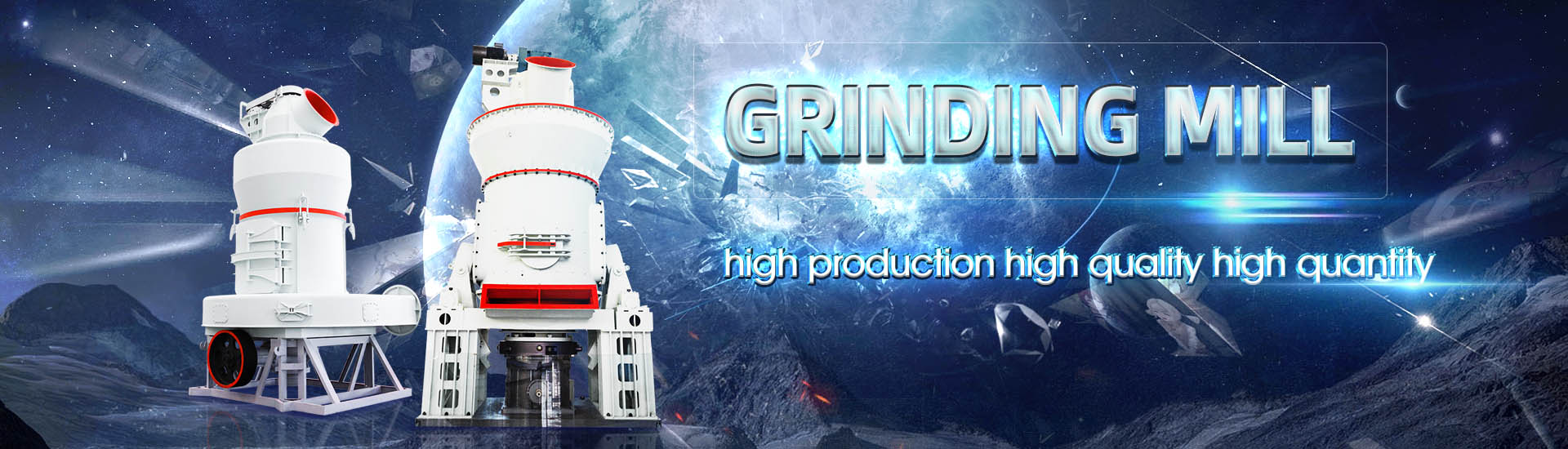
Conditions for using ore grinding machine
.jpg)
Factors affecting ores grinding performance in ball mills
The milling conditions can have a significant impact on the grinding performance of ores The most important factor is the speed at which the balls are moving through the mill Too much Grinding can be achieved by several mechanisms, including: impact or compression due to sudden forces applied almost normally to the particle surface; chipping or attrition due to Grinding Mill an overview ScienceDirect Topics2023年10月27日 Grinding media play an important role in the comminution of mineral ores in these mills This work reviews the application of balls in mineral processing as a function of the A Review of the Grinding Media in Ball Mills for Mineral Processing 2023年7月20日 Moist grinding, a special grinding method, is used to prepare pellets for smelting According to the grinding medium features, ore grinding is mainly classified into ball grinding Ore Grinding SpringerLink
.jpg)
Grinding Modeling and Energy Efficiency in Ore/Raw
2022年8月31日 The order of influencing factors of the two ores is as follows: grinding time > filling ratio > grinding concentration For Tongkeng ore, the optimized grinding conditions are grinding time 54 min, grinding concentration 2023年6月1日 The main parameters of grinding and classification process include measurement of millfeeding quantity, mill load measurement, measurement of ore slurry density, Online Measurement and Control for Ore Grinding and ClassificationA simple and novel nonlinear model of a runofmine ore grinding mill circuit, developed for process control and estimation purposes, is validated The model makes use of the minimum Analysis and validation of a runofmine ore grinding mill circuit 2022年10月13日 For Gaofeng ore, the optimized grinding conditions are grinding time 38 min, grinding concentration 73% and filling ratio 34% Grinding plays an important role in mining, construction, metallurgy, chemical, coal and Research on Grinding Law and Grinding Parameters
.jpg)
Stirred media mills in the mining industry: Material grindability
2020年6月1日 Stirred media mills are used by the mining industry for ultrafine grinding to enhance liberation, and to decrease particle sizes of industrial minerals to tailor functional 2024年4月13日 Additionally, grinding the concrete surface can expose the aggregate, resulting in a decorative effect that enhances the appearance of the concrete Lastly, a concrete grinder grinding machine can be used to flatten uneven surfaces, such as high spots or uneven slabs, ensuring a level and stable base for further construction or installationThe Ultimate Guide To Using A Concrete Grinder Grinding Machine2021年4月21日 This work presents a method to optimize centerless grinding geometrical configuration It is based on the regulation of the horizontal axes of operating and regulating wheels of the machine OPTIMIZATION OF SETUP CONDITIONS FOR STABILITY OF THE 2024年1月31日 Additionally, machine breakdowns often pose threats to the safety of workers Consequently, it is crucial to optimise the control of slag grinding systems, whether from a system optimisation control or safety Intelligent process control system for predicting
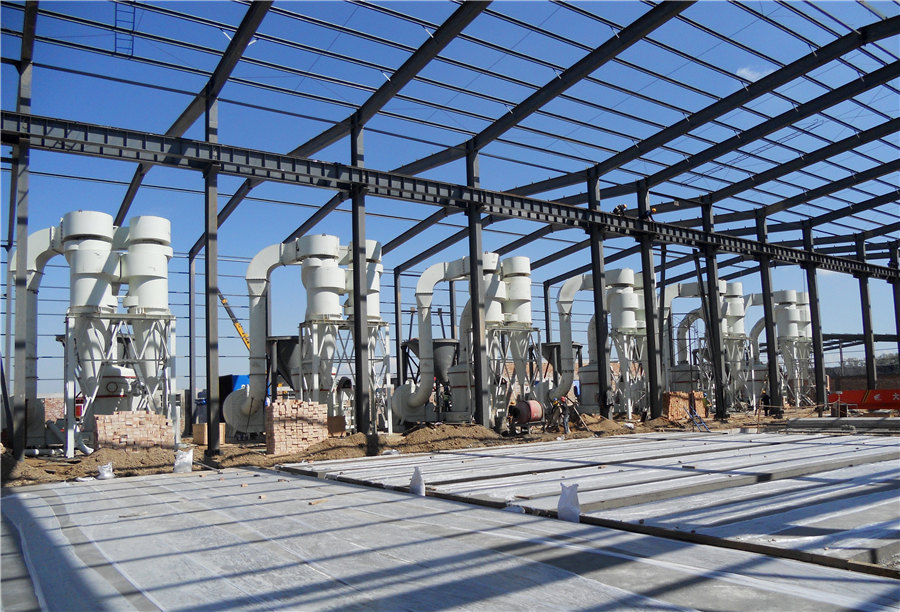
Industry Grinder for Mineral Processing JXSC Machine
A ball mill, also known as a ball grinding machine, is a wellknown ore grinding machine widely used in mining, construction, and aggregate applicationsJXSC started the ball mill business in 1985, supplying global services including design, manufacturing, installation, and Here’s a look at some of the most common types of precision grinding machines from Maximum AdvantageCarolinas 1 Surface Grinders: A surface grinder consists of an abrasive wheel, a chuck (a workpiece holding device), and a rotary table 2 Cylindrical Grinders: A cylindrical grinder is used for shaping the outside of a workpiece 3What Is Grinding Machine? Definition, and Types Mechdaily2023年7月6日 3 Inspect the Machine Before using a grinding machine, it is essential to inspect the machine for any damage or defects Check the grinding wheel for cracks or chips, and make sure it is mounted properly Ensure that the guards are in Grinding machines safe operation and inspection tips Safety BagGuideway grinding machines primarily operate using grinding stones The abrasion caused by the stone is factored into the pressing force to ensure the results achieved are consistent Wellknown manufacturers of guideway grinding machines include MEUSER MOL, SHW, SCHMALTZ, WALDRICHCOBURG and KRAFT Doubledisc grinding machinesUsed Grinding Machines Industrial Metal Grinders CNC
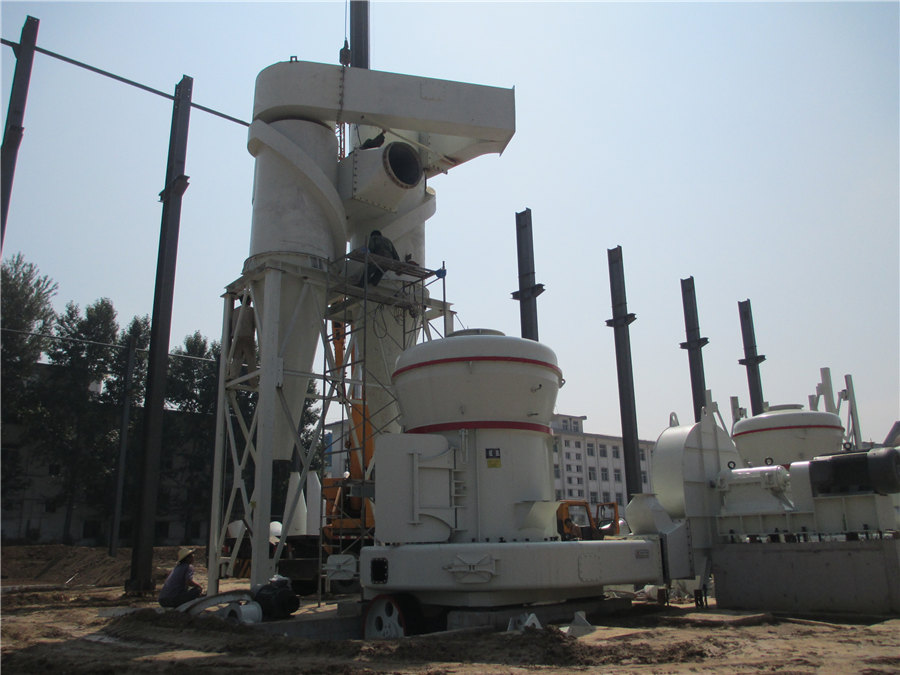
Machine Learning Models for Predicting Grinding Wheel Conditions Using
2004年5月14日 Intelligent models built with sensor information and machine learning techniques are predicting the condition of the tool with good accuracy In this study, statistical models are developed to identify the conditions of the abrasive grinding wheel using the Acoustic Emission (AE) signature acquired during the surface grinding operation2022年12月8日 A CNC grinding machine uses a rotating grinding wheel to remove small amounts of material from a workpiece They are, first and foremost, finishing machines In the case of round work, a machinist often removes significant amounts of material using a lathe before transferring the part to a cylindrical grinding machine for the finishing C Grinding Machine Buyers Guide: Types, Price, Uses, FeaturesOre grinding machines can be divided into many types according to different classification methods, each with significant characteristics The following is a general introduction to the types of oregrinding machines and their characteristics According to the different media of the mill, the grinding machines are divided into: If the medium is steel balls, it is called a ball mill;Ore Grinding Machines: Ball Mill, Rod Mil Grinding Media2021年2月1日 One type of machines that are often used in production lines are grinding machines Grinding is the process of removing material with the help of a grinding tool In grinding machines the tool is a wheel made of hardmaterial grains which are attached by a binding material on a basic body (Chen and Rowe, 1996)A survey of machinelearning techniques for condition monitoring
制粉-10.25公众号.jpg)
Machine tools — Test conditions for surface grinding machines
Machine tools — Test conditions for surface grinding machines with vertical grinding wheel spindle and reciprocating table — Testing of the accuracy 1 Scope This International Standard specifies, with reference to ISO 2301 and ISO 2307, both geometric and2021年2月1日 Request PDF A survey of machinelearning techniques for condition monitoring and predictive maintenance of bearings in grinding machines It is important to minimize the unscheduled downtime of A survey of machinelearning techniques for condition monitoring 2021年7月1日 A new methodology is proposed for accurate and timely identification of wheel wear in cylindrical grinding using Hilbert Huang transform and support vector machine During the grinding of EN31 carbon steel, the condition of the wheel and its wear was monitored with an accelerometer and power cellA robust condition monitoring methodology for grinding 2021年11月8日 Illite ore industrial grinding mill machines include ultrafine grinding mills, vertical roller mills, highpressure mills, wet stirring mills, coarse mills, and so on It can be applied to different illite grinding operation requirements and meet Illite Ore Industrial Grinding Mill Machine SBM Ultrafine

Analyzing process parameters for industrial grinding circuit based
2023年9月1日 The grinding and classification processes are systematic engineering that must comprehensively consider the influence of several factors to ensure good grinding fineness Based on the machine learning method, this study analyzed the full process parameters (ie, ball mill power, fresh ore feed rate, hydrocyclone feed pump power, hydrocyclone 2018年12月24日 The main parameters for the design of the grinding circuit are the ore specifications and the considered operating conditions Ore specifications were characterized by grinding tests, which EVALUATION OF THE ALTERNATIVES FOR GOLD ORE GRINDING CIRCUITS BY USING 2024年4月19日 Tip 9: Cool Down the Grinder Machine After using the grinder machine, allow it to cool down before storing it Grinding generates heat, and a hot machine can be a safety hazard Never leave a running grinder unattended and always unplug it after use Using a grinder machine can be a timesaving and efficient way to accomplish various tasksThe Grind: Understanding The Processes Of Grinding Machines2023年9月7日 A centerless grinding machine usually comprises a grinding wheel, work blade, machine base, and regulating wheel ensures that your workpiece attains a perfectly round shape after grinding to achieve roundness from outof The Ultimate Guide to Understanding Centerless Grinding
.jpg)
5 Grinding Considerations for Improving Surface Finish
2021年8月20日 Improving surface finish can be done by making adjustments to one or more of these points: operational parameters, wheel dressing, grit size, coolant delivery, and machine condition Precision CNC production grinding shines when parts require tight geometric tolerances and quality surface finishes2023年6月21日 Proper Grinding Machine Maintenance is Critical to Ensure Safe Grinding Wheel Usage ANSI B71 states: An employer shall maintain grinding equipment in a condition that will not create a hazard for an employeeThe employer shall instruct an employee to report defective equipment to an employee supervisorGrinding Machine Maintenance Norton Abrasives US and 2018年2月6日 A Review of Cylindrical Grinding Process parameters by using various Optimization techniques and their effects on the surface Integrity, Wear Rate and MRR(PDF) A Review of Cylindrical Grinding Process 2020年8月2日 For most cases, the dressing roll is driven at a peripheral velocity v r while being fed radially into the rotating wheel at an infeed velocity v i corresponding to a depth per wheel revolution a r (Fig 2) (Malkin and Guo 2008)When the wheel speed equals the dressing wheel, the rotary diamond dressing then calls the rolling dressing method (Guo et al 2010)Grinding and Dressing Tools for Precision Machines
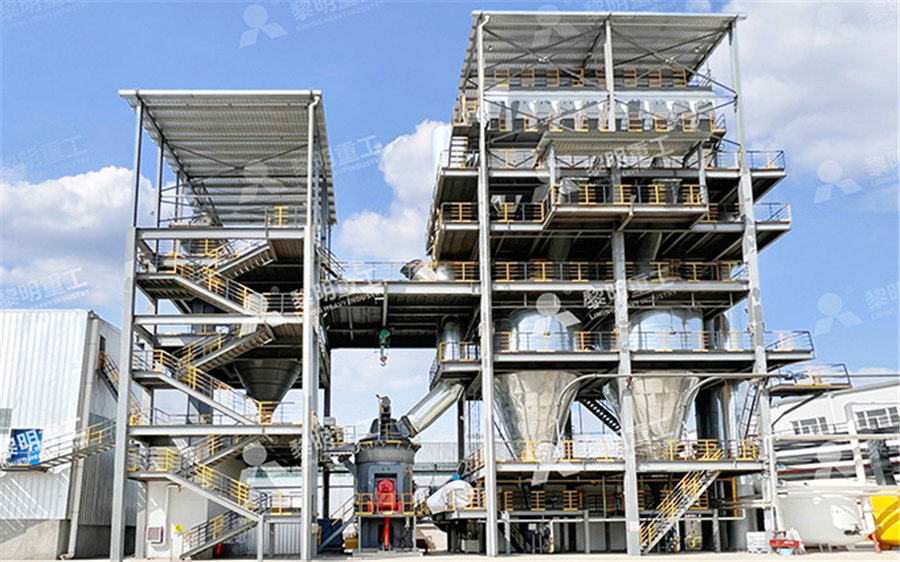
Preparing and using grinding machines UK Standards
Preparing and using grinding machines SEMPEO213 Preparing and using grinding machines 5 device, and how this can cause damage or distortion in the finished components K12 the various grinding operations that can be performed, and the types of grinding wheels that are used (such as surface grinding using solid,Machine tools — Test conditions for external cylindrical centreless grinding machines — Testing of the accuracy Machinesoutils — Conditions d'essai des machines à rectifier les surfaces extérieures sans centre — Contrôle de l'exactitude INTERNATIONAL STANDARD ISO 3875 Fourth edition 202001 Reference number ISO 3875:2020(E)Machine tools — Test conditions for external cylindrical 2012年12月1日 In some recent works, online condition monitoring tools like machine vision system and acoustic emission sensors were employed to improve the quality of grinding operations, increase productivity (PDF) Condition monitoring of grinding process through machine vision 2021年7月3日 Creep feed grinding is a slow, onepass operation that makes a deep cut of up to one inch in steel materials at low table speeds between 05 and 1 ipm It is not suitable for conventional grinding machines, but for those which are compatible with it, it offers high productivity and cost effectivenessMachining 101: What is Grinding? Modern Machine Shop
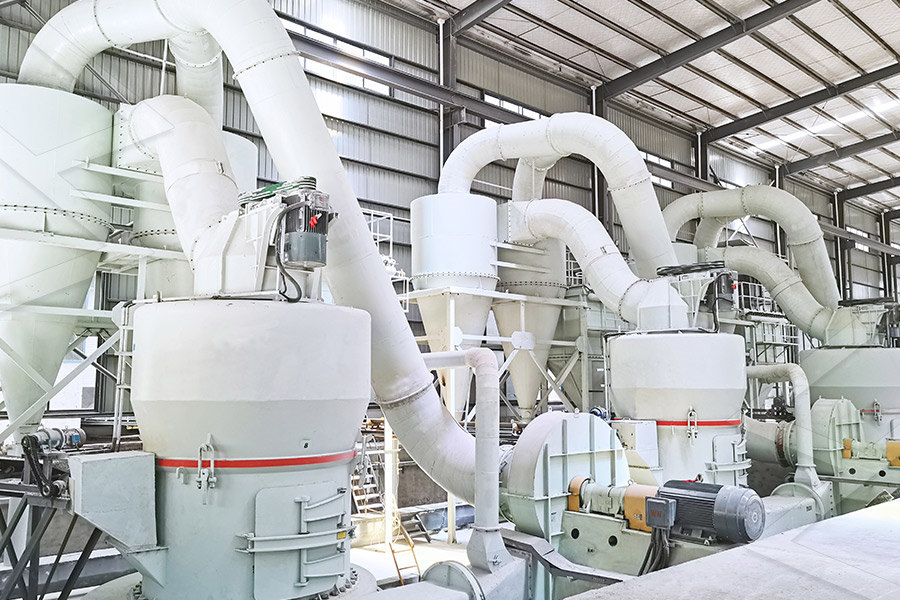
Grinding Machine: Definition, Parts, Working Principle, Operation
2021年5月5日 The grinding machine is widely used to finish the workpiece Do you know why? Because the work removal rate is low between 025 to 05 mm (This can be advantages or disadvantages also for various types of works) Grinding Machine Parts and Function: The Grinding Machine Consists of Following Main Parts: Base or Bed; Column; Headstock 2021年1月16日 Your Single Disc Surface Grinding Machine will look like a horizontal spindle surface grinding machine albeit smaller in size since it does not need a reciprocating or circular table The grinding action in your machine takes place by the abrasive particles on the face of the grinding wheel You will be able to give the feed (depth of cut) by moving the wheel headSurface Grinder Types of Grinders How They Work Fine 2023年9月1日 The grinding and classification processes are systematic engineering that must comprehensively consider the influence of several factors to ensure good grinding fineness Based on the machine learning method, this study analyzed the full process parameters (ie, ball mill power, fresh ore feed rate, hydrocyclone feed pump power, hydrocyclone Analyzing process parameters for industrial grinding circuit based 2018年1月17日 Common unsafe practices in Grinding operation: • Not using any of the mentioned PPE • Use of portable grinding machine as bench grinding machine • Fitting over size wheel than recommended size by machine / wheel Grinding machine PPT SlideShare
.jpg)
Preparing and using grinding machines Scottish Qualifications
the main features of the grinding machine, and the accessories that can be used 8 the range of workholding methods and devices that are used on grinding machines (such as magnetic chucks and blocks, vices, 9 You need to know and understand: SEMPEO213 Preparing and using grinding machines 42022年8月31日 For Tongkeng ore, the optimized grinding conditions are grinding time 54 min, grinding concentration 67% and filling ratio 35% For Gaofeng ore, the optimized grinding conditions are grinding time 38 min, Grinding Modeling and Energy Efficiency in Ore/Raw and flaws Highpressure grinding is the optimal process for removing scale, cracks and other surface defects Grinding largescale rounded parts however, requires specific grinding facilities Machines generally have extremely high driving power, between 50 and 630 kW The grinding speed is generally 80 m/s WORKPIECE TEMPERATURETECHNICAL SOLUTIONS FOR CUTTING GRINDING Norton The least influential parameter on grinding time is the wheel speed In addition, the optimal condition of cutting parameters obtained for grinding tablet shape punches by cubic boron nitride wheels on a CNC milling machine are a cutting depth of 003 mm, wheel speed of 5000 rpm and feed rate of 3500 mm/minOptimization of Grinding Parameters for Minimum Grinding Time
.jpg)
Chapter 17: Grinding Methods and Machines American Machinist
2020年6月29日 Grinding, or abrasive machining, once performed on conventional milling machines, lathes and shapers, are now performed on various types of grinding machines Grinding machines have advanced in design, construction, rigidity and application far more in the last decade than any other standard machine tool in the manufacturing industry Grinding Download scientific diagram Restitution coefficient "oreore" experiment conditions from publication: SemiAutogenous Wet Grinding Modeling with CFDDEM The paper highlights the features of Restitution coefficient "oreore" experiment conditionsURN: J/600/5861 Level: Level 2 Credit value: 15 GLH: 68 Relationship to NOS: This unit has been derived from national occupational standard Performing Engineering Operations Unit No 13: Preparing and using grinding machines (Suite 2) Aim: This unit covers the skills and knowledge needed to prove the competences required to cover a broad range of basic grinding activities Unit 211 Preparing and using grinding machines 1Library2021年8月1日 To retrieve the knowledge focusing on oreforming conditions from the text, we targeted six entity categories: ore/deposits, rocks, minerals, stratigraphic units, locations and geological timescales The pairwise links representing their association are identified based on verbs and/or prepositions that connect them in the text at sentence levelUnderstanding oreforming conditions using machine reading
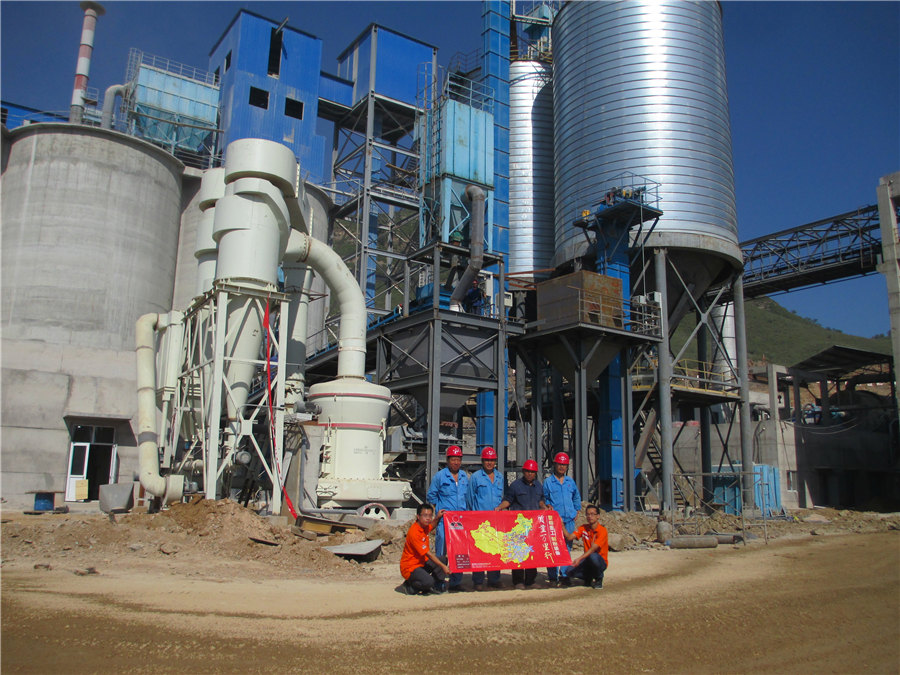
Grinding Machines SpringerLink
2015年1月1日 As grinding machines belong to the class of machines for the material removal with geometrically nondefined cutting edges, those machines can be classified in correlation to the classification of the different process technologies with geometrically nondefined cutting edges as it is given in DIN 8589, parts 11, 12, and 13 (DIN 858911 2003; DIN 858912 2003;