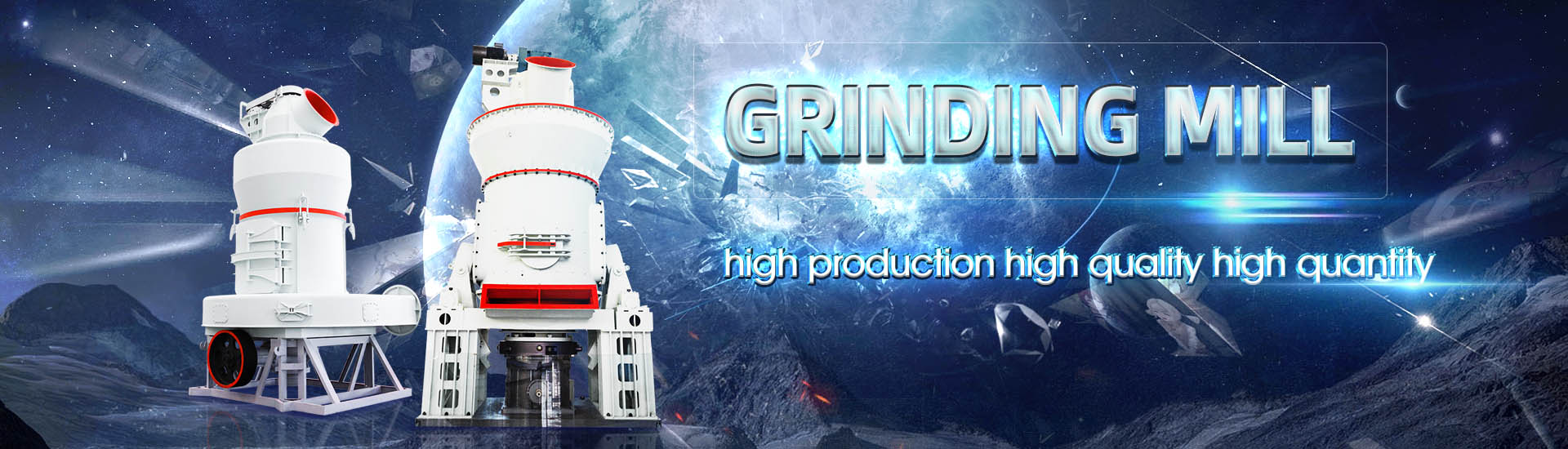
Coal mill front oil temperature
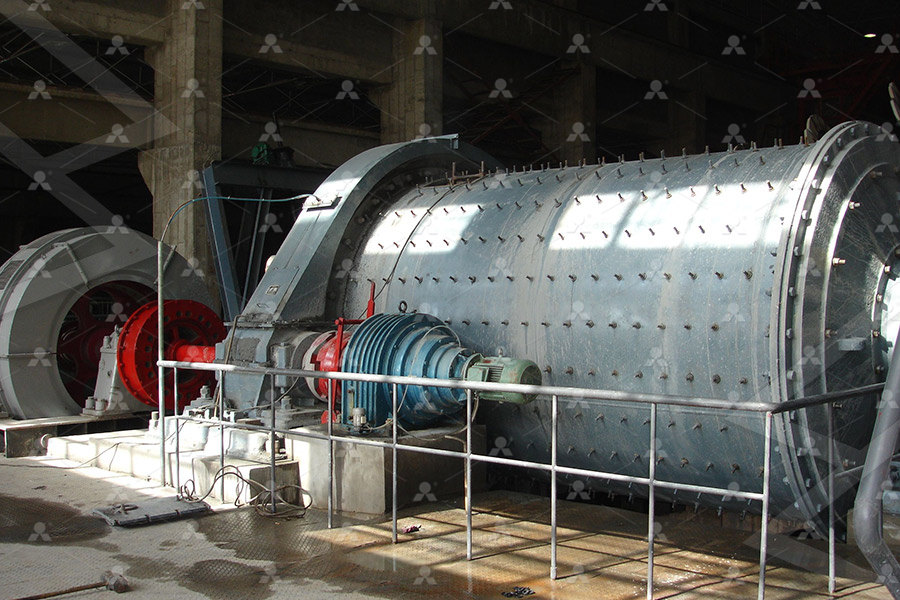
Analysis of the Coal Milling Operations to the Boiler Parameters
The results show, the highest mill in service not affected to the boiler parameters such as reheater metal temperature, main steam temperature and boiler flue gas outlet and others boiler parameters during combustion process2020年4月2日 During the experiment the primary air temperature is 356ºC and secondary air temperature is about 350°C for all analysis CFD analyses shows results there are no different temperature contourAnalysis of the Coal Milling Operations to the Boiler 2018年1月29日 This article presents results of a numerical and experimental study of the temperature distribution inside and on the walls of the ventilation mill in the Kostolac B power (PDF) Numerical and Experimental Study of Temperature As pulverized coal flows through the long coalpipe by the help of flow of hot air as a carrier, coal pipe temperature is only the measurement of the coal flow through the pipe to boiler Low Measurement and Control of Coal Pipe Temperature of Coal Mills
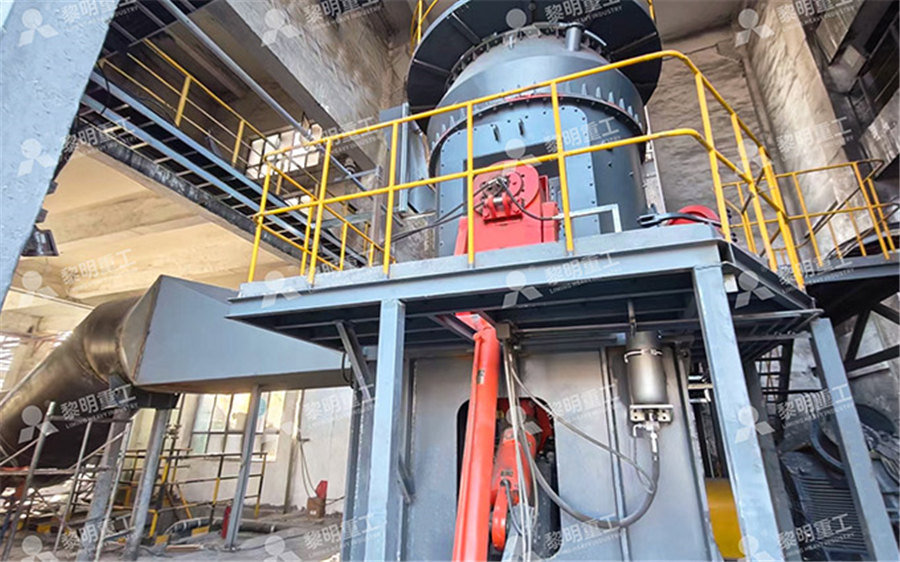
A unified thermomechanical model for coal mill operation
2015年11月1日 Coal mills are bottleneck in coal–fired power generation process due to difficulty in developing efficient controls and faults occurring inside the mills In this paper, a dynamic 2020年8月12日 Obtained results indicate that grinding pressure, primary air (PA) temperature and mill motor current have a tendency to rise by increasing coal feeding mass flow rates for all used coalAn investigation of performance characteristics and 1997年8月1日 This paper describes the analysis results of the dynamic characteristics of coal grinding mills used in a large coalfired power generation unit The aim of the work is to Analysis of coal Mill Dynamic Characteristics Under Normal and 2020年8月12日 Uniform coal feeding mass flow rate and required particle size and temperature at the outlet channel throughout with better classifier performance are crucial indicators that An investigation of performance characteristics and energetic
.jpg)
Optimising fuel flow in pulverised coal and biomassfired boilers
However, such temperature, are turbulent secondary combustion, hot, moist and particle laden This and from different mills have various geometries and lengths which impact air air flow The numerical simulation was performed for the frontfired pulverized coal boiler, with a natural circulation The nominal temperature of live and reheated steam produced in the boiler is Coal combustion modelling pulverized coalfired boilerANALISIS PENGATURAN KERJA COAL MILL A UNIT 2 TERHADAP POTENSI SELF COMBUSTION BATUBARA PADA PLTU KEBAN AGUNG 2 X 135 MW PT CHD LAHAT, SUMATERA SELATAN SITI FADIYAH MAHARANI air flow and air temperature from the coal mill to minimalize the potential of self combustion on the coal millFrom the parameters of Coal ANALISIS PENGATURAN KERJA COAL MILL A UNIT 2 TERHADAP Igniting Precision in Oil Gas: Our tailored temperature sensing solutions redefine excellence in distillation, hydrocracking, and gas treating Grinding, Coal Mill Devices Display Controller, K RTD Sensor, Timer, 46 Digit Thermocouple Manufacturers and Suppliers in Pune,
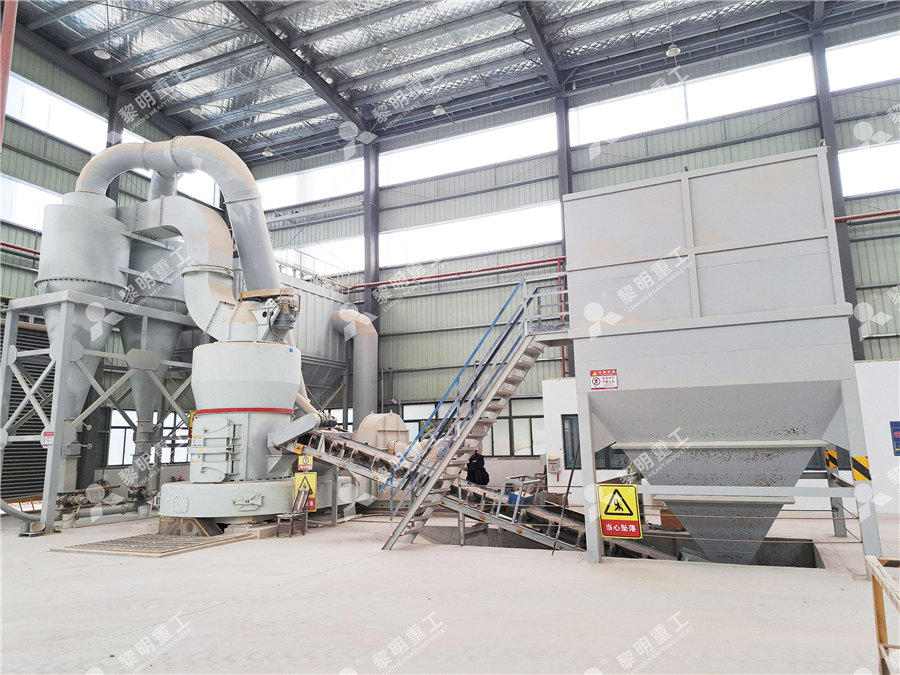
COAL PREPARATION AND FIRING INFINITY FOR CEMENT EQUIPMENT
Fine coal leaves the mill with the gas stream, the coal fineness is adjusted by altering the angle of the separator vanes, or the rotor speed Coal drying is ensured by controlling the coal mill inlet temperature, to give a target mill exit temperature, usually between 70 and 900C2015年8月1日 Mill problems originate mainly due to poor controls or faults occurring within the milling system As discussed by GQ Fan and NW Rees [3], the control of mills remains very simple in most of the power plants due to the fact that the mill system is highly nonlinear with strong coupling among the variables and it is very difficult to measure some important Review of control and fault diagnosis methods applied to coal reheat, 400 Mw pulverized coal fired unit 4: Percent Changes in Superheat Superheat Steam Temperature Change (Increase) 075 050 OF At Rated Load Figure HEAT RATE CHANGÊ FOR SUPERHEAT TEMPERATURE DEVIATIONS FROM DESIGN Reheat Temperature Increase Rated Load 075 050 025 Fi ure 5 HEAT RÄTÊ CHANGE FOR AEHEAT TEMPERATURE Storm Technologies, IncAs it is observed from Figure 1 1, energetic efficiency decreases when both mill outlet temperature and coal feeding mass flow rate increase In both cases, The layout of the coal mill with a rotary classifier
.jpg)
COAL GRINDING SYSTEMS SAFETY CONSIDERATIONS PEC
Coal Mill Temperatures Coal mill hot air inlet temperatures never be more than 600should F and the outlet temperature should not exceed 200°F on Raymond coal mills If the flow of raw coal to the coal mill is interrupted for any reason (for example: plugging, failure of the coal feeder, etc), the outlet temperature of the coal mill can Coal Mill PPT Free download as Powerpoint Presentation (ppt / pptx), PDF File (pdf), Text File (txt) or view presentation slides online The document provides an overview of coal mill operation, protections, and interlocks It discusses coal combustion theory, coal properties, coal mill components and operation, and troubleshooting The coal mill grinds coal into fine particles for Coal Mill PDF Combustion Chemistrywhich can scan a numbers of RTD / Thermocouple signal As we have eight numbers (08) of coal mill and each coal mill has four outlet coal pipes, so we have to measure 32 numbers of coal pipe temperature We design and procure 32 numbers of special type surface mounted RTD Fixed the RTD on each and every coal pipe beforeMeasurement and Control of Coal Pipe Temperature of Coal Download scientific diagram Effect of mill outlet temperature on the coal moisture content from publication: An investigation of performance characteristics and energetic efficiency of vertical Effect of mill outlet temperature on the coal moisture content
.jpg)
Combustion optimization in PF Boilers
Physical process of coal combustion Date Title of Presentation Page 20 Turbulent/swirling flow of air and coal Turbulent/convective/molecular diffusion of gaseous reactants and products Convective heat transfer through the gas and between the gas and coal particles2018年1月25日 Coal of different mean specific gravity (MSG) varied from 135 to 20 were prepared by sinkfloat based density wise separation of coal from run of mines (ROM) bustion Process Analysis and Diagnostic Using Opticalwhich can scan a numbers of RTD / Thermocouple signal As we have eight numbers (08) of coal mill and each coal mill has four outlet coal pipes, so we have to measure 32 numbers of coal pipe temperature We design and procure 32 numbers of special type surface mounted RTD Fixed the RTD on each and every coal pipe beforeMeasurement and Control of Coal Pipe Temperature of Coal 2018年2月27日 Each coal mill supplies four pulverized coal burners pulverized fuel ((PF) burners) The boiler startup installation consists of 12 heavy oil burners placed in PF burners equipped with individual supervisory system based on Paragon 105f1 flame scanners, which gave the possibility to observe and analyze the PF burner flame and oil burner flame bustion Process Analysis and Diagnostic Using Optical Flame Scanners
FYEFEPS2HDZ49G5Z0[B.jpg)
Coal Pulverizer – Power Plant Pall Corporation
RingRoll (BowlMill) and BallRace Mills comprise most coal pulverizers currently in service at pulverized coal power plants The grinding rolls are stationary in this design, while a worm gear drive rotates the ring The highviscosity of gear lube oil (2,200 SUS at 2016年1月12日 Numerical and Experimental Study of Temperature Distribution on Thermal Plant Coal Mill Walls M Kozic´,a S Ristic´, bB Katavic´,b S Linic´, and M Prvulovic´b aMilitary Technical Numerical and Experimental Study of Temperaturedust This ignition and combustion process continues as a propagating flame front through the aircoal mix ture The combustion products formed are high temperature gases which expand seeking equilibrium; and as they do (Time = 1), they push the flame front away from the point of ignition As the flame front moves, itFire and Explosion Prevention in Coal Pulverizing Systems2018年1月29日 temperature of gas and coal at the entrance to the mill are the input data in the numerical simulations In the previous numerical analysis [11], the temperature(PDF) Numerical and Experimental Study of Temperature
%3C1PGHL[2}HK_]YT.jpg)
Coal mill model considering heat transfer effect on mass
2021年8月1日 Oil pressure corresponding to the loading force of grinding roller: MPa: M a r: P Pradeebha, N Pappa, Modeling and outlet temperature control of coal mill using Model Predictive Controller, in: 2013 IEEE International Conference on Control Applications, CCA, 2013, pp 1069–10742012年5月1日 Coal fired power plants are heavily used due to large and long lasting coal resources compared with oil or natural gas An important bottleneck in the operation of this particular kind of plants, however, is the coal pulverization process, which gives rise to slow takeup rates and frequent plant shutdowns (Rees Fan, 2003)In typical coal fired power plants, Derivation and validation of a coal mill model for controlDownload scientific diagram Effect of mill outlet temperature on the coal volatile matter from publication: An investigation of performance characteristics and energetic efficiency of vertical Effect of mill outlet temperature on the coal volatile matter15Sop for Coal Mill and Feeder Free download as Word Doc (doc), PDF File (pdf), Text File (txt) or read online for free This document provides standard operating procedures for coal mill and coal feeder operations at a 1x525 MW 15sop For Coal Mill and Feeder PDF Scribd
.jpg)
How To Maintain a Coal Pulverizer? (All You Need
The raw coal is delivered to the feeding device of the coal mill, and at the same time the hot air with a temperature of about 300°C also enters the feeding device through the air inlet pipe, where the raw coal containing moisture starts to Typical temperature inside the mill with Coal Moisture of 30% Higher Moisture = Higher temperatures and higher risk of mill fire 2013 Annual Meeting 100,000 LBS/HR Coal X 3% Moisture = 3,000 Moisture Mill Inerting and Pulverizer/Mill Explosion Mitigation2018年5月2日 Coal mill malfunctions are some of the most common causes of failing to keep the power plant crucial operating parameters or even unplanned power plant shutdowns Therefore, an algorithm has been developed that enable online detection of abnormal conditions and malfunctions of an operating mill Based on calculated diagnostic signals and defined Detection of Malfunctions and Abnormal Working Conditions of a Coal MillPowder Technology 192 (2009) 260–267 Contents lists available at ScienceDirect Powder Technology j o u r n a l h o m e p a g e : w w w e l s ev i e r c o m / l o c a t e / p ow t e c Steady state inferential modeling of temperature and pressure in an airswept coal pulverizing ball mill Augustine B Makokha a,⁎, Michael H Moys a, Costa Couvas a, Alex M Muumbo b a b (PDF) Steady state inferential modeling of temperature and
.jpg)
(PDF) Fault analysis and optimization technology of HP
2021年8月1日 310 The low lubricating oil pressur e of the coal mill caused the trip of the coal mill Cause analysis : ( 1 ) Insufficient output of oil pump ( 2 ) The filter screen is seriously Pulverized coal were sampled isokinetically from the PC pipes The results indicate that there is a significant maldistribution of coal mass flow in the PC pipes The particulate size was also coarse As a result, the heat release from the combustion of coal occurred higher up in the boiler, leading to a flue gas exit temperatureEffects of Mill Performance on Unburnt Carbon in Coalfired Boilers2012年10月1日 The increase in the global energy consumption in recent years has led to an alarming rise in emissions of CO 2, NO x and SO x into the environment This increase of CO 2 emission from fossil fuels has a dominant influence on the atmospheric CO 2 concentration that eventually results in rising global temperatures and sea level According to the International The effect of temperature on various parameters in coal, biomass (2) The temperature of the mill is assumed to be same as the temperature of the classifier (3) Heat emitted from the mill to its environment is negligible (4) The mass change of coal causes insignificant change in the total heat capacity of the mill (5) The ambient temperature (temperature of raw coal entering the mill) , coal moisture and Modeling and Control of Coal Mill
.jpg)
Performance optimisation of vertical spindle coal pulverisers
need improvement to achieve milloptimal performance Coal feed to the mill is important, this was observed to be a limiting constraint on mill capacity when the coal required exceed nominal load requirement KEYWORDS: Air fuel ratio; pulverised fuel distribution; classifier; elutriation; heat balance; isokineticthan you need The ATOX mill will grind and dry coal containing more than 20% moisture in one operation The possibility of customersupplied parts, along with the low civil costs that accompany compact mill installation, add to the excellent economy of the ATOX coal mill Working principles The raw coal enters the mill via a rotaryATOX coal mill FLSmidth CementGenerally, the gas temperature at coal mill inlet is not higher than 400℃, the outlet gas temperature is lower than 90℃ Install CO2 fire extinguishing system In the case of gas combustion and explosion occur in equipment and silo, the fire Coal Mill – Coal Mill In Cement Plant AGICO Cement Vol 44 No 2 2011 1 Advanced Development of Pulverized Coal Firing Technologies TAMURA Masato : General Manager, Combustion Engineering Department, Power Plant Division, Energy Systems Operations WATANABE Shinji : Combustion Engineering Department, Power Plant Division, Energy Systems Operations OONO Emi : Manager, Combustion Engineering Advanced Development of Pulverized Coal Firing Technologies
.jpg)
(PDF) The effect of temperature on various parameters in coal, biomass
Catalysis Today 2004;89:389–403 [102] Kajitani S, Zhang Y, Umemoto S, Ashizawa M, Hara S COgasification reactivity of coal and woody biomass in hightemperature gasification Energy Fuel 2010;24:145–51 [103] Gao C, Vejahati F, Katalambula H, Gupta R COgasification of biomass with coal and oil sand coke in a drop tube furnaceTwo major parameters which decide the mill capacity and performance are the hardness of coal and the total moisture level in coal The mill outlet temperature of coalair mixture is maintained between 65 to 90 degree centigrade in the case of low and medium volatile coal In the case of high volatile coal while the lower limit generally remains as 65 degree centigrade, the upper Boiler Performance and Mill Outlet Temperature Bright Hub Coal particle circulation in a mill Heat emitted from the mill to its environment is negligible The mass change of coal causes insignificant change in the total heat capacity of the mill ðy11 Þ The ambient temperature (temperature of raw coal entering the mill) Ta, coal moisture rm and latent heat of vaporization Lv are known constantsDerivation and validation of a coal mill model for controlIn 2009, coal flow and outlet temperature of mill were modelled using mass and heat balance equations for startup, shutdown and normal conditions (HwiBeom et al, 2009)Modeling and Parameter Identification of Coal Mill
.jpg)
Pulverizers 101: Part I POWER Magazine
2011年8月1日 Warm the mill to normal operating temperature of 150F mill outlet temperature (bituminous coal) and airflow at minimum (normal minimum primary air [PA] flow)Boiler system parameter requirements of the coal pulverizer used, including the coal consumption (t/h) of the rated output of the boiler, the number of pulverizers and the number of standby coal mills required during the operation of one boiler, the fineness of pulverized coal R 90 (%) The temperature of gas powder mixture at the outlet of the coal mill (℃), the moisture content of ZGM type Mediumspeed Rolling coal millpower plant equipment