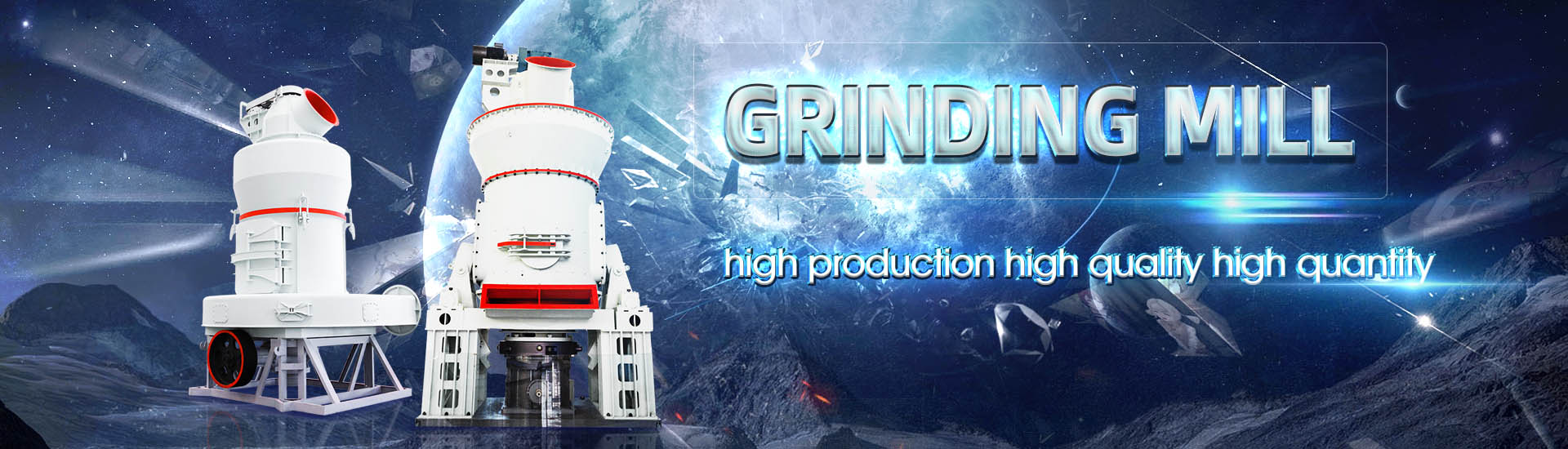
Optimization of calcite ore crushing and grinding process in a powder processing plant
.jpg)
An Optimization of Calcite Grinding Using the Taguchi Method
2010年1月6日 The purpose of this study is to demostrate how the application of Taguchi method can be used to develop an effective optimization process for calcite grinding In order to observe the influencing degree of contol factors in dry calcite grinding, three control factors namely mill This study focused on ultrafine grinding of calcite powder (CaCO 3) using a vertical stirred ball mill The influences of various operating parameters such as stirrer speed (rpm), ball filling Optimization of Wet Grinding Parameters of Calcite Ore in Stirred This study focused on ultrafine grinding of calcite powder (CaCO3) using a vertical stirred ball mill The influences of various operating parameters such as stirrer speed (rpm), ball filling [PDF] Optimization of Wet Grinding Parameters of Calcite Ore in 2018年9月30日 This study focused on ultrafine grinding of calcite powder (CaCO3) using a vertical stirred ball mill The influences of various operating parameters such as stirrer speed Optimization of Wet Grinding Parameters of Calcite Ore in Stirred
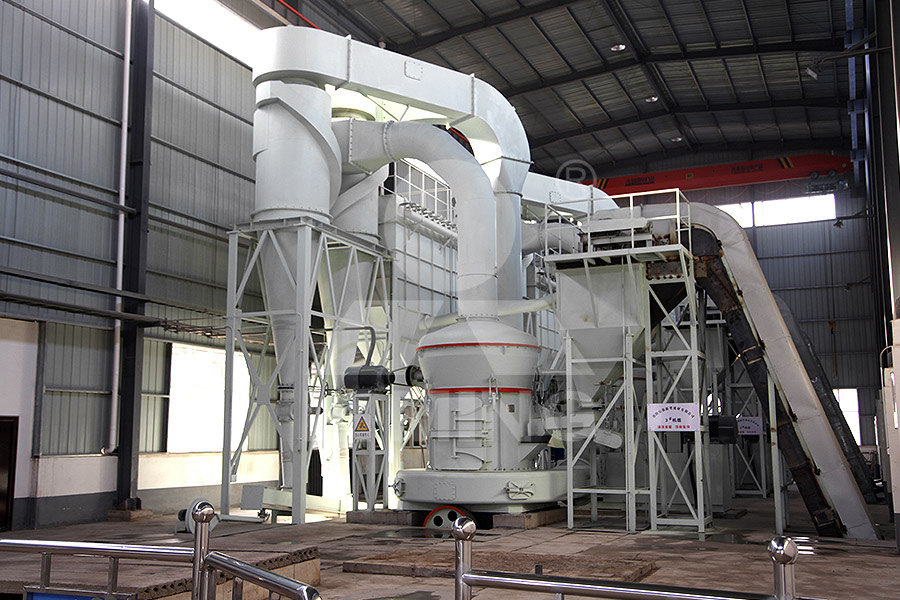
Optimization of Operating Parameters on Dry Grinding of Calcite
In this research, a three‐level Box‐Behnken design was used for the purpose of examining the impact of four independent factors—stirrer speed, grinding time, media filling ratio, and solid 2023年9月28日 On this basis, a multiobjective optimization model is established to maximize the useful power of the grinding circuit to improve the throughput of the grinding operation and MultiObjective Optimization for an Industrial Grinding and 2022年4月26日 An adaptation of the ISO 22400 standard for the aggregates production process is performed and applied in dynamic simulations of crushing plants A detailed optimization (PDF) Optimization Capabilities for Crushing Plants ResearchGateBased on the actual conditions during industrial production, this paper proposes an improvement method and solution to the typical grinding process model and derives a mathematical model Mineral Crushing and Grinding Circuits: Their Simulation,
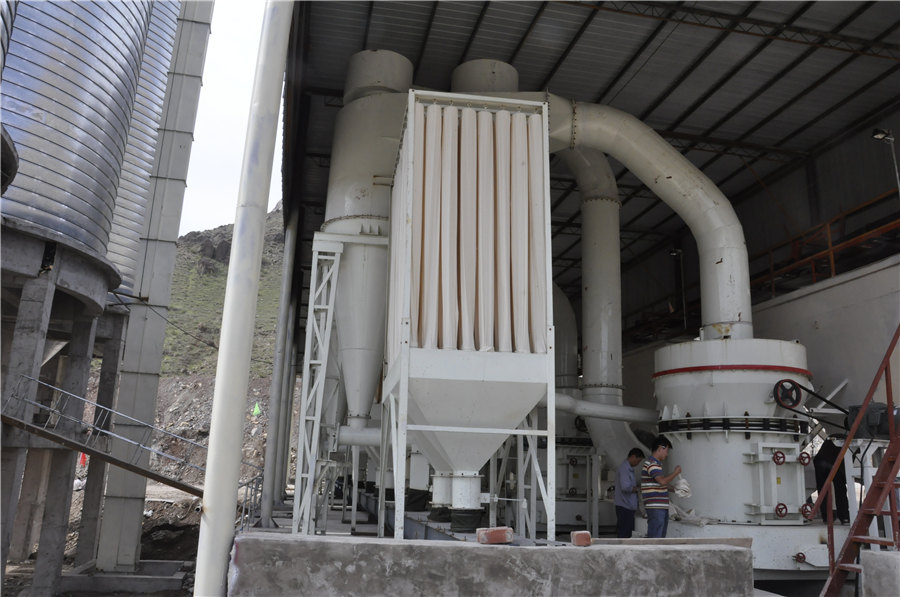
Wet Grindability of Calcite to UltraFine Sizes in Conventional Ball
2015年7月29日 In this study, the effect of wet grinding conditions on the production of fine particles was researched The influence of operating parameters such as operation speed (% 2022年3月1日 Influences of different grinding aids on dry fine grinding of calcite using a laboratorytype ball mill were investigated Tested grinding aids had affected the flowability Analysis of grinding aid performance effects on dry fine milling of 2018年12月31日 This paper presents an application of realtime optimization (RTO) to a simulated ore grinding plant The control and optimization methods are based on a dynamic linear model of the processINVESTIGATION AND OPTIMIZATION OF A CLOSED CIRCUIT CRUSHING mineral processing, art of treating crude ores and mineral products in order to separate the valuable minerals from the waste rock, or gangue It is the first process that most ores undergo after mining in order to provide a more Mineral processing Metallurgy, Crushing
.jpg)
(PDF) The Effects of Blasting on Crushing and
2003年1月1日 The impact of dynamic forces in rockblast fragmentation process has been the subject of investigation for years Nevertheless, while the influence of the macrofragmentation in downstream performance measuring system can be useful for process optimization and process improvements for industrial applications Keywords: Modelling, Dynamic Simulations, Comminution, Crushing, Classification, Screening, Minerals Processing, MultiDisciplinary Optimization (MDO), Multi Optimization Framework for Crushing Plants Chalmers2022年1月23日 Chemical Processing of Bauxite: Alumina and Silica Minerals—Chemistry, Kinetics and Reactor Design(PDF) Chemical Processing of Bauxite: Alumina and Silica Minerals 2014年1月1日 To achieve optimal performance of a crushing plant, not only the design of the individual machines but also the cost of running them should be taken into accountIn this paper a novel method for Factors affecting the performance of crushing plant operations
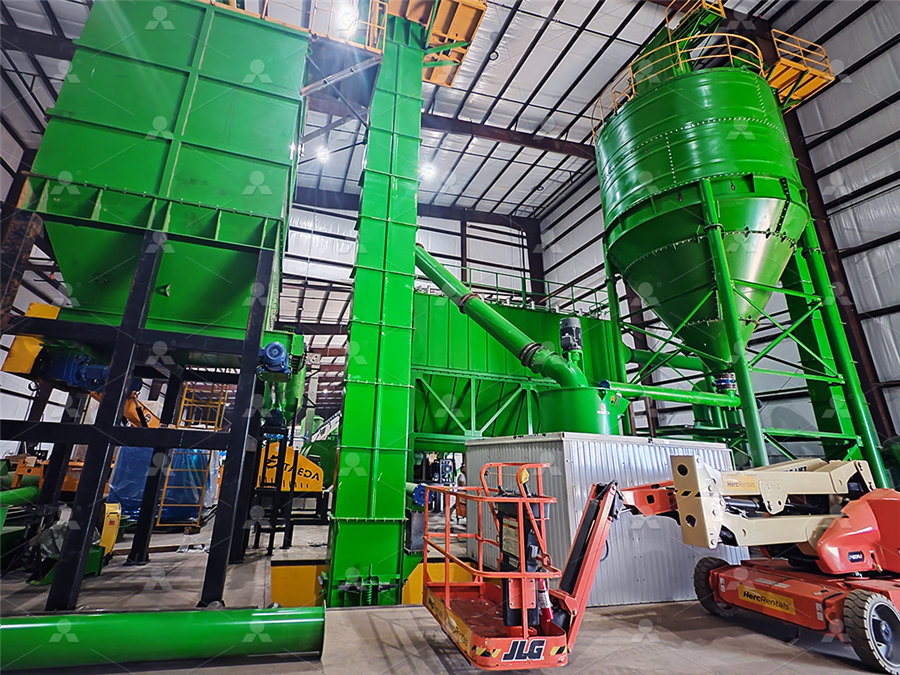
Crushing Plant Design and Layout Considerations 911 Metallurgist
crushing plant’s structure and enclosure can represent the largest single cost element in a primary crushing plant, it is imperative to optimize these structural and construction costs to suit the life of the operation Perhaps a steelsupported, modular design will be best for shortterm operations,Çukurova Üniversitesi Mühendislik Mimarlık Fakültesi Dergisi, 33(3), ss 225236, Eylül 2018 Çukurova University Journal of the Faculty of Engineering and Architecture, 33(3), pp 225236, September 2018 ÇÜ Müh Mim Fak Dergisi, 33(3), Eylül 2018 225 Optimization of Wet Grinding Parameters of Calcite Ore in StirredOptimization of Wet Grinding Parameters of Calcite Ore in The processing flow for products below 400 mesh is like: raw orecrushinggrindingclassifying The purpose of crushing and grading is to produce a product that meets the fineness requirements of the application field There are two kinds of superfine pulverization processes for calcite worldwide: dry method and wet methodcalcite grinding machine, calcite grinding mill, calcite processing plant2016年1月17日 In mineral processing, the reduction of minerals by crushing and grinding may be regarded as having one or other of two main objectives: the attainment of a size appropriate for the direct industrial application of the mineral, eg barytes, sand, aggregate; or the release of metallic or ore inclusions from an unwanted matrix with a view to maximum separationCrushing Mineral Processing 911Metallurgist
-2.jpg)
(PDF) Feasibility and necessity of mine to mill
2021年4月19日 Regarding this background, this article describes the feasibility of mine to mill optimization from three aspects: (1) different energy efficiencies between drillingblasting and crushinggrinding Grinding is the process of reducing the particle size, which plays an important role in mining, construction, metallurgy, chemical, coal and other basic industries [1–3] In terms of Optimization of Polymetallic Complex Ores ResearchGate2016年3月11日 In the crushing section, the ore as it comes from the mine is broken down dry to a size suitable for the wet grinding machines ; these can, if necessary, be 911 Metallurgist is a trusted resource for practical insights, Crushing Plant Flowsheet DesignLayoutThe grinding experiments were realized as a batch process with calcite specimens received from the grinding tank in a detected grinding‐time interval All of the media and calcite specimens wereOptimization of Operating Parameters on Dry Grinding of Calcite
.jpg)
Mineral Crushing and Grinding Circuits: Their Simulation,
Semantic Scholar extracted view of "Mineral Crushing and Grinding Circuits: Their Simulation, Optimisation, and fuzzysimilarity rough sets is proposed for product quality estimation and has been successfully applied in a large grinding plant in China Expand 48 Highly Influenced 4 Excerpts; Grinding process within vertical roller 2020年4月1日 On the other hand, since most plants are optimized for a specific size fraction (≥ 75 µm) and the tailings of chromite plants are generally characterized by fine particles, a recurring problem Process optimization of a chrome ore gravity concentration plant 2022年10月4日 21 Energy Rock drilling, blasting, and comminution (crushing and grinding) consume a vast amount of energy in hard rock mines As mentioned in Sect 1, statistics from hard rock mines indicates that drilling and blasting consumes 2% and comminution does 53% of the total energy input in the whole production chain from mining to mineral processing (Spathis Reduction of Fragment Size from Mining to Mineral Processing: A 2002年1月28日 Mono dispersed SiC powder having particle size of ∼225 nm has been obtained by crushing, grinding and milling of thus formed biomorphic SiC body A grinding limit is reported for the first time Changes of Surface and Volume Properties of Calcite
.jpg)
Efficient Modeling and Control of Crushing Processes in Minerals Processing
2019年12月10日 crushing process is fast in many cases and to accurately describe the process fast dynamic behavior needs to be resolved RQ3: How can a minerals processing plant’s degree of robustness be studied?2017年3月4日 The first process that most of the ores or minerals undergo after they leave any mine, is mineral processing or mineral/ ore dressing It is a process of ore preparation, milling, and ore dressing SIZE REDUCTION BY CRUSHING METHODS ResearchGate2008年11月1日 Computer simulation and mineral modeling was applied to the optimization of a grinding circuit in a plant processing 256 t/h magnetite, and a throughput increment of 100% was achieved with an important reduction in the energy consumption Computer simulation and mineral modeling was applied to the optimization of a grinding circuit in a plant processing 256 Optimization of a grinding and classification circuit of a characterization studies of different chromite ores, and (iii) optimization of the grinding circuit The schematic process flow sheet of the COB plant grinding circuit is shown in Figure 1 The ball mill is in closed circuit with a highfrequency screen, which has an aperture of 1 mm The specifications of the ball mill are given in Table IPerformance optimization of an industrial ball mill for chromite processing
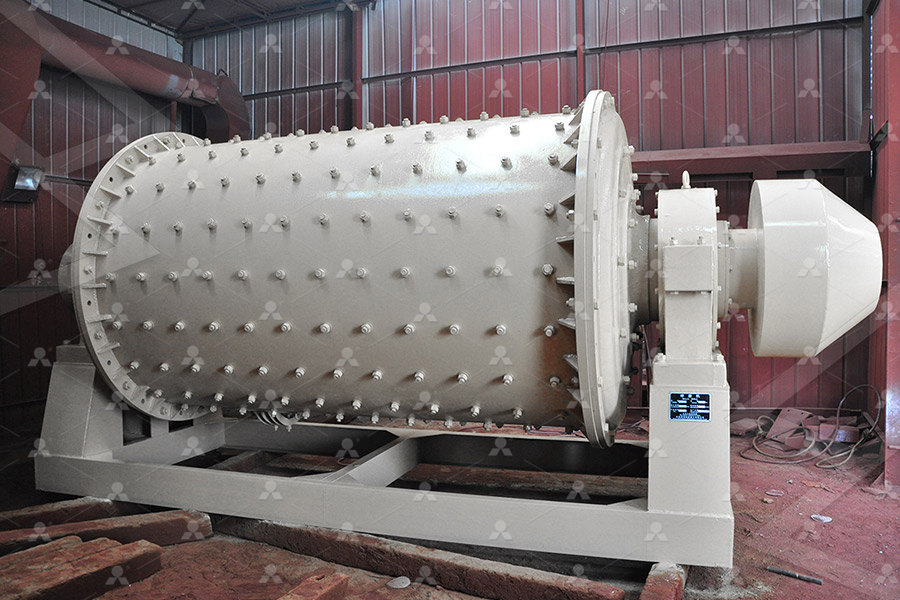
Crushing, Grinding and Concentration of the Ore
2023年7月3日 (1) Crushing and Grinding of the Ore The ores occur in nature as huge lumps They are broken to small pieces with the help of crushers or grinders These pieces are then reduced to fine powder with the help of a ball 4 天之前 A single sulfide ore is usually treated by flotation process, using crushinggrindingclassificationflotationconcentration process to select a single copper sulfide ore as copper concentrate Copper ore beneficiation process The principle of priority flotation process is: crushing and screening→grinding and classification→priority flotation of copper Copper Ore Processing Plants, Flow And Equipment2020年12月4日 Subjecting the aggregate to the grinding process results in an improvement in the crushing strength indicator, thus obtaining better strength parameters of the products manufactured from the Blastingcrushinggrinding: Optimisation of an ResearchGate2022年10月26日 The particle size composition of grinding products will significantly affect the technical and economic indexes of subsequent separation operations The polymetallic complex ores from Tongkeng and Gaofeng are selected as the research object in this paper Through the JK dropweight test, the batch grinding test, and the populationbalance kinetic model of Research on Grinding Characteristics and Comparison of Particle
.jpg)
Process optimization of a chrome ore gravity concentration plant
Process optimization of a chrome ore gravity concentration plant for sustainable development A conventional chromite ore beneficiation process plant (Figure 3) consist of two crushing (jaw and cone crushers) followed by twostage grinding (rod mill and ball mill), followed by a combination of drum, cone, and highgradient 2024年8月7日 After crushing, grinding refines ore into a fine powder to liberate valuable minerals Key types include Ball Mills , which grind ore using steel balls in a rotating cylinder; Rod Mills, which use long rods for a coarser grind; and SAG Mills, which combine crushing and grinding for efficient processing of large volumes of hard materialsMineral Processing Equipment for Mining Industry2022年10月13日 Grinding plays an important role in mining, construction, metallurgy, chemical, coal and other basic industries In terms of beneficiation, grinding is the most energy consuming operation So, reasonable grinding conditions according to the properties of ores is the key to obtain good grinding results and reduce energy consumption and resource waste In this Research on Grinding Law and Grinding Parameters Optimization 2019年2月25日 grinding time of cassiterite is 4 min and the grinding time of sulfide ore is 8 min, the grinding qualified size range index under unit energy consumption is the largest Cassiterite is brittleGrinding Optimization of CassiteritePolymetallic Sulfide Ore

Modeling and Improving the Efficiency of Crushing
2023年6月30日 optimization in the modeling of mineral processing, namely the crushing and grinding processes, has been investigated, and the effectiveness proven [ 26 ] The automation of any technological 2022年10月4日 The worldwide mining industry consumes a vast amount of energy in reduction of fragment size from mining to mineral processing with an extremely lowenergy efciency, particularly in ore crushing (PDF) Reduction of Fragment Size from Mining to Macraes Process Plant Block Diagram Each of the ore sources may contain different geological domains and mineralogies This material, if not blended well can introduce cyclic variations throughout the processing plant impacting on sampling precision, recoveries and production rate due to different hardness and mineralogical characteristicsOptimisation of metallurgical plant sampling procedures at the Semantic Scholar extracted view of "Crushing and grinding : the use of olive pomace oil as a grinding aid was investigated in the grinding of calcite to dry micronized sizes in a laboratory scale stirred ball mill For this purpose, Breakage process of Crushing and grinding : the size reduction of solid materials
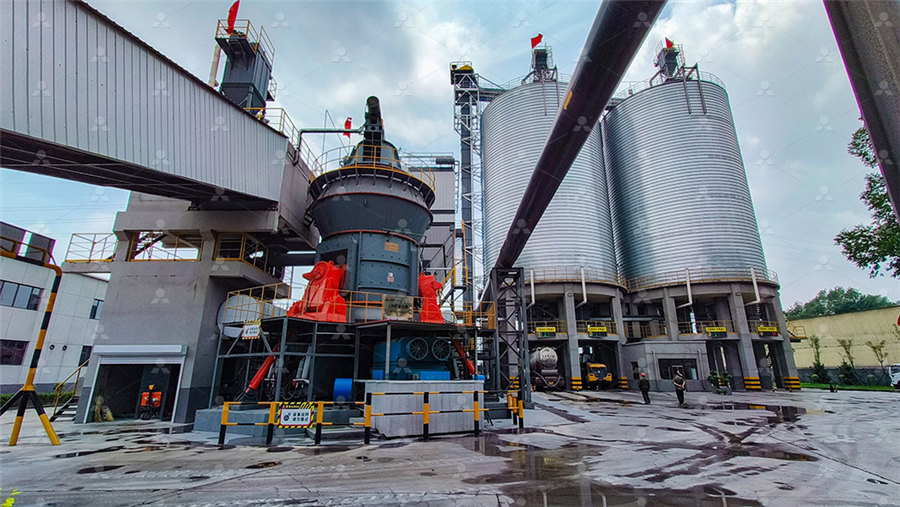
Overview of Mineral Processing Methods ResearchGate
2015年8月3日 The first process that most of the ores or minerals undergo after they leave any mine, is mineral processing or mineral/ ore dressing It is a process of ore preparation, milling, and ore dressing for an integrated mineral processing plant was not explored suciently Same is the case for plantwide optimization Optimization of individual grinding and otation units has been studied extensively using mathematical models in the past [35–38] However, optimization of an integrated mineral processing plant was not studied wellArtificial Intelligence for Monitoring and Optimization of an of a parallel crushing process made up with highpressure grinding rolls (HPGR) machines The aim is to reduce both energy consumption and cost through optimal control of the process and load shifting, respectively A case study of a copper crushing process is solved under three scenarios in order to evaluate the e ectiveness of the developed Systems optimization model for energy management of a parallel 2016年7月12日 The ores are composed of andesite, quartz, breccia, calcite, and kaolinized material which forms a sticky gangue that can be put through an ordinary crushing plant only with great difficulty The capacity of the mill operating on a 12in feed and crushing through a 1in punched plate was 20 tons per hour, and power consumption about 3 kwhr per ton of oreCrushing Screening Plant 911Metallurgist
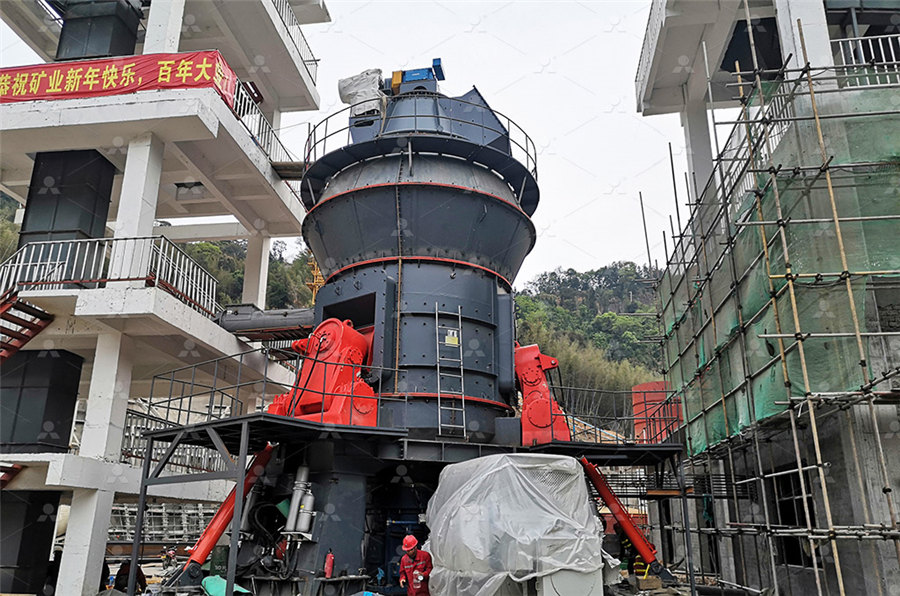
Physical Bauxite Processing: Crushing and Grinding of Bauxite
2022年1月23日 Additionally, when the downstream process involved grinding mills, the fines created from highspeed crushing circuit were a benefit to the comminution process In general, if the feed material, application parameters, and downstream process match with the capabilities of a highspeed impact style crusher, this is the crusher type to useGenerally, mineral processing begins when an ore is delivered from a mine, to a processing facility At this point, the ore is called runofmine material because there has been no treatment performed on it There are three primary types of runofmine materials: Runofmine consisting of useful materialsIntroduction to Mineral Processing or Beneficiation