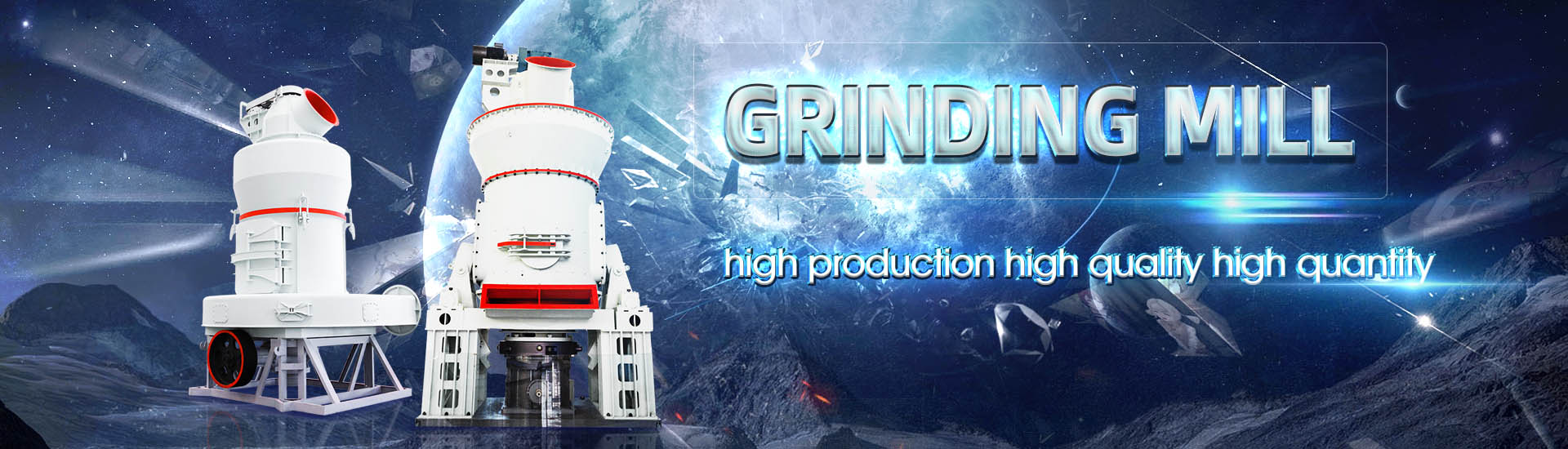
Dry powder limestone production flow chart
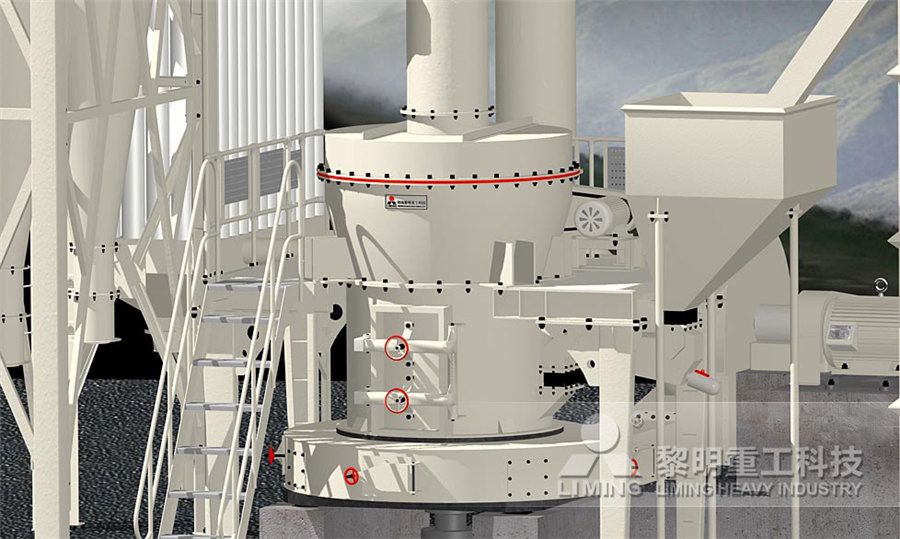
Limestone Quarrying and Processing: A LifeCycle Inventory
Process flow diagram for limestone processing operations Processing commences with transportation of the (raw) stone from the quarry to the processing facility, as depicted by A generalized material flow diagram for a lime manufacturing plant is given in Figure 11171 Note that some operations shown may not be performed in all plants The heart of a lime plant 1117 Lime Manufacturing US EPAThe document outlines the process for active lime production Limestone is fed into a crusher and preheater before entering a kiln where it is heated to a high temperature, converting it to Lime Production PFD PDF PDF ScribdLow heat skim milk powder is dried up to 3 to 4 per cent moisture, while high heat skim milk powder usually has not more than 35 per cent moisture (j) Cooling: Most milk driers have a continuous removal system to immediately separate the dry product from the hot air stream The dry product should be cooled at onceHow to Manufacture Dried Milk or Powdered Milk [With Process Flowchart]
.jpg)
Cement Manufacturing Process: Know Extraction,
2024年9月10日 Steps of Cement Manufacturing The steps involved in cement manufacturing are as follows: Quarrying: Raw materials such as limestone and clay are extracted from quarries or mines; Crushing and Grinding: The 2012年8月30日 Rotating table rotates continuously under the roller and brought the raw mix in contact with the roller Roller crushes the material to a fine powder and finishes the job Raw mix is stored in a prehomogenization pile after Cement Manufacturing Process Engineering IntroThe cement production process 1 The Quarry: The cement production process begins with the extraction of limestone and clay from the quarry 2 Crusher and PreBlending: The material is then crushed to reduce particle sizes and blended to reduce variability in composition 3 Raw Mill and Kiln: Raw materials and additives areA practical guide to improving cement manufacturing processes Milk powder manufacture is a simple process able to be performed on a large scaleProduction involves the gentle removal of water at the lowest possible cost under stringent hygiene conditions while retaining all the desirable natural properties of the milk such as Dry process of cement we civil engineers Dry process These are two different processes of manufacturing cementwet quicklime powder production process flow chartmd
.jpg)
Wet Process Of Cement Manufacturing With Flow Chart
Wet Process Of Cement Manufacturing With Flow Chart The raw materials are calcareous materials, like limestone or chalk, Cement manufacturing is done majorly by two methods known as wet process and dry process depending on their mixing is 2019年11月30日 c) The application of modern technology has made the production of cement by a dry process more economical and of superior quality Significant advancements have been made in raw material grinding, preheating, controlled clinker cooling, cement grinding, and packing technologies with advanced process control and instrumentation system in recent yearsManufacture Of Portland Cement Process Flow chart civil Burning: In this operation, the slurry is directly fed into a long inclined steel cylinder called a Rotary kilnIn this kiln there are 3 different zones shown in fig below Cement Manufacturing Process Flow Chart (i) Drying Zones: In the wet process, the drying zone is comparatively larger than the dry process It is because the raw material in slurry form is directly fed into the kiln Manufacturing of Cement By Dry and Wet Process Expert Civil2018年8月28日 Such raw materials are limestone, clay and sand Limestone is for calcium It is combined with much smaller proportions of sand and clay Sand clay fulfill the need of silicon, iron and aluminum Extraction of raw material and crushing of material Generally cement plants are fixed where the quarry of limestone is near byeCement Manufacturing Process The Engineering Community
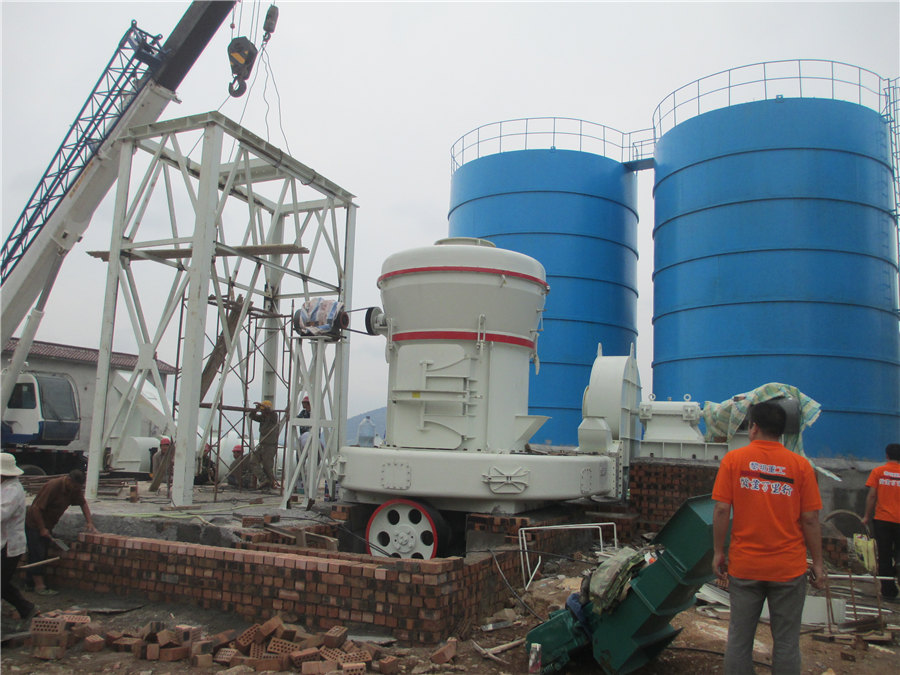
Flow chart of wet granulation (upper), dry granulation
It is a promising method that not only enhances individual fine API powder properties, [29][30] [31] [32][33][34] but also their blends 9,10,20,[35][36][37] Notably, Han et al (2013a), examined 2021年3月9日 In this study the process flow diagram for the cement production was simulated using Aspen HYSYS 88 software to achieve high energy optimization and optimum cement flow rate by varying the flow rate of calcium Simulation and Optimization of an Integrated Process 2024年8月9日 Limestone dry powder grinder machines are specialized equipment designed to grind limestone into fine or ultrafine powder for various industrial applications Applications: Commonly used in the production of limestone powder for agricultural lime, filler materials, and road construction See More Chat Now 26 Types Of Limestone Dry Powder Grinder Machinesprocesses in the production of lime are: (1) quarrying raw limestone; (2) preparing limestone for the kilns by crushing and sizing; (3) calcining limestone; (4) processing the lime further by hydrating; and (5) miscellaneous transfer, storage, and handling operations A generalized material flow diagram for a lime1117 Lime Manufacturing US EPA
.jpg)
Flow chart for the production of ogi powder ResearchGate
Flow chart for the production of ogi powder 22 Dry powder portions (3 g) each was put into dry clean 50 mL graduated cylinders, and the initial volume noted after being carefully leveledMilk Powder Production Milk Powder Producers Milk Powder Specification Some links for manufacturers of powders Lumps containing dry powder in the middle are formed and, if enough air is locked into these lumps, they will float to Milk Powder Production Milk Powder Producers Milk Powder The slurry is introduced into a rotary kiln, a lengthy cylindrical boiler that rotates on its axis The kiln consists of three zones: the upper zone, known as the preheating zone, where hot gases from the lower zone dry and heat the slurry; the middle zone, known as the calcining zone, where a temperature of about 1500 °C is reached and the calcium carbonate in the slurry breaks down 2 Types of Manufacturing of Cement Wet and Dry Process2000年7月31日 Emissions Control Strategies for Power Plants Bruce G Miller, in Coal Energy Systems, 2005 Dry Flue Gas Desulfurization Technology Dry FGD technology includes lime or limestone spray drying; dry sorbent injection, including furnace, economizer, duct, and hybrid methods; and circulating fluidizedbed scrubbersDry Flue Gas Desulfurisation Technology ScienceDirect
.jpg)
Limestone Density kg/m³: Bulk, Crushed, and Powder
Limestone Powder Density kg/m³ Limestone powder, also known as ground limestone or limestone dust, is a fine material obtained by grinding limestone rock The density of limestone powder typically ranges from 2,600 to 2,800 kg/m³ This high density is due to the fine particles packing closely together, leaving minimal void spaces2016年1月20日 In 2011, the world cement production was approximately 360 Bt/330 Bt (clinker) (USGS, USGeological Survey 2014), requiring more than 300 Bt of limestone for the manufacture of clinker (Schneider et al, 2011) However, large material flows solely related to cement production have a significant impact on society and the environmentAnalysis of material flow and consumption in cement production duce cement in dry route is approximately half of the energy required to produce it through the wet process The most common way to manufacture Portland cement is through a dry process The first step is to quarry the principal raw materials, mainly limestone, clay, and other materials After quarrying, the rock is crushedChapter 4 Cement Manufacturing and Process Control2014年6月10日 It begins with an overview of what cement is and how it is used to make concrete It then describes the industrial process for manufacturing cement, involving grinding raw materials like limestone and clay at high Cement manufacturing process PPT Free Download
.jpg)
(PDF) Milk Powder Production Food processing
2021年5月1日 The milk powder production process is a simple process carried out on a lar ge scale The feed inlet rate (F) is given at wet basis, yet it must be used at dry basis in the The block diagram of the production process of cement is given below : Figure 1 : Cement production process block diagram 2 Cement production step by step 21 Limestone rock crushing Limestone rock crushing typically involves the use of a crusher machineCement Production Demystified: StepbyStep Process and Table 91 Limestone and Other Crushed Rock Production and Energy Consumed by Type a Units 1987 1992 1997 Limestone and Rock Production b Billion tons 12 12 Energy Consumption Coal Thousand tons Withheld 785 430 Fuel oil c Million bbl 36 34 40 Gas Billion Cubic Feet 17 32 54 Gasoline Million Gallons 142 155 147 ElectricityLimestone and Crushed Rock Department of Energy2021年3月3日 Lime is the least expensive and one of the most heavily used alkali in the world, being essential to our society It is a nonhydraulic binder, excepting the socalled hydraulic lime, meaning that it will not set under waterFor this reason, lime is sometimes called air lime since it hardens on exposure to air It was used for thousands of years in masonry mortars to bind the Lime SpringerLink
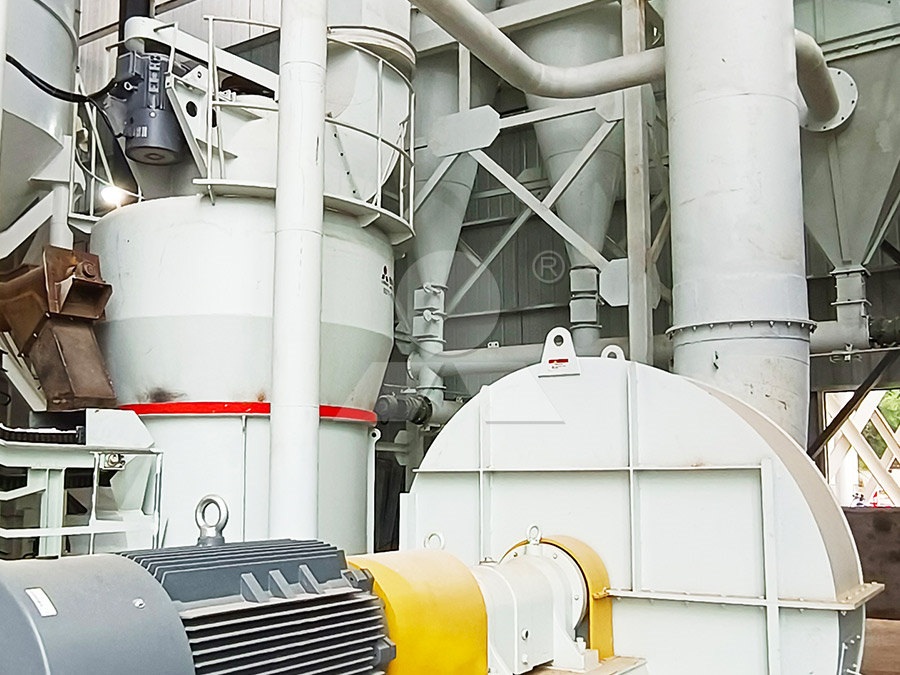
How Cement is Made Portland Cement Association
With this crude method, Joseph Aspdin of Leeds laid the foundation for an industry that annually processes literally mountains of limestone, clay, cement rock, and other materials into a powder so fine, it will pass through a sieve Portland cement is the basic ingredient of concreteQuicklime When a calcium limestone or chalk rock, that comprises mainly of calcium carbonate (CaCO 3), is heated in a kiln, it changes by a process called calcination into quicklime also known as 'burnt lime' and chemically is mainly calcium oxide (CaO), and the calcination process releases a gas from the rock which is carbon dioxide (CO 2) Hydrated LimeMaking LimePowder production is carried out in two phases In the first phase, the pretreated milk is evaporated to a dry matter content of typically 48 – 52 % Whey is concentrated to a dry matter content of 58 – 62 % In the second phase, the concentrate is turned into powder in a spray dryer Likewise, drying is also a multiplestage process:MILK AND WHEY POWDER Dairy Processing Handbook2024年11月23日 Cement Extraction, Processing, Manufacturing: Raw materials employed in the manufacture of cement are extracted by quarrying in the case of hard rocks such as limestones, slates, and some shales, with the aid of blasting when necessary Some deposits are mined by underground methods Softer rocks such as chalk and clay can be dug directly by Cement Extraction, Processing, Manufacturing Britannica
.jpg)
Milk Drying Systems and Processes [with flow chart]
The systems and process of milk drying can be classified as follows: Drying Milk by Cold Treatment: (a) Drying Milk by Freezing Out the Water and Centrifuging: This system was proposed and patented as early as 1884 and is now obsolete (b) Drying Milk by Freezing and Sublimation: This freezedrying method, which seems to have []The production flow chart for wet calcium carbide slag, 1# and dry calcium carbide slag, 2# are described in Figures 1 and 2 respectively In a general, the processes mainly include measures to stabilize the composition of the raw Application technology of calcium ZKG1971年8月17日 sixdigit SCC for plants with dry process kilns is 305007 Portland cement accounts for 95 percent of the hydraulic cement production in the United States The balance of domestic cement production is primarily masonry cement Both of these materials are produced in portland cement manufacturing plants A diagram of the process, which116 Portland Cement Manufacturing US EPAIn a bin, the powder is submitted to pressure, due to the fact that there is a height of powder in the bin, the powder on top pushing on the powder below the hopper Due to the pressure, some solids tend to be more cohesive , when powders Hopper design Flow of powder
.jpg)
Flow Chart Of Cement Industry { Dry Process } Blogger
Dry grinding generally use closed operating system Normally open wet milling system, but there is also a closed system Second, the cement production of calcined Currently mediumsized multi use rotary kiln cement plant , small cement plant kiln multi use , there are more than 50 percent of China’s cement kiln production still use A Download scientific diagram Synthetic gypsum production flow chart from publication: Structurally controlled synthesis of synthetic gypsum derived from industrial wastes: sustainable approach Synthetic gypsum production flow chart ResearchGate2022年12月21日 ProjectManager’s kanban boards turn production flow charts into workable plans Learn more How Does a Production Flow Chart Work? The production flow chart works as a visual production management tool It’s a picture that illustrates each step of a process in sequential order and it’s used for defining or analyzing new processes, standardizing or How to Make a Production Flow Chart for Manufacturing 2024年7月29日 The combined CO 2 emissions of limestone powder, groundnut shell ash and caustic soda for block production was range between 50% and 62% of the total CO 2 emissions The mortar mix L50G50Na15 has the lowest CO 2 emission rate, measured in kgCO 2 , which is 60% lower than the control mortarAlkaliactivated limestone powder and groundnut shell ash based
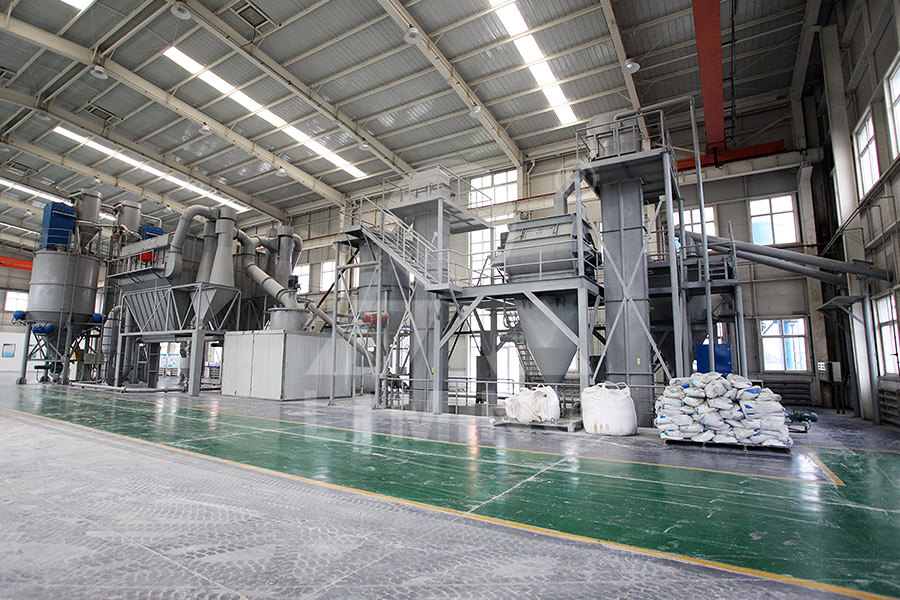
Limestone Grinding Mill That You Need To Know Dry Mortar Plant
2023年9月19日 Limestone grinding mill Material: Limestone Finished product particle size: 01730044mm Processing capacity: 8176t/shift Applicable materials: calcium carbonate crushing processing, gypsum powder processing, power plant desulfurization, nonmetallic ore pulverizing, coal powder preparation, etc Main limestone grinding machines Vertical roller [0016] Such as figure 1 As shown, a limestone dry grinding process system includes a feeder, a dry vertical mill 2, a bag dust collector 3, a main fan 4, a pneumatic conveying device 6 and a finished limestone powder storehouse 7; the feeder It is connected with the dry vertical mill 2, and the dry vertical mill 2 is connected with the bag filter 3, and the bag filter 3 is connected with Limestone dry grinding powder manufacturing process systemA multistage production process is necessary to transform the SO 2 in flue gas, into panelgrade FGD gypsum that will meet the precise specifications of gypsum panel manufacturers As flue gas is generated, it is passed through an electrostatic precipitator that separates fine particles, including fly ash, from the gasFGD Gypsum Production Process