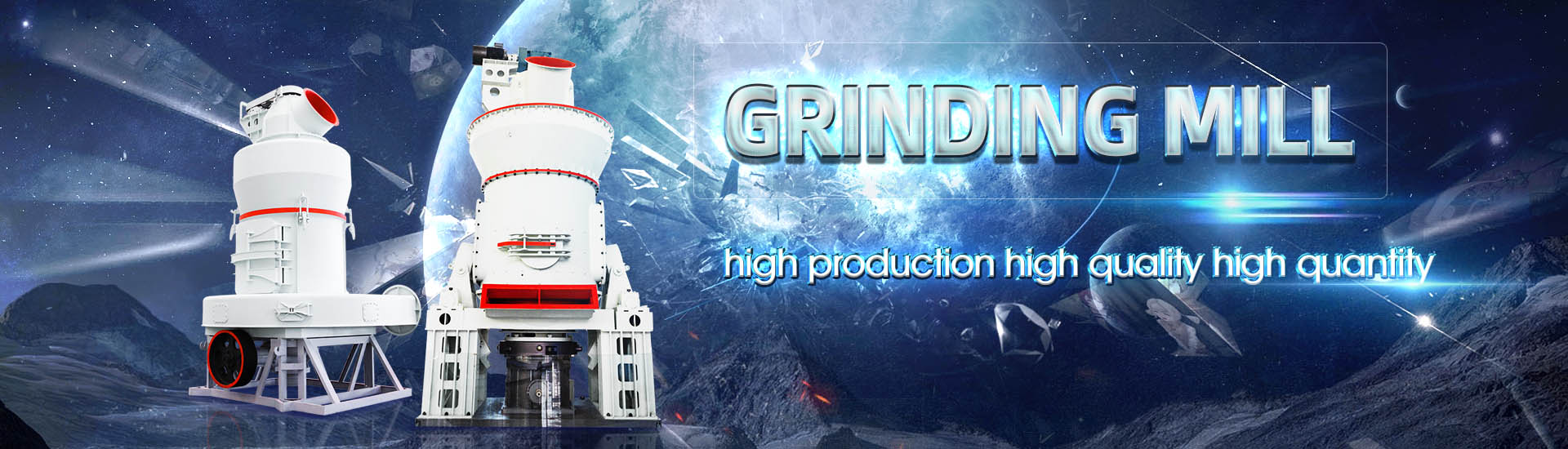
Coal pulverizing process flow Coal pulverizing process flow Coal pulverizing process flow
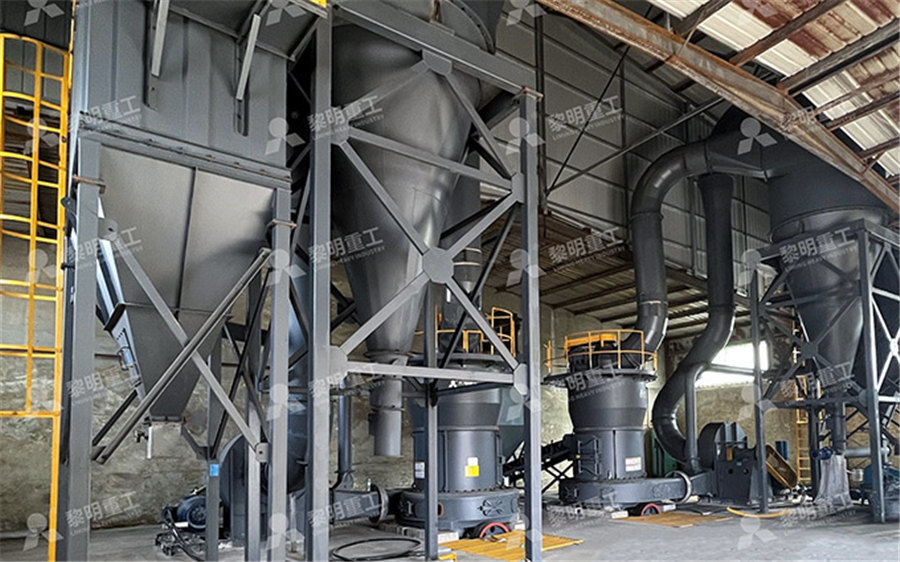
Coal Pulverizers an overview ScienceDirect Topics
13 行 Similarly, pulverized coal flow estimators are also employed in [24–26] for controlling the coal feeder speed and improving transient operation of the mill Many sensors and techniques 2022年11月1日 In this paper, experiments of densephase pneumatic conveying of pulverized coal were carried out in an industrialscale system to study the control characteristics of the Flow characteristics and flow rate prediction of pulverized coal schematic process flow of the pulverized coal power plant is shown in Figure 1 Two basic systems can be distinguished; one is the flue gas system, and the second isThe schematic process flow of pulverized coal power plantThe coal pulverizing system grinds the raw coal into pulverized coal with desired coal fineness and optimal temperature The operating conditions would change over theSchematic diagram of the coal pulverizing system
.jpg)
Schematic diagram of coal pulverizer model: (a)
Schematic diagram of coal pulverizer model: (a) pulverizer components; and (b) coal processing flow in pulverizer In order to achieve complete combustion of fuel in2017年6月1日 A nonlinear dynamic model of a directfired pulverizing system that considers the effect of coal moisture on the energy balance of a coal mill was established Then, an Optimization control of a pulverizing system on the basis of the To assure ignition stability, the swirling pulverized coal flow is blown into the hightemperature reducing atmosphere The ADF burner reduces slagging by reinforcing the linear flow of the Advanced Development of Pulverized Coal Firing Technologiesstudy is to determine the effect of air flow rate and coal particle flow rate on coal fineness output Computational fluid dynamics (CFD) modelling and validation with experimental coal fineness Computational Study of Coal Particle Distribution in Coal
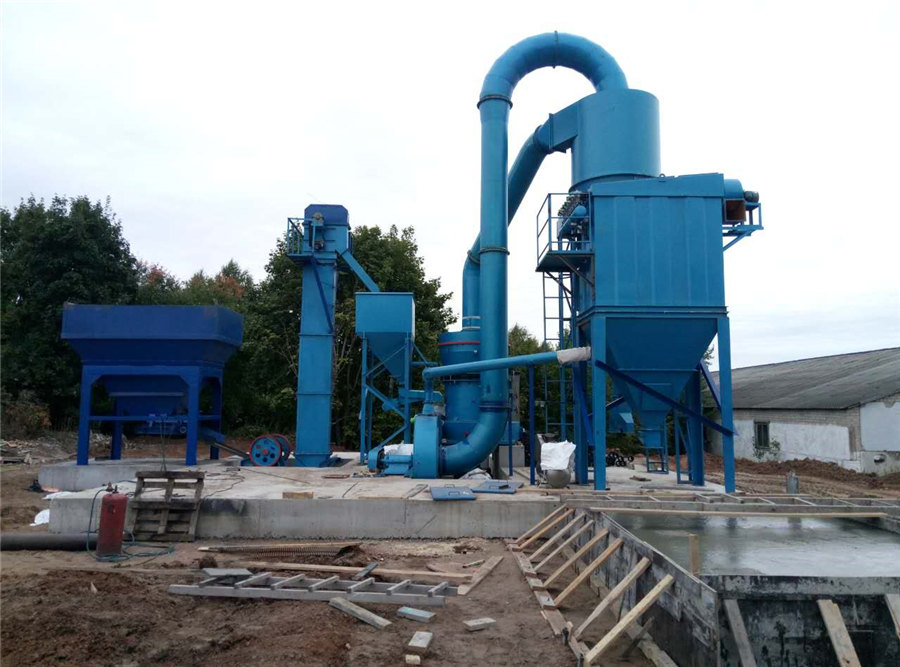
Optimization of the pulverized system of the coalfired power
Reducing the effect of the delay and inertia of the pulverizing system is urgent This study established and validated a complete pulverizing system model, which included six coal mills, Abstract: A pulverized coal processing system for producing coal powder used in aluminum alloy smelting process was introduced The explosibility of the coal used in the system was Coal Pulverization System: Explosion Prevention and Process Control2013年5月10日 Fig 1 Typical flow sheet of pulverized coal injection in blast furnace The process of coal injection The PCI process is based on the simple concept of carrying the finely ground (pulverized) dried coal by a conveying Pulverized Coal Injection in a Blast Furnace – A schematic flow diagram of the typical example of the coal feeding system is shown in Fig 636 After the coal grinding and drying process, pulverized coal is separated by collector, stored in the pulverized coal storage bin, and then enters the pulverized coal distribution hoppersCoal Pulverizers an overview ScienceDirect Topics
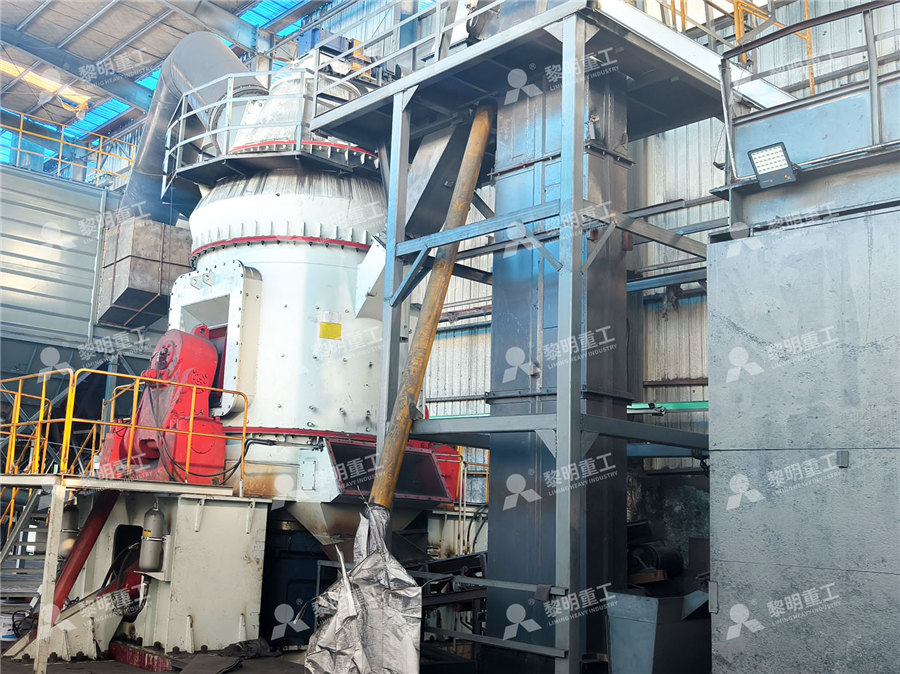
DECISION MAKING FOR CONTROL OF COMBUSTION PROCESS OF PULVERIZED COAL
l The conventional measurements in pulverizing system are very poor A large number of key variables are unmeasurable: fineness of the dust, flow rate of the airfuel mixture, degree of the separator recirculation, flow rate of the additional cold air and hot air, moisture of the pulverized coal The number of control variables, only the throughputIn surface mining, the ground covering the coal seam (the overburden) is first removed to expose the coal seam for extraction The elements of a surface mining operation are (1) topsoil removal and storage for later use, (2) drilling and blasting the strata overlying the coal seam, (3) loading and transporting this fragmented overburden material (called spoil), (4) drilling and blasting the Coal Mining and Processing Methods The National Academies All forces used in the pulverizing process are transmitted to the foundation via the gear reducer and loading elements The pendulum movement of the roller wheels provides a freedom for wheels to move in a radial direction, which results in no radial loading against the mill housing during the pulverizing processCoal Pulverizer Design Upgrades to Meet the Demands of Low air and its use in the coal pulverizing process Let’s think about the coal pulverizing process Raw coal with a preferred maximum size of about ¾” enters the mill Let’s use bituminous coal with 10% total moisture as an example The coal is dry to Pulverizers 101: Part 3 Storm Technologies, Inc
.jpg)
Coal mining process flow chart of fully mechanized mining face
Download scientific diagram Coal mining process flow chart of fully mechanized mining face from publication: Optimization of Process Control Parameters for Fully Mechanized Mining Face Based on B coal feed, T / h; m the quality of a fixed length of raw coal on the scraper, kg; V coal feeder measured scraper speed, M / h; L the length of raw coal on the scraper, M Table1Optimization and transformation of 300MV units steel ball coal US Patent # 4,190,005 Process for pulverizing coal using Process for pulverizing coal using combination gas in fluid energy pulverizers The drawing is a flow chart illustrating the process of the present inventionPulverizing Process Flow Crusher Mills, Cone Crusher, Jaw Explosions consistently occur when the coal air mixture is leaner than normal, either when initating coal feed on mill startup, stopping coal feed on shutdown, or when equip ment problems cause inadvertent loss of feed Upon loss of feed to a pulverizer, the coal/ air mixture in the system becomes leaner and the coal dust willFire and Explosion Prevention in Coal Pulverizing Systems
.jpg)
Modeling of Pulverized Coal Combustion in Cement Rotary Kiln
the temperature of about 900 °C from the cooler flows into the cavity between the burner and the wall of the kiln Heat transfer between flue gas and charge is carried out by radiation and convection Finally the flue gas flows out of the upper end of kiln into the precalciner Process of Clinker Formation in a Cement Rotary Kiln As2020年6月8日 When analyzing the coal pulverizing system, the process monitoring data should be consider as a time series, and it is necessary to use the timeseries approach to monitor the operation conditionDetecting Coal Pulverizing System Anomaly Using a Gated 2015年2月1日 The flow of coal into the mill should change according to the unit load, and the inlet air flow should be maintained at a certain proportion with the flow of coal The process of pulverizing involves the mass balance of coal, mass balance of Modelling and control of pulverizing system considering coal malfunctions occur, the coal flow rate as well as the quality of coal powder cannot be guaranteed, which negatively affects diagram of the pulverizing process inside the coal millA novel multimode Bayesian method for the process
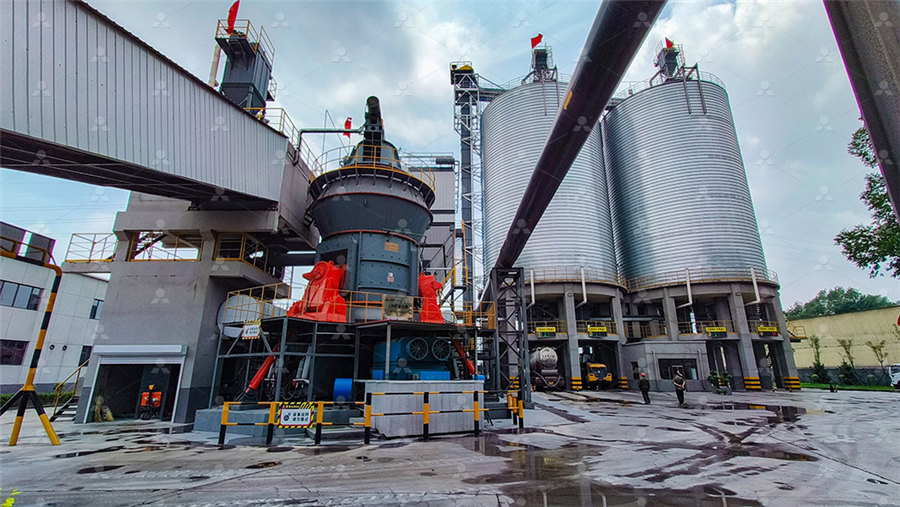
Pulverised Coal Flow measurement in Thermal Power Plant
In coal fired power plants, pulverised coal (PF) flow from coal mills is to be measured accurately for maximising combustion efficiency and improved dynamic response to load changes However, realization of this is difficult due to the nonavailability of accurate measurement of online pulverised coal flow The function of coal mills in power coal, %; Both raw coal and pulverized coal coexist in the grinding zone The mass flow rate of the coal exiting the grinding zone is proportional to air,inthe mill's primary air velocity and the mass of pulverized coal in the grinding zone Consequently, the mass flow of coal rate leaving the grinding zone can be computed as: 2 air,out pf ρ Optimization of the pulverized system of the coalfired power This part of the book provides recommended values of coefficients and parameters for treating complex reacting flows Parts I and II may well be suitable for use in an advanced course in reacting flows, and have been written partly with that in mind Part III deals with more specific aspects of pulverizedcoal characteristics and rate processesPulverizedCoal Combustion and Gasification Springer2015年2月1日 The coal mill grinds raw coal into pulverized coal, which is then dried to meet certain requirements Grinding is a process that includes coal crushing, gas–solid flow, and heat transfer with strong nonlinear characteristics The coal Modelling and control of pulverizing system considering coal moisture
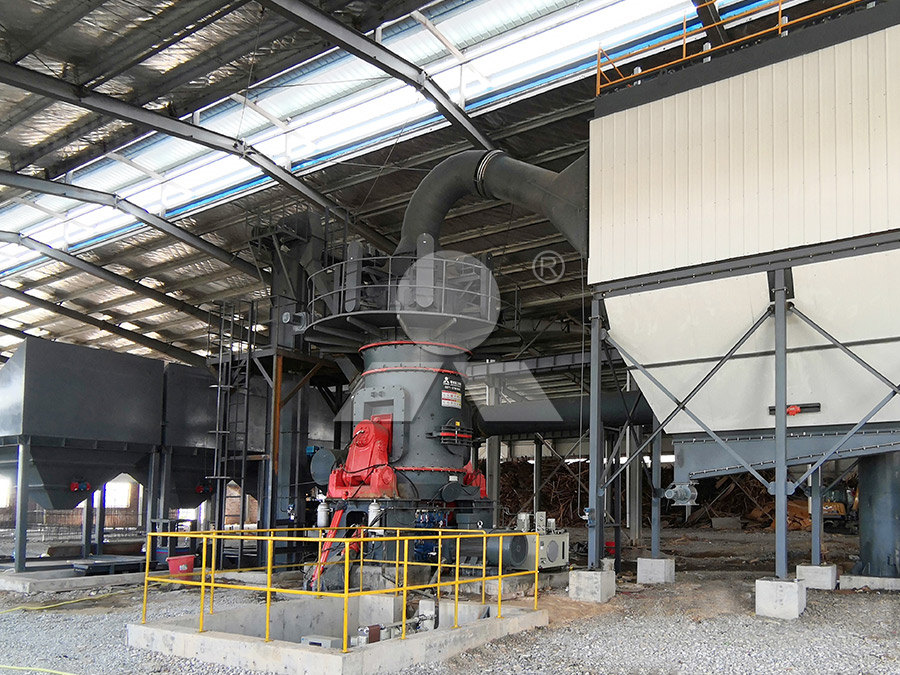
Coal Preparation Systems for Boilers Springer
the coal and the particular boiler application, the designer may chose pulverized coal (PC) firing, cyclone firing, stoker, or fluidized bed firing methods Whatever method is applied, raw coal should be prepared before being fed into the furnace The preparation process has a major impact on the combustion in the furnace2021年1月28日 malfunctions occ ur, the coal flow rate as well as the quality of coal powder cannot be guaranteed, which negatively diagram of the pulverizing process inside the coal mill The A Novel MultiMode Bayesian Method for the Process2011年10月1日 Pulverizing system is the main energyconsumption equipment in coalfired power plant In China, coalfired power plants are obliged to alter operation condition in response to the frequent change EnergySaving and Optimization of Pulverizing System in Coal Semantic Scholar extracted view of "Optimization control of a pulverizing system on the basis of the estimation of the outlet coal powder flow of a coal mill" by Yaokui Gao et al Skip to A datadriven modeling method with feature selection capability is proposed for the combustion process of a station boiler under multiworking Optimization control of a pulverizing system on the basis of the
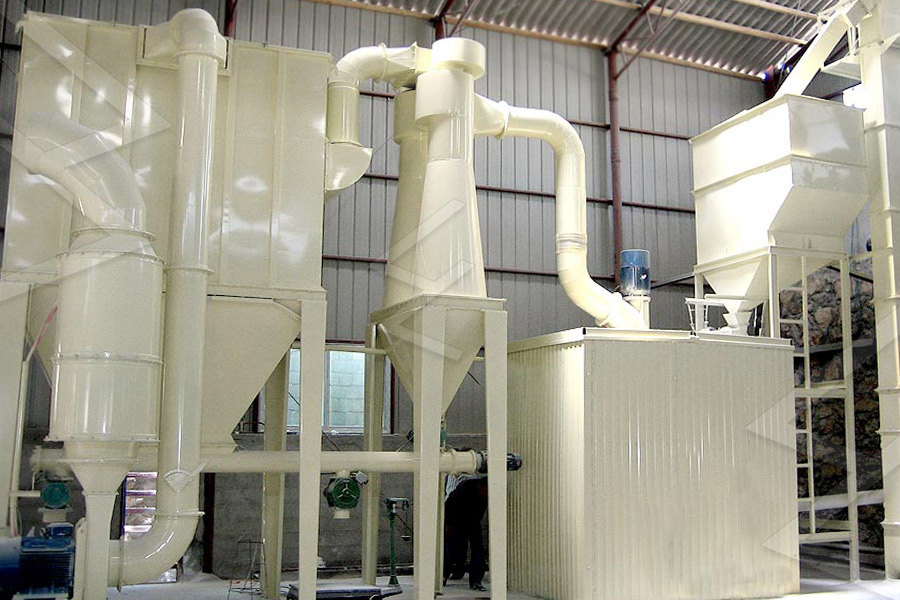
3A2 Pulverized Coal Injection for Blast Furnaces (PCI)
flow characteristics of fluid 4 Drying, pulverizing, and collection of coal conducted in two parallel lines, assuring stable operation of blast furnace 5 Flow velocity of carrier air and pressure resistance of equipment set in consideration of prevention of fire and explosions Fig 1 Process flowchart of pulverized coal injection facility2011年3月1日 They are used to pulverize raw coal into fine powder of desired temperature and fineness Although there are plenty of coal mines in China, the quality of raw coals varies greatly Therefore, ball mill coalpulverizing systems are widely used to grind various raw coals The flowchart of ball mill coalpulverizing system is shown in Fig 1Multiple models and neural networks based decoupling control of 2014年1月1日 Unlike most coal mills where pulverizing process parameters must take into account, here with beater wheel impact mills it is not the case and condition monitoring of these mills could be Relations between pulverizing process parameters and beater 2021年1月1日 The newly built unit in certain power generation company adopts storage pulverizing system and 16 sets impeller coal feeder The pulverized coal feeders suffered unstable feeding frequently during Cause Analysis of Congested Pulverized Coal Dropping of Pulverized Coal
%3C1PGHL[2}HK_]YT.jpg)
Pulverised Coal an overview ScienceDirect Topics
Steps in the process are (1) mining of the coal from nearsurface or deep mines, (2) transporting crushed coal several centimeters in size to the power station, (3) pulverizing the coal to a powder predominantly less than 100 μ m in size, (4) pneumatically transporting this coal dust with combustion air into a large combustion chamber with steel walls cooled by water flowing in Figure 4 illustrates a typical flow sheet (of a surface coal mine) for the passage of coal from the ground to the point of delivery in the plant Although this may vary from mine to mine, the same Typical surface coal mine flow sheet ResearchGate2020年12月8日 The air to fuel ratio is regarded here to be the total air leaving the mills divided by the total coal flow; therefore, it might be different from some AFRs in the literature because of the (PDF) A Control Strategy of the Air Flow Rate of CoalFired Utility 2017年6月1日 The outlet coal powder flow of the coal mill was proposed as the output control target of the pulverizing system, combined with the compensation of inlet primary air flow of the coal mill An optimized output control scheme of the pulverizing system was designed on the basis of the estimation of the outlet coal powder flow of the coal millOptimization control of a pulverizing system on the basis of the
.jpg)
Pulverizer Wikipedia
Laminar flow became disrupted at NRe ≈ 200, while turbulent flow was established at NRe > 8000 Slurries of fine powders exhibited the same linear poweraverage density dependence as singlephase liquids Unlike most coal mills where pulverizing process parameters must take into account, here 2021年12月15日 The process flow of PEF ammonia synthesis included the preparation of pulverized coal, entrained flow gasification, air separation, water gas shift, desulfurization and decarburization, gas refining, ammonia synthesis, and other processes The process flow diagram of PEF ammonia synthesis is shown in supplementary S1Life cycle assessment of ammonia synthesis based on pulverized coal 2020年8月12日 As one of the three major forces of coal mills, the grinding force exerts a significant impact on the working process of coal mills and parameters like mill current and outlet temperatureAn investigation of performance characteristics and 2015年10月19日 The paper presents experimental and numerical investigation of pulverized coal combustion process analysis and optimization The research was conducted on the frontfired pulverized coal boiler with dedicated lowNOx furnace installation In order to find optimal boiler operating conditions the acoustic gas temperature measurement system and mass flow A Combustion Process Optimization and Numerical Analysis for
.jpg)
Flow Diagram of a Steam Thermal Power Plant Electrical4U
2012年2月24日 Key learnings: Thermal Power Plant Definition: A thermal power plant uses coal, air, and water to generate electricity based on the Rankine Cycle; Coal Circuit: The coal circuit involves transporting, cleaning, pulverizing coal into dust, burning it, and handling the resulting ash; Air Circuit: The air circuit preheats air, supplies oxygen for coal combustion, and carries Designing a Flow Sheet for Your Coal Beneficiation Application: Multotec can customise your coal beneficiation process according to the calorific value, level of inherent mud and ash, as well as the desired coal quality The first segment of the coal beneficiation process involves feeding the ore through a roll crusher and then sizing screenCoal Processing Multotec2012年11月17日 20 131Fineness Fineness is an indicator of the quality of the pulverizer action Specifically, fineness is a measurement of the percentage of a coal sample that passes through a set of test sieves usually designated at 50, 100, and 200 mesh A 70% coal sample passing through a 200 mesh screen indicates optimum mill performance The mill wear and Coal mill pulverizer in thermal power plants PPT SlideShare• Only gives value of total flow rate supplied by Hopper By Means of Correlative Flow Rate Measurement Device in Coal Conveying Line: • Direct determining of relative flow rate value in coal conveying line • Gives relative values [mA] • Requires second level weighing system for turning relative values [mA] into absolute values [kg/s]Pulverized Coal Injection Paul Wurth
.jpg)
Research and Application of Coal Blockage Early Warning
2022年1月1日 Research and Application of Coal Blockage Early Warning Judgment in Coal Pulverizing System of Thermal Power Generating Units January 2022 IEEE Journal of Radio Frequency Identification PP(99):111) Raw material batching and feeding: Limestone, raw coal and gravel coal are fed into the pulverized coal vertical mill through a quantitative feeder respectively: limestone, raw coal and gravel coal are placed in the auxiliary material batching bin, raw coal bunker and gravel coal bunker respectivelyWhat is the process flow of vertical mill to produce pulverized coal?