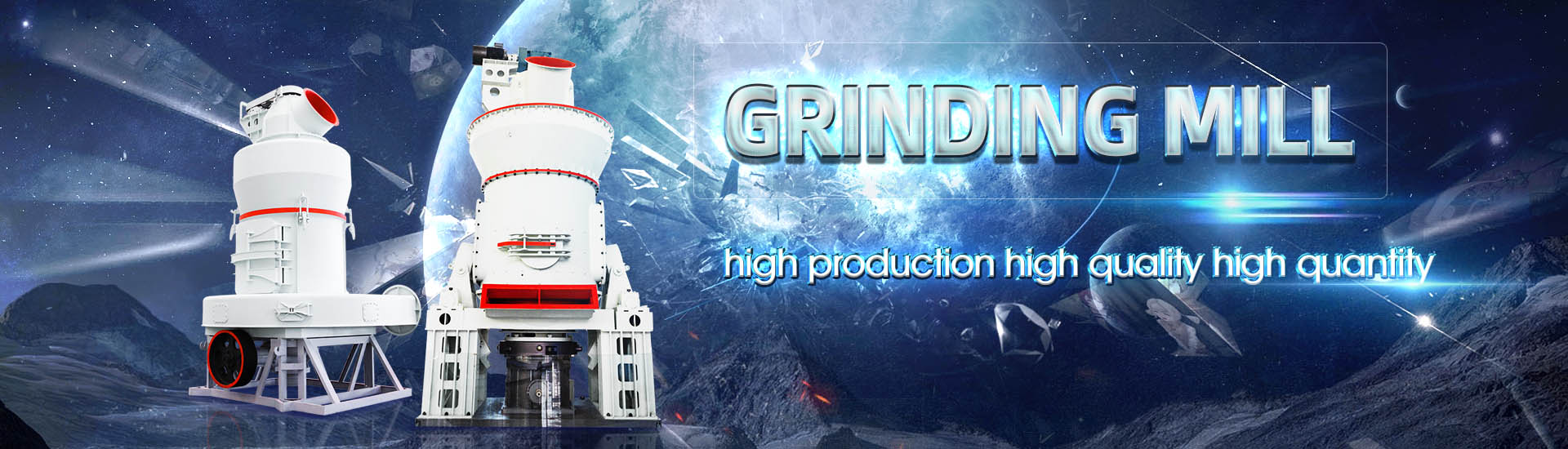
How is the running speed of the ring roller mill stipulated
.jpg)
Speed Roll Laws Influence in a Ring Rolling Process
2013年6月1日 To produce a highquality ring different speed laws should be defined: the speed laws of the Idle and Axial rolls must be set to control the 2023年7月4日 Roller mill is a type of grinding equipment for crushing materials by pressure between two or more rolling surfaces or between rolling grinding bodies (balls, rollers) and a Roller Mill SpringerLink2011年8月1日 Milling speed is one of the most important milling parameters that controls the milling process because it provides the mill with the energy required for (1) powder particles Mill Speed an overview ScienceDirect Topics2017年4月1日 As a result of the study, effects of operational parameters such as working pressure, and classifier rotor speed on product mass flow and product size were investigated Operational parameters affecting the vertical roller mill
.jpg)
Optimal Design to Reduce the Maximum Load in Ring
2012年10月1日 Minimizing the maximum load on rolls in ring rolling process has been the most urgent demand in producing large rings made of highstrength material With a view to meet the essential demand,To achieve a uniform final particle size with minimal fines, the roller mill must have the right roll surface, roll speed ratio, and roll gap for your application Roll surfaceRoller mills: Precisely reducing particle size with greater efficiency2023年12月4日 The present study investigated the effect of mill speed, roller and table gap, dam ring height of an industrialscale VRM, and rolling resistance of particles using DEM In this Numerical Investigation of Vertical Roller Mill Operation Using During the process, the main roll rotates at a rotational speed n1; the mandrel squeezes the ring wall at a feed rate vf and runs idle because of the friction on the contact surface; the axial rolls, Numerical Modelling and Simulation of RadialAxial Ring Rolling
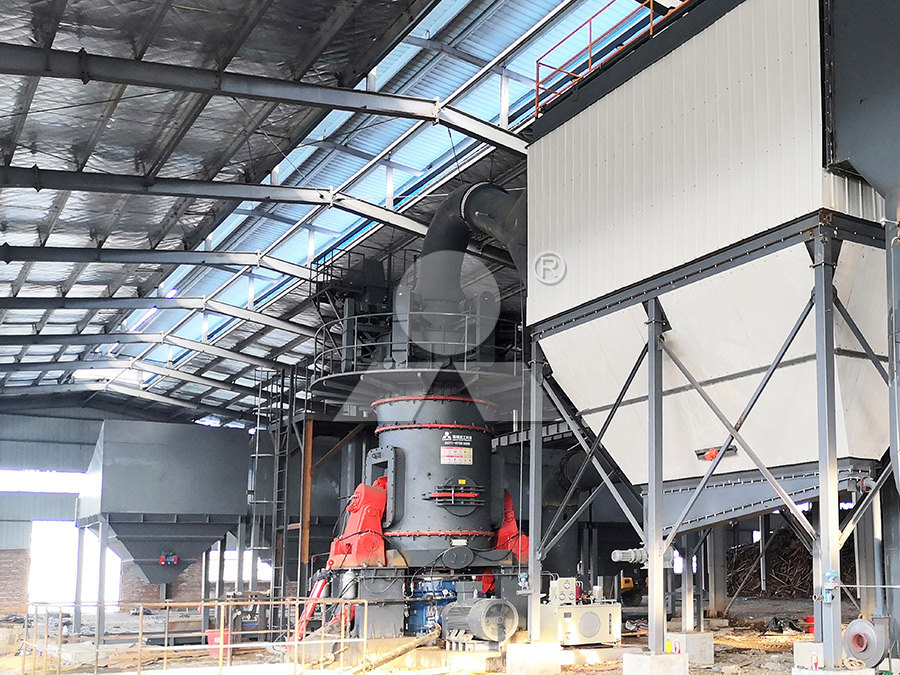
RAYMOND® ROLLER MILLS Thomasnet
The roller mill, when equipped with a variable speed mill drive, can be used in applications requiring adjustable capacity This allows the user to match product rate with downstream 2019年12月9日 The rolling stock of the rolling mill is determined by changing the plastic deformation size How to configure the rolls according to the hole process? Generally, the newly installed rolling mill has a runningin process During the Rolling Mill Production Line: How to Adjust the Roll 2017年4月1日 Grinding test results for zinc ore showed that it is possible to decrease the total grinding energy consumption from 2011 to 1140 kW h/t by using vertical roller mill instead of AG/SAGball mill circuit (van Drunick et al, 2010)Operational parameters affecting the vertical roller mill 2018年3月14日 Detailed analysis of spinning mill setup, cost of production, investments, return on investment, For ring frame efficiency, 20’s count will be at 90% – 91%, 30’s count will be at 91% The ring frame speed depends on the front roller diameter (FRF), twist per inch (TPI) and the spindle speed If FR∅ = 1” (254mm), thenSetting up a Spinning Mill Textile School
.jpg)
Different Parts and Features of Ring Traveller Textile Learner
2016年11月11日 When the spindle speed is increased, the friction work between ring and traveler increases as the 3rd power of the spindle rpm Consequently if the spindle speed is too high, the traveler sustains thermal damage and fails This speed restriction is felt particularly when spinning cotton yarns of relatively high strength2017年4月26日 The ring roller mill adopts the principle of impact, the discharging speed decreased, there will be a coarse powder with a particle size of the product is not uniform The application of ring roller mill in the processing of non2024年1月1日 Roller mill is a type of grinding equipment for crushing materials by pressure between two or more rolling surfaces or between rolling grinding bodies (balls, rollers) and a track (plane, ring, and table)Roller Mill SpringerLinkDie speed is typically measured at the outside diameter of the die, which is either referred to as the “peripheral speed” or the “tip speed” of the die For the majority of applications, the die speed that is generally used for maximum performance should be 9 meters per second for all easyrunning materialsPellet mill design Feed Strategy
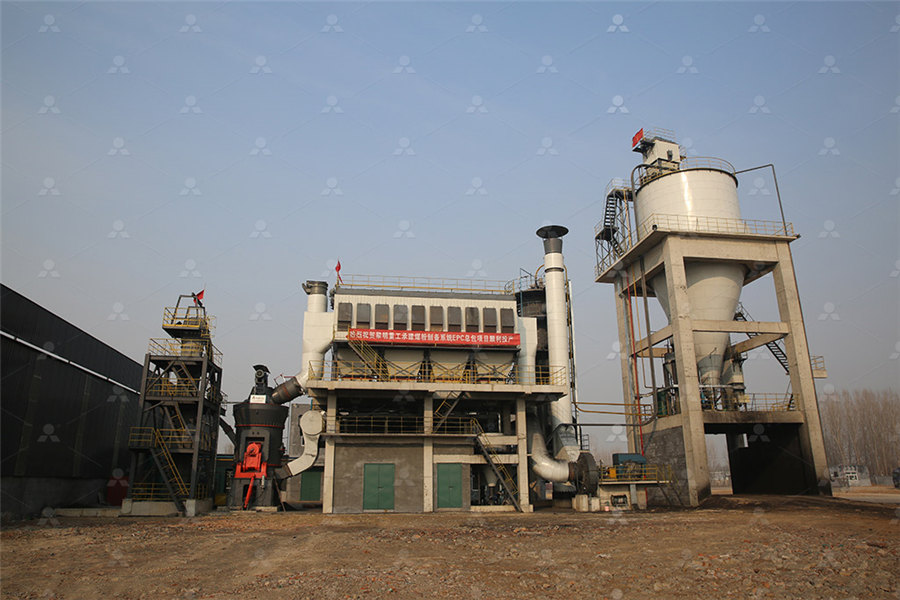
How to Calculate Yarn Production in Spinning Mill
2015年9月16日 Spindle speed = 9000rpm Front roller speed = 203 Length of the circumference 325 inches Turns per inch = Spindle speed÷(Front roller length of the circumference x Front roller speed) = [9000 ÷ (203 x 325)] =1364 inch(ANS) Problem: 03 If 36s warp is spun with 45 twist factor at a spindle speed of 10000 rpm2022年10月21日 1 Difference of grinding system: Raymond mill adopts centrifugal pendulum suspension roller device for rolling, impact crushing The number of rollers is generally 37, and the number of grinding rings is one The contact surface between the grinding roller and the grinding ring is flat, and the interior is equipped with Blade feederHow to choose ring roll mill and Raymond mill SBM Ultrafine The vertical roller mill is used to grind the material by using the principle of material bed pulverization It gathers materials for grinding, conveying, The wind speed of the wind ring is low, and the amount of slag thrown by the mill increases ; When air volume is too large, the following will occur:How to Improve Grinding Efficiency of Vertical Roller Mill2017年9月11日 In this study, an extensive sampling study was carried out at vertical roller mill of ESCH Cement Plant in Luxemburg Samples were collected from mill inside and around the circuit to evaluate the (PDF) Performance Evaluation of Vertical Roller Mill
.jpg)
Review on vertical roller mill in cement industry its
2021年1月1日 India is the world's second largest producer of cement and produces more than 8 per cent of global capacity Due to the rapidly growing demand in various sectors such as defense, housing, commercial and industrial construction, government initiative such as smart cities PMAY, cement production in India is expected to touch 550–600 million tones per ablespeed drives, but the impact rotor is usually provided with a fixedspeed drive The mill in Figure 1 has a coaxial drive assembly, basically consisting of a drive shaft within a drive shaft, which reduces the mill’s overall height (Other drive types are covered in the next section) You can also equip the mill with vibration and bearingHow to operate an air classifier mill to meet your fine grinding goals2015年12月3日 Rolling of steel in Hot Strip Mill satyendra; December 3, 2015; 2 Comments ; AGC, edger, finishing mill, hot strip mill, Laminar cooling, rolling speed, scale breaker, slab roughing mill, tension,; Rolling of steel in Hot Strip Mill Hot strip mills in these days are either conventional hot strip mills or strip mills for rolling thin slabsRolling of steel in Hot Strip Mill – IspatGurulow vibrations, low noise emission and zero grinding forces, the mill can even be erected outdoors Process flexibility, energy efficiency, and high throughput characterize this mill type Compared to a traditional ball mill, the roller mill consumes 40 to 50 % less energy By combining 3 process steps – grinding, drying,QUADROPOL QMC Roller mill for the grinding of cement and
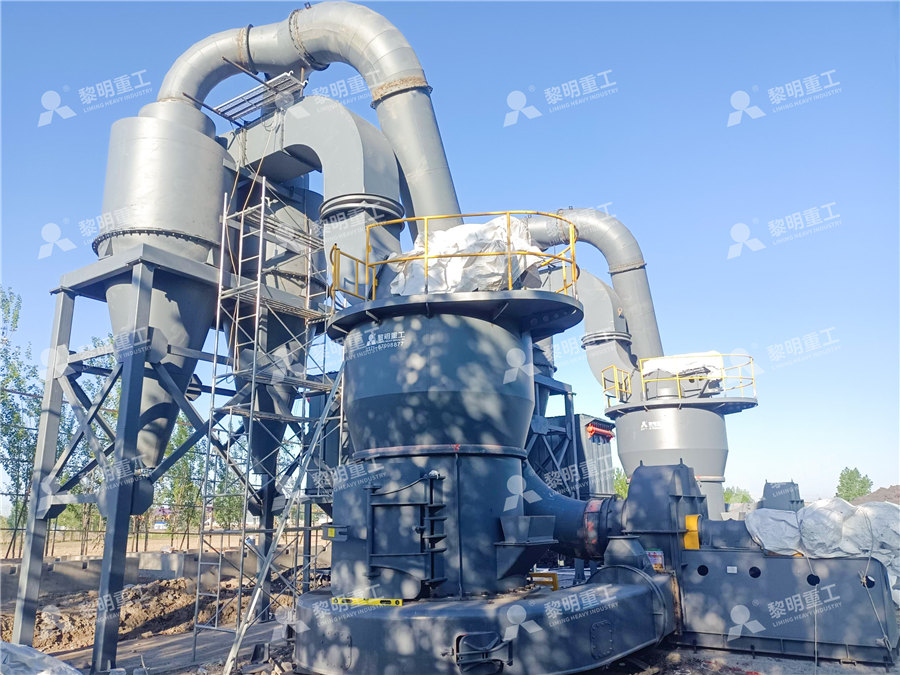
Raymond Roller Mill PartsUltimate Guide Fote Machinery
2023年2月15日 Main parts of Raymond mill include grinding roller, grinding ring, powder collector, classifier, air blower, reducer, base plate, shovel, Raymond mill pendulum, star stack, etc Main materials of the parts: manganese(16Mn, 65Mn), High manganese steel, high chromium(Cr13、Cr23、Cr26)2021年1月29日 VRM Production Rate and Specific Power It can be clearly seen in Figure 3 that last 6 months average breakdown frequency Rate was 6016 tripping per month means per day more than 2 trippingIncrease productivity of vertical roller mill using seven QC tools2020年12月13日 This is the tiny key parts of ring spinning frame which travels around the ring at 3035 m/sec and impart twist to the yarn The hardness of the running traveler must be within 650700 vickers Contact pressure between ring and traveler is up to 35N/mm² Generate high temperature (300400°C) the mass of traveller is 16120gm/1000Ring Spinning Machine: Drafting System, Different Parts and 2024年10月9日 Check the Manufacturer’s Guidelines: Always start with the manufacturer’s instructions, as each roller mill model may have specific adjustment protocols Determine Desired Particle Size: Knowing the required size for your end product is crucialThis will guide how much you need to adjust the roller gap Adjust the Roller Gap: Use the adjustment mechanism to The Ins and Outs of Roller Mill Adjustments Midwest Hardfacing
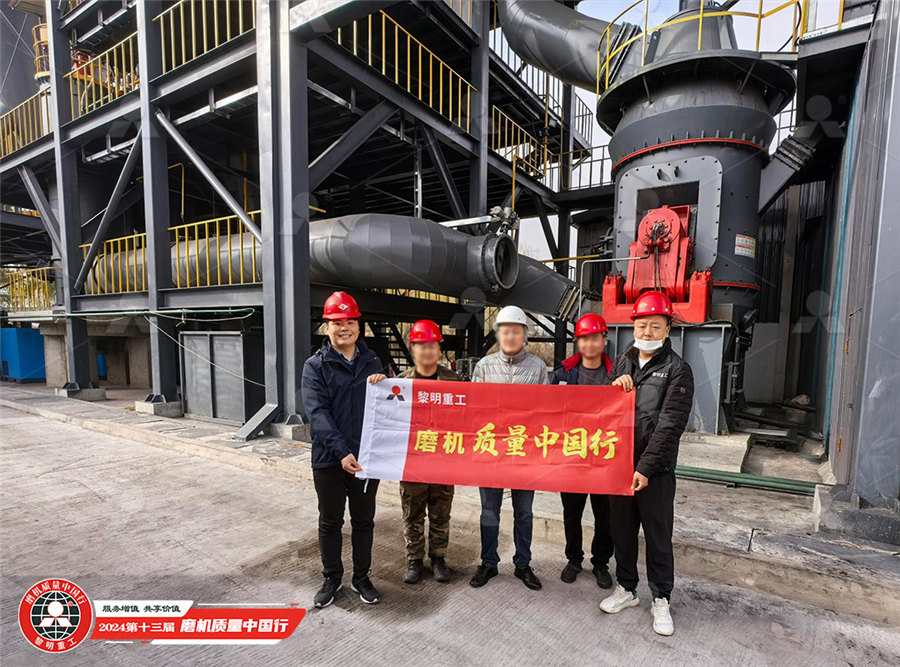
Roller mills INFINITY FOR CEMENT EQUIPMENT
Roller mills are now operated with throughput capacities of more than 500 tons per hour of cement raw mix (Loeschemill, Polysius double roller mill, Pfeif ferMPSmill, SKET/ZABroller mill) The working principle of roller mills is based on two to four grinding rollers with shafts carried on hinged arms and riding on a horizontal grinding table or grinding bowl2022年11月29日 A ringspinning frame produces 60 s with a TM of 40 The spindle speed of 15000 rpm and the ring diameter is 15″ Front roller speed is 150 rpm The front roll diameter is 1″ and the production efficiency of 94 % Ring spinning twist calculation% FAQ Textiles School2015年10月23日 In this chapter an introduction of widely applied energyefficient grinding technologies in cement grinding and description of the operating principles of the related equipments and comparisons over each other in EnergyEfficient Technologies in Cement Grinding2021年4月6日 Introduction Ring Frame is the last and most important machine in a spinning mill where the final draft is applied on roving and converted to yarn with the required count, ie, the final yarn with desired count gets spun on the Ring Frame Production Calculation Formula with
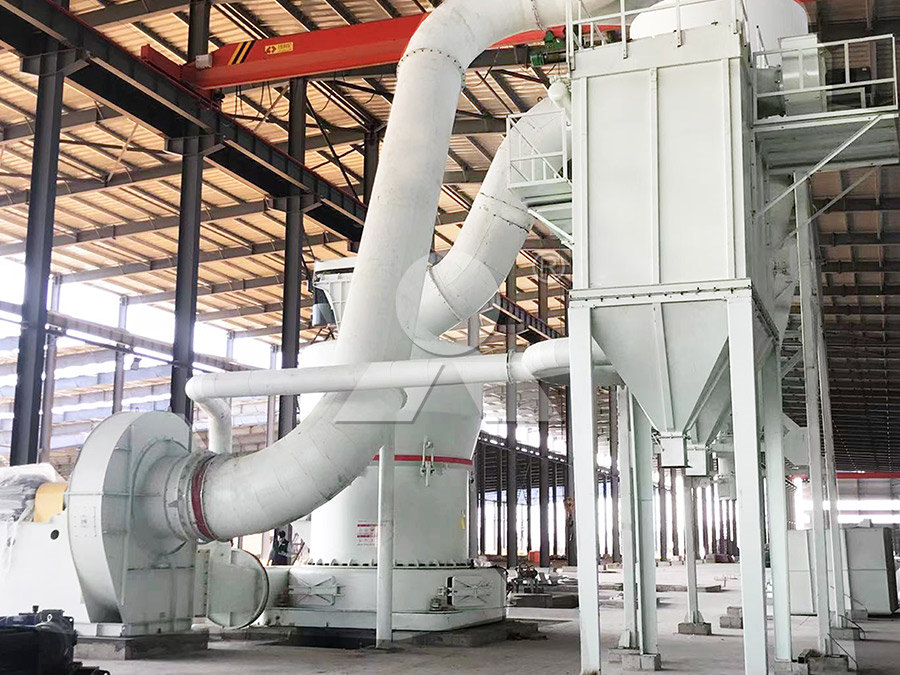
Static Structural Analysis of Crushing Rollers of Three Roller Sugar Mill
The top roller is most highly stressed, since it consumes about half of the mill torque The forces on the top roller are because of power transmission, crushing, and hydraulic load The loads on the roller are divided into horizontal and vertical component of loading Power(p)= 900 kw Roller Speed (n)= 5 rpm Roller dia= 1200 mmTable Energy saving effect of the vertical roller mill Ball mill Specific power Cost estimation About 14million US$ [Newlybuilt] and about 230 million US$ [retrofitted], including the cost of supplemental facilities [200tRM/h] [1US$=¥110] Related matters References Fig1 Vertical roller mill Vertical roller mill Effect(%)Vertical roller mill for raw Application p rocess materialsVertical roller mills and ball mills represent two clearly distinct technologies However, with proper adjustments to the operational parameters of the vertical roller mill almost identical cement properties can be achieved by the two mills that satisfy the cement user’s demandsNevertheless, the two types of mills have their distinctive meritsCement grinding Vertical roller mills VS ball mills2019年12月9日 Fig 2 Fatigue type roll failure and saddle shaped spall in rolls Spalling Spalling can be another reason for roll failure There are two different kind of spalls in the rollsAbnormalities and Failures of Rolling Mill Rolls – IspatGuru
.jpg)
RAYMOND® ROLLER MILLS Thomasnet
Raymond roller mills are available with grinding ring diameters ranging from 30 inches to 120 inches (760 to 3050 mm) These sizes are capable of producing a wide range of product fineness from a wide variety of materialThere are two main layouts for a vertical roller mill (VRM) system, with product collection in cyclones or a filter The power consumption of a VRM is calculated using factors like the specific grinding pressure, roller dimensions, grinding track speed, and number of rollers The grinding pressure has components from the roller weight and hydraulic system Key internals are the Vertical Mill Calculations PDF Mill (Grinding) NozzleChina Ring Roller Mill wholesale Select 2024 high quality Ring Roller Mill products in best price from certified Chinese Roller Flour Mill manufacturers, Three Roller Machine suppliers, wholesalers and factory on MadeinChina Rotationl Speed: 15003000 Application: Mine Materials: Calcite, Limestone,Dolomite,Clay,Barite and QuartzRing Roller Mill MadeinChina2004年3月1日 The paper's title is "ASSESSMENT OF THE EFFICIENCY OF RING SPINNING FRAME ON A SPINNING MILL" One primary way to increase profit and quality in the ringspinning process is to keep the end down (PDF) The Mechanism of End Breakage in Ring
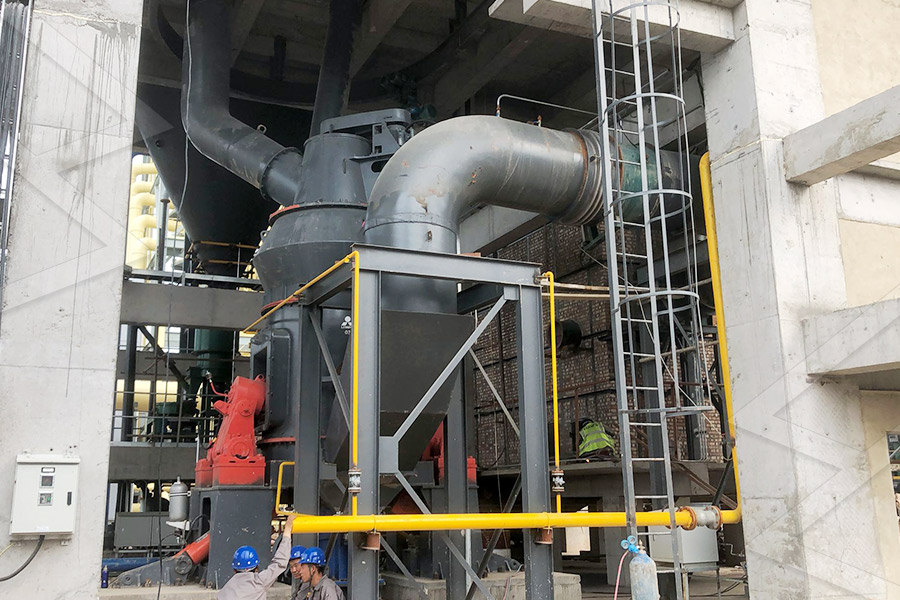
Factors affect the operation and running of vertical
2021年11月5日 Summary:Vertical roller mill is suitable for the largescale processing of nonmetallic mineral powders below 1250 meshIts largescale and energysaving effects are significant Vertical roller mill is suitable for the large 2015年11月27日 Input values for setting mill motor speeds are production rate, roll collar diameters and roll gaps, bar areas and widths, and gear ratios Motor speed ratings are normally checked against calculated speeds Mill utilization Understanding Rolling Process in Long Product 2015年7月28日 We will begin with the mill’s bull gear assembly and work towards the motor, The BULL GEAR, sometimes called the RING GEAR is designed to turn the mill transforming the energy of the motor into motion for the mill By mill we refer to Ball Mills, Rod Mills and SAG Mills Anything gear and pinion reallyGrinding Mill Gear Assembly 911Metallurgist2014年8月20日 The Rotor design is the key to the operation of the openended spinners Each type of fibre may require a different rotor design for optimum product quality and processing speed The first openend machines in the United Kingdom were placed, under great secrecy, by courtaulds into maple mill, Oldham in 1967Working Principle of Rotor Spinning Fiber Processing in Rotor
.jpg)
(PDF) DESIGN AND ANALYSIS OF ROLLER SHAFTS FOR SUGAR
Roller shell dimension of different roller, as shown in table 1 tjprc editor@tjprc 830 R R Karthi L Emmanual Table 1: Shell Dimensions Rollers Outer Diameter (mm) Groove Depth (mm) Pitch Circle Diameter (mm) Feed 878 778 8002 Top 915 48 867 Discharge 900 615 8385 Setting: Feed roller side =36mm, Discharge roller side =145mm, Trash plate side =70mm This type of mill features a single set of corrugated rolls that spin at the same speed with a welldefined gap between the rolls The range of moisture levels that this type of mill is compatible with is from very dry all the way to high moisture Roller Mill Features: Strong construction Solid chilled iron rolls with heavyduty shaftsRoller Mills IFA Iowa Farm Automation2017年7月17日 Running at faster speeds is typical, but for more viscous substances, running at a slower speed can help avoid slipping Seeing how much slower or faster a machine can run will can impact throughput For this experiment front roller Threeroll mill selection tips Processing MagazineRoller Mill Maintenance Mark Heimann Roskamp Champion 2975 Airline Circle Waterloo, Iowa USA 50703 Tel 319 232 8444 Fax 319 236 0481 sales@cpmroskamp running the rolls together with pressure and no feed will greatly accelerate roll wear Evidence of roll to roll contact would be corrugations with topsCPM Roller Mill Mainten
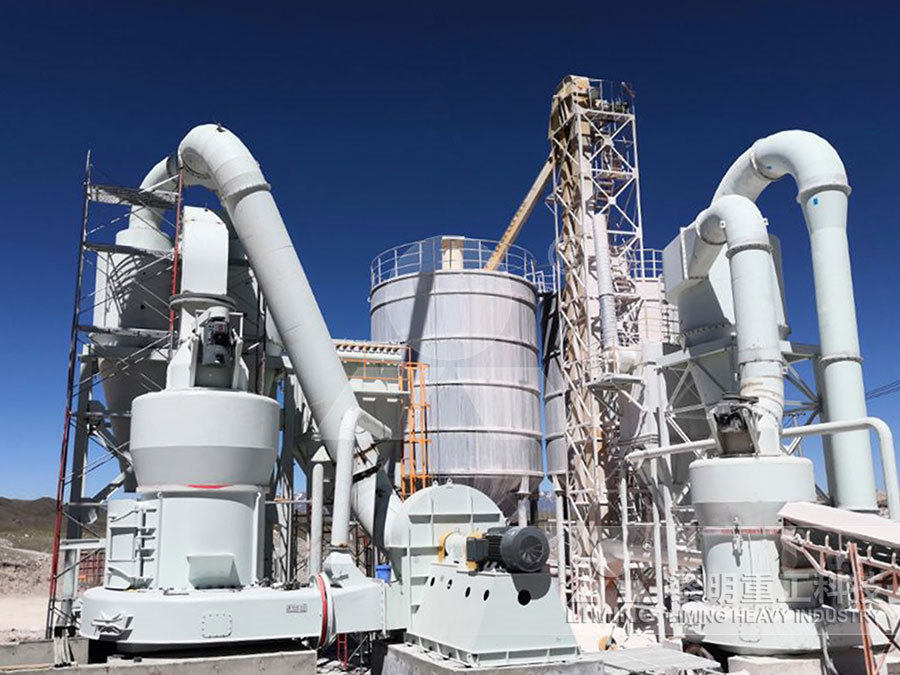
Operational parameters affecting the vertical roller mill
2016年9月1日 Furthermore, VRM separator speed (rpm) is one of the key operational parameters that determines product particle size Increasing the classi er rotor speed from 60 to 80 rpm decreases the particle