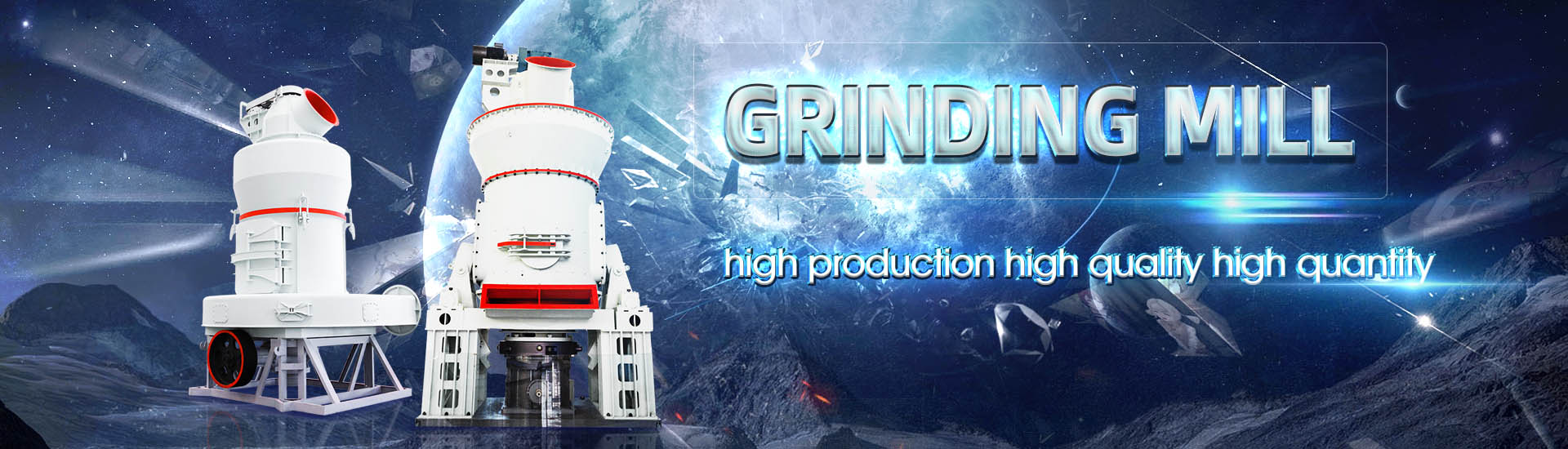
Cement grinding station process can generally be divided into raw material preparation
.jpg)
Raw Material DryingGrinding Cement Plant Optimization
Closed circuit ball mill with two compartments for coarse and fine grinding and a drying compartment with lifters are generally found in cement plants for raw material grinding Compartments (filled with grinding media) are divided by a double diaphragm with flow control process can be divided into the following primary components: raw materials acquisition and handling, kiln feed preparation, pyroprocessing, and finished cement grinding Each of these 116 Portland Cement Manufacturing US Environmental In the cement industry, natural raw materials are processed to produce an end product which is a fine powder As shown in the flow diagram, several size reduction processes are needed The major raw materials are usually Cement Kilns: Size Reduction and GrindingGrinding of cement raw material – material separation in cyclones The cement raw material mixtures are ground, dried, and classified in the Pfeiffer vertical roller mill For drying the material, hot gases are directed into the millRaw mills for all requirements Gebr Pfeiffer
.jpg)
Process and Equipment of the Cement Production Line
2012年9月12日 according to the raw material preparation , cement production equipment methods can be divided into dry process cement production lines (including semidry) and wet The most important raw materials for making cement are limestone, clay and marl These are extracted from quarries by blasting or by ripping using heavy machinery Wheel loaders and From raw materials Extracting raw materials Raw material 1971年8月17日 As shown in the figure, the process can be divided into the following primary components: raw materials acquisition and handling, kiln feed preparation, pyroprocessing, 116 Portland Cement Manufacturing US EPA2017年9月5日 The heart of the portland cement manufacturing process is the pyroprocessing system This system transforms the raw mix into clinkers, which are gray, glasshard, spherically shaped nodules that range from 032 to 51 centimeters (cm) (0125 to 20 inches [in]) in Portland Cement Manufacturing Process Systems Design Blog
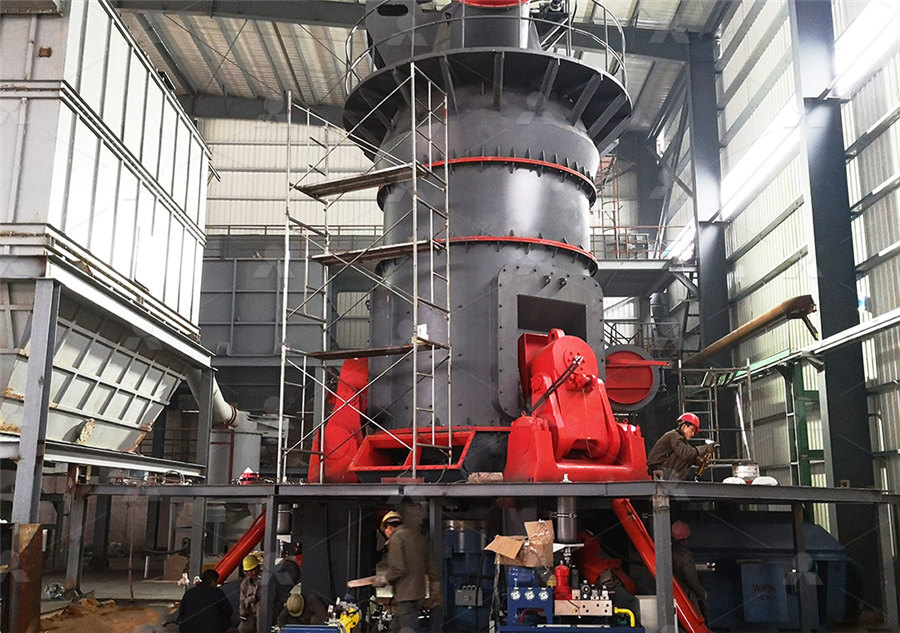
Raw Material DryingGrinding Cement Plant Optimization
However, it would be seen that the most significant process and types used for raw material grinding operations in modern cement industry are: Process: Dry Closed circuit drygrinding Type of mill: Ball and tube mills Vertical Roller Mills (VRM) Horizontal roller mill (Roll Press) Roller press with Ball mill2020年8月25日 The Portland cement manufacturing process is representative of all types of cement limestone and clay are the main raw materials of cement making, the cement raw materials will be processed into a raw meal by Cement Production Process Cement Manufacturing Raw Material Preparation and Raw Meal Design Part One: Raw Material Preparation General; The production of cement is started from quarrying the raw material The main raw materials are limestone, basalt, sand stone, pumice, gypsum Site Exploration of suitable deposits, for the raw material has three main aims:Cement Manufacturing Process INFINITY FOR CEMENT EQUIPMENTProcess Overview of Cement Grinding Grinding in cement manufacturing typically involves breaking down clinker nodules and other raw materials into finer particles This process can be accomplished through various types of mills that grind the materials down to the required size for cement productionGrinding in Cement Manufacturing: Key Process, Types of Mills,
.jpg)
Everything you need to know about cement Raw Materials
In the cement production process, since there are quite a few unit operations employing different hardware systems, it is important to examine the role of raw materials in this perspective For example, a full understanding of the characteristics of the limestone to be used in a given situation will help in selecting the right type of crusherGrinding Operation Objectives and KPIs Chemical analysis of cement, generally on hourly basis Product fineness, Blain surface and 45micron residue Cement SO3, % Grinding aid usage, grams/tonne Cement moisture, % Production rate, tonnes/hour Operating hours as run factor in % Specific power consumption (SPC) kWh/tonneCement Grinding Cement Plant OptimizationCalcareous raw material Raw materials containing calcium carbonate as the main component are all calcareous raw materials It can be divided into natural calcareous raw materials and artificial calcareous raw materials Commonly used in cement production is natural ore containing calcium carbonate (CaCO3) Types and characteristics of What Raw Materials Are Used for Cement ProductionWorking principle of Cement Grinding plant The production of cement, generally can be divided into raw meal preparation, clinker calcining and finished cement three processes, etc Silicate cement production technology is representative in the cement production, is a limestone and clay as the main raw material, through crushing, ingredients, which takes limestone and clay as the Cement Grinding StationHenan Zhongke Engineering
.jpg)
116 Portland Cement Manufacturing US Environmental
in the figure, the process can be divided into the following primary components: raw materials acquisition and handling, kiln feed preparation, pyroprocessing, and finished cement grinding Each of these process components is described briefly below The primary focus of this discussion is on2022年3月3日 Cement Raw Materials Grinding Process (Raw Mill System) English VersionRaw Mill System is a system for grinding raw materials in the form of raw materialsCement Raw Materials Grinding Process (Raw Mill 4 The process chain at a glance xCrushing: crushers break up the raw material delivered from the quarry and provide the raw mill with the feed size range it requires Crushers xRaw material analysis:the POLAB® CNA online analyser provides the first data regarding the chemical contents and/or homogeneity of the raw materialRaw material preparation From the quarry to raw meal feeding into This article introduces the classification of carbon emission sources and me thods of carbon dioxide emission measurement in the cement production process Carbon dioxide emission sources can be divided into direct emission sources and indirect emission sources, meanwhile methods of carbon dioxide emission measurement mainly include carbon Cement Technology
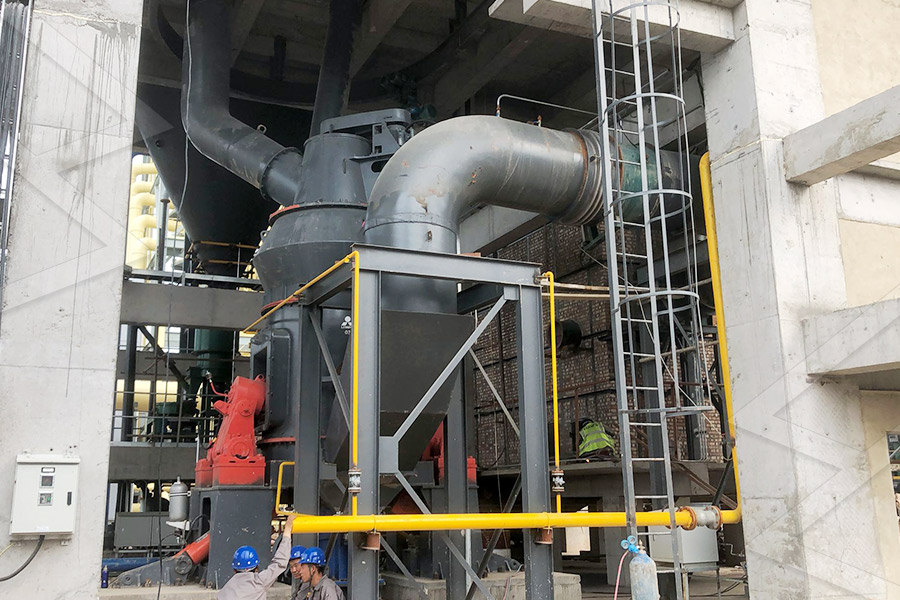
Everything you need to know about clinker/cement Grinding
Gross wear rate 15 g/kWh (my estimate) Wear rate is the same for raw material and cement Different for slurry grinding (6 times more) This value can change a lot depending on the cement composition and the abrasivity of these components For example, for pure slag grinding the value can be doubled Specific ball wear costsThe cement product production process can be divided into three parts: raw material preparation, clinker calcination, and clinker grinding Clinker grinding is a key part and accounts for about 40 % of the total energy consumption of the entire production processDOUDCGAN: Optimization of cement grinding operational Raw material blending is an important process affecting cement quality The aim of this process is to mix a variety of materials such as limestone, shale (clay), sandstone and iron to produce The cement raw material blending process and its control systemSince blasting is not required for quarrying of chalk, and the crushing process can also be omitted, this kind of raw material considerably lowers the cement production costs In some deposits the calcium carbonate content of chalk amounts to 9899 Raw materials used for Cement Production
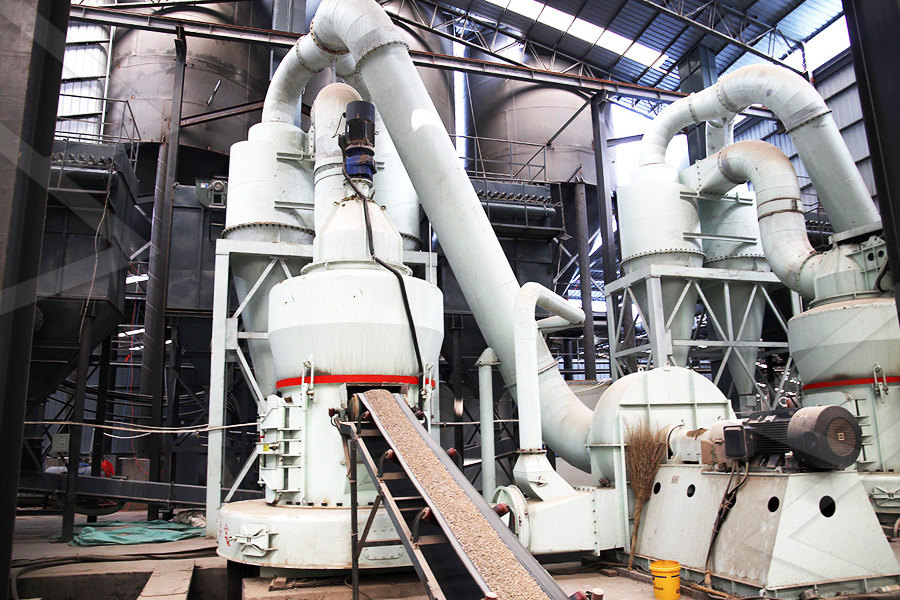
The Effect on the Performance of Cement Grinding Aid Components
quality of cement As we all know that, the production process of cement can be broadly divided into “two grindings and burn", which means raw meal preparation, clinker calcining and cement grinding, and cement grinding is the most important process in the whole cement productionin the figure, the process can be divided into the following primary components: raw materials acquisition and handling, kiln feed preparation, pyroprocessing, and finished cement grinding Each of these process components is described briefly below The primary focus of this discussion is on116 Portland Cement Manufacturing US EPA2024年4月26日 In recent years, the variability in the composition of cement raw materials has increasingly impacted the quality of cement products However, there has been relatively little research on the homogenization effects of equipment in the cement production process Existing studies mainly focus on the primary functions of equipment, such as the grinding efficiency of Evaluation and Analysis of Cement Raw Meal Homogenization2012年12月10日 This paper focuses on modelling and solving the ingredient ratio optimization problem in cement raw material blending process A general nonlinear timevarying (GNLTV) model is established for Modeling and Optimization of Cement Raw
.jpg)
CEMENT RAW MATERIALS BLENDING PROCESS BY
2023年2月1日 Raw material blending is an important process affecting cement quality The aim of this process is to mix a variety of materials such as limestone, shale (clay), sandstone and iron to produce 2023年10月23日 The use of grinding aids can significantly improve clinker production and fineness while decreasing energy consumption, which can help reduce the costs and CO2 emissions associated with cement (PDF) A study of different grinding aids for lowenergy 2015年8月1日 The results show that approximately 248t, 469t, and 341t of materials are required to produce a ton of the product in raw material preparation, clinker production, and cement grinding stages Analysis of material flow and consumption in cement production processThe Portland cement manufacturing is a complex process which can be mainly divided into three parts: raw materials preparation, clinker calcination and cement grinding Raw materials preparation: after materials are quarried, they need to undergo crushing, blending, grinding and storage four processes to finish the raw materials preparation before they are sent into the Portland Cement Manufacturing Process In Cement Plant AGICO
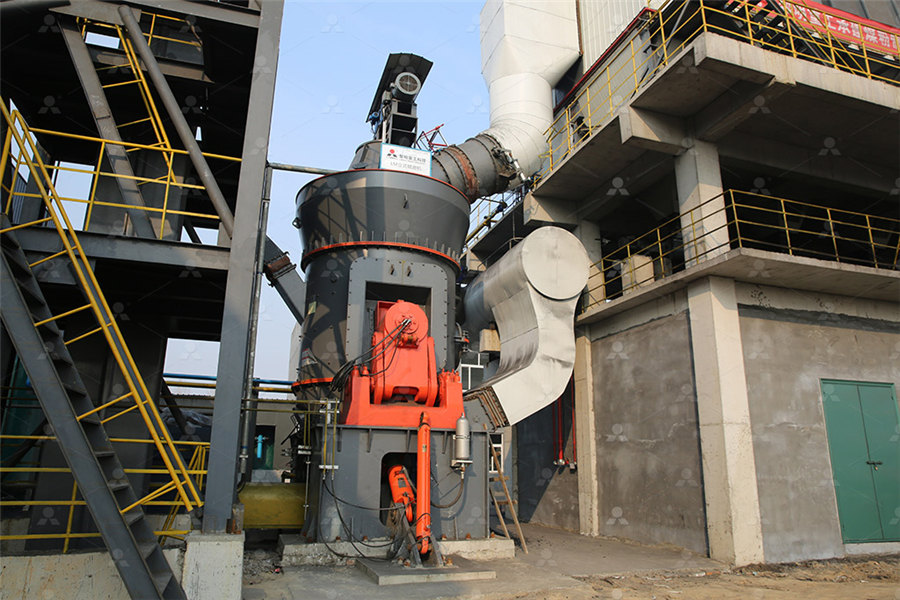
116 Portland Cement Manufacturing US Environmental
A Dry Process Kiln 06 B Raw material unloading 07 C Raw material piles 08 D Primary crushing 09 E Secondary crushing 10 F Screening 11 G Raw material transfer 12 H Raw material grinding/drying 13 I Clinker cooler 14 J Clinker piles 15 K Clinker transfer 16 L Clinker grinding 17 M Cement silos 18A Dry Process Kiln 06 B Raw material unloading 07 C Raw material piles 08 D Primary crushing 09 E Secondary crushing 10 F Screening 11 G Raw material transfer 12 H Raw material grinding/drying 13 I Clinker cooler 14 J Clinker piles 15 K Clinker transfer 16 L Clinker grinding 17 M Cement silos 18116 Portland Cement Manufacturing US Environmental From raw materials to cement Extracting raw materials Crushing and transportation Raw material preparation I: Storage and homogenisation Raw material preparation II: Drying and raw grinding Burning The burning of the raw meal at approx 1,450°C is carried out in Lepol or preheater kilns that work by varying methods, the main difference being From raw materials Extracting raw materials Raw material preparation Cement grinding plants are primarily used to produce finished cement products by grinding cement clinkers and moderate mixed materials After gypsum, clinker, and limestone are measured by the belt weigher, they will be mixed together in accordance with particular proportions, and then sent to the stable weighing warehouseCement Grinding Plant CHAENG
.jpg)
116 Portland Cement Manufacturing US EPA
1971年8月17日 in the figure, the process can be divided into the following primary components: raw materials acquisition and handling, kiln feed preparation, pyroprocessing, and finished cement grinding Each of these process components is described briefly below The primary focus of this discussion is onThe production of cement can generally be divided into three processes: raw material preparation, clinker calcination, and cement production The process of silicate cement is representative of cement productionCement Grinding Plant FTM MachineryClinker Grinding: The main process in cement grinding units involves grinding the clinker into a fine powder using a cement ball mill or vertical roller mill This step is crucial as the fineness of the cement determines the rate of hydration and, StepbyStep Guide to the Manufacturing of Cement2019年3月8日 Raw material preparation provides a mixture of raw materials Rotary kilns are divided into two groups, dry process and wet Traditional ball mills used for raw material grinding can be IMPROVING THERMAL AND ELECTRIC ENERGY
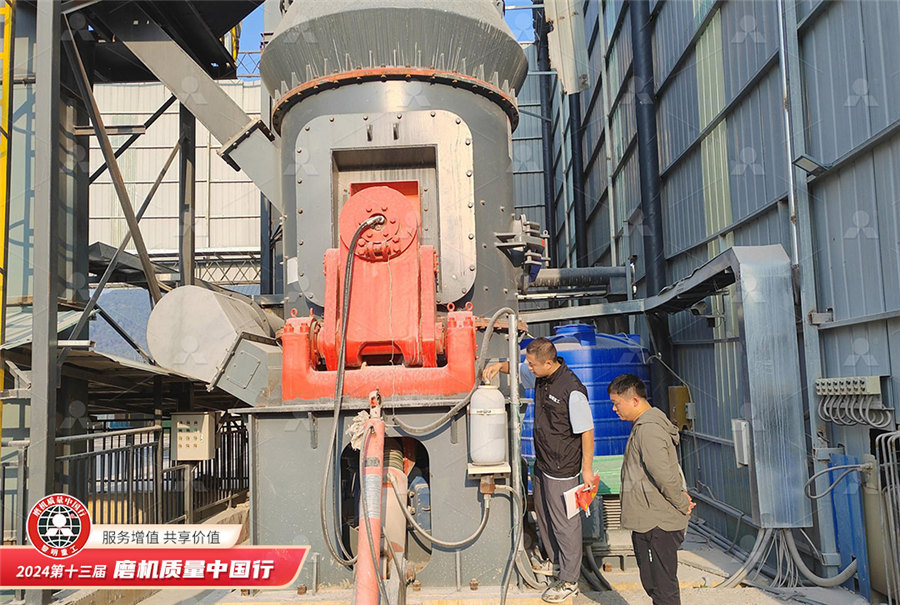
116 Portland Cement Manufacturing US EPA
in the figure, the process can be divided into the following primary components: raw materials acquisition and handling, kiln feed preparation, pyroprocessing, and finished cement grinding Each of these process components is described briefly below The primary focus of this discussion is onThe cyclone preheating system Phase IV: Calcination The calcination is the core phase of the cement making dry process The calcination of the preheated raw meal takes place in the rotary kiln of the cement plant The rotary kiln is a huge rotating furnace in which the raw meal is heated up to 1450 ⁰C and turned to clinkerHow Is Cement Produced in Cement Plants Cement Making Process1971年8月17日 in the figure, the process can be divided into the following primary components: raw materials acquisition and handling, kiln feed preparation, pyroprocessing, and finished cement grinding Each of these process components is described briefly below The primary focus of this discussion is on116 Portland Cement Manufacturing US EPAThe raw material production of cement plant can be classified into four steps: crushing, grinding, mixing and homogenizing Crushing: the limestone and other materials are crushed into small pieces by cement crusher, such as hammer crusher, cone crusher, jaw crusher, impact crusher, etc Mixing: according to the requirement of clinker, compound Preparation Of Cement Raw Material Cement Mill, Cement

Everything you need to know about Crushers in Cement industry
An intermediary storage of the raw material is necessary since the material flow has to be divided up after the primary crusher and the secondary crushers should be loaded The jaw crusher should be mentioned as alternative to the primary gyratory crusher However, its use for cement raw materials is advantageous only under very special conditions2024年1月17日 Contemporary methods of manufacturing cement can be divided into two ways: dryprocess cement production and wetprocess cement production of which raw material grinding accounts for more than 30%, coal grinding accounts for about 3%, and cement grinding station account for about 40% Therefore, What Do You Know About Wet Process Of Cement Production2022年8月10日 Cement grinding station can greatly digest the slag, fly ash, slag, coal gangue and other industrial waste residues near the city, is a green industry Evolution of cement grinding technology A cement mill is the equipment used to grind the hard, nodular clinker from the cement kiln into the fine grey powder that is cementGrinding: Smarter Solutions Indian Cement Review