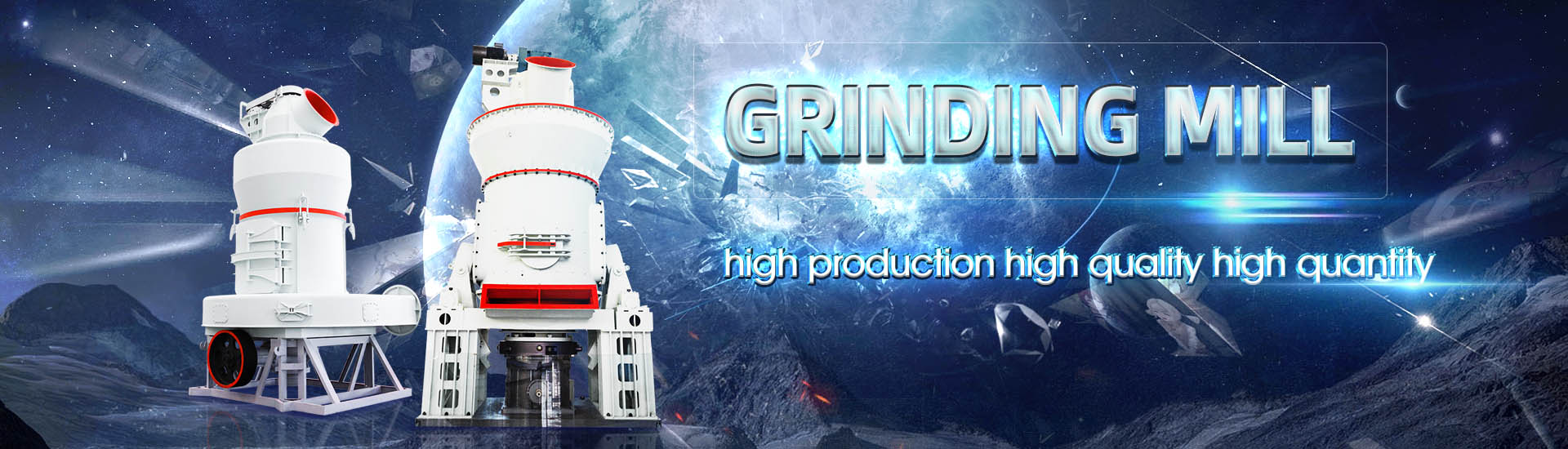
How to install the grinding roller of ore grinding mill
.jpg)
Raymond Roller Mill PartsUltimate Guide Fote Machinery
Main parts of Raymond mill include grinding roller, grinding ring, powder collector, classifier, air blower, reducer, base plate, shovel, Raymond mill pendulum, star stack, etc Main materials of the parts:manganese(16Mn, 65Mn), High manganese steel, high chromium(Cr13、Cr23、Cr26) 4 types of casting processes:casting 展开optimize grinding plants from the start of the material feed onwards The LMmaster is a software based application which can either be installed in a PLC or on a separate PC The PROCESS OPTIMISATION FOR LOESCHE GRINDING PLANTSThis paper discusses wear and the measures taken to overcome this problem; availability and the procedures implemented to reduce downtime for replacement of the rolls; criteria for selection High Pressure Grinding Rolls for Minerals AusIMM2023年7月4日 The Raymond grinding mill, Raymond mill for short, is a roller mill in which the central spindle drives the multiple grinding rollers installed on the plumblossom rack to swing Roller Mill SpringerLink

Roller mills: Precisely reducing particle size with greater efficiency
This article introduces roller mills and explains how they efficiently grind friable materials to a uniform final particle size while using relatively little energy2012年9月1日 Mills (VRM) installations and summarises the main benefits of the dry compressive Loesche grinding technologies in Airflow and OverflowMode Some of these Latest Installations And Developments Of Loesche Vertical Roller Some of the VIBRADRUM® Grinding Mill features to keep installation costs low include: No drive speed reducers, ancillary machinery, nor large support bearings Very few moving parts No massive concrete foundation required for a typical VIBRADRUM® Grinding Mill Solutions General Roller mills are mills that use cylindrical rollers, either in opposing pairs or against flat plates, to crush or grind various materials, such as grain, ore, gravel, plastic, and others Roller grain Roller mill Wikipedia
.jpg)
Research of iron ore grinding in a verticalrollermill
2015年3月15日 Verticalrollermills (VRM) are an energyefficient alternative to conventional grinding technology One reason is the dry inbed grinding principle Results of extensive test The dry milling of ore in LOESCHE vertical roller mills has shown significant process advantages, as well as economic and ecological benefits To demonstrate these a mobile oregrinding plant the OGPmobile has been Mills for minerals and ores Loesche2019年10月8日 Roll grinding To maintain rubber covered rolls in the best operating condition frequent grinding must be performed Grinding restores the original properties and qualities of the cover Oxidation and surface checks, Roll grinding procedures, wheels, belts, setup, end Video credit: shsbjq / CC BYSA 40 Specifications Important specifications when selecting grinding mills and pulverizers include, The size of the mill can range from pilot/lab to production, eg, 35 to 1600 cu ft; Feed size, material, and Grinding Mills and Pulverizers Information
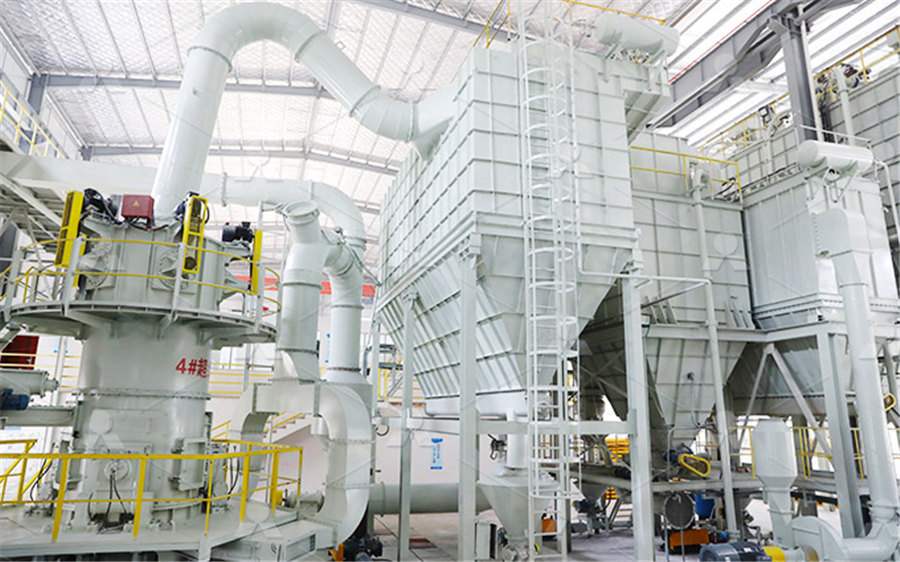
Raymond Roller Mill PartsUltimate Guide Fote
2023年2月15日 Disassemble and Installation of important parts of Raymond roller mill Removal steps of the grinding roller of Raymond mill 1 Remove the protective cover on the left side of the Raymond mill body, the Vbelt and the Vertical roller mills are not only used for grinding cement raw materials but also find an application in grinding a wide variety of coal types in cement and power plants Gebr Pfeiffer SE (GPSE) describes its vertical roller mills for coal grinding and provides a case study of an MPS225BK installed at CBR’s Lixhe cement works in BelgiumCOAL GRINDING IMPS: more than meets the eye Gebr Pfeiffer2023年7月20日 Therefore, the rod mill is mostly used for coarse grinding of the previous period of ball mill, or grinding of brittle materials and materials against overcrushing, such as tungsten and tin ore before gravity separation; and (3) autogenous mill – it refers to the materials which themselves are collided and ground mutually to be crushed when the grinding mill rotates, and Ore Grinding SpringerLink2021年1月1日 For the past three decades the vertical roller mill has emerged to be the preferred choice for grinding raw materials With the grinding capacity of a vertical roller mill and the ability to dry, grind and sort in a single unit, the vertical roller mill offers a definite advantage over the ball mill system [10]Review on vertical roller mill in cement industry its
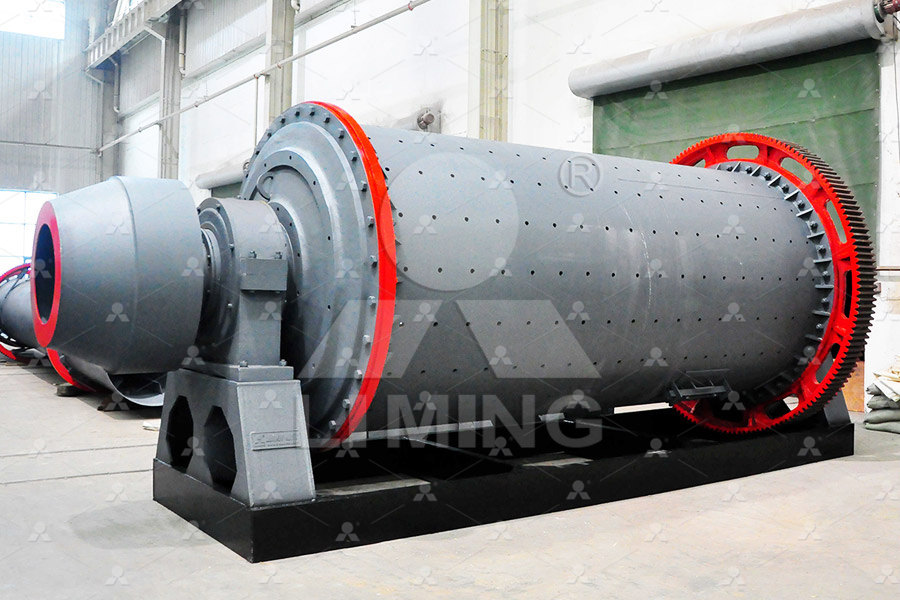
Application of HLMX Ultrafine Vertical Roller Mill for Nonmetallic Ore
Compared with the ultrafine vertical grinding mill in the same industry, HCMilling(Guilin Hongcheng) HLMX nonmetallic ore ultrafine vertical grinding mill equipment has the following advantages: lower cutting point of the classifier; The median diameter is smaller; The content of fine powder is higher; Higher yield; Lower energy consumption; The floorstation structure is Find your ore mill easily amongst the 42 products from the leading brands (Fritsch GmbH, Retsch, Eriez, ) on DirectIndustry, the industry specialist for your professional purchases doubleroller grinding mill WTM series Output: 6 t/h 350 t/h Motor power: 75 kW 3,300 kWOre mill, Ore grinding mill All industrial manufacturersand cement Roller presses are used mainly in combination with a ball mill for cement grinding applications and as finished product grinding units, as well as raw ingredient grinding equipment in mineral applications This paper will focus on the ball mill grinding process, its tools and optimisation possibilities (see Figure 1) The ball millBALL MILLS Ball mill optimisation Holzinger Consulting2017年9月11日 Grinding and separation efficiency of vertical roller mill were evaluated In addition to these, performance figures of vertical roller mill and conventional closed ball mill circuit were comparedPerformance Evaluation of Vertical Roller Mill in Cement Grinding
.jpg)
EnergyEfficient Technologies in Cement Grinding
2015年10月23日 In this chapter an introduction of widely applied energyefficient grinding technologies in cement grinding and description of the operating principles of the related equipments and comparisons over each other in 2017年8月5日 The installed power in the primary mill is generally much greater than in conventional circuits Since the semiautogenous or autogenous mill is dependent at least in part, if not entirely, on the ore to grind itself, a small change in ore grinding characteristics can produce a relatively large change in the grinding capacity of the millHow to Control a SAG Grinding Mill Circuit 911Metallurgist2017年9月1日 With the continual depletion of high grade simple ore bodies, more complex, finely disseminated ore bodies are being processed, which has led to an increase in the prevalence of fine grinding (Sinnott et al, 2006)This has been evident in the platinum group element (PGE) industry in South Africa, where the Bushveld Complex hosts 70% of global Fine grinding: How mill type affects particle shape characteristics Clinker grinding / Raw Material Grinding VRPM can be integrate with existing Cement Mill circuit to have substantial saving in specific power consumption and increase in production capacity We have experience of system engineering layout engineering which allows us to install the VRPM circuit within limited space in existing plantVRPM – AMCL Machinery Limited
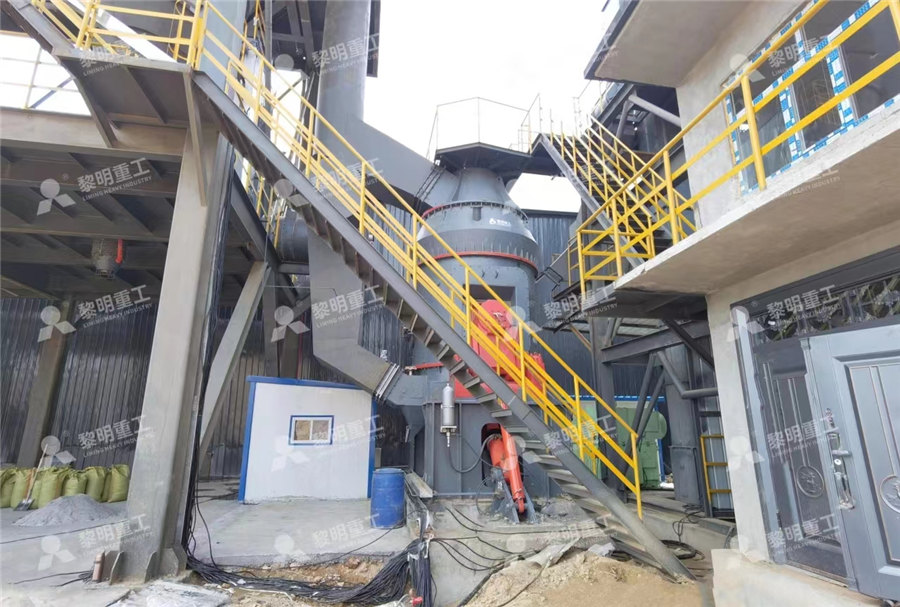
Research of iron ore grinding in a verticalrollermill
The total energy consumption for ore comminution will further increase within the next decades One contribution to minimise the increase is to use more efficient comminution equipment Verticalrollermills (VRM) are an energyefficient alternative to conventional grinding technology One reason is the dry inbed grinding principle2017年1月17日 The main mechanical and electrical components typically installed in a grinding mill a re the transformer, variable speed drive (for mill speed modulation), electric motor, gearbox, mill trunnions andBreaking down energy consumption in industrial grinding mills2024年8月17日 The operation of a roller mill is based on the principle of compression and shearing Grains are fed between rotating cylinders, with the gap between them determining the fineness of the resulting grind As the cylinders rotate, they crush and grind the grains, resulting in the desired textureExploring Roller Mills: Essential Machinery for Grain Processing2018年8月17日 SemiAutogenous Mills/ SAG Mills (primary grinding mill) — these mills use grinding balls with forces of attrition, impact, and abrasion between grinding balls and ore particles that result in Grinding Mills — Types, Working Principle Applications
.jpg)
Copper Ore Grinding in a Mobile Vertical Roller Mill Pilot Plant
2014年10月1日 To assess the feasibility of extending this vertical mills' improved performance to ore grinding applications, Altun et al [14] studied chalcopyrite ore grinding processes using a vertical roller Grinding Mills: Ball Mill Rod Mill Design PartsCommon types of grinding mills include Ball Mills and Rod Mills This includes all rotating mills with heavy grinding media loads This article focuses on ball and rod mills excluding SAG and AG mills Although their concepts are very similar, they are not discussed herePhotographs of a glass ended laboratory ball mill show Grinding Mills 911MetallurgistThe roller press is used for crushing minerals like clinker, limestone, slag, and trass in the cement industry It crushes minerals between two counterrotating cylinders under high pressure, forming a thin band or "cake" of crushed Roller Press FL Smidth PDF PDF Mill (Grinding)2019年8月14日 Ball mill is a common grinding equipment in concentrator Common Types of Ball mill back to top The common industrial ball mills mainly include cement ball mill, tubular ball mill, ultrafine laminating mill, cone ball mill, ceramic ball mill, intermittent ball mill, overflow ball mill, grid ball mill, wind discharge ball mill, double bin ball mill, energy saving ball millThe Ultimate Guide to Ball Mills Miningpedia
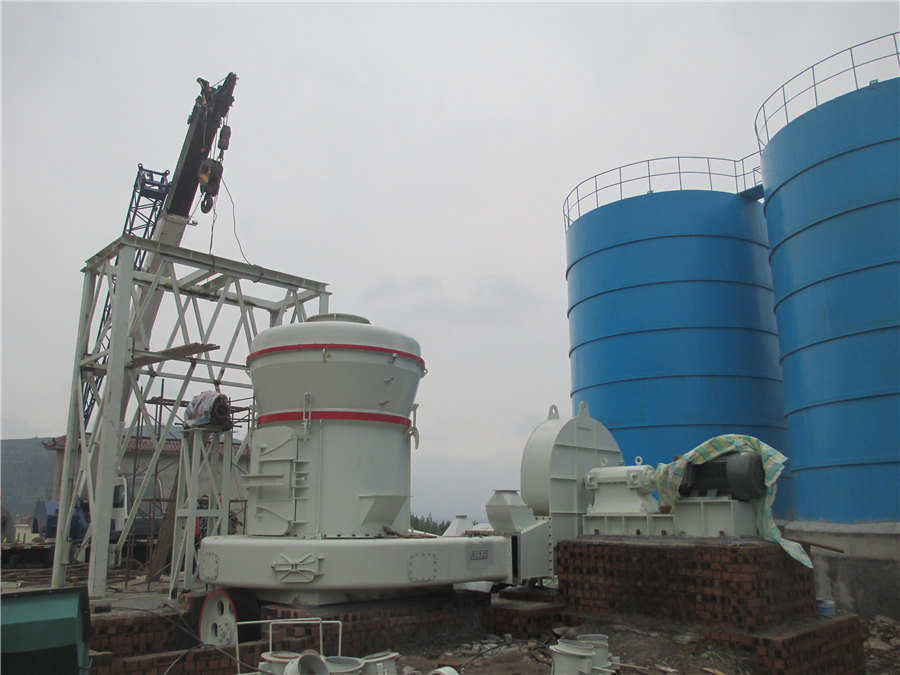
Roller mills: Precisely reducing particle size with greater efficiency
roller mill tests of your material in the manufacturer’s test facility with various roll corrugation styles and under conditions that duplicate your operating environment Figure 1 Particle size distributions: Roller mill versus other grinding methods Other grinding methods Roller mill Overs Target particle size Fines Figure 22019年4月16日 installed for grinding coal for power plants Research of iron ore grinding in a verticalrollermill, Minerals Engineering 73 (2015), 109–115 Roy, GR (2002)(PDF) LEARNING FROM OTHER INDUSTRIES; WHY THE VRM2020年8月12日 Altun et al [15] explored the influence of the parameter settings of a vertical roller mill on grinding performance and demonstrated the influence of grinding pressure values on the size and mass An investigation of performance characteristics and energetic Read this indepth blog to learn about the working principle of Vertical Grinding Mill, its application, and its advantages +91 226796 9655 sales@macawberindia 130131, Hindustan Kohinoor Complex, LBS Road, Vikhroli, Mumbai Home; 11 Advantages Vertical Grinding Roller Mill Machine As a vertical structure, Vertical Grinding Mill: How it Works, Application And Advantages
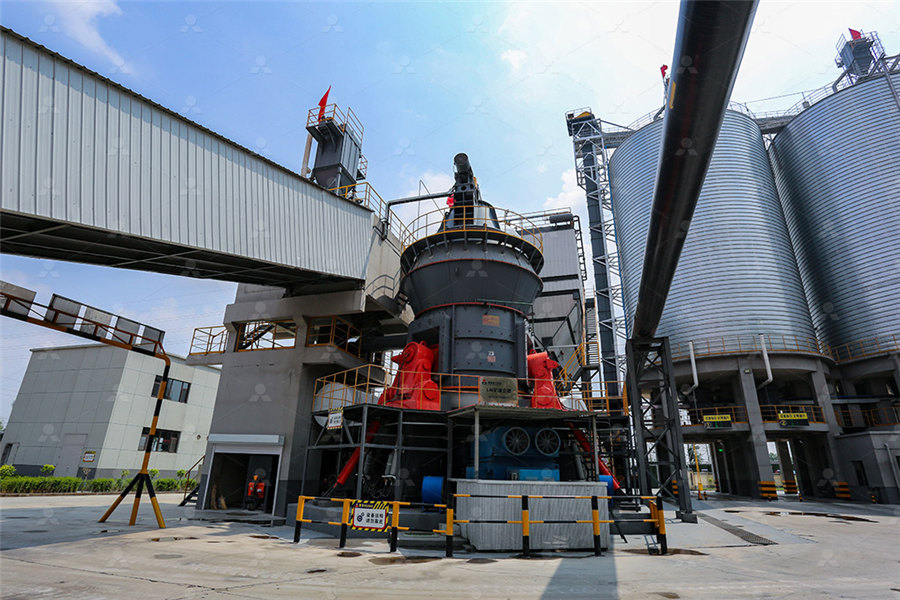
Grinding Process Optimization Featuring Case Studies and
Fig 1 Flowsheet of modular vertical roller mill 5000 R4 The required throughput rates were achieved in short time All fineness figures met the target values as well without any2022年1月23日 This work concentrates on the energy consumption and grinding energy efficiency of a laboratory vertical roller mill (VRM) under various operating parameters For design of experiments (DOE), the response surface method (RSM) was employed with the VRM experiments to systematically investigate the influence of operating parameters on the energy Analysis and Optimization of Grinding Performance of Vertical Roller 2015年3月25日 1 The working principle of the hydraulic system vertical roller mill The hydraulic system ofvertical mill is an important system, the main function ofthe hydraulic system is to break the grinding roller, which is when the internal grinding cavity wear parts wear, can stop open on both sidesofthe grinding roller mill, to replace the inside parts or repairThis type vertical roller Hydraulic system vertical roller mill operation PDF SlideShareRequest PDF On Mar 15, 2015, Mathis Reichert and others published Research of iron ore grinding in a verticalrollermill Find, read and cite all the research you need on ResearchGateResearch of iron ore grinding in a verticalrollermill
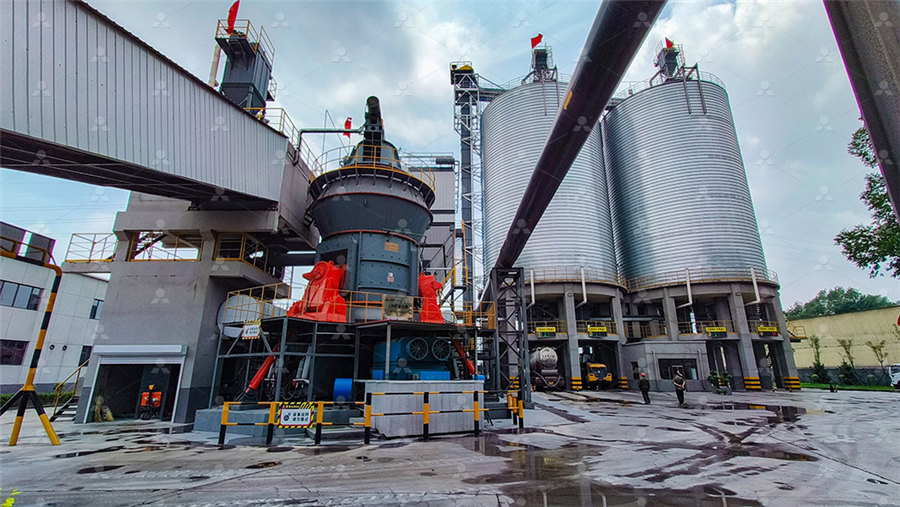
Research of iron ore grinding in a verticalrollermill
2015年3月15日 This pilot scale mill is a special development for ore grinding, which is reflected by several features The mill has four rollers, which are able to stress the particle bed with grinding pressures of up to 5000 kN/m 2 Various different roller geometries are available for grinding to generate different shear stress ratios2024年4月26日 The choice of grinding mill depends on factors such as the desired product size, capacity requirements, and energy consumption b Autogenous and SemiAutogenous Mills: In some cases, autogenous (AG) Iron Ore Processing: From Extraction to Manufacturing½ 2in / 1050mm, the roller mill can produce particles ranging from coarse, granular products of approximately 10% R2000 micron 90% minus 10 mesh (10%R2000 microns) to as fine as 999% minus 325 mesh (0001%R44 Raymond Roller Mill airswept vertical ringroll2016年1月1日 In wet grinding practice, highstress abrasion occurs over a small region when ore particles are trapped between the grinding balls and the mill liner, and the load is sufficient to fracture A comparison of wear rates of ball mill grinding media
.jpg)
Increase productivity of vertical roller mill using seven QC tools
2021年1月29日 Vertical roller mills, VRMs, are widely used for grinding raw materials in factories engaged in the extraction and processing of minerals Any machine used for grinding or crushing consumes around 2015年8月6日 It affects retention time and helps distribute the ore throughthe mill so each piece of rock will come in contact with the surface of the rods The % solids by volume of the rod mill discharge Rod mill grinding efficiencies have been shown to increase in the range of 5 to 15% with more dilute discharge slurry (ie, Ball Rod Mill Density – How Water Impacts Grinding2015年8月6日 Rubber liners absorb the impact of the larger grinding media and thus protecting – the mill structure and prolonging it’s life Weight: Rubber weighs about 15% of an equivalent volume of steel This means that a rubber liner system reduces the load on the mill structure and also reduces the basic power drawGrinding Mill Liners 911Metallurgist2023年10月3日 Grinding Rollers: Grinding roller is the main part for crushing and grinding materials The grinding roller is composed of cast steel roller sleeve, forging shaft and wearresistant surfacing bushing The grinding roller is installed on the rocker arm of the cement vertical roller mill, under the action of external force, it is pressed tightly on the material of the grinding What is a vertical roller mill (VRM)? A Comprehensive Guide to
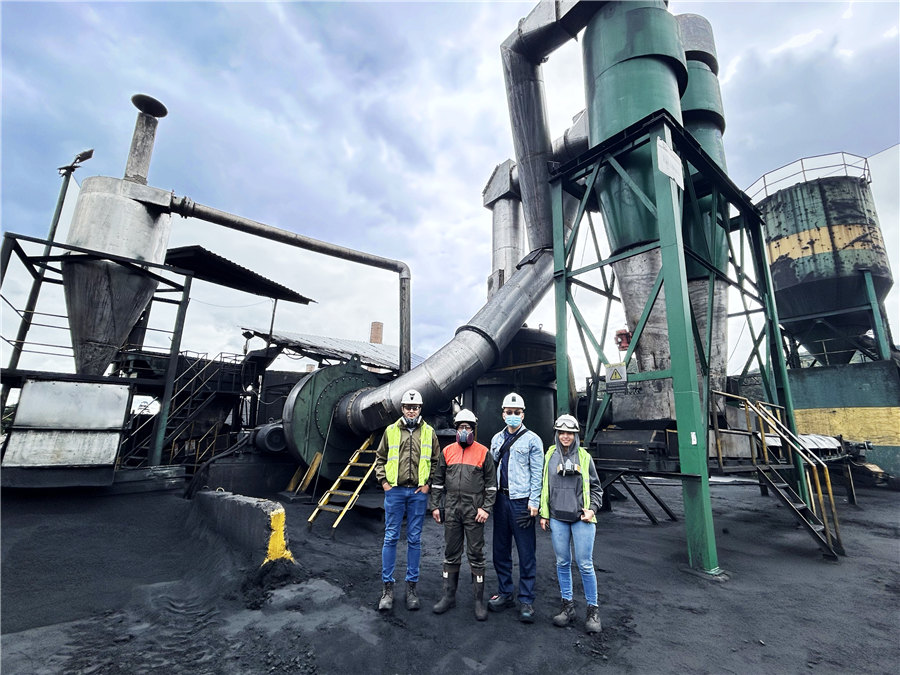
VRM – AMCL Machinery Limited
The essential countermeasure to suppress mill vibration is to increase (improve) friction coefficient of material in the grinding area directly beneath the mill roller Over the years UBE has wellestablished 2+2 and 3+3 system of Main Roller and Sub Roller for Cement and Slag grindingSpeed also plays a role in ore grinding; too high of a speed can cause damage to the mill gears and other components, while too low of a speed can cause excessive wear on these same components It is important to find a balance between these two variables in order to achieve optimal grinding performanceFactors affecting ores grinding performance in ball mills