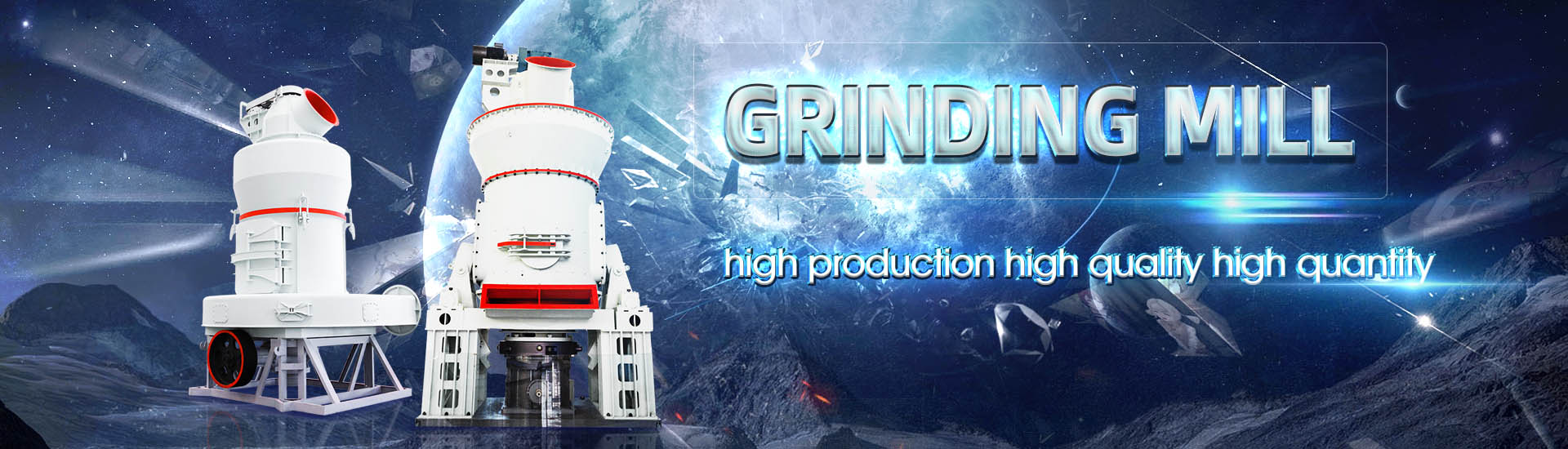
Ball mill output improvement
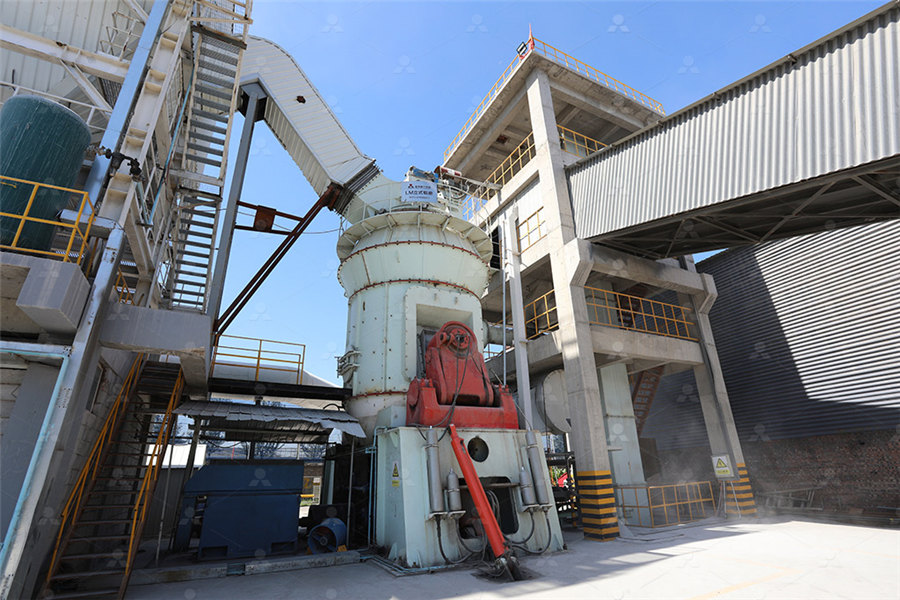
How to Improve Ball Mill Performance 911Metallurgist
2017年10月25日 Ball Mill Breakage Efficiency Consider a ball mill circuit processing material of a given feed size and at a given throughput rate to a target product size, the latter which once again distinguishes the “fines” from the “coarse” material2024年8月14日 Improving the output of ball mills can not only improve the economic benefits of mining companies, but also optimize production processes and reduce resource waste To this How to Improve Ball Mill Output? Xinhai2021年2月19日 Optimization results confirmed that the balls to powder weight ratio were the most influential process parameter The optimum process parameters setting concluded that Comparative Study on Improving the Ball Mill Process Parameters the ball mill had an average production rate of 190tph with a specific electrical energy consumption of 355kWh/t Its operational issues included: • oversized limestone • wornout BALL MILLS Ball mill optimisation Holzinger Consulting
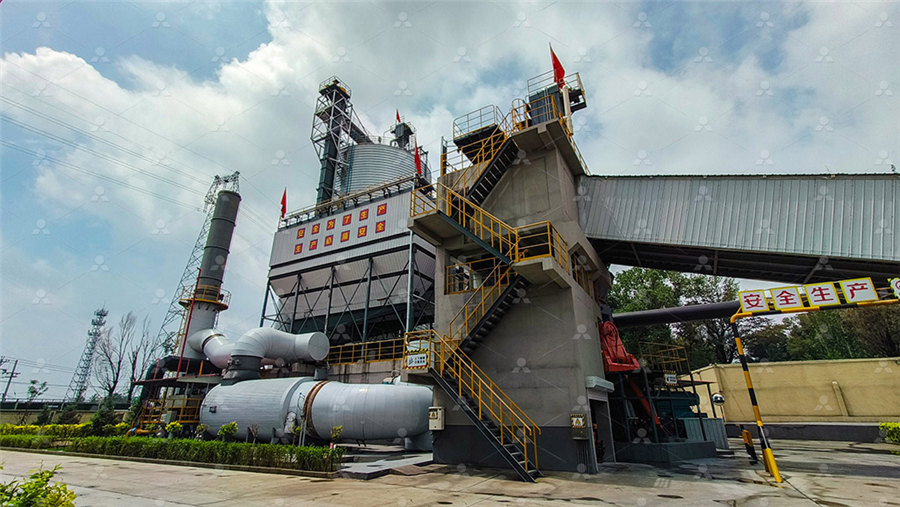
Ball Mill Success: A StepbyStep Guide to Choosing
2024年8月8日 In the intricate dance of ball milling, where raw materials are transformed into finely milled particles, the choice of grinding media emerges as a pivotal performance lever This seemingly minor selection can dramatically Ball mill mill internals o Ball mill (L/D, speed, drives reducers, etc) o Ventilation o Liners o Diaphragms o Media composition fill ratio Ball mill typically accounts for 85% of the total energy consumed in the grinding plant Improvements in New Existing Cement Grinding 2024年4月28日 Critical Speed: Critical speed is the hypothetical speed at which the centrifugal force is equal to the gravitational force, and the grinding media starts sticking to the inner shell of the equipment instead of falling What is a Ball Mill Explained: InDepth Guide JXSCBall mills are used for the stage of grinding ore in mining operations with the alignment of grinding balls Controlling the operating conditions of ball mills is a key factor for optimal mill operation and high mill productivity The main factors affecting the efficiency of a ball mill are ball loading, drum rotation, lining wearImprovement of methods to ensure energy efficiency of ball mills
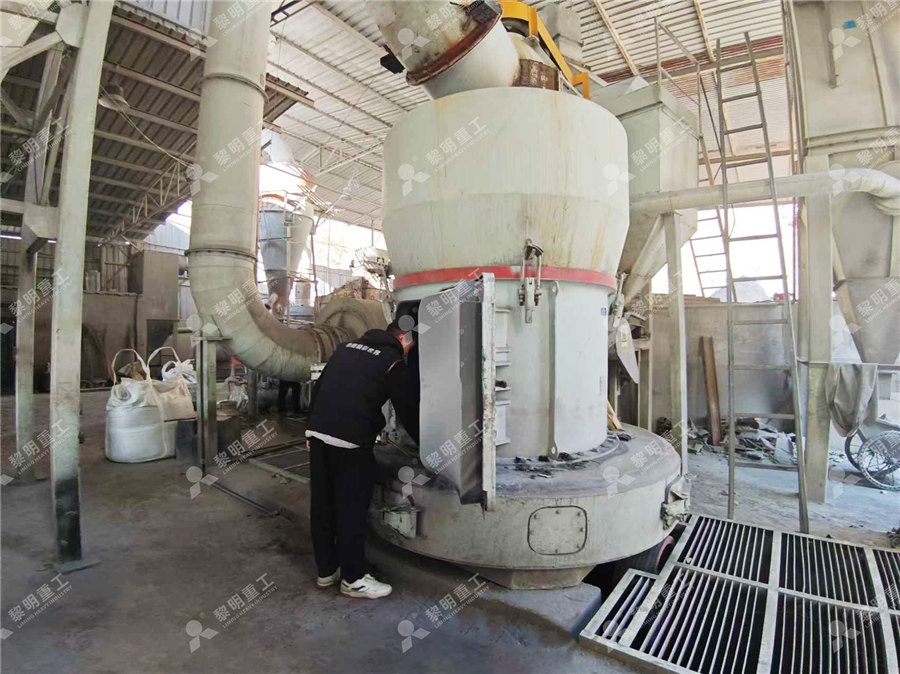
Improvement of methods to ensure energy efficiency of ball mills
Ball mills are used for the stage of grinding ore in mining operations with the alignment of grinding balls Controlling the operating conditions of ball mills is a key factor for optimal mill operation and high mill productivity The main factors affecting the efficiency of a ball mill are ball loading, drum rotation, lining wearThe characteristic tumbling motion of these mills has given them the name ‘tumbling mills’, which include the ball mill, tube mill and rod mill Ball mills are horizontal rotating cylindrical or conical steel chambers, approximately one third to half full of steel, alloy steel or iron balls, like that shown in Fig 410 A–C , or flint stonesBall Mill an overview ScienceDirect Topics2002年11月1日 The effect of ball load composition, by varying the grinding media size distribution (eg alternatively by mixing four groups of 195, 38 mm; 195, 50 mm; 38, 50 mm and 195, 38, 50 mm), on the The energy efficiency of ball milling in comminutionBall Mill DesignOptimization Of Feeding Device Design of BallnormalMill Feeding Method Whether the design of the feeding device is reasonable or not, determines the operation of the ball mill feeding system, which directly affects the actual output of the ball mill There are generally two types of feeds designed for traditional ball mills: 1Ball Mill DesignOptimization Of Feeding Device
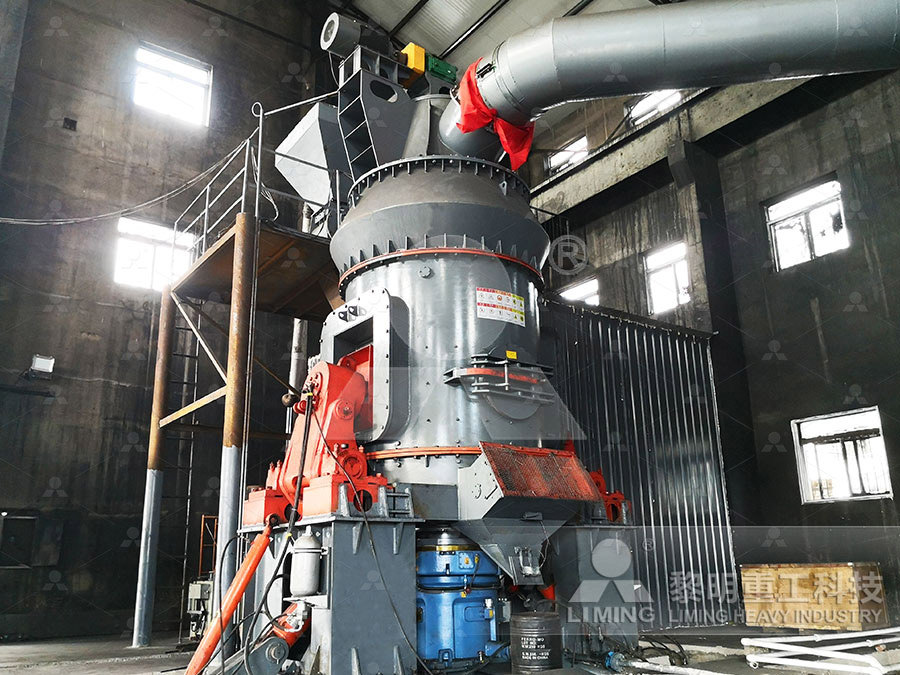
Effect of ball and feed particle size distribution on the milling
2018年2月1日 In another study to investigate ball size distribution on ball mill efficiency by Hlabangana et al [50] using the attainable region technique on a silica ore by dry milling, a threeball mix of Introducing retainer ring for the improvement of mill performance Location: Southeast Asia Client: Leading cement producer in the region Result: 5 to 16 % increase in output with two main products along with achieving required blaine generation Client had complaint of poor blaine generation after converting their mill into monochamber designTechnical support to the client Introducing retainer ring for the 2023年12月28日 Many factors affect the output and quality of ball mills, which can generally be divided into three categories: process, mechanical, and management From the perspective of production technology, the influencing Factors Affect The Output and Quality of Ball Mills In a ball mill circuit, the "output" can be defined as the production rate of fines of the circuit As for any output, ball mill circuit output is a function of both its inputs and efficiencies There are two "inputs" to a ball mill circuit: the ore fed to the circuit and the power delivered by the grinding millMODULE #5: FUNCTIONAL PERFOMANCE OF BALL MILLING
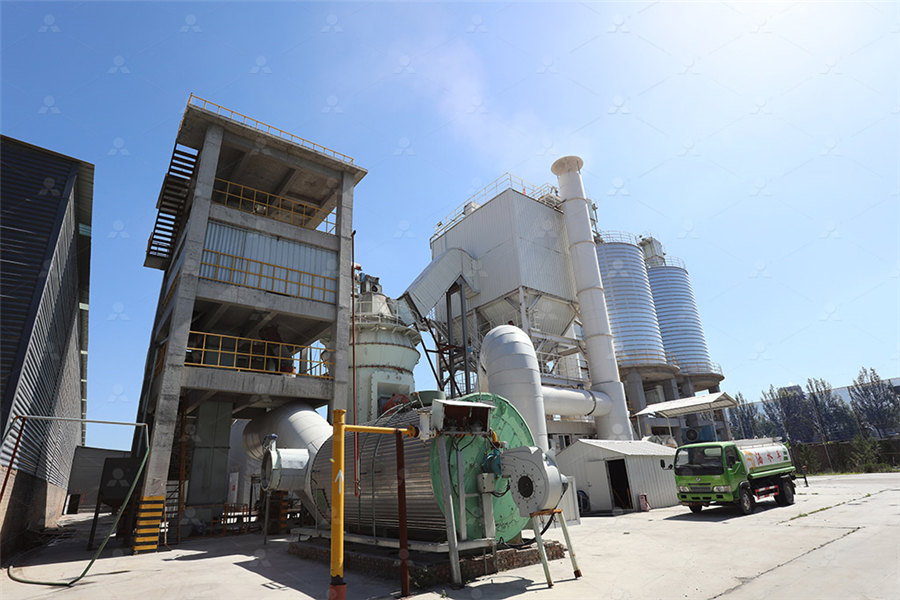
IMPROVEMENT IN RELIABILITY AND EFFICIENCY IN BALL TUBE MILLS
pulverization ball mill used in coal power plant There are total nine numbers BBD mills installed in three Units of Panipat Thermal Power Station Each Unit is having three mills Ball tube mills model BBD4772 are installed in Unit7 8 with coal crushing capacity as 759 Tons/Hour for design coal at ball load of 80 tons2013年7月15日 PDF The ball mill in closed circuit with hydrocyclones is an industry standard, The big improvement in fine screening is achieved by high frequency screens that utilise different (PDF) Energy Efficient Ball Mill Circuit – Equipment Sizing 2024年8月14日 In modern mining production, ball mill is a kind of key grinding equipment, and their performance directly affects the efficiency and output of ore processing Improving the output of ball mills can not only improve the economic benefits of mining companies, but also optimize production processes and reduce resource waste To this end, it is particularly important to How to Improve Ball Mill Output? Xinhai2021年2月19日 The ball mill process parameters discussed in this study are ball to powder weight ratio, ball mill working capacity and ball mill speed As Taguchi array, also known as orthogonal array design, adds a new dimension to conventional experimental design, therefore, Orthogonal array (L9) was carefully chosen for experimental design to understand the effects Comparative Study on Improving the Ball Mill Process Parameters
.jpg)
(PDF) Grinding Media in Ball MillsA Review ResearchGate
2023年4月23日 One of the most used tumbling mills is the ball mill improvement in the pulp chemistry and a reduction of reagent dosage rates by 25% The presence of o xygen freed in Ball mills are furthermore characterized by significant differences in the sizes of available grinding jars Retsch offers mills with jar capacities from 15 ml up to 150 l and balls are available from 01 mm to 40 mm, see Figure 2 A third and very important characteristic of a ball mill, Ball Mills Suitable for every application RetschOperation and Elements of a ClosedCircuit Ball Mill System Cement ball mills typically have two grinding chambers The first chamber is filled with larger diameter grinding media andlined with lifting liners The first chamber coarsegrinds the feed material and prepares it for the second chamber The second chamber is the fine grinding OPTIMIZATION OF CEMENT GRINDING OPERATION IN BALL MILLSA ball mill is a type of grinder filled with grinding balls, used to grind or blend materials for use in mineral dressing processes, paints, pyrotechnics, ceramics, and selective laser sintering It works on the principle of impact and attrition: size reduction is done by impact as the balls drop from near the top of the shellBall mill Wikipedia
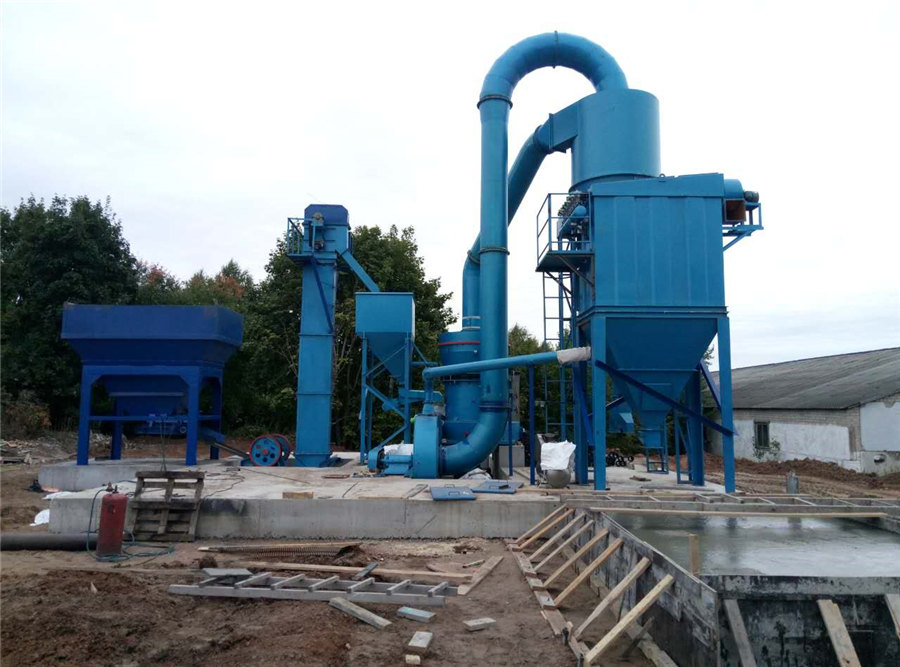
Ball Mill (Ball Mills Explained) saVRee saVRee
Ball Mill Introduction There are three main stages to mineral processing in the mining industryThese are: Comminution (crushing and grinding); Beneficiation (separation and concentration); Smelting and refining; Ball mills are 2023年10月16日 Full MinetoMill Optimization Continuous Improvement of Lundin Mining's SAG and ball mills, and cyclones), liner design, and These key fragmentation output parameters and the Full MinetoMill Optimization Continuous 2023年2月15日 High temperature of the ball mill will affact the efficiency 3 For every 1% increase in moisture, the output of the ball mill will be reduced by 8% 10% 4 when the moisture is greater than 5%, the ball mill will be unable to 17 Signs of Problems with Ball Mills: Quickly Ball MillSlicer – Ball Mill Fill Level Measurement The main unit requires AC power (100–220 VAC, 50/60 Hz) and has a 420mA output that corresponds to each of the fill vectors for Longterm value – Investment in the Ball Miscan offers additional data and insights for ongoing mill optimisation and continuous improvement Related Ball MillSlicer Molycop
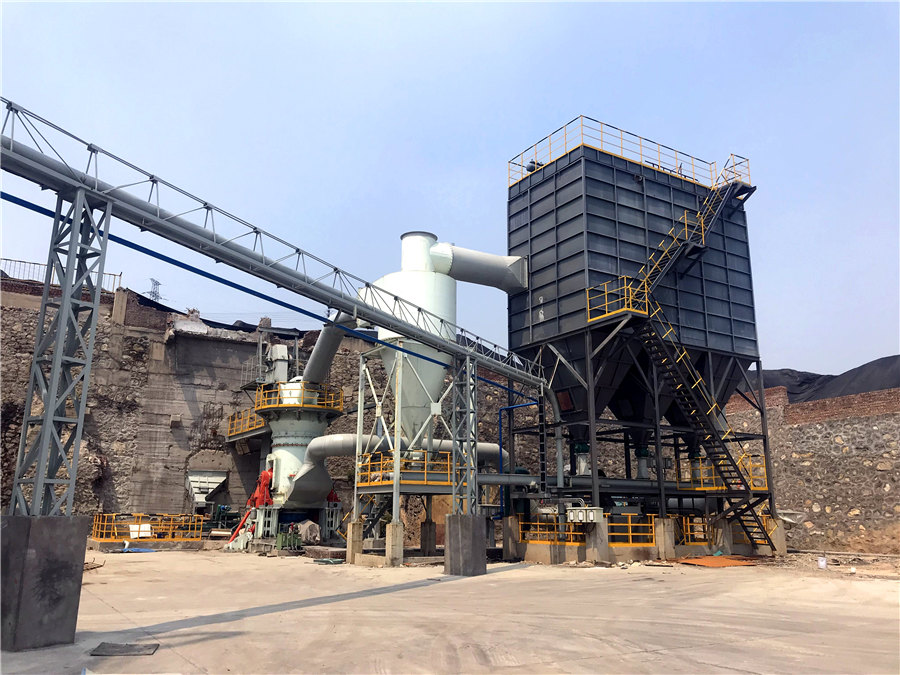
Improving the efficiency of the coal grinding process in ball drum
2022年2月24日 Curves of mill productivity, power consumed, specific surface of coal dust in terms of the relative rotational speed of the ball drum mill Composition of the balls loading the mill with a standard 2013年4月1日 The ball millhydrocyclone circuit and the ball millscreen circuit were sampled in order to measure and compare the performance of the circuits The ball mills are different in design Therefore, simulation studies were carried out to eliminate the differences in factors affecting the performance of the circuits such as milling conditionsClosed circuit ball mill – Basics revisited ScienceDirectmany problems in drum ball millThe pulverizer has insufficient output and longterm low load operation[1]The power consumption of pulverizing is highThe phenomenon of powder leakage isOptimization and transformation of 300MV units steel ball coal mill 2013年8月3日 In Grinding, selecting (calculate) the correct or optimum ball size that allows for the best and optimum/ideal or target grind size to be achieved by your ball mill is an important thing for a Mineral Processing Engineer AKA Metallurgist to do Often, the ball used in ball mills is oversize “just in case” Well, this safety factor can cost you much in recovery and/or mill liner Calculate and Select Ball Mill Ball Size for Optimum Grinding
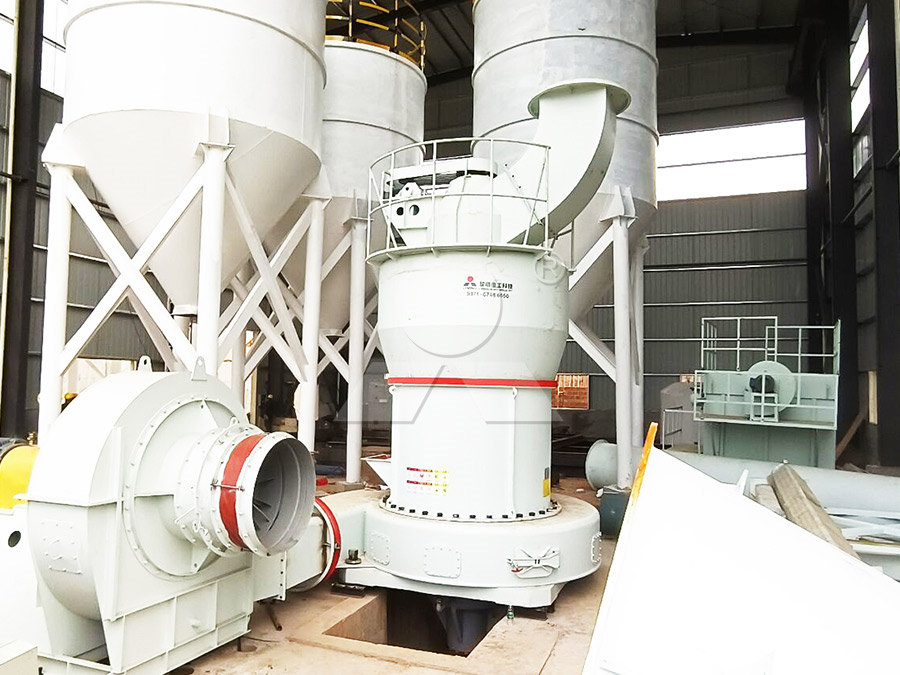
The Ultimate Guide to Ball Mills Miningpedia
2019年8月14日 Ball mill is a common grinding equipment in concentrator : hm@gmail Toggle navigation Home About us; Mineral process Mineral process and then affect the ball mill output In the production of the processing plant, the more common steel ball ratio of ball mill is twostage ratio and multistage ratio2021年1月1日 Comchambered with the design of Φ 35 × 13m threechamber ball mill, the design process of ball mill is described in detail General arrangement of the mill Filling rate of grinding body in each (PDF) Design of Threechamber Ball Mill ResearchGate2023年8月21日 In this study, the Bond (1961 ) approach and the Morrell (1996) approach proposed forthe prediction of the power of wet ball mills, autogenous mills and semiautogenous mills were testedImprovement of methods to ensure energy efficiency of ball mills Our smallscale miner’s Ball Mills use horizontal rotating cylinders that contain the grinding media and the particles to be broken Present day MARCYS embody important improvement – including a NEW Open End Ball Mill which creates 05 TO 15 TPH SMALL SCALE MINER’S BALL MILL
.jpg)
Model Predictive Control of Duplex Inlet and Outlet Ball Mill
2019年3月7日 The directfired system with duplex inlet and outlet ball mill has strong hysteresis and nonlinearity has the defects of easy to fall into local minimum and nonadjustable parameters Firstly, a LSSVM model of mill output is established and is verified by simulation in this paper Improvement of PSOparameters and their interaction on the output response (Soleymani Yazdi and Khorram, 2010) In this work, the grinding media's static and dynamic voidage inside the ball mills were studied to improve the accuracy of Hogg and Fuerstenau's model in Improvement of the accuracy of Hogg and Fuerstenau's model in 2012年6月1日 PDF The paper presents an overview of the current methodology and practice in modeling and control of the grinding process in industrial ball mills Find, read and cite all the research you Grinding in Ball Mills: Modeling and Process ControlThe mill performance is evaluated and recommendations are formulated based on the past history of the mill operations, inspections, process measurements, feed/product characteristics and grinding performance, in order to improve mill output and reduction in power consumptions in the ball mill system DIAGNOSTIC STUDY History of mill operationsPROCESS DIAGNOSTIC STUDIES FOR CEMENT MILL
.jpg)
STEEL MILLING BALLS FOR BALL MILLS Energosteel Grinding Media Ball
31 The ball mill The device with a rotating drum filled by grinding balls and shredded material for materials crushing 32 The grinding balls Products with ball form for material crushing in ball mills by abrasion, impact and crushing 33 The conditional ball diameter Ball diameter rounded to standard values 34 The nominal ball diameterOutput: 10 t/h 20 t/h Ball mill is common used grinding plant in the industry, and it is key equipment used for milling after materials are crushed Your suggestions for improvement: Filters: find the right products faster Terminology: use the most common industry termsBall mill, Ball grinding mill All industrial manufacturers2023年10月1日 The inner diameter and the length are 0305 m, and the ball load is 194% of mill volume (equaling a total weight of 20125 kg) The mill has a frequency inverter with 220 V singlephase The mill design, operating conditions, and ball size distribution were based on Bond’s (1961 a,b) work index methodology and are shown in Table 2Estimation methodology for Bond ball mill work index experiment output Analysis of the efficiency of the grinding process in closed circuit ball mills Valery I Telichenko1, Rashid R Sharapov1*, Svetlana YLozovaya2 and Vladimir ISkel1 1Moscow State University of Civil Engineering, Moscow, Russia 2Belgorod State Technological University named after VG Shukhov, Belgorod, Russia Abstract Ball mills for fine grinding cement clinker and additives areAnalysis of the efficiency of the process in closed circuit ball mills