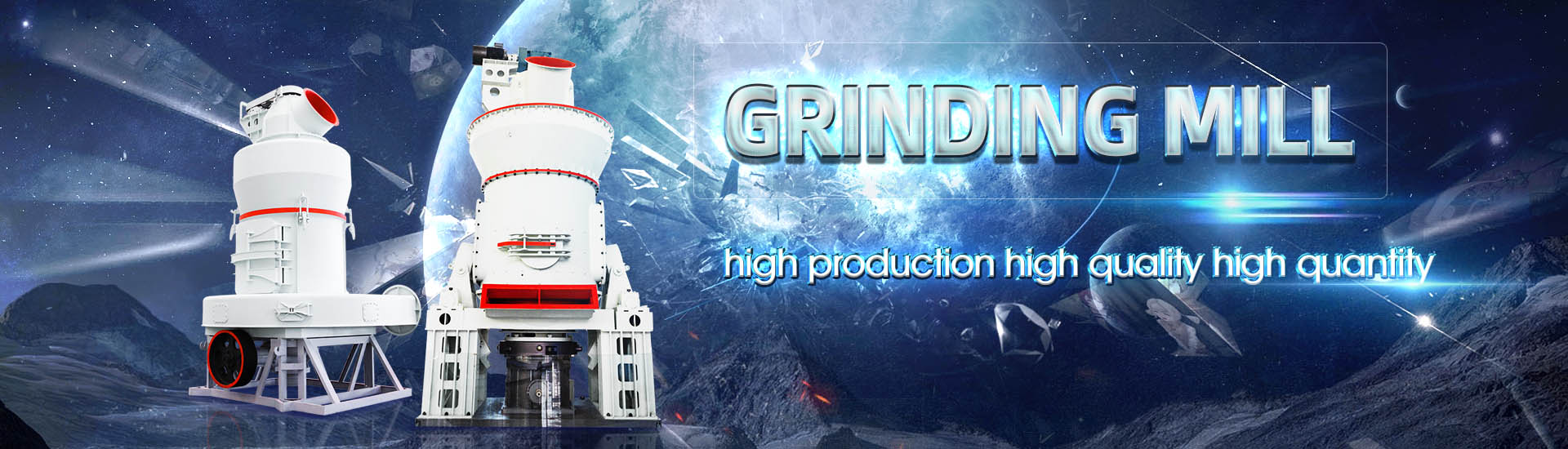
How to increase the hourly output of raw material mill

BALL MILLS Ball mill optimisation Holzinger Consulting
common solution to grind raw materials and cement Roller presses are used mainly in combination with a ball mill for cement grinding applications and as finished product grinding units, as well as raw ingredient grinding equipment in mineral applications This paper will focus on Optimizing the operation of cement mills is essential to maximize productivity, reduce energy consumption, and improve the quality of the final cement product In this article, we will delve into practical strategies for cement mill Cement Mill Optimization: Practical Strategies for the grinding circuit of a raw mill are an increase in output and a reduction in power consumption Expert Optimizer has been successfully applied in more than 90 mills, to optimize milling Industrial : Optimization for the Cement Industry ABB2021年1月29日 High productivity and low power costs can be achieved by increasing output, lowering breakdowns and optimizing the grinding process which eats almost 60% of power costIncrease productivity of vertical roller mill using seven
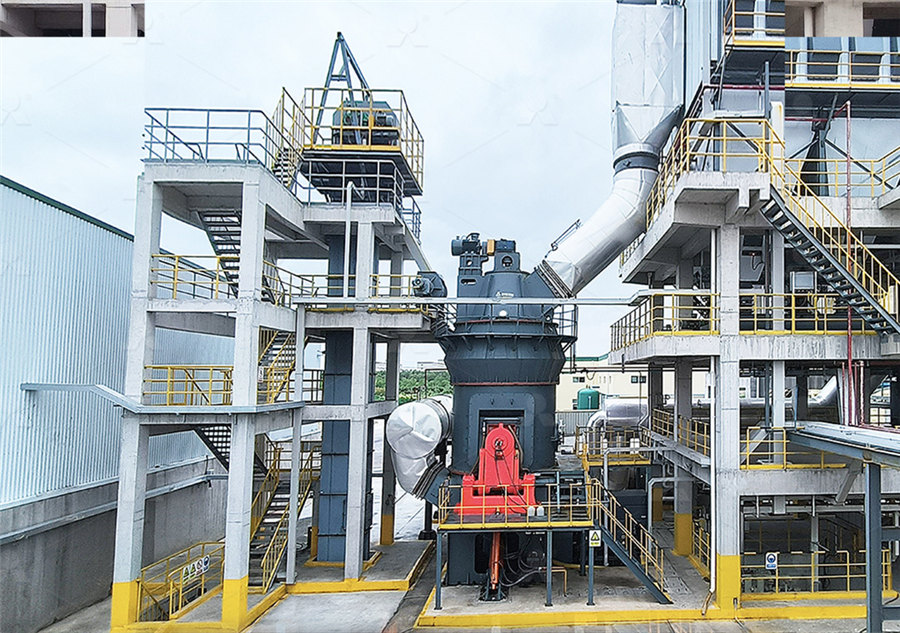
Factors Affecting Ball Mill Grinding Efficiency
2017年10月26日 The following are factors that have been investigated and applied in conventional ball milling in order to maximize grinding efficiency: a) Mill Geometry and Speed – Bond (1954) observed grinding efficiency to be a Drying of moisture in raw materials is required for effective grinding and subsequent handling of raw meal This is achieved normally by ducting part of the kiln exhaust gas through the mill Raw Material DryingGrinding Cement Plant OptimizationOptimization of the Cement Ball Mill Operation Optimization addresses the grinding process, maintenance and product quality The objective is to achieve a more efficient operation and OPTIMIZATION OF CEMENT GRINDING OPERATION IN BALL MILLSGrinding raw materials needs lots of energy Tube mills had been used for grinding, but the energy efficiency level was lower Therefore, the introduction of highly efficient grinding Vertical roller mill for raw Application p rocess materials

Tactics for Optimizing Crusher and Mill Efficiency: A
2023年5月19日 But, through predictive maintenance, you can reduce downtime, increase throughput, improve product quality, help extend the equipment's life and reduce maintenance costs In this article, we will explore several tactics that For a new animal feed mill plant, whether it is a wide variety of raw materials or product varieties, the warehouse area planning of the housetype raw material warehouse and the finished product warehouse can make different kinds of How to build the internal functional area of a new 2021年1月22日 In the whole process of cement production, the electricity consumption of a raw material mill accounts for about 24% of the total Based on the statistics of the electricity consumption of the raw material mill system of 1005 production lines in China between 2014 and 2019, it is found that the average electricity consumption of the raw material preparation A Survey and Analysis on Electricity Consumption of Raw Material Mill 2022年7月24日 Productivity in a spinning mill could be taken as an indication of the mill performance level As the productivity increases, product cost reduces, which in turn raises the standard contribution Productivity of spinning mill is How to Improve Productivity in Spinning Mill Textile
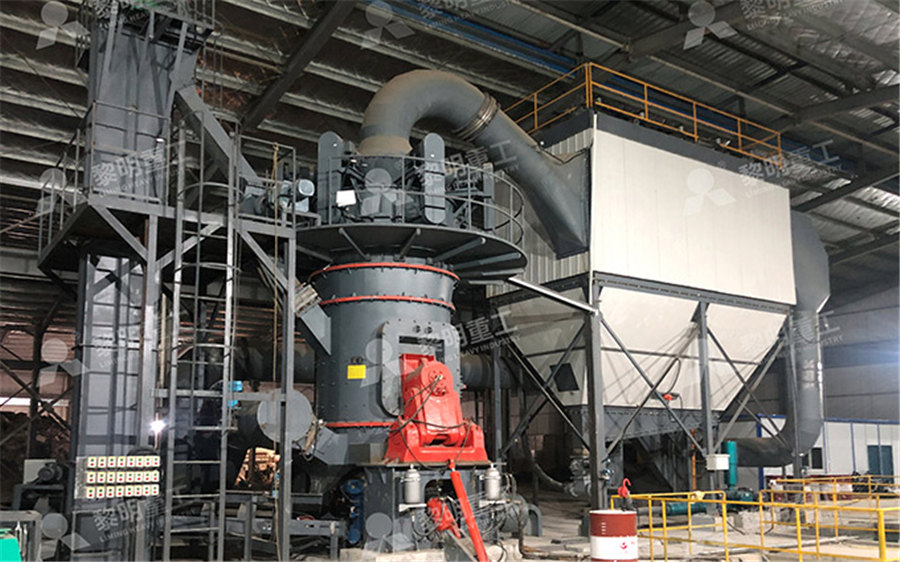
Raw milling and blending INFINITY FOR CEMENT EQUIPMENT
Operationally, roller mills are quite sensitive to changes in parameters Abrasive raw materials such as sand can cause quite rapid wear of grinding surfaces Material is retained on the table using a dam ring at its circumference As the table wears, the depth of material on the tab(e increases and mill power consumption increasesin combination with a ball mill for cement grinding applications and as finished product grinding units, as well as raw ingredient grinding equipment in mineral applications This paper will focus on the ball mill grinding process, its tools and optimisation possibilities (see Figure 1) The ball mill comminution process has a high electricalBALL MILLS Ball mill optimisation Holzinger ConsultingConversely, crushing to smaller output sizes lowers the TPH, reflecting the increased effort and time required to achieve finer material granularity Larger jaw box sizes, such as 20 X 30, exhibit significantly higher TPH values, demonstrating their capacity for greater material handling compared to smaller jaw box sizes like 10 X 16 and 10 X 19Increase Your Material Output: A Guide to Tons per Hour in 2016年3月21日 Pulp Densities Pulp densities indicate by means of a tabulation the percentages of solids (or liquidtosolid ratio) in a sample of pulp This figure is valuable in two ways—directly, because for each unit process and operation in milling the optimum pulp density must be established and maintained, and indirectly, because certain important tonnage calculations are Common Basic Formulas for Mineral Processing Calculations
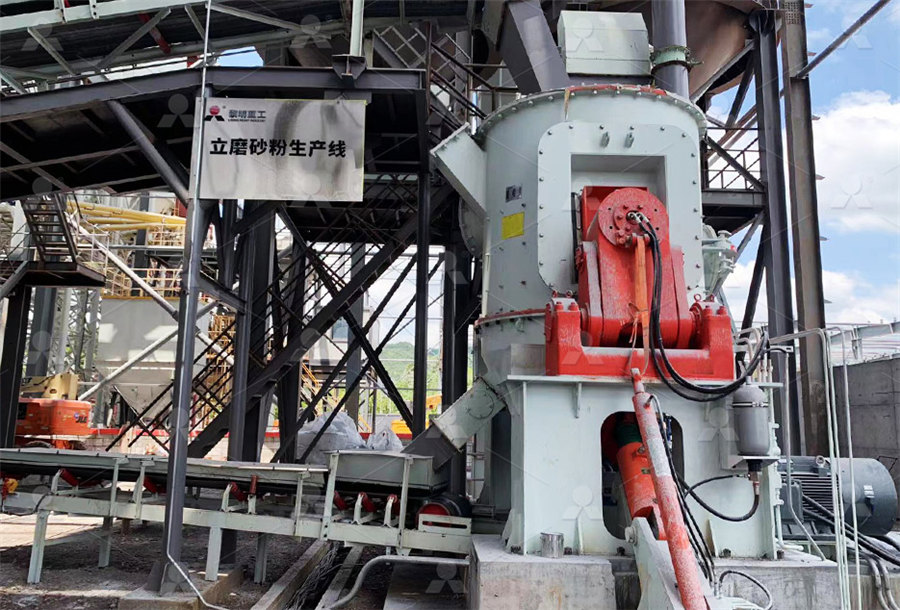
10 Ways to Improve the Grinding Efficiency of Your Ball Mill
2 More crushing and less grinding to reduce the feed size into mill The larger feed size, the more work that the ball mill needs to do on the ore To achieve the specified grinding fineness, the workload of ball mill will be increased inevitably, and then, the energy consumption and power consumption will be increased accordingly2023年4月6日 (1) Strengthen the connection between each section of the rolling mill and adjacent workshops, so that all production works are in accordance with certain production procedures and schedules so that the hot charging rate and hot charging temperature of the raw material charging furnace can be increased (2)What Are the Ways to Increase the Output of the Rolling Mill The cost of the raw material per one piece is given by this formula: In the previous example, assuming 0,7 Euro per kg as the Material cost per kg, and density of steel 7,8 kg/dm3 we obtain: RAW MATERIAL COST = 7 * 5 * 0,01 * 7,8 * 0,7 = 1,91 Euro This procedure has to be repeated with each of the raw materials entering the process4 steps to calculate the manufacturing cost of sheet metal2024年8月8日 In the intricate dance of ball milling, where raw materials are transformed into finely milled particles, the choice of grinding media emerges as a pivotal performance lever This seemingly minor selection can dramatically Ball Mill Success: A StepbyStep Guide to Choosing
.jpg)
Tactics for Optimizing Crusher and Mill Efficiency: A
2023年5月19日 Did you know that 29% of plants spend 5 to 10% of their annual budget on maintenance, and 44% spend more than 40 hours a week performing maintenance? Considering this, crusher and mill efficiency must be one of the 2017年10月26日 The following are factors that have been investigated and applied in conventional ball milling in order to maximize grinding efficiency: a) Mill Geometry and Speed – Bond (1954) observed grinding efficiency to be a Factors Affecting Ball Mill Grinding Efficiency2024年8月30日 Given the steep increase in crude oil prices, the sugar industry has experienced an upswing in the last few years through the realization of better sugar prices A sugar mill is also ecofriendly and offers a renewable source of energy through the generation of power from its coproduct bagasse and alcohol from molassesHow to Start a Sugar Mill Business Cost, Investment, Licenses2010年10月1日 The objective of the present study is to build a reliable model of the dynamics among the chemical modules in the outlet of raw meal grinding systems and the proportion of the raw materials(PDF) Modeling of Raw Material Mixing Process in Raw
.jpg)
Vertical roller mill for raw Application p rocess materials
Production % 100 160~180 60~80(increase) consumption kWh/tRM 20 ~26 1418 About 30 (Reduction) The reduction of power consumption(*) kWh/y 2,240,000 67 2 Item Raw material tube mill Mixed raw materials Pregrinder Coarse powder Coarse powder Product Separ ator 70 5 Item Classification of powder returned2023年5月31日 Definition of a Rolling Mill Generally, a rolling mill refers to a machine used in metalworking works or projects to shape metal materials by passing them through a pair of rolls Similarly, these machines’ main objective is to reduce metal materials’ thickness and redesign them for use in different industrial projects Some of the byproducts produced by rolling A Definitive Guide to Rolling Mills: All You Need to Know Tuolian2010年1月1日 The crushing process in hammer crushers is built in such a way that the interaction between the rotor hammers and the surrounding layer of material in the crushing chamber is possible only when STUDY THE EFFECT OF SOME OPERATIONAL FACTORS ON HAMMER MILL 2016年4月27日 4 Manufacturing processes Productivity improvement also depends on the manufacturing processes In weaving, various manufacturing processes and parameters are done to accomplishing the production such as warping, sizing, looming etcIf these processes are being completed at the right time with shift then the productivity will be increased because of the How to Improve Productivity and Efficiency in Weaving Mill
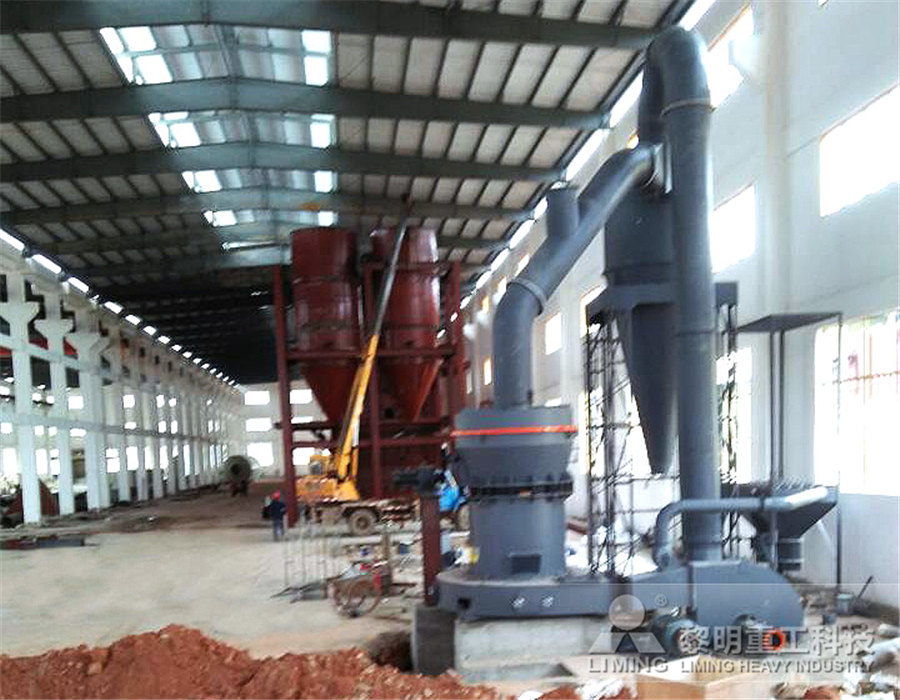
Raw mill Cement Plant
Raw mill is generally called cement raw mill, raw mill in cement plant, it refers to a common type of cement equipment in the cement plantIn the cement manufacturing process, raw mill in cement plant grind cement raw materials into the raw mix, and the raw mix is sent to the cement kiln to make cement clinker, next, clinker and other admixtures will be ground into finished cement by 2024年11月22日 In conclusion, managing a sugar mill involves navigating several complex financial risks, from raw material and energy price volatility to regulatory compliance costs and global market shifts Effective risk management strategies are essential to maintaining profitability and ensuring the longterm sustainability of the businessHow to Increase Sugar Mill Profitability Through FinModelsLab2024年10月5日 Eliminating waste – or going lean, as it’s popularly referred to – has long been associated with manufacturing productivity The concept of lean manufacturing was documented in the early 1900s, but it wasn’t until Toyota How to Improve Productivity in Manufacturing: 5 2016年9月1日 In contrast, increasing the separator speed from 60 to 80 rpm at a constant grinding pressure results in a reduced raw material production rate from 240,000 kg/h to 230,000 kg/h and which Operational parameters affecting the vertical roller mill
.jpg)
Cement Manufacturing Process INFINITY FOR CEMENT EQUIPMENT
Part Three: Raw Mill Process of Raw Mill The proportioned raw material is feed first to a grinding mill In the mill, particles ground in to very fine sizes In the grinding unit, drying, grinding and mixing takes place simultaneously Hot gas from clinker burning unit is passed into the grinding unit to assist the drying and grinding process2024年2月23日 The operation of the cement raw mill is a critical step in cement production By grinding the raw materials into a fine powder, these powders can be more easily mixed with other cement ingredients and burn more evenly during the cement clinker process Therefore, the efficient operation of the cement raw mill directly impacts the production efficiency and quality How Does a Raw Mill Work in a Cement Industry2014年12月1日 The collaborative relationships between suppliers help increase understanding of raw material sourcing On an annual basis, TDV and its suppliers come together and dev elop the annual production(PDF) Managing Raw Materials in Supply Chain ResearchGate2016年5月10日 To stabilize the vertical mill grinding table, we must do a good adjustment of dam height , which is the basis of a vertical mill grinding table, the key of vertical mill normal operation Chaeng will introduce you to describe how to establish stable abrasive bed Material thickness can be adjusted to adjust the height of dam, retaining ring material vertical mill is a How to stabilize the vertical roller mill material dam ring?
.jpg)
Understanding the effects of liner wear on SAG mill performance
2015年9月7日 It is also crucial that the user has knowledge about the process, and potential changes in the plant that can cause process drift For example, liner wear can greatly affect SAG mill performance 2021年5月13日 This may be to meet actual increases in demand or planned increases in demand They may also be used for shortterm and longterm spikes in demand as well Regardless, several basic strategies help companies develop a production capacity calculator to increase production capacity and optimize a manufacturing plant to take on the extra load Tips to Increase Production Capacity and Maximize Manufacturing2024年11月22日 Tips for Enhancing Rice Milling’s Profitability Implement advanced technology: Upgrading to highefficiency machinery can reduce operational costs and increase output, significantly boosting revenue Focus on quality: Highquality rice products can command premium prices and strengthen customer loyalty, driving up sales volumes Expand market How to Increase Revenue in the Rice Milling Businessdone by the pellet mill is used for compression For example, if the feed mix contains a high level of fibrous ingredients such as bagasse, bran or ground alfalfa, the mill will expend a large amount of energy simply compressing the mash to the density of the subsequent pellet Conversely,Factors affecting pellet quality Feed Strategy
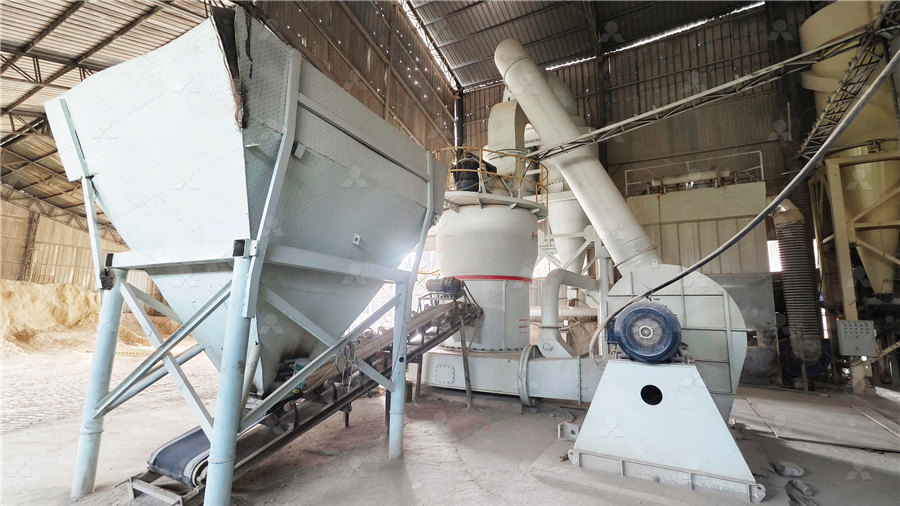
Cement Mill Optimization: Practical Strategies for
Adjusting mill parameters: Finetuning mill parameters such as mill speed, ball charge, filling ratio, and grinding media size can have a substantial impact on the grinding efficiency of the mill For example, a 10% increase in mill speed can 2017年1月1日 An increase of over 10% in mill throughput was achieved by removing the ball scats from a single stage SAG mill These scats are non spherical ball fragments resulting from uneven wear of balls (PDF) Performance optimization of an industrial ball 2023年9月28日 Let’s go through all the steps for calculating total manufacturing costs Step #1: Calculate the cost of direct materials To calculate the cost of direct materials you need to know the cost of inventory Let’s see how to find out the value of inventoryManufacturing Costs: Significance, Types, and Cost Calculation32 Optimizing Raw Mill Operations Adjusting operational parameters in the raw mill can help control moisture levels and enhance grinding efficiency Key adjustments include: Mill air flow: Increasing the air flow rate through the mill can enhance drying efficiency by carrying moisture away from the materialRaw Mill Moisture Content Management: A Comprehensive Guide
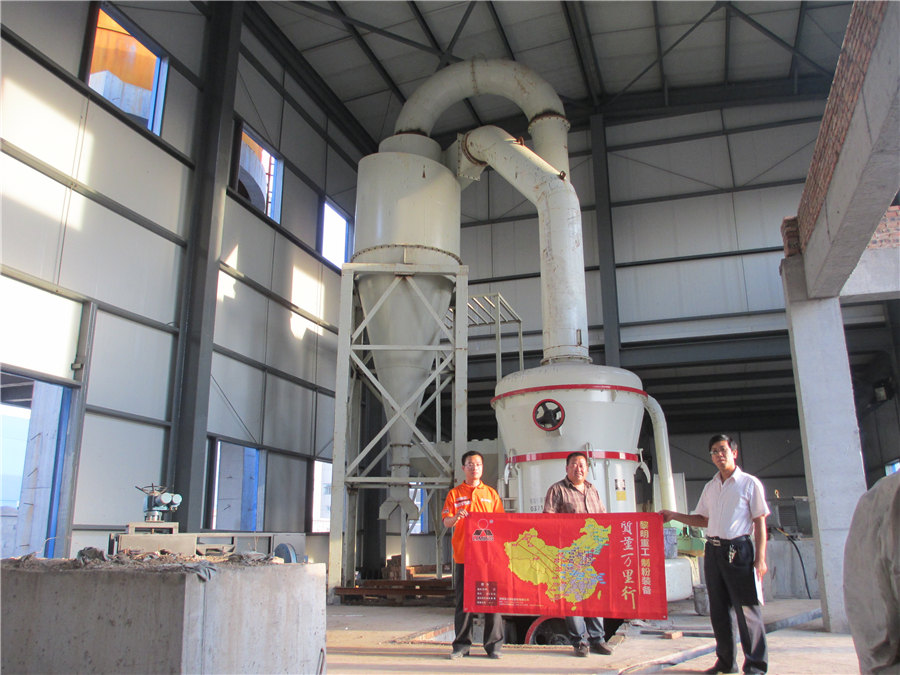
Fact sheet Energy use in the steel industry
technology, and material efficiency • Energy is also consumed indirectly for the mining, preparation, and transportation of raw materials In the blast furnacebasic oxygen furnace (BFBOF) route, this accounts for about 9% of the total energy required to produce the steel, including raw material extraction and steel production processes2024年3月21日 Investment in modern machinery and technology: Automated rice mill machinery can improve efficiency and reduce operational costs in a rice milling business, contributing to increased profitability (Milling and Grain) Upgrading to modern machinery and technology enables faster processing, higher quality output, and reduced labor requirementsStrategies for Improving Rice Mill Business ProfitabilityFor example, if a manufacturing unit uses 100 kilograms of raw material per hour to produce 100 units, its input measure of capacity is 1 unit per kilogram of raw material If the unit can improve its efficiency and produce 120 units with the same amount of raw material, its capacity increases to 12 units per kilogram Utilization MeasureCapacity: Manufacturing Explained Mingo Smart Factory2013年8月1日 The use of waste paper as a raw material for paper production is being emphasised due to increasing energy costs and global competitiveness [22], [38] The SEKA PPM located in İzmit, Turkey, is used here as a reference site in order to examine exergy reduction opportunities in its sulphidecellulose preparation plant, which cooks the chips with an acid An assessment of a pulp and paper mill through energy and
.jpg)
How to Improve Cement Ball Mill Performance
Table 1 From Table 1 we can learn that if the particle size of the feed material is reduced from 25 mm to less than 2 mm, the mill output can be increased by at least 60%, which is relatively consistent with the actual production