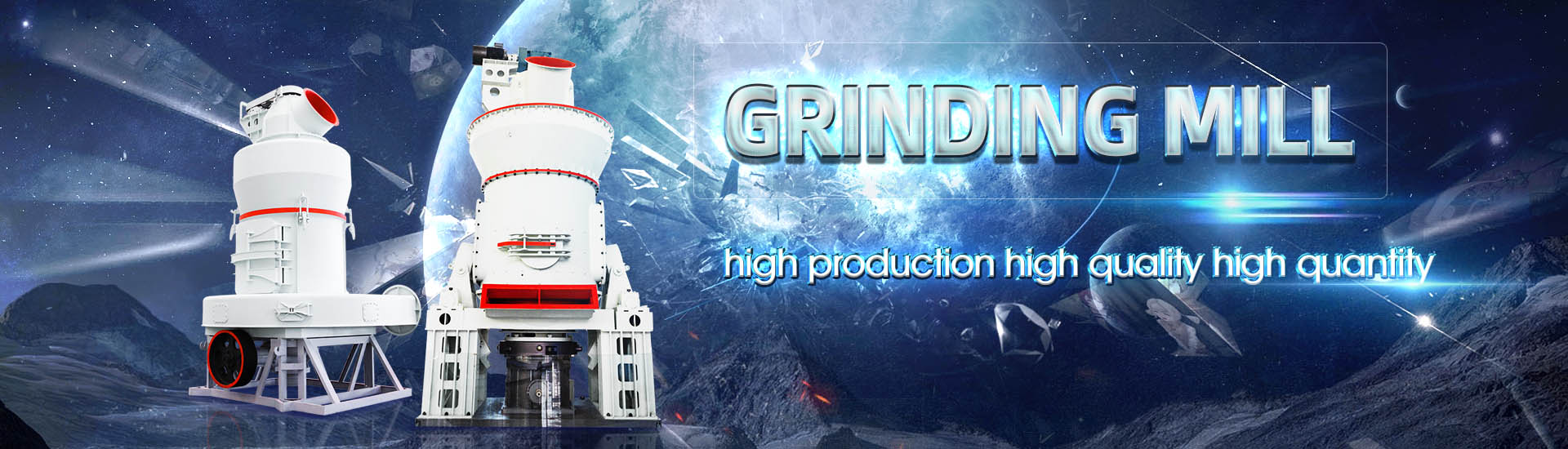
Coal powder grinding equipment process flow
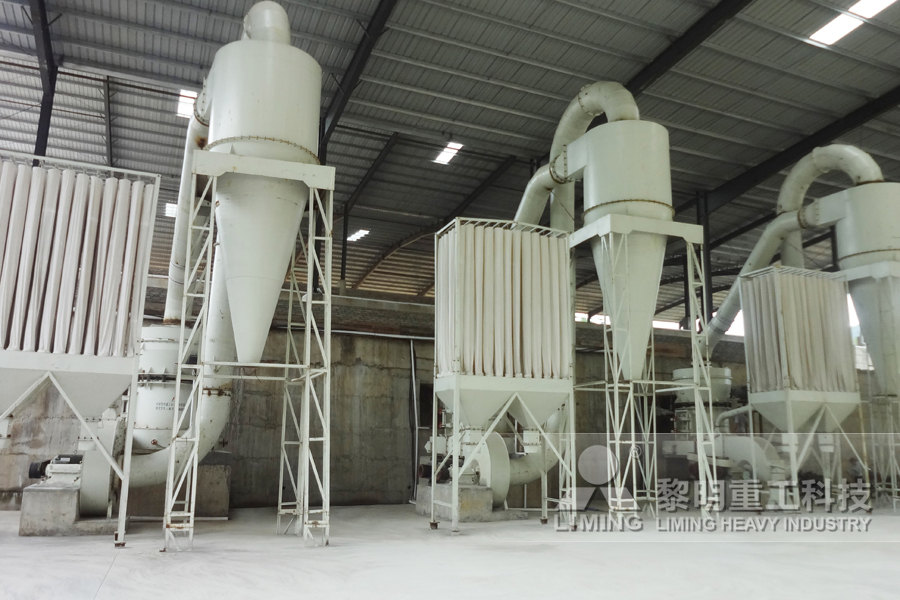
How is pulverized coal processed? SBM Ultrafine
2022年2月24日 Pulverized coal processing and milling equipment According to the fineness of coal feed, moisture content, finished product fineness, usage and other factors, SBM micropowder technology can help customers to reasonably Coal grinding is an essential process in the coal preparation process, energy industry, and cement manufacturing Coal grinding machines are used to achieve particle size reduction and surface Coal grinding machine Coal grinding process flow NEWS13 行 Coal mills or pulverizers play a very essential part in the coalfired power production system Coal mills grind the coal into fine powder, and the primary air entering the mill dries Coal Pulverizers an overview ScienceDirect Topics2024年1月11日 Processing raw coal into pulverized coal involves several intricate steps that ultimately convert raw coal into fine powder primed for energy generation However, it is crucial to handle pulverized coal carefully due to its How to Process Coal into Pulverized Coal in 5 Steps?
.jpg)
Coal grinding technology: a manual for process engineers
Four coal grinding devices three dry, one wet are discussed with the appropriate ancillary equipment for complete systems The mills examined are the: airswept ball mill, roll or ball 2023年1月1日 This chapter discusses research that has contributed to improved understanding of pulverized fuel (PF) technology The processes studied are the grinding of PF in power Advances in pulverised fuel technology: understanding coal The coal is ground between the rollers and grinding table When enough coal has been reduced in size, it will flow over the top of the dam ring (retention ring) Coal Pulverizer Inlets and Outlets Louvres (nozzle ring) around the outerVertical Grinding Mill (Coal Pulverizer) Explained saVRee2017年6月1日 A nonlinear dynamic model of a directfired pulverizing system that considers the effect of coal moisture on the energy balance of a coal mill was established Then, an Optimization control of a pulverizing system on the basis of the
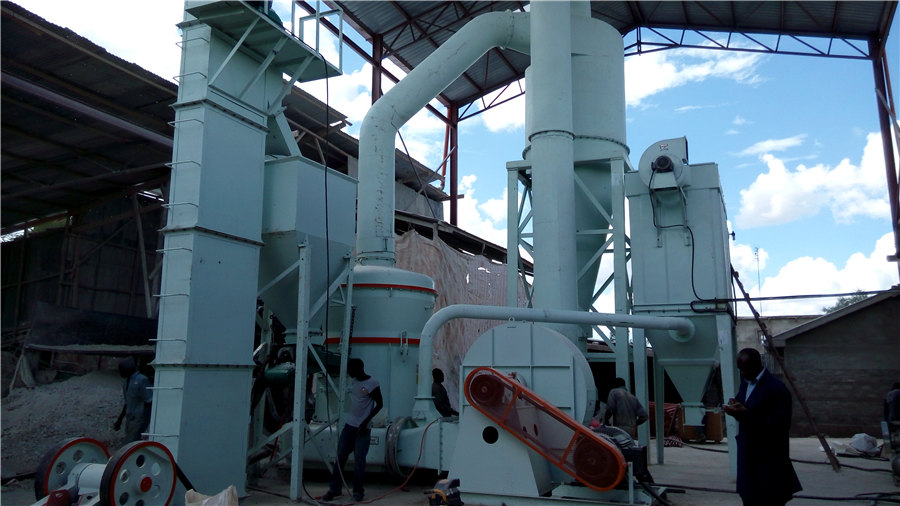
Performance optimisation of vertical spindle coal pulverisers
Coal pulverisers’ performance optimisation is an important process in power generation plants Pulveriser operation is costly; reliability and availability is key to power generation and cost 2020年8月12日 Obtained results indicate that grinding pressure, primary air (PA) temperature and mill motor current have a tendency to rise by increasing coal feeding mass flow rates for all used coalAn investigation of performance characteristics and 2024年8月17日 Charcoal Powder Production with Coal Crushers Charcoal powder production with coal crushers, including the use of a charcoal powder crusher, involves key components such as carbonization furnaces, conveyors, Coal Crushers with Charcoal Powder Grinding Download scientific diagram Flowsheet of a modern coal preparation plant incorporating four parallel circuits from publication: Genetic algorithms — A novel technique to optimize coal Flowsheet of a modern coal preparation plant incorporating four
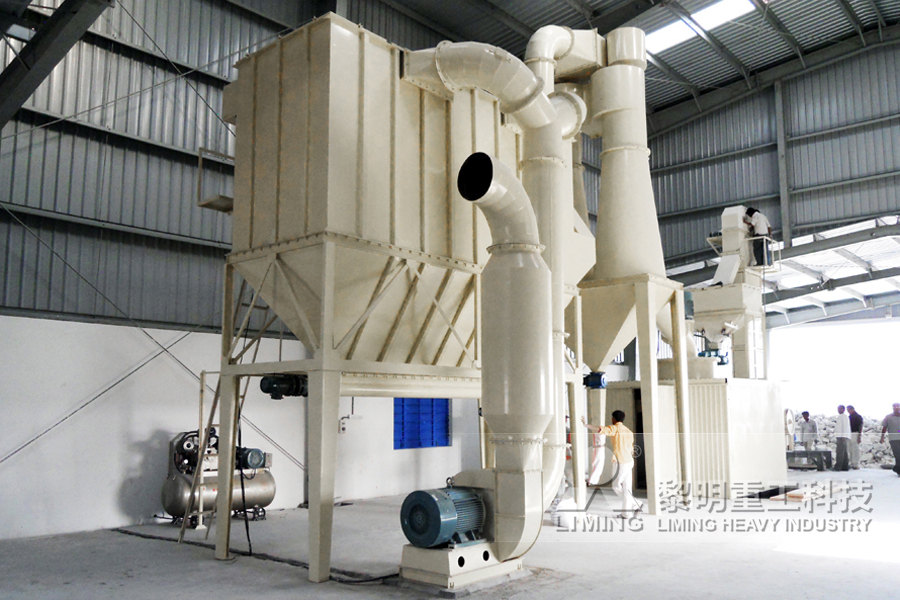
An investigation of performance characteristics and
2020年8月12日 As one of the three major forces of coal mills, the grinding force exerts a significant impact on the working process of coal mills and parameters like mill current and outlet temperature2018年9月28日 However, during the process of blasting, Ttype fracture generates at the point of blast and it propagates through the weak structures like cleats present in the mineralcoal barrier by breaking Generation of low ash fine clean coal powder by autogenous grinding processIntroduction This article concerns itself with vertical grinding mills used for coal pulverization only (coal pulverizers), although vertical grinding mills can and are used for other purposes The 3D model in the saVRee database represents a vertical grinding bowl millOther grinding mill types include the ball tube mill, hammer mill, ball and race mill, and , roll and ring millVertical Grinding Mill (Coal Pulverizer) Explained saVRee2024年9月20日 The primary crushed graphite ore enters the grinding process, usually using equipment such as a grinding mill The grinding process of graphite requires the use of special grinding tools and abrasives to ensure the quality and purity of graphite Separating; The ground graphite powder enters the screening equipment to separate graphite powder How Does The Graphite Grinding Plant Process?
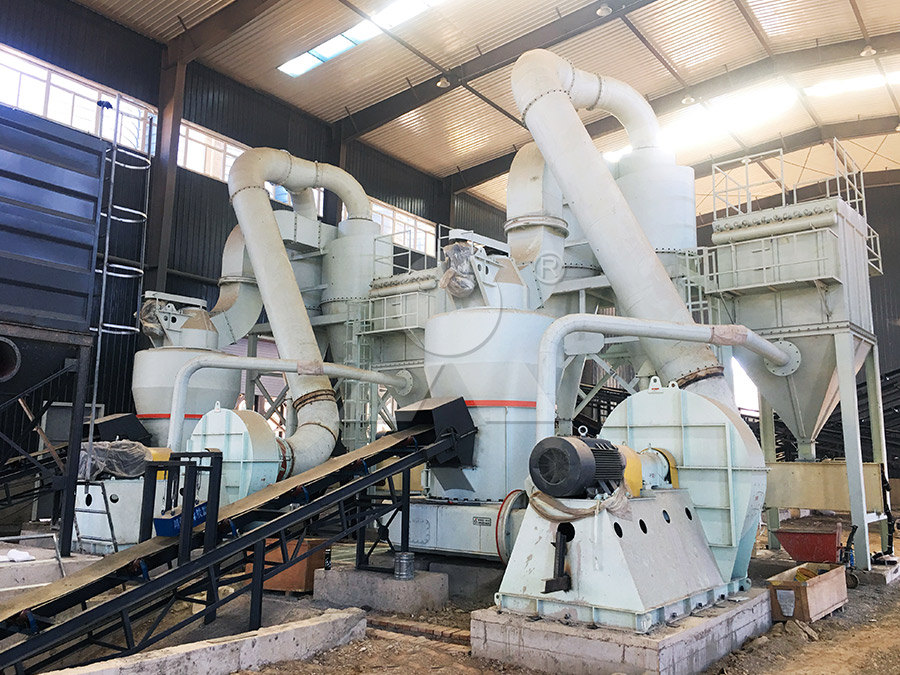
Generation of low ash fine clean coal powder by autogenous grinding
2019年1月15日 Autogenous grinding is the process in which, the ore is grounded itself without any grinding media As the grinding media is harder than the ore, there is always high impact force applied to the ore, which leads to the breakage throughout the materials but not through the interfaces between the materials present in ore [21]For the present study, two different run of conservative coal mill control strategies employed There is thus a need to improve the existing control of the grinding process and fuel ow to achieve better exibility of such units Furthermore, coal grinding consumes signi cant amounts of energy and hence it is desired to optimize the process ensuring higher overall plant e ciencyAalborg Universitet Improved coal grinding and fuel flow control 2022年2月24日 Pulverized coal processing and milling equipment According to the fineness of coal feed, moisture content, finished product fineness, usage and other factors, SBM micropowder technology can help customers to reasonably choose the grinding and powder selection process, and determine the type, model and quantity of pulverizers according to How is pulverized coal processed? SBM Ultrafine Powder The process is called a drying /grinding process, Air slide pneumatic conveying equipment used to convey dry and powder material In DMC it is used to convey fine material and cement powder Caking problem in fine coal bin and disturbed coal flow;Cement Manufacturing Process INFINITY FOR CEMENT EQUIPMENT
.jpg)
7 basic process flows of ultrafine grinding ALPA Powder Equipment
2023年9月13日 The mechanical ultrafine grinding process generally refers to the grinding and classification process for preparing particle size distribution d97≤10μm, which is divided into dry method and wet method The ultrafine grinding unit operation (ie onestage ultrafine grinding) currently used in industry has the following process flows:The introduction of hot air helps to improve the drying effect of coal powder and carries coal powder into the coal mill shell during the coal grinding process Coal Powder Conveying System The pulverized coal conveying system is used to Air Swept Coal Mill Cement Plant Equipment Coal 2023年12月14日 Jaw Crusher( feldspar production line equipment) It is necessary to crush big feldspar stones into small pieces before the grinding process The crushing equipment usually uses a jaw crusherIt has Feldspar Powder Crushing Grinding Production Line Schenck Process Group Your Partner Worldwide Kemutec is part of the Schenck Process Group, a worldwide manufacturer of bulk material handling products and systems The Kemutec brand specializes in the supply of custom engineered process solutions for powders used in the food, chemical, pharmaceutical and environmental industriesPowder Processing Equipment Systems Qlar
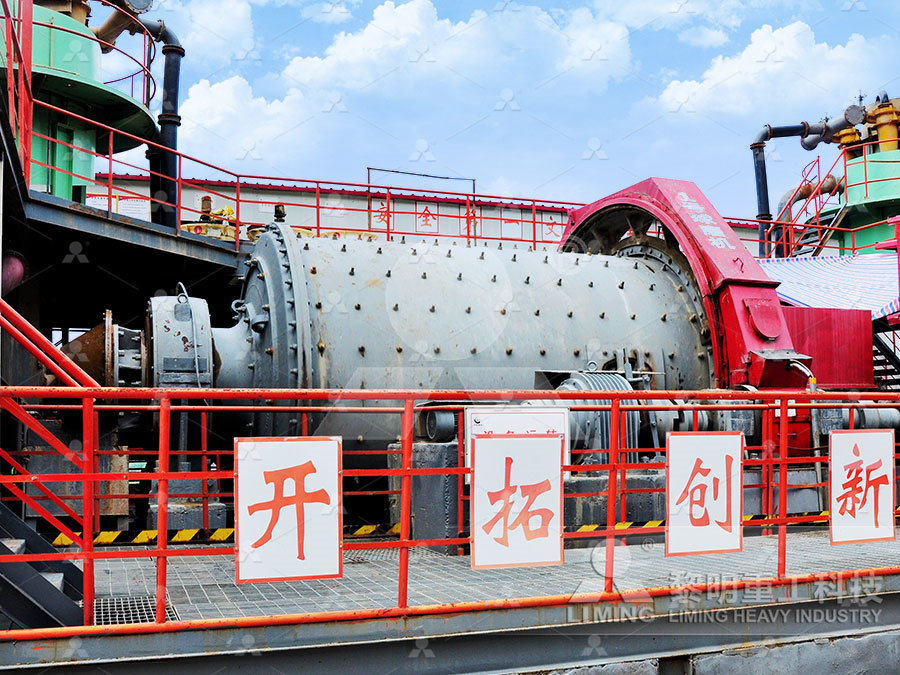
coal mining process flow chart in south africa
mining629 mining and processing of coal plasmarau Coal mining Wikipedia Coal mining is the process of extracting coal from the ground Coal is valued for its energy content, and, since the 1880s, has been widely used to generate electricity coal mining processing flow chart Crusher Machine coal mining processing flow chartA complete set of coal powder preparation equipment is essential for the coal injection process in blast furnaces often required for the subsequent milling process 3 Coal Grinding and Milling System: Mills: Typically ball mills or vertical Sensors and meters to monitor critical parameters such as coal flow, powder fineness, and air Complete set of coal powder preparation equipmentHigh Capacity High Quality Coal Vertical Mill 90t/h Vertical Coal Grinding Equipment Get Best Price Summary Table of Engineering Project Situation Project Name Coal powder pneumatic conveying system of Xinjiang XX Aluminum Power Currently, the project has been smoothly put into operation, and our advanced process flow, Quality Vertical Coal Mill, Limestone Vertical Mill factory, Vertical After coal comes out of the ground, it typically goes on a conveyor belt to a preparation plant that is located at the mining site The plant cleans and processes coal to remove dirt, rock, ash, sulfur, increasing the heating value of the coal During this coal processing, the used industrial equipment can be called coal processing equipmentsprocess flow diagram of coal based power plant Grinding Mill
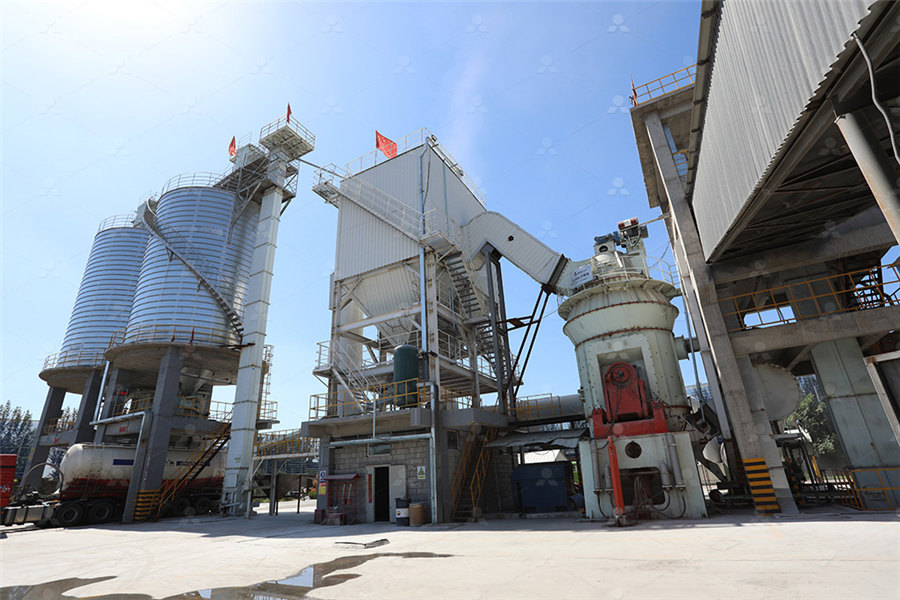
Calcium Carbonate and Coal Powder Production Line In China
In a bid to enhance their production capabilities and expand their product offerings, this customer has invested in 3 sets of HGM125 micro powder grinding millsThese mills are specifically used to produce ultrafine calcium carbonate and coal powder, achieving a fineness of 600 meshThe final product, which expands upon mixing with water, is utilized as an expansion agent in various 2016年2月29日 SAG mills, rod mills and ball mills are the classical pieces of grinding equipment employed in gold recovery plants The pregnant solution can be treated by activated carbon or zinc powder (Merryl Crowe process) The coaloil agglomeration process combines one of the classic separations in the treatment of coal oresGold Extraction Recovery Processes 911Metallurgist2012年11月17日 It describes how pulverized coal is dried, ground, circulated, and classified within the mill to produce a fine powder that is then transported to the boiler burners The main types of pulverizers discussed are ball tube mills, Coal mill pulverizer in thermal power plants PPTRequest PDF On Jan 1, 2019, Santosh Kumar Sriramoju and others published Generation of low ash fine clean coal powder by autogenous grinding Find, read and cite all the research you need on Generation of low ash fine clean coal powder by autogenous grinding
.jpg)
coal grinding machine CHAENG
Process introduction Vertical coal mill, also known as vertical roller coal mill or vertical coal grinding mill, is a mechanical equipment for crushing and grinding coal into coal powerMainly used for grinding raw coal, bituminous coal, and other fuels into coal powder, which is supplied to rotary kiln and other kilns in the cement plant and thermal power plant41 Commercially available coal flow measurement and control equipment 32 411 GreenBank’s PFMaster 33 412 Mistras Products Systems’ Coal Flow Monitoring Systems (CFM) 33 413 PROMECON’s MECONTROL Coal (in USA licensed to Air Monitor Power as PF FLO III) 34 414 MIC’s Coal Flow Analyser 35Optimising fuel flow in pulverised coal and biomassfired boilersA pulverizer coal mill works by grinding coal into a fine powder and then drying it in a hot air fan The coal powder is then blown into a combustion chamber where it is burned to generate heat The hot gases and heat energy produced from burning the coal powder then pass through a series of heat exchangers where the heat is transferred to water to produce steamHow does a Coal Mill Work? AGICO Mining and Cement Milling Equipment 2023年1月1日 The selection of coals mills for power station applications is dependent on a number of process issues such as coal grindability [usually given as Hardgrove Grindability Index (HGI) or bond index], coal moisture, feed size, abrasion index, coal rank (lignite mills, eg, tend to be of very specific design), as well as some practical considerations such as plant layout, Advances in pulverised fuel technology: understanding coal grinding
.jpg)
MPS mills for coal grinding AYS Engineering
2021年3月12日 1 Introduction Two mill systems are employed for most coal grinding applications in the cement industry These are, on the one hand, vertical roller mills (VRM) that have achieved a share of almost 90% and, on the other Coal grinding mills are specialized equipment designed to break down coal into fine particles suitable for combustion The coal grinding process involves crushing and grinding coal into small particles, which are then heated to high temperatures in a furnace, producing steam that drives a turbine to generate electricityWhat is a Coal Grinding Mill• Process flow sheets and Process and Instrument Diagrams • List of Process control loops and Process and Safety Interlocks • List of Instrumentation and Alarms and Process variables with all limits Equipment: Coal grinding mill Author: Jagrut Upadhyay Created Date:COAL GRINDING AND FIRING SYSTEMS HAZOP ANALYSIS2019年8月23日 Coal processing description from its geology mineral property to how to extract coal, and how to increase coal heating, related processing plant flow chart and layout designCoal Processing Equipment, Process Flow, Cases JXSC Machine
.jpg)
Preparation process of coal tar pitch powder and its stability
Temperature[℃] Heat Flow [W/g] 2 Experimental 21 Raw material and reagents Therawmaterialofthecoaltarpitchpowderwas selectedinthehightemperaturecoaltarpitchproducedIn coal combustion, the efficiency and safety of the process are paramount Indirect firing coal grinding systems play a critical role in optimizing these aspects, especially in industrial applications such as power plants and cement manufacturing This article explores the components, advantages, and operational considerations of indirect firing cIndirect Firing Coal Grinding Systems: Enhancing Efficiency and 2023年2月15日 During the process, the crushed limestone mixed with the coal in a ratio of 4 is to 1 It can also be mixed with petrol coke, but ratio will have to be altered then it is burnt in a kiln to release carbon dioxide reaction, which Lime Production Process and Required Equipmentthe temperature of about 900 °C from the cooler flows into the cavity between the burner and the wall of the kiln Heat transfer between flue gas and charge is carried out by radiation and convection Finally the flue gas flows out of the upper end of kiln into the precalciner Process of Clinker Formation in a Cement Rotary Kiln AsModeling of Pulverized Coal Combustion in Cement Rotary Kiln
.jpg)
Pelletizing: The Process, The Equipment, and the Benefits LinkedIn
2022年5月4日 Pelletizing, not to be confused with pelleting (extrusion), continues to see increasing use across industries for the many benefits it can offer to previously difficulttohandle bulk solids and 2014年1月1日 Two mill systems are employed for most coal grinding applications in the cement industry These are, on the one hand, vertical roller mills (VRM) that have achieved a share of almost 90% and, on (PDF) MPS mills for coal grinding ResearchGateCoal mills, essential components in power generation and various industrial processes, pose significant safety risks if not properly managed These mills, used to grind coal into a fine powder for combustion, present potential hazards such as fire, explosion, and mechanical failures This article outlines best practices and precautions to ensure thEnsuring Safety in Coal Mills – Best Practices and Precautions Coal Vertical Coal Mill (VCM) is equipment for grinding and pulverizing coal into micron size Rotary kilns then use the powders as fuel burners The VCM has a housing section equipped with a lining The layout of the coal mill with a rotary classifier
.jpg)
Generation of low ash fine clean coal powder by autogenous grinding
2019年1月15日 Coal is a carbonaceous ore contains maceral and minerals with different properties Due to the presence of high mineral content, the mineral beneficiation process is adopted where the liberation of inorganic minerals plays key role As coal is a soft material, use of impact mills generates coal with homogeneous distribution of minerals In this paper, coal on the grinding table consists of coal to be ground, m c (t), and pulverized coal, m pc (t) The unground coal consists of the raw coal supplied by the feeder belt and coal rejected in the classi cation process The mass of pulverized coal on the table is dependent on the grinding rate Mass of coal suspended in the pneumatic transport, m Improved coal grinding and fuel flow control in thermal power