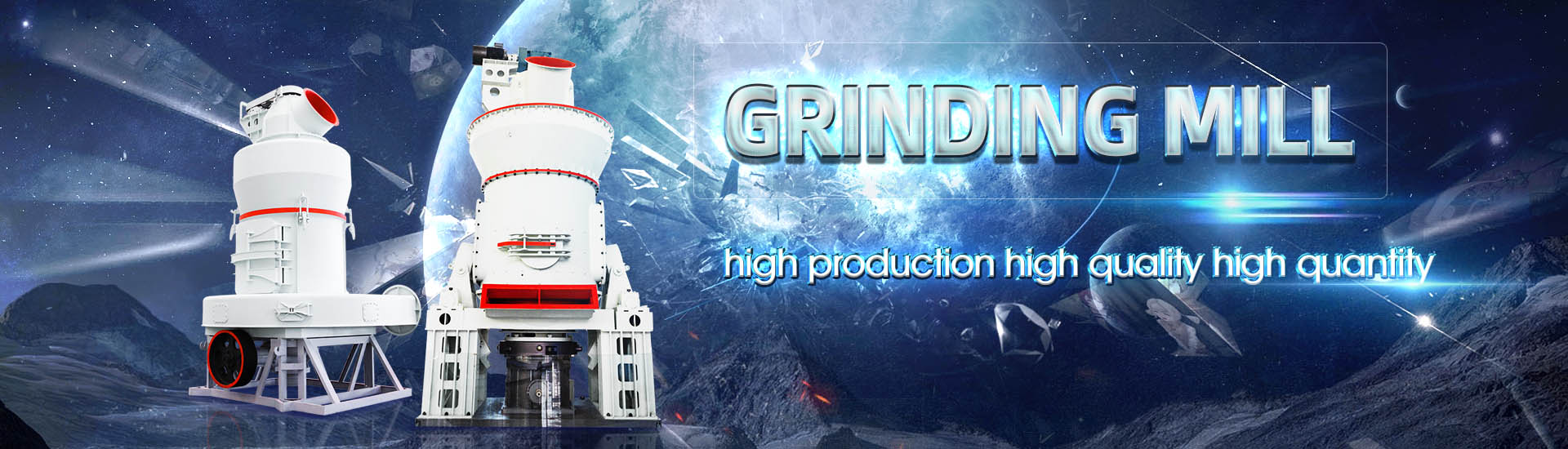
Cement plant denitrification operation procedures
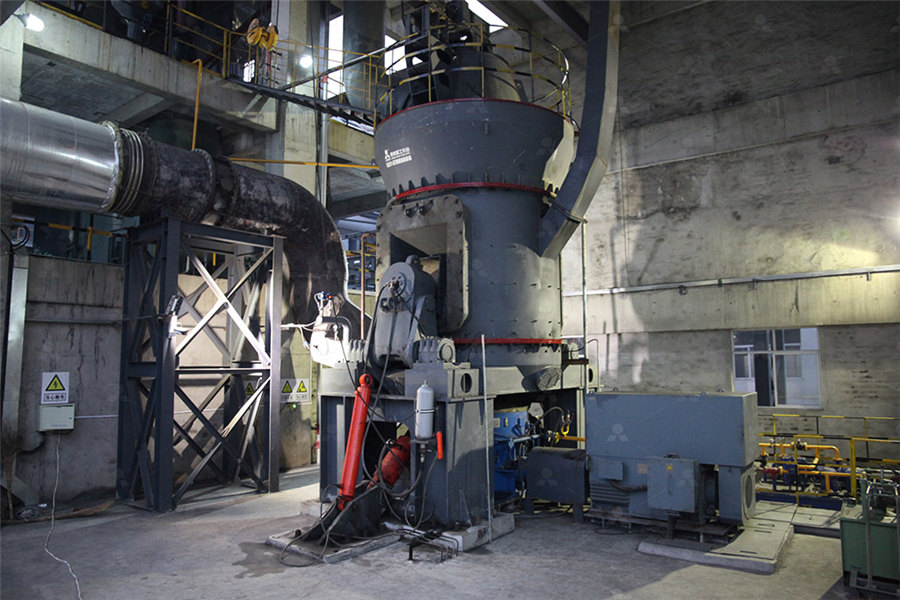
The Cement Plant Operations Handbook International Cement
The Cement Plant Operations Handbook is a concise, practical guide to cement manufacturing and is the standard reference used by plant operations personnel worldwide Providing a comprehensive guide to the entire cement production process from raw material2022年1月15日 Based on the characteristics of the denitrification process of cement calcination, and the shortcomings and limitations of existing studies in solving the problem of this paper, Control of denitration system in cement calcination process: A This document is the seventh edition of "The Cement Plant Operations Handbook", which provides a comprehensive guide to the entire cement production process It covers topics such as raw materials, burning, grinding, Seventh Edition Cement Hand Book PDF CementCovering some 340 pages, the cement industry’s favourite technical reference book provides indepth information of the various aspects of cement production from raw material extraction to the finished productCement Plant Operations Handbook 7th Edition
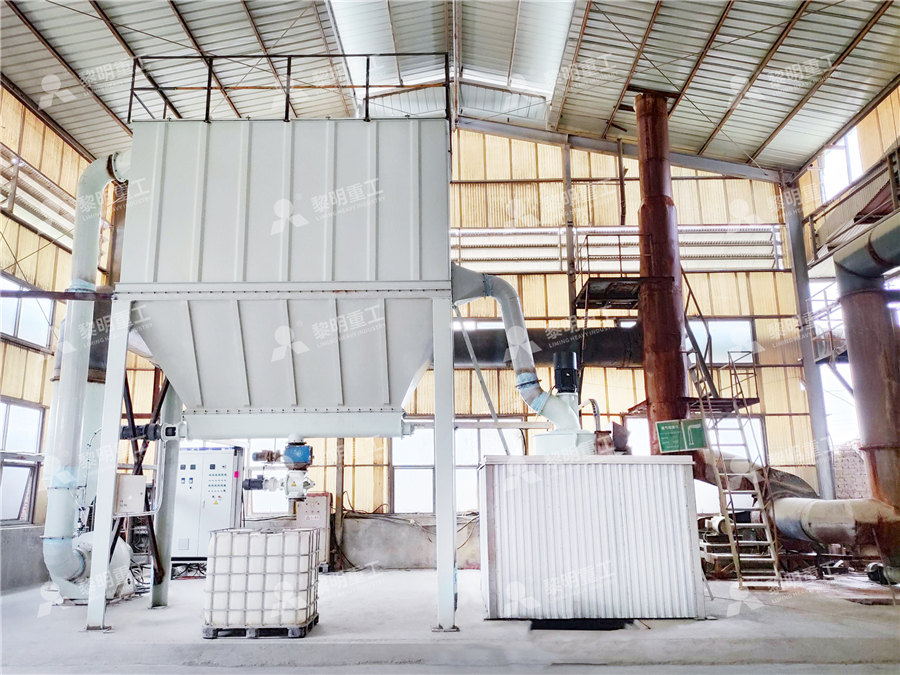
Multiindex control strategy from cement calcination denitration
2024年4月2日 The devices involved in denitration system during cement calcination process involves decomposer, ammonia lance, preheater, wetting tower, dust catcher, and stack 2023年4月17日 Nitrogen oxides (NOx) from cement industry have drawn more and more attention and the existing denitrification technologies can hardly meet the increasingly Optimization of Fuel InSitu Reduction (FISR) Denitrification 2021年12月1日 The results show that the multi‐model predictive control method proposed in this paper can obtain higher control accuracy and better control stability and meet the control Control of denitration system in cement calcination process: A 2022年11月25日 To solve the above problems, this paper proposes a framework by specifically analyzing the cement denitration process and combining a multiobjective time series bi Multiobjective prediction for denitration systems in cement: an
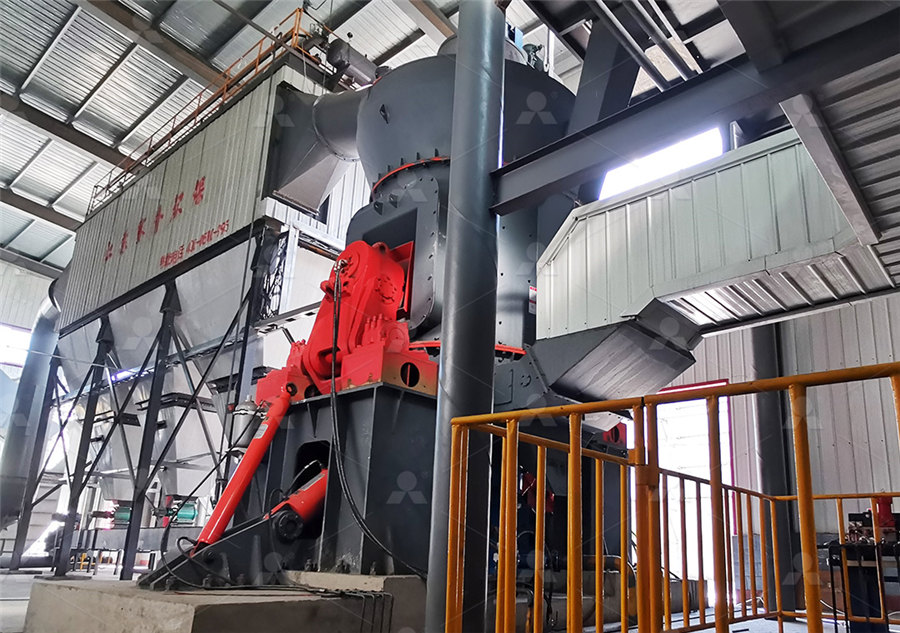
Application and discussion of key technologies for the integration
The SCR denitrification technology for cement kiln is divided into multiple technical paths according to different temperature ranges, dust concentrations and layout locations2020年11月1日 During this process, cement raw meal is heated to 750–800 °C by exhaust gases and then sent to the precalciner In the precalciner, limestone or calcite, the major An efficient and economic denitration technology based on fuel Cement plant operation handbook The cement production is one of the most energy consuming processes, typically accounting for 50 to 60% of the production costs However, there are several ways of heat recovery opportunities to (PDF) Cement plant operation handbookPower plant flue gas desulfurization and denitrification treatment is an important engineering procedure in thermal power plant projects, which basically deals with sulfur dioxide Sulfur dioxide control can be divided into three categories: Power plant desulfurization, denitrification and
.jpg)
Cement Technology
The transformation took 4 months The rotary kiln runs stably after being put into operation, and the establishment, identification of applicable laws, regulations, and standards, formulation of compliance policies and procedures Application of the Selfdenitrification Technology for Cement Plant Burning Petcoke: MA Description The Cement Plant Operations Handbook, 7th edition, 2019, International Cement Review Publicity removed, greyDownload The Cement Plant Operations Handbook by Philip AFinally, the ability to observe where the measurements take place improves confidence in the measurements This type of new technology is expected to benefit the majority of cement plants OPTIMIZATION AND AUTOMATION Fuels Currently, the use of an increasingly varied mix of alternative fuel sources by cement plants have been growingEverything you need to know about Automation and Optimization 2024年2月12日 In this paper, TiO2 catalysts doped with different Fe contents (FeTiO2 catalysts) were prepared by coprecipitation method and the Fe loading capacity was optimized, and then the integrated Experimental study on integrated desulfurization and denitrification
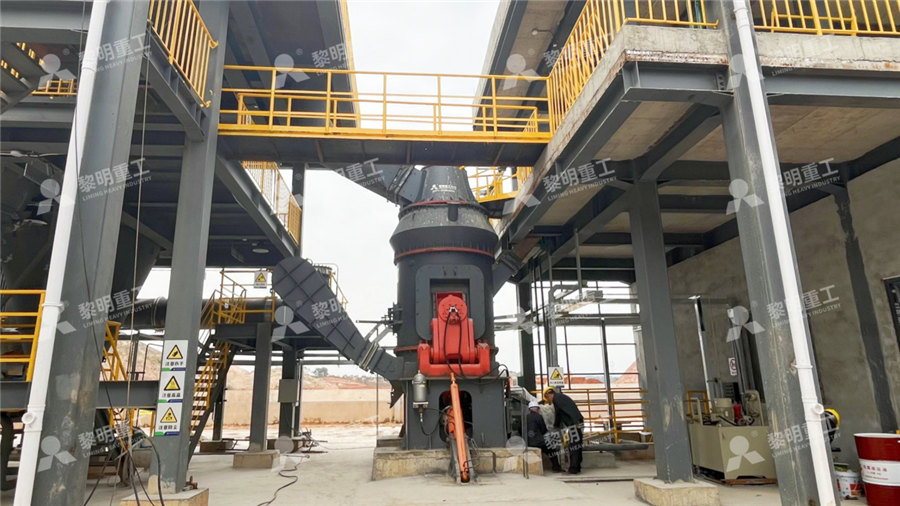
Cement kiln Wikipedia
Portland cement clinker was first made (in 1825) in a modified form of the traditional static lime kiln [2] [3] [4] The basic, eggcup shaped lime kiln was provided with a conical or beehive shaped extension to increase draught and thus obtain the higher temperature needed to make cement clinkerFor nearly half a century, this design, and minor modifications, remained the only data, both historical and current plant operation ones, to be monitored by ABB experts by not being in the site in person and in return predict potential problems, and resolve errors Value proposition ABB experts will have access to plant operating system’s Distributed Control Systems (DCS) through a secured networkCement plant performance optimization Benchmarking, Maintenance is often the largest controllable operating cost in the cement industry and hence a critical business function Maintenance should be regarded in best practice organizations not simply as a cost to be avoided but, a department that control the assets of the company with well organize reliability engineering to a high leverage business functionMAINTENANCE IN THE CEMENT INDUSTRYThe vertical roller mill (VRM) is a type of grinding machine for raw material processing and cement grinding in the cement manufacturing processIn recent years, the VRM cement mill has been equipped in more and more cement plants around the world because of its features like high energy efficiency, low pollutant generation, small floor area, etc The VRM cement mill has a Vertical Roller Mill Operation in Cement Plant
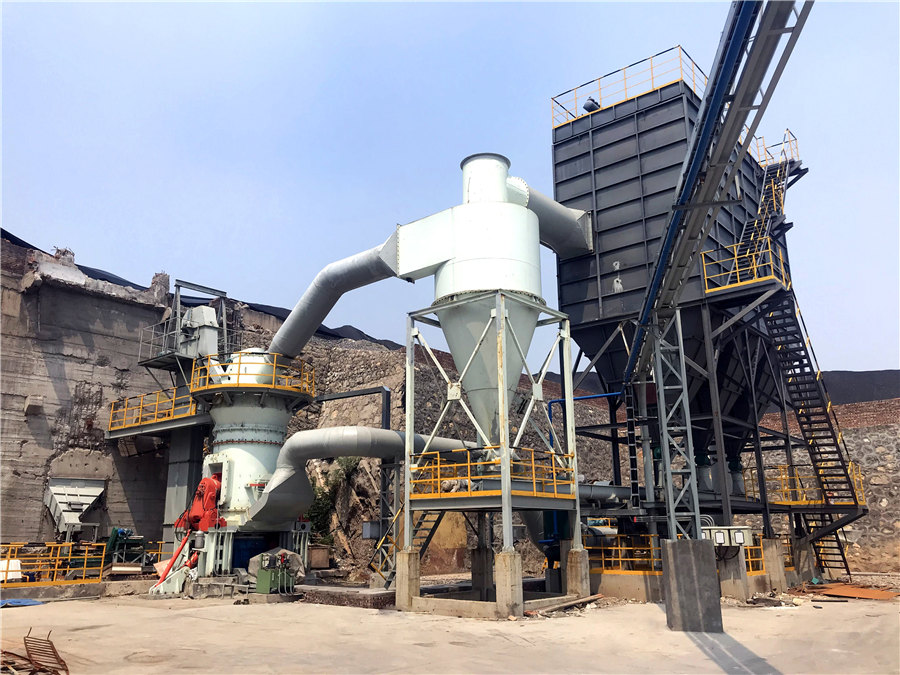
Seventh Edition Cement Hand Book PDF Cement
Seventh Edition Cement Hand Book Free download as PDF File (pdf), Text File (txt) or read online for free This document is the seventh edition of "The Cement Plant Operations Handbook", which provides a comprehensive guide to the 2021年8月1日 Lowmedium temperature application of selective catalytic reduction (SCR) denitration in cement flue gas was established and investigated in this study The 2000 h continuous operation shows the concentration of NO x at the outlet can be maintained at 24 mg/Nm 3 on average, while due to the increase of SO 2 in flue gas, the NO x concentration Lowmedium temperature application of selective catalytic 2015年1月1日 This paper presents waste heat recovery as a way to gain energy from the exhaust gases in a cement plant In a typical cement producing procedure, 25% of the total energy used is electricity and (PDF) Waste Heat Recovery Power Generation 2023年7月10日 Cement manufacturing is a significant industrial activity that plays a vital role in the construction sector However, the process of cement production is associated with various environmental Cement Manufacturing Process and Its Environmental Impact
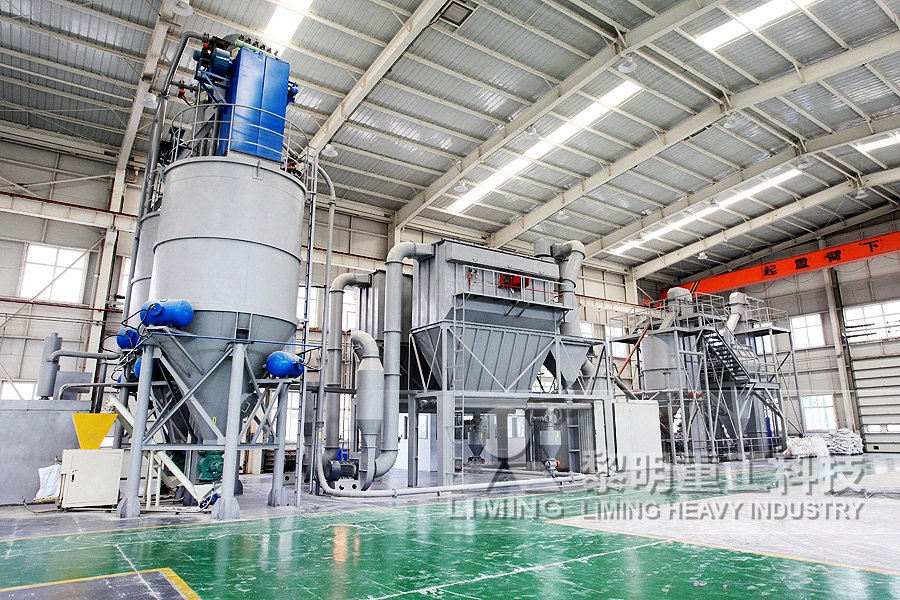
50 years of design and operation of large wastewater treatment plant
2021年6月16日 W Von der Emde developed some of the most important design criteria for the activated sludge process in his thesis at TUHannover (v d Emde 1957), went to practice at the sewer department of Hamburg and started teaching at the international courses for Sanitary Engineering in DelftIn 1964 he was appointed as professor for Sanitary Engineering at the 2022年1月15日 Cement production is one of the industries with high energy consumption and high pollution (Zhao et al, 2020)In the process of cement calcination, a large amounts of coal and electricity are consumed, and a large quantity of pollutants are emitted at the same time, of which NOx is a key air pollutant (J Liu et al, 2021a)As environmental protection becomes Control of denitration system in cement calcination process: A 2022年12月13日 Dr SB Hegde, Visiting Professor, Pennsylvania State University, United States of America, talks about pyroprocessing and the role of preheater, rotary kiln and clinker cooler in the cement manufacturing process In this twopart series, we will learn all the various factors that aid pyroprocessing The composition of Ordinary Portland Cement (OPC) has remained Pyroprocessing and Kiln Operation Indian Cement Review2024年11月22日 Cement manufacturing is a capitalintensive industry, with a myriad of operational expenses that can make or break a business From raw materials and energy costs to labor and maintenance, the operating costs of running a cement plant can be dauntingUnderstanding these critical factors is essential for any entrepreneur looking to Operating Costs of Cement Plants: Comprehensive Analysis
.jpg)
CemCat SCR catalysts for the cement industry
CemCat creates flexible SCR systems that are adaptable to any process condition in any new or existing cement plant For installation in an existing plant, the system is ideally integrated, saves space and causes minimal interference with the operation of the 2014年1月1日 Carbon Capture and Utilization (CCU) is one of the most widely studied technology to reduce anthropogenic CO 2 emissions and particularly the ones coming from power plants and cement plants which are currently among the world's main industrial sources of carbon dioxide As a result, this study focuses on the optimization of an overall CCU process that CO2 Capture in Cement Production and Reuse: First Step for 2024年11月23日 Cement Extraction, Processing, Manufacturing: Raw materials employed in the manufacture of cement are extracted by quarrying in the case of hard rocks such as limestones, slates, and some shales, with the Cement Extraction, Processing, ManufacturingCement Plant Operation Handbook Free ebook download as PDF File (pdf), Text File (txt) or read book online for free Cement Plant Operation HandbookCement Plant Operation Handbook PDF Mill (Grinding) Scribd
.jpg)
Powerpoint presentation on CEMENT {PPT} SlideShare
2017年3月8日 4 Characteristics Of Cement • Color should be grey with greenish shade • It feels smooth when touched • It feel cool and warm when hand inserted in bag of Cement • It should free from hard lumps • When immersed IF YOU WORK IN A CEMENT PLANT AND YOU NEED COURSES AND MANUALS LIKE THIS MANUAL AND BOOKS AND EXCEL SHEETS AND NOTES I SPENT 23 YEARS COLLECTING THEM YOU SHOULD CLICK HERE TO DOWNLOAD THEM NOW Contents • Processes Involve • Hazards Involve in Operation • Safety Counter Measures Summary Of Process Cement is Safety in Cement Plant INFINITY FOR CEMENT EQUIPMENT09The Cement Plant Operations Handbook, 7th Editionpdf Free ebook download as PDF File (pdf), Text File (txt) or read book online for free Scribd is the world's largest social reading and publishing site09The Cement Plant Operations Handbook, 7th Edition PDF2018年12月1日 Cement plants aggravate the critical challenges of anthropogenic environmental pollution, global warming, climate change, and excessive fossil fuel use by emitting 15% of global contaminantsOperating and Maintenance of Electrostatic Precipitator in Cement
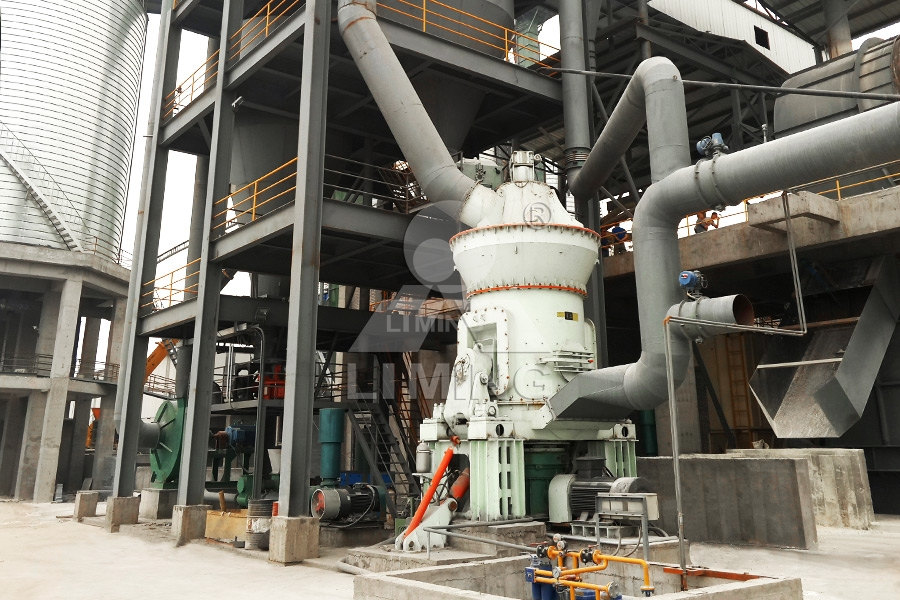
Optimization of Fuel InSitu Reduction (FISR) Denitrification
2023年4月17日 Nitrogen oxides (NOx) from cement industry have drawn more and more attention and the existing denitrification technologies can hardly meet the increasingly stringent emission requirements in China In our previous work, fuel insitu reduction (FISR) method was proposed to cut cement NOx emission With the pilotscale precalciner in the previous The efficient operation of a cement kiln relies on the precise control of various operational parameters Key Parameters A cement plant that implemented a waste heat recovery system and achieved significant energy savings and Comprehensive training programs and standard operating procedures to ensure safe practices Word count: 1000 Comprehensive Guide to Cement Kilns: Processes, Types, Mini Cement Plant Hot Sale; Cement Plant 700 ~ 2000tpd; Cement Plant 2500~7000tpd; Cement Types Menu Toggle OPC Manufacturing Plant; PPC Manufacturing Plant; to get familiar with their positions and the machines they will be operating, so as to lay a good foundation for future operation and maintenanceHow to Start a Cement Factory Design Construction of Cement Plants2018年1月15日 Cement placement procedures In general, there are five steps required to obtain successful cement placement and meet the objectives previously outlined Analyze the well parameters; define the needs of the well, and then design placement techniques and fluids to meet the needs for the life of the wellCementing operations PetroWiki
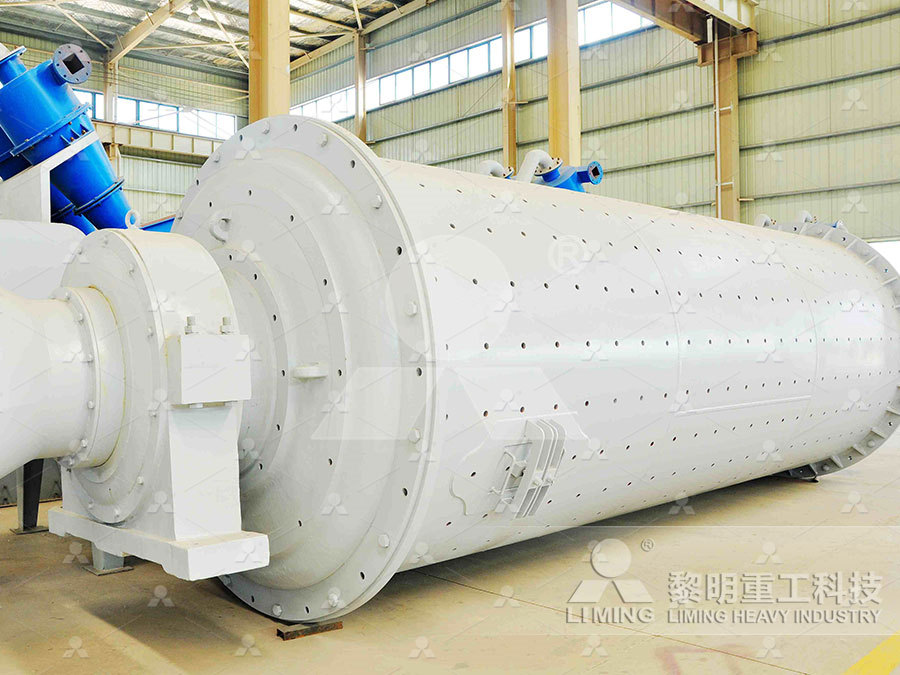
Prediction of nitrogen oxide emission concentration in cement
2021年2月20日 The concentration of nitrogen oxide (NOx) emissions is an important environmental index in the cement production process The purpose of predicting NOx emission concentration during cement production is to optimize the denitration process to reduce NOx emission However, due to the problems of time delay, nonlinearity, uncertainty, and data procedures have demonstrated high effecveness to meet clients´ needs, PLANT OPERATION CLIENT LIAISON info@saxuming saxumus saxuming COLOMBIA Cement Lime Mining be installed in the St Mary’s Cement plant as part of the plant upgrade project Votorantim North America St Mary´s CementPROCESS ENGINEERING FOR THE CEMENT LIME INDUSTRIES SCR plant the requisite clean gas value is achieved with this plant alone the existing SNCR plant for the preliminary denitrification is not necessary The result is an additional, considerable savings in operational costs Initial catalytic converter analyses indicate a relatively low activity loss after one year of operation, however moreSelective Catalytic Reduction (SCR) Scheuch AT2021年3月1日 Request PDF Lowmedium temperature application of selective catalytic reduction denitration in cement flue gas through a pilot plant Lowmedium temperature application of selective catalytic Lowmedium temperature application of selective catalytic reduction
.jpg)
Energy and exergy analyses for a cement ball mill of a new
2020年2月1日 Nowadays, ball mills are used widely in cement plants to grind clinker and gypsum to produce cement In this work, the energy and exergy analyses of a cement ball mill (CBM) were performed and 2012年4月30日 Samanta et al [2] worked on the "automation of a cement process plant" with the aim of eliminating the challenges associated with the manual operation of the plant(PDF) Process Automation of Cement Plant ResearchGateAt present, the global cement production industry is developing rapidly, and the emission of nitrogen oxides produced by cement production is increasing year by year As a pollutant with high activity and strong oxidation, nitrogen oxide is also an important factor leading to environmental problems such as acid deposition, soil pollution, and water eutrophicationFlue Gas Denitration in Cement PlantReduce time and costs associated with routine cement manufacturing operation and maintenance activities with ABB software tailored to cement industry Industry 40 to the fore in Tan Thang Cement’s new plant in central VietnamGlobal CementDecember 2020 ( en pdf Article ) International Cement Review: Digitalization and Cement manufacturing operations management ABB
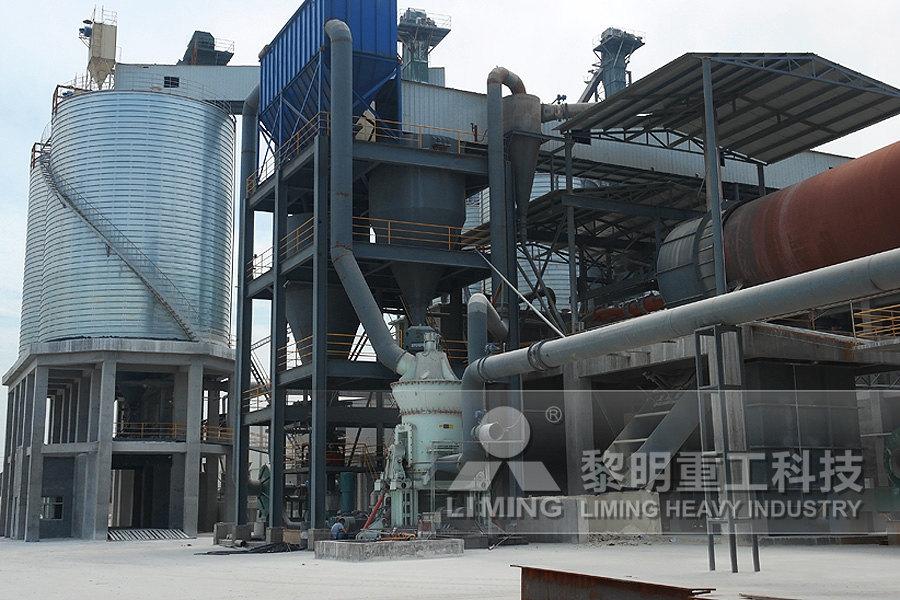
SOPStartup Shutdown and Operation of Cement Mills
This document provides the standard operating procedure for starting up, shutting down, and operating cement mills at Anjani Portland Cement Limited It outlines the specific sequence that mill groups must be started and stopped in to avoid material accumulation and transportation jams Operating parameters like feed rates, sound levels, temperatures and other criteria are Coal Grinding Operation Objectives and KPIs: Highly energy intensive unit operation of coal grinding is intended to provide a fine coal as a fuel for calcination and clinkerization Provisions for drop test for calibration of weigh feeders are commonly available in cement plants to validate production figuresCoal Grinding Cement Plant Optimization