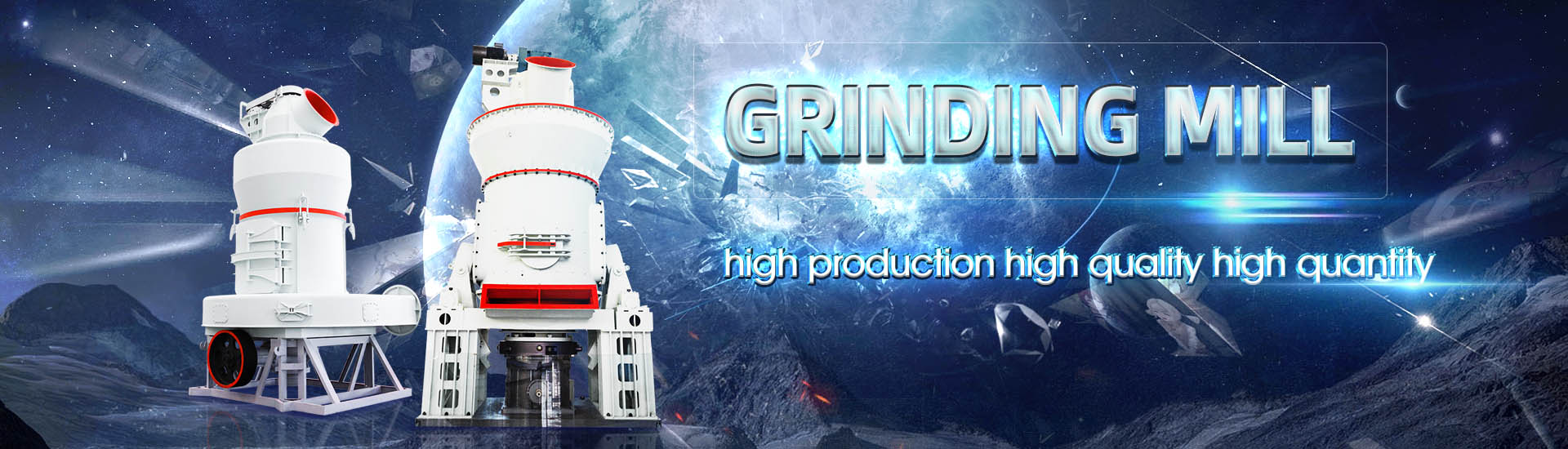
What does a cement plant with a daily output of 5,000 tons use
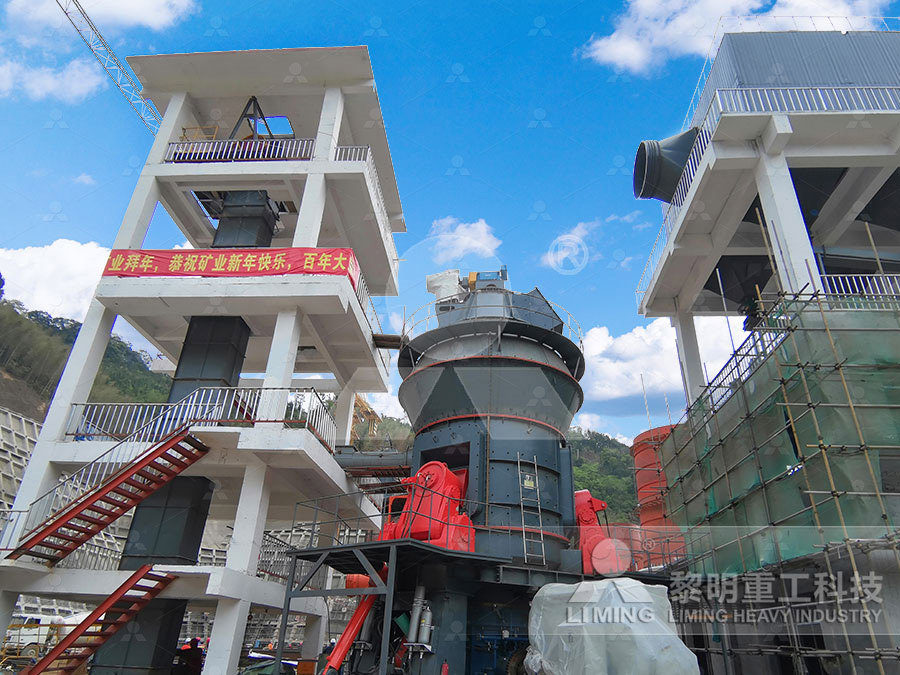
What Are the Major Operating Costs of Cement Plants?
2 天之前 Discover the top operating costs of a cement manufacturing plant Get insights on optimizing expenses and improving profitability $50/ton: 5,000: $250,000: Natural Gas: $30/MWh: including reduced productivity and lower quality output, which can negatively The Cement Plant Operations Handbook is a concise, practical guide to cement manufacturing and is the standard reference used by plant operations personnel worldwide Providing a The Cement Plant Operations Handbook International Cement Tongli provides a full set of EPC solutions for cement production lines with daily output of 800 tons to 5,000 tons5000 TPD Cement Production Line CEMENTL2022年10月1日 In this paper, a mass and thermal balance experiment of a 5000 t/d cement plant in China is performed to obtain the operating parameters and energy distribution The Energy and thermodynamic analysis of a typical cement
.jpg)
Cement kiln Wikipedia
Over a billion tonnes of cement are made per year, and cement kilns are the heart of this production process: their capacity usually defines the capacity of the cement plant As the main energyconsuming and greenhousegas–emitting 2022年9月1日 A standard cement plant with a daily output of around 3000 tons of clinker requires around 2500–4000 kJ/kg of clinker of energy [3] As a result, different energy Evaluating the thermodynamic efficiency of the cement grate Setting up a cement plant involves numerous components and stages, each contributing significantly to the overall cost This detailed guide will break down the costs associated with each component and stage of a cement factory, The Comprehensive Guide to Cement Plant Costs: An 2020年5月14日 Daily output requirement Investors have different requirements for the daily output of the cement factory, so we can find a largecapacity cement plant and mini cement plant in the real case, and the investment capital will How Much Does It Cost To Start A Cement Plant?
.jpg)
Cement Plant an overview ScienceDirect Topics
68 行 In the present context, the majority of new plants are large plants with clinkering capacities of 5000 tpd (single line) and annual capacities of + 25 million tons When designing layouts 2024年11月22日 Production Efficiency Rate Definition The Production Efficiency Rate is a key performance indicator that measures the effectiveness of a cement manufacturing plant in utilizing its resources to produce finished What to Achieve with Cement Manufacturing2022年9月1日 Cement production is one of the highly energyintensive sectors and uses about 5 % of global industrial energy with an estimated 30–40 % share of production costs [1], [2]A standard cement plant with a daily output of around 3000 tons of clinker requires around 2500–4000 kJ/kg of clinker of energy [3]As a result, different energy efficiency strategies have Evaluating the thermodynamic efficiency of the cement grate 2014年5月10日 Output also enables to calculate time required to complete a job The following example illustrates this Find the working hour required to complete a concrete slab 30 m * 50 m 8 020 m size using 200 T mixerHOW TO CALCULATE OUTPUT OF A CONCRETE
.jpg)
Mastering Process Control Instrumentation in Cement Plants: A
2023年9月5日 Gas analyzers used in the kiln and the stack need to be capable of measuring a wide range of gases, including CO2, NOx, SOx, and CO They also need to be resistant to high temperatures and aggressive gases Importance of Cement Plant Monitoring for Efficient Production Cement plant monitoring is essential for efficient productionThe hammer crusher with feed rollers (FLS) is a special form of construction to avoid complicated, multistage crushing, a hammer has been developed, which does not require preceding primary crushing This crusher reduces rock lumps from 2 m size down 25 mm The crusher uses a single hammer rotor with peripheral speed of about 40 meters per Everything you need to know about Crushers in Cement industryFigure 321 Multistage cyclone preheaters and precalciners in a cement plant Besides enabling a high output of the kiln system, In the current practice, onestring preheaters are usually proposed for a production rate of up to 50006000 ton/dayEverything you need to know about Preheaters and PrecalcinersHow does the above affect kiln operations at a cement plant? Composition of the raw material mix in regard to percentage of CaCO3 has a substantial effect on the calcining zone If the raw mix design is higher in CaCO3, it will require more energy for calciningEverything you need to know about Kiln System Operations in Cement
.jpg)
Cement manufacturing components of a cement plant Understanding Cement
Cement manufacturing: components of a cement plant This page and the linked pages below summarize the cement manufacturing process from the perspective of the individual components of a cement plant the kiln, the cement mill etc For information on materials, including reactions in the kiln, see the ' Clinker ' pages2020年6月24日 Therefore, the integration of the utilization and recovery of waste heat is an essential and effective way for the reduction of the energy that is required to capture CO 2 []Thus, the heat recovery from the waste heat can improve the energy utilization efficiency in cement industries []This phenomenon does not only play a vital role in the conservation of energy, but Thermal energy consumption and its conservation for a cement 2020年2月1日 Nowadays, ball mills are used widely in cement plants to grind clinker and gypsum to produce cement In this work, the energy and exergy analyses of a cement ball mill (CBM) were performed and Energy and exergy analyses for a cement ball mill of a new 2020年9月9日 Italian cement industries are among the major cement producers in the European panorama In the last decades, because of the increasingly stringent specifications on environmental impact and energy saving, technology in the cement plant has been significantly improved []In this context, Advanced Process Control (APC) systems have become the Optimization of the Clinker Production Phase in a Cement Plant
.jpg)
Energetic assessment of a precalcining rotary kiln in
2021年11月1日 Cement production has been increasing rapidly leading to energy consumption, with serious cost implications and environmental challenges Energy efficiency is a key component required to maintain 2021年7月1日 Different input and output data for a rotary cement kiln were collected from a cement plant producing 10,000 tons of clinker per day The raw data were preprocessed to remove the outliers and the (PDF) DEVELOPMENT OF SUITABLE MACHINE stressed that the Project, being WIH Group’s first overseas clinker cement production line with a daily output of 5000 tons, is a milestone for the implementation of WIH Group's strategy of "developing Africa and developing the world" Dugongo Cimentos has achieved a great landmark and he hoped that everyone can work together withThe 5000 t/d Cement Clinker Kiln of Mozambique Dugongo 2022年4月4日 Nothing There’s no difference between a cement truck and a concrete truck They’re actually the exact same thing The terms concrete and cement are often used interchangeably But the truth is, they’re not the same Cement is the active ingredient in concrete along with sand, stone and water But cement and concrete are different products15 Things You Always Wanted To Know About Concrete Trucks
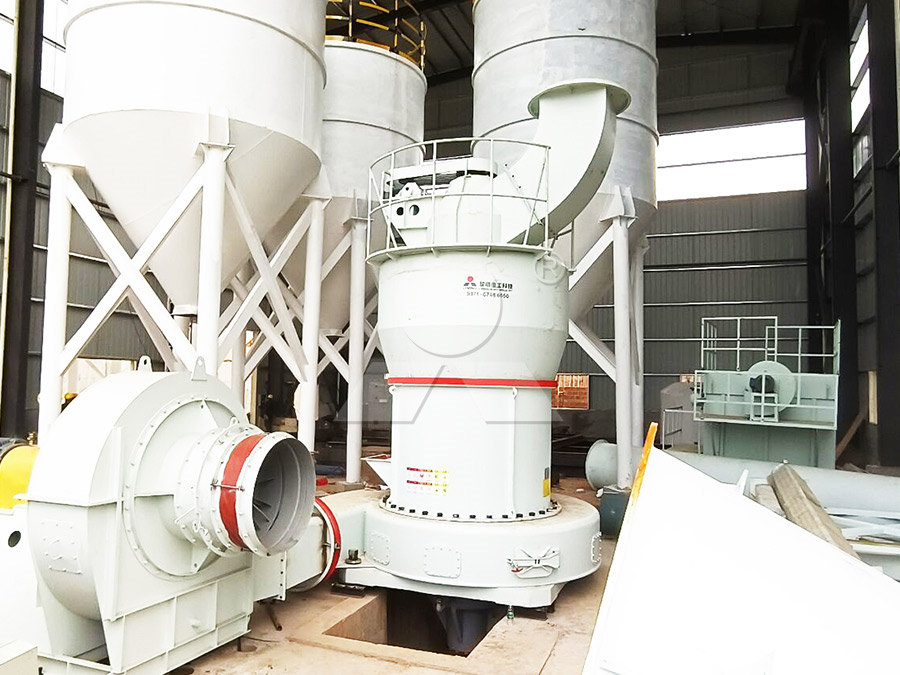
United States cement industry statistics facts Statista
2024年5月22日 Production capacity of cement in the United States from 2020 to 2022, by plant type (in million metric tons per year) Premium Statistic US cement shipments to final customers 年12月19日 A case study has been done at a cement factory having two units, 1600 TPD and 5500 TPD, identified three waste heat rejections at 176 °C, 330 °C and 420 °C and designed a suitable power plant Design and analysis of a cogeneration plant using heat recovery 3,600 million metric tons of cement in 2021 [18,19] According to predictions in Fig 1, the world could consume up to 5800 million metric tons of cement by the year 2050 [19] Awareness of the adverse impacts of cement and concrete production on Impacts of Cement Production on the Environment with Practical 2017年3月1日 Data from a working 1 Mt per annum plant in India is used to obtain an energy balance for the system and a Sankey diagram is drawn It is found that about 35% of the input energy is being lost (PDF) The generation of power from a cement kiln waste gases
.jpg)
Aspen Plus process simulator flow sheet for a typical cement
Furthermore, in actual production, by mixing 100 tons of SS and FA with Portland cement with a daily output of 2500 tons, the compressive strength during early hydration stages can reach 3452 MPa 2023年9月15日 Cement manufacturing is one of the most energy and carbonintensive industries worldwide, accounting for 7 % of the global industrial energy use and 27 % of the global industrial carbon emissions (WBCSD and IEA, 2018)Cement, as a cementitious material of concrete, has been widely used in construction, transportation, water conservancy, and other Historical trend and decarbonization pathway of China's cement 2024年10月1日 A cement plant with a daily output of 5000 t and a methanol plant with a 2677 t output per day are chosen as the case study The scale of the methanol plant is determined by the utilization scale of the CO 2 captured from the cement factory Current typical technology (CTT) is defined as the existing cement plant and methanol plant using coalA Coproduction system of cement and methanol: Unveiling its 2024年5月22日 Cement and clinker sales volume of China National Building Material (CNBM) from 2012 to 2022 (in million tons) Premium Statistic Total revenue of CRH Group 20042023Global cement industry statistics facts Statista
.jpg)
Cement Manufacturing Plant Report 2024: Setup and Cost
Report Overview: IMARC Group’s report titled “Cement Manufacturing Plant Project Report 2024: Industry Trends, Plant Setup, Machinery, Raw Materials, Investment Opportunities, Cost and Revenue” provides a complete roadmap for setting up a cement manufacturing plant It covers a comprehensive market overview to microlevel information such as unit operations involved, 2020年1月3日 Setting up a cement plant is both time and capital intensive; it could take anywhere between five to seven years from concept to commissioning and an investment of around to Rs 1,8002,000 crore for a typical integrated plant of 3 million tpa cement capacity Size of a cement plant could vary from 02 million tpa to 50 million tpaKey factors in setting up a cement plant Indian Cement Review2011年12月19日 Large amounts of energy are consumed during the manufacturing of cement especially during the calcination process which also emits large amounts of CO2 A large part of the energy used in the making of cement is released as waste heat A process to capture CO2 by integrating the recovery and utilization of waste heat has been designed Aspen Plus software Recovery of waste heat in cement plants for the capture of CO 2Deep decarbonisation of industry: The cement sector Cement sector overview Cement is the binding agent of concrete, the most widely used construction material in the world The cement sector is a major greenhouse gas emitter, responsible for about 7% of CO 2 emissions globally (1), and about 4% in the EUDeep decarbonisation of industry: The cement sector Europa
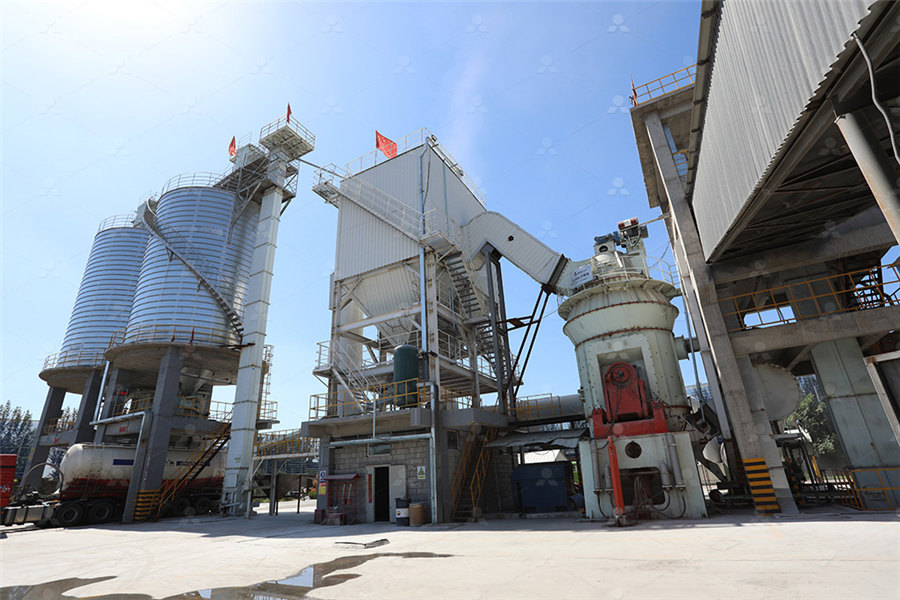
Why Cement Plants Are Ideal Candidates for IoTBased Predictive
Replacing plant machinery requires a colossal capital influx and is not a feasible option According to Entrepreneurship magazine, setting up a cement plant today producing 5000 MT/day would require an investment of at least USD 1377 million to start with, only for the plant machinery2024年5月23日 In cement plants, belt conveyors are used to move raw materials such as limestone, clay, and other additives from the quarry to the processing plant They are also employed in the transportation of intermediate products like clinker and finished goods like cement to storage or shipping areasOptimizing Material Flow with Belt Conveyor in Cement Plant2019年3月8日 use and now account for over 90 percent of cement consumption worldwide (41 billion tons in 2016) Cement accounts for at least 5 percent of anthropogenic emissions of greenhouse gases, and IMPROVING THERMAL AND ELECTRIC ENERGY EFFICIENCY AT CEMENT 2003年6月5日 In general, the use of up to 5% limestone does not affect the performance of portland cement Strengths of cements with limestone can be optimized by grinding to an appropriate particle size The Use of Limestone in Portland Cement: A State
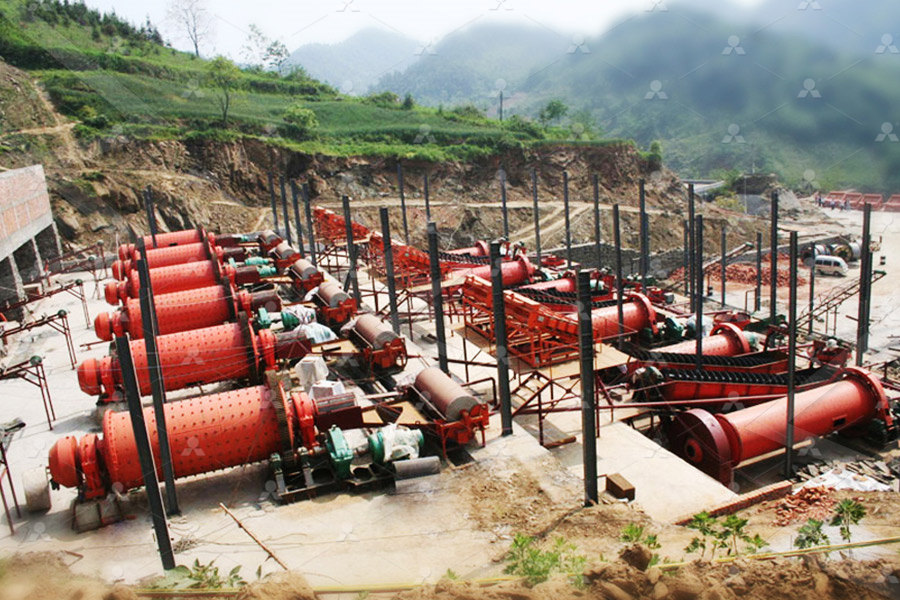
8 Tips For Cement Plant Design
2023年11月1日 In the design of a large cement plant, the raw fuel, especially limestone, is equipped with a prehomogenization yard, but because limestone has been consciously matched in the mining process, and the daily amount is 2012年4月30日 Samanta et al [2] worked on the "automation of a cement process plant" with the aim of eliminating the challenges associated with the manual operation of the plant(PDF) Process Automation of Cement Plant2017年11月22日 Mombasa Cement owns a clinkering plant in Vipingo, Mombasa—which last year announced plan to triple daily capacity to 9,000 tonnes—and is a sister company to Tororo Cement of UgandaMombasa Cement to double output at its Athi River plant2022年10月1日 Cement production is one of the energyintensive industries, which consumes nearly 5% of the global industrial energy [1, 2]In cement production, energy cost accounts for 30%–40% of the total production cost [3]In particular, China's cement production accounts for 55–60% of the world's cement production [4]The new dry process cement production Energy and thermodynamic analysis of a typical cement
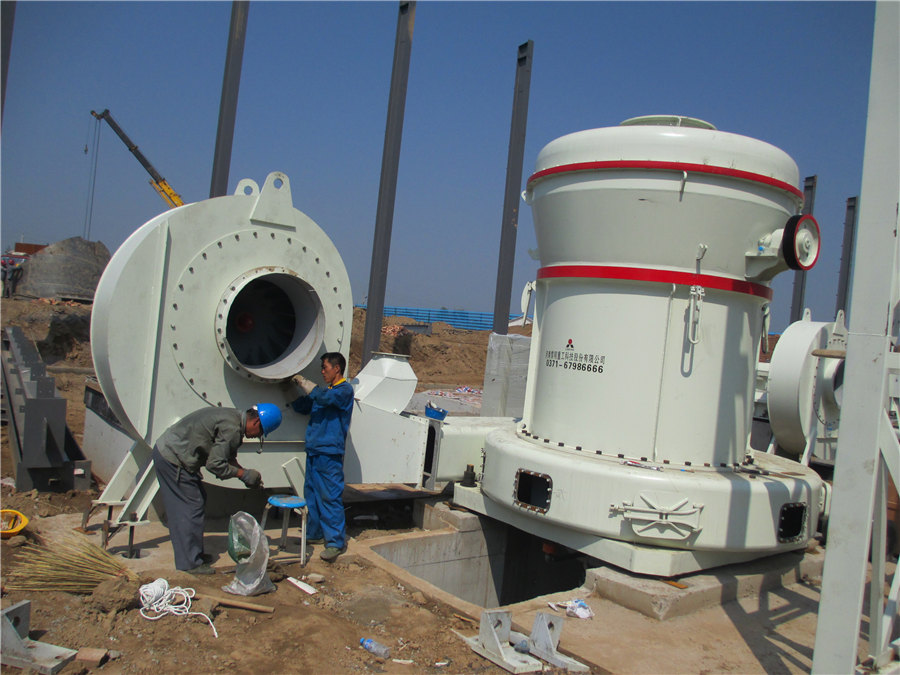
Why You Choose Mini Cement Plant AGICO Small Cement Plant
Cement Grinder The diameter of clinker particles is usually between 032 and 50cm, while the finished cement we use daily is a finer powdery object2014年5月1日 The applications prevent the emission of 161448 tons of CO2 per year to the atmosphere Rotary kiln flow diagram The energy band diagram (Sankey) of the rotary kilnAnalysis of the parameters affecting energy consumption of a Cement Silo Common Issue: Coating in cement Silo It happens due to storage of cement in silos at high temperature (>70 oC), and improper water spray system in cement mill Strategy to fix the issue: Use cement coolers if cement temperature is higher than specified Do not store cement for long time in siloCEMENT PLANT TALK001The clinker cement production line with a daily output of 6,000 tons in Andijan, Uzbekistan officially started; The group grandly held the 2021 annual work summary and 2022 annual mobilization meeting; The group The clinker cement production line with a daily output of 6,000 tons
.jpg)
Energy balance and cogeneration for a cement plant
2002年4月1日 The cement industry is an energy intensive industry consuming about 4 GJ per tonne of cement produced A thermodynamic analysis for cogeneration using the waste heat streams is not easily available