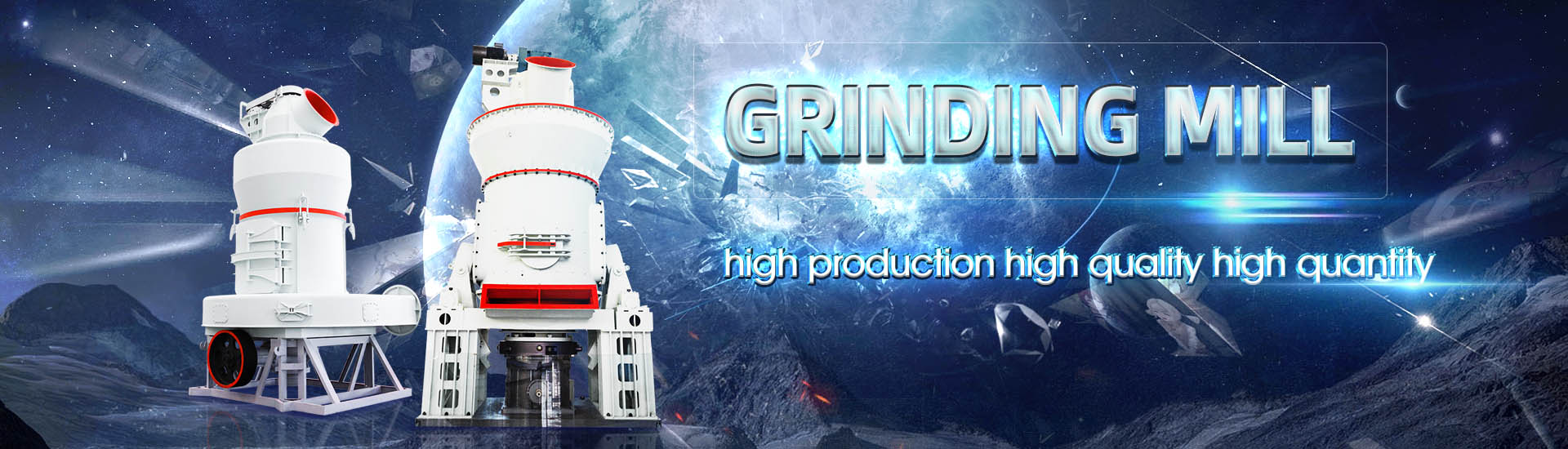
Blast furnace method to produce sulfur
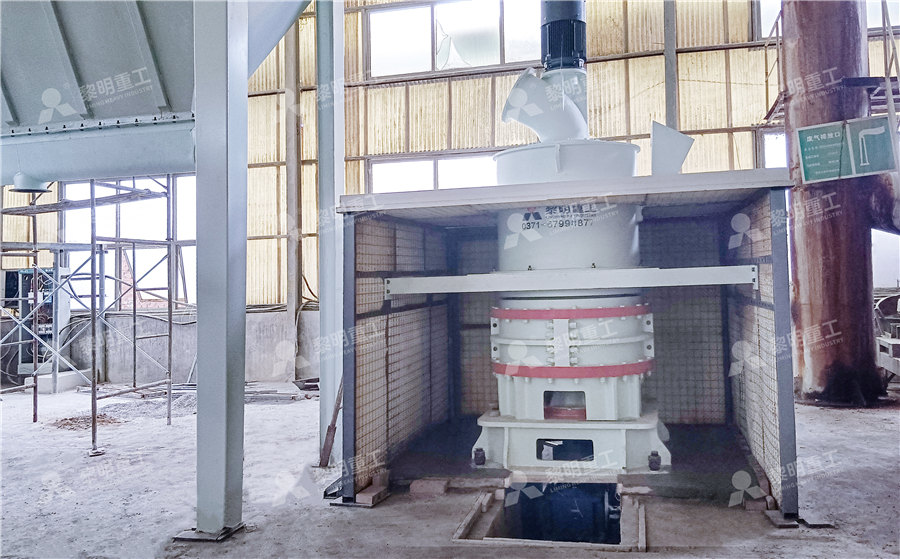
Blast Furnace Process an overview ScienceDirect Topics
The blast furnace is a tall, vertical shaft furnace which has the purpose of heating and reducing iron oxides (hematite and magnetite) into hot metal which is basically a carbonsaturated 2023年12月15日 Understanding the transformation behavior of sulfides in the blast furnace raw materials during the ironmaking process is crucial for controlling the form and emission of Reaction behavior of sulfides in blast furnace raw materials under 2022年6月1日 This article clarifies main sources and forms of sulfur in blast furnace gases Then, COS/H2S removal methods that are commonly used are introducedA Review on Desulfurization Technologies of Blast The behavior of sulfur in the blast furnace depends to a considerable extent on temperature conditions; there fore, the change in concentration of sulfur in the solid, liquid, and gaseous The behavior of sulfur in the process of blastfurnace smelting
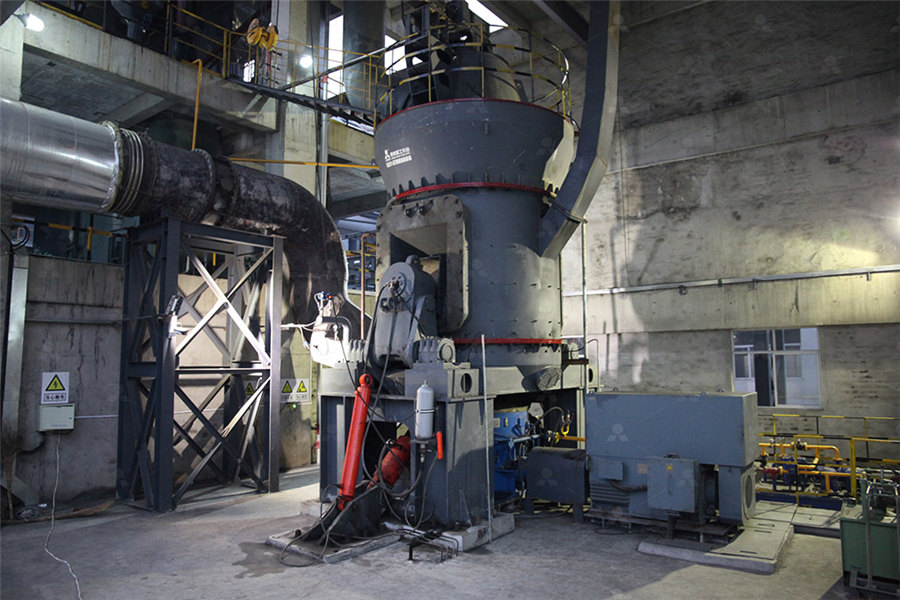
A Review on Desulfurization Technologies of Blast Furnace Gases
2022年3月29日 This article clarifies main sources and forms of sulfur in blast furnace gases Then, COS/H2S removal methods that are commonly used are introduced In fact, blast 2023年9月18日 A carbonyl sulfide (COS) hydrolysis catalyst can play an efficient role in blast furnace gas (BFG), but the life of the catalyst is greatly shortened due to the presence of O2 and H2S in the atmospHydrolysis of Carbonyl Sulfide in Blast Furnace Gas 2016年12月13日 Sulfurrelated problems in the blast furnace were studied by applying a balance equation for the element at three industrial blast furnaces, tracking errors in the in and Datadriven Analysis of Sulfur Flows and Behaviour in the Blast 2023年4月4日 Carbonyl sulfide (COS) causes issues with blast furnace gas (BFG) treatment due to its unique physical and chemical properties Here, we review the sources of COS in Research progress on adsorption and separation of carbonyl
.jpg)
Simplified sulfuriodine cycle process to hydrogen blast furnace
2022年6月25日 The sulfuriodine (SI) cycle has high potential as the H 2 source for ironmaking plants It utilizes the heat from nuclear plants to produce massive quantities of H 2 (Brown, 2011)The process is a promising H 2production method for a fullyfluidized process that produces no CO 2 with high heat efficiency (∼40%) and low unit production cost (∼20 US$ kg The blast furnace is the first step in producing steel from iron oxides The first blast furnaces appeared in the 14th century and produced one ton per day Even though equipment is improved and higher production rates can be achieved, Steel Production American Iron and Steel InstituteExperience and lessons learned Michele Laraia, in Beyond Decommissioning, 2019 6224 Blast furnaces “A blast furnace is a large structure in which iron ore is heated under pressure so that it melts and pure iron metal separates out and can be collected “(Collins Dictionary) The heritage value of blast furnaces built before 1900 has been recognized already for a long time, and Blast Furnace an overview ScienceDirect Topics2020年9月25日 Catalytic performance and reaction mechanism of an ironloaded catalyst derived from blast furnace slag for the COSO 2 reaction to produce sulfur Author links open overlay panel Wen Ren, Ping Zhou, Yeshun Tian, sulfur dioxide catalytic reduction is a promising method to mitigate sulfur dioxide pollution while transforming waste Catalytic performance and reaction mechanism of an iron
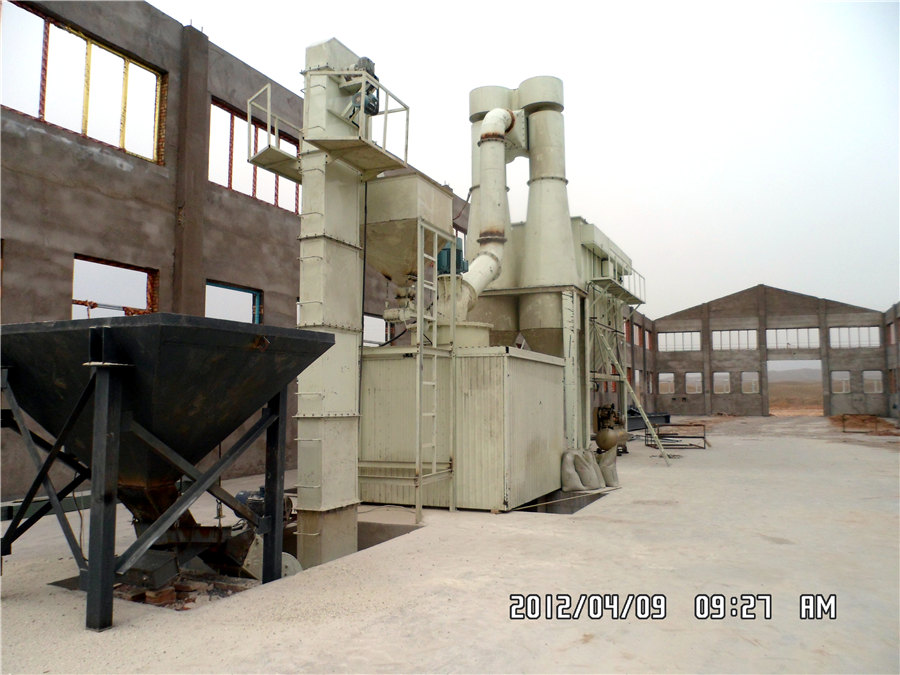
Research progress of carbonyl sulfide removal from blast furnace
2023年6月1日 Recently, desulfurization process methods by AC can divid into adsorption method, adsorption oxidation method, and catalytic oxidation method [47] Qiu et al [48] developed Cu 2 (OH) 2 CO 3 CoPcSKOH modified AC as a sorbent for COS removal, which could remove COS at 60 °C, 30% relative humidity and 10% oxygen, with a penetration sulfur 2020年8月19日 Blast furnaces able to produce 12,000 tons of pig iron per day have been built, and they had a hearth, in the zone of tuyeres, of 14 m (maximum at the beginning of the twentyfirst century for the blast furnace) In the last years, alternative processes to the sequence blast furnace–converter used to produce steel have been developedProduction of Iron in the Blast Furnace SpringerLink2017年10月10日 In the upper region of the blast furnace where temperature range from 600 to 700 C the iron ore or iron oxide is reacts with the gaseous CO reductant to produce iron: Fe 2 O 3 (s) + 3CO(g) → 2Fe + 3CO 2 (g) Lower in the blast furnace where higher temperatures occur, the iron ore may react directly with the coke or carbon:Ironmaking 101 – From Ore to Iron with Blast Furnaces2022年11月1日 Carbonyl sulfide (COS), also called carbon oxysulfide or carbon monoxide monosulfide, is the most abundant reduced sulfur trace gas found in the atmosphere (Zumkehr et al, 2017; Renda et al, 2022)It is well documented that COS forms sulfate aerosol particles through chemical reactions in the stratosphere and troposphere, adversely affecting the Carbonyl sulfur removal from blast furnace gas: Recent progress
.jpg)
Blast Furnace Ironmaking ScienceDirect
Blast furnace iron has limited engineering applications It is mainly for use for iron castings, and for abrasion resistance and heattransfer applications Most blast furnace iron is the raw material for oxygen steelmaking, where the molten iron is refined to produce the world’s most popular metal for engineering applications—rolled steelA blast furnace is a steel cylinder lined with refractory It operates continuously until the lining wears out, which takes many years to occur The term blast furnace comes from the blast of hot air that is blown into the lower part of the furnace at between 1400º to 2100ºF Molten iron is produced in a blast furnace by the following steps: 1Blast Furnace Process Steel Museum2023年10月6日 The smelting process of blast furnace is carried out in the shaft furnace of a closed countercurrent reactor and heat exchanger The complex physical changes and chemical reactions are completed in the process of the countercurrent movement of the charge and gas in which the raw materials containing iron oxide (sinter, pellets, etc), coke, slag flux (limestone) Blast Furnace Ironmaking SpringerLinkThe carbon monoxide in the blast furnace reduces the iron(III) oxide in the hematite ore to produce molten iron Iron ores contain a large amount of sandy impurities These impurities are removed from the blast furnace when they react with calcium oxide compoundsLesson Explainer: Extracting Iron Nagwa
.jpg)
Iron processing Smelting, Refining, Alloying Britannica
Iron processing Smelting, Refining, Alloying: Most blast furnaces are linked to a basic oxygen steel plant, for which the hot metal typically contains 4 to 45 percent carbon, 06 to 08 percent silicon, 003 percent sulfur, 07 to 08 Reactors in Process Engineering Gary L Foutch, Arland H Johannes, in Encyclopedia of Physical Science and Technology (Third Edition), 2003 IVB Blast Furnace IVB1 Description The blast furnace, a vertical shaft kiln, is the oldest industrial furnaceReactant enters in the top of the shaft and falls down through a preheating section, a calcinating section, past oil, gas, or Blast Furnace an overview ScienceDirect TopicsUsing recycled heat from the blast furnace, outside air is heated to 1,000°C – 1,200°C in the heat exchanger of the hot blast stove This hot blast air is blown in through pipes called tuyeres at the bottom of the blast furnace and heats the three key ingredients to start the chemical reactions needed for ironmaking Additional fuels such What is a Blast Furnace? Reibus International2020年9月1日 Request PDF Catalytic performance and reaction mechanism of an ironloaded catalyst derived from blast furnace slag for the COSO2 reaction to produce sulfur For realizing resource Catalytic performance and reaction mechanism of an iron
.jpg)
Mathematical Modeling of the Blast Furnace Process
during blast furnace melting, and its application to the study of processes determining the recovery of metals from multicomponent ores The analytical method to investigate the blast furnace process is developed and applied practically This The invention discloses a blast furnace gas desulfurization and sulfur resource utilization method and device, and belongs to the field of energy conservation and environmental protection The methodcomprises the following steps that: (1) 80180DEG C hot coal gas generated by a blast furnace is dedusted and purified, the purified coal gas isintroduced into a COS conversion d Blast furnace gas desulfurization and sulfur resource utilization 2023年1月31日 The sulfur content of hot metal in a blast furnace is an important index that reflects the production effects and quality of the hot metal Establishing an accurate prediction model for hot metal Predictive Modeling of the Hot Metal Sulfur Content in a Blast Furnace 2024年1月1日 Modern smelting copper blast furnace was mostly used for treating agglomerate and the concentration of fume SO 2 was low In the 1950s, it was changed to treating kneading concentrate and some block materials, and with material sealing the top of the furnace, which increased the concentration of fume SO 2, the sulfur in the concentrate was utilized wellBlast Furnace SpringerLink
.jpg)
Reclaiming Tibearing blast furnace slag into widetemperature
Reclaiming Tibearing blast furnace slag into widetemperature and sulfur (NO 3) 2 and Mn(NO 3) 2 to produce doped TFBS derivatives Then, effects of Ce and Mn doping as well as their catalysts synthesized in this study were compared with that of stateoftheart counterparts fabricated via routine methods, including Mn and Ce 2024年9月12日 In this paper, a novel process for synergistic carbon in situ capture and the utilization of blast furnace gas is proposed to produce CO via chemical looping Through thermodynamic analysis, this process was studied Thermodynamic Feasibility of Chemical Looping CO 2024年6月15日 Blast furnace (BF) ironmaking properties along the height inside the BF and examined the effects of variations in coke properties and BF operational methods on furnace conditions, as depicted in Fig 10 leading to gasification and dissolution reactions that produce reducing gases such as CO and H 2Physical and chemical properties of metallurgical coke and its 2024年1月1日 Charcoal or coal as fuel was used in the early blast furnace and was replaced by coke in the eighteenth century, and cold air was changed to hot air in the middle of the nineteenth century (see “History of Metallurgy”)At the beginning of the twentieth century, the blast furnace ironmaking developed rapidly after the use of gas internal combustion engine blower and Blast Furnace Ironmaking SpringerLink
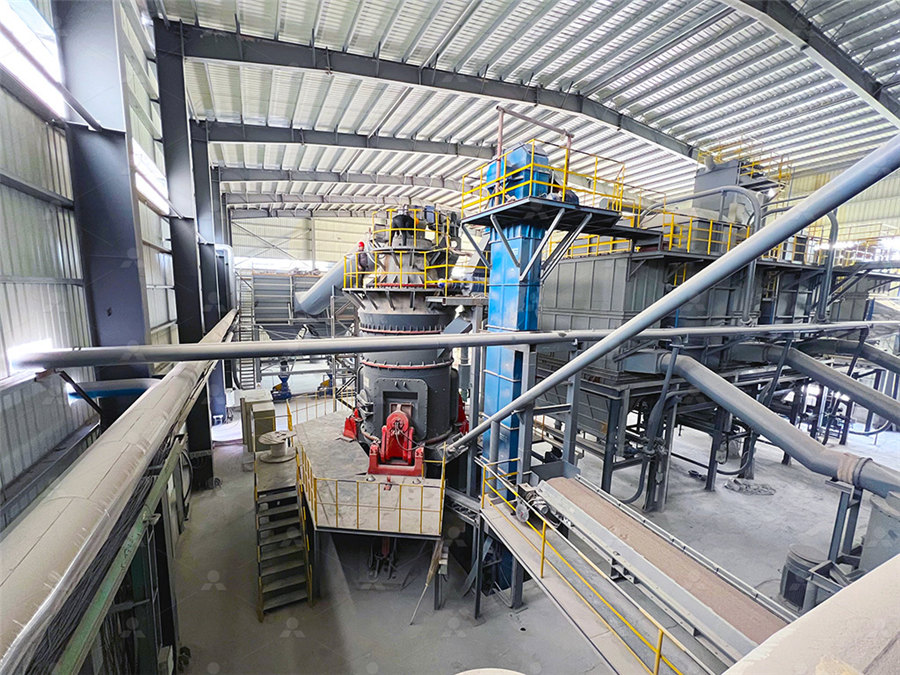
233: Metallurgy of Iron and Steel Chemistry LibreTexts
Impurities in the iron from the Blast Furnace include carbon, sulfur, phosphorus and silicon, which have to be removed Removal of sulfur: Sulfur has to be removed first in a separate process Magnesium powder is blown through the molten iron and the sulfur reacts with it to form magnesium sulfide2019年7月2日 Modern blast furnace ironmaking technology: Comparison between the conventional charging method and coke mixed charging method sintering process to produce PRA as can be seen i n Fig 7 [58]Modern blast furnace ironmaking technology: potentials to 2023年7月23日 Blast furnaces are chemical metallurgical reactors used to produce hot metal and blast furnace slag Hot metal is obtained in liquid state and AF, Iskhakov, II, Skopov, GB, Kirichenko, AN: Using oxygenenriched blast during the operation of shaft furnaces of the Mednogorsk CopperSulfur combine LLC Metallurgist 63, 62 Data Mining and Machine Learning to Predict the Sulphur Content A key component of the lowtemperature blast furnace operation is to reduce the fuel rate significantly by lowering operating temperatures by 150–200 °C particularly in the thermal reserve zone [43]Consequently, the kinetics of the major blast furnace reactions must be increased so that production rates at lower operating temperatures are the same as for the traditional Blast Furnace Operation an overview ScienceDirect Topics
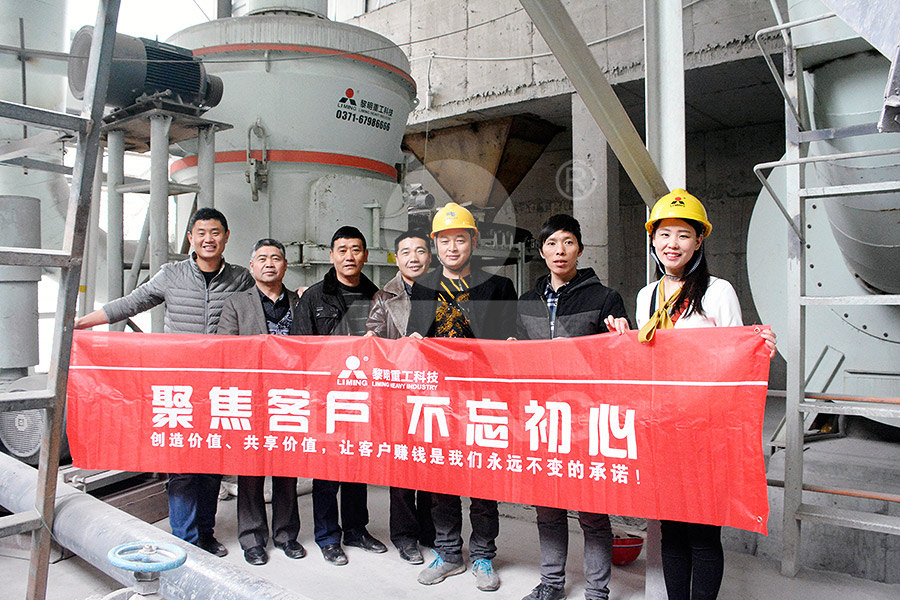
Simplified sulfuriodine cycle process to hydrogen blast furnace
2022年6月25日 The sulfuriodine (SI) cycle has high potential as the H 2 source for ironmaking plants It utilizes the heat from nuclear plants to produce massive quantities of H 2 (Brown, 2011) The process is a promising H 2production method for a fullyfluidized process that produces no CO 2 with high heat efficiency (∼40%) and low unit production cost (∼20 US$ kg H2 −1) The Blast Furnace The heat source The air blown into the bottom of the furnace is heated using the hot waste gases from the top At the high temperature at the bottom of the furnace, carbon dioxide reacts with carbon to produce IRON AND STEEL chemguide2020年1月15日 This method works by removing the CO 2 from the BFG and then recycling the CO 2depleted BFG back into the blast furnace [27], [28] The Linde Group has developed a PSA system that features a unit capacity of up to 300,000 Nm 3 /h and the ability to achieve a product purity of 95 vol% [29] Technoeconomic analysis of coke oven gas and blast furnace 2022年3月30日 While these twostep blast furnace gas desulfurization processes are mature, they also have some significant disadvantages First, the catalysts used for COS hydrogenation or hydrolysis use expensive metal oxides such as Al 2 O 3 as a carrier Second, the temperature of blast furnace gas often decreases below 100 °C after passing through the top gas recovery Efficient removal of carbonyl sulfur and hydrogen sulfide from blast
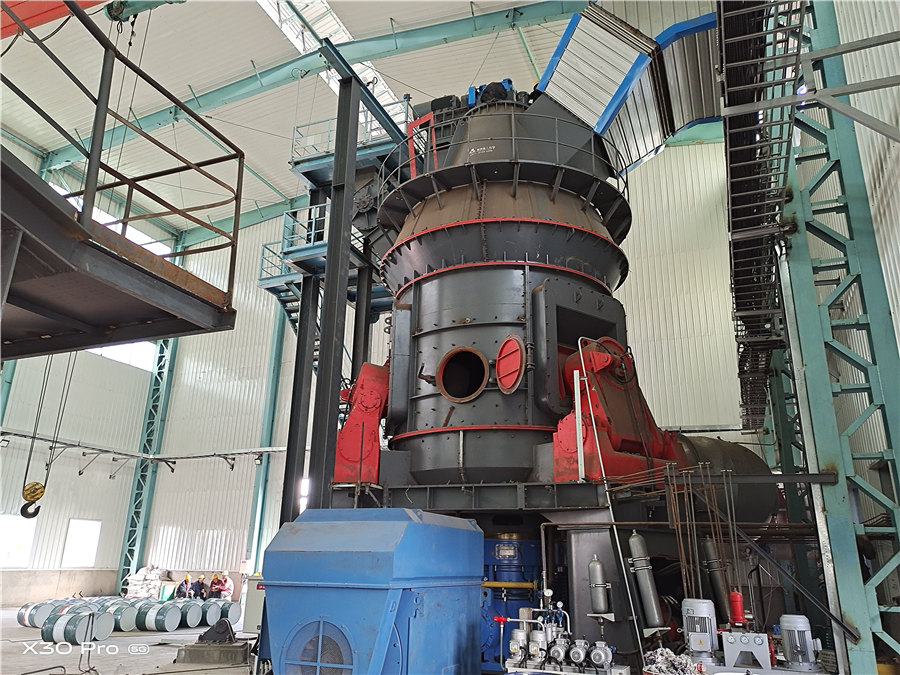
Recent Trends in the Technologies of the Direct Reduction and
2023年4月5日 These methods include the Blast furnace/Blast Oxygen Furnace [5, 6], Direct Reduction Method , Indirect Reduction Method [8, 9], and ReducerSmelter Process [10, 11, 12] Thus, it is, therefore crucial to know that this processing technique has proven to have produced quality iron but not without a high cost of production, increased environmental pollution, and 2022年2月11日 Relative change of passage time (left) and frequency (right) as a function of binder type and number of cycles (SHsodium hydroxide activated blast furnace slag; SWGsodium water Figure parison of Testing Methods for Evaluating the Resistance of Iron oxide ore and coke are used in a blast furnace to produce pig iron at the bottom of the furnace and molten slag on top of molten iron The molten slag usually consists of silica and alumina which combine with lime and magnesia from the added limestone into the furnace Small amounts of manganese and sulfur areChapter 3 Granulated Blast Furnace Slag SpringerA blast furnace is a block that smelts ores, raw metals and metal armor and tools twice as quickly as a furnace but cannot smelt anything else It also serves as an armorer's job site block A blast furnace can be picked up using any pickaxe If mined without a pickaxe, it does not drop Blast furnaces drop their contents when broken Blast furnaces can generate in any armorer house; Blast Furnace – Minecraft Wiki
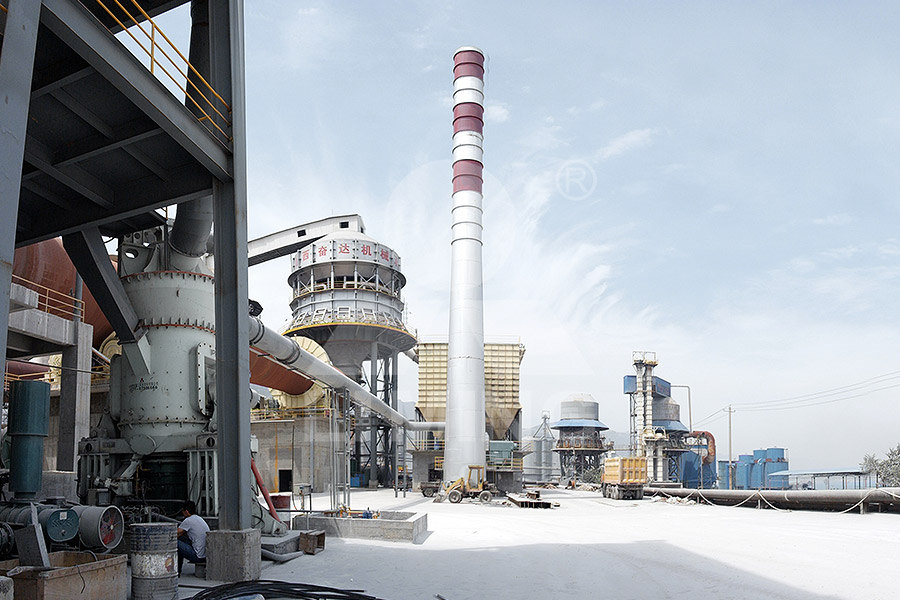
Ironmaking ScienceDirect
2014年1月1日 This blast furnace process is the oldest but still the main method to produce large quantities of molten raw iron, One such large blast furnace can produce 10,000 The total input of sulfur into blast furnaces is typically 25–35 Iron Extraction Manufacturing Process Blast Furnace Method Iron is extracted from different ores exist in the world Hematite (Fe 2 O 3) is reduced to iron metal in the blast furnace under several steps Limestone and coke are used as other Iron Extraction Manufacturing Process Blast Furnace Method2013年6月23日 Automatic process control improves the furnace productivity since it minimize consumption of reductant, avoids furnace process disturbances such as hanging, slipping, scaffolding, gas channeling etc through an immediate counteraction by the system, stabilizes hot metal and slag parameters etc the effect of automatic process control on the blast furnace Blast Furnace Productivity and the Influencing Parameters