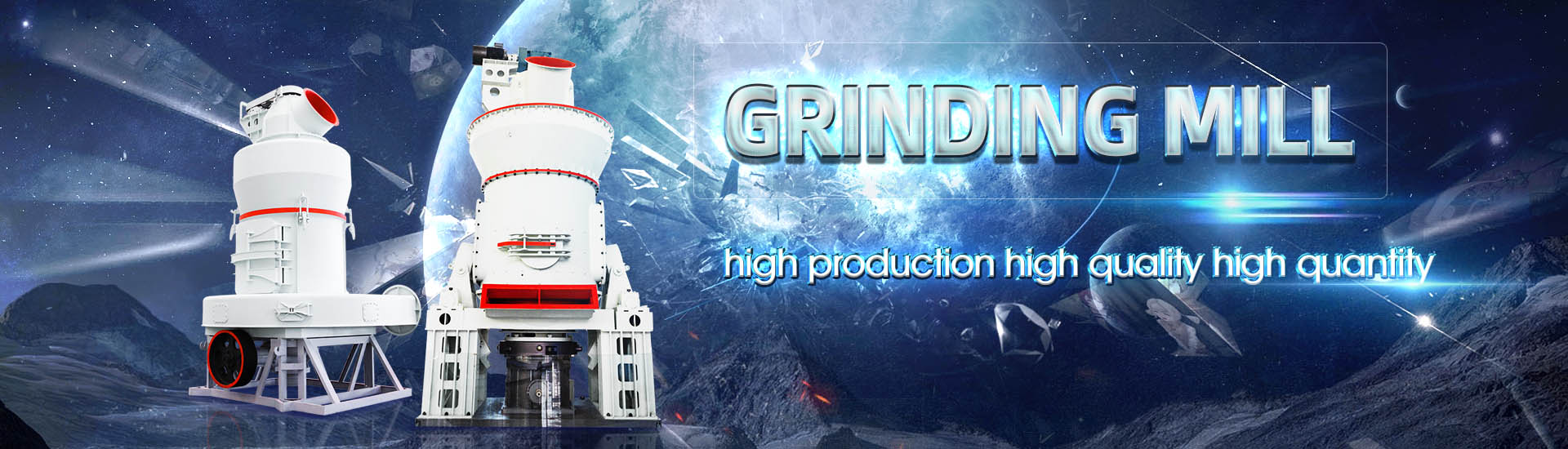
Material required for large coal mill manufacturing
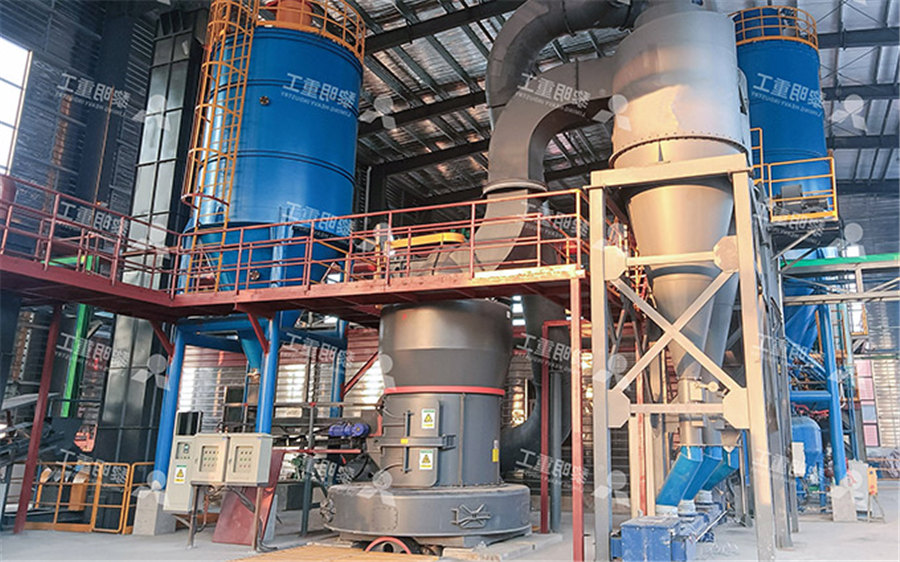
Raw materials Coking plant ArcelorMittal
In the coking plant, coal is heated in the absence of oxygen to 1250c This removes any impurities in the coal, resulting in coke, which is a porous substance that is nearly all carbon To make steel in a blast furnace, coal must first be turned into cokeBeneficiation produces two waste streams: fine materials that are discharged as a slurry to a tailings impoundment, and coarse material (typically greater than 05 millimeters (mm) that is Coal Mining and ProductionKey raw materials needed in steelmaking include iron ore, coal, limestone and recycled steel The two main steel production routes and their related inputs are: • The integrated steelmaking FACT SHEET Steel and raw materials2016年3月30日 In book: Encyclopedia of Iron, Steel, and Their Alloys (pppp 10821108) Chapter: i) Direct Reduced Iron: Production; Publisher: CRC Press, Taylor and Francis Group, New York(PDF) i) Direct Reduced Iron: Production
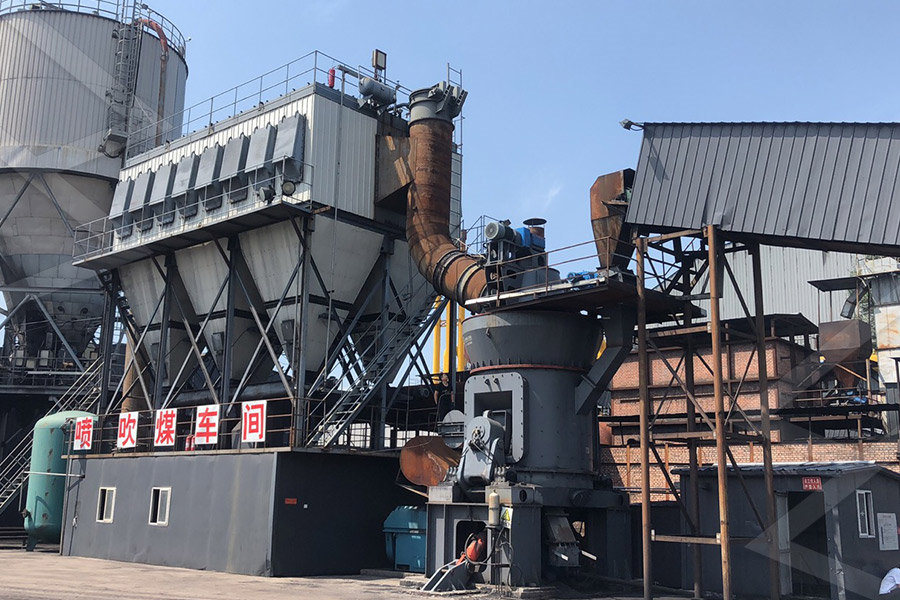
Cement Manufacturing Process INFINITY FOR
The principal raw materials for cement manufacturing are: Limestone; Silica and alumina from basalt , the raw material, required for production of PPC cement, is not available in Derba This material has to be transported by trucks from 2024年3月20日 At the forefront of these materials is iron ore, the primary ingredient and the backbone of steel production Coke, derived from coal, is another essential element, acting as a reducing agent to facilitate the Understanding the Steel Making Process: A Flow 2023年9月1日 The Effects of Chemical Elements on Steel Properties 1 Carbon (C): As the carbon content in steel increases, the yield point and tensile strength rise, but plasticity and impact resistance decrease When the carbon content exceeds 023%, the weldability of the steel deteriorates Therefore, for lowalloy structural steel used for welding, the carbon content Steel Production Process: The Comprehensive GuideMill liners can be made of various materials, including rubber, steel, and composite materials, and can be designed to match the specific grinding requirements of the coal material Mill Drives Mill drives are critical components of coal grinding mills, responsible for transmitting power from the motor to the grinding mediaWhat is a Coal Grinding Mill
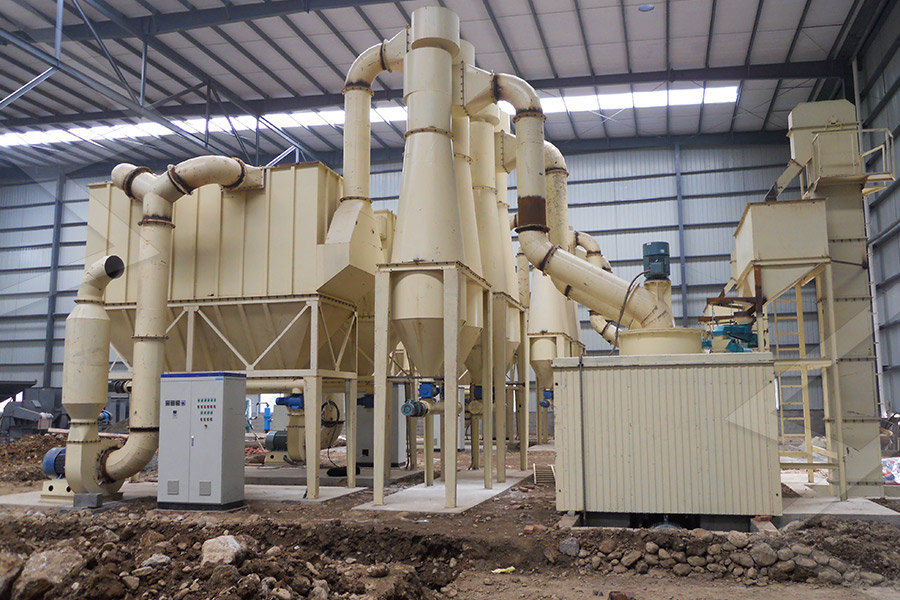
Emission reduction through process integration and exploration of
2023年1月7日 Like coal, basic raw materials required for clinker manufacturing also contain a small amount of nitrogen and during burning, it is emitted as NO x It is reported that the kiln feed raw materials also contain small amount of nitrogen, though the concentration of feed NO x to total NO x is very less (Mittal et al 2012) Pinch technologyLime Component Limestone: Common forms of calcium carbonate used as raw material for cement manufacturing are limestone and chalkLimestone is of predominantly fine grained crystalline structure, its hardness is between 18 to 30 of the Mohs scale of hardness and specific gravity 2 To 28 Limestone usually contains admixtures of clay substance or iron compounds, Raw materials for cement manufacturing Cement Plant 2022年4月6日 • For burning the kiln feed, pulverized coal is fed through the lower end of the kiln • Raw coal is ground in a coal mill (VRM/ball mill) to fine coal or pulverized coal • The hot materials coming out of the kiln are known as clinker • Clinker is in the form of nodules of various sizes, usually 125 mm in diameterFrom raw materials to 8 steps of cement manufacturing, read2012年11月17日 20 131Fineness Fineness is an indicator of the quality of the pulverizer action Specifically, fineness is a measurement of the percentage of a coal sample that passes through a set of test sieves usually designated at 50, 100, and 200 mesh A 70% coal sample passing through a 200 mesh screen indicates optimum mill performance The mill wear and Coal mill pulverizer in thermal power plants PPT SlideShare
.jpg)
Analysis of material flow and consumption in cement
2016年1月20日 As shown in Fig 11, 121 t of limestone, 581 t of air, and 040 t of other materials (silica, corrective materials, gypsum, fly ash, and coal) are required for manufacturing one ton of cement Meanwhile, 479 t of waste gases are discharged into the atmosphere, 151 t of high and lowtemperature gases are recycled to generate electricity, and 012 t of hot air is 2023年5月17日 If fine grinding is required, we may require additional machinery such as ball mills or roller mills Can a coal hammer mill be used for other materials besides coal? Yes, we can grind and pulverize every kind of material What Is Coal Hammer Mill? SBM Mill Crusher2020年6月15日 As shown in Fig 2, material flows present the dynamic movement and transformation of ironbearing materials [23], including iron ores, steel scrap, hot metal, liquid steel, cast slabs, finished steel, etc Energy flows include coke, coal, blast furnace gas (BFG), coke oven gas (COG), Linz–Donawitz converter gas (LDG) or BOF gas, power, water, steam, Material and energy flows of the iron and steel industry: Status Homepage /; About Making steel Steel is made from iron ore, a compound of iron, oxygen and other minerals that occurs in nature The raw materials for steelmaking are mined and then transformed into steel using two different Making steel ArcelorMittal
.jpg)
COAL PREPARATION AND FIRING INFINITY FOR CEMENT EQUIPMENT
Previous Post Next Post Contents1 COAL PREPARATION AND FIRING11 INTRODUCTION12 2COAL RESERVES13 CHARACTERISATION OF COALS BY CHEMICAL131 31 Major components132 32 Minor Components14 4CHARACTERISATION BY PHYSICAL AND MECHANICAL PROPERTIES141 41 Coal Storage142 42 Variation of Physical and For example, in a direct fired coal mill system if the moisture content of the coal drops, the kiln will get more tons of dry coal at the same setting on the raw coal feeder Changes in the percentages of coal versus coke, for a kiln firing both fuels simultaneously, will also affect the CO and O2 levelEverything you need to know about Kiln System Operations in 2022年5月19日 Following the international climate change policy and the major use of coalbased blast furnace–basic oxygen furnace (BF–BOF) in the steel sector, with an average emission of 20 t CO2/t steel, alternative processing routes must be considered to reduce the emission intensities An approach of progressive amalgamation with alternative gas and Climate Change and Emission Reduction Pathways for a Large Coal Moisture: The degree of drying, and therefore the required mill outlet temperature (from 6580 0 C) will depend upon the type of coal ground Some residual moisture in fine coal is recommended (Graph below) to minimize the potential of spontaneous ignition of fine coal, which will again vary for different coal types as below:Coal Grinding Cement Plant Optimization
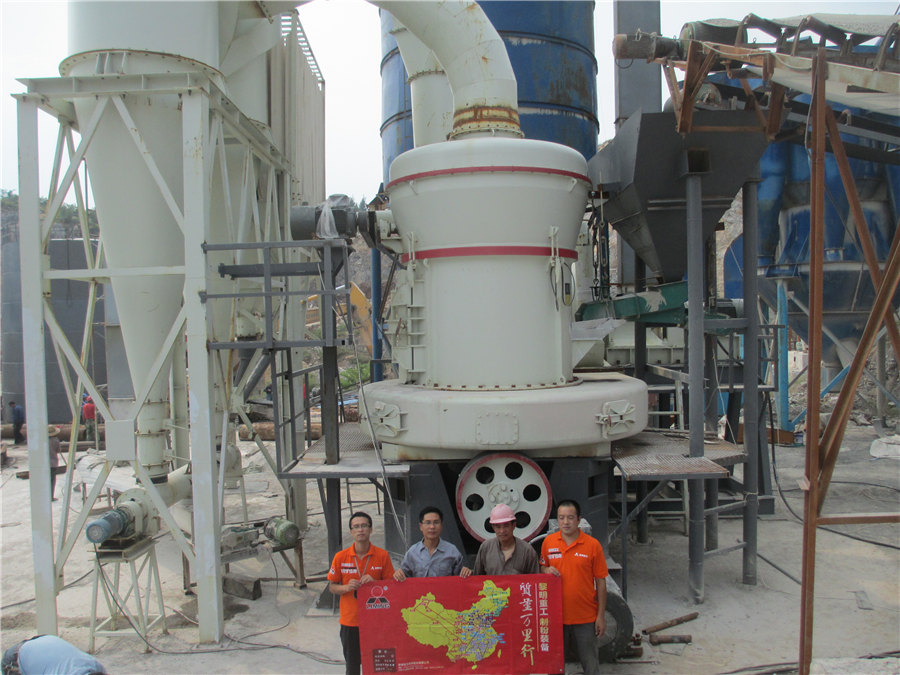
Raymond Bartlett Snow Milling Technologies Specialized
various materials such as iron ore, coal and additives Raymond Bartlett Snow Raymond Bartlett Snow India Operations have indigenized mill component‟s manufacturing to a large extent in line with “Make in India initiatives” and are committed to No complex adjustments required for grinding various types of material andfineness2016年3月1日 Similarly, in October 2014, Misr Beni Suef Cement announced plans to build a US$279m coal mill by the end of 2015 Next, in November 2014, Titan Cement ordered a Gebr Pfeiffer SE type MPS 2800 BK vertical roller mill for coal Coal for cement: Present and future trendsThe ball mill is a traditional coal pulverizer machine, which has been widely used since it was invented In the cement plant, the new dry process cement manufacturing requires the moisture content of coal powder to be 05% ~ 15%, while that of raw coal is 15% ~ 40%Coal Mill in Cement Plant6 Construction and Maintenance of Belt Conveyors for Coal and Bulk Material Handling Plants practicalmaintenance also oscillating horizontally This phenomenon results in internal agitation to the material on belt and therefore the material’s external faces assume inclination at surcharge angleConstruction and Maintenance of Belt Conveyors for Coal and
.jpg)
Cage Mill Crushers Industrial Pulverizing Equipment
Stedman’s range of multicage mills and pulverizers includes the HSeries, FSeries for sticky, high moisture and YSeries designed for less abrasive material applications In general, the larger the pulverizer, the larger the feed size it will 2021年3月19日 The current dependency on steel within modern society causes major environmental pollution, a result of the product’s life cycle phases Unfortunately, very little data regarding single steel Life Cycle Assessment of an Integrated Steel Mill Using 2013年3月1日 Request PDF Datadriven modeling and simulation framework for material handling systems in coal mines In coal mining industry, discreteevent simulation has been widely used to support Datadriven modeling and simulation framework for material handling Thanks to a bed material grinding concept, the vertical FCB Emill offers power consumption reduced by 50% compared to the ball mill for coal grinding Customer benefits Low power consumption Low noise level Low maintenance Constant product quality Technical advantages Long life of grindingBall mill FCB Emill Fives vertical / for coal grinding
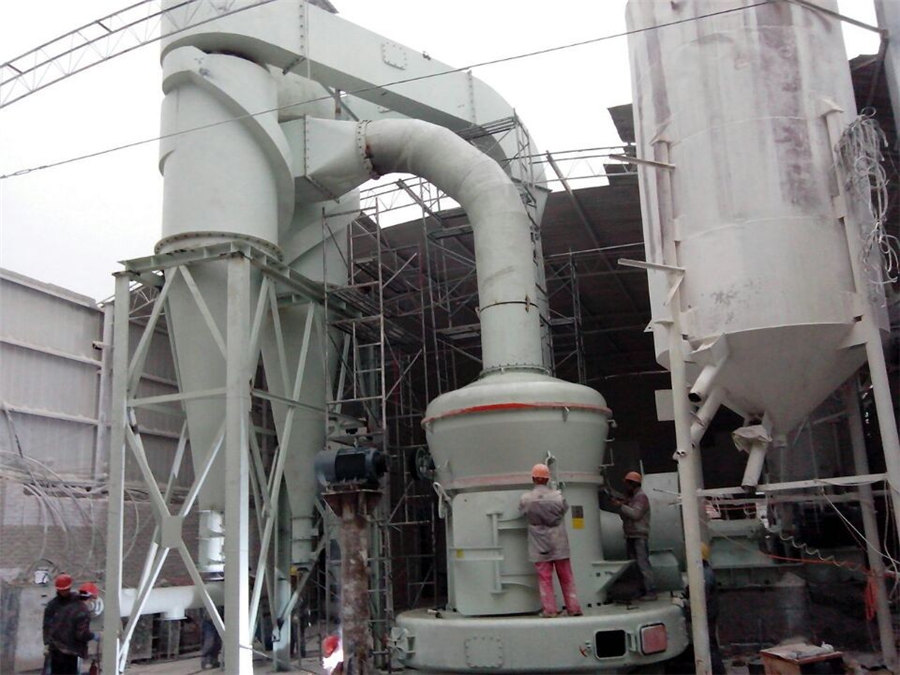
Ball Mill Grinding Media Steel Balls for Ball Mills AGICO Group
The length of steel bars should be 50100 mm shorter than that of the mill chamber Grinding Media Material The grinding media in the ball mill is required to have great wear resistance and impact resistance The material to make the grinding 2015年8月1日 The material efficiency values for a raw mill, pyroprocessing tower, large mate rial coal) are required for manufacturing one ton of cement(PDF) Analysis of material flow and consumption inStage of Cement Manufacture There are six main stages of the cement manufacturing process Stage 1: Raw Material Extraction/Quarry The raw cement ingredients needed for cement production are limestone (calcium), sand and clay (silicon, aluminum, iron), shale, fly ash, mill scale, and bauxite The ore rocks are quarried and crushed into smaller pieces of about 6 inchesHow Cement is Made Cement Manufacturing Process2013年3月13日 Ultimately, we face fundamental thermodynamic as well as practical constraints on our ability to improve the energy intensity of material production A strategy to reduce demand by providing material services with less material (called ‘material efficiency’) is outlined as an approach to solving this dilemmaThe energy required to produce materials: constraints on energy
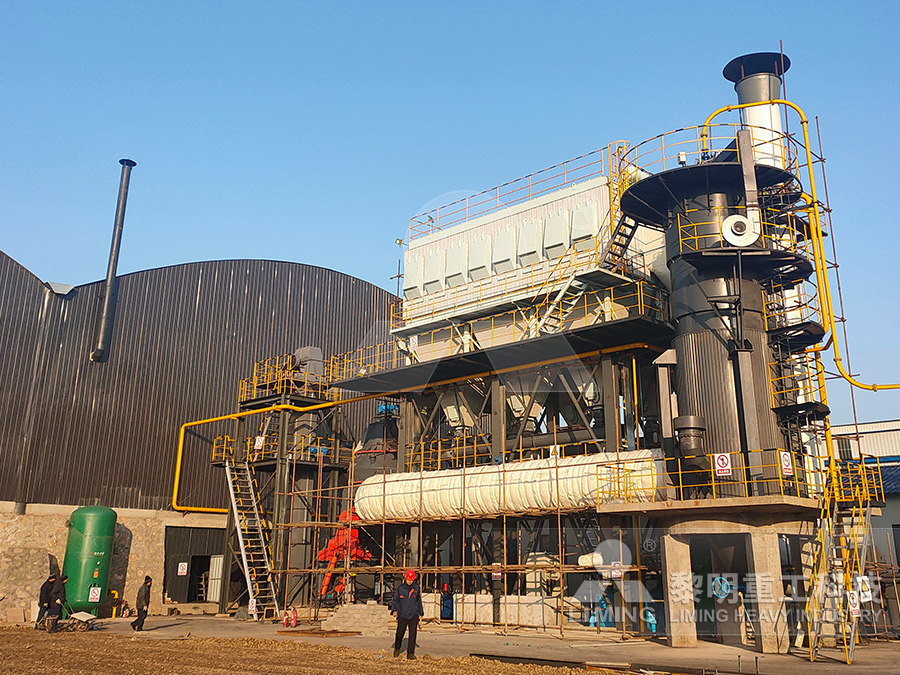
Case Study – Coal Mill Rejects Handling System for PF Boiler
The pneumatic cylinder operated plate valve at mill outlet (Pyrite Hopper Inlet) is normally kept open Mill Rejects from coal mill drop into the Pyrite Hopper through the grid Oversized material is retained on the grid Manual Operated Plate Valve on Oversize material discharge chute is operated on need basis2023年12月20日 Cement operators also use these analysis systems to analyze and adjust the coal mix instream, which enables the plant to reduce energy consumption by using exactly the amount of coal fuel required to meet the The Cement Manufacturing Process Thermo Fisher The MPS ZGM coal mill is a type of coal mill that operates at a speed of 50300r/min This equipment is used to prepare and process auxiliary materials for blast furnace ironmaking It provides suitable coal powder for the blast MPS ZGM Coal MillGrinding Equipment YingYong 2022年1月1日 The use of nonrenewable resources such as coal, oil, gas, and uranium is expected to decrease by 432% in 2050 worldwide compared to the 2019 level (DNVGL, 2020)The total amount of wind, solar, geothermal, and hydropower should increase by 5517% by 2050 (DNVGL, 2020)Today, wind energy represents 5% of all electricity generated globally, Material consumption and environmental impact of wind turbines
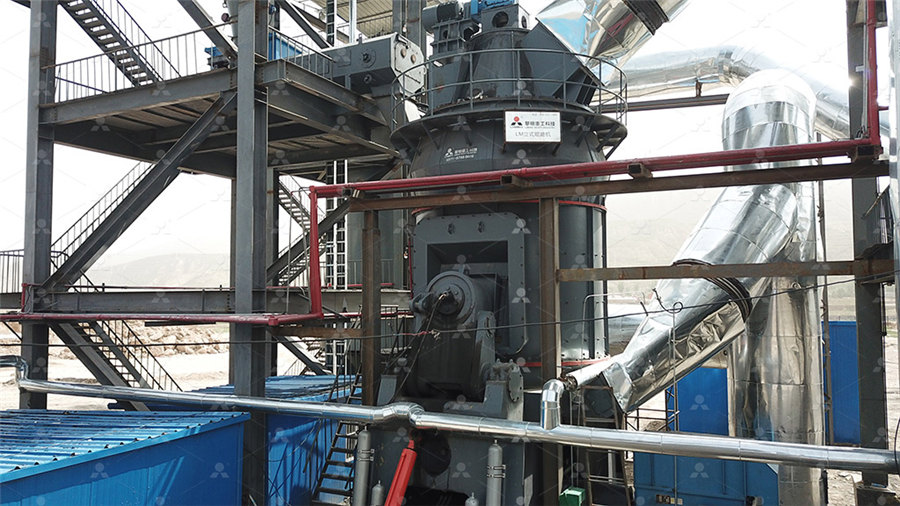
Steel manufacture SteelConstructionfo
The coal is heated, or ‘carbonised’ in the ovens until it becomes coke It is then removed from the oven, cooled and graded before use in the blast furnace The coal gas produced during carbonisation is collected and used as a fuel in the manufacturing process while byproducts such as tar, benzole and sulfur are extracted for further refining2023年1月1日 Most coal mill designs are based upon a 50–55 HGI design point However, grindability is a complex issue and factors such as coal moisture content and required fineness (high volatile coals can require a coarser grind), along with the milling and burner systems are all factors in assessing coal grindabilityCoal utilization in the cement and concrete industries5 天之前 The manufacture of Portland cement is a complex process and done in the following steps: grinding the raw materials, mixing them in certain proportions depending upon their purity and composition, and burning them to sintering in a kiln at a temperature of about 1350 to 1500 ⁰C During this process, these materials partially fuse to form nodular shaped clinker by Manufacturing of Portland Cement – Process and MaterialsThe US wind market has grown substantially over the years into an increasingly complex supply chain There are more than 500 US manufacturing facilities specializing in wind components such as blades, towers, and generators, as well as turbine assembly across the countryWind Manufacturing and Supply Chain Department of Energy
.jpg)
The Division of Air Quality (DAQ) received a copy of NCgov
2014年3月4日 mill, coal mill, and clinker cooler system that will vent through a common main stack Production is limited in the permit to 2,190,000 tons per year of clinker The fuels burned at this facility will be coal and petroleum coke with distillate fuel oil used for startup The raw materials for clinker production will include2024年5月21日 I always thought that coal is “only” important for electricity, contributing to 36% of global power demand, or over 8h of 24h every single day of the year I always thought that coal is “only” required to produce all steel Let us have a look at solar panel manufacturing, which is really about silicon productionCoal’s Importance for Solar Panel Manufacturing CO2 Coalitionof the roller mill Adjustable nozzle ring The gas required for transporting and drying the material inside the mill flows through the nozzle ring The gas distribution and velocity can be optimally adjusted to suit the required material loading or drying capacity, thus minimising the specific gas flow rate and the pressure drop in the grinding Polysius Roller Mills For grinding