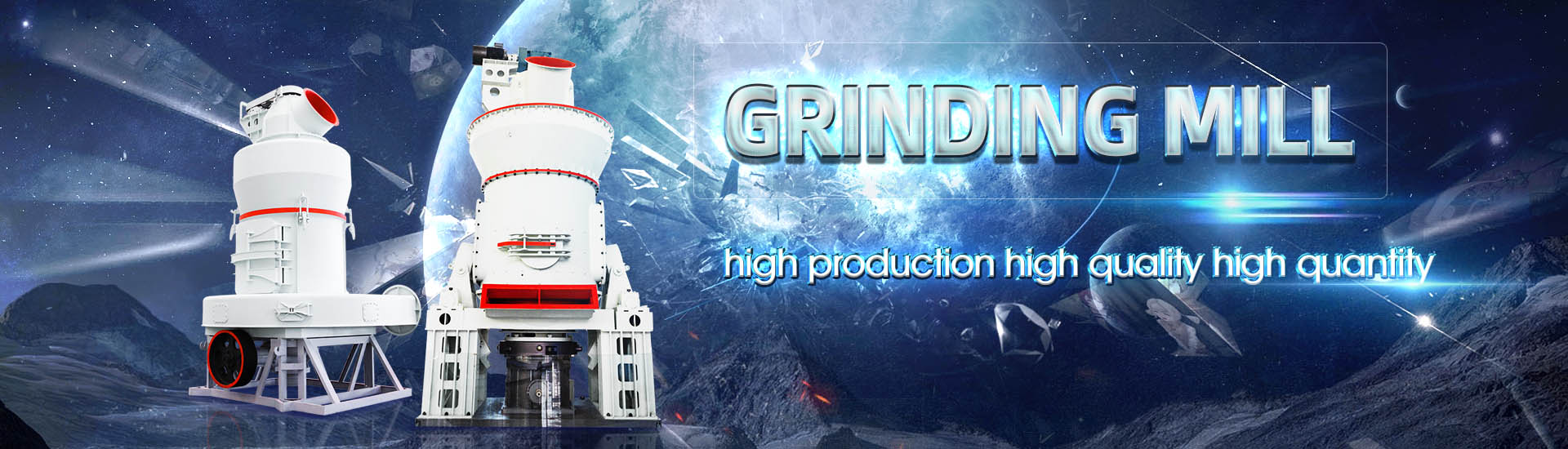
Requirements for the installation of rollertype ore mill
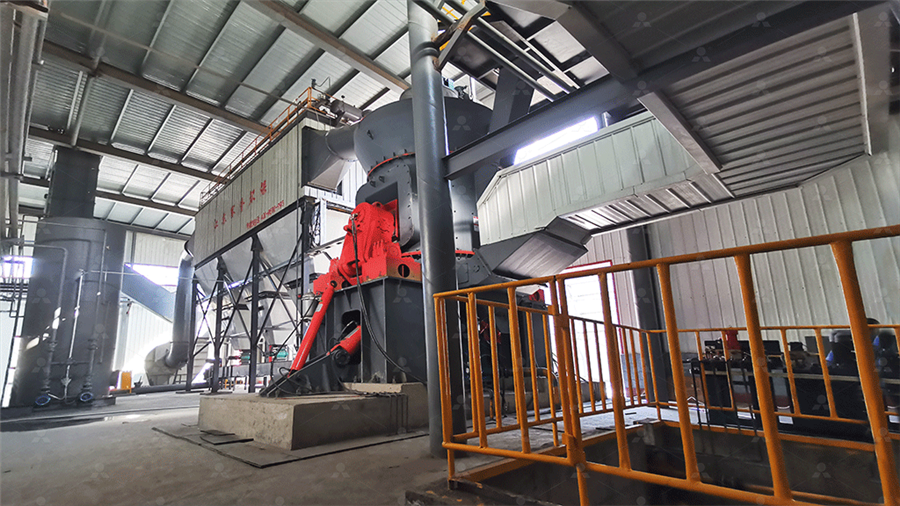
Latest Installations And Developments Of Loesche Vertical Roller
2012年9月1日 Mills (VRM) installations and summarises the main benefits of the dry compressive Loesche grinding technologies in Airflow and OverflowMode Some of these benefits are optimised energy efficiency of the grinding classifying circuits, increased 2001年10月1日 Recent research has shown, that the application of these vertical roller mills in dry grinding of ores and minerals can lead to significantly better recovery rates and higher Loesche vertical roller mills for the comminution of ores and a vertical roller mill (VRM) • Surpasses the classic methods if the controlled process demonstrates significant disturbances • A high degree of attention to the process states is required in order PROCESS OPTIMISATION FOR LOESCHE GRINDING PLANTSVertical roller mills follow the interparticle comminution principie They are known for almost 100 years However mills for high throughput rates havc been developed just in the last 3 decades U Schaefer LOESCHE VERTICAL ROLLER MILLS FOR MINERAL
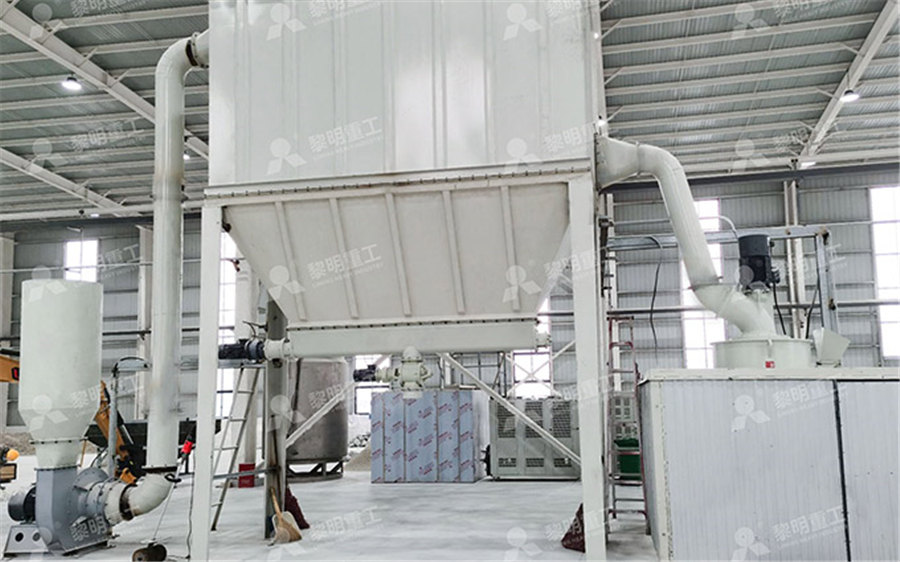
Operational parameters affecting the vertical roller mill
2017年4月1日 Vertical roller mills (VRM) have found applications mostly in cement grinding operations where they were used in raw meal and finish grinding stages and in power plants The Pfeiffer pilot mill used in this study is a semiindustrial vertical roller mill of type MVR with a table diameter of 400 mm The mill can be equipped with different classifiers for specific Vertical Roller Mills used for the comminution of mineral ores2024年1月1日 Roller mill is a type of grinding equipment for crushing materials by pressure between two or more rolling surfaces or between rolling grinding bodies (balls, rollers) and a Roller Mill SpringerLink2017年4月1日 Pilot plant test results with various ores showed that low energy consumption feature of vertical roller mills is applicable to the ore industry Grinding test results for zinc ore Operational parameters affecting the vertical roller mill
.jpg)
Vertical roller mill for raw Application p rocess materials
Vertical roller mills are adopted in 20 cement plants (44 mills) in Japan In the vertical roller mill which is widely used in the raw material grinding process, raw materials input grinding table If HPGRs are operated correctly, ball mills can be downsized and use smaller grinding media, which substantially reduces steel ball consumption, increases the grinding efficiency and lowers operating costs of the milling substantiallyHigh Pressure Grinding Roller (HPGR) DirectIndustryThe flaking roller mill is a versatile yet compact processing device for your flaking line The feeding roll is integrated into the upper section of the roller mill, which saves you up to 60 cm of installation height The custom position of the drive Flaking roller mill type FWS Streckel SchraderWe offer two different types of rolls – steel or cast; multiple roll configurations ranging from 4 to 15 grooves per square inch depending on the particle size you require – and a variety of input and discharge options, including our Elevator RENN Roller Mills High Performance Grain Processing
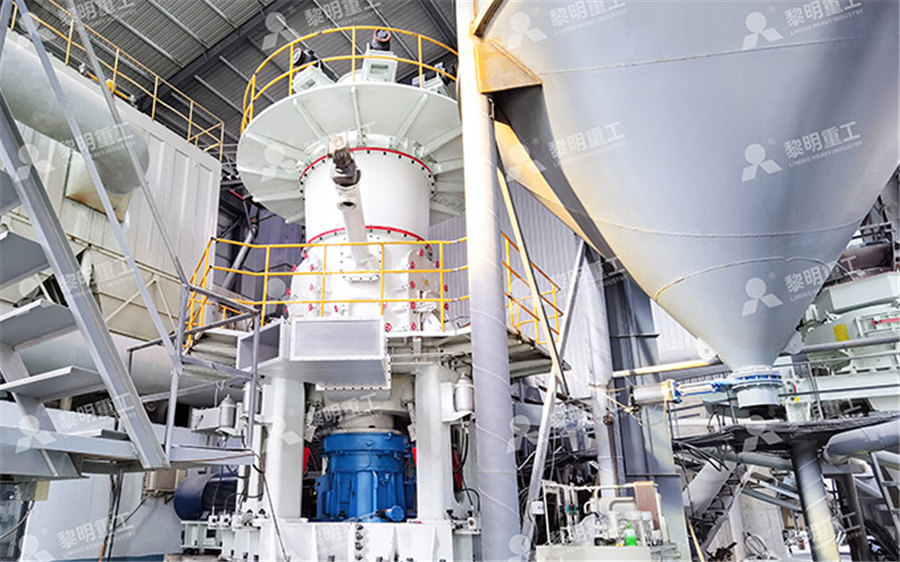
Selection and installation of a vertical roller mill for clinker
1996年4月18日 Roller presses have become well established as a method for increasing the capacity of finish grinding ball mill circuits While other competing technologies exist, notably the vertical impactor, the vertical roller mill, and most recently the Horomill, none of these has become common in North American cement plants This paper describes the first application of a TABLE I Typical 7stand hot finishing mill with 26in OD gear spindles and Ujoint lubrication manhours Coupling Type Lubrications/ year Manhr/ stand Total time, hr* Total cost/ year, $** Gear spindle 48 3 1008 80,640 Ujoint 12 1 84 6720 * 7 stands TABLE II Typical 7stand hot finishing mill with 26in OD gear spindlesDesign and Selection of Universal Joints for Rolling Millssteel mill Nonuniform and heavy shock loads are considered normal operating conditions Many design engineers handle this requirement by increasing the service factor of the gearbox According to the American Gear Manufactures Association (AGMA) selection criteria, reducers can be selected by Service Factor or Load ClassificationRoll Drive Design Considerations for Steel Mill Rolling Operations2014年4月1日 For decades vertical roller mills have been in use in the cement industry for the grinding of cement raw material and coal Since the 1980's this mill type has also been used for combined or (PDF) The latest innovative technology for vertical roller mills
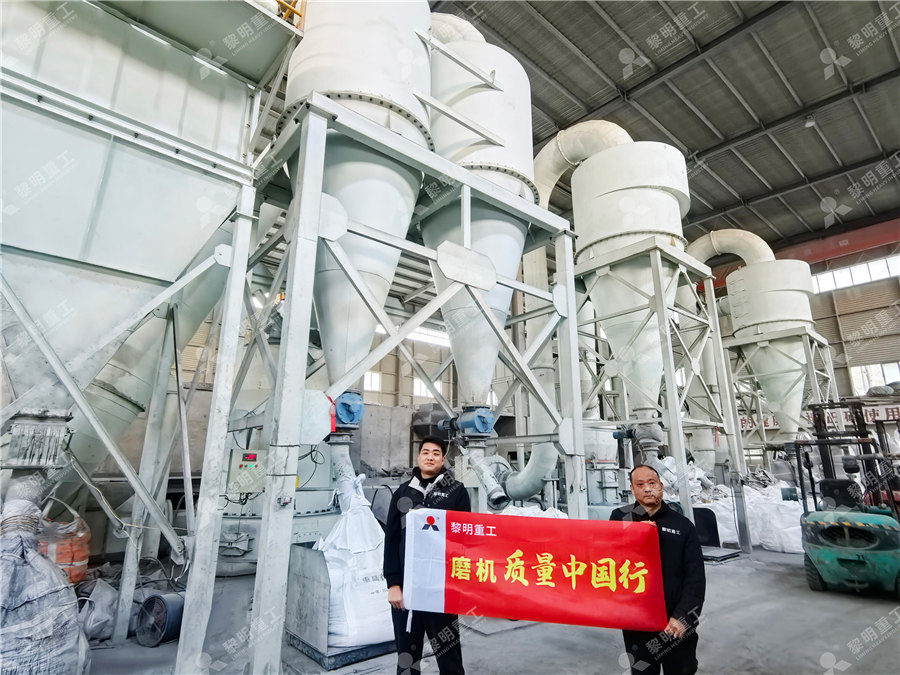
Crushing Plant Design and Layout Considerations 911 Metallurgist
studies, shortterm operations should aim for lower capital cost, while longlife installations should be designed to minimize operating costs and emphasize maintainability “Operating availability is a function of the design of the processing lines and the ease and type of their maintenance” (Shoemaker and Gould, Modern Mill Design, 1980)The appropriate solution for any requirement SDX Economic batch size 2–150 kg The SDX is suitable for small to mediumsized production batches The system is available with centrifugally cast rolls or alternatively with VIVA rolls Motors with a capacity of 75 to 135 kW can be supplied The threeroll mill can be explosionproof and variousSD threeroll mills For topquality requirements Bühler Group2015年4月9日 Typically, this type of mill can produce a product with a fineness of less than 01 mm Testing of materials is needed beforehand for determining the suitability of the ore for processing in an autogenous mill This type of mill has a distinct advantage of accepting coarse input material and supplying a relatively fine ground productGrinding Mills and Their Types – IspatGuruVertical Roller Mill (VRM) Figure 26: Sectional View of a Babcock Wilcox Type Ball Race Mill (Babcock Wilcox, Figure 57: Comparison of Net Specific Energy Requirements between the BRM and Ball Mill 49 Figure 61: Simulated Locked Cycle Grinding Circuit Adaptation of the Ball Race Mill Technology for Wet Comminution
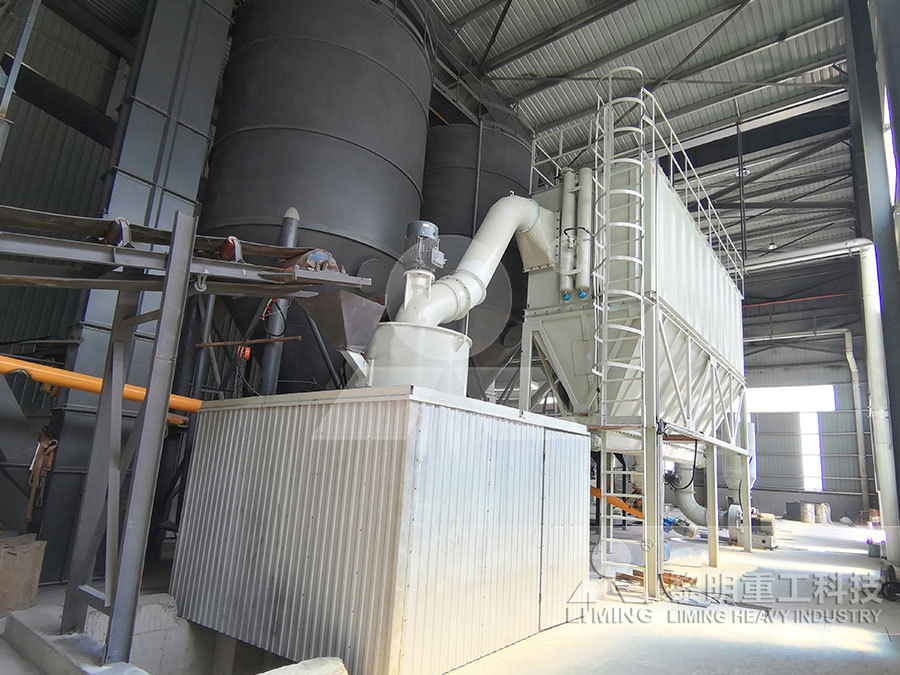
BALL MILLS Ball mill optimisation Holzinger Consulting
type of installation: ball mills, combined in circuit with an air classification system of varying generations and sophistications Depending on the local market situation and product portfolio, VRMs are the most common solution to grind raw materials and cement Roller presses are used mainly in combination with a ball mill for cementRequest PDF On Mar 15, 2015, Mathis Reichert and others published Research of iron ore grinding in a verticalrollermill Find, read and cite all the research you need on ResearchGateResearch of iron ore grinding in a verticalrollermillHeart of the RENN Roller Mill For the last 60 years the heart of the RENN Roller Mill has been its precisionmachined 16” diameter rolls The large diameter provides more rolling area per revolution compared to other brands of roller mills with their smaller diameter rolls RENN Roller Mills save you timeRoller Mill2013年3月1日 This study investigated a mathematical model for an industrialscale vertical roller mill(VRM) at the Ilam Cement Plant in Iran The model was calibrated using the initial survey's data, and the Cements ground in the vertical roller mill fulfil the quality
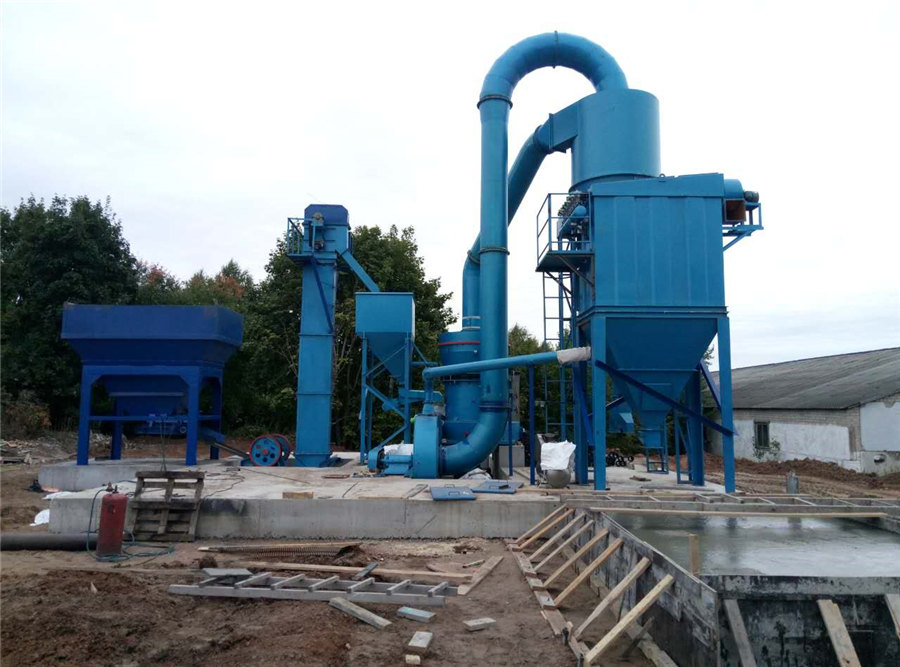
COMPARISON OF ROLLING MILL DRIVE SHAFT CONCEPTS
requirements, ie rising productivity, product quality, high machine lifetime and energy efficiency necessitates the selection of an optimal drive concept for the respective type of rolling mill with a special focus on LCC (also referred to as TotalCostofOwnership / TCO) This paper elaborates on the two most common types of2017年9月11日 In this study, an extensive sampling study was carried out at vertical roller mill of ESCH Cement Plant in Luxemburg Samples were collected from mill inside and around the circuit to evaluate the (PDF) Performance Evaluation of Vertical Roller Mill inroller mill tests of your material in the manufacturer’s test facility with various roll corrugation styles and under conditions that duplicate your operating environment Figure 1 Particle size distributions: Roller mill versus other grinding methods Other grinding methods Roller mill Overs Target particle size Fines Figure 2Roller mills: Precisely reducing particle size with greater efficiency2007年1月1日 the various areas of a flour mill production facility are likely to be Type I, or II construction with occupancy classifications that could include: F1, H2, B, or S1 Type I construction allows forDesign Considerations for the Construction and Operation of
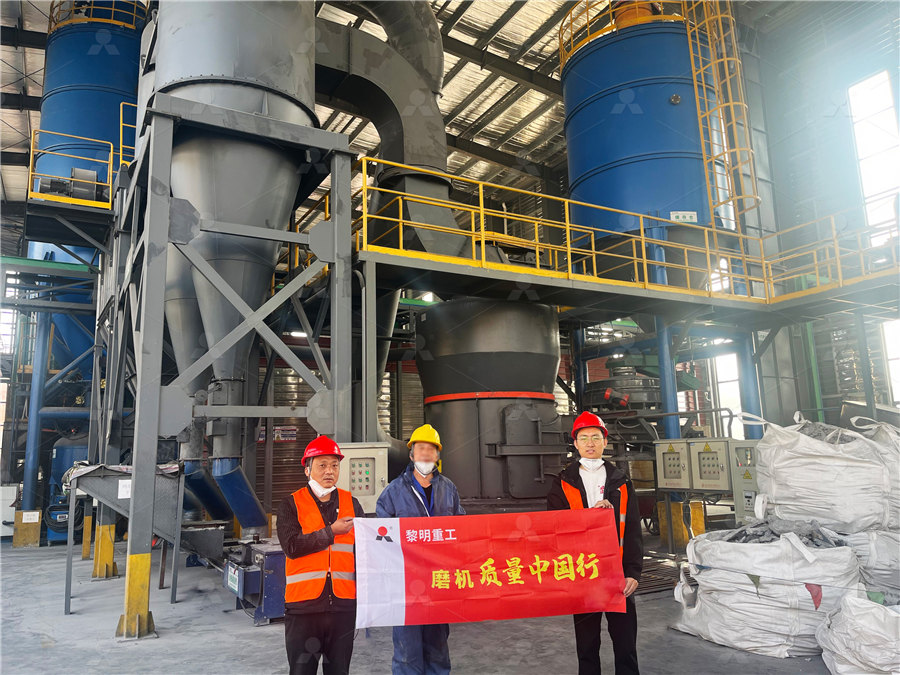
VF2 Preinstall Guide Haas Automation Inc
Automation Accessories Shop Support Mill Toolholding Mill Cutting Tools Boring Systems Mill Workholding Lathe Toolholding Lathe Cutting Tools Lathe Workholding Package Kits ER Collets Chucks Holemaking Threading Broaching Tombstones Kits Manual Chucks For Milling Deburring Abrasives Tool Presetter Heat Shrinkers Storage Handling Machine Mill linings, Weir Rubber Engineering, Salt Lake City, UT 84126, United States of America ABSTRACT Dramatic shortcomings of mill liner designs, especially of large SAG mills, such as rapid failure and even mill shell damage arising from The Selection and Design of Mill Liners 911 MetallurgistRod Mill The rod mill is another type of grinding mill used in the copper ore mining process This machine uses steel rods as the grinding media instead of balls, which are commonly used in ball mills The rods grind the ore by Understanding the SAG Mill in Copper Ore Mining CLUM vertical roller mill is a new type of milling equipment that includes grinding, grading, conveying, secondary powder selection, and finished product packaging It is a largecapacity ultrafine grinding and separation equipment developed Vertical Roller Mill SBM Ultrafine Powder Technology
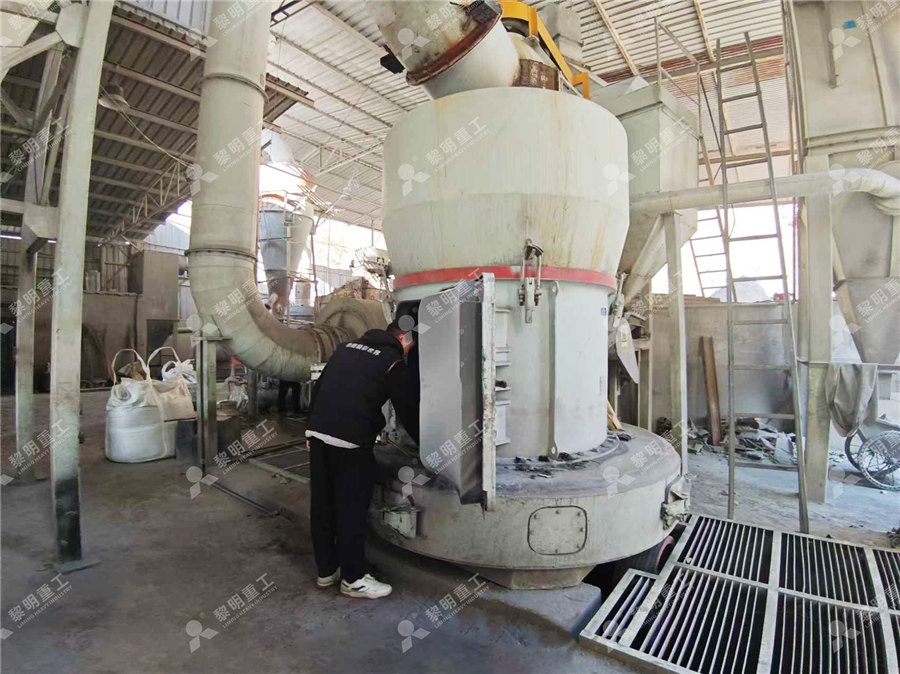
An investigation of performance characteristics and
2020年8月12日 This study shows the performance of a currently running vertical roller coal mill (VRM) in an existing coalfired power plant In a power plant, the coal mill is the critical equipment, whose 2020年1月3日 The stateoftheart of both technology and operational practice of a hot rolling mill are discussed The focus is first on the control of entry temperature in the finish mill2020 Technology and Operation of a Hot Rolling Mill2023年12月4日 When higher rolling resistance is applied due to particle shape complexity at less mill speed, more vertical force is exerted on the roller, and the roller speed is insensitive to rolling resistance This study provides the basis for further experimental investigations on industrialscale VRM and supports the design optimization of the VRMNumerical Investigation of Vertical Roller Mill Operation Using 2022年11月30日 Crackers – A mill used to crack grain or other types of friable materials; Flakers – Mills used to flake grains or other materials; Grinders (Rollers mill grinders) – Roller mills that are used to grind in a feed mill Crimpers – Roller mills that crimp grains; Crimper – Crackers a roller mill that cracks and at the same time crimp grainsRoller Mill: Components, Designs, Uses, Advantages and Disavan
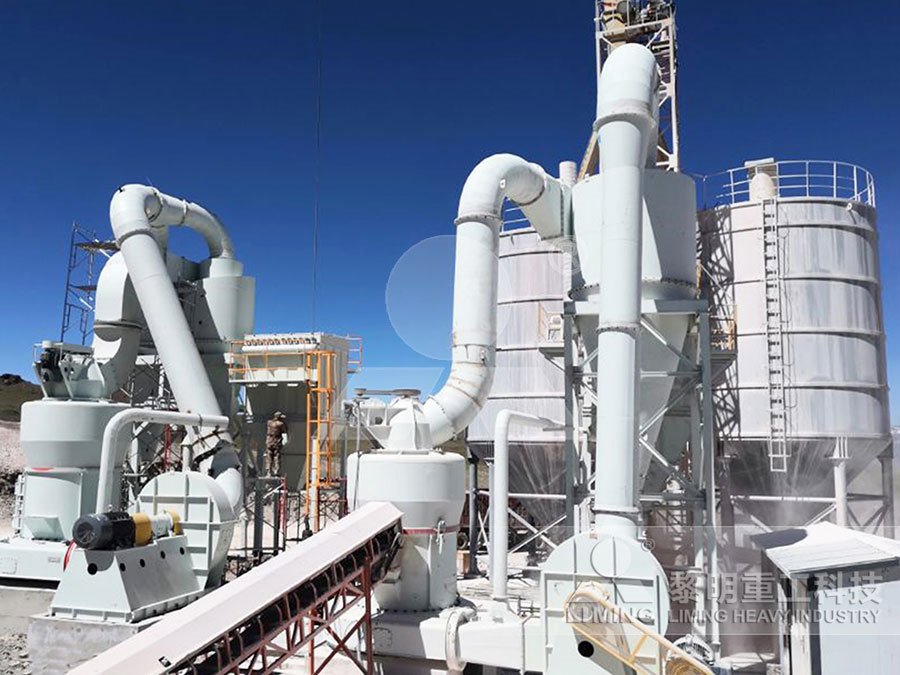
The World of Steel Mills: Engineering, Maintenance, and More
2023年9月16日 Installation and Upgrades As technology advances, steel mills must adapt to remain competitive Typically, new equipment installation, and upgrades to existing systems, are essential to enhance efficiency, reduce energy consumption, and comply with evolving industry standardsThese projects demand careful planning, precise execution, and a thorough Mill control system monitoring picture contains raw ingredients system, roller mill system, tran sportation and storage system of raw material the running state ofthe equipment and operation pa Design and Realization Of Roller Mill Control Systemlike with Bühler’s Mill E3 This futureoriented milling solution break new ground at all levels – from machines, to processes, to the complete plant layout The result sets new benchmarks with respect to efficiency – with fast installation times, lower energy consumption, and less space requirements Preserving the good, revolutionizingFor every requirement the best milling solution Bühler Group2023年10月17日 Factors for choosing a suitable ore powder grinding mill 1 Raw material characteristics: Different raw materials have different hardness, humidity and grinding and crushing properties, and the corresponding ore powder grinding mill needs to be selected to meet the processing requirements 2 Production capacity: Determine the required processing How to choose a suitable ore powder grinding mill?
.jpg)
Latest Installations And Developments Of Loesche Vertical Roller
2012年9月1日 The paper is giving an overview about successful operating Loesche Vertical ? Roller ? Mills (VRM) installations and summarises the main benefits of the dry compressive Loesche grinding technologies in Airflow and OverflowMode Some of these benefits are optimised energy efficiency of the grinding classifying circuits, increased mineral recoveries 2017年7月17日 A threeroll mill is used mostly for dispersion, but does some grinding as well It uses three rollers of different speeds and directions to cause the sheer force between them to disperse and grind particles The threeroll Threeroll mill selection tips Processing Magazine2017年2月13日 In all ore dressing and milling Operations, including flotation, cyanidation, gravity concentration, and amalgamation, the Working Principle is to crush and grind, often with rod mill or ball mill, the ore in order to liberate the Ball Mills 911Metallurgistmill installations The composition of the dust will depend upon the materials being processed Under the worst conditions, the dust can be corrosive or abrasive A geardriven pellet mill has a gearbox that is sealed to prevent any dust from entering, and is also usually fitted with a lubrication system thatPellet mill design Feed Strategy

The QUADROPOL roller mill
Roller diameter of 23 m QUADROPOL® roller during manufacture Installation of roller unit Principle of functioning The QUADROPOL® roller mill integrates three work operations in a single unit: drying, grinding and separating The ground material spills over the grinding table rim and is entrainedanddriedbythe stream of hot gas emerging162 PostInstallation Running Test There are various forms of each type of bearing, each having its own particular Rolling bearing Sliding bearing Generally has inner and outer rings, in between which there are ball or roller rolling elements which support a rotating load by rolling Rotating load is supported by the surface, and makes ROLLING BEARINGS HANDBOOK NTN AmericasFind your ore mill easily amongst the 42 products from the leading brands (Fritsch GmbH, Retsch, Eriez, The POITTEMILL pendulum roller mill is a vertical mill that works by compressing the material bed The overflow type ball mill is a new type of ball mill equipment with simple structure and selfflow discharge of oreOre mill, Ore grinding mill All industrial manufacturers2019年4月16日 This paper brings together two separate studies, in which the vertical roller mill was used to grind two different precious metal ores, an epithermal gold deposit hosted in quartz vein from Turkey (PDF) LEARNING FROM OTHER INDUSTRIES; WHY THE VRM
.jpg)
OK Mill: The 3: Mechanical optimized and 31: Grinding concept
The OK mill is the FLSmidth vertical roller mill offered for finish grinding It is highly rated by our customers as an efficient, reliable and versatile finish grinder Efficiency: Low power consumption when compared to ball mill installations and to the other vertical roller mills on the market Reliability: The run factor is very high;Features of the Rolling Mill Guides Our mill guide has excellent features such as corrosive resistance, unique design, and simple maintenance Our roller entry guide is made in sliding type plus rolling type It is provided with heavy taper roller bearings for different sections We provide the best quality of mill guides at a lower priceRolling Mill Guides Roller Spares Equipment and Guide