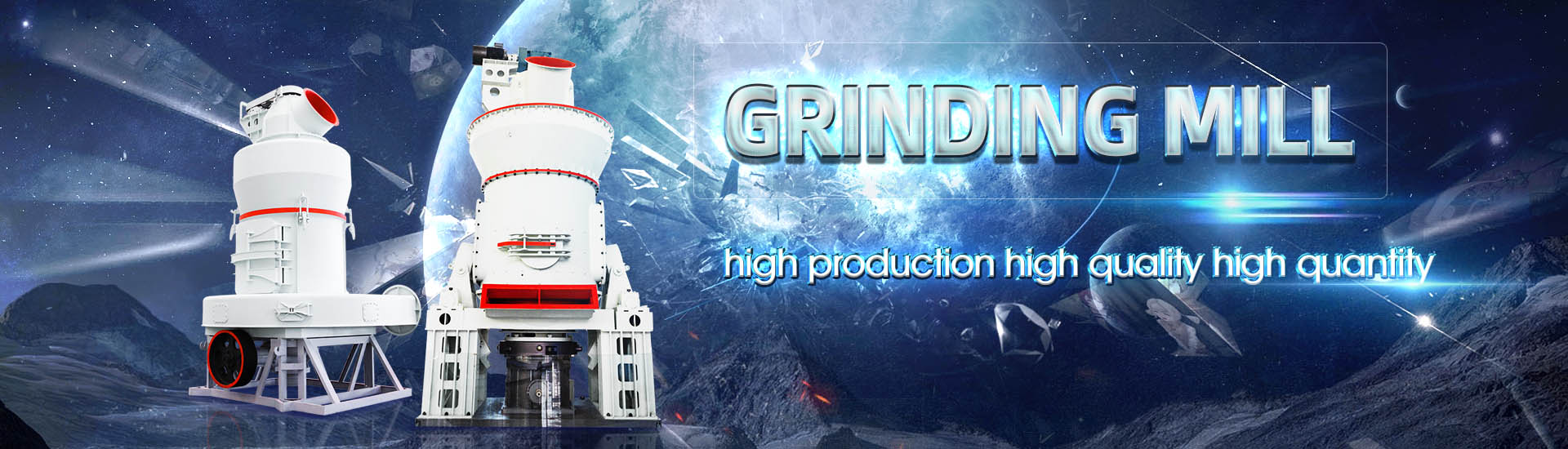
What are the iron oxide processing equipment
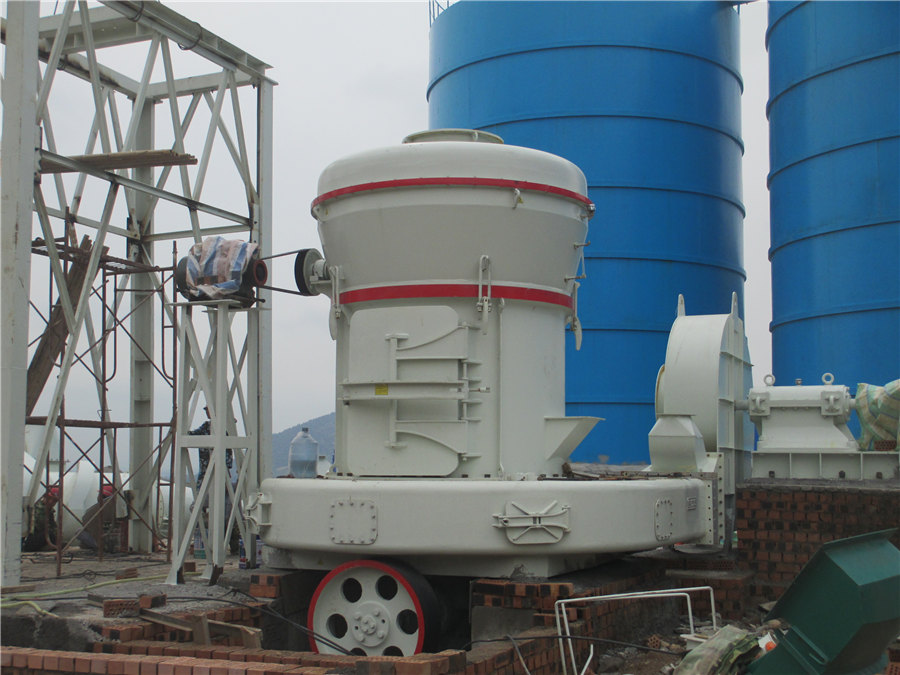
From Ore to Iron with Smelting and Direct Iron Reduction
2017年10月17日 The Hismelt process employs a single smelt reduction vessel (SRV) where iron oxide fines are injected deep into hot metal melt, which instantly reduces the ore to produce iron and carbon monoxide Flux and coal are also injected into the bath near the bottom, which 2024年4月26日 Iron ore, a naturally occurring mineral composed primarily of iron oxides, is mined and processed to extract iron for various industrial applications This article provides a comprehensive overview of the iron ore Iron Ore Processing: From Extraction to Manufacturing2017年10月10日 Blast furnacing, smelting and direct iron reduction are the current ironmaking processes Iron is made by reacting iron ore (iron oxide and impurities), coke (a reductant) and limestone (CaCO 3) in a blast furnace Iron Ironmaking 101 – From Ore to Iron with Blast FurnacesThe primary objective of iron making is to release iron from chemical combination with oxygen, and, since the blast furnace is much the most efficient process, it receives the most attention here Alternative methods known as direct Iron processing Smelting, Refining, Alloying Britannica
.jpg)
Introduction to Iron ore Pellets and Pelletizing processes
2013年2月23日 There are four stages involved in the production of iron ore pellets These stages consist of (i) raw material preparation, (ii) formation of green balls or pellets, (iii) induration of the pellets, and (iv) cooling, storage and 2024年1月1日 Ironmaking is the process of refining iron oxides in iron ores into metallic iron The earth’s crust is rich in iron, accounting for 42% of the total elements, ranking fourth With no Ironmaking SpringerLink2017年1月1日 Effective technology for a complex wasteless processing of the iron ores has been designed and includes three main components (plats): comminution plant, briquette plant, pigment plant The(PDF) Effective Processing of the Iron OresCalcium oxide is a basic oxide and reacts with acidic oxides such as silicon dioxide present in the rock Calcium oxide reacts with silicon dioxide to give calcium silicate The calcium silicate melts and runs down through the furnace IRON AND STEEL chemguide
.jpg)
Iron processing Ores, Smelting, Refining Britannica
The most widely distributed ironbearing minerals are oxides, and iron ores consist mainly of hematite (Fe2O3), which is red; magnetite (Fe3O4), which is black; limonite or bogiron ore (2Fe2O33H2O), which is brown; and siderite 2017年10月10日 Fe 3 O 4 decomposes when heated to ferrous oxide (FeO) and ferric oxide (Fe 2 O 3) via Fe 3 O 4 → FeO + Fe 2 O 3 A specialized type of coal, called hard coal, is used to make coke, a porous form of carbon Coke is a Ironmaking 101 – From Ore to Iron with Blast FurnacesFor instance, Fe 3 O 4 is a mixed iron oxide with Fe in different oxidation states as Fe 2 + and Fe 3 +Due to the flexible oxidation state of Fe, iron oxides can assume different phases and singlecrystalline structures with very different chemical and physical properties (cf Table 1 for an overview) This flexibility of their oxidation state makes iron oxides very interesting to be used Iron Oxide an overview ScienceDirect Topics2023年11月7日 Generally, black oxide or black iron oxide refers to the oxide of iron known as magnetite (Fe3O4) that is formed when a ferrous metal is exposed to special oxidising chemicals It is a type of conversion coating, thus the Black Oxide Coating – How It Works, Benefits Types
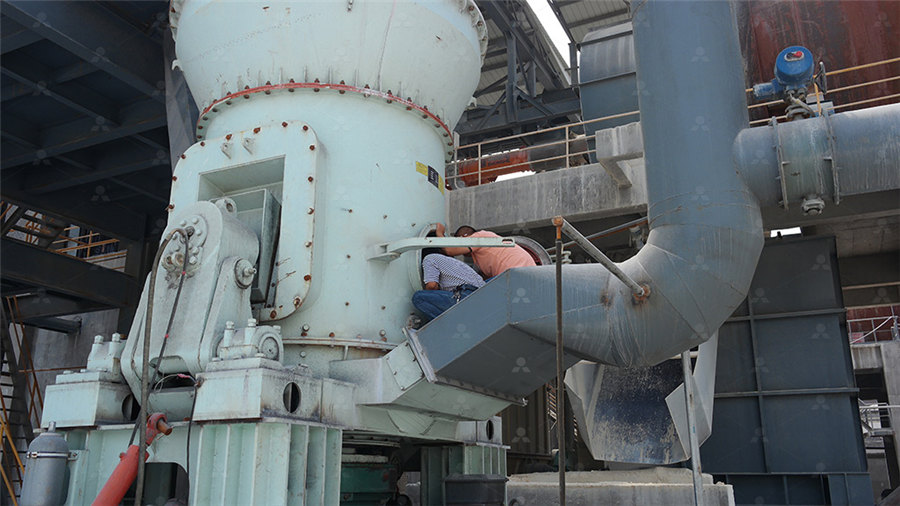
Introduction to Iron ore Pellets and Pelletizing processes
2013年2月23日 Recrystallization of iron oxides is essentially a physical process in which smaller particles consolidate into larger ones with the loss of surface energy During the recrystallization of iron oxides, continued growth of iron oxide crystals imparts sufficient strength During the process, the grain growth for hematite starts at around 1100 deg Ccc: Estruagua Static screens, also known as stationary screens, are used to separate materials based on their size and shapeThey consist of a stationary frame or structure that is fitted with a series of screens or meshes Materials are fed onto the screen, and larger materials are separated from smaller onesWhat are The Different Types of Industrial Screening Equipment2019年8月23日 Iron processing description from its geology mineral property to how to extract mineral from rock and placer deposit, Oxide Chemical Formula Fe2O3, αFe2O3 (hematite), Fe2+Fe3+2O4 (magnetite) How much the iron ore processing equipment?Iron Processing Equipment, Process Flow, Cases JXSC Machine2024年7月8日 The matching of the equipment capacity to the processing requirements eliminates the formation of bottlenecks and improves overall efficiency Oxidized ores may contain minerals such as iron oxides which are beneficial to the cyanide leaching process since they counter the effect of sulfides on gold extractionMastering Oxidized Gold Ore Processing Techniques JXSC
.jpg)
Gold processing Refining, Smelting Purifying Britannica
2024年11月14日 gold processing, preparation of the ore for use in various products For thousands of years the word gold has connoted something of beauty or value These images are derived from two properties of gold, its colour and its chemical stabilityThe colour of gold is due to the electronic structure of the gold atom, which absorbs electromagnetic radiation with 2017年1月1日 Effective technology for a complex wasteless processing of the iron ores has been designed and includes three main components (plats): comminution plant, briquette plant, pigment plant(PDF) Effective Processing of the Iron Ores ResearchGate2022年1月1日 Since the magnetic susceptibilities of limonitic iron oxides are the smallest of the iron minerals in oxidized iron ores, they are most difficult to recover with high intensity or high gradient magnetic separators Because the crystal water in limonitic iron oxides reports to the iron ore concentrate, the final concentrate grade is limitedPhysical separation of iron ore: magnetic separation ScienceDirectA number of iron objects, including cannons, remain from the Han period (202 BC to AD 221) The Bible also includes many mentions of iron For example, a long passage in the book of Job describes the mining of iron Other passages IRON Chemistry Explained
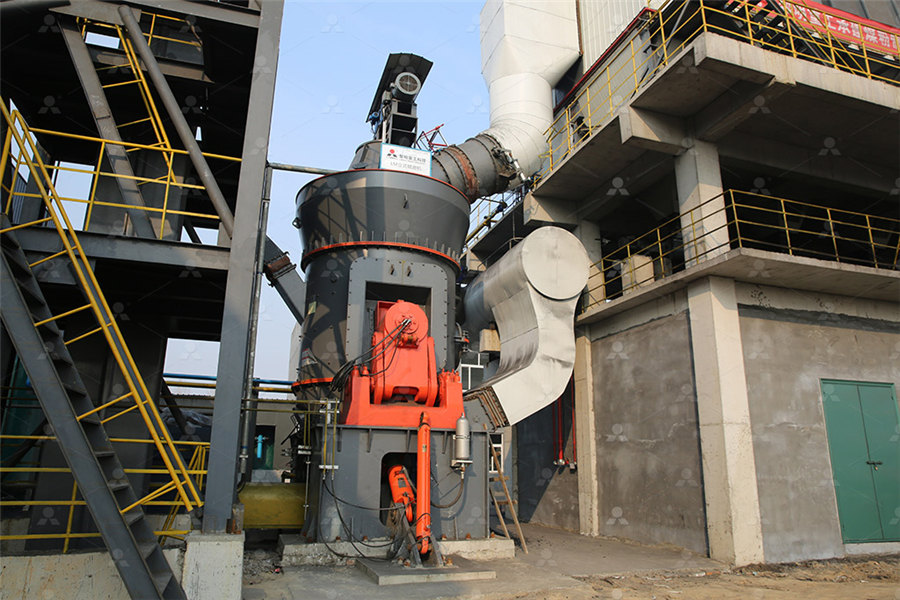
Steel Pickling: The Essential Guide MachineMFG
2024年8月9日 Fig3 Structure of iron oxide scale The scale on the surface of carbon structural steel or lowalloy steel is loose, porous, and cracked In addition, the scale is repeatedly bent, straightened, and conveyed along with 2017年10月1日 The iron oxide precipitated on the filter media was ferrihydrite, which acted as the catalyst during the oxidation of iron [61] Another filter media, called Constructed Soil Filter (CSF) has been utilized by Nemade et al for iron remediation from groundwater by setting the preliminary concentrations of iron as 5 and 10 mg/LRecent strategies for the removal of iron from water: A review2021年5月18日 21 Iron (III) Oxides Iron (III) oxide is, of course, a compound that exhibits four different crystalline polymorphs: αFe 2 O 3, βFe 2 O 3, γFe 2 O 3, and εFe 2 O 3Hematite and maghemite usually appear in nature, while beta and epsilon structures are generally synthetic oxides [10, 11]In general, the iron (III) oxides anions arrange in closepacked structures, Synthesis, Properties, and Applications of Iron Oxides: Versatility Micaceous Iron Oxide (MIO) is iron oxide in a form that resembles mica, a highly structured, layered mineral (crystalline Fe 2 O 3) Minerals with this highly layered structure are termed lamellar When MIO pigments are ground into smaller, finer particles, they tend to cleave along their layers, revealing flat, shiny faces that act like TECH NOTE 521 MIO COATINGS – WHAT ARE THEY? Dulux
.jpg)
How to Process Copper Ore: Beneficiation Methods and Equipment
2023年3月13日 There are different methods of processing copper mines, such as preferential flotation, bulkseparating flotation, etc for copper sulfides, and sulphidizing flotation, fatty acid flotation, etc for copper oxidesAluminum, for example, is the most common metal in the Earth's crust, occurring in all sorts of minerals However, it isn't economically worthwhile to extract it from most of these minerals Instead, the usual ore of aluminum is bauxite which contains from 50 70% of aluminum oxideAn Introduction to the Chemistry of Metal Extraction2014年5月7日 Once the ore is mined, it’s transferred to a processing plant for electrolytic processing or smelting Prior to the development of advanced technology mining equipment, freeing manganese from open pit rock beds required a lot more manpower and timeManganese Mining and Processing: Everything you Need to Know2000年10月1日 This layer is called the passive layer The passive layer is composed primarily of chromium and iron oxides The amount of chromium and iron oxide varies depending on the type of stainless steel (eg, 410, 416, 316, etc) Layers with more chromium are generally more passive; that is, more resistant to corrosionSpotting, Staining, and Corrosion of Surgical Instruments
.jpg)
Iron Powder: Characteristics,types,Specifications Additive
2023年9月15日 Iron oxide pigments are produced by oxidizing iron powder Used in paints, plastics, rubber, ceramics, Safe and efficient operation of iron powder processing equipment requires proper procedures and training Safety Require personal protective equipment – respirators, gloves;If you had to name the technologies that had the greatest effect on modern society, the refining of the heavy metal element iron would have to be near the top Iron makes up a huge array of modern products especially carbonrich, How Iron and Steel Work HowStuffWorksIron Oxide Processing Systems Iron oxide, also known as ferric oxide, is an inorganic compound with the formula Fe 2 O 3 It is one of the three main oxides of iron, and occurs naturally as the mineral hematite It is the main source of iron in the steel industry Iron oxide is ferromagnetic, meaning it is attracted to magnetic sources, and is Iron Oxide Drying Processing The ONIX Corporation2021年1月1日 The main iron oxides phases presented in IOT are hematite of processing the ore The iron compounds present in the to this end, availability of physical space, equipment, and Iron Ore Tailings: Characterization and Applications
.jpg)
Granulating Iron Oxide Pigments for Use in Concrete
Iron oxide can be either natural or synthetic and as such, may be produced for use as a pigment in a variety of ways Some pigments may even utilize a blend of both natural and synthetic sources of iron oxide Natural Iron Oxide Natural iron oxides have long been used as a pigment, of which prehistoric cave paintings are a prime exampleIron Oxides (Hematite and Goethite) Iron minerals normally are found in bauxite as: Hematite (Fe 2 O 3) Goethite (FeO(OH) or Fe 2 O 3 H 2 O) The solubility of iron oxides increases with increase in temperature, and free caustic Each processing route utilizes different equipment to achieve its process targetsChemical Processing of Bauxite: Alumina and Silica 2022年5月1日 Iron oxide nanoparticles are becoming progressively significant for the improvement of innovative biomedical and nanotechnology requests The keywords iron oxide nanoparticles, Fe 3 O 4 nanoparticles and magnetite nanoparticles have been utilized as a research object in the gross database of articles from the Web of Science The results of these Iron oxide nanoparticles: Preparation methods, functions, 2017年10月17日 Figure 1: Steelmaking byproducts for blast furnace (BF), basic oxygen furnace (BOF) and electric arc furnace (EAF) processes Source: World Steel Association (worldsteel) The first step in the production of steel or cast iron alloys is the reduction of iron ore—which contains iron oxide and gangue or mineral impurities—to unrefined, reduced iron formFrom Ore to Iron with Smelting and Direct Iron Reduction
.jpg)
How iron is made material, manufacture, making, history, used
1 After processing, the ore is blended with other ore and goes to the blast furnace A blast furnace is a towershaped structure, made of steel, and lined with Scrap which isn't recycled eventually turns into iron oxide, or rust, and returns to the ground2016年8月24日 This special issue of Mineral Processing and Extractive Metallurgy presents a selection of the best metallurgy papers delivered at the very successful international ‘Iron Ore 2015’ conference held at the Perth Convention and Exhibition Centre, Australia, on 10–12 July 2015 This was the seventh in the series of biennial conferences featuring recent Full article: Iron ore processing Taylor Francis OnlineNickel processing Extraction, Refining, Alloying: The extraction of nickel from ore follows much the same route as copper, and indeed, in a number of cases, similar processes and equipment are used The major differences in equipment are the use of highertemperature refractories and the increased cooling required to accommodate the higher operating temperatures in nickel Nickel processing Extraction, Refining, Alloying BritannicaIn general, the industry uses iron oxide or iron ore mixed with fine sand, and mineral coal or charcoal for steel production This charcoal is used in the production process with two functions Then, the liquid steel is solidified in Steel production process: what are the steps? Blog
.jpg)
(PDF) i) Direct Reduced Iron: Production
2016年3月30日 the iron oxide feedstock, especially because of a more uniform size, better chemical consistency, as well as the guaranteed higher furnace availability Extra cost of pellets is compensated by 2017年12月14日 The iron concentrate was mainly imported from Brazil and selfprovided by Jinshandian The iron concentrates were dried and ground by the high pressure roller The ground iron concentrates were pelleted by drum and disc pelletizers The qualified green pellets were subjected to grate, rotary kiln, and ring cooler successivelyA case study on largescale production for iron oxide pellets: 2019年11月19日 PDF A tremendous amount of research has been done on refining the flotation process for iron ore and designing the reagents which go into it This Find, read and cite all the research you (PDF) Flotation of Iron Ores: A Review ResearchGateThe iron ore production has significantly expanded in recent years, owing to increasing steel demands in developing countries However, the content of iron in ore deposits has deteriorated and lowgrade iron ore has been processed The fines resulting from the concentration process must be agglomerated for use in iron and steelmaking This chapter shows the status of the Iron Ore Pelletizing Process: An Overview IntechOpen
.jpg)
IOCG Iron Oxide Copper Gold Ore Deposits 911Metallurgist
2015年1月22日 IOCG Iron Oxide Copper Gold Ore Deposits goes with porphyries as they are also loosely associated with a large felsic intrusions and form at moderate depths, 911 Metallurgist is a trusted resource for practical insights, solutions, and support in mineral processing engineering HighPerformance Equipment for Mineral The common iron ore hematite (iron oxide) changes to metallic iron at ∼1250°C, 300°C below the melting point of iron (1538°C) Addition of flux helps the melting of oxide ores, chemically reacts with unwanted impurities (silicon compounds), and assists in the formation of slag Calcium oxide, in the form of limestone, is commonly used as fluxRoasting an overview ScienceDirect Topics2024年8月5日 The transition to green steel production is pivotal for reducing global carbon emissions This study presents a comprehensive technoeconomic analysis of various green steel production methods, including hydrogen reduction and three different electrolysis techniques: aqueous hydroxide electrolysis (AHE), molten salt electrolysis, and molten oxide electrolysis Economics of Electrowinning Iron from Ore for Green Steel 2020年2月1日 Production of Iron Oxide Nanoparticles by CoPrecipitation method with Optimization Studies of Processing Temperature, pH and Stirring Rate, Beh Hui Hui, Optimization processing condition that produce smallest crystallite size of 73657 nm was 50 °C, pH 1140 and 550 rpm by using Design of Expert software (DOE)Production of Iron Oxide Nanoparticles by CoPrecipitation

Hydrometallurgical nickel and cobalt plants and processes
expertise in iron precipitation, nickel and cobalt producers benefit from environmentally acceptable iron residue storage or further use Manganese, an impurity often associated with these raw materials, can be precipitated as manganese oxide either together with iron or separately From iron and manganese removal, the pregnant leach