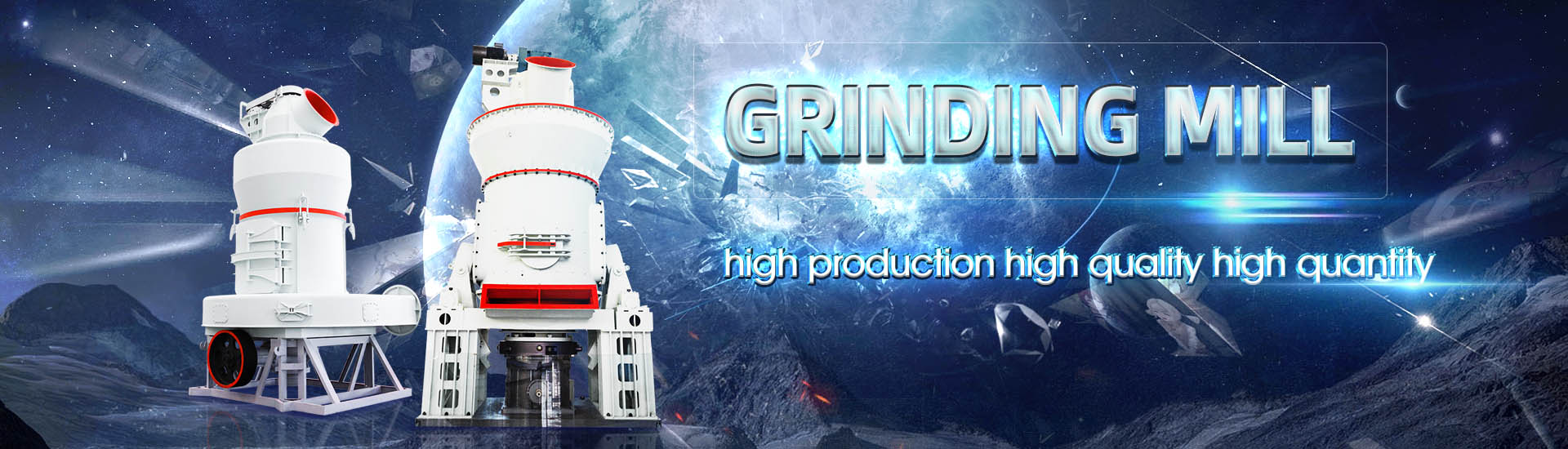
The function of the circulating air valve of the slag vertical mill What is it used for
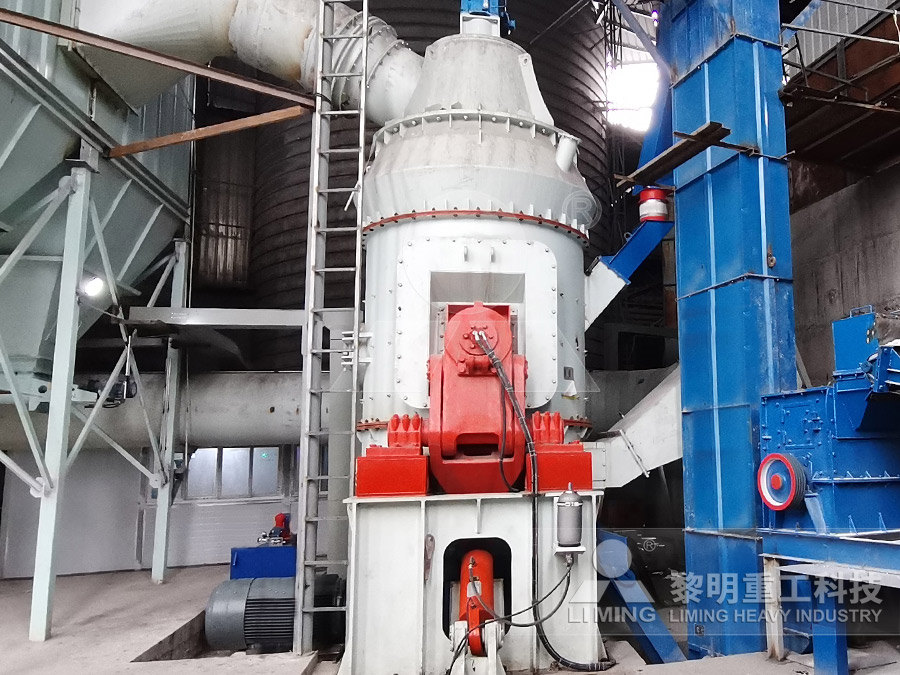
2 µm 5 µm Loesche
slag in roller grinding mills (vertical airswept grinding mills) is a technology introduced by Loesche The first use of a Loesche mill, with a grinding track diameter of only 11 metres, was used as 2017年4月1日 The control of the circulating load is achieved by adjusting the pressure drop over the mill comprising out of the gas flow and the solid loading inside the mill Higher classifier Operational parameters affecting the vertical roller mill 2005年2月1日 Steelmakers have made attempts to reduce slag volumes in the individual unit processes and to strive towards slagless steelmaking by recycling slags internally A much (PDF) Industrial uses of slag The use and reuse of iron and 2007年2月1日 The finished material is transported by the circulating mill air directly to a bag filter, where it is collected and then conveyed to the pulverised slag silo A portion of the Slag grinding with the Polysius Roller Mill in China
.jpg)
Vertical roller mill for raw Application p rocess materials
In case that the proposed external circulating system is provided to the vertical mill, the uncrushed materials jumped out from the table fall through gas inlet box to and collected by the a vertical roller mill (VRM) • Surpasses the classic methods if the controlled process demonstrates significant disturbances • A high degree of attention to the process states is required in order PROCESS OPTIMISATION FOR LOESCHE GRINDING PLANTSVertical roller mill is a type of grinder used to grind materials into extremely fine powder for use in mineral dressing processes, paints, pyrotechnics, cements and ceramics It is an energy Vertical roller mill Wikipedia2015年3月1日 The model explicitly incorporates mill design data (mill diameter, grinding table diameter, air classifier geometry) and operational conditions (coal feed rate, air flow rate, air Modelling of vertical spindle mills Part 2: Integrated models for E
.jpg)
Ironmaking Blast Furnace SpringerLink
2023年6月15日 Its function is to protect the hearth bottom from slag and alkali metal erosion and reduce the damage caused by molten iron circulation to the hearth side wall Its depth is about 2011年10月27日 This not only caused a loss of confidence in the material but such cases have at times been confused with BOS slag In fact, the descriptions of the failures have usually revealed that the slag was used with no form of quality control, and in some cases the users were not even aware that of what type of slag was being usedBasics of slag production Article on the slag industry from Global Slag2019年12月9日 Metallurgical slags are produced at a massive rate of over 750 Mt/year, and carry a thermal energy equivalent to 40 Mt/year of coal The potential mineral and thermal energy values of slags are in the order of $22 b and $3–6 b per year Such attractive figures, together with tightening legislation on disposal of slag and the carbon footprint associated with the loss Granulation and Heat Recovery from Metallurgical Slags2007年2月1日 The hot air used for drying is generated by a hot gas generator The finished material is transported by the circulating mill air directly to a bag filter, where it is collected and then conveyed to the pulverised slag silo A portion of the circulating mill air is returned to the mill, which helps to save thermal energy Insulation and heatingSlag grinding with the Polysius Roller Mill in China
.jpg)
Modeling Based on the Extreme Learning Machine for Raw Cement Mill
2015年1月1日 Adjusting the amount of wind mill is generally circulating the air through the control valve opening to achieve From the above, we can see that the two most important quality evaluations are the mill pressure and raw material fineness in A recirculating pump can be used to recirculate the hot water in the piping This ensures that heated water is available instantaneously when taps are opened A circulator is used on both types of hot water systems; those with storage tanks and those with instantaneous tankless water heaters What is a circulator and how does it work?Circulator Basics Answers To The Most Common QuestionsValve Functions and Basic Parts These valves are available in three body patterns: horizontal, angle, and vertical Figure 24: Lift Check Valve Flow to lift check valves must always enter below the seat As the flow enters, One application of solenoid valves is in air systems such as those used to supply air to pneumatic valve actuatorsValves Engineering LibraryThe superficial gas velocity in a bubbling fluidized bed system is kept around 1–2 m/s depending on the particle characteristics In a circulating fluidized bed system, it may go up to 5–10 m/s typically as given in Van den Aarsen []The solids, in circulating bed systems, not only circulate in the outer loop through the return leg, but there is also internal circulation of the solids in Hydrodynamics of Circulating Fluidized Bed Systems
.jpg)
INVESTIGATION OF THE CLASSIFICATION OPERATION IN A COAL
Samples around the vertical spindle mill (ie coal fed to the mill, pulverised fuel and mill reject) were collected by the conventional equipment used at the plant in daily operation 2013年3月1日 This study investigated a mathematical model for an industrialscale vertical roller mill(VRM) at the Ilam Cement Plant in Iran The model was calibrated using the initial survey's data, and the Cements ground in the vertical roller mill fulfil the quality relationship which can be used to calculate the reduced recovery This recovery, along with the bypassed solids, is used to predict the complete size distribution for the underflow product R r = e 4X 1 (eq 1) e4X + e4 –2 Where R r = Recovery to underflow on corrected basis X = Particle diameter /D50 C particle diameterThe Sizing Selection of Hydrocyclones 911 Metallurgist2016年8月30日 The vertical and directional drilling are the key technologies for the exploration and exploitation of oil and gas resources in deep formations Meanwhile, they are also the very important ways to exploit deep geothermal Overview on vertical and directional drilling
.jpg)
Five essentials for optimizing hammermill operations
At higher rpms, a rotary valve will approximate a continuous feed to the mill, but air intake is not an integral part of the valve, so it requires a separate air intake on both sides The rotary valve can meet class 1 construction for isolation, which 2022年6月25日 Depending on different heating methods, the common drying systems can be divided into fuel oil/gas heating drying system, electric heating drying system, vacuum drying system and heat pump drying system and so on [7], [8]As is known, the fuel oil/gas heating drying system and electric heating drying system have the advantages of simple structure, Study on the effect of circulating air volume on the performance 2016年10月5日 In this chapter an introduction of widely applied energyefficient grinding technologies in cement grinding and description of the operating principles of the related equipments and comparisons over each other in terms of grinding efficiency, specific energy consumption, production capacity and cement quality are given A case study performed on a EnergyEfficient Technologies in Cement Grinding IntechOpen2013年1月15日 Understanding of the properties of slags is a prerequisite in optimizing their functions towards the making and refining of steel Important contributions towards this objective have been made (PDF) Understanding the Properties of Slags ResearchGate
.jpg)
Effect of Cooling Rate and Slag Modification on the Copper
2020年7月31日 31 The Form of the CopperRich Phase in the Cooling Results Figure 3 shows the process used for analyzing one polished crosssection in the vertical direction in the crucible The first picture reveals a macro view of the polished crosssection, while the second micrograph shows an overall view of it at low magnification, where the dark gray area (a) is the crucible Tube mills had been used for grinding, but the energy efficiency level was lower Therefore, the introduction of highly efficient grinding equipment was anticipated Descriptions The vertical roller mill has high energy efficiency and the installation space is smaller compared with tube mills These days, the vertical roller mills have been widelyVertical roller mill for raw Application p rocess materials2020年8月12日 This study shows the performance of a currently running vertical roller coal mill (VRM) in an existing coalfired power plant In a power plant, the coal mill is the critical equipment, whose An investigation of performance characteristics and energetic bution predominantly between 200 and 400mm is used, diluted by fuel ashes Fig3 gives an example of pressuremeasurement results Fig3a shows pressures measured along the height of the riser during a typical full load run with coal (bed temperature 850 C, air ratio 12) with all air entering from the bottomFluidization Characteristics of Circulating Fluidized Bed Boilers
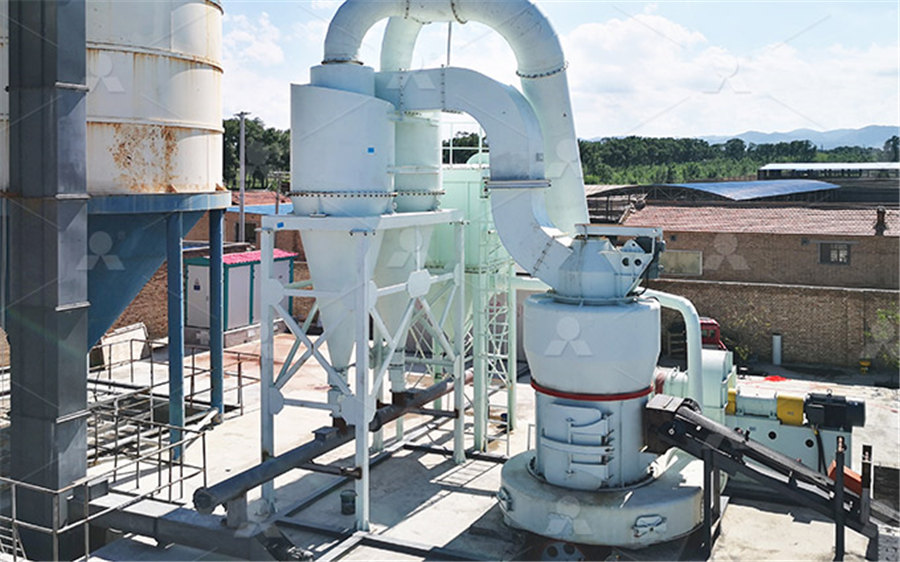
Improvement of cement performances through the use of
Improvement of cement performances through the use of grinding aids in vertical roller mill PD’Arcangelo, MMagistri – Mapei SpA, Milan, Italy Abstract Due to the stringent requirement of energy saving, the use of vertical roller mills for cement grinding is now common Even though the reliability and operation stability of modern VRM is very2020年10月9日 Increased inplant recycling and lower quality raw material in terms of alkali content drive the alkali load in the blast furnace (BF) to higher levels Excessive load of alkalis, primarily potassium, has several negative effects on the BF operation, which necessitates means to control the removal of potassium from the BF One method to improve the removal is by The Quantitative Effect of Blast Furnace Slag Composition and 2016年8月1日 Little difference between the size distribution of the classifier feed and classifier reject indicated that the classification performance of the classifier is poor Classifier circulating ratios of six surveys are all between 7 and 10 Air rate has a direct influence on the classifier circulating ratioPerformance of the static air classifier in a Vertical Spindle MillCement mill separator, or cement separator, is a type of equipment that was widely used in the cement grinding system and raw mill system of cement plantsThe function of the separator is to separate the finesized particles from the coarsesized particles, so as to avoid material condensation and over grinding in the mill, and improve the milling system’s grinding efficiencyCement Milll Separator Cyclone Air Separator in Cement Plant
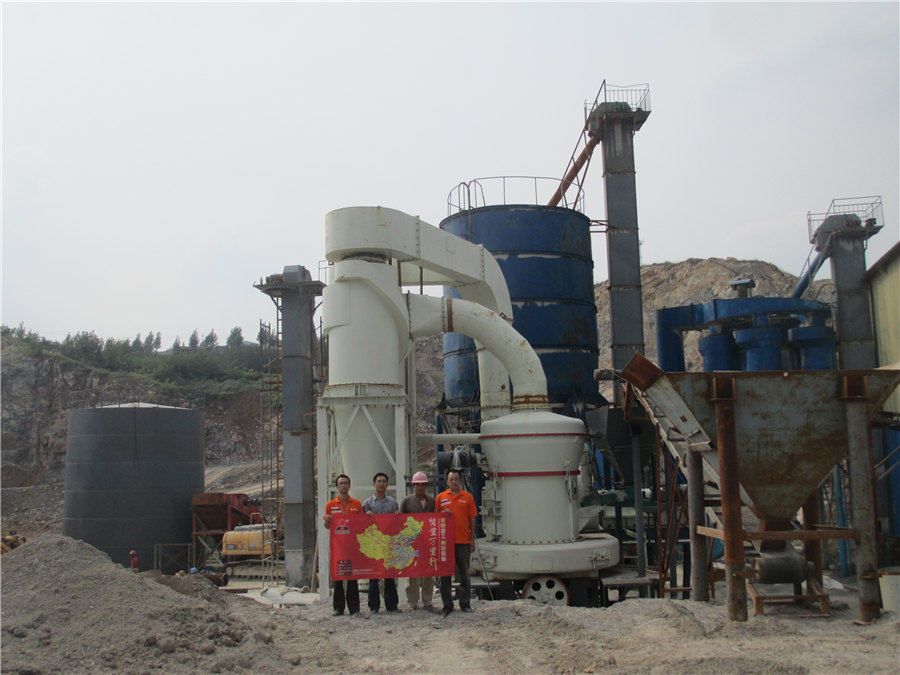
Ball Mill Circulating Load Formula 911Metallurgist
2015年10月9日 Calculating a grinding circuit’s circulating loads based on Screen Analysis of its slurries Compared to %Solids or Density based Circulating load equations, a more precise method of determining grinding circuit tonnages uses the screen size distributions of the pulps instead of the dilution ratiosPulp samples collected around the ball mill or rod mill and 2019年10月24日 Due to its high content of Ca(OH)2, carbide slag becomes a potential alternative to limestone as the inbed desulfurizer of circulating fluidized bed (CFB) boilersFeasibility Study of Using Carbide Slag as InBed Desulfurizer in vertical mill Combined drive In this classifier mill, as shown in Figure 2b, the classifier wheel and rotor disc are mounted on one shaft and rotate at the same speed As a result, the mill is smaller, has a lower purchase cost, and requires less installed horsepower than the vertical mill However, the apFigure 1 Vertical air classifier How to operate an air classifier mill to meet your fine grinding goalsIt is well known in the industry that good classification system performance is vital to efficient ball mill circuit performance But what is meant by good classification system performance, and how is it achieved? Unfortunately, the perceived complexity of classification systems, and the daytoday time demands placed on the practicing metallurgist, all too often put the lowhanging fruit of A guide to maximising ball mill circuit classification system
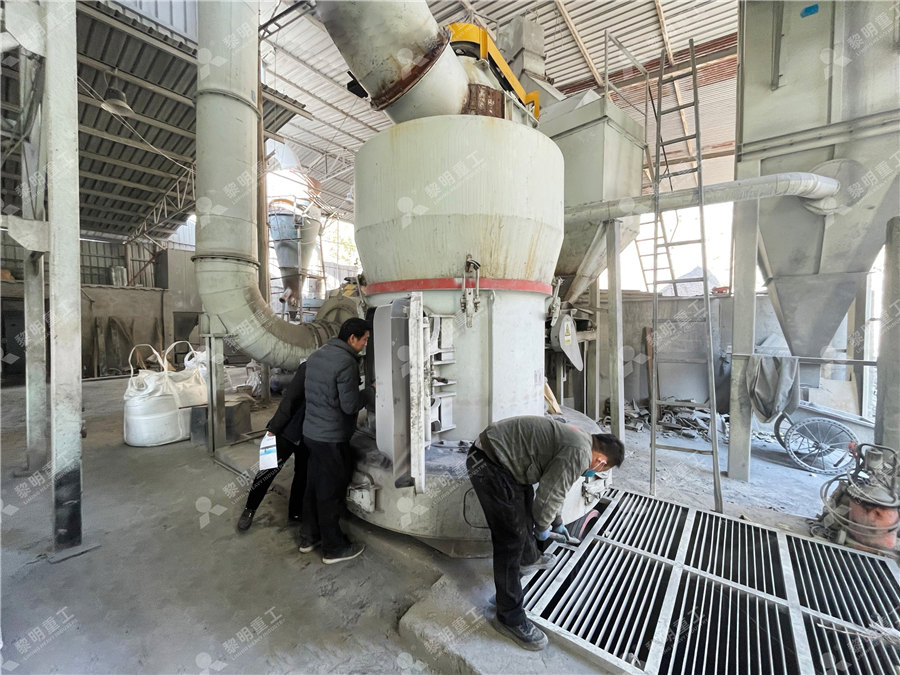
Circulating Valve an overview ScienceDirect Topics
2015年12月6日 Well Control During Well Test Operations Howard Crumpton, in Well Control for Completions and Interventions, 2018 12615 Reverse circulating valve: single operation This tool is used at the end of the well test to reverse hydrocarbons out of tubing Pressure applied to the tubing or, more commonly, the annulus will shear a rupture disk opening a circulation path Vertical roller mill is a type of grinder used to grind materials into extremely fine powder for use mill [1] Overview The vertical roller mill is a kind of grinding machine for cement, raw material, cement clinker, slag and coal slag It has the benefits of simple structure and low ring by adjusting the air valve, Vertical roller mill WikipediaPrevious Post Next Post AIR SEPARATORS 40 AIR SEPARATORS 41 Introduction Separators are utilized in a closed circuit grinding system for the purpose of separating (classifying) the fine and coarse particles of the feed The fine particles are passed through the separator to become finished product while the coarse particles are returned to the AIR SEPARATORS INFINITY FOR CEMENT EQUIPMENT2020年11月4日 The vertical roller mill is an important crushing and grading screening device widely used in many industries Its classification efficiency and the pressure difference determine the entire Effects of Blade Parameters on the Flow Field and Classification
.jpg)
An energy based comparison of vertical roller mills and tumbling mills
2015年3月10日 The Institute of Mineral Processing at the Montanuniversitaet Leoben in cooperation with the company CEMTEC has developed a pilot scale, 200 mm table diameter, vertical roller mill for energy controlled laboratory testsThe mill provides the technical options to vary process parameters like airflow, mass flow, grinding force and classifier speed in a wide 2020年4月7日 Monitoring and diagnosis of coal mill systems are critical to the security operation of power plants The traditional datadriven fault diagnosis methods often result in low fault recognition rate or even misjudgment due to the imbalance between fault data samples and normal data samples In order to obtain massive fault sample data effectively, based on the Modeling of Coal Mill System Used for Fault Simulation MDPI2012年9月26日 1 Introduction During the last decades, the continuous casting process has made enormous advances and more than 90% of the world steel production is now continuously cast []In this process, the liquid steel is poured into a watercooled copper mould through a submerged entry nozzle (SEN), see Figure 1 []At this stage the solidification process beginsMould Fluxes in the Steel Continuous Casting Process2021年1月29日 Vertical roller mills, VRMs, are widely used for grinding raw materials in factories engaged in the extraction and processing of minerals Any machine used for grinding or crushing consumes around Increase productivity of vertical roller mill using seven QC tools
.jpg)
Design of continuous circulation sub for gas drilling and the
2016年7月1日 The current gas drilling is always challenged by a rather low ROP and low drilling efficiency due to a huge volume of formation water invasion in a well2021年11月3日 The technological factors required to improve the operational properties of granulated metallurgical slags demanded in the building industry have been analyzed In order to satisfy these factors, a new technology for hydrovacuum granulation of slag melts (HVG) has been developed It is shown that the main advantage of the proposed HVG process is the A new technological approach to the granulation of slag melts of 2015年8月1日 Use of calcined dolomite can greatly improve the lining life Recently, slag splashing has become an established practice to prolong converter life The residual slag in the converter is conditioned for chemical composition and temperature after tapping and is splashed by a violent nitrogen flow around the converter wallRole of Slag in Converter Steelmaking – IspatGuru2001年10月1日 Hence, the treatment of circulating loads is essential for the energy saving and environment protection As the breakage of coal happens in the closed industrial VSP with high air pressure, studies are mainly conducted on machines with similar structure in the lab or pilot scale (Werner et al, 1999; Schaefer, 2001; Ozcan and Benzer, 2013; Chi et al, 2015; Zhou et al, Loesche vertical roller mills for the comminution of ores and minerals