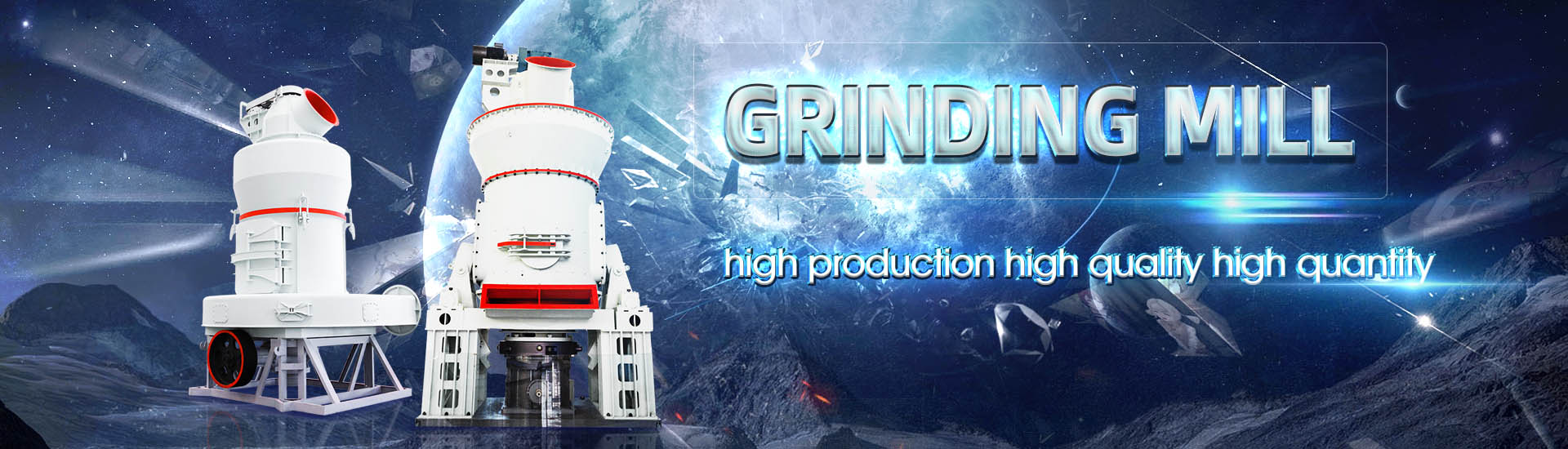
Ball mill Fineness index
.jpg)
A Bond Work index mill ball charge and closing screen product
2017年8月10日 A new commercially available mill ball charge for Bond grindability tests to determine the Bond Work index closely approximates those of Bond's (1961) original total ball 2015年6月6日 This Grindability Test or Bond Ball Mill Work Index Procedure is used to determine the Bond Work Index of minus six mesh or finer feed ore Bond Work Index Procedure and Method2005年8月5日 In this paper, we show the construction of a lowcost, highquality ball mill for obtaining finely divided powders, with the goal of presenting guidelines for achieving the best results for theDetermination of work index in a common laboratory The grindability of raw material is generally determined by Bond’s standard ball mill grindability test (developed by the Allis Chalmers company) The ball mill grindability test is used for describing ore hardness and it is so widespread (PDF) COMPARISON OF THE DIFFERENT WAYS OF THE
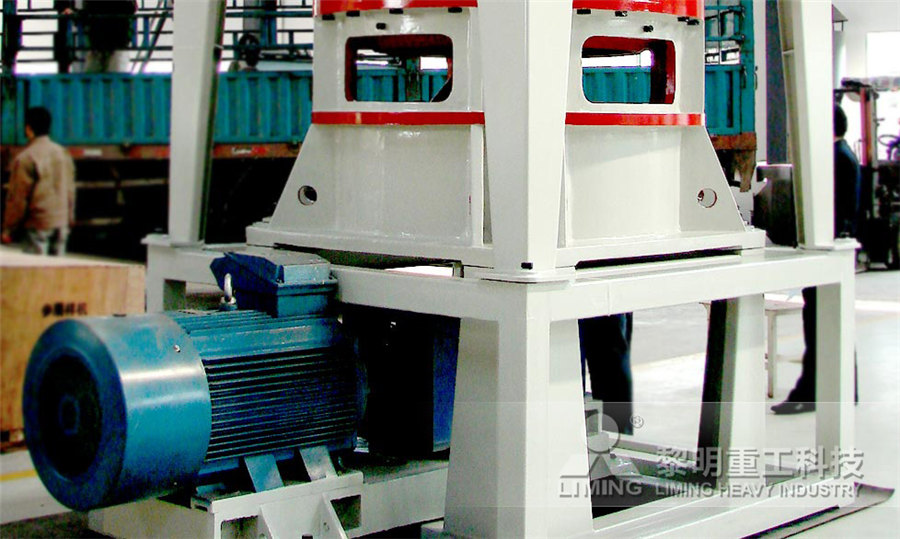
Understanding production of fines in batch ball milling for mill
2018年9月1日 In this paper, we analyze and discuss the rate of production of fines in the ball milling operation There are two main approaches to the scaleup design of ball mills: the Bond 2009年1月31日 It provides the Bond Ball Mill Work Index which expresses the resistance of material to ball milling This happens after 7–10 grinding cycles, which shows that the Procedure for determination of ball Bond work index in the 2016年11月8日 Design engineers generally use Bond equation to estimate specific energy requirements using a parameter called, Bond Work Index, which is determined experimentally Estimation of the Specific Energy Requirement for Size Reduction 2021年7月12日 All of the methods aim to give a close estimation of the Bond work index when the standard Bond ball mill is not available and are faster procedures with a reduced number of grinding steps The longest alternative A Review of Alternative Procedures to the Bond Ball
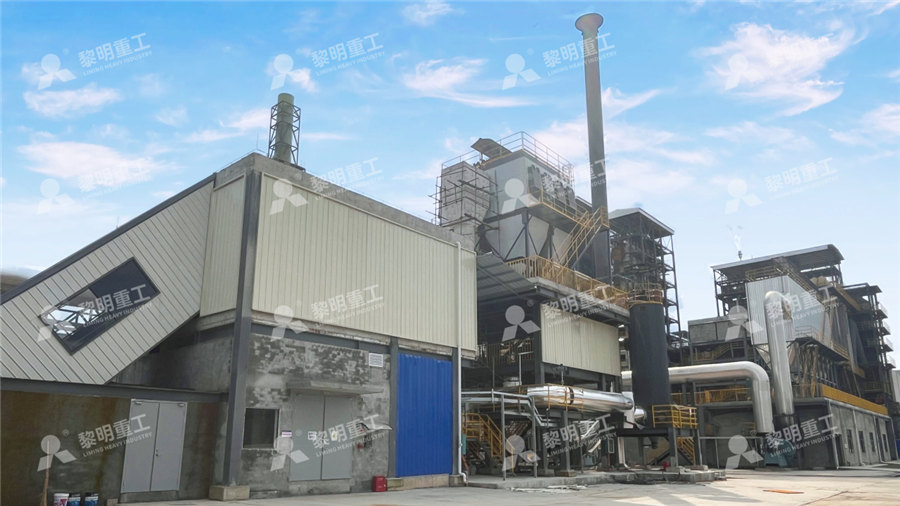
A Study on 500 MW Coal Fired Boiler Unit’s Bowl Mill Performance
For low volatile coals, the fineness passing between 8085% through 200 mesh is suitable to avoid carbon loss due to improper combustion Excessive fineness will lead to wastage of mill power since mill output varies inversely with mill fineness Hence it is recommended that periodic analyses of coal samples and the proper adjustments of2009年1月31日 The Bond ball mill grindability test is run in a laboratory until a circulating load of 250% is developed It provides the Bond Ball Mill Work Index which expresses the resistance of material to Procedure for determination of ball Bond work index in the 2013年8月3日 In Grinding, selecting (calculate) the correct or optimum ball size that allows for the best and optimum/ideal or target grind size to be achieved by your ball mill is an important thing for a Mineral Processing Engineer AKA Calculate and Select Ball Mill Ball Size for Optimum 2023年10月27日 The ball mill is a rotating cylindrical vessel with grinding media inside, which is responsible for breaking the ore particles Grinding media play an important role in the comminution of mineral ores in these mills This work reviews the application of balls in mineral processing as a function of the materials used to manufacture them and the mass loss, as A Review of the Grinding Media in Ball Mills for Mineral
.jpg)
Ball Mill an overview ScienceDirect Topics
A ball mill is a type of grinder containing various metal balls of different sizes that work on the principle of impact mm, K d E is the linear wear rate of balls, µm per kWh t −1, Ai is the Bond abrasion index determined in a laboratory test (unitless), F 80 is the feed 80% passing size of the which are ground to mediumfineness, The Tovarov grindability index is used to determine the influence of materials on the cement clinker grinding capacity of a mill; the basis is rotary kiln clinker with a defined grindability index of a = 1According to this, a mill grinding 30 t/h clinker, will grind 30 x 140 = 42 t/h of marl or 30 x 06 = 18 t/h of silica sand The grindability index of rotary kiln clinker itself varies with Grinding work index according to Bond INFINITY FOR CEMENT EQUIPMENT2005年8月5日 In the Bond ball mill test, the work index is finally obtained by w A correlation between required energy and fineness of grind in comminution is obtained by considering the process over Determination of work index in a common laboratory mill2017年2月13日 The apparent difference in capacities between grinding mills (listed as being the same size) is due to the fact that there is no uniform method of designating the size of a mill, for example: a 5′ x 5′ Ball Mill has a working diameter of 5′ inside the liners and has 20 per cent more capacity than all other ball mills designated as 5′ x 5′ where the shell is 5′ inside diameter and Ball Mills 911Metallurgist
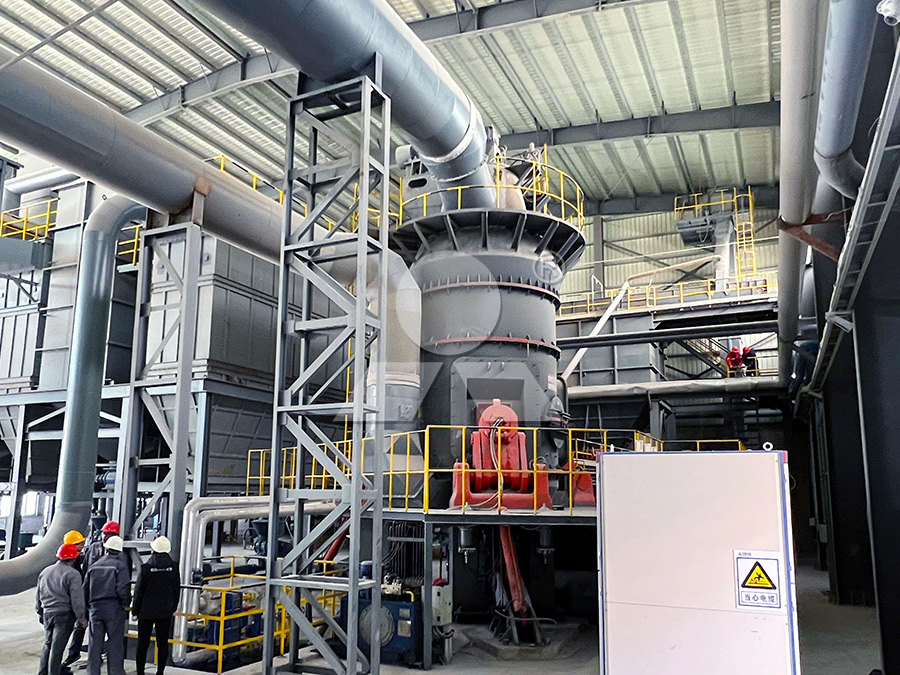
Finish grinding INFINITY FOR CEMENT EQUIPMENT
Fineness requirements for Portland cement are stated in terms of specific surface in square centimeter per gram Grinding aids are materials which facilitate grinding in ball or tube mills, by eliminating ball coating or by dispersing the 4400 HP drive) Bond’s work index for grinding of this ore was determined to 127 kWh/ton 2019年4月3日 Through the analysis of the relationship between the grinding fineness of the Sandaogou gold mine and the mineral dressing index, as well as mathematical analysis of the grinding fineness Ball Mill: Is the Grinding Fineness the Finer, the Better?2023年2月15日 Early signs indicate the ball mill problems, and this article tell people that how to avoid the problems Home; Equipment 1 It refers to the abnormal phenomenon that the fineness of the grinding product is significantly 17 Signs of Problems with Ball Mills: Quickly 2022年10月1日 Based on the standard procedure defined by Bond, the ball mill work index is determined by simulating a closed cycle dry grinding in a laboratory Bond ball mill until a stable circulating load of 250% is established (Bond, 1949, Bond, 1952, Bond, 1961) The ball mill work index is determined by Eq (10)A new methodology to obtain a corrected Bond ball mill work index
.jpg)
AMIT 135: Lesson 7 Ball Mills Circuits – Mining
Bond estimated the amount of wear in terms of kilograms per kWh based on the abrasion index, A;, ie, Wet Ball Mill = kg kWh = 016(A i0015) 033; Fineness of media; Pulp density; Abrasiveness of the material to be ground; To modify Planetary Ball Mills are used for fast and reproducible grinding of materials to analytical fineness versatile in use high energy input Learn More To find the suitable ball size for the desired final fineness, usually a factor of approximately 1000 can be applied If a grind size of 30 µm (D90) Planetary Ball Mills RETSCH fine grinding of materials2018年2月1日 In another study to investigate ball size distribution on ball mill efficiency by Hlabangana et al [50] using the attainable region technique on a silica ore by dry milling, a threeball mix of Effect of ball and feed particle size distribution on the milling 2016年6月3日 Therefore, its foundation can be a concrete floor slab designed for dead load only, whereas a cylindrical ball mill requires a reinforced concrete submat with a minimum of two times the mass of the rotating parts Regrind Mill Work Index The operating work index was also calculated for all available full scale mill data and is shown in Figure 16Tower Mill Operating Work Index 911Metallurgist
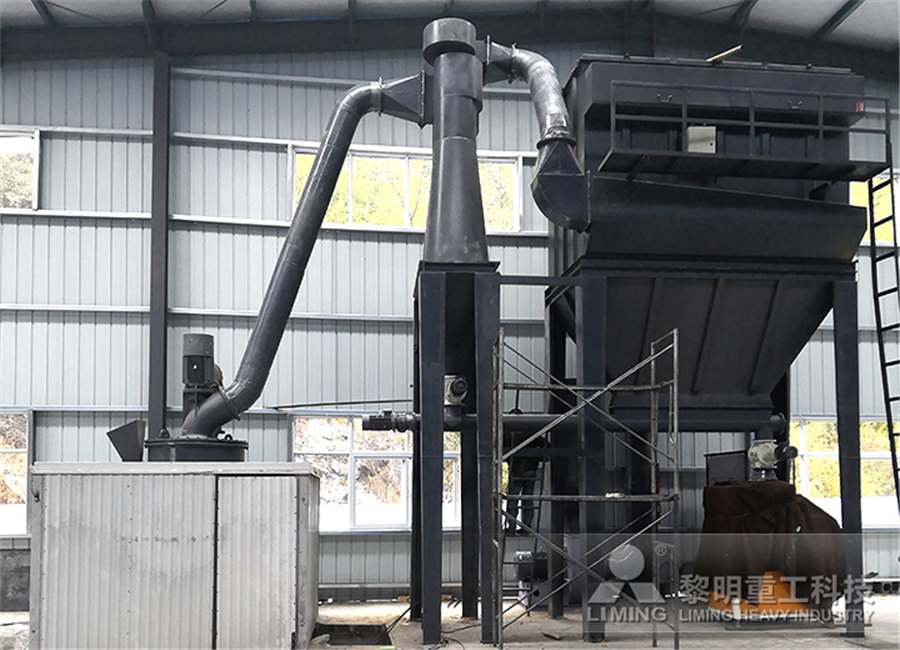
Bond Work Index Procedure and Method 911Metallurgist
2015年6月6日 Cleaning and Storing of Ball Mill Charge after the Bond Work Index Procedure is done: Add about 500 g of silica sand into the mill containing the ball charge Seal the mill Rotate for 20 revolutions to clean Empty the mill charge and sand into the ball try once grinding is complete Clean out the mill using a brush Put the lid on the mill2022年11月1日 With a steadystate population balance model (PBM), their simulation results (Genc, 2016) suggested that for a given cement product fineness, the twocompartment mill yielded approximately 10 % higher mill capacity compared to the threecompartment mill, which contradicts the traditional design in the cement industry of operating threecompartment ball Impact of ball size distribution, compartment configuration, and The drum mill is a type of ball mill suitable for the pulverization of large feed sizes and large sample volumes Final fineness*: 20 µm used as Bond Index Tester: 100 µm with ball module / 2,100 µm with rod module; Grinding drum sizes: 5 l / 10 l / 217 l / 433 lDrum Mills RETSCH fine grinding of large volumesgrinding process (eg cement grinding in a ball mill to a grinding fineness of 3000 cm2/g Blaine), the grindability of a material is characterized in k'Yh/t, the The Hardgrove index is calculated according to the empirical formula H = 13 + 693D (51) where D is the passing rate in gGRINDABILITY OF MATERIALS
.jpg)
Optimization of continuous ball mills used for finishgrinding of
2004年12月1日 The grinding parameters were adjusted over time to maximize mill productivity under stable conditions while achieving similar Blaine fineness as the control mix (ie, Blaine of 3850 ± 75 cm 2 /g)2014年1月1日 accordance to some researc hers (Austin, Klimpel Luckie, 1984) Bond work index may fineness of industrial mill discharge as in a dry ball mill reveals that the following (PDF) Population balance model approach to ball mill 2019年1月19日 Stirred ball mills are generally used for fine and ultrafine grinding of ceramic materials, in food and chemical industry, but this equipment is still an uptodate and relatively new one and SCALE UP FOR ULTRAFINE GRINDING IN STIRRED BALL MILL Ball Mills Insmart Ball mills are completely novel kind of mills for high power granulating The unique Bond’s Work Index Ball Mills; Planetary Micro Milling – PBM; Compaction Insmart 40 Ton Hydraulic Press; Final fineness: Upto 200 mesh: Batch size / feed quantity: 2 Kg, 5 Kg, 10 Kg: Speed at 50 Hz : 50 rpm:Efficient Ball Mills for Cement Plant Quality Control insmart
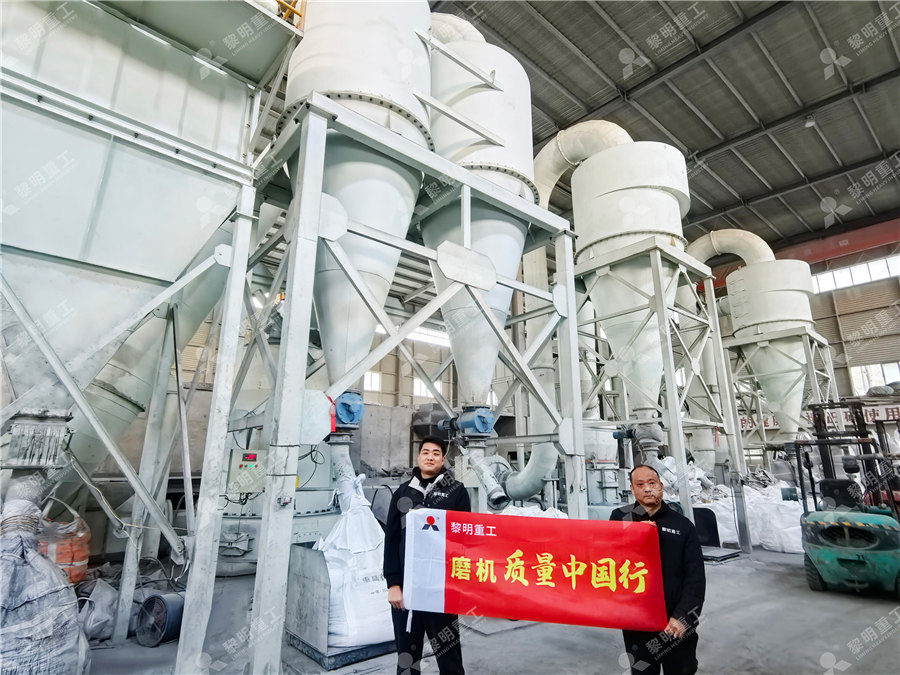
(PDF) Grinding Media in Ball MillsA Review ResearchGate
2023年4月23日 One of the most used tumbling mills is the ball mill [88] in a pilot plant showed an increase in product fineness when ball loading increased from 25%30% and a decrease 2024年8月8日 Unlock the secrets to ball mill efficiency with our comprehensive guide on choosing the right grinding media Learn how material composition, size, shape, Conversely, larger media offer faster size reduction but may not achieve the desired fineness The shape of the media also plays a role, Ball Mill Success: A StepbyStep Guide to Choosing the Right Ball mill optimisation As grinding accounts for a sizeable share in a cement plant’s power consumption, can then measure the material fineness evolution of nominated grain sizes, starting from around 2mm, down to 45µm by drawing such graphs, as shown in Figure 10BALL MILLS Ball mill optimisation Holzinger Consulting2016年1月1日 PDF The Ball Mill Abrasion (BMA) The test produces an index value, which is then used in a formula to provide the m etal wear rate for a particular piece of equipment A comparison of wear rates of ball mill grinding media
.jpg)
Factors Affect The Output and Quality of Ball Mills And How to
2023年12月28日 3 The ball mill is of good quality The better the quality of the ball mill, the more stable the performance of the ball mill will be during operation In addition, as for the lining plate of the ball mill’s wearing parts, the quality of the lining plate affects the overall production efficiency of the ball mill As we all know, the lining Tube and ball mill Bowl Mill, Ball and Race mill Beater Mill, Impact Mill 13 BOWL MILL Coal grindability index Mill inlet and outlet temp Effect of fineness Maximum Mill capacity vs PF fineness at 12 % Raw coal moisture and at Coal HGI 100110 3300 3400 3500 3600Pulverizer Plant OM Aspectspulverised to fineness such that 7080% passes through a 200 Mesh sieve Normally low speed ball mills or medium speed vertical spindle mills are employed in thermal power plant for this purpose The milling system is an important part of the auxiliary equipment of a coalfired power plant Pulveriser mill are one of the critical equipment of coalPulveriser Mill Performance Analysis Optimisation in Super2015年4月24日 2 Ball mill consist of a hollow cylindrical shell rotating about its axis Axis of the shell horizontal or at small angle to the horizontal It is partially filled with balls made up of Steel,Stainless steel or rubber Inner surface of the Ball mill PPT Free Download SlideShare
.jpg)
Process Training Ball Mill INFINITY FOR CEMENT
Process Training Ball Mill The capacity of a system depends on the grindability of the clinker and the fineness it is ground to Depending on the used index, this value indicates the ratio of two percentage portions of two grain sizes It is 2023年11月24日 The ball mill is a rotating cylindrical vessel with grinding media inside, improves the technical index of the classification circuit, Simba, KP; Hlabangana, N; Hildebrandt, D Fineness of the Grind produced by Mixtures of Grinding media of Different shapes In Proceedings of the 16th International Mineral Processing Grinding Media in Ball Mills for Mineral ProcessingRetsch visualises the features and strengths of each ball bill model in a diagram to help finding the right model for a specific application In the example shown it is easy to see that the Planetary Ball Mill PM 300 offers advantages in terms of power, final fineness and maximum jar volume compared to the Mixer Mill MM 500 controlBall Mills Suitable for every application Retsch2022年5月22日 Dry and wet grinding experiments have been carried out with a Bond mill and a laboratory stirred ball mill During the grinding processes, the grinding time and the filling ratio have been adjusted The second goal of this research assessed the resources, emissions and environmental impacts of wet laboratory grinding with the help of life cycle assessment (LCA)EnergyModel and Life CycleModel for Grinding Processes of
.jpg)
Estimation of the Specific Energy Requirement for Size Reduction
2016年11月8日 Table 1 shows a comparison of the specific energy values calculated from Eqs () and for the 100 mesh test sieve (S = 150 µm) and seven values of G in the range of 033–3 g/revIt can be seen that at a G value of 15 both the equations give the same estimate of the specific energy For G values greater than 15 the Bond equation gives relatively higher 2021年7月12日 Determining the Bond index using the Fred Bond method [1,2] is considered the stateoftheart methodology for mill calculations and a critical process parameter in raw materials selection and grinding process controlAlthough it is usually referred to as a standard test, no ISO (International Organization for Standardization) or ASTM (American Society for Testing and A Review of Alternative Procedures to the Bond Ball Mill MDPI2020年1月1日 The ball mill was differentiated into two parts (Fig 3 a), the first part known as the grinding section and the second as the discharge section Both parts are fabricated in such a way that they can easily be fitted by using bolts and nuts, as shown in Fig 3 bA comparative study on a newly designed ball mill and the 2018年6月1日 It was also observed that a binary mixture resulted in more material reporting to the required product fineness compared to having two mills in series with one having 20 mm and other 10 mm ball size For the finer feed material, it was also observed that a binary mixture again resulted in more material reporting to the required product specificationEffect of ball and feed particle size distribution on the milling