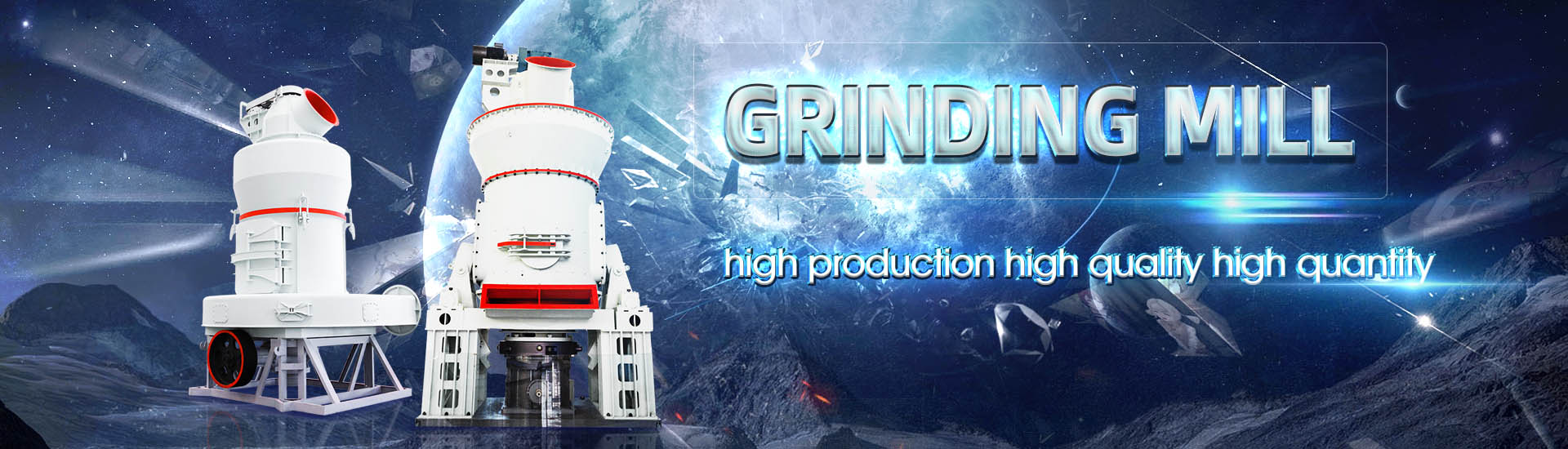
Desulfurization slag treatment process
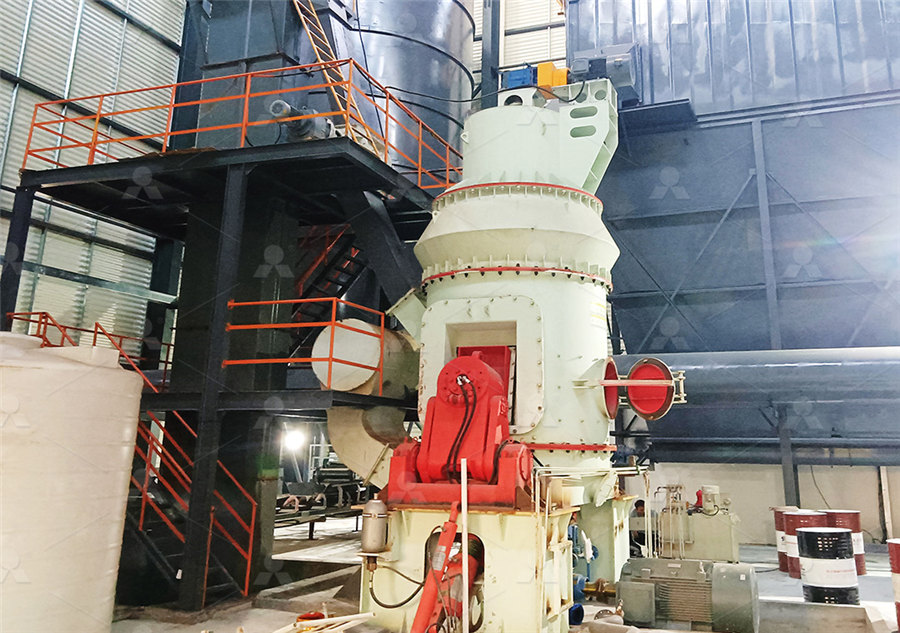
Optimal hot metal desulphurisation slag considering
2021年2月21日 The aim of this study is to find the optimal slag for the HMD process, which is defined as a slag with an optimal balance between 2022年5月1日 In order to make the slag from desulphurization and slag skimming (SDSS) to be comprehensively recycled and utilized, a combined process of beneficiation and building Resource utilization of slag from desulphurization and slag 2022年12月1日 In this paper, we propose a technique to break the lumping of iron desulfurization slag using a hightemperature converter slag The technique has zero energy Numerical study on the mixing process of hot desulfurization slag 2021年8月12日 Slag engineering was done in a novel way to make conditions more conducive for desulphurisation of steels Deoxidation and flux addition practice was modified in an (PDF) An Innovative Slag Engineering Approach for Improving De
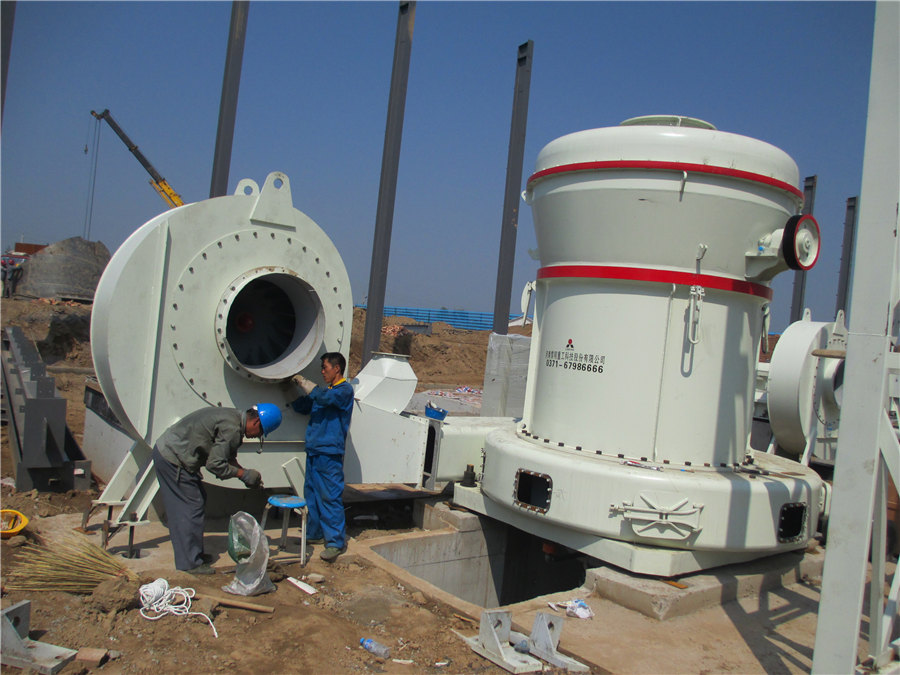
Deep Steel Desulfurization Practice Transactions of the Indian
2022年6月24日 At the beginning of the secondary metallurgy process, it was crucial to prepare a suitable chemical composition of ladle slag with advantageous properties for good assimilation 2022年12月1日 Desulfurization slag (DS), generated from molten iron predesulfurization process, has a high alkalinity that may cause seriously environmental issues To solve the DS Application of molten iron desulfurization slag to replace steel slag The kinetics of carbide slag desulfurization process conforms to pseudorstorder kinetics, and the sulfur content of calcium carbide slag reaches to 1000 mgSO 2Desulphurization mechanism and engineering practice of carbide 2002年6月1日 Within several cooperative projects, KTH (Royal Institute of Technology), Ovako Steel AB, and MEFOS have investigated the desulphurisation of bearing steel during vacuum [PDF] Slagmetal reactions during ladle treatment with focus on
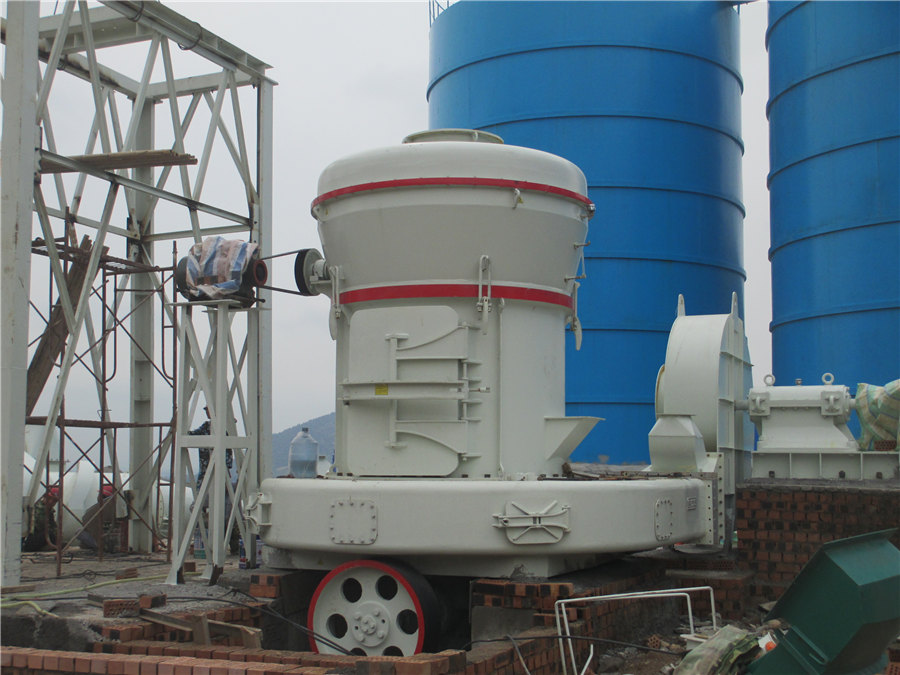
A Review of Modeling Hot Metal Desulfurization
Hot metal desulfurization serves as the main unit process for removing sulfur in blastfurnace based steelmaking The available body of literature on modeling hot metal desulfurization is reviewed to provide an indepth analysis of the 2023年11月21日 High sulfur content in hot metal desulfurization slag is one of the major barriers for recycling of the slag in the ironmaking and steelmaking process How to effectively remove sulfur from the hot metal desulfurization slag is a crucial step for improving its recyclability Thermodynamic analysis shows that CO2 is a better oxidation gas for sulfur removal from the Treatment of Hot Metal Desulfurization Slag With CO2014年5月12日 AbstractKambara reactor desulfurization slag (KR slag) is a solid waste generated from the desulfurization process of molten iron by a KR mechanical stirring process in a steel factory (AMD) treatment process as a replacement of lime due to its high CaO contentPotential Reuse of Slag from the Kambara Reactor Desulfurization Dry desulfurization can be mainly divided into source control technology and end treatment technology from the process segment Compared to the traditional wet/semidry desulfurization process, dry desulfurization has the characteristics of simple operation and low equipment investment, which has recently been widely used in industryRecent advances in process and materials for dry desulfurization
.jpg)
Summary of research progress on industrial flue gas desulfurization
2022年1月15日 The desulfurization process was a process controlled by the gas film Various factors had little effect on the desulfurization effect, and the removal rate was almost 100% [167] Y Jia et al established a mathematical model of the total sulfite oxidation process of ammonium sulfite and ammonium bisulfite in the ammonia desulfurization process1 Introduction Hot metal desulfurization serves as the main unit process for removing sulfur in blastfurnacebased steelmaking Hot metal desulfurization is commonly conducted in a ladle or a torpedo car, 1 using a desulfurization reagent that is either injected into the metal bath or added on top of it 2 From the thermodynamic point of view, the fundamental requirement for the A Review of Modeling Hot Metal Desulfurization Visuri 年7月11日 Desulfurization techniques process and future challenges for commercial of crude oil much of the recent work focuses on creatin g an efficient biocatalyst for the treatment of vast quantities (PDF) Desulfurization techniques process and future challenges 2013年4月1日 It is expected that existing hot metal ladle pretreatment processes can deliver the required sulphur reduction, but that a process providing improved kinetics, such as the Kanbara Reactor process Desulfurization strategies in oxygen steelmaking ResearchGate
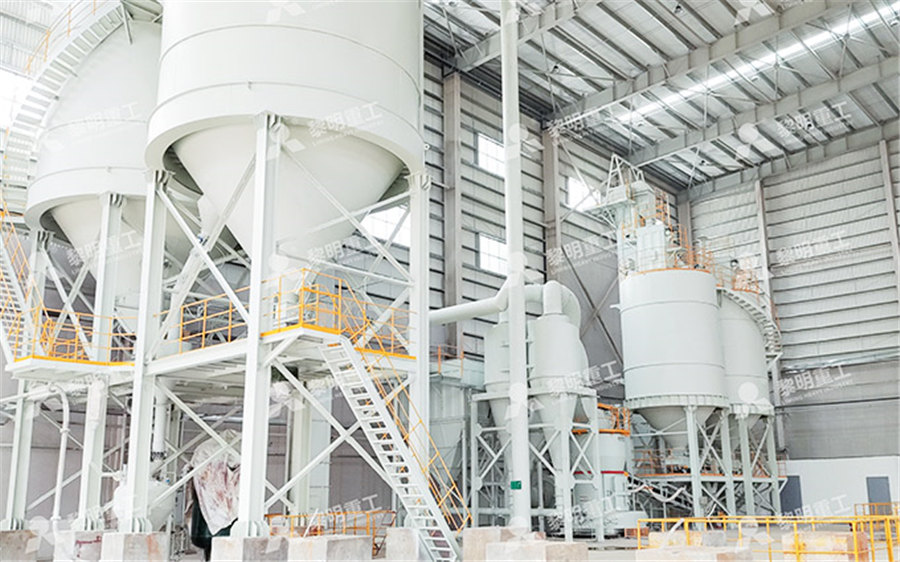
Desulphurization of Steel Metal World Insight
2021年4月7日 Removal of sulphur takes place by two methods: 1use of basic slag and 2 injection of active agents 1Basic slag for desulphurisation Desulphurization using basic slag can be brought about by two mechanism: 1 Reaction takes place between basic synthetic or refining slag (which is added to the empty ladle) and the liquid steel being tapped2023年10月31日 Kinetic characteristics of desulfurization reactions can be described by the twofilm theory In the kinetic process of desulfurizer desulfurization, the kinetic process can be divided into (1) The movement of [S] from the molten steel through the boundary layer on the molten steel side to the slag–steel interface; (2) (O 2−) in the slag moves from the top slag through the Kinetic Model of Desulfurization During RH Refining Process2002年6月1日 Within several cooperative projects, KTH (Royal Institute of Technology), Ovako Steel AB, and MEFOS have investigated the desulphurisation of bearing steel during vacuum degassing The work includes thermodynamic calculations of the slagmetal equilibrium, CFD modelling of slagmetal reactions, and plant trials Results from the various studies are [PDF] Slagmetal reactions during ladle treatment with focus on 2022年12月1日 Molten iron desulfurization slag (DS) is the tail slag produced in the predesulfurization process of molten iron Molten iron desulfurization produces approximately 7–9 kg/t of DS (Zhang and AnJun 2009)The main components of DS are Ca(OH) 2, CaSO 4, CaF 2, CaCO 3, CaS, and Ca 2 SiO 4 (Tong et al, 2016)With a pH above 125, DS is almost Application of molten iron desulfurization slag to replace steel slag
.jpg)
The Research Progress of Steel Slag Utilization and Stabilization
2024年10月10日 Steel slag is a byproduct of steelmaking process The producing of steel slag in China is proximately 100 million tons, but the utilization ratio of comprehensive resources is the lower This paper described the production and composition characteristics of steel slag, reviewed current situation and progress of resource utilization and stabilization of steel slag Steel slag 2024年1月10日 Flue gas desulfurization (FGD) is a critical process for reducing sulfur dioxide (SO2) emissions from industrial sources, particularly power plants This research uses calcium silicate absorbent Modeling based on machine learning to investigate flue gas AbstractKambara reactor desulfurization slag (KR slag) is a solid waste generated from the desulfurization process of molten iron by a KR mechanical stirring process in a steel factory Most of the KR slag is sent to landfills or stored onsite The KR slag may be potentially used in an acidic mine drainage (AMD) treatment process as a replacement of lime due to its high CaO Potential Reuse of Slag from the Kambara Reactor Desulfurization Treatment of Hot Metal Desulfurization Slag With CO 2 Gas in the Temperature Range of 873 K to 1473 K for Better Recycling of the Slag from solid slag was a slow process and independent of temperature, but the removal rate was significantly increased when Treatment of Hot Metal Desulfurization Slag With CO2 Gas in
.jpg)
Recent research progress on recycling metallurgical waste slag
2024年11月1日 In section 4, the law of P and S recovery in the electric field strengthened waste slag recycling process is proposed and analyzed Finally, a novel concept for the future application of electric field strengthening waste slag treatment in iron and steel enterprises is proposed and analyzed2023年11月15日 With the increasing demand for energy conservation and emission reduction, more attentions have been paid to the intelligentization, greenization and low carbonization during the transformation and upgrading of steelmaking plants Ladle furnace (LF) refining is one of the key procedures in steelmaking process and has been widely used in steelmaking plants for its Modeling of LF refining process: a review Journal of Iron and 2024年4月1日 The desulfurization rate (Ds) of SFGDA is defined by the weight change during heat treatment: (2) D s = (1T S 1 × m 1 T S 0 × m 0) × 100 % where T S0 is the S content in the raw material before calcination, wt%; T S1 is the S content in the raw material after calcination, wt%; D S is the SFGDA desulfurization rate, %; m 0 is the mass of the original mixture, kg; m Resource utilization of semidry flue gas desulfurization ash by As a hot metal desulfurization process, a mechanical stirring method employing a rotating impeller with addition of CaO based flux1) has been adopted in many companies It has been reported that sulfur is distributed only at the surrounding edge of the slag particles in the EPMA mapping image of desulfurization slag after treatment2) In order toEffects of Temperature and Oxygen Potential on Removal of Sulfur
.jpg)
Potential Reuse of Slag from the Kambara Reactor Desulfurization
2014年5月12日 Kambara reactor desulfurization slag (KR slag) is a solid waste generated from the desulfurization process of molten iron by a KR mechanical stirring process in a steel factory Most of the KR 2021年11月1日 Flue gas desulfurized gypsum mainly comes from thermal power plants, smelters, and largeenterprise boilers, and contains industrial byproducts produced through a wet desulfurization combustion process, where SO 2 gas and lime slurry react under strong oxidation conditions The main component of this gypsum is calcium sulfate dihydrate, which also Production and resource utilization of flue gas desulfurized 22 小时之前 Steel rolling sludge, an oilcontaining waste generated during steel production, was difficult to manage Prolonged storage poses significant environmental and health hazards Most steel enterprises in China use steel rolling sludge directly as a raw material for sintering However, its adhesive nature caused poor mixing with other materials, affecting the quality of the sinter Treatment of steel rolling sludge incineration slag via iron ore DOI: 1021203/rs3rs/v1 Corpus ID: ; Study on a New Process and its Kinetics of Iron Recovery and Glassceramics Preparation from Desulfurization Slag @article{Tong2021StudyOA, title={Study on a New Process and its Kinetics of Iron Recovery and Glassceramics Preparation from Desulfurization Slag}, author={Zhibo Tong and Jingjing Sun Study on a New Process and its Kinetics of Iron Recovery and
.jpg)
Desulphurization of Hot Metal IspatGuru
2013年10月16日 Fig 2 Schematic view of Kanbara reactor process for desulphurization Around 1970 a similar process called RheinstahlRuhrer was developed in Germany It was soon abandoned due to the large slag volumes created The KR process is widely used With the KR process, sulphur concentrations below 0001 % (10 ppm) have been reported2023年10月16日 The effect of sulfur enrichment on desulfurization reaction in ladle furnace slagrecycled process could be partially offset mainly by two aspects: the amount of slag increased with increases in Research Progress of Desulfurization Refining Slag: A Review2022年2月4日 Together with desulfurization reactions, a slag rich in sulfides is collected at the top, and it is then skimmed out Other than hot metal treatment stage, further removal of sulfur may be accomplished in secondary steelmaking, depending primarily on suitability of metallurgical conditions in that specific vesselRecent Studies on Hot Metal Desulfurization SpringerLinkHigh Efficiency Hot Metal Desulfurization by Enhancing Flux Dispersion in Mechanical Stirring Process of the slag The average particle diameter of the desulfurization slag after the experiment was 076 mm with batch addition, but in contrast, the average diameter decreased to 039 mm with continuous addition and 038 mm with powder blastingHigh Efficiency Hot Metal Desulfurization by Enhancing Flux
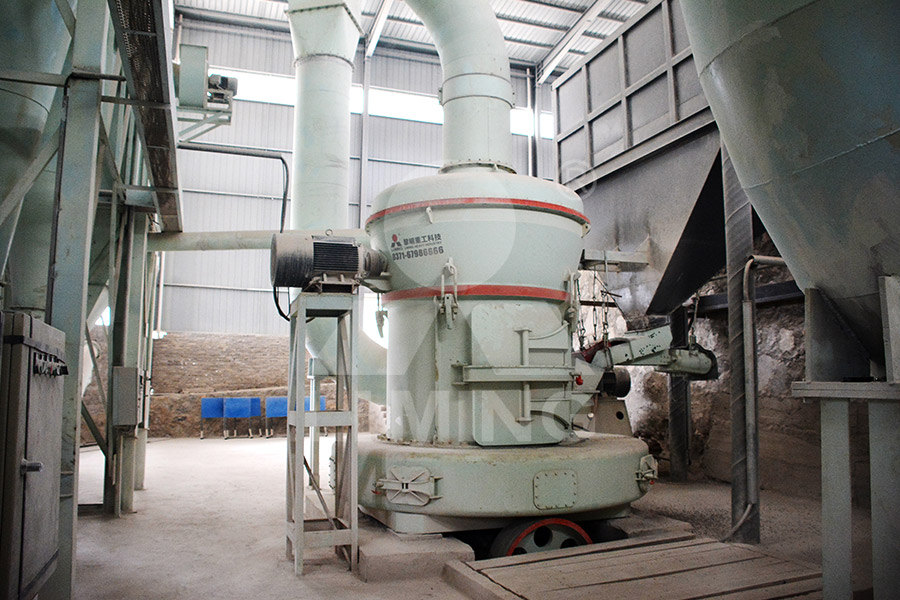
Hot Metal Pretreatment Facility (Kanbara Reactor; KR) Nippon
It is characterized by its acceleration of the desulfurization reaction through the submersion and rotation of an impeller in hot metal, and subsequent mechanical mixing of the hot metal and desulfurizing agent The KR process efficiently advances the desulfurization reaction by means of highspeed (approx 120 rpm) rotation of the impeller2015年9月9日 The desulfurization waste slag from hot metal pretreatment process is a typical solid waste generated in the integrated steel company About 7 to 9kg waste slag is produced per ton hot metal treated in the Kanbara Reactor (KR) desulfurization process, and the waste slag contains approximately 40–60 % CaO and large amounts of iron Therefore, effectively Characterization and Valorization of Kanbara Reactor Desulfurization 2019年12月1日 According to the US Energy Information Administration's statistics, in the 2006–2016 period, approximately 42% of the electricity consumed in the USA was produced by coal combustion (US Energy Information Administration, 2018)The coal combustion process generates various types of residues such as fly ash, bottom ash, boiler slag, flue bed Recent advances in flue gas desulfurization gypsum processes 2017年3月9日 Desulfurization behavior was investigated based on a wide slag composition and working temperature range Moreover, the ratecontrolling step (RCS) for desulfurization with regard to the ladlerefining conditions and the transition of the RCS by changing the slag composition was systematically discussed The desulfurization ratio reached an equilibrium Effect of Slag Chemistry on the Desulfurization Kinetics in Secondary
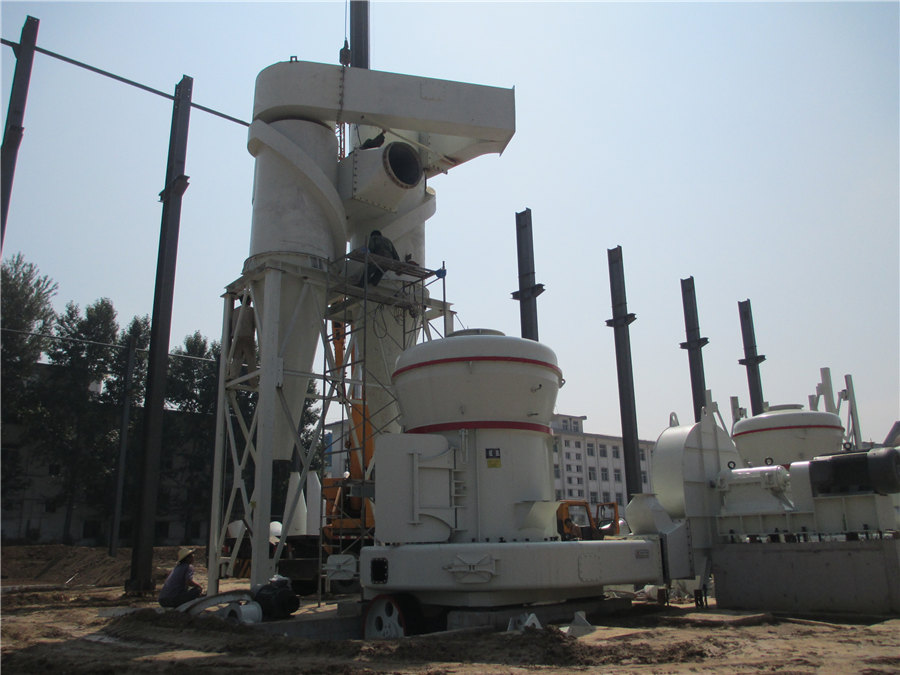
Potential Reuse of Slag from the Kambara Reactor
2014年5月12日 AbstractKambara reactor desulfurization slag (KR slag) is a solid waste generated from the desulfurization process of molten iron by a KR mechanical stirring process in a steel factory (AMD) treatment process as a 2021年2月1日 Compared with limestonebased wet flue gas desulfurization (WFGD), magnesiabased WFGD has many advantages, but it is not popular in China, due to the lack of good wastewater treatment schemesLimestoneGypsum Wet Flue Gas Desulfurization 2015年9月9日 The desulfurization waste slag from hot metal pretreatment process is a typical solid waste generated in the integrated steel company About 7 to 9kg waste slag is produced per ton hot metal Characterization and Valorization of Kanbara Reactor Desulfurization 2018年1月15日 Afterwards, the resulting slag, called desulfurization slag (abbreviated to DeS slag), is discharged as a waste and then transported to treatment facilities Some studies [3], [4] reported that DeS slag is primarily composed of excessive lime and entrapped iron, and the desulfurization products (CaS and Al 2 O 3 ), residual fluorspar, and graphite are also presentRecycling of desulfurization slag for the production of autoclaved
.jpg)
Selfdigestion of CrBearing Vanadium Slag Processing Residue
2022年1月31日 The vanadium slag processing residue (VSPR) is a hazardous waste produced during the vanadium extraction process based on steelmaking process, which contains various toxic and valuable metal elements including chromium, vanadium, and iron To remediate the VSPR and recover the valuable elements, we propose a novel approach for VSPR self 2021年4月1日 Deep desulfurization of transportation fuels such as gasoline, kerosene, jet fuel, and diesel has been of great urgency due to more stringent environmental regulations worldwide Currently, refineries mainly rely on the HDS process for desulfurization The production of ultralow fuels through HDS is expensiveReview on recent advances in adsorptive desulfurization2020年5月16日 Numerous mitigation techniques have been incorporated to capture or remove SO2 with flue gas desulfurization (FGD) being the most common method Regenerative FGD method is advantageous over other methods due to high desulfurization efficiency, sorbent regenerability, and reduction in waste handling The capital costs of regenerative methods are Sulfur dioxide removal: An overview of regenerative flue gas 2022年1月26日 A threedimensional mathematical model was established to predict the multiphase flow, motion and dispersion of desulfurizer particles, and desulfurization of hot metal during the Kanbara reactor (KR) process The turbulent kinetic energy–turbulent dissipation rate ( k–ε ) turbulence model, volumeoffluid multiphase model, discretephase model, and Mathematical simulation of hot metal desulfurization during KR process
.jpg)
Modeling on the Desulfurization of the Molten Steel During RH Process
2024年8月7日 The present study integrated the multiphase flow of molten steel, desulfurizer dispersion, and desulfurization kinetics to explore the impact of injection amount, injection speed, and lance position on desulfurizer injection desulfurization This investigation employed a coupled kε model, Volume of Fraction (VOF) model, Discrete Phase Model (DPM), userdefined scalar