suppliers, JXSC’s feeders strictly control the amount of feeding and calcium carbide, quartz stone, dolomite, iron ore, concrete, coal, gypsum, etc more Belt Conveyor Capacity: 01284 TPH Processing Material: Bulk and and its feeding particle size is below 35100 mm It is not suitable Feeding Machines Manufacturer JXSC
.jpg)
Ore, Rock Aggregate Screening (Complete Guide)
2016年6月20日 SEPARATION SIZE/ SPLIT SIZE Particle size at which feed separates into two products (coarse fraction and fine fraction) OVERSIZE Material larger than the hole size UNDERSIZE Material smaller than the hole size HALF SIZE Material smaller than half of the hole size SCREENING CAPACITY (Q) Amount of material passing through the screen deck in 2017年3月20日 An effect of a grinding method, that is ball mill and high pressure grinding rolls (HPGR), on the particle size, specific surface area and particle shape of an iron ore concentrate was studiedPhysicochemical Problems of Mineral Processing Investigation 2024年9月15日 In mineral processing, traditional methods for determining the grinding characteristics of ores, such as singlesizefraction grinding tests, are timeconsuming and costly This study investigated an efficient alternative that uses an artificial neural network (ANN) to predict the particle size distributions (PSDs) of breakage productsPrediction of particle size distribution of grinding products using 2020年3月20日 Stone Crusher Machine Mobile Crusher Ore Flotation Grinding Machine Cement Plant Dry Machine Briquette Machine Production Lines; Feeding size: ≤25mm: ≤50mm: 300400mm: Capacity : 062—180t/h: 065—615t/h: 15338t/h: Discharging size: The SAG mill has a wide range of feeding particle sizes and can process larger What’s the Difference Between Ball Mill, Rod Mill and SAG Mill?
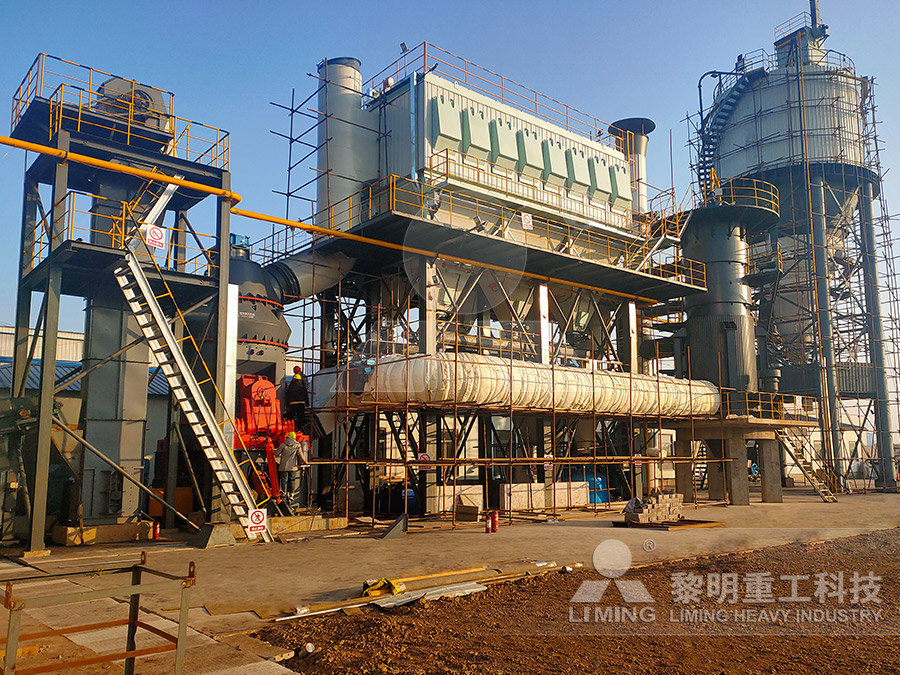
Research on Grinding Characteristics and Comparison of ParticleSize
2022年10月26日 The particle size composition of grinding products will significantly affect the technical and economic indexes of subsequent separation operationsOre Grinding Processing Plant Gold Milling Machine Working Principle The transmission device drives cylinder to rotate Materials and water are fed from the feeding end of cylinder and materials are grinded by impact and grinding of steel balls and ores into fine particlesOre Grinding Processing Plant Gold Milling Machine