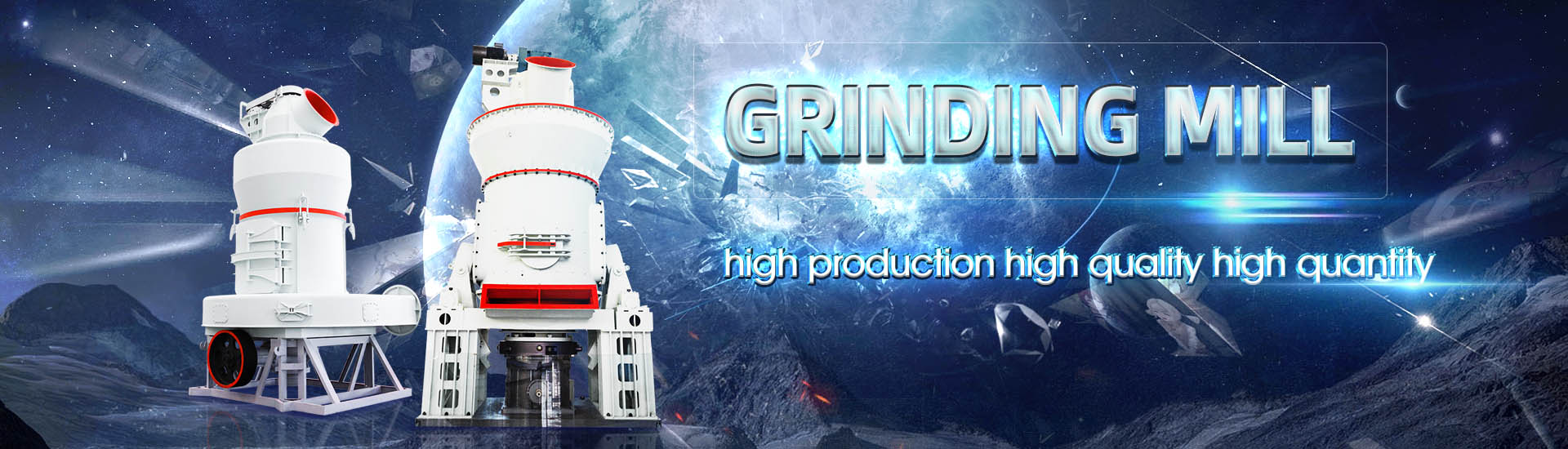
What is the speed ratio of ore mill
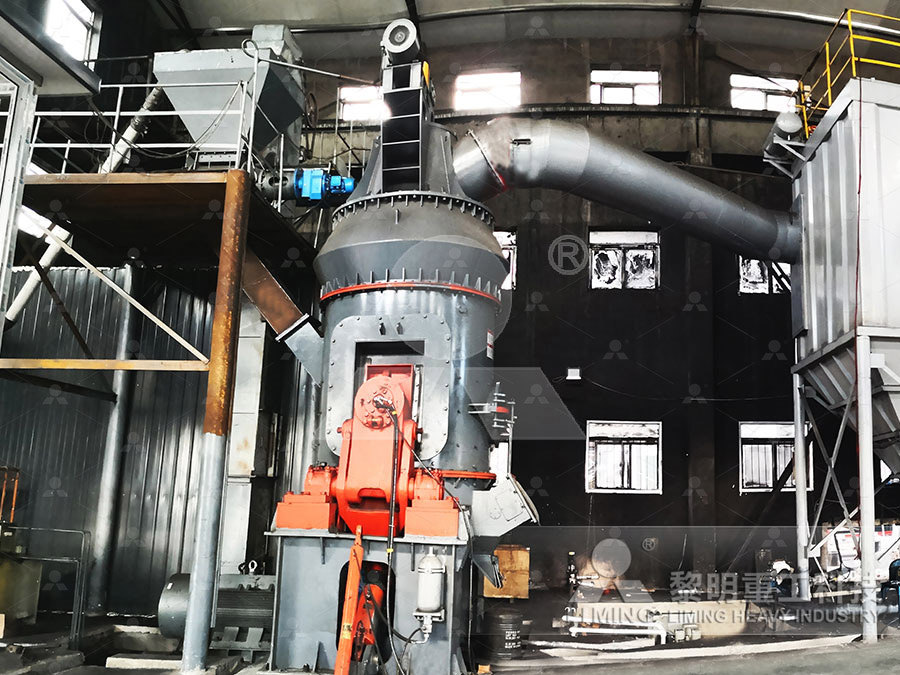
AMIT 135: Lesson 7 Ball Mills Circuits
Size rated as diameter x length Feed System 1 One hopper feed 2 Diameter 40 – 100 cm at 30 ° to 60 ° 3 Top of feed hopper at least 15 meter above the center line of the mill Feeder 1 Single or double helical scoop feeder or a spout feeder 2 Double helical feeders used in closedcircuit with classifiers 3 Spout feeders 展开2011年8月1日 Milling speed is one of the most important milling parameters that controls the milling process because it provides the mill with the energy required for (1) powder particles Mill Speed an overview ScienceDirect Topics2023年11月24日 Factors that influence the grinding efficiency include mill design, liner design, mill speed, mineralogical composition of the ore, charge ratio, and grinding media properties Grinding Media in Ball Mills for Mineral Processingin the center of gravity with speed The center of gravity first starts to shift to the left as the speed of rotation increases but as critical speed is reached the center of gravity moves towards the TECHNICAL NOTES 8 GRINDING R P King
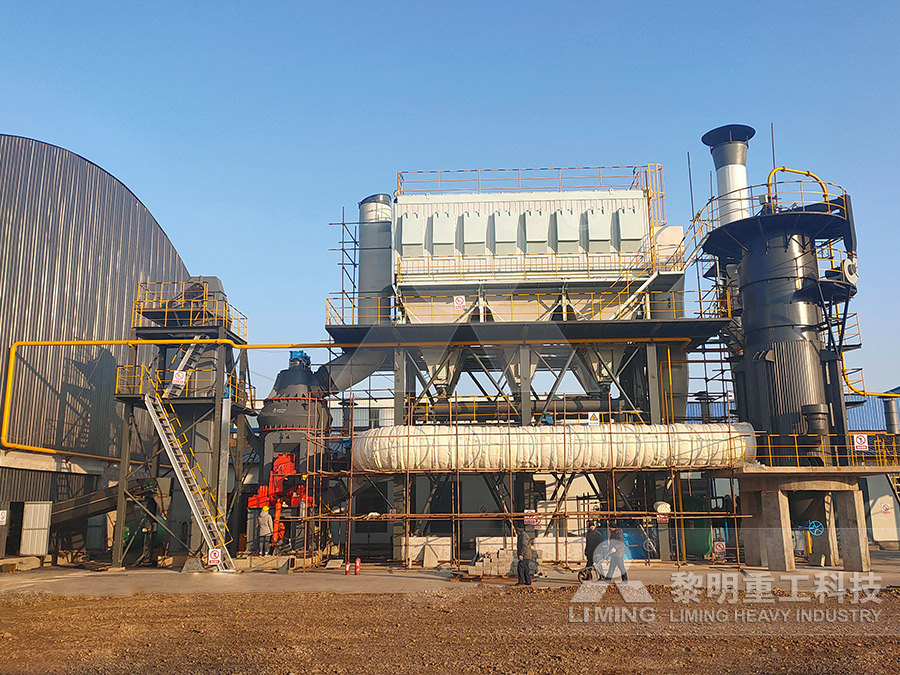
The influence of mill speed and pulp density on the grinding
These tests were done with the ∅ 082 x 1 m overflow mill with a 30 mm graded ball charge and a 30% filling degree The speed was increased from 65% to 90% Vcrit The data is summarized 2016年1月1日 Since the breakage of ore in AG/SAG mills is mostly due to impact on particles and media from a height, these mills generally have a large diametertolength (D / L) ratio Autogenous and SemiAutogenous Mills ScienceDirect2023年10月27日 Factors that influence the grinding efficiency include mill design, liner design, mill speed, mineralogical composition of the ore, charge ratio, and grinding media properties A Review of the Grinding Media in Ball Mills for Mineral Processing benchmarking of mill selection (regardless of the modelling methodology that is used to arrive at a given mill sizing) At its most rudimentary, this involves comparisons with historical reference SAG Mill Design and Benchmarking Using Trends in the JKTech
.jpg)
A guide to SAG Mill management
2024年5月17日 Once the mill load is measured, operators can adjust various factors to achieve the desired level: This refers to the amount of ore entering the mill Increasing the feed rate 2016年3月21日 Mill Water to Ore Ratio Requirements Resistance of Various Materials to Crushing Pulp Calculations W—Tons of solids per 24 hours R—Ratio of weights: solution/solids V—Ratio of volumes: solution/solids Common Basic Formulas for Mineral Processing 2019年8月14日 • Central discharge ball mill: the inlet of medium unloading ball mill is at both ends, and the outlet is in the middle of the ball mill 4 According to the ore discharge of ball mill: • Overflow ball mill: Discharge the ore through hollow shaft • Grid ball mill: Discharge the ore through the plaid plateThe Ultimate Guide to Ball Mills MiningpediaInlet – crushed ore is fed to the ball mill through the inlet At critical speed, the grinding mill charge clings to the mill inner surface and does not tumble Ball mills are usually designed with a maximum reduction factor/ratio of 60:1 Ball Mill (Ball Mills Explained) saVRee saVRee
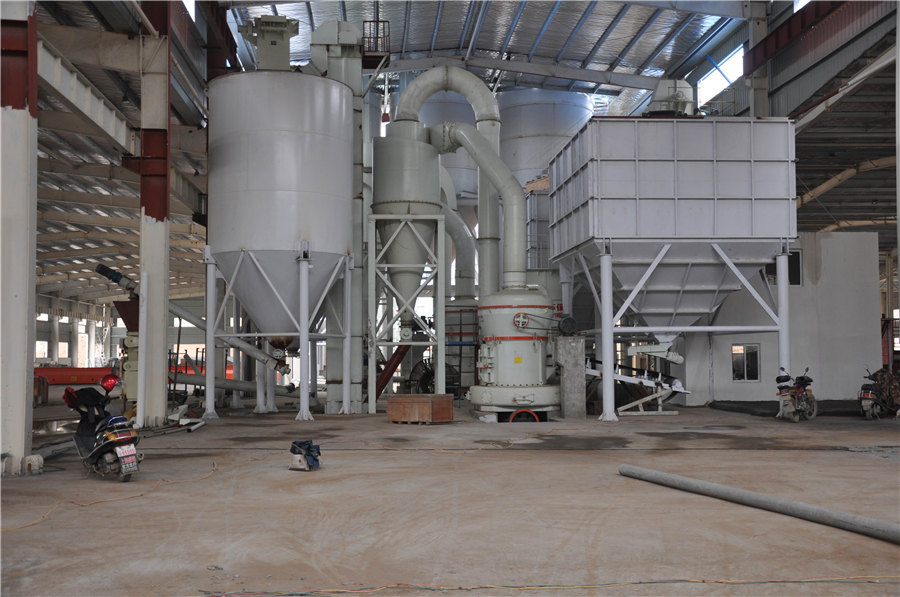
A Review of the Grinding Media in Ball Mills for Mineral Processing
2023年10月27日 The ball mill is a rotating cylindrical vessel with grinding media inside, which is responsible for breaking the ore particles Grinding media play an important role in the comminution of mineral ores in these mills This work reviews the application of balls in mineral processing as a function of the materials used to manufacture them and the mass loss, as 2010年11月13日 The theoretical maximum efficiency of a wind turbine is given by the Betz Limit, and is around 59 percentPractically, wind turbines operate below the Betz LimitIn Fig 4 for a twobladed turbine, if it is operated at the optimal tip speed ratio of 6, its power coefficient would be around 045At the cutin wind speed, the power coefficient is just 010, and at the cutout The Betz Equation and Optimal Rotor Tip Speed Ratio2013年8月3日 In Grinding, selecting (calculate) the correct or optimum ball size that allows for the best and optimum/ideal or target grind size to be achieved by your ball mill is an important thing for a Mineral Processing Engineer AKA Metallurgist to do Often, the ball used in ball mills is oversize “just in case” Well, this safety factor can cost you much in recovery and/or mill liner Calculate and Select Ball Mill Ball Size for Optimum Grinding2016年1月1日 Working with a 732 m diameter and 366 m long mill, NapierMunn et al [4] observed that the breakage rate for the finer size fractions of ore (say 01 mm) at lower speeds (eg, 55% of the critical speed) was higher than that Autogenous and SemiAutogenous Mills ScienceDirect
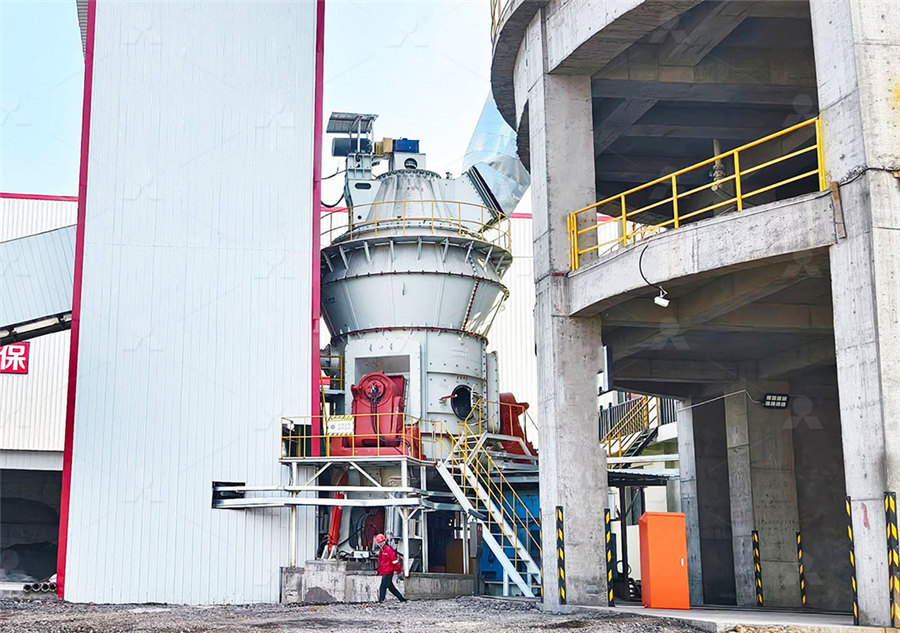
BALL MILLS Ball mill optimisation Holzinger Consulting
Ball mill optimisation As grinding accounts for a sizeable share in a cement plant’s power consumption, optimisation of grinding equipment such as ball mills can provide significant cost and CO 2 emission benefits to the cement producer n by Thomas Holzinger, Holzinger Consulting, Switzerland2017年5月8日 Since as has already been mentioned, the critical speed is a criterion for the occurrence of many phenomena in a mill, it is perhaps of interest to mention that during the course of tests at various speeds, the configuration of the balls within the shell was observed through a perspex end cap, and, in the case of the smooth mill, centrifuging of the outer layer Grinding Mill Power 911Metallurgist2011年8月1日 In 2004, Hashimoto et al [19] pointed out to the importance of theoretical investigations regarding effect of the rotation and revolution speeds and their directions on the impact energy of balls and grinding characteristics of the product in the mill They have studied experimentally and theoretically the effect of the rotationtorevolution speed ratio on the Mill Speed an overview ScienceDirect TopicsThe effect of relative rotational speed, the ratio of actual speed to critical speed, was found to be complex At loadings between 04 and 08, Ball mills are often operated at higher speeds than rod mills, so that the larger balls cataract and impact on the ore particles The work input to a mill increases in proportion to the speed, Ball Mill an overview ScienceDirect Topics
.jpg)
MillGears
Impact of Gear Ratios on Industrial Gearbox Performance 1 Torque and Speed Adjustment The primary impact of gear ratios is on the torque and speed of the output shaft A higher gear ratio means increased torque but reduced speed, while a lower gear ratio results in 2017年3月4日 Ore, Copper Ore, Zinc Ore and Manganese Ore 41 The art of crushing: Crushing means different things for differe nt operations and the production goals are not alway sSIZE REDUCTION BY CRUSHING METHODS2016年7月8日 UNTIL THE THIRD THEORY OF COMMINUTION of "Work Index" method of determining crushing and grinding mill size Sizing a Ball or Rod Mill Sizing a Crusher using >1200 Wi of Ores from This can be obtained by averaging the reduction ratios at 90, 70, 50, 30 and 10% passing The reduction ratio, at any percent passing Equipment Sizing: Crusher or Grinding Mill 911Metallurgist500 rpm, the roll speed ratio is 2:1 (1,000/500) More shear — and thus a larger roll speed ratio — is required to crush less friable particles Running the rolls at the ideal roll speed ratio will achieve the desired shearing effect as the material passes through the nip point; the higher the shear, the more tearing the crushed particle Roller mills: Precisely reducing particle size with greater efficiency
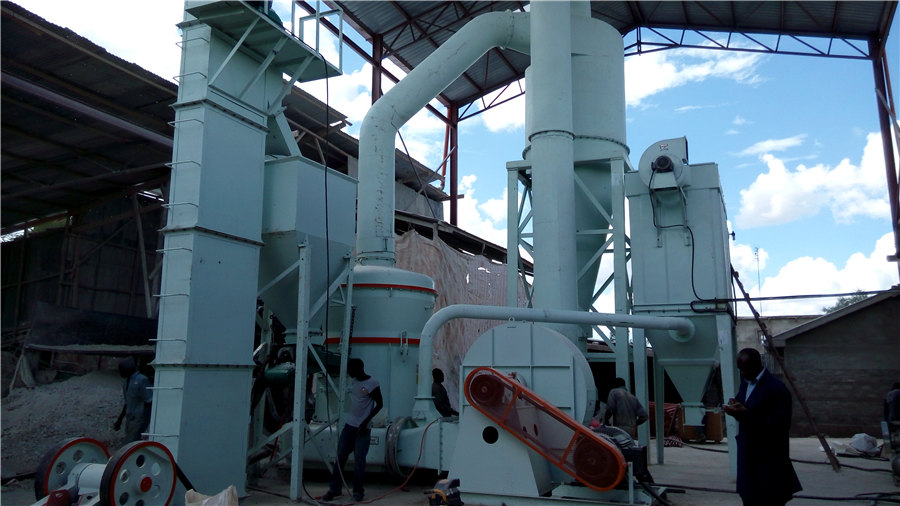
Design of a verticalaxis wind turbine: how the aspect ratio
2014年8月2日 This work analyses the link between the aspect ratio of a verticalaxis straightbladed (HRotor) wind turbine and its performance (power coefficient) The aspect ratio of this particular wind turbine is defined as the ratio between blade length and rotor radius Since the aspect ratio variations of a verticalaxis wind turbine cause Reynolds number variations, any 2020年9月10日 Critical speed is calculated by the formula: where: D – inside diameter of ball mill drum, m Ratio of grinding mill loading by grinding balls Ratio of grinding balls volume to mill working volume is calculated by the formula: where: G н – mass of grinding balls, kg; γ – apparent density of grinding media, kg/m3; L – drum length, mTHE MODE OF BALL MILL OPERATION Energosteel Grinding 2017年2月13日 In all ore dressing and milling Operations, including flotation, cyanidation, gravity concentration, and amalgamation, the Working Principle is to crush and grind, often with rod mill or ball mill, the ore in order to liberate the minerals In the chemical and process industries, grinding is an important step in preparing raw materials for subsequent treatmentBall Mills 911MetallurgistEFFECT OF ROTOR TIP SPEED RATIO The choice of the tip speed ratio for a particular wind turbine design depends on several factors In general a high tip speed ratio is a desirable feature since it results in a high shaft rotational speed that is needed for the efficient operation of an electrical generator A high tip speed ratio however OPTIMAL ROTOR TIP SPEED RATIO Worcester Polytechnic
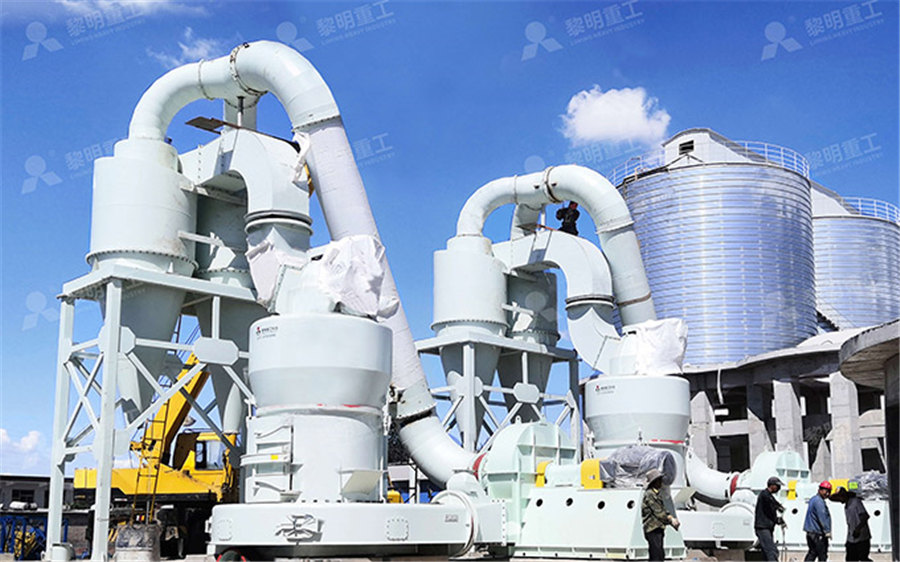
Best way to determine the balltopowder ratio in ballmilling?
To really choose, I guess it depends on the material and your mill (vial, RPM, media, filling volume) Ie Si80Ge20 is easily alloyed in the high energy SPEX mill911 Metallurgist can enter the scene and see what you have become blind to We can fix issues in ways you never thought possible Our fresh eyes will open new opportunities for your plant Each mineral processing plant has varied ore types, mining equipment, (crusher, ball mill, flotation, tailings), and management (operating) philosophyThe evaluation and prioritization of variables Metallurgists Mineral Processing Engineers 911Metallurgist2020年10月9日 Simulation results under the ∅5250 × 500 mm mill model show that the mill operates with the optimal effect when the mill is under the condition of 80% critical speed and 15% fill level; the Operation Analysis of a SAG Mill under Different 2019年2月1日 As indicated earlier in the introduction section, it has previously been shown that 1/t ig and the energy milling power provided by a mill are directly linked [18]In Fig 4, 1/t ig is plotted as a function of k for the different ω d and BPR, from which the multi dependence of k, ω d and BPR on the milling efficiency can be observed In this figure, it is more clearly visible as Effects of the speed ratio on the efficiency of planetary mills
.jpg)
Mill (grinding) Wikipedia
A mill is a device, often a structure, machine or kitchen appliance, that breaks solid materials into smaller pieces by grinding, crushing, or cutting Such comminution is an important unit operation in many processesThere are many different types of mills and many types of materials processed in them Historically mills were powered by hand or by animals (eg, via a hand crank), Structure of a mixing mill A mixing mill consists of two rolls arranged in parallel The two rolls can, independently of one another, be moved towards each other The speed is adjusted to a specific ratio here Depending on the mixture, either the front roll facing the machine operator or the rear roll rotates fasterMixing mills DEGUMASCHÜTZ GmbHthe mill The common range of mill speeds is 65% to 80% of critical, depending on mill type, size and the application The critical speed of a ball mill is calculated as 5419 divided by the square root of the radius in feet The rotational speed is defined as a percentage of the critical speed Smaller diameter millsATTRITORS AND BALL MILLS HOW THEY WORK Union ProcessOre Work Index; Ore Feed Size; (13586)] A chart showing rod mill capacity vs reduction ratio [image: (13587)] Rod Mill Capacity Problems Difficulty in manufacturing perfectly straight rods The Rowland and Kjos equation indicates that power draw is a function of the fraction of the critical speed for the millAMIT 135: Lesson 8 Rod Mills – Mining Mill Operator Training
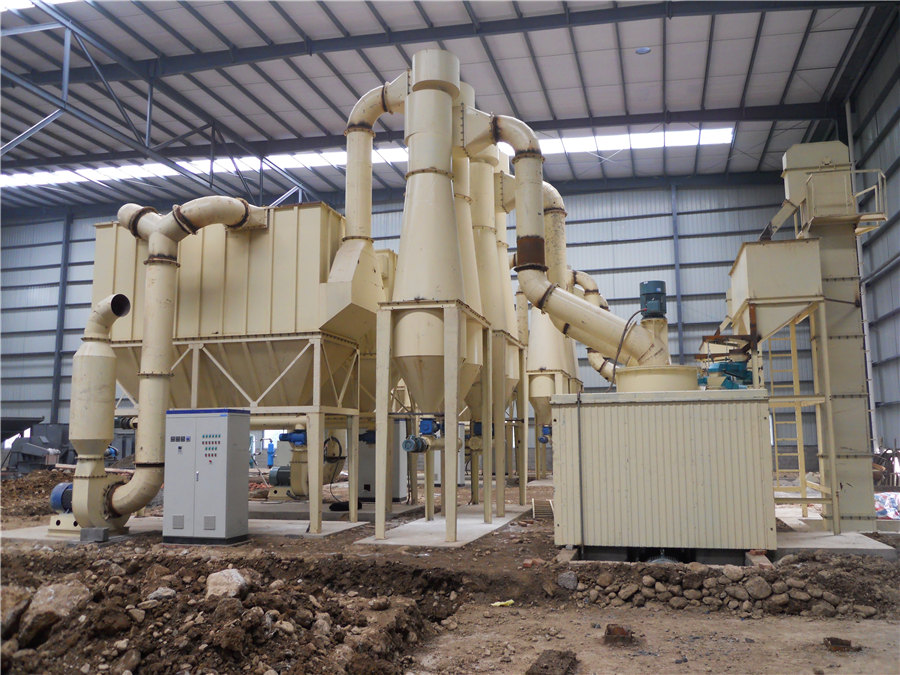
High Speed Hammermills For Fine Grinding: Part 3 Feed
The following discussion covers such factors as tip speeds, screen hole size, hammer patterns and position, horsepower ratios (to hammer and screen area), and air assist systems (Figure 2) Tip Speed Tip speed is simply a factor of mill diameter and motor RPM; D x RPM = TIP SPEEDThe profile can be better customised to suit mill speed and filling and therefore optimise performance, and it allows more material in the lifter for a given base width, but the mill must only run in one direction 7 High–low double wave ball mill The Selection and Design of Mill Liners 911 Metallurgist2017年10月25日 For example, using well established relationships between power draw and mill diameter and speed, 50 mm (2 inches) of liner wear results in about 14 percent power increase (at constant loading and rotational speed) for a 24 meter (8 foot) diameter mill, as opposed to only 6 percent for a 50 meter (16½ foot) diameter unitRecommended Ball Mill Speed Liner Configuration2023年11月24日 Factors that influence the grinding efficiency include mill design, liner design, mill speed, mineralogical composition of the ore, charge ratio, and grinding media properties The grinding efficiency of a ball mill is determined by the product size distribution, energy consumption, and the grinding costsGrinding Media in Ball Mills for Mineral Processing

Grinding Mills and Their Types – IspatGuru
2015年4月9日 Typically this type of mill can deliver a product with a fineness of less than 01 mm Testing of material is needed before hand to determine the suitability of the ore for processing in an autogenous mill The rod mill (Fig 1) 2023年2月15日 A beneficiation plant in Singapore loads balls into a ϕ 1500mm×3000mm wet grid type ball mill, determines the filling rate ϕ = 50%, and selects cast steel grinding balls δ = 45 t/m 3 The ball mill processes the Method of Steel Grinding Ball Proportioning and 2018年4月17日 AllisChalmers has a proprietary equation, adapted from the kilowatt hours per ton of balls (Kwb) equation for calculating ball mill power published by Bond, to determine the power which an autogenous mill or semiautogenous mill will draw under specified conditions or ore specific gravity, pulp density in mill, mill speed and volumetric Autogenous and SAG SemiAutogenous Mill Design Calculations2012年6月1日 [4, 5] and an empirical relation is suggested expressing the mill capacity as a ratio u 2 − fresh ore feed rate, u 3 − mill critical speed fraction, u 4 − sump dilution water Grinding in Ball Mills: Modeling and Process Control
.jpg)
Roll Mill an overview ScienceDirect Topics
Routes to thick films Robert Dorey, in Ceramic Thick Films for MEMS and Microdevices, 2012 261 Roll mill Two counterrotating rollers made of hard materials crush the powder that passes between them It is possible to obtain powder sizes down to approximately 10 μm Due to the coarse size of the powder obtained, this form of rolling is rarely used for powder processing in 2021年3月26日 Ball mill grinding efficiency is influenced by many factors: ore grindability, feed size, grinding product size, ball mill diameter and length, ball mill working speed, liner type, steel ball loading system, grinding concentration, return sand ratio in closedcircuit grinding and feed rate (Ball mill) To improve the ball mill grinding efficiency, you must first understand the What Factors Will Influence Ball Mill Grinding Efficiency?2023年4月30日 Peripheral discharge ball mill, and the products are discharged through the discharge port around the cylinder According to the ratio of cylinder length (L) to diameter (D), the ball mill can be divided into short cylinder ball mill, L/D ≤ 1; long barrel ball mill, L/D ≥ 1–15 or even 2–3; and tube mill, L/D ≥ 3–5Ball Mill SpringerLink2024年5月17日 Once the mill load is measured, operators can adjust various factors to achieve the desired level: Feed rate: This refers to the amount of ore entering the mill Increasing the feed rate raises the mill load, while decreasing it lowers it Mill speed: The rotational speed of the mill significantly impacts the grinding actionA guide to SAG Mill management
.jpg)
The effects of ore blending on comminution behaviour and
2018年8月17日 The concept of ore blending is a very relevant notion in modern high tonnage production mines It is not only essential for the prolongation of the mine life of the concerned mine but as well as a