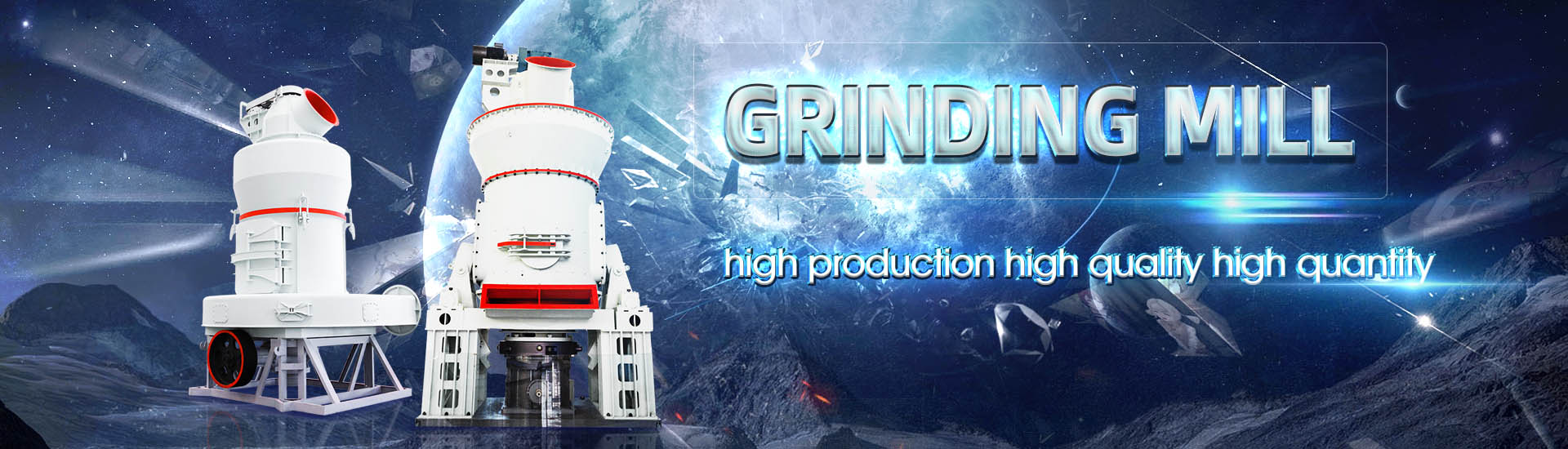
Ore sintering ore mill
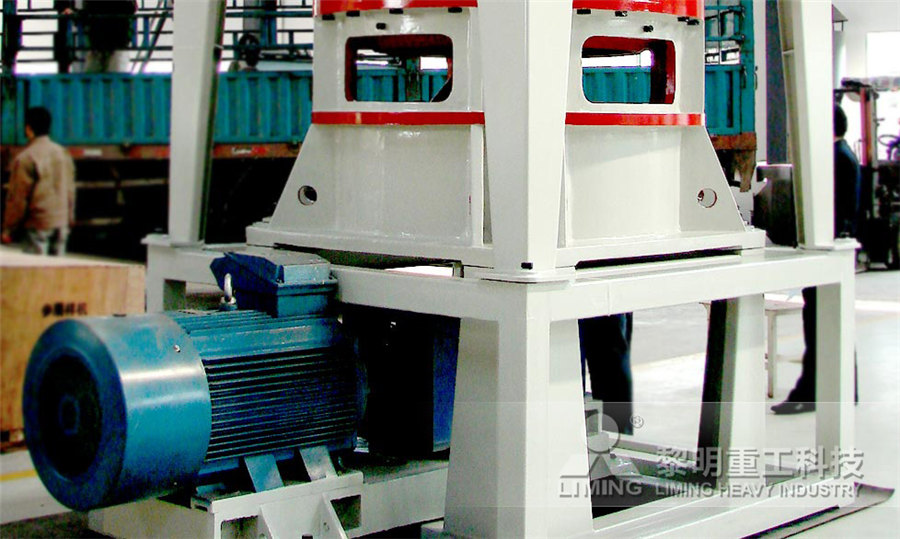
Sinter plant Wikipedia
Sinter plants agglomerate iron ore fines (dust) with other fine materials at high temperature, to create a product that can be used in a blast furnace The final product, a sinter, is a small, irregular nodule of iron mixed with small amounts of other minerals The process, called sintering, causes the constituent 展开2017年2月16日 Sintering is a thermal agglomeration process that is applied to a mixture of iron ore fines, recycled ironmaking products, fluxes, slagforming (PDF) Iron Ore Sintering: Process ResearchGateThe sintering process begins with the preparation of a sinter mixture consisting of iron ore fines, fluxes, solid fuel (called bonding agents in Japan) such as coke breeze, and return fines from Ore Sintering an overview ScienceDirect Topics2017年3月24日 Sintering is a thermal agglomeration process that is applied to a mixture of iron ore fines, recycled ironmaking products, fluxes, slagforming agents, and solid fuel (coke) The Iron Ore Sintering: Process Taylor Francis Online
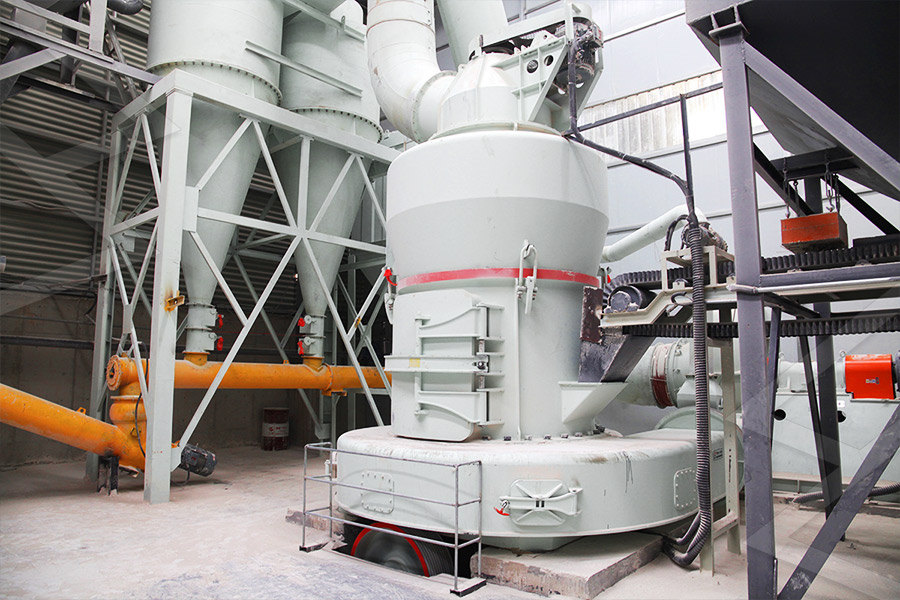
Sintering: A Step Between Mining Iron Ore and
2019年6月11日 According to the US Environmental Protection Agency, the sintering process converts finesized raw materials, including iron ore, coke breeze, limestone, mill scale, and flue dust, into an agglomerated product, 2022年1月1日 Sintering is the most economic and widely used agglomeration process to prepare iron ore fines for blast furnace use In this chapter, the sintering process is first Iron ore sintering ScienceDirect2016年9月1日 Sintering is the most economic and widely used agglomeration process to prepare iron ore fines for blast furnace use Owing to the depleting reserves of traditional high grade iron ore, there have been considerable Recent advances in iron ore sintering L Lu, O2016年8月24日 Sintering is the most economic and widely used agglomeration process to prepare iron ore fines for blast furnace use Owing to the depleting reserves of traditional high grade iron ore, there have been considerable Recent advances in iron ore sintering Taylor Francis
.jpg)
Treatment of steel rolling sludge incineration slag via iron ore
1 天前 The sintering pot experiment is a standard laboratory method for simulating the sintering process in steel plants It involves using a sintering pot experiment with dimensions of 200 mm 2012年4月1日 Ironrich (65 to 70 pct total Fe) mill scale generated during processing by steel mills can be recycled by using it as a ferrous raw material in the sintering process The effect Recycling of steel plant mill scale via iron ore sintering plant2015年1月1日 Like other sintering processes, iron ore sintering converts iron ore fines of often − 8 mm sizing into larger agglomerates, namely, sinter, between 5 and 50 mm particle size, which possess the physical and metallurgical characteristics and gas permeability required for efficient blast furnace operationAs shown in Figure 141, iron ore sintering is carried out in three Iron ore sintering ScienceDirect2009年8月1日 Mill scale is a valuable ferrous raw material, containing 65 to 70 pct iron [2] and is often recycled through the sintering process [3] During iron ore sintering, iron ore fines are mixed with Recycling of steel plant mill scale via iron ore ResearchGate
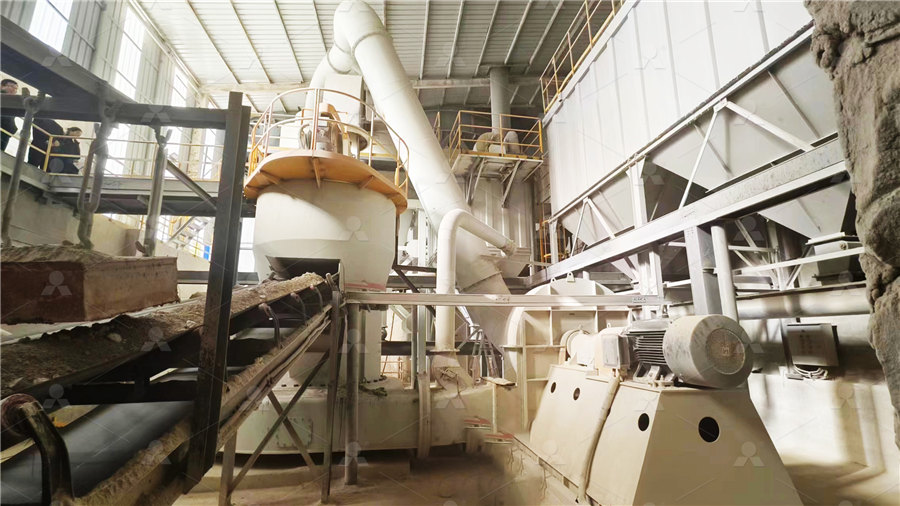
(PDF) Utilising of the oiled rolling mills scale in iron ore
Components Oil content, mass% Sintering ore Iron ore concentrate Gas cleaning sludge Blast furnace top dust Scale from primary settling tanks Scale from secondary settling tanks Scale–peat blend Mnbearing slag Steelmaking slag 2018年11月25日 Theory and Practice of Sintering of Iron ore Sintering of iron ore is a generic term which is used to describe the process whereby a sinter mix (raw mix or green mix) of iron ore fines, fluxes, fuel (coke breeze) and plant return fines (eg mill scale, blast furnace dust, and returned sinter fines etc) are converted into a particular form of Theory and Practice of Sintering of Iron ore – IspatGuru2023年12月15日 This study proposes a sintering process using WM in place of some limestone, and we compare the composition, microstructure, and thermal decomposition characteristics of WM and limestone The feasibility of using WM for iron ore sintering is evaluated based on sinter pot experiments, and the appropriate addition ratio is discussedA new disposal method for white mud: Replacing limestone in iron ore 2016年10月28日 Sintering is an agglomeration process that fuses iron ore fines, fluxes, recycled products, slagforming elements and coke The purpose of sintering is to obtain a product with suitable Iron Ore Sintering: Raw Materials and Granulation ResearchGate
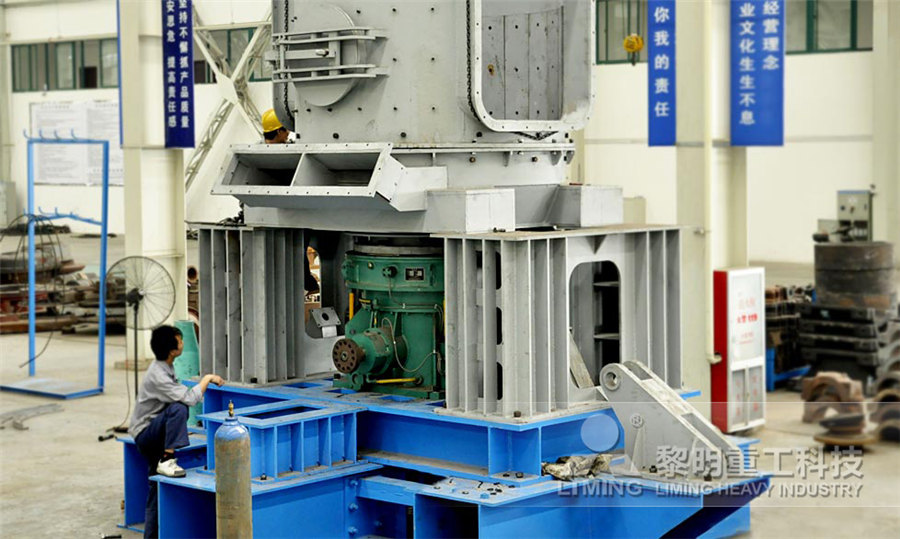
Iron Ore Sintering: Quality Indices ResearchGate
Iron Ore Sintering: Quality Indices D FernándezGonzáleza, I RuizBustinza b, J Mochón , C GonzálezGascac, and L F Verdejaa aGrupo de Investigación en 2016年6月30日 Request PDF Effect of Addition of Mill Scale on Sintering of Iron Ores Ironrich (65 to 70 pct total Fe) mill scale generated during processing by steel mills can be recycled by using it as a Effect of Addition of Mill Scale on Sintering of Iron Ores2017年12月20日 Sintering process is also used in the ironmaking and steelmaking as recycling system as apart from using iron ore fines and additives (such as fluxes and coke breeze), mill scale, collected dusts (and to a much lower extent sludges) from gas cleaning, other recycled byproducts of steel manufacture and recycled sinter particles from sinter screening are treated in Iron Ore Agglomeration Technologies IntechOpen2022年2月28日 The present work proposes a novel process to sinter porous iron ore (porosity ~23–24%) with enhanced productivity and quality The iron ore is preprocessed in the presence of calcined lime for the temporary closure of pores, which further prevents water absorption during the granulation process in drum in the presence of water The calcined lime coated iron ore A Novel Sintering Process for Porous Iron Ore Sintering with
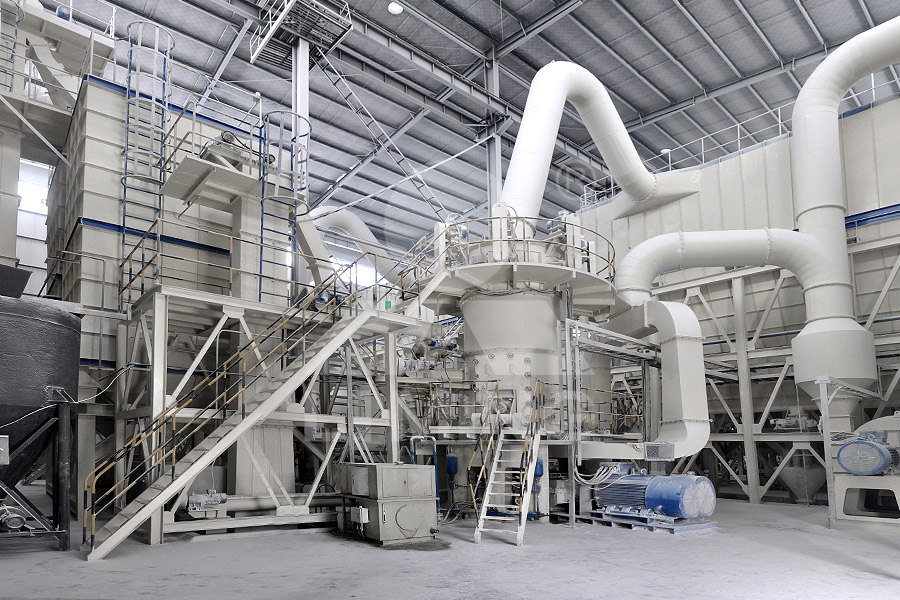
Utilising of the oiled rolling mills scale in iron ore sintering
2011年2月1日 Request PDF Utilising of the oiled rolling mills scale in iron ore sintering process Up to 5% of steel is lost with the scale at hot rolling operation This waste contains 69–72% of iron in 2011年1月1日 Infect only a few investigators worked on the kinetics of mill scale reduction [24][25][26][27][28][29][30]In previous studies on the use of the catalyst for iron ore or mill scale reduction (PDF) Recycling of mill scale in sintering process F Verdeja (2017) Iron Ore Sintering: Raw Materials and Granulation, Mineral Processing and Extractive Metallurgy Review, 38:1, 3646, DOI: 101080/2016Iron Ore Sintering: Raw Materials and Granulation ResearchGate2017年5月2日 blends for sintering also include several iron ores, wastes and byproducts that can deteriorate the sinter quality, and for that reason, causing an unstable and irregular blast furnace(PDF) Iron Ore Sintering: Quality Indices ResearchGate
.jpg)
(PDF) Sintering Performance of Magnetite–Hematite–Goethite
2014年7月4日 Parallel experimentation allowing comparison of magnetite–hematite–goethite inland and hematite–goethite coastal mill blends in terms of sintering performance is reported2013年11月12日 Thus, recycling it through the sintering process helps in the saving of raw materials like iron ore and limestone This paper presents preliminary findings of a study that investigates the potential for recycling steel mill scale in the sintering process Experiments were conducted using the mill scale in sinter making from 0 to 70 kg/t of sinterRecycling of steel plant mill scale via iron ore sintering plant2014年11月21日 Fig 1 Schematics of sinter mix and product sinter Sintering process is a generic term that is used to describe the process of agglomeration of a green mix of iron ores, fluxes and coke and plant solid wastes having a particle size of 10 mm so as to produce sinter which can withstand operating pressure and temperature conditions existing in a BFSinter Quality and Process of Sintering Iron Ores – IspatGuru2011年2月1日 The scheme of the iron ore sintering process is represented by Fig 5 Sinter mixture contains iron ore, solid fuel (usually coke breeze), flux and some additives (eg solid wastes like BOF slag, gas cleaning dust and sludge etc) The mixture is granulated with the addition of moisture and loaded to the travelling grate of the sintering plantUtilising of the oiled rolling mills scale in iron ore sintering
.jpg)
Sintering plant at a glance PPT SlideShare
2014年10月27日 5 5 Material flow Diagram Sintering Plant Flux Hammer Crusher Flux Screen +3mm Stock Bin proportioning section Iron Ore Fines 3mm Coke breeze from C O PMD Hot Sinter return 5mm Cold Sinter return Cold Sinter return Coke return from B F 25mm 3mm Fuel Storage Coke crusher Sinter M/c Hot screen SLC Cold screen Sinter to BF 8mm 5mm Waste 2023年1月15日 This review focuses on explaining the role that various reductants/fuels play in the sintering of iron ore and how those choices affect product quality and the surrounding Recycling of Mill Scale in Sintering Process, 102298/SOSE Google Scholar [44] Won Yang, Kwangheok Yang, Sangmin Choi Effect of fuel characteristics Reductants in iron ore sintering: A critical review ScienceDirect2017年2月16日 Sintering is a thermal agglomeration process that is applied to a mixture of iron ore fines, recycled ironmaking products, fluxes, slagforming agents and solid fuel (coke)(PDF) Iron Ore Sintering: Process ResearchGate2016年6月30日 Ironrich (65 to 70 pct total Fe) mill scale generated during processing by steel mills can be recycled by using it as a ferrous raw material in the sintering process The effect of mill scale addition on the phase formation of sintered specimens from an industrial sinter blend containing 0 to 15 wt pct mill scale was examined, and the mineral phases formed during Effect of Addition of Mill Scale on Sintering of Iron Ores
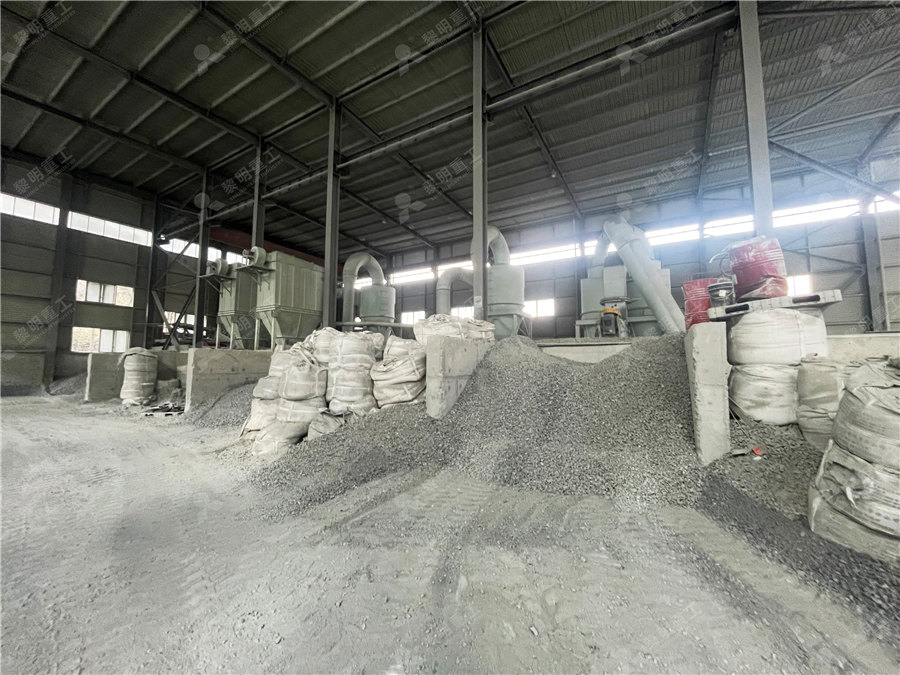
Biomass–Coal Hybrid Fuel: A Route to NetZero Iron
2023年3月21日 The global steel industry uses fossil fuels to produce millions of tonnes of iron ore sinter each year Sintering is an energyintensive process that fuses iron ore and flux to produce material that balances a high mechanical 2018年7月11日 Correspondingly, the challenges in sintering granulation field are proposed to include: (1) Development of iron ore sintering industry; (2) Ore blending optimization based on synergistic coupling Iron Ore Agglomeration Technologies Provisional chapter Iron Ore iron ore sintering process, but they must be reconsidered due to the rise of coke price, the unstable supply of anthracites and the global warming by CO 2 emissions (Murakami et al, 2013)Iron Ore Sintering: Process ResearchGate2023年6月24日 2 a screened size of 10 mm to 30 mm, can withstand pressure and temperature conditions in the blast furnace Principle of sintering Sintering is a thermal process (carried out at 1300 deg C to 1400 deg C) by which a mixture of iron ore, return fines, recycled products of the steel plant industry (such as mill scale, blast furnace dusts, etc), slag forming elements, fluxes Sintering process of Iron Ore Generaldocx SlideShare
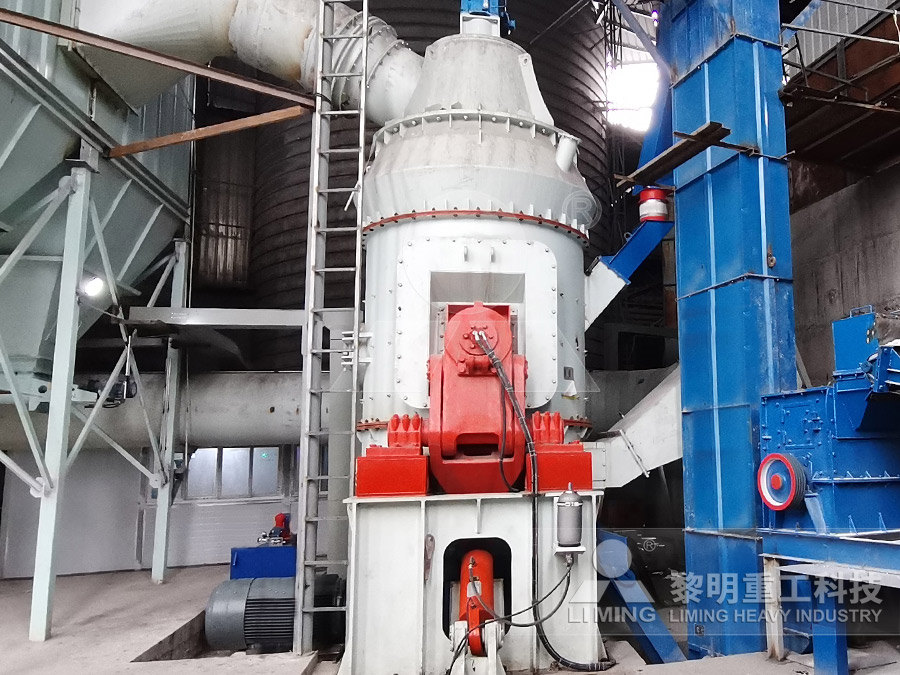
Effect of Mill Scale Adding Methods on NOx Emission of Coke
In this research,the effects of mill scale adding method on NOx emission of coke combustion during iron ore sintering were studied Firstly, the behavior of the coke combustion and NOx emission on 2017年2月16日 Sintering is a process of agglomeration of iron ore fines, fluxes, recycled products, slagforming elements and coke with the purpose of achieving an agglomerated product with the suitable Iron Ore Sintering: Environment Automatic and Control Techniques2009年8月1日 Mill scale is an iron oxide waste generated during steelmaking, casting and rolling Total generation of mill scale at JSWSL is around 150 t/day and contains 60–70%FeO and 30–35%Fe2O3 To recover the iron, the mill scale must be smelted in a blast furnace or other reduction furnace; however, it is usually too fine to use without previous agglomeration such Recycling of steel plant mill scale via iron ore pelletisation process 2022年1月24日 The use of sinter influences hot metal production substantially and significantly affects an integrated steel mill’s total emissions Sintering of iron ores is an enormous energyintensive and (PDF) Model of an iron ore sinter plant with selective waste gas
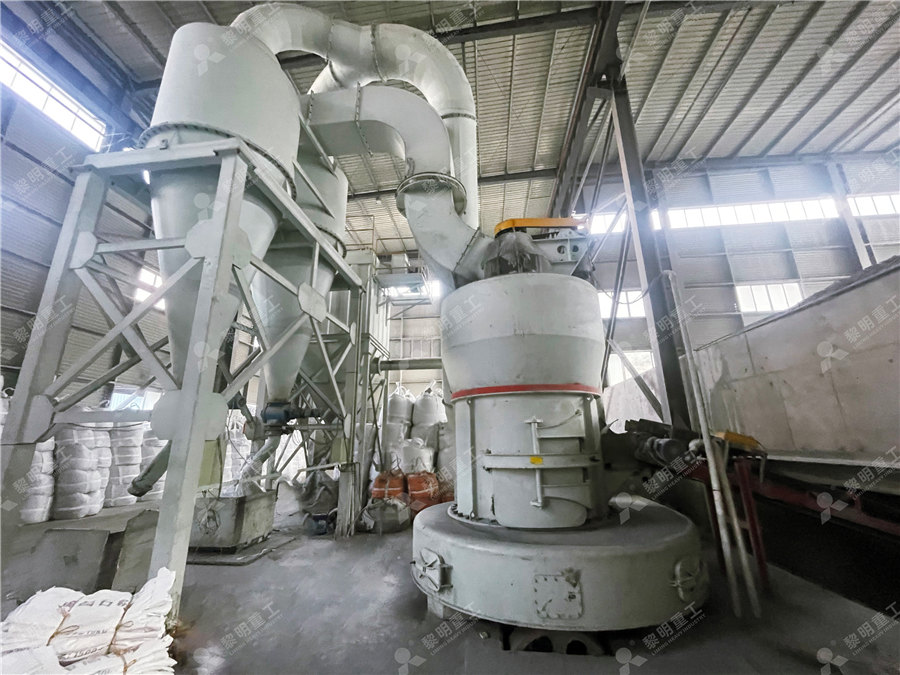
Iron Ore Sintering Process Model to Study Local Permeability
Iron Ore Sintering Process Model to Study Local Permeability Control Y Kaymak1, T Hauck1, M Hillers2 1 VDEh Betriebsforschungsinstitute GmbH, Düsseldorf, NW, Germany 2 Shuangliang Clyde Bergemann GmbH, Ratingen, NW, Germany Introduction The iron ore sintering process prepares fine iron the ores for the blast furnace process In iron ore sintering, the blended particulate bed on the strand is partially melted in the flame front to form a threephase solidmeltgas mix passing 100 ˜m using a ring mill A liquid pycnometer was used to determine the density of the ground products TheImportance of Melt Generation and Properties in Iron Ore Sintering2023年2月13日 The iron and steel industry has made an important contribution to China’s economic development, and sinter accounts for 70–80% of the blast furnace feed charge However, the average grade of domestic iron ore is low, Research Progress of Intelligent Ore Blending ModelIron Ore Sintering: Environment, Automatic, and tives such as lime, olivine, collected dust and mill scale, dusts (and to a much lower extent sludges) from gas cleaning inIron Ore Sintering: Environment, Automatic, and Control Techniques
.jpg)
(PDF) Iron Ore Granulation for Sinter Production: Developments
2022年12月29日 Correspondingly, the challenges in sintering granulation field are proposed to include: (1) Development of iron ore sintering industry; (2) Ore blending optimization based on synergistic coupling But, Ore B has Fe 2O 3 as the main phase, and contains 003 wt pct of sulfur Since iron ores contain sulfur, the content of sulfur in the iron ores was considered when evaluating the conversion ratio of sulfur to SO 2 In sinter mix condition, Ore A and Ore B were mixed in the weight ratio of 8 to 2, which was similarly adjusted to actual Effects of Adding Calcined Dolomite and Mill Scale to Sinter Mix 2022年1月1日 Sintering is the most economic and widely used agglomeration process to prepare iron ore fines for blast furnace use In this chapter, the sintering process is first described to identify the key Iron ore sintering ResearchGateEmission Optimized Sintering (EOS®) for lower costs Iron ore sintering creates substantial offgas volumes, and treating these in order to meet increasingly stringent environmental standards is expensive EOS® uses recycling technology to reduce offgas volumes by 40 to 50 %, resulting in smaller secondary gas treatment systems This means:SINTERING AND PELLETISATION OF INDIAN IRON ORES
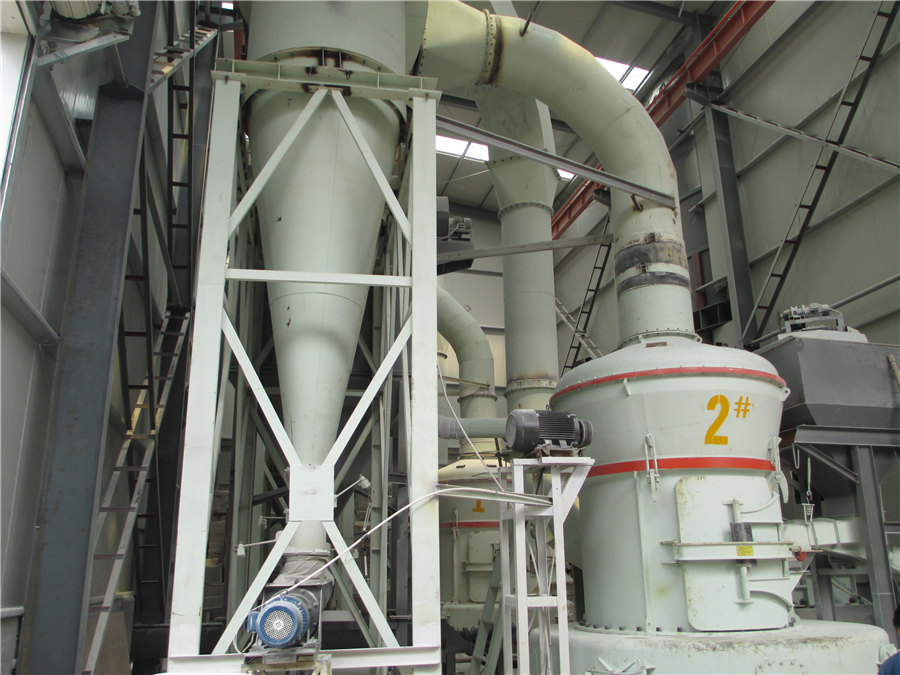
Model of an iron ore sinter plant with selective waste gas
2022年3月1日 With iron ore sintering, iron fines are utilizable for pig iron production The sintering process is influenced extensively by the properties of the input material and process conditions rolling mill) Solid fuels are the second important source of sulfur by about 24% (scenario without SWGR)2020年8月19日 The sintering process can be defined as a thermal agglomeration process that is applied to a mixture of iron ore fines, recycled ironmaking products, fluxes, slagforming agents, and solid fuel (coke) with the objective of obtaining a product with the suitable characteristics (thermal, mechanical, physical, and chemical) to be fed to the blast furnaceSintering SpringerLink