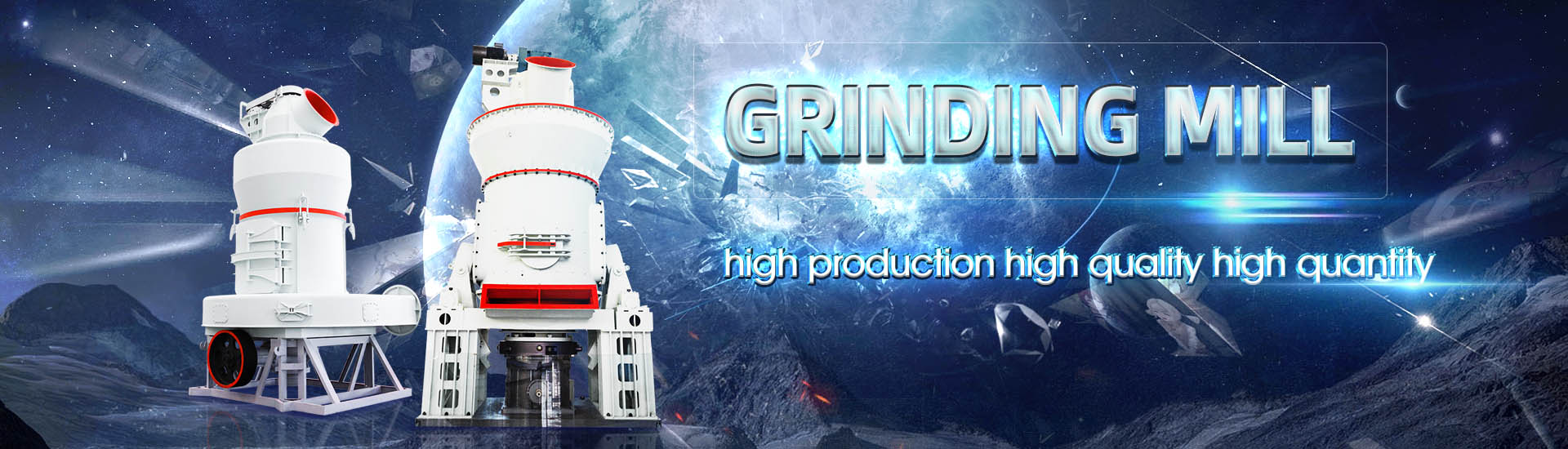
Coking plant process
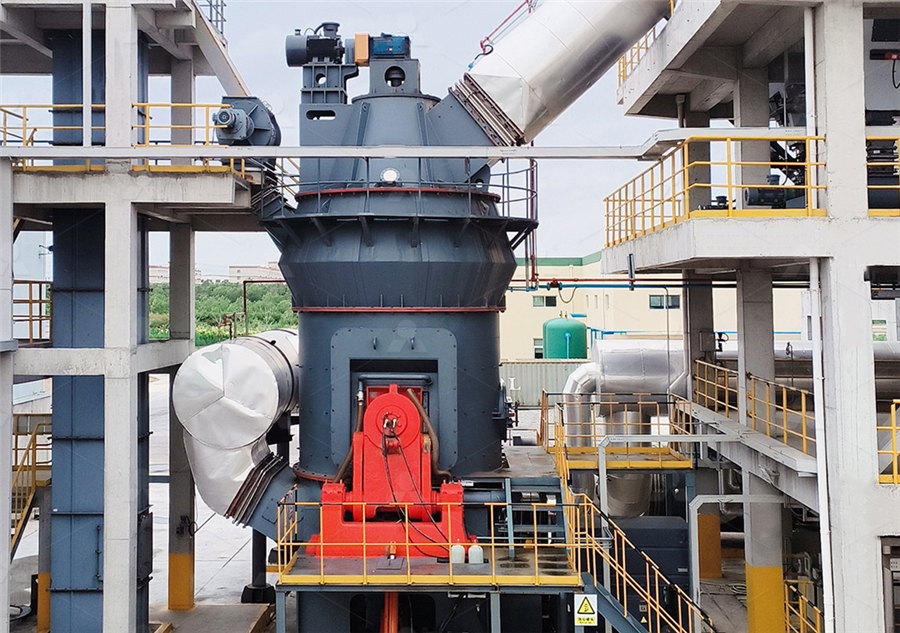
Coking Wikipedia
Coking is the process of heating coal in the absence of oxygen to a temperature above 600 °C (1,112 °F) to drive off the volatile components of the raw coal, leaving behind a hard, strong, porous material with a high carbon content called coke Coke is predominantly carbon Its porous structure provides a high surface 展开A new coking process is designed to accept viscous feedstocks (including vacuum residua) from a conventional residuum heater in a coking plant and continuously discharges volatiles and dry Coking Plant an overview ScienceDirect TopicsCoking plant To make steel in a blast furnace, coal must first be turned into coke Coke has a dual role in the steelmaking process First, it provides the heat needed to melt the ore, and Raw materials Coking plant ArcelorMittal2019年1月1日 Noncoking coals have higher ash content and are typically used in thermal power plants as steam coals Coking coal is the type of coal which on heating in the absence of air Industrial perspective of the cokemaking technologies

Coke (fuel) Wikipedia
Coke is a grey, hard, and porous coalbased fuel with a high carbon content It is made by heating coal or petroleum in the absence of air Coke is an important industrial product, used mainly in iron ore smelting, but also as a fuel in stoves 2019年7月19日 Coke making is the fundamental process related to the traditional blast furnace route Coke provides the reducing actions, increases temperature through its thermal energy, Coke Making: Most Efficient Technologies for Greenhouse 2019年11月14日 The optimization and control model for the coking process takes the coking energy consumption as optimization target; the coal blend moisture, the target temperature, Intelligent Optimization and Control of Coking Process2022年8月5日 Coking is a process in which raw materials are thermally decomposed into prod ucts with lower boiling points Different types of coking processes include delayed(PDF) Coking ResearchGate
.jpg)
Exergy analysis and optimization of coking process
2017年11月15日 Taking the exergy loss minimization as the optimization objective, an optimization model of coking process is established based on the material balance and energy balance The optimization problem is solved with the practical production data of a coking plant The minimum exergy loss and the optimal design parameters are obtained2020年12月29日 Types of coking process Delayed Coking Fluid Coking Flexi Coking In this article we will see Delayed Coker unit What is Delayed Coking? Delayed coking is a process, which is used to convert vacuum residue feed COKING PROCESS IN REFINERY The Engineering A modern coking plant: the Carbonaria plant in Duisburg–Schwelgern, operated by ThyssenKrupp since 2003 ArcelorMittal's Prosper coking plant in Bottrop with its chimney and lowpressure gasometer (Thyssen construction) A coking factory or a coking plant is where coke and manufactured gas are synthesized from coal using a dry distillation processCoking factory Wikipedia2019年11月14日 Coking is a complex process It features a large time constant, strong nonlinearities, and timevarying characteristics To achieve good control performance, it is important to obtain a precise COT in a realtime fashion; but this is difficult owing to restrictions imposed by the structure of a cokeoven and operating costsIntelligent Optimization and Control of Coking Process
.jpg)
Coking plant Global Energy Monitor
A coking plant is used to produce coke (coking coal) from metallurgical coal Coking plants consist of coke ovens (aka coking ovens, coke furnaces, coking furnaces) Coal is used to reduced iron ore to produce pig iron (aka hot metal) in the blast furnace (BF)However, it cannot be burned directly in the furnace because it contains numerous harmful byproducts that gets generated2022年8月5日 This process combines fluid coking with coke gasification, which, similar to fluid coking, is a fluidized bed process developed from catalytic fluid cracking technology A fluidized bed is added to the process, which acts as a gasifier in which coke from the heater is reacted with steam and air in a fluidbed gasifier to produce a gas of low heating value (20–40 BTU/sCF) Coking IntechOpen2012年8月22日 Due to the larger distance of the measuring point from the plant, and to the less coking capacity, the BaP concentrations near coking plant B are lower than those near plant A The annual BaP concentrations lie at 08 ng/m 3 and complies with the relevant ambient air standard of 1 ng BaP/m 3 as given by the EU (EU, 2004)Environmental Control and Emission Reduction for Coking Plants2022年8月5日 The delayed coking process can be applied to all residues in general, as they are not limited to constraints such as metal, sulphur, and asphaltene content Heavy residues(PDF) Coking ResearchGate
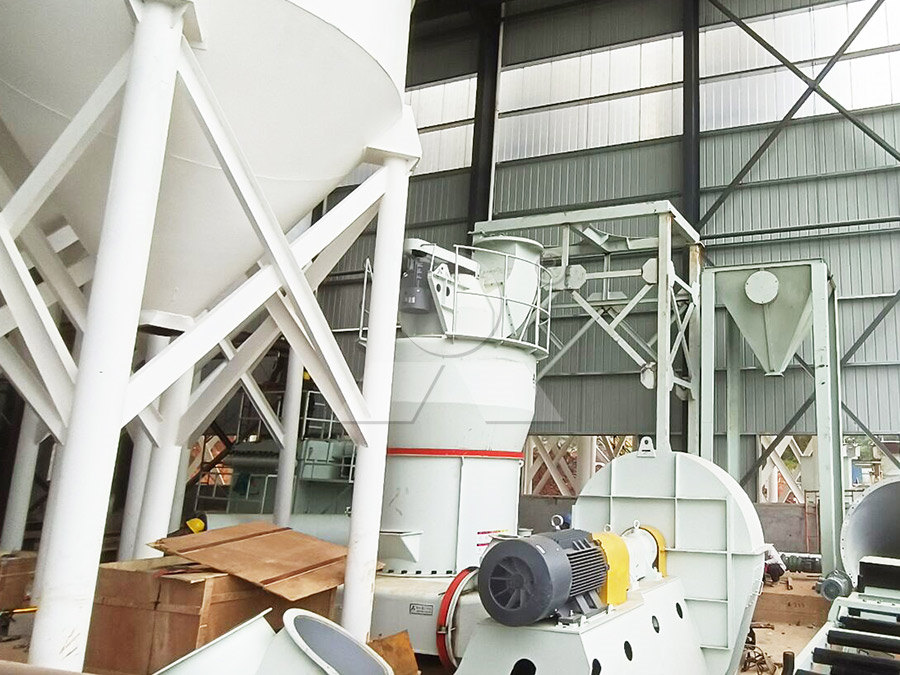
Characteristic Analysis of VOCs Emitted from a Typical Coking Plant
2019年5月21日 The coking industry is an important VOCs emission source in China Due to the complex production process, the VOCs emission characterization is lack, so a typical mechanized coking plant was selected to study Samples were collected from coke oven chimney, coke pushing, coal charging and coke oven top GC/MS was used to analyze the samples, and 2023年7月15日 Coking chemistry is the subject of relative theories, technologies, processes, and equipment of process where main material coal in the condition of isolating air is researched, and coal is transformed into coke (or semicoke) and raw gas after physicochemical action like thermolysis and coking, and the raw gas is purified and separated to obtain coal tar and Coking Chemistry SpringerLinkA coker or coker unit is an oil refinery processing unit that converts the residual oil from the vacuum distillation column into low molecular weight hydrocarbon gases, naphtha, light and heavy gas oils, and petroleum cokeThe process thermally cracks the long chain hydrocarbon molecules in the residual oil feed into shorter chain molecules leaving behind the excess carbon in the Coker unit WikipediaCOKE MAKING COAL CARBONISATION : Coking coals are the coals which when heated in the absence of air, first melt, go in the plastic state, swell and resolidify to produce a solid coherent mass called coke SINTERING PROCESS A Sinter Plant typically comprise the following subunits as shown belowCoke OvensSinterBFBOF Route SAIL
.jpg)
Methods for Modeling and Optimizing the Delayed
2023年2月2日 The technological processes of processing raw materials and manufacturing products in oil refining, petrochemicals, and other industries proceed in chemicaltechnological systems (CTS) [1,2]These CTS include a 2021年7月22日 water that is generated by the coke making process Top The byproduct plant gas train The gas treatment processes in the byproduct plant typically consist of the following plant items, arranged in the order in which they are described Top Primary cooler The first step in Steelmaking: The Coke Oven ByProduct Plant accci2019年1月1日 About 90% of the coke produced from blends of coking coals is used to maintain the process of iron production in the BF (Diez et al, 2002, Diez, 2016, Liu et al, 2009) The coking process has remained unchanged for over 100 years (Zhang et al, 2013) Coke is the indispensable basis for the BF processIndustrial perspective of the cokemaking technologiesAll of the heat necessary for coking is provided in the heater, whereas coking takes place in the coke drum; hence, the process is called “delayed coking” The hot product vapors and steam from the top of the drum are quenched by the incoming feed in the fractionator to prevent coking in the fractionator and to strip the lighter components of the vacuum residue feedDelayed Coking FSC 432: Petroleum Refining John A Dutton e
.jpg)
Raw materials Coking plant ArcelorMittal
To make steel in a blast furnace, coal must first be turned into coke Coke has a dual role in the steelmaking process First, it provides the heat needed to melt the ore, and second, when it is burnt, it has the effect of ‘stealing’ the oxygen from the iron ore, leaving only the pure iron behind In the coking plant, coal is heated in the absence of oxygen to 1250c2024年8月20日 Petroleum coke ranked among the top 10 major types of US petroleum products consumed in 2022, with 255,000 barrels consumed per day, according to the US Energy Information Administration However, the process of creating petroleum coke — called “coking” — remains largely unfamiliar to the average American consumerWhat Is Coking? What Happens to the Coal? Cadence2024年2月28日 The coking wastewater was collected from the effluents of a coking wastewater treatment plant after Anoxic/Oxic (A/O) process in Liuzhou, China The temperature, COD, pH, and UV254 and Vis380 levels in the coking wastewater were found to be 36–40 °C, 75–81, 235–275 mg L −1 , 26–30, and 050–058Treatment of Coking Wastewater Using Hydrodynamic Cavitation The new Schwelgern coke plant Pioneering coke plant technologies are part of our daily business The effi ciency and environmental performance of our plants are renowned worldwide Tailor made complete coke oven plants from a single source – that’s our commitment and your advantage gained from a partnership with us 500 coking plants worldwideThe new Schwelgern coke plant ThyssenKrupp
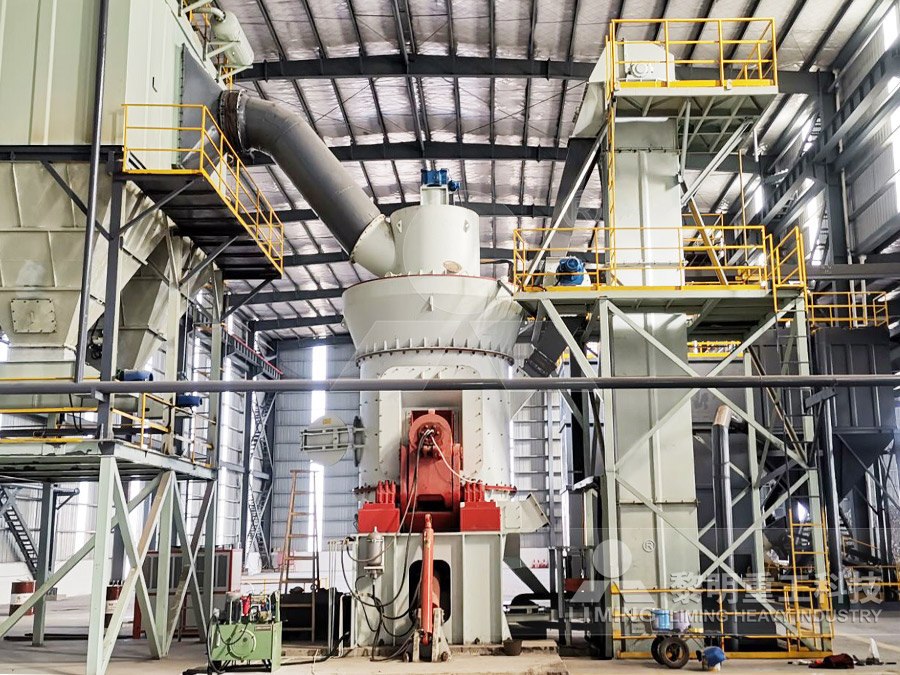
122 Coke Production
The coking process produces approximately 338,000 L of coke oven gas (COG) per megagram of coal charged (10,800 standard cubic feet of COG per ton) During the coking cycle, volatile matter driven from the coal mass passes upward through cast coke ovens, other plant combustion processes, or sold 1223 Emissions And Controls Particulate, 2015年3月21日 Existing energy resources are struggling to cope with the current energy requirements It is therefore, necessary to increase energy efficiency and reduce greenhouse gases emissions in integrated steel A review of coke making byproducts Coke and 2015年3月9日 Fig 1 Typical flow diagram of a byproduct coke oven plant Environmental issues The coke oven is a major source of fugitive air emissionsThe coking process emits particulate matter (PM), volatile organic Understanding Coke Making in Byproduct Coke 2020年6月19日 ABSTRACT The source profiles, emission factors, and chemical reactivity of volatile organic compounds (VOCs) generated by two typical coking plants, one employing a nonrecovery process and the other, a mechanical process, in Shanxi Province, a major coking hub in China, were determined for different segments of coke production during normal operations Segmentbased Volatile Organic Compound Emission
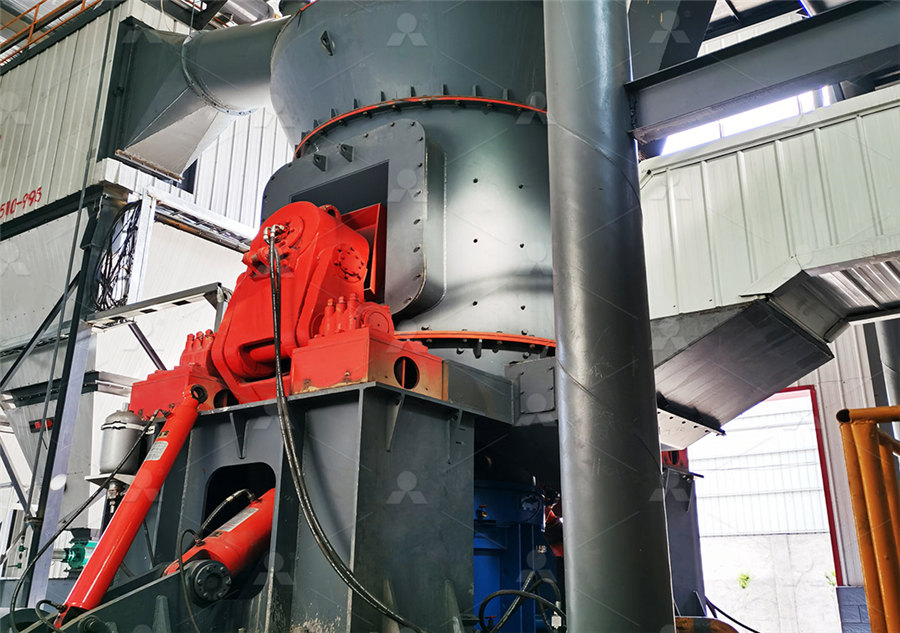
Chemistry and geology of coal: nature, composition, coking
2023年1月19日 Coking Coking coal is an essential raw material for the production of iron and steel Coke is a solid carbonaceous residue formed from coking coal (a lowash, lowsulphur bituminous coal, also known as metallurgical coal), which is used in make steel and other iron products []Coke is produced by burning coal at temperatures up to 1000 °C in the absence of Coke’s role in steelmaking is to provide the heat needed to melt the ore, whose natural state is iron oxide, the rust you see on iron after it has been exposed to the atmosphere Coke also ‘steals’ the oxygen from the iron ore, so that it can become iron In the coking plant, coal is heated to 1250c in the absence of oxygen, removing impurities and creating coke, a porous Coking plant ArcelorMittalNo wonder that they set the style for industrial architecture in the Ruhrgebiet Between 1957 and 1961 the Zollverein plant was extended by the addition of a coking plant And soon after that its 192 furnaces had to be increased to 304, making it the largest industrial plant of Zollverein Mine and Coking Plant World Heritage Site – ERIHFuels and Combustion Dipak K Sarkar, in Thermal Power Plant, 2015 Caking, coking An essential property of coal that is important for the production of coke is cakingWhen caking coals are heated they soften, swell, become plastic, then form lightweight, porous coke particlesCoking Coal an overview ScienceDirect Topics
.jpg)
Study on emissions of volatile organic compounds from a typical coking
2021年1月15日 Here, a representative coking chemical plant is selected for the emission characterization, which locates in Tangshan, Hebei province (E118°, N39°) 2019), but more reasonable since individual step in the whole coking chemical process is calculated separately and actual treatment of coke oven gas is consideredDelayed coking is a process that occurs in batch In order to make a semicontinuous process, it is always employed as pairs of reactors, wherein one reactor is under reaction, the other is in the decoking step, and so on The delayed coking process occurs Delayed coking as a sustainable refinery solution DigitalRefiningFluid coking can process heavier VDR and gives a higher distillate yield (and lower coke yield) than delayed coking Figure 69 shows a schematic diagram of flexicoking A gasifier is added for conversion of some or all coke produced in Fluid and FlexiCoking FSC 432: Petroleum RefiningA 4drum delayed coking unit in a petroleum refinery A delayed coker is a type of coker whose process consists of heating a residual oil feed to its thermal cracking temperature in a furnace with multiple parallel passes This cracks the heavy, long chain hydrocarbon molecules of the residual oil into coker gas oil and petroleum coke [1] [2] [3] Delayed coker Wikipedia
.jpg)
Tutorial: Delayed Coking Fundamentals
MODERN DELAYED COKING PROCESS The delayed coker is the only main process in a modern petroleum refinery that is a batchcontinuous process The flow through the tube furnace is continuous The feed stream is switched between two drums One drum is online filling with coke while the other drum is being steamstripped, cooled, decoked, pressureProcess flow sheet: Illustrated in Figure Figure 321 Flow sheet of coking of coal 323 Functional role of each unit (Figure 321): (a) Coal crusher and screening: At first Bituminous coal is crushed and screened to a certain size Preheating of coal (at 150250˚C) is done to reduce coking time without loss of coal qualityLecture 32: Coke production National Institute of Technology, 2016年6月22日 In either coke or noncoked coal, the quality of the coal affects the quality of the steel Metallurgical coke is made from bituminous coals by a distillation process Ash deposited by the coal must be kept to a minimum, preferably below 10% of the original mass The ash can lower furnace temperatures and leave noncombustible materialsHow does coke and coal play into steel making?2024年4月12日 Sampling process Four stable coking furnaces—A, B, C, and D—of coking plants in North China were randomly selected The designed production capacity of coking furnaces A and B was 15 million Composition, characteristics, and treatment technologies of
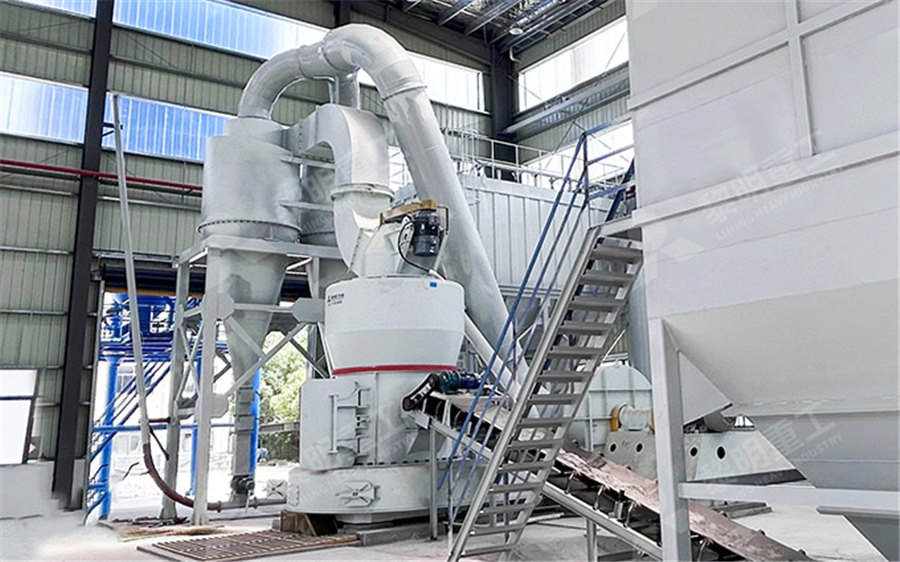
Qualifying and Quantifying the Emissions of Volatile Organic
2022年8月26日 The research subject is the coking process of an integrated steel plant in Taiwan There are four coke oven batteries, two sets of wet quenching equipment, and two sets of dry quenching equipment in the coking process of the steel plant The sampling of VOCs was conducted mainly at the No 4 coke oven battery and No 4 coke dry quenching equipmentRecommended resources may include advanced courses on coking plant management, advanced process control, and specialized training in environmental compliance By following established learning pathways and best practices, individuals can progressively develop their skills in the coking process and unlock new career opportunities in the energy, steel, and Coking Process: The Complete Skill Guide RoleCatcherCoking is the most severe thermal process used in the refinery to treat the very bottomofthebarrel of crude oil, ie, vacuum residue Because of the high severity of thermal cracking during coking, the residue feed is completely converted to gas, light and medium distillates, and coke with no production of residual oilCoking FSC 432: Petroleum Refining John A Dutton e Coking process has historically been a very polluting process especially with the evolution of sulfur and nitrogen oxides from the coke ovens In Europe and the United States, only a few coking plants remain in operation and the emissions, byproducts and waste from these plants are very closely controlledCoking Industry SOLVAir®