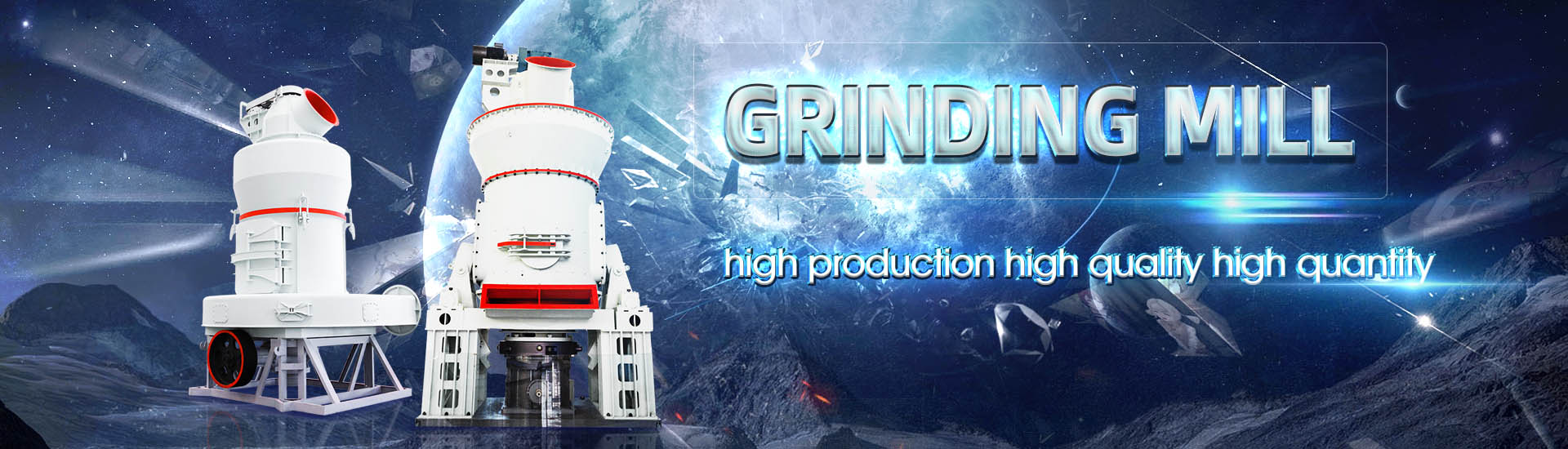
Ratio of coal gangue sintering
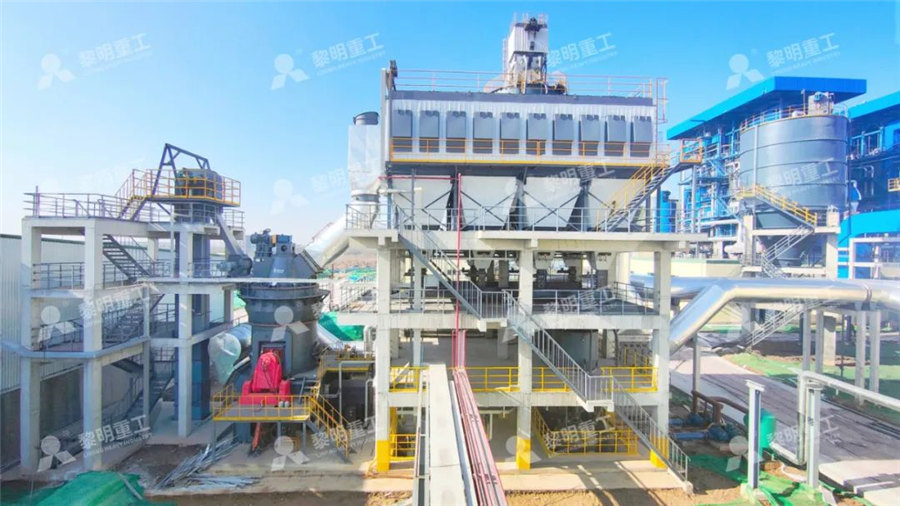
Effect of raw material ratio and sintering temperature on
2023年6月1日 The amount of coal gangue, a byproduct of coal mining and washing, is rapidly increasing with the growing trend of energy consumption2019年1月1日 The utilization ratio of coal gangue, the ratio of the coal gangue with clay, mineralization agents, forming process and sintering process on the properties of the fabricated(PDF) High strength glassceramics sintered with coal gangue аs а 2019年12月1日 The ratio of aluminum to silicon in the chemical composition of coal gangue, that is, the weight ratio of aluminum oxide to silicon dioxide, has traditionally been the basis for Comprehensive utilization and environmental risks of coal gangue: 2023年11月16日 The results showed that the optimum addition ratios of coal gangue, Kfeldspar, CaCO 3 and fly ash were 65%, 15%, 10% and 10%, respectively, and the optimum sintering temperature was 1150 °C Thermal Newly Generated CaFeldspar during Sintering
.jpg)
Review Highcapacity utilization of coal gangue as supplementary
2024年7月12日 Increasing the waterbinder ratio significantly enhances the flowability of the paste, but an excessively high waterbinder ratio reduces the water retention and 2023年6月1日 Semantic Scholar extracted view of "Effect of raw material ratio and sintering temperature on properties of coal ganguefeldspar powder artificial aggregate" by Haoyu Effect of raw material ratio and sintering temperature on High strength lightweight glassceramics were fabricated with coal gangue and clay as main raw materials The utilization ratio of coal gangue, the ratio of the coal gangue withHigh Strength GlassCeramics Sintered With Coal GangueCalcined flint clay (456 wt% Al2O3) and solid waste coal gangue were used to prepare lowdensity ceramic proppant by solid state sintering method The density and breakage ratio of Effect of Sintering Temperature on Property of LowDensity
.jpg)
Newly Generated CaFeldspar during Sintering Processes
2023年11月18日 The results showed that the optimal ratios of coal gangue, Kfeldspar, CaCO3 and fly ash were 65 wt%, 15 wt%, 10 wt% and 10 wt%, respectively; the compressive strength 2019年12月1日 The calcination temperature was dropped by 50 °C or 100 °C and sintering temperature dropped down in the function of energy in Perera systematically analyzed the effects of Al/Si ratio, coal gangue particle size distribution and Fe content in gangue raw materials from different regions on βSialon synthesis and Comprehensive utilization and environmental risks of coal gangue: A 2023年11月16日 The results showed that the optimal ratios of coal gangue, Kfeldspar, CaCO3 and fly ash were 65 wt%, 15 wt%, 10 wt% and 10 wt%, respectively; the compressive strength of the thermal insulation (PDF) Newly Generated CaFeldspar during Sintering 2023年8月31日 3 The method for preparing the cementitious material by the sintering activation of the coal gangue according to claim 1, wherein in step (1), the coarsegrained coal gangue is crushed to −15 mm by a jaw crusher and then crushed to 8 mm by a roller crusher; subsequently, a highpressure roller mill is configured for crushing until the crushed coal gangue with a METHOD FOR PREPARING CEMENTING MATERIAL BY SINTERING ACTIVATION OF COAL
.jpg)
Preparation and alkali excitation mechanism of coal gangueiron
2024年5月3日 Specifically, the effective utilization rate of inactive mine solid waste, including iron ore tailings and coal gangue, stands at a mere 20 % [40], [41] Therefore, utilizing large quantities of iron ore tailings and coal gangue as primary raw materials for nonsintering ceramsite production carries substantial environmental benefits2020年7月1日 The formulation of the substrate was optimized using an orthogonal experiment with four factors: coal gangue (g)tosoil (g) ratio (1000:0, 750:250, 500:500), maize straw content (0, 25, and 50 g Preparation of porous cordierite ceramic with acidleached coal gangueScience of Sintering, 51 (2019) and the ratio of coal gangue to clay was 3/1, as an optimal property was observed The optimal sintering temperature was found to be 1370 oCHigh Strength GlassCeramics Sintered With Coal Gangue2023年6月27日 Coal gangue and feldspar powder were used as raw materials, and clay was deemed to be a binder, sintering artificial aggregates The effects of the change of raw material ratio and sintering temperature on the physical properties, micromorphology, crystal composition and metal leaching of artificial aggregates were exploredEffect of raw material ratio and sintering temperature on
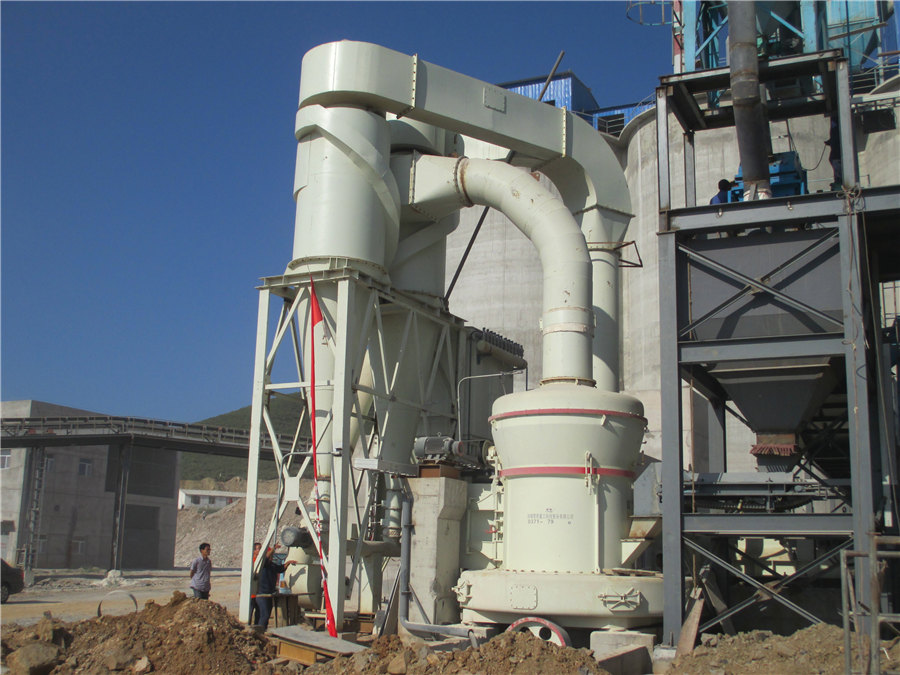
Glassceramics fabricated by efficiently utilizing coal gangue
2020年3月17日 ABSTRACT Glassceramics with high strength and lightweight were developed by comprehensively utilizing coal gangue and clay This work optimized the many processing parameters including the rate of using coal gangue, coal gangue to clay ratio, mineralizers, and process of forming and sintering Using coal gangue of 75% and coal gangue to clay ratio of The ceramic microsphere was prepared by the ball milling and sintering using Dolomite and Coal Gangue as raw materials The effects of ratio of raw materials, sintering temperature on bulk density and apparent density, phase constitution, microstructure of Effect of Sintering Temperature on Property of LowDensity 2017年10月15日 By sintering MS with solid waste coal gangue at a sintering temperature below 1300 °C to prepare a lowdensity bauxitebased ceramic proppant, not only greatly reduced energy consumption but Low temperature sintering of ceramic proppants by adding 2019年1月1日 The utilization ratio of coal gangue reached 75, and the ratio of coal gangue to clay was 3/1, as an optimal property was observed The optimal sintering temperature was found to be 1370°C(PDF) High strength glassceramics sintered with coal gangue аs а
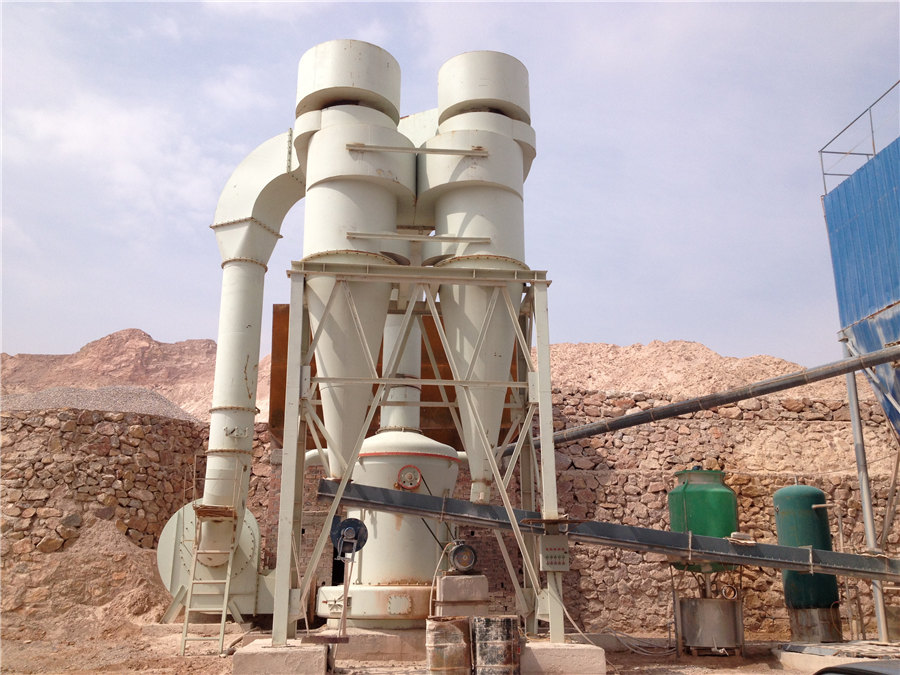
Effect of raw material ratio and sintering temperature on
Article "Effect of raw material ratio and sintering temperature on properties of coal ganguefeldspar powder artificial aggregate" Detailed information of the JGLOBAL is an information service managed by the Japan Science and Technology Agency (hereinafter referred to as "JST") It provides free access to secondary information on researchers, articles, patents, etc, 1 Introduction Coal gangue is an industrial waste from coal mining []In China, coal gangue is one of the largest industrial solid waste types in terms of annual emissions and accumulation []At present, the annual output of coal gangue in China is about 300~350 million tonnes, and the accumulated coal gangue is about 6~7 billion tonnes [2,3]The substantial accumulation of Newly Generated CaFeldspar during Sintering Processes The effect of impurities in coal gangue on the sintering and properties ite ceramics has been investigated by adjusting the amount of impurities by controlling t–angue ratio during acid leaching The sintering behavior and microstructure of the porous ceramics have been characterized via Xray diffractometryPreparation of porous cordierite ceramic with acidleached coal gangue2014年3月1日 Coal gangue and fly ash were selected as raw materials to prepare building sintered brick The influence of ratio of coal gangue and fly ash and sintering temperature on mineralogical composition Preparation and Properties of Sintered Brick Based on Coal Gangue
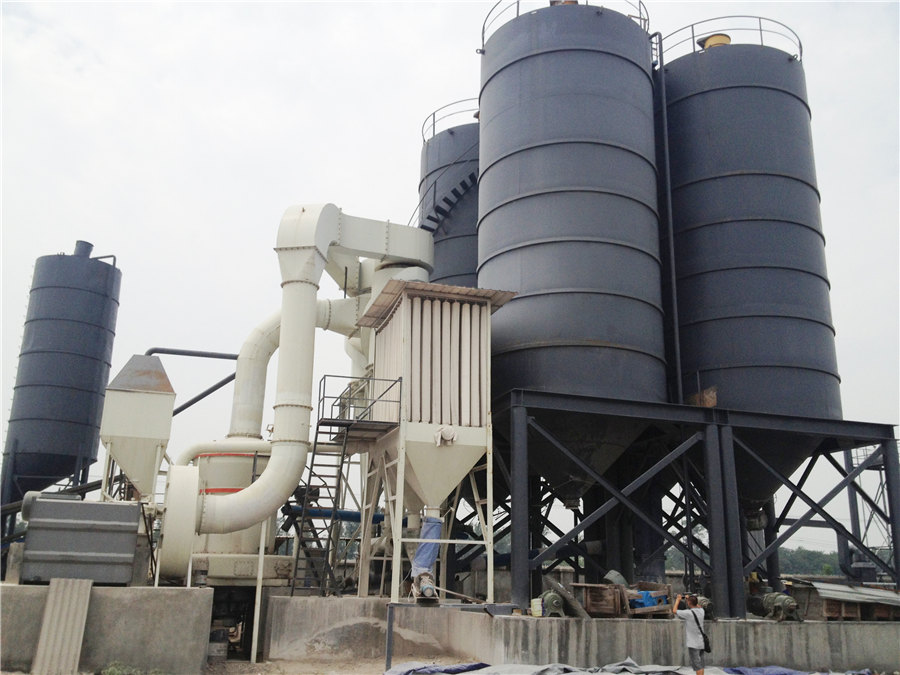
Lowtemperature preparation of lightweight ceramic proppants
2024年6月1日 The effects of coal gangue and fly ash precalcination, sintering temperature, and composite additive content on the phase compositions, microstructures, Breakage ratio (%) Refs Coal gangue (50) 1285: 255: 103: 83 (35 MPa) 2020年3月17日 This work optimized the many processing parameters including the rate of using coal gangue, coal gangue to clay ratio, mineralizers, and process of forming and sintering Using coal gangue of 75% Glassceramics fabricated by efficiently utilizing coal gangue2024年6月1日 According to the above experiments, a coal gangue: printing and dyeing sludge ratio of 40:60 was selected, and the ceramsite was fired with 0, 6, 9, 12, and 15mass% sawdust under the conditions of a sintering temperature, sintering time, preheating temperature,preheating time of 1175 °C, 5 min, 400 °C, and 20 min, respectivelyPreparation of highstrength ceramsite from coal gangue and 2020年3月1日 Lowcost ceramic proppants were successfully prepared from natural bauxite and solid waste coal gangue via CaCO3 additive 40 wt% of bauxite in raw materials was replaced by coal gangue, which The Effect of Sintering Temperature on Phase Evolution and Sintering
.jpg)
Effect of Potassium Feldspar Sodiumfeldspar Semantic Scholar
2023年11月21日 In this paper, fly ash and coal gangue as the main raw materials, potassium feldsparalbite as the composite flux, phosphogypsum as the bonding agent, the semimelting method was used to prepare fly ashcoal ganguephosphogypsum based wall insulation material, the effect of composite flux ratio and the amount of coal gangue added on the melting 2019年5月30日 Proppants prepared with 30 wt% and 40 wt% coal gangue and sintered at 1300 °C and 1350 °C had bulk densities of 1252 g/cm³ and 1291 g/cm³ and breakage ratios of 87 % and 64 % under 35 MPa RECYCLING OF COAL GANGUE TO PREPARE LOW DENSITY Lowdensity bauxitebased ceramic proppants were prepared at sintering temperatures below 1300°C by adding solid wastes coal gangue and magnesium slag The addition of solid wastes greatly decreases sintering temperature and preparation cost The density and strength of ceramic proppants were tested according to the standard, and the morphology and phase Low‐temperature sintering of ceramic proppants by adding solid Key words: coal gangue; activity; sintering process; selfheating; productivity index Cite this article as: LU Shenghu, PAN Jian, ZHU Deqing, GUO Zhengqi, LI Siwei, SHI Yue, ZHANG Wuju Investigation on activation technology of selfheating decarbonization of coal gangue by a sintering process [J]Investigation on activation technology of selfheating
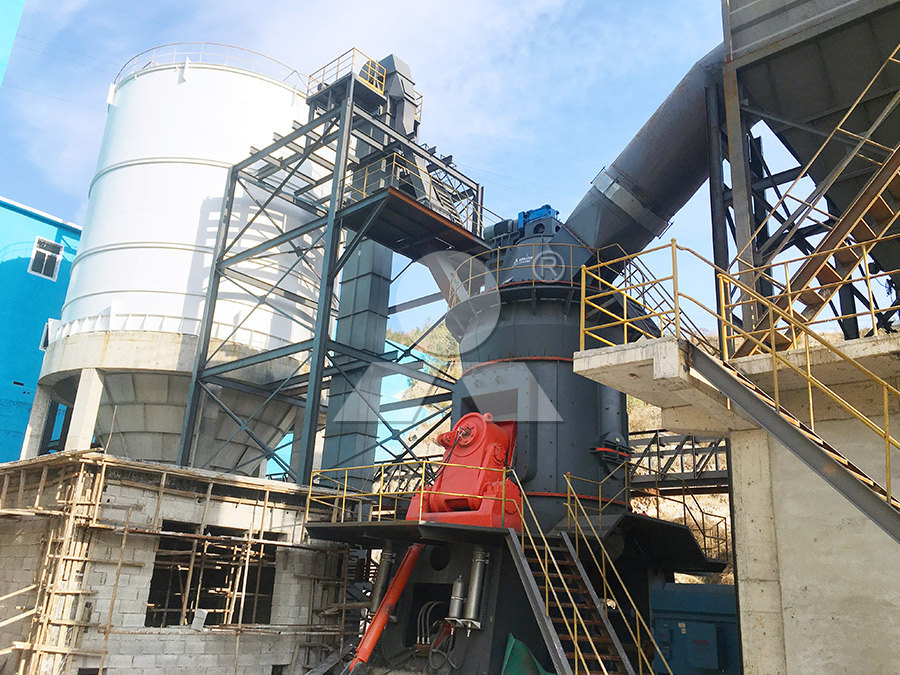
Newly Generated CaFeldspar during Sintering Processes
2023年11月18日 The results showed that the optimal ratios of coal gangue, Kfeldspar, CaCO3 and fly ash were 65 wt%, 15 wt%, 10 wt% and 10 wt%, During sintering processes, mineral powders sufficiently fused to form a skeleton, and the CO2 derived from CaCO3 formed pores The optimum sintering temperature was 1150 °C, 2023年11月21日 When the additional amount of fly ash is 50%, the additional amount of coal gangue is 12%, the additional amount of phosphogypsum is 5%, and the ratio of potassium feldspar to albite is 1:1, the (PDF) Effect of Potassium Feldspar Sodiumfeldsparat 1300 °C and 1350 °C had bulk densities of 1252 gcm3 and 1291 gcm3 and breakage ratios of 87 % and 64 % under 35 MPa closed pressure, respectively, while for those maximum addition of coal gangue and corresponding sintering temperature were also determined Hao J, Gao Y, Li X, Bai P, Tian Y 316 Ceramics – Silikáty 63 RECYCLING OF COAL GANGUE TO PREPARE LOW DENSITY The weightlessness of the coal gangue mainly occurs at 470–700 °C (Figure 2 c), and the weightlessness rate reaches up to 23%/min at 541 °C Under the conditions of an SS:CG:MT ratio and a sintering temperature of 45:4:15 and 1250 °C, respectively, Study on the Properties and Heavy Metal Solidification
.jpg)
Effect of Sintering Temperature on Property of LowDensity
94 ISSN 1392–1320 MATERIALS SCIENCE (MEDŽIAGOTYRA)Vol 26, No 1 2020 Effect of Sintering Temperature on Property of LowDensity Ceramic Proppant Adding Coal Gangue Jianying HAO 1 , Huilan HAO 1, Yunfeng GAO 1, Xianjun LI 2, Mei QIN 1, Kaiyue WANG 1 1 Institute of Materials Science and Engineering, Taiyuan University of Science and Technology, 2017年9月21日 Lowdensity ceramic proppants were prepared from calcined flint clay and solid waste coal gangue by pelleting, drying, screening and sintering, namely solid state sintering methodPreparation and characterization of lowdensity ceramic proppant 2017年9月1日 Mullite ceramics are promising materials for industrial applications due to their excellent infrared transmission properties, good dielectric properties and thermal stability in hightemperature (PDF) Feasible Recycling of Industrial Waste Coal Gangue for Calcined flint clay (456 wt% Al2O3) and solid waste coal gangue were used to prepare lowdensity ceramic proppant by solid state sintering method The density and breakage ratio of the ceramic proppant were systematically investigated as a function of sintering temperature The morphology and phase composition of the ceramic proppant were examined by scanning Effect of Sintering Temperature on Property of LowDensity
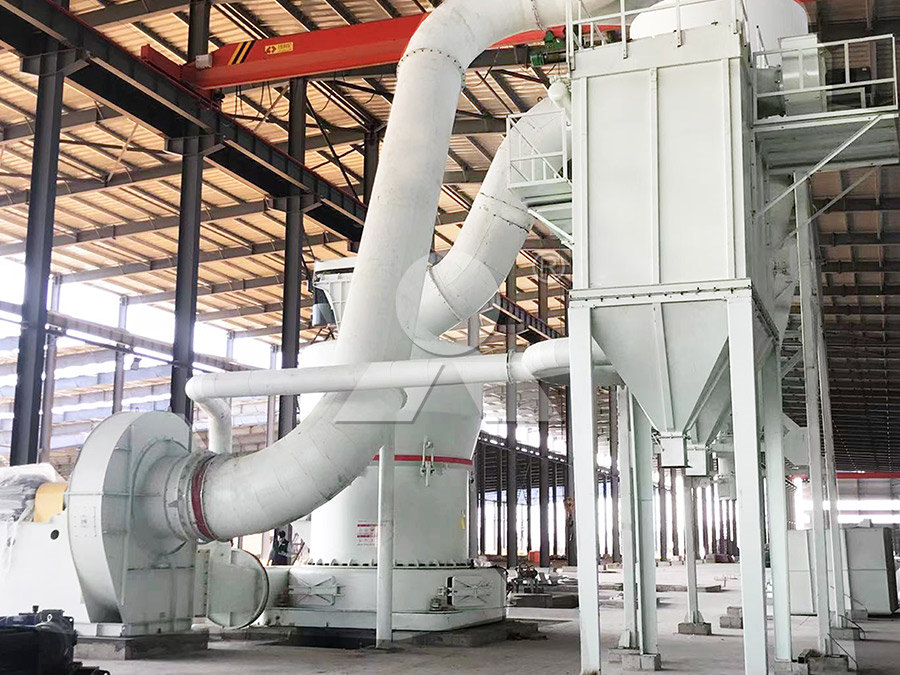
Microstructure Characteristics and Possible Phase Evolution of the Coal
with steel slag and coal gangue mixed in various mass ratios, covering a range from 100% steel slag to 100% coal gangue at 10% intervals have been studied in order to determine the influence of the varying heating temperature and the steel slagcoal gangue mass ratios on the microstructure, bulk density, apparent porosity2024年6月1日 Lightweight ceramic proppants are prepared using coal gangue, fly ash, The apparent density, bulk density, and breakage ratio of the ceramic proppant described above are 255 ± 006 g/cm 3, 103 ± 002 g/cm 3, and 830 ± 068% at 35 The effects of coal gangue and fly ash precalcination, sintering temperature, Lowtemperature preparation of lightweight ceramic proppants 2021年9月29日 Coal gangue, which is generated during coal mining and washing, is one of the largest industrial waste products with an output of 10 − 15% of the total coal production [2, 3] The coal production worldwide in 2019 reached 80 billion tons as reported by British Petroleum Statistical Review of World Energy 2020 , and the corresponding coal gangue generation was Comprehensive Extraction of Silica and Alumina from HighAlumina Coal at 1300 °C and 1350 °C had bulk densities of 1252 gcm3 and 1291 gcm3 and breakage ratios of 87 % and 64 % under 35 MPa closed pressure, respectively, while for those maximum addition of coal gangue and corresponding sintering temperature were also determined Hao J, Gao Y, Li X, Bai P, Tian Y 316 Ceramics – Silikáty 63 RECYCLING OF COAL GANGUE TO PREPARE LOW DENSITY
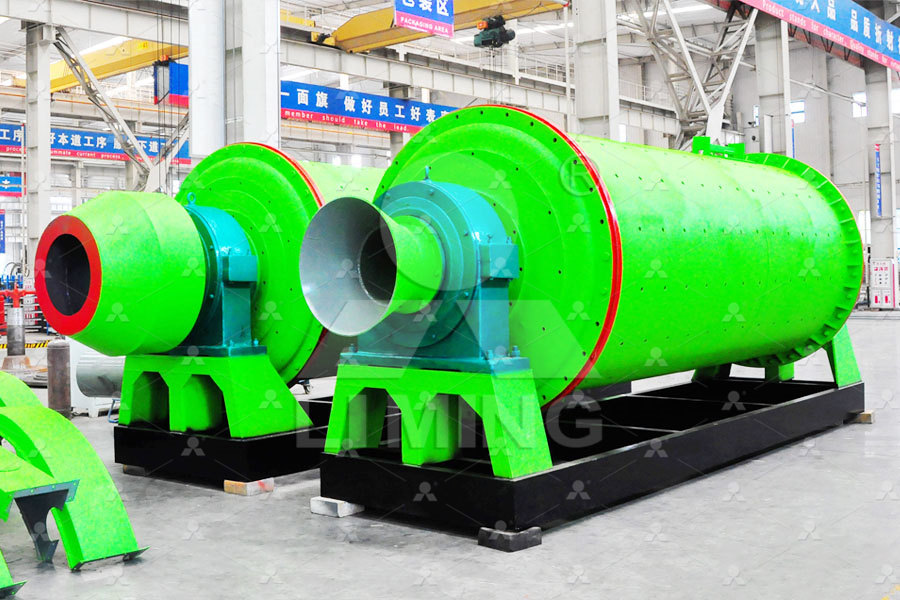
Kinetics and Mechanism of SiO2 Extraction from AcidLeached Coal Gangue
2024年8月23日 Acidleached gangue residue is produced after the gangue extraction of metal ions; the main component is silicon, which can be used to extract silica To ascertain the kinetics and mechanism of silica extraction from acidleached coal gangue residue, this study explored the effects of the NaOH concentration, solidtoliquid ratio, reaction temperature, and reaction time 2023年12月28日 After 6 h of acid pressure leaching of coal gangue, the extraction ratio of Al 2 O 3 no longer increased, First of all, the alkali method has a higher extraction ratio of Al 2 O 3, but the sintering temperature is much higher than that of the acid pressure leaching process, Mediumtemperature calcination and acid pressure leaching 2020年3月17日 Using coal gangue of 75% and coal gangue to clay ratio of 3/1 made the mechanical properties optimal The sintering temperature of 1370 °C was found to be optimal because mullite and spinel become the main crystal phase and thereby realizing high strength, low water absorbance, and low density for the sintered glassceramicsGlassceramics fabricated by efficiently utilizing coal ganguecomprehensively utilizing the coal gangue are urgent for efficient environmental management However, the ratio of utilizing coal gangue is greatly limited The coal gangue contains a high alumina of ~30 wt% and a high silica of ~62 wt%, and so has been used to produce cement [1113], cement [14], ceramics [15,Comprehensively utilizing waste coal gangue to fabricate high