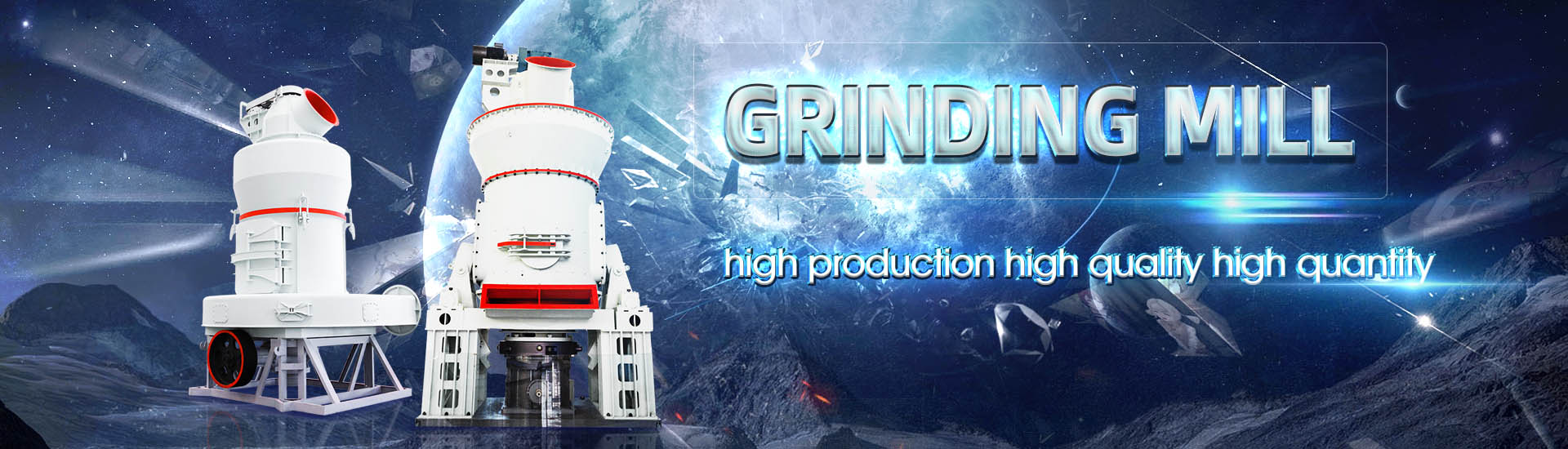
Fault analysis of cement raw material vertical mill hydraulic system
.jpg)
Causal analysis of vertical mill process failure based on Bayesian
Because traditional manual fault judgment cannot match the criteria for cement vertical mill diagnosis as equipment reliability and production processes improve, this study offers a As most faults of VRM relate to hydraulic pressure of loading system and mechanical vibration, research on hydraulic monitoring and vibration monitoring is prerequisites, which determines Reliability assessment of the vertical roller mill based on ARIMA As most faults of VRM relate to hydraulic pressure of loading system and mechanical vibration, research on hydraulic monitoring and vibration monitoring is prerequisites, which determines Full article: Reliability assessment of the vertical roller mill based Cite this article: QIU Zhanming MPS5300B vertical mill hydraulic system fault analysis[J] Journal of Cement, 2023, 0(10): 46 URL:MPS5300B vertical mill hydraulic system fault analysis
.jpg)
Common fault phenomenon and diagnosis of hydraulic system of
Cite this article: LIU Peng Common fault phenomenon and diagnosis of hydraulic system of ZGM113G coal vertical mill[J] Journal of Cement, 2022, 00(01): 83Our bestinclass OK™ Mill is a globally successful vertical roller mill solution for grinding raw material, cement and slag In 2017 we released the OK™ vertical roller mill for raw materials grinding This vertical roller mill uses a hydro OK™ Raw and Cement Mill2017年9月11日 Due to the compact design and material transportation system of vertical roller mills (VRM), some important streams (total mill feed and discharge, dynamic separator feed and reject) remain in the (PDF) Performance Evaluation of Vertical Roller Mill 2012年12月31日 PDF a Distributed Control System(DCS) of cement raw materials is presented for the vertical roller mill by the application of ABB's IndustrialIT The Find, read and cite all the research Design and Realization Of Roller Mill Control
.jpg)
Vertical Roller Mill for Cement Raw Material SINOMALY
Vertical Roller SINOMALY produces cement raw material grinding mills in various specifications These machines are suitable for grinding mill production lines with an output of 2500t/d, 3200t/d, 4000t/d, 5000t/d, 6000t/d and 8000t/d The vertical grinding mill is utilized for the grinding of raw materials, mixed cement, and slag powder2021年1月22日 In the whole process of cement production, the electricity consumption of a raw material mill accounts for about 24% of the total Based on the statistics of the electricity consumption of the raw A Survey and Analysis on Electricity Consumption of Raw Material Mill 2024年4月1日 In the whole process of cement production, the electricity consumption of a raw material mill accounts for about 24% of the total Based on the statistics of the electricity consumption of the raw Summary of intelligent fault diagnosis technology for vertical millsMombasa Cement Ltd ordered a QMK² 24/12 with three roller units for the 5,000 tons per day kiln line In addition, the raw material grinding process will be supported by a QMR² 48/24 For the 4,000 tons per day kiln line Shiva Cement Ltd contracted a quadropol® vertical roller mill for grinding pet coke with a QMK² 32/16quadropol® thyssenkrupp Polysius Grinding Technologies
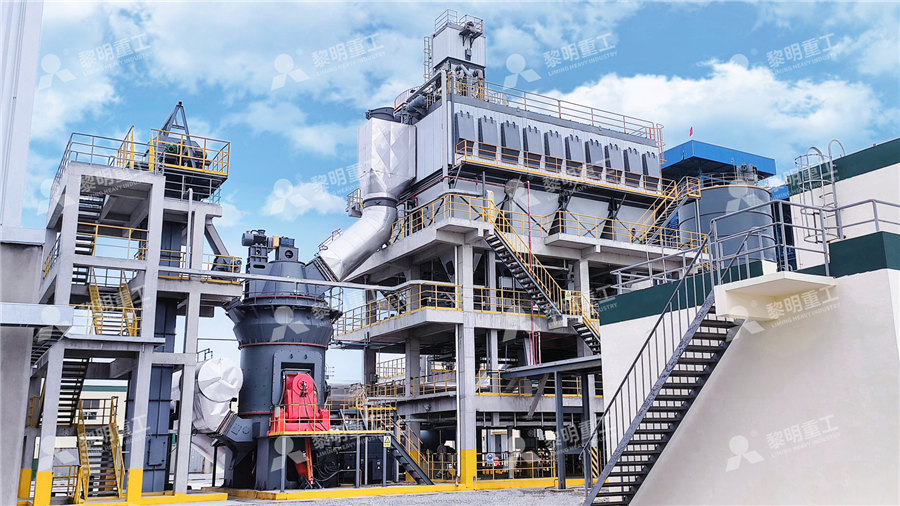
Vertical roller mills FLSmidth Cement
For raw materials and cement clinker, Further, our vertical roller mill solution for cement grinding has an ability to dry, grind and separate within a single unit Offering you more than just a product In addition to our Grinding systems in cement production make up approximately 85 to 90 percent of total plant electrical energy mining ore vertical roller mill hydraulic system Nov 20, 2016 Zhengzhou Jinma Mining Machinery Co, Ltd, Experts in Manufacturing and Exporting Ball Mill, Crusher and 3402 more Products A Verified CN Gold Supplier on mining ore vertical roller mill hydraulic system Large Capacity Vertical Roller Mill Cement Buy Vertical Roller Mill roller mill hydraulic system KOOKSNo matter what type of material has to be ground – cement raw material, cement clinker or granulated blastfurnace slag – and how different their grindability and abrasiveness may be, the MVR mill ensures throughput rates of a different dimension, around the clock, reliably and on the long term Forget about downtimeCement mills and raw mills for high throughput rates Gebr PfeifferVertical cement mill pressurize with a hydraulic system, the pressure acts on the material between the grinding roller and the grinding disc, so as to achieve the purpose of grinding Vertical cement mill is applied for the processing of non Vertical Cement Mill, Vertical Roller Mill Buy
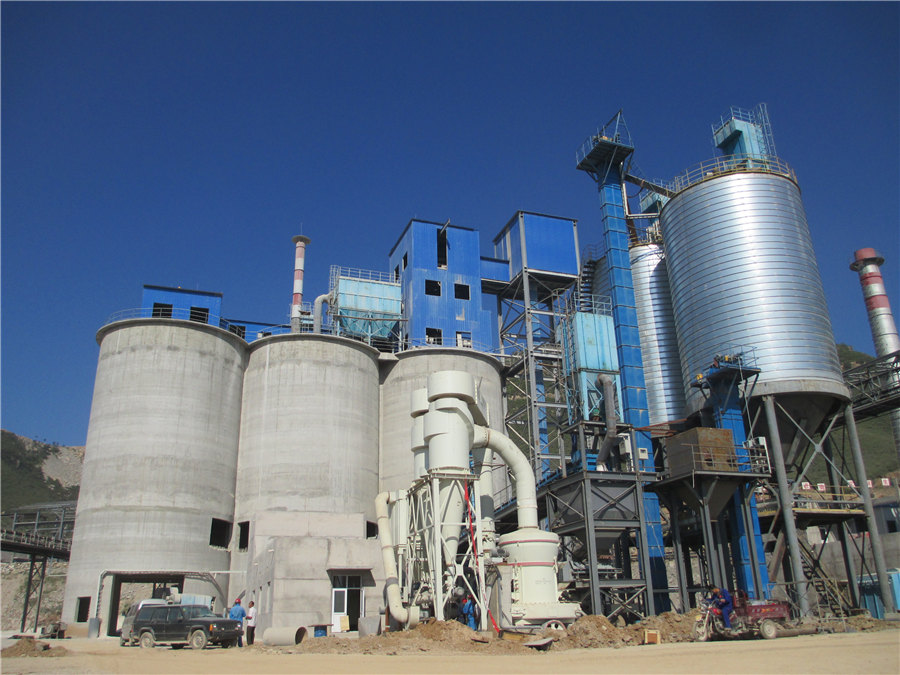
PROCESS OPTIMISATION FOR LOESCHE GRINDING PLANTS
6 – Control Parameters for Loesche Vertical Mills Variable clocking • 50 / 100 ms: Signal detection • 1 second – 10 minutes: Signal evaluation • Material grindability • Material temperature • Material moistureTable 6: Simulation result for the exergy balance of the raw mill Exergy balance of raw mill Material Raw feed Moisture in raw feed Hot gas from kiln Unit kJ/h kJ/h kJ/h Input Simulation 3194 9053 8 Material Raw meal Gas Thermodynamic Analysis of Raw Mill in Cement 2021年1月29日 Vertical roller mills, VRMs, are widely used for grinding raw materials in factories engaged in the extraction and processing of minerals Any machine used for grinding or crushing consumes around Increase productivity of vertical roller mill using seven QC toolsThe cement vertical mill is a type of grinding equipment that merges fine crushing, drying, grinding, and powder separating into a single, which simplifies the production process and has many irreplaceable advantages, such as high grinding efficiency, large feeding size, low power consumption (2030% less power than a cement ball mill), large drying capacity Cement Vertical Mill Vertical Grinding Mill Vertical Mill
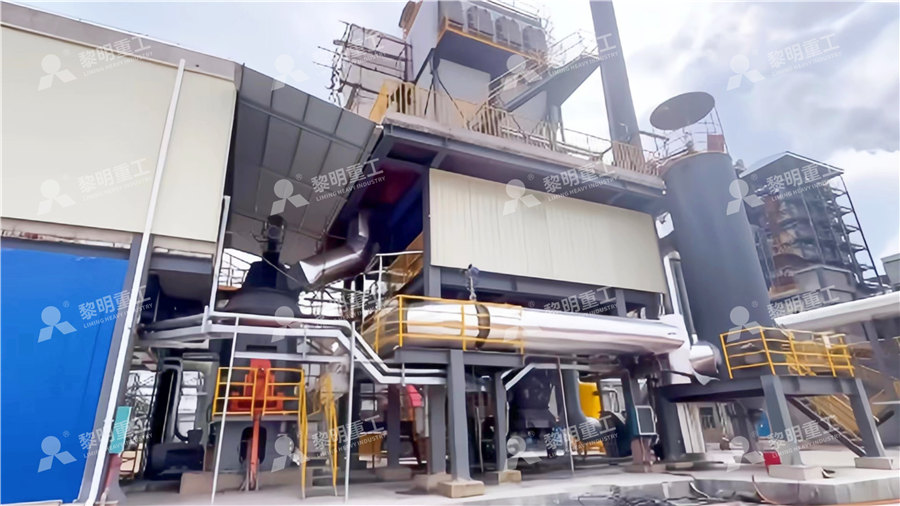
Operational parameters affecting the vertical roller mill
2016年9月1日 The results demonstrated that the VRM unit consumes around 81% (975 kWh/t of raw materials), and 36% (58 kWh/t of raw materials) more energy to grind raw material than the IBAT unit and domestic The vertical roller mill (VRM) is a type of grinding machine for raw material processing and cement grinding in the cement manufacturing processIn recent years, the VRM cement mill has been equipped in more and more cement plants around the world because of its features like high energy efficiency, low pollutant generation, small floor area, etc The VRM cement mill has a Vertical Roller Mill Operation in Cement PlantThe vertical grinding water spray system plays an important role in stabilizing the material bed, especially in the case of more powdery materials or low water content in the raw materials, the effect is more obvious, the toughness and rigidity of the material can be increased, and the material grinding is facilitated, protect the roller surface and the grinding discImportant Operation Tips For Cement Vertical Mill2013年3月1日 Initially, this focused on grinding coal and the cement raw materials, with the adoption of vertical roller mills for cement product grinding with its finer grinding requirements coming more Cements ground in the vertical roller mill fulfil the quality
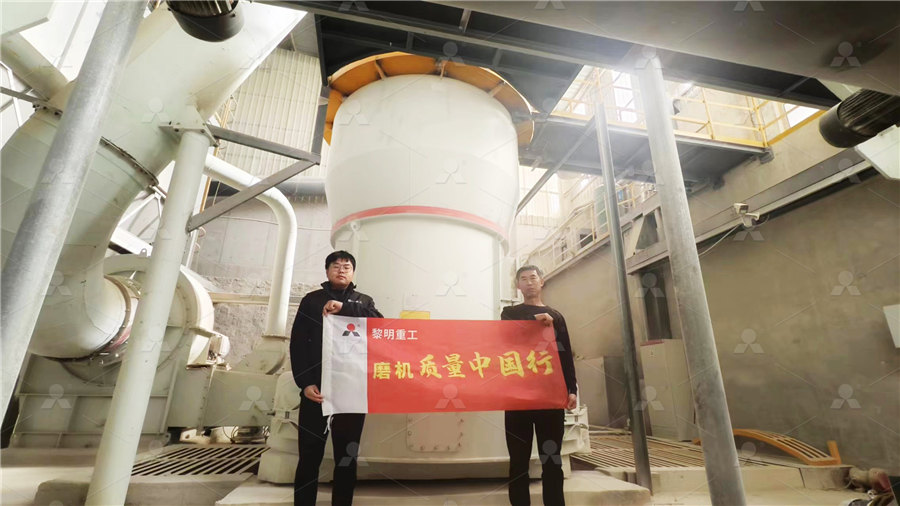
VERTICAL ROLLER MILLS A holistic VRM approach
Figure 2: QMR² for raw material grinding “The quadropol differs from other VRM systems due to the arrangement of the roller units outside of the mill housing Since the hydraulic systems of each roller unit can be controlled independently, a change in an operation from four rollers to two rollers, and viceversa, is easily achieved This also2021年1月22日 In the whole process of cement production, the electricity consumption of a raw material mill accounts for about 24% of the total Based on the statistics of the electricity consumption of the raw material mill system of 1005 production lines in China between 2014 and 2019, it is found that the average electricity consumption of the raw material preparation A Survey and Analysis on Electricity Consumption of Raw Material Mill 2018年9月10日 The simulator was used for the thermodynamic performance of a raw mill (RM) and raw materials preparation unit in a cement plant in Nigeria using actual operating data The raw mill has a capacity (PDF) Thermodynamic Analysis of Raw Mill in Application of Vertical Roller Mill in Cement Industry Vertical roller mill (VRM) technology has become an integral part of the cement industry, offering several advantages over traditional grinding mills Today, this type of grinding Application of Vertical Roller Mill in Cement Production
.jpg)
(PDF) The latest innovative technology for vertical roller mills
2014年4月1日 For decades vertical roller mills have been in use in the cement industry for the grinding of cement raw material and coal Since the 1980's this mill type has also been used for combined or Raw Material Cement Slag amcl Coal separator is installed at the upper parts of the mill The raw material fed through the air lock gate is ground between the rollers and table with the grinding force added by hydropneumatic spring system which consists of hydraulic cylinders, hydraulic accumulators and hydraulic unit, andVERTICAL ROLLER MILLS AMCL2021年3月3日 In this chapter, the term cement is used in its classical meaning: a crystalline compound of calcium silicates and other calcium compounds having hydraulic properties Cement is therefore a hydraulic binder, that is, a material that chemically reacts with water by converting the waterbinder system into a solid matrix with the capacity to agglomerate other solid materialsCement SpringerLinkPDF On Apr 19, 2015, LIAN GUODONG and others published Intelligent Control System for Cement Raw Mill Quality Based on Online Analysis Find, read and cite all the research you need on ResearchGate(PDF) Intelligent Control System for Cement Raw Mill
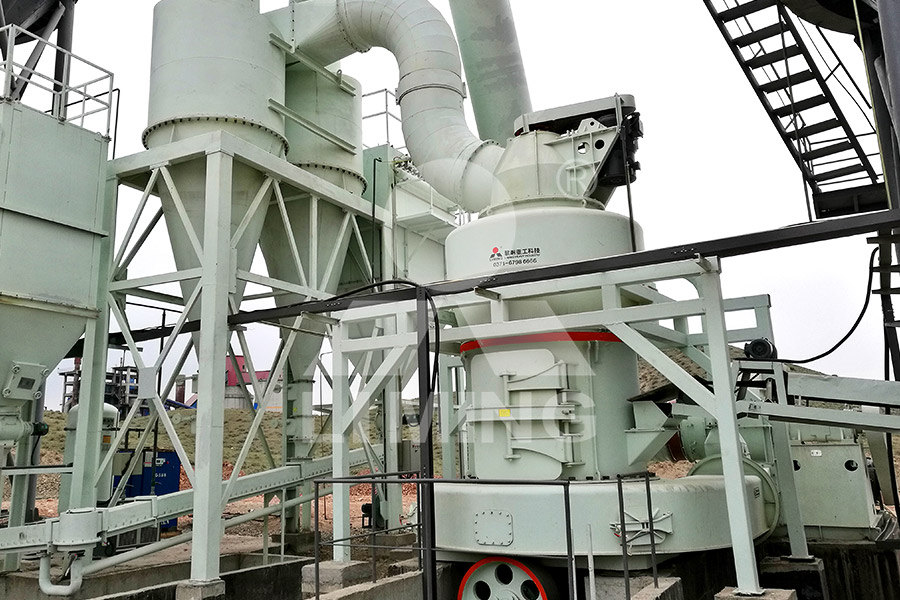
Full article: Reliability assessment of the vertical roller mill based
1 Introduction The vertical roller mill (VRM) is heavy mechanical equipment that used in the cement materials industry to process cement, slag, and coal cinder (Pani Mohanta, Citation 2015)The equipment always needs to work in the environment of heavy load, high temperature, high pressure, high corrosiveness, electromagnetic radiation interference, and multifield In terms of power saving, the following includes an account for you: Economic benefit analysis: the economic benefit caused by the high running rate, power saving and operation maintenance cost of vertical mill system If one ton of cement saves 45kwh/t power, one day produces 5000T cement, one year works 300 days, and electricity cost is 07 yuan per kilowatt hour, you can VERTICAL CEMENT MILL Xinxiang Great Wall Machinery Co, IOP Conference Series: Materials Science and Engineering PAPER OPEN ACCESS Analysis of Raw Mill Machines Maintenance in Cement Industry To cite this article: R M Sari et al 2020 IOP Conf Ser: MaterAnalysis of Raw Mill Machines Maintenance in Cement IndustryRaw mill is generally called cement raw mill, raw mill in cement plant, it refers to a common type of cement equipment in the cement plantIn the cement manufacturing process, raw mill in cement plant grind cement raw materials Raw mill Cement Plant
.jpg)
Vertical Raw Mill for Cement Raw Meal Grinding in
So the vertical raw mill particularly suitable for the grinding of cement raw meal in cement factory The vertical raw mill in cement industry has been applied in the field of medicine and food because of its high grinding efficiency, can dry up to 2023年6月8日 Assessment of the thermodynamics efficiency of a cement vertical raw mill using Aspen Plus and artificial intelligence models June 2023 DOI: 1021203/rs3rs/v1Assessment of the thermodynamics efficiency of a FLSmidth Cement flsmidthcement 3 OK™ Raw Mill QUALITY AND PROFITIMPROVING FEATURES Vertical Roller Mills (VRMs) have been the standard option for raw materials grinding in the cement industry for several decades FLSmidth Cement has supplied the global cement industry with leading VRM designs for allOK RAW AND CEMENT MILL2023年12月4日 A vertical roller mill (VRM) is a grinding equipment used for the size reduction of minerals, cement Xu P, Xie Q (2022) Analysis of vertical roller mill performance with changes in Jensen LRD, Fundal E, Møller P, Jespersen M (2011) Wear mechanism of abrasion resistant wear parts in raw material Vertical Roller Numerical Investigation of Vertical Roller Mill Operation Using
.jpg)
Analysis of vertical roller mill performance with changes in material
2022年5月31日 Mineral crushing is the main source of energy consumption in mineral processing According to statistics, this consumption accounts for about 35–50% of the total cost of the mine (Curry et al, 2014), or even higherIt may also account for 18% of the global electrical energy consumption (NapierMunn, 2015)More efficient crushing equipment needs to be The motor as well as the gearing are wearfree and the entire drive is built in the same dimensions as conventional gearboxes It is suitable for replacements of existing vertical mill drives CONCLUSION With the trend towards large single VRMs for raw material and cement grinding the reliability of the drive systems are only becoming more Drive Systems for Vertical Roller Mills INFINITY FOR CEMENT 2015年3月25日 1 The working principle of the hydraulic system vertical roller mill The hydraulic system ofvertical mill is an important system, the main function ofthe hydraulic system is to break the grinding roller, which is when the internal grinding cavity wear parts wear, can stop open on both sidesofthe grinding roller mill, to replace the inside parts or repairThis type vertical roller Hydraulic system vertical roller mill operation PDF SlideShareTable 3 Power Consumption Of Roller Press Grinding System Overall, we can conclude the three tables: After the longterm operation, although unit raw material grinding power consumption of the cement roller press grinding system is still low, the indexes of the vertical roller mill grinding system are very close to it, among which the output power of the vertical mill and the roller Comparison Of Vertical Roller Mill And Roller Press Mill
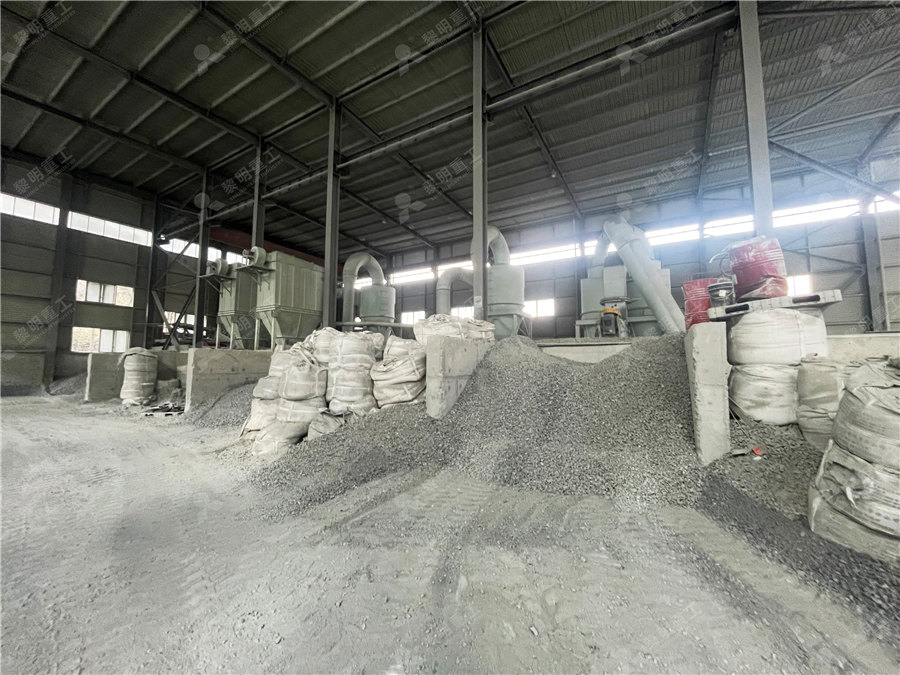
Fault Diagnosis and Root Cause Failure Analysis of Press Roller Mill
2019年7月31日 This case study is to identify and evaluate the root cause for failure of a roller press mill Cement plant has a heavy crushing operation the roller#8217;s top surface is eroded, which is replaced by hard metal deposition by welding In manufacturing, most of the