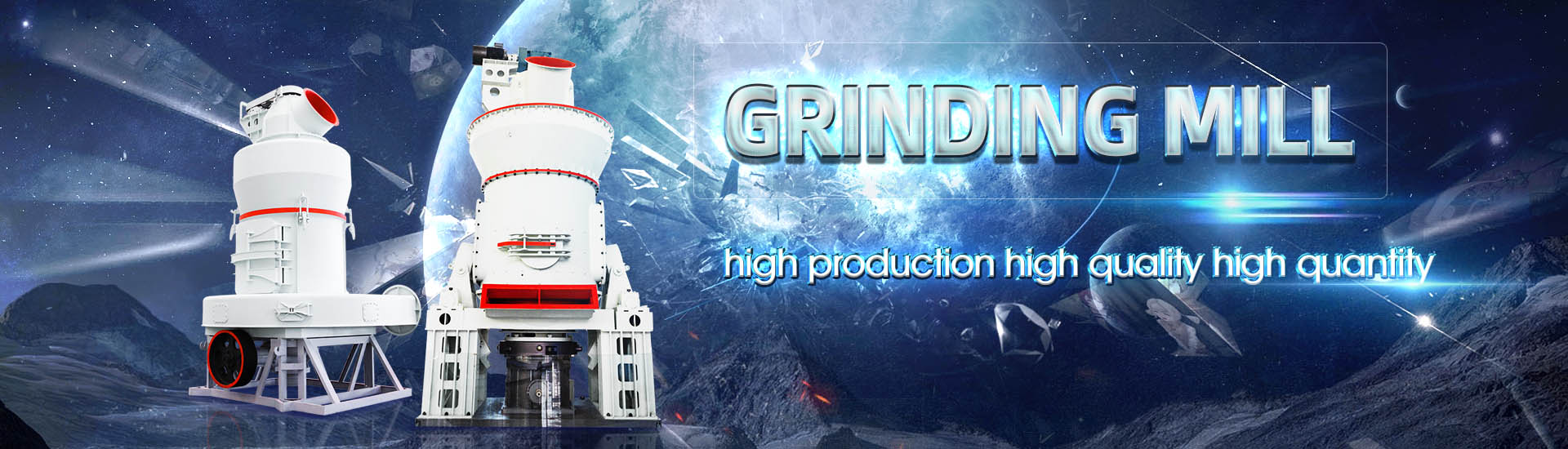
Factors affecting the coal grinding system of cement plants
.jpg)
Coal Grinding Cement Plant Optimization
Highly energy intensive unit operation of coal grinding is intended to provide a fine coal as a fuel for calcination and clinkerization Coal grinding operation is monitored for following parameters to ensure objectivity and economy of operationCement grinding In Table 1, three common cement grinding systems are compared on their electrical consumption for a typical 3500 Blaine ordinary portland cement (OPC) Roller press Thomas Holzinger, Holzinger Consulting, grinding system 2023年1月1日 The utilization of coal in the cement and concrete industries takes three basic forms: (1) as a fuel in the production of cement clinker; (2) ash produced by burning coal in Coal utilization in the cement and concrete industries2017年4月1日 Vertical roller mills (VRM) have found applications mostly in cement grinding operations where they were used in raw meal and finish grinding stages and in power plants Operational parameters affecting the vertical roller mill
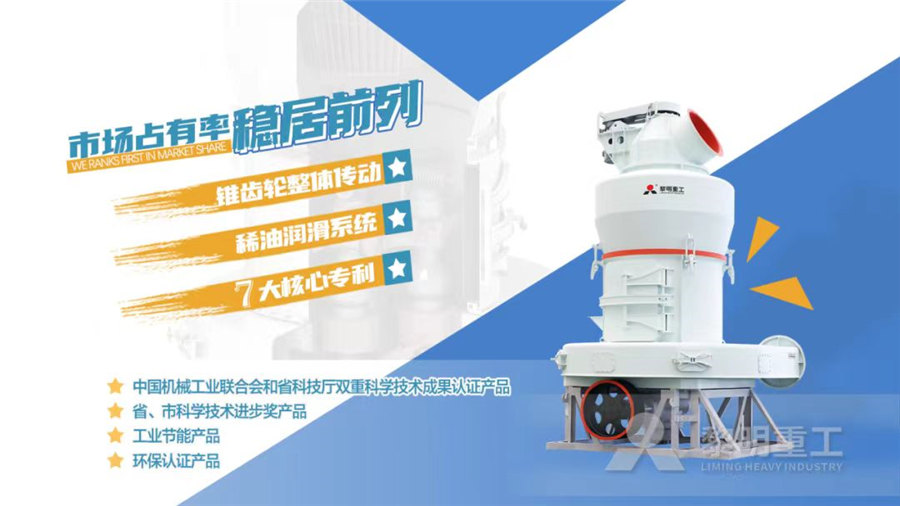
Coal for cement: Present and future trends
2016年3月1日 Coal provides around 90% of the energy consumed by cement plants around the world, despite the environmental harm caused by its combustion It takes 200 450kg of coal LOESCHE coal grinding mills are distinguished by characteristics that improve efficiency, safety and environmental protection, from the standard version to topoftherange installations Special versions are available with characteristics Coal Mills for Cement Plants Loeschethe grinding process, maintenance and product quality The objective is to achieve a more efficient operation and increas the production rate as well as improve the run factor OPTIMIZATION OF CEMENT GRINDING OPERATION IN BALL MILLS2022年1月23日 As reported by Boehm and by Altun , there are several factors affecting the grinding effect, among which the loading pressure and feed rate are more important, while the motor rotation speed and the moisture content of Analysis and Optimization of Grinding Performance of
.jpg)
THE NEED FOR EFFECTIVE RISK MITIGATION IN CEMENT PLANTS
nd oversized particles are fed back to the grinding system The vertical ends of such mills, also known as trunnion walls, through which material enters and discharges, are most susceptible 2016年10月5日 In this chapter an introduction of widely applied energyefficient grinding technologies in cement grinding and description of the operating principles of the related equipments and comparisons over each other in EnergyEfficient Technologies in Cement Grinding2020年1月3日 Key factors in setting up of a cement plant Some of the important factors which need to be kept in mind during setting up a cement plant are: Markets: Revenue for the business comes from the market, and thus, it is Key factors in setting up a cement plant Indian Everything you need to know about clinker/cement Grinding if You read and understand this article , you will be ready to be a cement grinding area manager FEED AND FEED SYSTEM Feed Temperature Plants with satellite coolers Everything you need to know about clinker/cement
.jpg)
Cement Clinker Quality Control
Cement Grinding Plant Hot Sale; Modular Grinding Plant; Concrete Batching Plant; The following are several important factors affecting the cement clinker quality which is not conducive to the normal operation of the kiln system 3 Coal Fines Many cement plants use bituminous coal as the fuel of rotary kiln, so the ash content, 2020年9月14日 Power supply distribution in cement plants Many young engineers consider cement plants pretty complicated because of their weird technology The reason probably lies in the fact that you cannot understand all those technologies unless you worked in such a plant and saw all processes from scratchThe essentials of electrical systems in cement plants EEPThe vertical roller mill (VRM) is a type of grinding machine for raw material processing and cement grinding in the cement manufacturing processIn recent years, the VRM cement mill has been equipped in more and more cement plants around the world because of its features like high energy efficiency, low pollutant generation, small floor area, etc The VRM cement mill has a Vertical Roller Mill Operation in Cement Plant2013年1月1日 As of 2009, world cement output was estimated at 304 billion tonnes (metric tons) 6 China represents 561% of the world’s output while the USA represents 20% 7 Fuel used by the US cement industry is 60% coal, 13% petroleum coke, and 3%, natural gas 8 According to the US Energy Information Administration (EIA), the manufacture of cement Coal utilisation in the cement and concrete industries

Grinding process is a critical stage in cement production
2023年8月21日 Tushar Khandhadia, General Manager – Production, Udaipur Cement Works, discusses the role of grinding in ensuring optimised cement production and a high quality end product How does the grinding process contribute to the production of highquality cement?The quality of cement depends on its reactive properties and particle size grinding helps to reduce AGICO Cement is a cement grinding plant manufacturer, we'd like to helps you learn more about cement grinding plant and cement grinding machines Skip to content +86 Cement Grinding Plant Overview Cement Grinding Unit AGICO Cement2021年2月1日 Cement grinding aid is a kind of material which can promote cement grinding, and it is an important part of energysaving development of industry at present It can not be ignored in improving Analysis on Influencing Factors of Grinding Aid Effect of Cement 2020年9月22日 The use of cement and concrete, among the most widely used manmade materials, is under scrutiny Owing to their largescale use, production of cement and concrete results in substantial emission Environmental impacts and decarbonization strategies in the cement
.jpg)
Cement plant design under EPC contract ESFC
The use of coal is associated with numerous technical tasks for its drying and grinding, Grinding cement Modern plants produce Portland cement by mixing cement clinker with industrial gypsum Factors affecting layout An ideal plant 2023年11月1日 The system obtains production and quality data through the MES platform, comprehensively considers the factors such as coal matching, raw mill startup and shutdown, gets through the data communication with the neutron analyzer, fluorescence analyzer and distributed control system (DCS), realizes the quality closedloop control of raw meal proportioning, reads The digitization work of cement plant in China ScienceDirect2020年10月15日 This research focused the role to study the effects and ways to control the chemical composition of clinker for better cement production Cement is a substance produced by grinding a mixture of a Effects and Control of Chemical Composition of 2019年1月3日 Clinker grinding technology is the most energyintensive process in cement manufacturing Traditionally, it was treated as "low on technology" and "high on energy" as grinding circuits use more than 60 per cent of total energy consumed and account for most of the manufacturing cost Since the increasing energy cost started burning the benefits significantly, Clinker grinding technology in cement manufacturing
.jpg)
DISCUSSION ON SAFETY PRODUCTION OF COAL MILLING SYSTEM IN CEMENT PLANT
2022年1月27日 The burnup of coal in cement production requires the support of a coal grinding system Sign in to view more content Create your free account or sign in to continue your search2014年5月1日 In this study, the effects of refractory bricks and formation of anzast layer on the specific energy consumption of a rotary kiln are investigatedAnalysis of the parameters affecting energy consumption of a Evaluation of a coal grinding system’s fire and explosion protection, including the raw coal storage and the fine coal silo storage normally can be done in one day, mostly without having to stop coal grinding The evaluation will be done by way of touring the plant, making photos and having interviews with the people responsible for the Fire and explosion protection of coal grinding systems Where are Summary: With dedusting of coal grinding plants, the state of the technology is determined by the explosion protection measures, the filtration performance and the design of the plant To ensure safe operation of a plant, only certified and tested concepts and components should be used for its design and manufacture With plants protected against explosion, such issues will always Stateoftheart explosion protection for dedusting of coal grinding plants
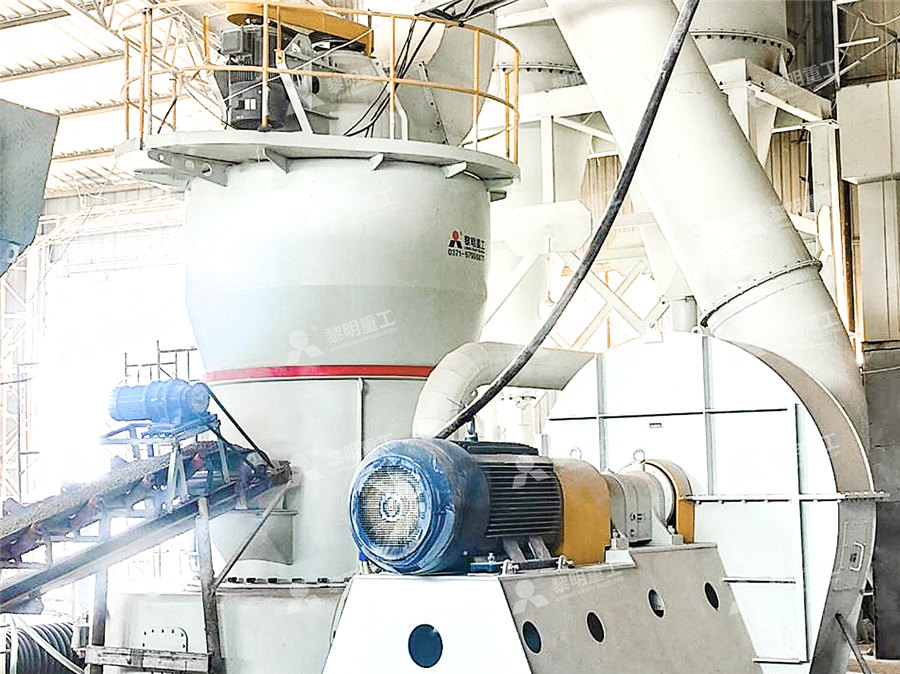
Guide To Cement Plants Site Selection
2023年10月30日 Before you send inquiry Please provide us with project information as much as possible: For a complete project: the material availability, the required output capacity, the process technology, your budgetary and financing status, the estimated starting time, etc For singular machinery: the model, the capacity, your budgetary information, other requirements, etc2014年1月1日 The emission factors of kiln end, kiln head, coal mill, crushing and cement mill was 0156 clinker g/t, 3914 clinker g/t, 1538 coal g/t, 0016 stone g/t and 0056 cement g/t respectively, the (PDF) MPS mills for coal grinding ResearchGate2023年12月28日 Some grinding aids will affect the grinding effect because the most commonly used grinding aids are organic substances with strong surface activity During the material grinding process, they can be adsorbed on the Factors Affect The Output and Quality of Ball Mills 2023年1月1日 However, grindability is a complex issue and factors such as coal moisture content and required fineness (high volatile coals can require a coarser grind), along with the milling and burner systems are all factors in assessing coal grindability Generally, a value of 55 represents an average grinding coalCoal utilization in the cement and concrete industries
.jpg)
Improving the efficiency of the coal grinding process in ball drum
2022年2月24日 Ensuring the reliable operation of the dust fuel preparation system at thermal power plants (TPP) is a topical issue since it determines the energy strategy of any country that fires coals for COAL GRINDING SYSTEMS SAFETY CONSIDERATIONS Most rotary kilns use solid fuels as the main heat source to produce cement clinker A training program should be developed and extensive training coal mill system for operators provided on a regular basis Safety considerations, such as the prevention ofCOAL GRINDING SYSTEMS SAFETY CONSIDERATIONS PEC kiln feed preparation, pyroprocessing, and finished cement grinding Each of these process components is described briefly below to the extent that such replacement can be implemented without adversely affecting plant 1162 EMISSION FACTORS 11/21 operations, Pulverized Coal Kiln Feed Units 21 General 99 A Dry Process Kiln 06116 Portland Cement Manufacturing US Environmental 2016年9月1日 Modern cement plants trend for the usage of vertical mill in cement grinding because of its many The VRM system for coal, cement, there are several factors affecting the grinding Operational parameters affecting the vertical roller mill
.jpg)
Everything you need to know about Kiln System Operations in Cement
For example, in a direct fired coal mill system if the moisture content of the coal drops, the kiln will get more tons of dry coal at the same setting on the raw coal feeder Changes in the percentages of coal versus coke, for a kiln firing both fuels simultaneously, will also affect the CO and O2 level2015年2月9日 Star Cement operates one 24Mt/yr integrated cement plant in Ras alKhaimah, one 12Mt/yr cement grinding plant in Abu Dhabi and one 900,000t/yr cement grinding plant in Ajman Star Cement owns the largest number of cement plants in the UAE Sharjah Cement operates a 2Mt/yr capacity cement plant in SharjahThe growing cement industry of the UAE2022年4月4日 Introduction World cement production has grown steadily in the last decades and represents an energyintensive industry, which accounts for ~14 Gt of CO 2 emissions per year, corresponding to roughly 6–7% of global anthropogenic GHG emissions ()The cement industry is therefore required to restructure its sector significantly to play a role in mankind's quest to Evaluating the Carbon Footprint of Cement Plants Integrated 2021年1月1日 Coal Grinding: Grinding Mill These factors affect the mortar properties of cement viz water demand, Rashmi cement limited environmental pre feasibility report for Expansion of existing cement grinding plant from 096 MTPA to 111 MTPA by enhancing capacity of 2000 TPD VRM base grinding units to 2500 TPD, Review on vertical roller mill in cement industry its performance
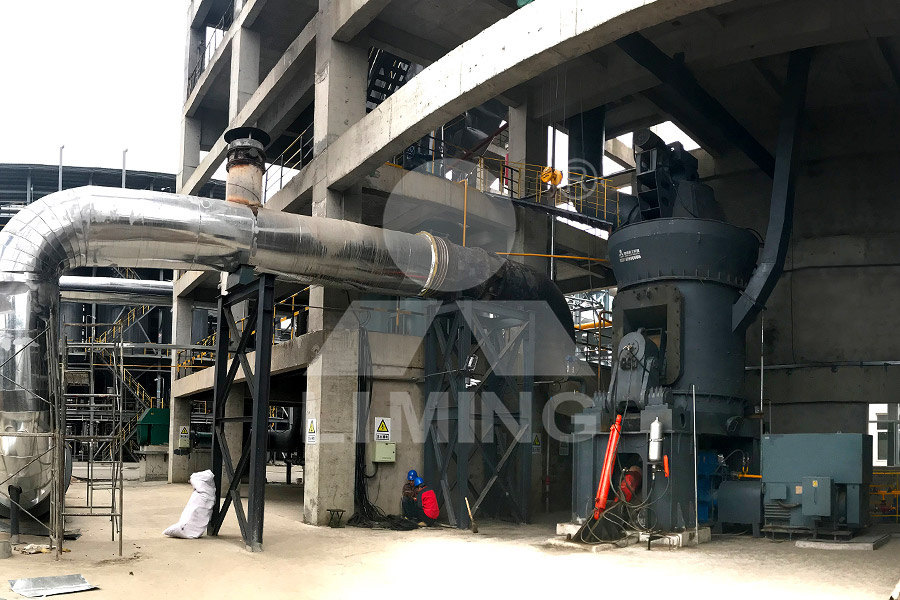
Coal Grinding and Firing Systems – HAZOP Analysis
Human factors affecting the operation Ensure that the coal grinding and firing system can be started, operated and shut down safely He is an expert process engineer whose core competence lies in the optimization of cement plant operationsChoose the right cement manufacturing machine is an important influence factor to produce highquality cement The cement making machine frequently used in cement plants includes cement rotary kiln, shaft kiln, cement vertical mill, Cement Manufacturing Machine Cement Making 2015年10月20日 It has also been found that the length/diameter ratio of about 3 which is usual for cement mills may well be too large for ball mills in combined grinding plantsINVESTIGATION OF EFFECTS OF GRINDING MEDIA 2020年9月9日 Italian cement industries are among the major cement producers in the European panorama In the last decades, because of the increasingly stringent specifications on environmental impact and energy saving, technology in the cement plant has been significantly improved []In this context, Advanced Process Control (APC) systems have become the Optimization of the Clinker Production Phase in a Cement Plant
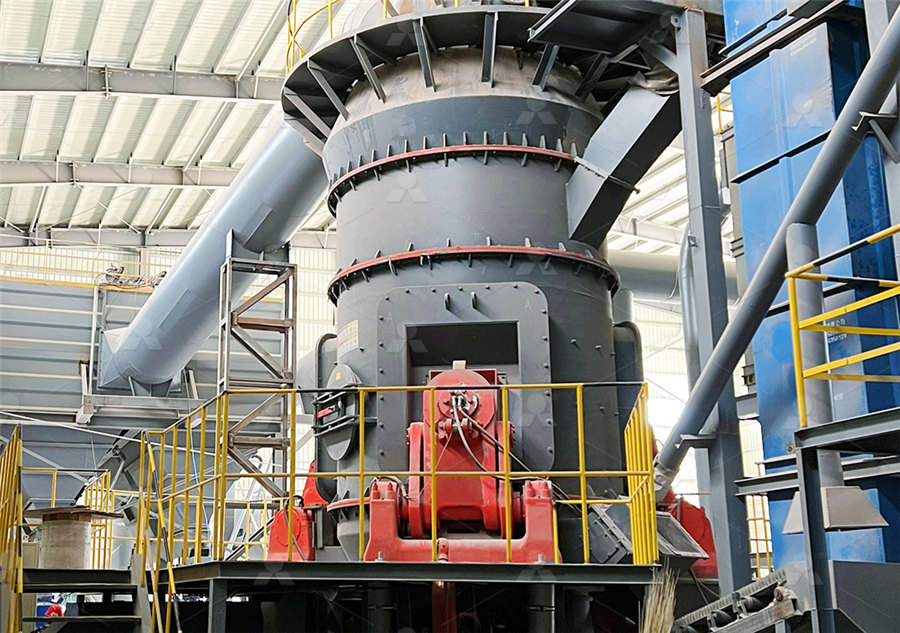
Modeling of energy consumption factors for an industrial cement
2022年5月9日 Cement production is one of the most energyintensive manufacturing industries, and the milling circuit of cement plants consumes around 4% of a year's global electrical energy production It is 2019年7月31日 grinding, during which the Number of factors that affect the strength of cement Those are watercement ratio, (coal and gas fired power plants, cement industry, etc) In this study, Environmental Pollution by Cement Industry ResearchGate2023年10月13日 Cement producers and their investors are navigating evolving risks and opportunities as the sector’s climate and sustainability implications become more prominent While many companies now Global database of cement production assets and upstream 2023年7月10日 Cement manufacturing is a significant industrial activity that plays a vital role in the construction sector However, the process of cement production is associated with various environmental Cement Manufacturing Process and Its Environmental Impact
.jpg)
Cement grinding Vertical roller mills VS ball mills
Vertical roller mills and ball mills represent two clearly distinct technologies However, with proper adjustments to the operational parameters of the vertical roller mill almost identical cement properties can be achieved by the two mills that satisfy the cement user’s demandsNevertheless, the two types of mills have their distinctive merits2022年1月25日 The burnup of coal in cement production requires the support of a coal grinding system In the operation of the coal mill system, there are many unsafe factors, which are easy to cause safety Discussion on Safety Production of Coal Milling System in Cement Plant