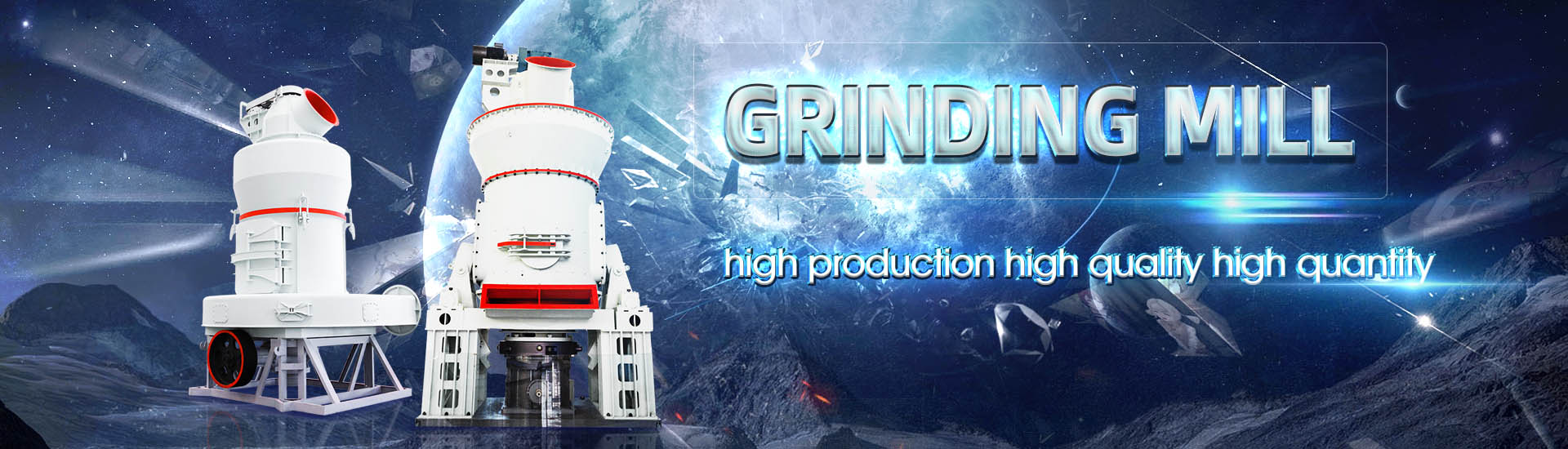
Particle size requirements for sintered lime after crushing
.jpg)
Crushing mechanism analysis of sintered ore and study of particle
2024年4月24日 To improve the crushing effect and reduce the range of particle size distribution after crushing, the crushing mechanism and the particle size distribution pattern after crushing of sintered ore under different roller rotation speeds are analysed in this paperSinter with limestone mean particle size of 125 to 152 mm yielded better sinter strength and lower RDI compared to sinter with smaller or larger limestone mean particle size Higher sinter strength is due to better and uniform distribution of (PDF) Influence of limestone particle size on iron ore 2024年10月24日 This research analyzes the influence of specific impact energy and initial particle size on the impactcrushing characteristics of limestone particles It also examines the Experimental Study of the Crushing Characteristics of Single Influence of limestone particle size on iron ore sinter properties and productivity × Close Log In Log in with Facebook Log in with Google or Password Remember me on this (PDF) Influence of limestone particle size on iron ore sinter
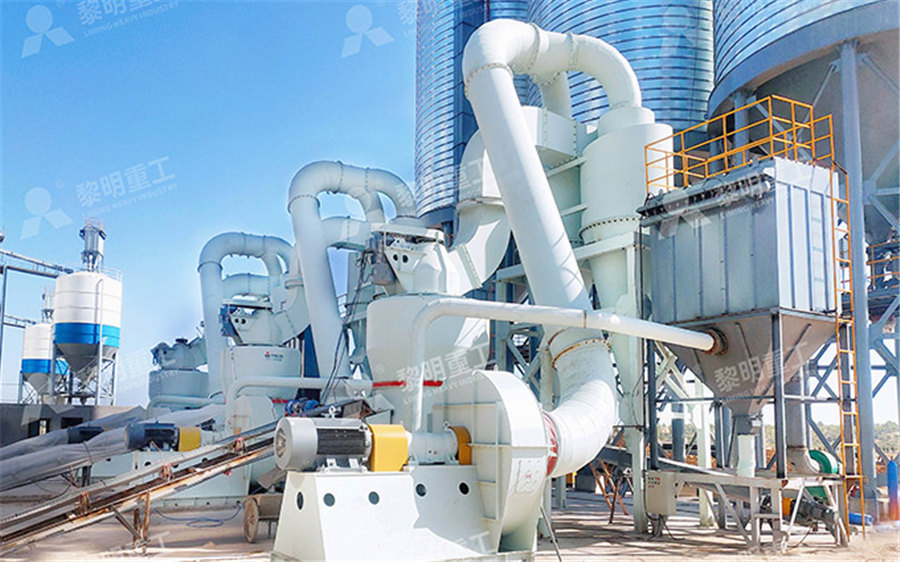
Influence of Particle Packing, Size, and Gradation on Crushing
2024年11月25日 The mean size of individual ballast particles was determined by calculating the arithmetic mean of the dimensions of three sides of the particle Ballast particles were selected 2010年6月15日 Sinter with limestone mean particle size of 125 to 152 mm yielded better sinter strength and lower RDI compared to sinter with smaller or larger limestone mean particle size Influence of limestone particle size on iron ore sinter properties scale granulation experiments to predict the particle size composition of mixes by Litster and Waters The predictions of the model are based on the theory of the partition coefficients Iron ore granulation for sinter production: Developments, 2020年3月1日 In this study, singleparticle crushing tests were carried out on rockfill materials with nominal particle diameters of 25 mm, 5 mm and 10 mm to investigate the particle size Effects of particle size on crushing and deformation behaviors of

The effects of agglomeration time and burnt lime addition on the
Burnt lime speeds up particle bonding while increasing the agglomerate’s holding capacity On the other hand, the adequate mixing time and drum speed are fundamental to promote the 2023年6月8日 The flux and fuel used for sintering are subject to particle size requirements and thus usually need to be crushed and sieved, which may happen in the raw material yard or in Iron Ore Sintering SpringerLink2023年12月1日 Due to the decreasing reserves of highgrade iron ore and secondary resources used for steelmaking, it has become an important research and development area to improve the grade of iron ore through crushing (Gul et al, 2014)The quality of iron ore crushing directly affects the performance of pellets and sinter, so as to influence the quality and performance of Crushing characteristics and performance evaluation of iron ore in How to optimize the sintered ore particle size composition, reduce the coarse and fine particle size difference, and improve the strength index is the key point to improving the quality of sintered ore at this stage However, due to the diversity of sintering raw materials and the complexity of crushing particle size, people have not been able toOptimization of roller teeth based on the analysis of the crushing
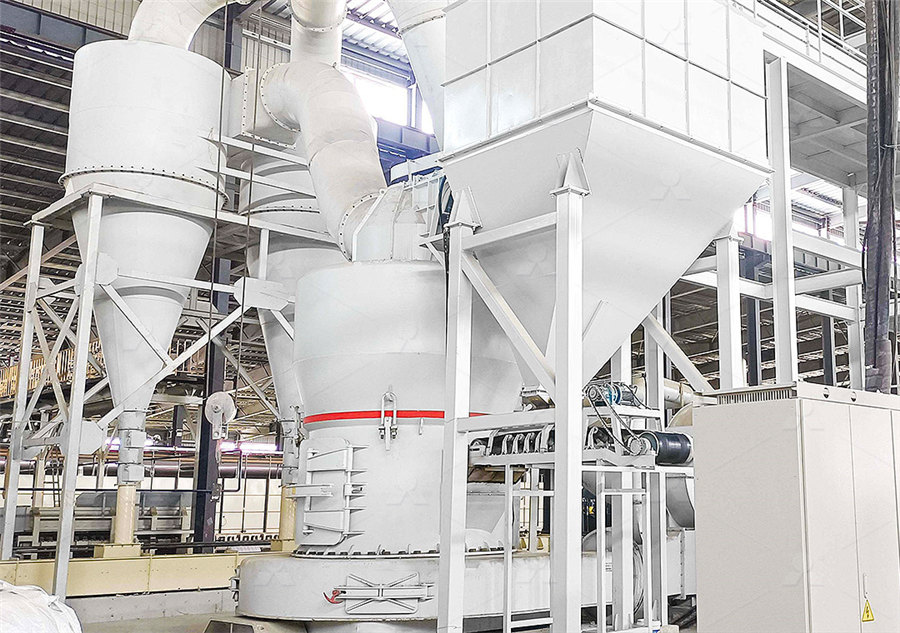
AA04 Bauxite Particle Size Requirements for the Bayer
AA04 Bauxite Particle Size Requirements for the Bayer Process: Back to Basics Ahmed Ibrahim1, Ahmad Hommadi2, Abdullah Otaibi3 and Peter Swash4 1 Engineer 2 Engineer 3 Each bauxite will have its own distinctive crushing and milling characteristics Bauxite can be highly variable through the mine pit profile, 2007年1月1日 In order to reliably size crushing processes and crushers phenomenological concepts are developed which investigate and determine the particle behaviour by statistical means These concepts cannot principally fulfil any requirements to explain the nature of fracture, but they yield all necessary information concerning the phenomenological reaction of a particle Chapter 4 The Principles of SingleParticle Crushing2014年5月29日 Based on a standard compaction test and a standard sieve analysis test on five tested materials, the effects of the particle size distribution on the compaction behavior and particle crushing of a crushed mudstone particle mixture were investigated Testing results indicate that the value of the maximum dry density ranges from 209 to 217 g/cm3, the Effects of Particle Size Distribution on Compaction Behavior and 2017年3月4日 The double jaw crusher is designed for crushing hard materials, also quarried materials, sand and gravel, and recycling [4, 5] crusher [4] The tie rod and compression spring ensure that the SIZE REDUCTION BY CRUSHING METHODS ResearchGate
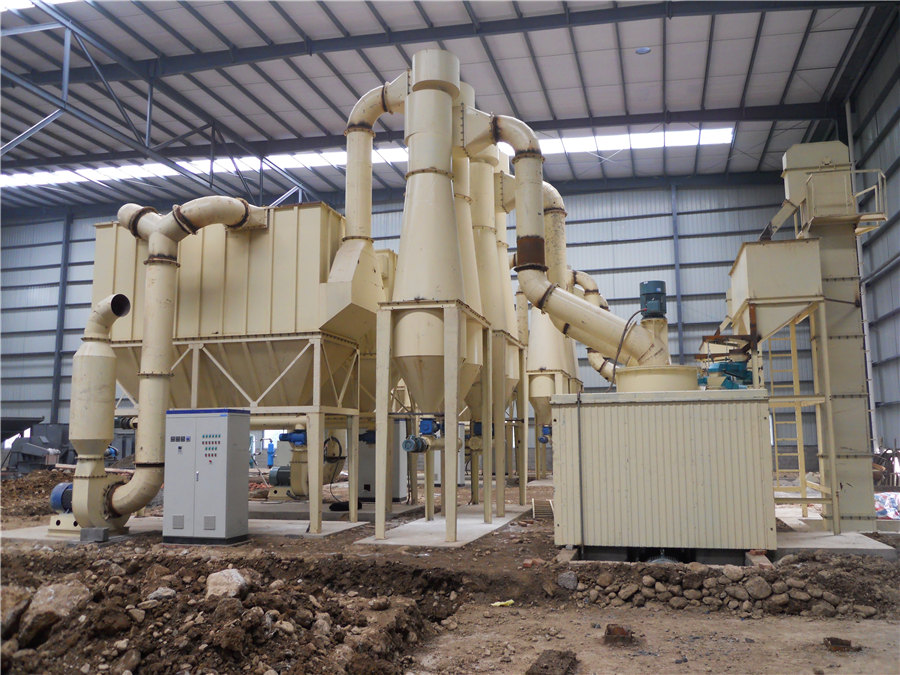
Effects of particle size on crushing and deformation behaviors of
DOI: 101016/JGSF201810010 Corpus ID: ; Effects of particle size on crushing and deformation behaviors of rockfill materials @article{Xiao2020EffectsOP, title={Effects of particle size on crushing and deformation behaviors of rockfill materials}, author={Yang Xiao and Minqiang Meng and Ali Daouadji and Qingsheng Chen and Zhijun Wu and Xiang Jiang}, 2022年9月29日 This study examines the particle size and distribution of the main chemical components of gangue during the crushing process Coal mine gangue was chosen as the research object, and its particle size and chemical components at various crusher discharge settings were examined through screening, grinding, chemical composition testing, and other Experimental Investigation of Particle Size Alteration and the 2021年7月9日 Particle size distribution (PSD) is an essential property of cement The only standard method to measure the PSD of cement, namely ASTM C115 is limited in scope; this standard describes a method Particle size distribution of cement and concrete ResearchGate2022年9月11日 particle size on the mechanical properties of the nal materials A general trend of obtaining higher exural strength when using smaller particles upon sintering dense ceramics was reported for B(PDF) Role of particles size on the cohesive strength of nonsintered
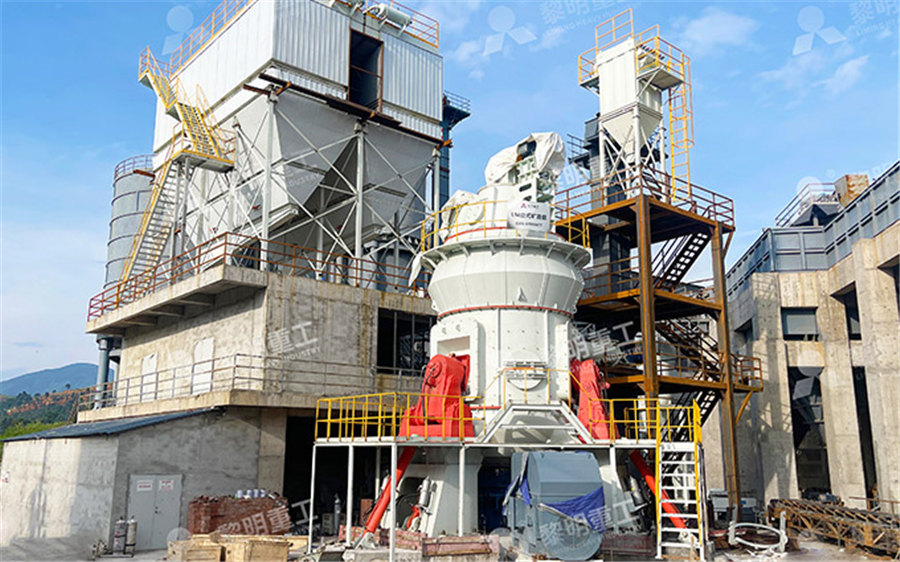
Mechanical behavior and particle crushing of irregular granular
2023年5月15日 Guo, R F et al Effect of particle size on recrushing characteristics of crushed coal during axial loading Powder Technol 407, 1–12 (2022) Google Scholar2023年11月10日 Shear strength of the sintered Ag layers was over 40 MPa and elastic modulus of the sintered Ag layer was 14 GPa before and after the storage tests at 250 °C and for 1000 h View Show abstractParticle Size Effects of NanoAg Films on the Interface Sintered 2020年3月1日 However, the effect of particle size on crushing and deformation behaviors of rockfill materials has not been fully investigated Download: Download highres image (408KB) Download: Download fullsize image; Figure 1 Typical singleparticle crushing forcedisplacement relationship based on Nakata et al (1999)Effects of particle size on crushing and deformation behaviors 2021年3月3日 Lime is the least expensive and one of the most heavily used alkali in the world, being essential to our society It is a nonhydraulic binder, excepting the socalled hydraulic lime, meaning that it will not set under waterFor this reason, lime is sometimes called air lime since it hardens on exposure to air It was used for thousands of years in masonry mortars to bind the Lime SpringerLink
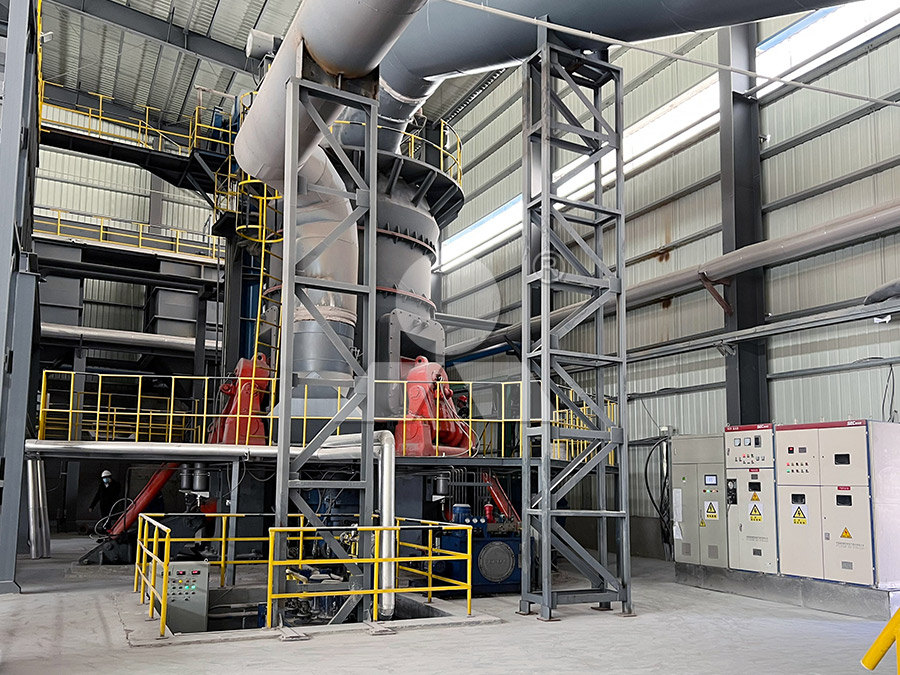
Singleparticle crush test for ultrafine particles and direct numerical
2021年5月1日 The singleparticle crush tests were performed under the conditions of a maximum loading speed of 2074 mN/s; to derive the loaddisplacement curve and determine the breakage force, F c, pressure was applied until the particles were crushedPortnikov et al reported on the effects of the loading speed on the singleparticle crush test results for glass 2017年9月30日 The ore particle size distribution is an important basis for the evaluation of crushing effect The particle size parameters mainly include the particle area, perimeter, equivalent diameter, shape factor and so on In order to obtain the ore particle size distribution, we mainly study the following aspects: (1)Research of Ore Particle Size Detection Based on Image Processing2024年7月14日 In a single particle crushing test, the splitting stress of the irregular particle can usually be expressed by (Jaeger, 1967): (19) where is the main peak force on the loaddisplacement curve, which refers to the load that the particle occurs throughgoing splitting in this study; is the initial distance between the loading platens, which corresponds to the length of Influence of real particle morphology on single particle crushing 2018年1月8日 The paper provides an indepth exploration of the role of particle crushing on particle kinematics and shear banding in sheared granular materials As a twodimensional approximation, a crushable granular material may be represented by an assembly of irregularly shaped polygons to include shape diversity of realistic granular materials Particle assemblies Role of particle crushing on particle kinematics and shear
.jpg)
Validation of Particle Size Segregation of Sintered Ore during
The particle flows in the hopper and the chute were simulated by using DEM, and the particle size segregation in the simulation work was compared with the experimental results to validate the properties in this simulation The geometry of the chute was completely same as that of experimental, and the size of sintered ore particle was deter2024年4月15日 Fig 11 shows the difference in the particle size distribution before and after compaction (step 0 and step 1) The particle size distribution of the coarse and fine aggregate differed markedly In addition, a marked difference in the particle size distribution occurred in Case 1, which involved a large particle sizeCrushing characteristics and particle size distribution of Download scientific diagram Particle size distributions (PSDs) of limestone measured by ICA for outlets: (A) limestone O1–O4 and (B) FA collected in different outlets O4–O7 The median Particle size distributions (PSDs) of limestone measured by ICA for the particle size distribution functions of a mill product Figure 112 provides the particle size distribution of a mixture of two plastic waste products After grinding, the particle size distribution changed to that shown in Figure 113 Clearly, the two different types of plastic displayed different behaviour during crushing Both were crushed:11 Crushing and classification
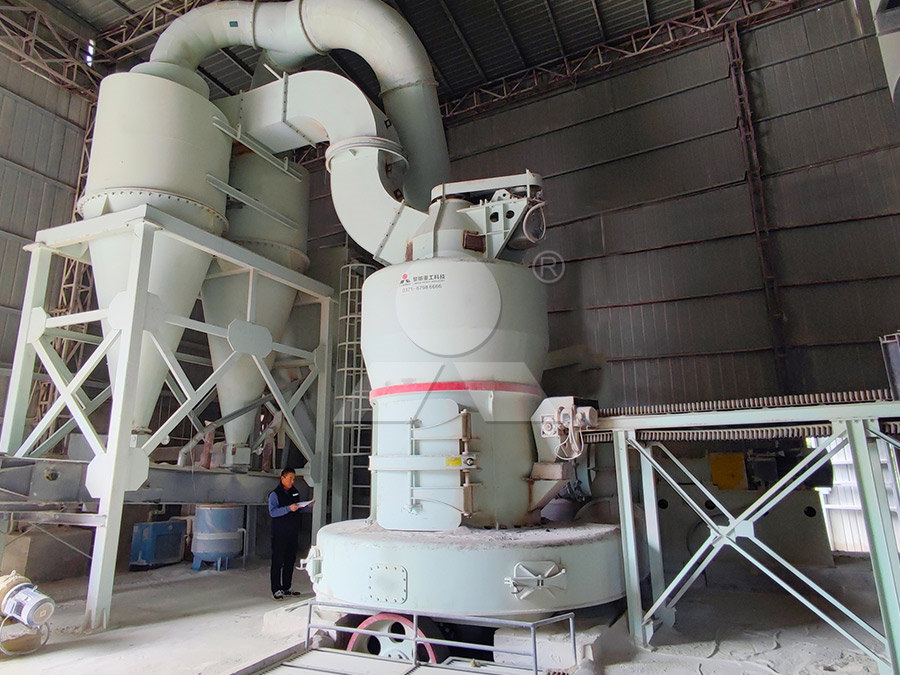
Effect of particle size on recrushing characteristics of crushed
2022年7月1日 The particle recrushing characteristics of crushed anthracite with different particle sizes during axial compression are evaluated Subsequently, the effect of particle size on the recrushing characteristics of crushed anthracite is analyzed comprehensively Finally, the layered recrushing mechanism for crushed particles is discussed 22023年11月11日 For converter steelmaking, the particle size requirement of active lime is to ensure the slag formation speed and effect in the steelmaking process with time requirements If the particle size of lime is too large, the reaction time between lime particles and molten steel will be prolonged, the slag formation speed will be slowed down and the slag formation effect will The Quality Requirements For Active Lime You Should KnowDownload scientific diagram Particle size distribution curves of hydrated lime, Portland cement (CP) and RCW [Figura 1: Curvas de distribuição granulométrica da cal hidratada, cimento Particle size distribution curves of hydrated lime, Portland cement 2010年10月1日 The obvious way to reduce the water requirement is to maximise the powders packing density, ie to have an Andreasen particle size distribution modulus, q, near 037 7 While modelling particle size distributions (PSD), Andreasen defined the particle size distribution modulus, q, given by Eq (1), as a measure of the contribution of the various ingredient size Designing particle sizing and packing for flowability and sintered
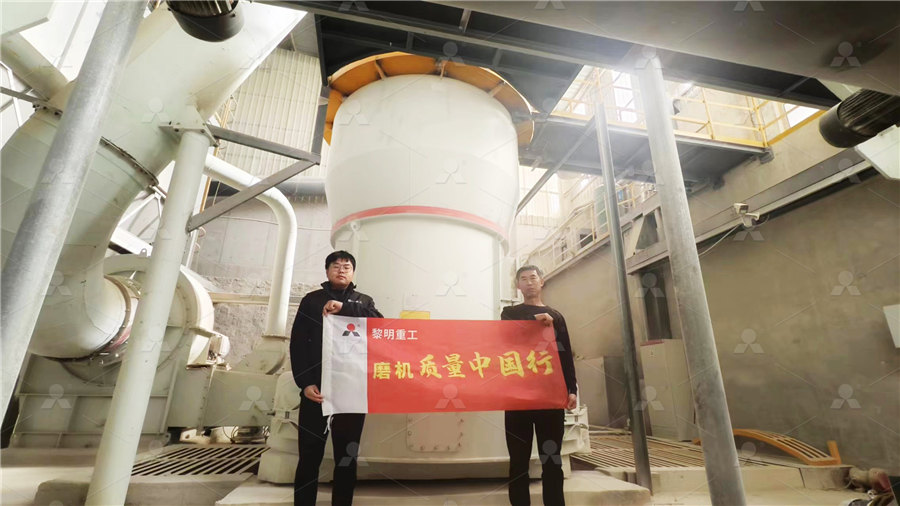
The sintering kinetics and properties of sintered glassceramics
2019年10月1日 Moreover, the properties (water absorption, flexural strength and chemical resistance) of the sintered glassceramics were enhanced with the decrease of the particle size and reached the standards 2024年5月30日 Assuming that the coal particles are standard spheres, the new surface area during the crushing process of coal particles may be obtained according to the particle size distribution data obtained after crushing [[28], [29], [30]], (2) Δ S = S i − S 0 (3) Δ S = ∑ 6 m γ i ρ d i − 6 m ρ d where S is the new surface area in the crushing process, m 2; m is the total mass Study on coal pulverization characteristics and gas desorption technologies also require lab measurements to track changes in particle size including crushing, homogenization, emulsification and microfluidization Separation steps such as screening, filtering, cyclones, etc may be monitored by measuring particle size before and after the process Particle size growth may be monitoredA GUIDEBOOK TO PARTICLE SIZE ANALYSIS University of Iowa2023年7月10日 The present literature review explores the energyefficient ultrafine grinding of particles using stirred mills The review provides an overview of the different techniques for size reduction and the impact of energy requirements on the choice of stirred mills It also discusses the factors, including the design, operating parameters, and feed material properties, EnergyEfficient Advanced Ultrafine Grinding of Particles Using
.jpg)
Quantifying the influence of single particle shape on crushing
2024年8月16日 The singleparticle crushing modes of geotechnical bodies can be varied [31], and this paper categorized the results of compressed and crushed RA particles of different shapes (sphericity Φ) based on criteria such as particle size after crushing and cracking method2024年1月11日 Due to the reliance on the plate hammer and rotor, it is more suitable for crushing limestone powder with low hardness, reducing wear and tear of vulnerable parts It is convenient to meet the user’s requirements for the Limestone Crushing And SandMaking Plant Eastman 2013年1月1日 Size reduction is energy intensive especially for cases where the target particle is small and precise in dimension Mineral and food industries have developed empirical and semiempirical Development of Size Reduction Equations for 2024年1月23日 Scanning electron microscope (SEM) images of a crushed particle with a diameter of 500 mm were taken, as shown in Fig 2Xray tomography images of LECA particles were also taken to reconstruct threedimensional models, as presented Fig 3, where the particle diameter is 440 mmThe binarized image sequences in Fig 3a were taken every 010 mm Structure feature and compressive crushing behavior of
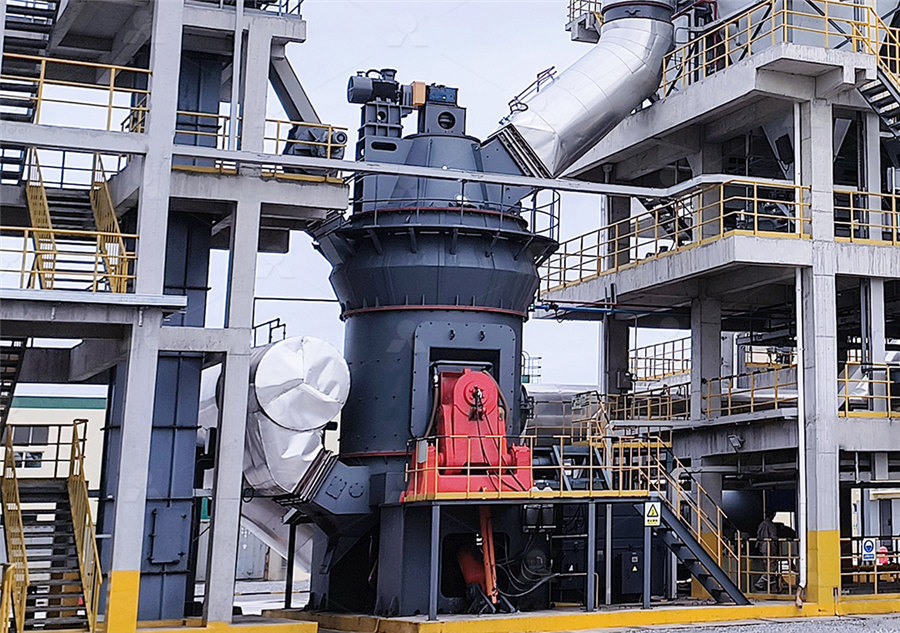
Powder Mass of Coal After Impact Crushing: A New Fractal
2020年6月17日 Firmness is one of the most important physical properties of rock, and indicates the rock’s ability to resist damage It has considerable relevance to mining, blasting, tunneling, construction, and other engineering fields In this study, the fractal particlesizedistribution theory was used to calculate the surface areas of coal particles after impact crushing Combining the 2023年2月5日 A general trend of obtaining higher flexural strength when using smaller particles upon sintering dense ceramics was reported for B 4 C and SiC materials [14], [15]However, little to no experimental evidence was given for nonsintered materials, apart from the experiments with thin colloidal films, where the film hardness increases with the decrease of particles size [16]Role of particle size on the cohesive strength of nonsintered Engineering particle size distribution of sintered lightweight aggregates manufactured from waste coal combustion ash Yousif Alqenai1*, Puput Risdanareni2, Mohammadamin Zooyousefin1, Thuy Nguyen1, and Yaghoob Farnam1 1 Department of Civil, Architectural, and Environmental Engineering, Drexel University, 3141 Chestnut St, Philadelphia, PA, 19104, USAEngineering particle size distribution of sintered lightweight 2024年2月15日 In Fig 4 (left hand) the raw signal is depicted after Fast Fourier Transformation (FFT) for a random single 5min block The crushing noise peaks from the sinter in the hot crusher can be observed after 05, 18, 3 and 42 min in the image but also smaller following peaks after the main peak at 3–35 and 42–45 minNew Measurement Techniques Describing the Sinter Process
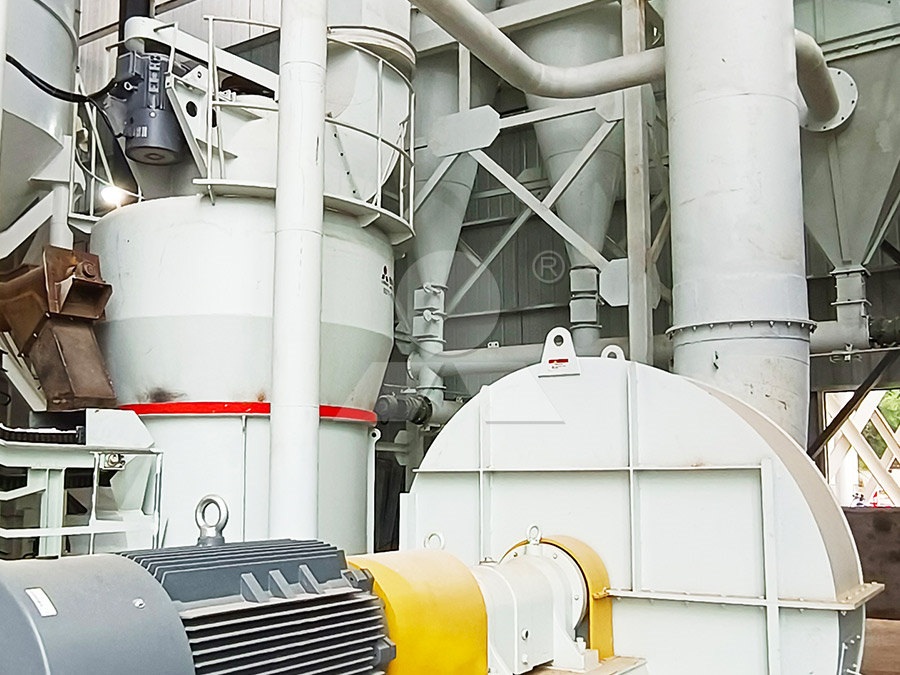
Choose Hydrated Lime Plant for Advanced Lime Processing
Process Flow of Hydrated Lime Production Line Raw Material Preparation: Quicklime needs to be crushed and screened to obtain the raw material with uniform particle monly used raw materials are limestone, dolomite and so on Hydration of Quicklime: the raw materials quick lime after crushing and screening are mixed with appropriate amount of water, and the hydration 2021年5月14日 Evaluation of Different Agricultural Lime Sources for their Agronomic Effectiveness, Yield of Food Barley and Faba Bean and Acid Soil Properties in the Central Highlands of Ethiopia(PDF) Evaluation of Different Agricultural Lime Sources for their