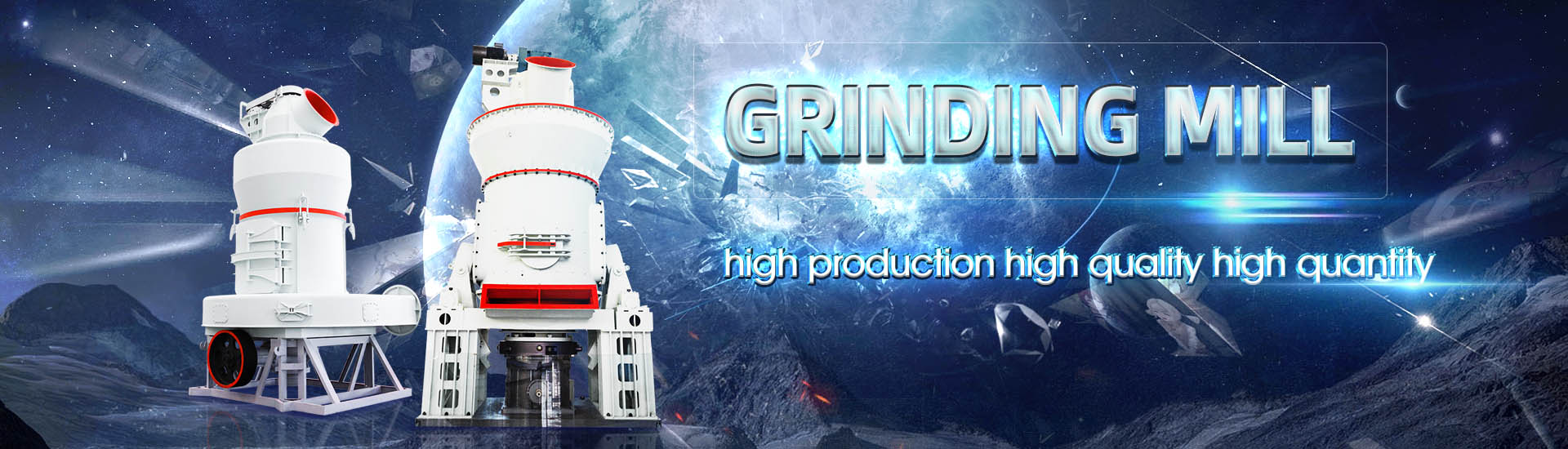
Chute iron oxide selection process
.jpg)
Unrevealing energy dissipation during iron ore transfer through
2024年2月15日 Industrialscale chute transfer of iron ore is analyzed by a GPUDEM model Both conventional and modified head chute designs are evaluated comprehensively The location and mechanisms of energy dissipation affect transfer performance A microboxed design 2022年1月1日 This chapter first introduces the principles and recent advances in magnetic separation technology in processing iron ore, followed by examples of flow sheets for Physical separation of iron ore: magnetic separation ScienceDirect2016年3月30日 Processes that produce iron by reduction of iron ore (in solid state) below the melting point are generally classified as DR processes Based on the types of reductant used, DR processes(PDF) i) Direct Reduced Iron: Production ResearchGateDirect reduction of iron (DRI) forms an important subsector of the Indian steel sector, accounting for about 33% of the total steel production, which is about 3415 million tonne of steel produced inENERGYEFFICIENT TECHNOLOGY OPTIONS FOR DIRECT
.jpg)
(PDF) An Overview of the ReductionSmelting Process
2022年8月23日 This study gave an overview of the reductionsmelting process as a third generational alternative for the modernday iron and steelmaking process whose hallmark is to mitigate the2024年2月15日 Coalbased direct reduced iron (DRI) reduces CO2 emissions by 38 % compared with traditional blast furnace–basic oxygen furnace (BFBOF) ironmaking Using a Direct reduction of iron to facilitate net zero emissions in the steel 2024年6月21日 Hydrogen metallurgy has been regarded as the most promising way to mitigate CO 2 emissions from ironmaking and it has been shown that the HyDRIEAF process can Iron Oxide Direct Reduction and Iron Nitride Formation Using 2024年10月15日 The H 2 consumption in this study refers to the amount of hydrogen gas required to reduce various iron oxides to metallic iron in the direct reduction process H 2 Optimization of Hydrogen Utilization and Process Efficiency in the
.jpg)
Basic Oxygen Steelmaking Slag: Formation, Reaction,
In this process, valuable metals reduced from their oxides form an alloy with molten iron, and then can be recovered by separating the ironbearing alloy from the slag Recovering vanadium and chromium from BOS slag was reported 2022年8月23日 Preliminary studies have revealed that there are tendencies to achieve more than a 90 % metallization degree from the direct reduction of iron ore/oxides using noncoking coal or charcoal as a (PDF) An Overview of the ReductionSmelting Process 10 Background of Iron and Steel Industry 1 11 Overview of Iron and Steel Industry 2 12 Details of Direct Reduction of Iron Plants 2 13 Mapping of Direct Reduction of Iron Units 4 14 Production Process 5 20 Key Performance Indicators of Direct Reduction of Iron Process 9 21 Capacity Utilization 10 22 Yield 10ENERGYEFFICIENT TECHNOLOGY OPTIONS FOR DIRECT REDUCTION OF IRON PROCESSIron rust is scientifically known as iron III oxide, but it’s not just that Technically, it's a complex mixture of hydrated iron III oxides, iron III oxidehydroxide, and iron III oxide And this compound doesn't form on the iron surface instantly It's a multistage processIron Rust: Formula, Prevention, Process Causes Vaia
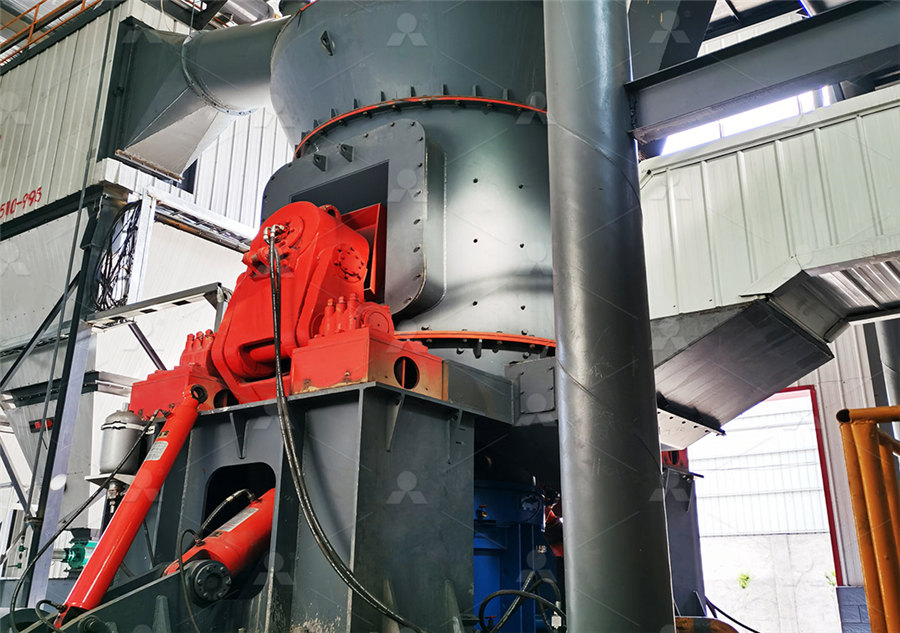
Lining Materials for Bulk Solids Handling Equipment – Selection of
The hardness on R45N scale may be maintained in the range of 7581As the Alumina ceramic tiles are manufactured with powdered Aluminium Oxide by sintering process, these can be obtained in any predefined shape and sizeThe Alumina ceramic tiles exhibit extremely good physical, mechanical, thermal and electrical properties for industrial applications2024年4月26日 The intense heat generated by the combustion of coke reduces the iron oxides in the ore to metallic iron The limestone or dolomite reacts with impurities, forming a slag that floats on top of the molten iron The molten iron, known as hot metal, is periodically tapped from the bottom of the furnace and further processed in steelmakingIron Ore Processing: From Extraction to Manufacturing2022年8月3日 1 Iron ore crushing process: In the iron ore crushing process, the feeder, first crushing, secondary crushing, screening, fine crushing and dry selection are generally used For the sake of economy, generally the finer the ore particle size entering the dry separator, the higher the proportion of ironbearing ore that is dry selectedIron ore crushing and screening process SBM Ultrafine Powder 2024年3月22日 Figure 31 is the binary phase diagram obtained from the calculation with Fact Sage 72 The reason why Fe 1–x O is unstable under 570 ℃ is explained in Fig 31The figure shows that Fe 1–x O is only stable when the temperature is higher than 570 ℃, otherwise, it will be decomposed into Fe 3 O 4 and Fe In addition, since the vacancy in the iron lattice of Fe Direct Reduction of Iron Oxides with Hydrogen SpringerLink
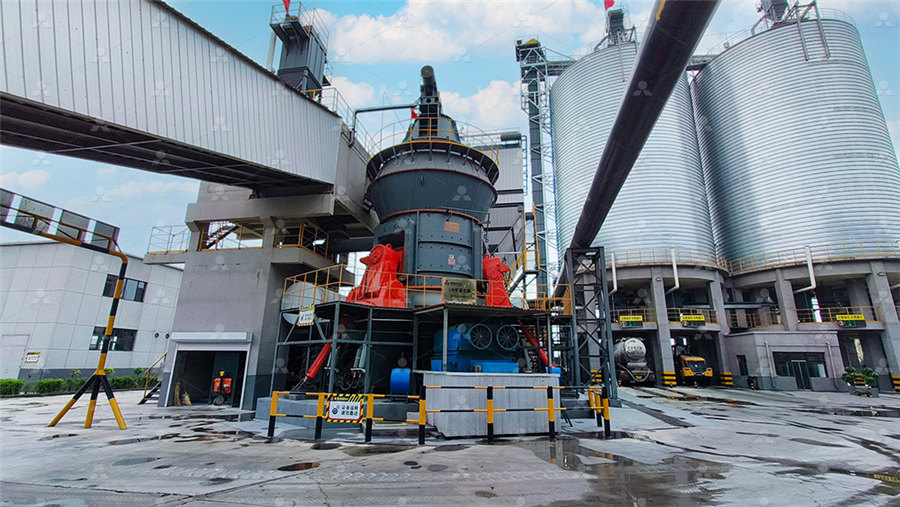
Iron and SteelMaking Process SpringerLink
2020年6月10日 224 Direct Reduction of Iron Oxide by Solid Carbon The direct reduction process of iron oxide by solid carbon is highly endothermic in nature and occurs when the molten slag flows over incandescent coke in the bosh region at a temperature above 1000 °C Therefore, the corresponding reaction can be written as follows:2014年11月25日 The practice of using electrodes to process oxides appeared as soon as reliable, largescale electric power had been mastered 52 For example, as early as 1906, 53 Paul Héroult used graphite as electrodes in a commercialized direct current electric arc furnace to melt and perform the reduction of an iron oxide feedFeatures and Challenges of Molten Oxide Electrolytes for Metal 2020年7月15日 Currently, approximately 95% of hot metal is produced by the blast furnace ironmaking process, which is also predicted to be the largest single ironmaking process until 2050 because of its advantages in production cost and efficiency Therefore, replacing fossilbased fuels with H 2 as the reductant is expected to relieve environmental concerns and, Blast Furnace Ironmaking an overview ScienceDirect Topics2023年7月7日 Similarly, Iron Oxide NPs showed excellent antimicrobial potential against bacterial species “Salmonella typhi” “Xanthomonas Oryzae” and “Lactobacillus” at low concentrations (150 µg/mL)(PDF) Synthesis, characterization, and applications of
.jpg)
Recent status of fluidized bed technologies for producing iron input
2011年2月1日 While the iron atom diffusion flux at the root of the iron whisker during the pregrowth process is much larger than the flux when the layered iron is produced, which are defined to be 0081 mol 2023年2月22日 Process parameters and sensitivities of the batch chloriron cell (A) Relationship between ηFe and J for Fe plated in a batch cell divided by Nafion 115 ηFe >85 % was sustained for current Electrochemical ChlorIron Process for Iron Production from Iron Oxide The iron in iron ore comes from iron oxides found in deposits such as massive hematite (the most commonly mined), magnetite, titanomagnetite, and pisolitic ironstone Most major deposits can be found in sedimentary rocks created by chemical reactions between iron and oxygen in fresh and marine waters between one billion and three billion years agoIron Ore: From Mining to Processing to Dust Control2011年4月19日 This novel technology electrolyzes iron oxide into metallic iron that is of crude steel quality (Allanore, Ortiz and Sadoway, 2011; Allanore, 2014;Wiencke et al, 2018)Molten Oxide Electrolysis for Iron Production: Identification of
.jpg)
Recent Trends in the Technologies of the Direct Reduction and
2023年4月5日 Among the reduction methods of iron oxides in ironmaking processes are direct reduction, blast furnace/blast oxygen furnace, and smeltingreduction process Reduction of iron oxide involves the upgrade of iron ore in pellets, lumps, or sintered form under a highly thermalcharged atmosphere in the presence of carbonaceous materials [18, 19 2018年6月27日 The primary energy source for the reduction of iron oxides for the integrated steelmaking process is coal while for the DREAF route the source of reducing gases can be not only natural gas (NG Optimization of the Iron Ore Direct Reduction Process through 2023年8月1日 The literature devoted to the reduction of iron oxide is abundant Patisson et al [1] reported about twenty thousand publications listed by the Web of Science [2] on this topic over the time period 1900–2020 This research has been driven by the economic and academic importance of the field, mostly for its application in the iron and steel industryThermochemical reduction of iron oxide powders with hydrogen: 2017年7月14日 The elements iron and oxygen are the most common in the earth’s crust, causing the natural formation of iron oxides through rocky weather, both on land and in oceans mainly for use in environmental decontamination process The oxides, Fe 2 O 3 and Fe 3 O 4, for example, are semiconductors of small “bandgap” (∼ 22 eV), Iron Oxides Applied to Catalysis SpringerLink
.jpg)
Redox reaction induced morphology and microstructure evolution of iron
2018年7月15日 In general, a reliable oxygen carrier should follow the selection criteria, such as high reactivity in redox reactions, sufficient oxygen transport capacity, chemical and mechanical stability at high temperatures, the redox reaction induced morphology and microstructure evolution of iron oxides in CLC process were investigated2019年11月30日 The iron ore mine also uses contractors for cleaning purposes The contractors use 40t payload Articulated Dump Trucks (ADT) 27 Quality/Grade Control At the iron ore mine, the Run of Mine (ROM) is taken through a grade control process to check if the ROM meets the product specifications in respect to the physical properties and gradeMine Planning and Optimisation Techniques Applied in an Iron 2024年3月20日 Ironmaking processes that do not generate greenhouse gas (GHG) emissions are needed for netzeroemissions energy systems 1 Most emissions associated with iron and steel production result from stochiometric quantities of CO 2 (∼15 kg CO 2 per kg Fe) produced during reduction of iron oxide ores in blast furnaces 2, 3 Demand for steel is unlikely to Electrochemical chloriron process for iron production from iron oxide Iron oxide dispersants for industrial water systems: types, performance, and selection criteria Z Amjad Department of Chemistry, Division of Mathematics and Sciences, Walsh University, N Canton, Ohio 44270, USA Email: zamjad@walsh Abstract Dispersion of solid particles separating out from fluids is very important for fouling due toIron oxide dispersants for industrial water systems: types,
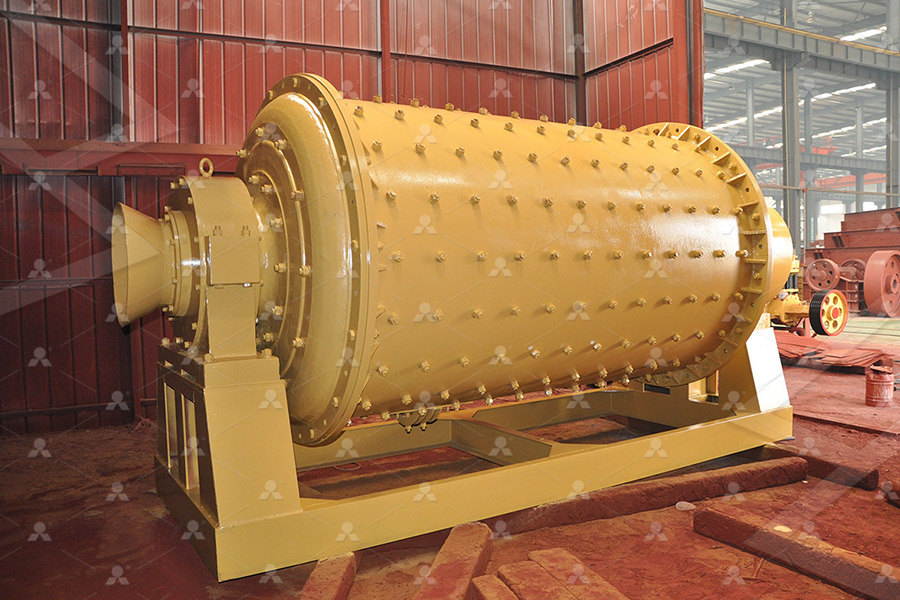
Amino Acids in Iron Oxide Mineralization: (Incomplete) Crystal Phase
2008年7月22日 The synthesis of an aqueous suspension of aminoacidadsorbed magnetic ironoxide nanoparticles can be conducted in a twostep process with the synthesis of the nanoparticles in the first step and 2022年11月7日 This work aims at investigating the kinetic mechanisms of the reduction/oxidation (redox) reactions of iron oxide/iron pellets under different operating conditions(PDF) On the Kinetic Mechanisms of the Reduction and Oxidation 2023年4月7日 Magnetite is the main mineral in iron ore beneficiation, which has industrial value and is mined in large quantities Here we will introduce the beneficiation method and process of magnetite ore in detail What is magnetite? Magnetite is an iron oxide ore, which belongs to the equiaxed crystal system, and its chemical formula is Fe 3 O 4How to Recover Iron from Magnetite: 4 Methods and Stages2023年2月15日 Hematite, also spelled haematite, is a weakly magnetic iron ore with better floatability than magnetite and wide distributionIt is one of the most important raw materials for the extraction of iron Its composition is complex In addition to containing a small amount of magnetite, the impurity embedding of haematite has uneven particle size and high content of How to Extract Iron from Hematite: Methods and Plants
.jpg)
Kinetics of Monodisperse Iron Oxide Nanocrystal Formation by
2007年9月22日 We studied the kinetics of the formation of iron oxide nanocrystals obtained from the solutionphase thermal decomposition of iron−oleate complex via the “heatingup” process To obtain detailed information on the thermal decomposition process and the formation of iron oxide nanocrystals in the solution, we performed a thermogravimetricmass spectrometric analysis 2020年11月1日 Applications involving iron oxide nanoparticles (IONPs) Synthesis of highly crystalline and monodisperse maghemite nanocrystallites without a sizeselection process J Am Chem Soc, 123 (2001), pp 1279812801 View in Scopus Google Scholar [24] Coprecipitation synthesis of stable iron oxide nanoparticles with 2015年4月8日 Low temperature electrochemical reduction of iron(III) oxide to iron in a strongly alkaline solution has been systematically investigated in this article The facile electrochemical process was carried out in 50 to 70 wt pct aqueous NaOH solution at 383 K (110 °C) and 17 V The preformed spherical Fe2O3 pellets with porous structures were used directly as Electroreduction of Iron(III) Oxide Pellets to Iron in Alkaline Media 2012年2月13日 modeling of thermal conductivity for de nse iron oxide and porous iron ore agglomerates in stepwise reduction ISIJ International, vol 32, No 7, (July, 1992),(PDF) Modeling Sintering Process of Iron Ore
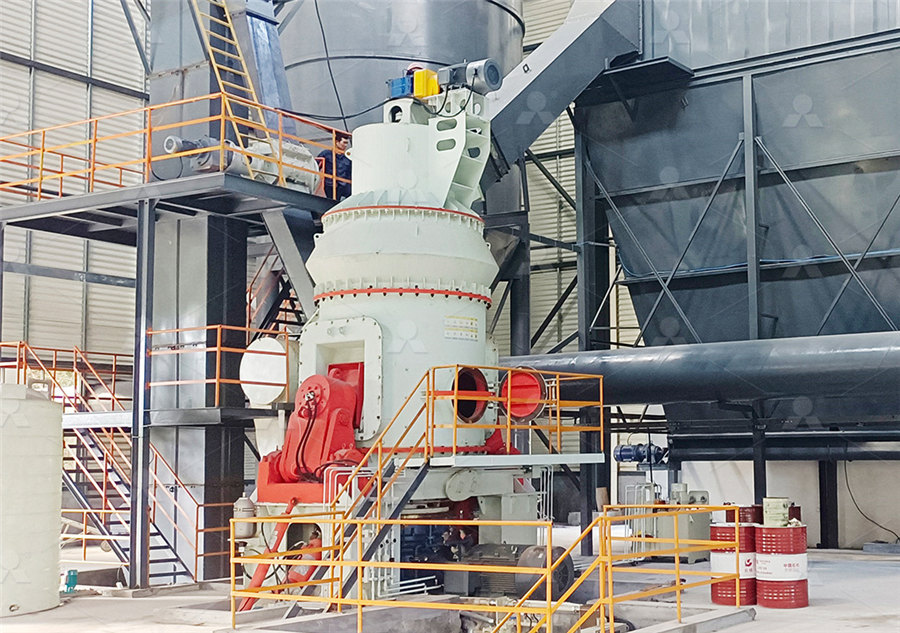
Introduction of Iron Oxide Red Production Process Chemate
The yellow iron oxide prepared by the wet method is washed with water to remove the watersoluble salt, filtered and dried, then put into the calciner Calcined into iron red at 600℃1000℃, then crushed and packaged to obtain finished products The calcination of iron yellow into iron red is the process of removing the crystal water from the iron yellowWhen the temperature Download scientific diagram a) Possible pathways to reduce iron (Fe) from iron oxide (Fe 2 O 3 or other oxidation state, commonly termed rust) using carbon, hydrogen or electricity (electrons a) Possible pathways to reduce iron (Fe) from iron oxide (Fe 2 2024年3月20日 The iron and steel industry accounts for ∼8% of global greenhouse gas emissions Electrochemical reduction of iron ore to metal for electric arc furnaces can enable sustainable steel production, but existing electrochemical processes require expensive capital or electrolytes We report a lowtemperature, electrochemical cell that consumes lowcost and Electrochemical chloriron process for iron production from iron oxide 2024年4月1日 The process is performed continuou sl y in three O 2rich sideblown furnaces linked by chutes: oxidation melting desul furization (to produce Pb rich slag), reduction melting (to produce Technology Selection for Slag Zinc Fuming Process ResearchGate
.jpg)
On the Kinetic Mechanisms of the Reduction and Oxidation
2022年11月7日 This work aims at investigating the kinetic mechanisms of the reduction/oxidation (redox) reactions of iron oxide/iron pellets under different operating conditions The reaction principle is the basis of a thermochemical hydrogen storage system To simulate the charging phase, a single pellet consisting of iron oxide (90% Fe2O3, 10% stabilising cement) The iron ore production has significantly expanded in recent years, owing to increasing steel demands in developing countries However, the content of iron in ore deposits has deteriorated and lowgrade iron ore has been processed The fines resulting from the concentration process must be agglomerated for use in iron and steelmaking This chapter shows the status of the Iron Ore Pelletizing Process: An Overview IntechOpenIn general, the reduction of Fe 2 O 3, called hematite, does not occur directly to metallic iron, FeIf the reduction temperature is lower than 570 °C, reduction to Fe occurs stepwise from Fe 2 O 3 to Fe 3 O 4, called magnetite, and continues to FeThe intermediate oxide, wüstite Fe (1−x) O, is not stable at temperatures lower than 570 °C At reduction temperatures higher than 570 °C Reduction of Iron Oxides with Hydrogen—A Review2022年8月29日 Pure and doped iron oxide and hydroxide nanoparticles are highly potential materials for biological, environment, energy and other technological applications On demand of the applications, single phase as well as multiple phase of different polymorphs or composites of iron oxides with compatible materials for example, zeolite, SiO2, or Au are prepared The Mössbauer spectroscopic investigations on iron oxides and