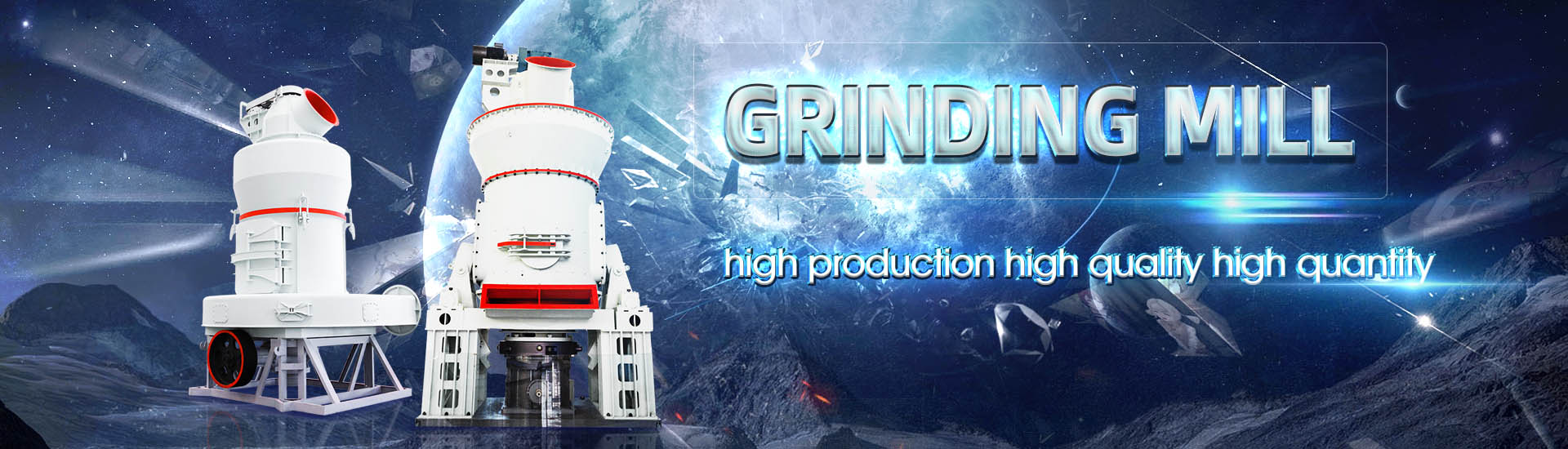
Micro powder Separation
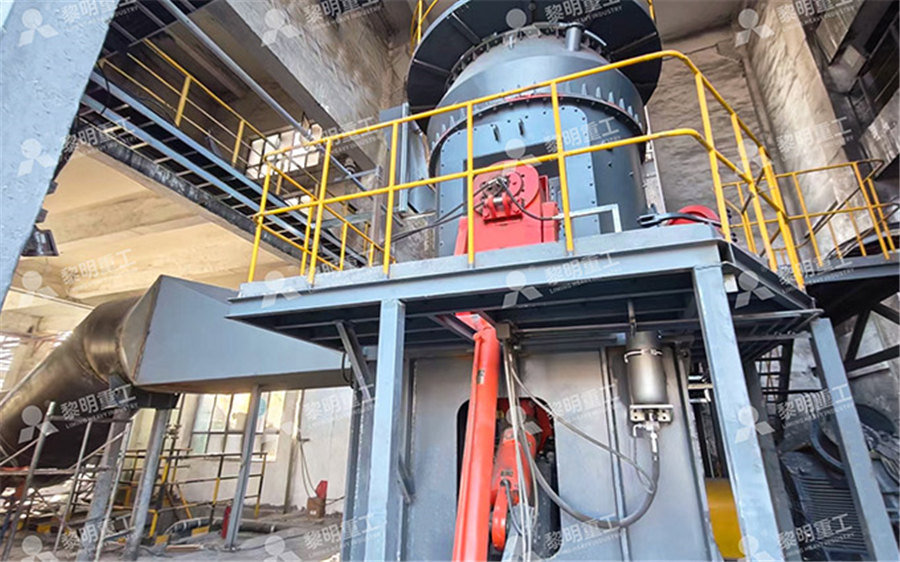
Separating microparticles by material and size using Nature
2021年8月19日 Results from experiments and simulation show a good agreement for the separation of binary PS particles mixtures with respect to size and more importantly, for the challenging task ofMixing in powders generally results from relative motion of groups of particles ‒ convective mixing ‒ or of individuals ‒ diffusive mixing Segregation or demixing occurs when the motion ofMixing and Segregation in Powders: Evaluation, Mechanisms and 2024年11月12日 In this study, a twodimensional separation of microparticles based on their settling velocity and triboelectric charge ability is achieved using an air classifier for size fractionation and simultaneous charging, followed by an electrostatic separatorSize Classification and Material Sorting of Fine Powders with a 2016年5月20日 Microfluidic techniques for separating microparticles can be divided into two categories: active and passive methods Active methods use external forces such as electric field, magnetic field,Cloggingfree microfluidics for continuous sizebased separation
.jpg)
Enhanced microfluidic multitarget separation by positive and
2024年6月10日 We introduce magnetophoresisbased microfluidics for sorting biological targets using positive Magnetophoresis (pM) for magnetically labeled particles and negative Magnetophoresis (nM) for2013年11月29日 A microhydrocyclone device for particle–liquid separation (Bhardwaj et al 2011) employs a cylindrical chamber with a frustoconical bottom and an inlet channel tangential to this cylindrical chamber to separate particles Particle separation and sorting in microfluidic devices: 2021年11月18日 In this paper, we present a comprehensive review of the recent advances in microfluidic separation of micro/nanosized bioparticles by summarizing the physical principles behind the separation system and Progress of Microfluidic Continuous Separation Here, we review the recent advances in nanoparticle separation using microfluidic devices, focusing on its techniques, its advantages over conventional methods, and its potential applications, as well as foreseeable challenges in the Advancements in microfluidics for nanoparticle
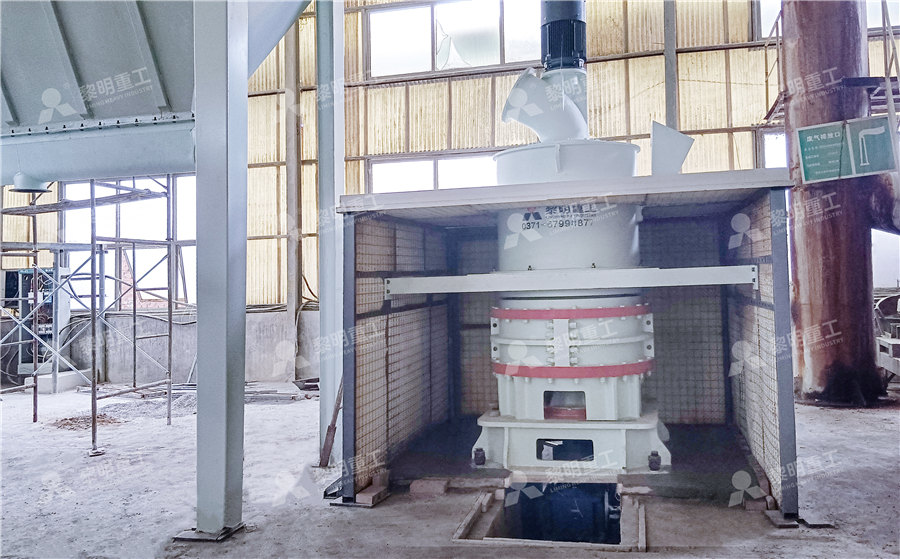
Size separation of biomolecules and bioparticles using
Reports of novel micro/nanostructures designed to separate biomacromolecules and bioparticles are increasing in number, and these studies have greatly advanced our understanding of nanoscale fluidics and nanoparticle behavior @article{Nie2023EcofriendlySF, title={Ecofriendly strategy for advanced recycling waste copper from spent lithiumion batteries: Preparation of micronano copper powder}, author={Chunchen Nie and Xiguang Li and Shunxiang Shi and Yisu Wang and Xianjun Lyu and Guyue Li and Xiangcheng Zhu and Zhe Wang}, journal={Separation and Purification Ecofriendly strategy for advanced recycling waste copper from KONA Powder and Particle Journal No27 (2009) 3 Introduction Mixing of particulate solids is an important process in its own right, as in blending of the components of a mixed powder; it can also play a critical role in the performance of other particle processing operations such as grinding, granulation, classification and chemical treatmentMixing and Segregation in Powders: Evaluation, Mechanisms and 1 Micropowder injection molding: Investigation of powderbinder separation using synchrotronbased microtomography and 3D image analysis O Weber 1,*, A Rack 2, C Redenbach 3, M Schulz 1, O Micropowder injection molding: Investigation of powderbinder
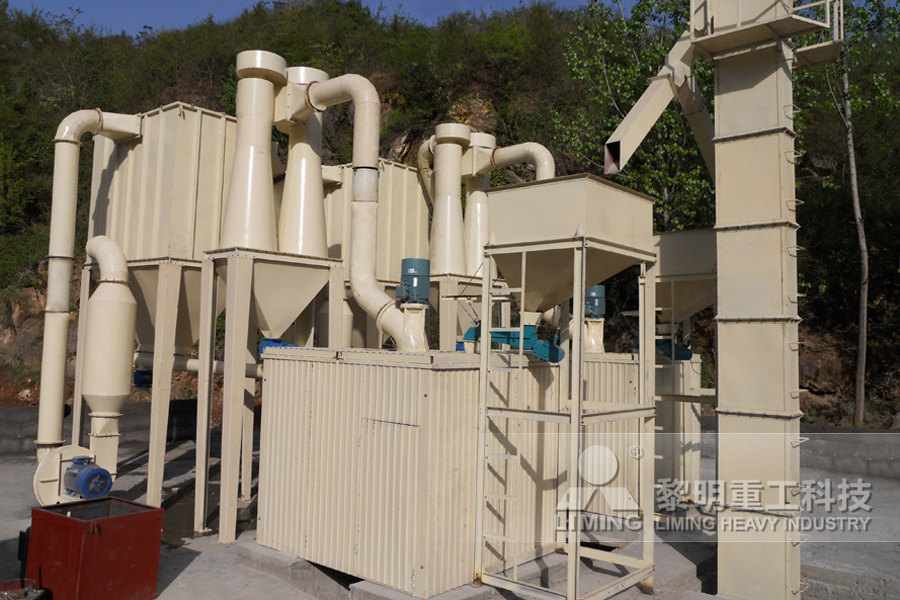
Particle separation and sorting in microfluidic devices: a review
2013年11月29日 However, some of the passive separation techniques including the inertial and dean flow fractionation and microhydrocyclone are not discussed In another review paper by Lenshof and Laurell ( 2010 ), some of the passive microfluidic separation and sorting techniques were discussed, but few other techniques including crossflow filtration and Zweifach–Fung DOI: 101016/JPOWTEC201401065 Corpus ID: ; The effects of filling patterns on the powder–binder separation in powder injection molding @article{Fang2014TheEO, title={The effects of filling patterns on the powder–binder separation in powder injection molding}, author={Wei Fang and XinBo He and Ruijie Zhang and Shidi Yang and Xuanhui Qu}, The effects of filling patterns on the powder–binder separation in 2011年8月1日 Request PDF Modelling the powder–binder separation in injection stage of PIM In this paper, a nonisothermal multiphase flow numerical model has been developed based on Eulerian approach to Modelling the powder–binder separation in injection stage of PIM2020年5月26日 Molding of micro objects by micron injection molding is called μPIM (micro powder injection molding) More rigid specifications are laid for down for these workpieces [ 39 ] Heated molding mixture (normally 125 – 150°C) moves within a mold after filling is cooled in order to conduct workpiece separation from a moldHighdensity Micro and NanoGrain Size Ceramics Transition
.jpg)
Preparation of Nano/Micro Bimodal Aluminum Powder by
2021年11月2日 In this research, Ti–Al bimodal powders were produced by simultaneous electrical explosion of titanium and aluminum wires The resulting powders were used to prepare powder–polymer feedstocks2011年3月25日 The powder bed absorbs the molten binder and stabilises the structure against mechanical impact This approach is feasible for micro parts with restrictions only On the one hand, separation of the micro parts from powder bed is problematic On the other hand, the particles of the powder bed deteriorate the surface quality of the parts (Fig 18)Powder injection moulding of metallic and ceramic micro parts2020年6月3日 Abstract Powder injection molding (PIM) is a wellknown manufacturing technique for the production of complex, netshaped macroparts using a broad range of materials and alloys Eventually, the PIM method has been modified into micropowder injection molding (μPIM) because of the increasing demand of microparts in global market Nowadays PIM and μPIM Process Parameters Used in Macro/Micro Powder Injection Molding2020年5月26日 Highdensity Micro and NanoGrain Size Ceramics Transition from Open into Closed Pores Part 1 Powder Preparation, Molding Mixture, MoldingHighdensity Micro and NanoGrain Size Ceramics
.jpg)
Ecofriendly strategy for advanced recycling waste copper from
2023年6月1日 Ecofriendly strategy for advanced recycling waste copper from spent lithiumion batteries: Preparation of micronano copper powder June 2023 Separation and Purification Technology 322(5):Sometimes, the separation between these phases can be directly observed via microscopy Tunneling electron microscopy (TEM) is a technique that can generate images of a crosssectional slice of the material The material is generally stained with a heavy metal, such as osmium, that binds preferentially to one phase or the other46: Microphase Separation Chemistry LibreTexts2024年9月27日 Hosokawa Micron Powder Systems designs and manufactures size reduction systems and powder processing solutions for the chemical, mineral, pharmaceutical, cosmetic, food and plastic industries Hosokawa Micron Powder Systems specializes in coarse to ultrafine grinding, classification, mixing, drying, containment, compaction and analytical equipmentHome Hosokawa Micron Powder SystemsMicro powder silica gel,production lines of various series of chromatography materials, designing of new highefficiency separation materials, controllable customization of silica gel adsorption and separation performance, design and application of overall scheme of separation and preparation We can provide a variety of chromatography consumables related to sample pretreatment Micro powder silica gel Qingdao Bangkai Hitech Materials
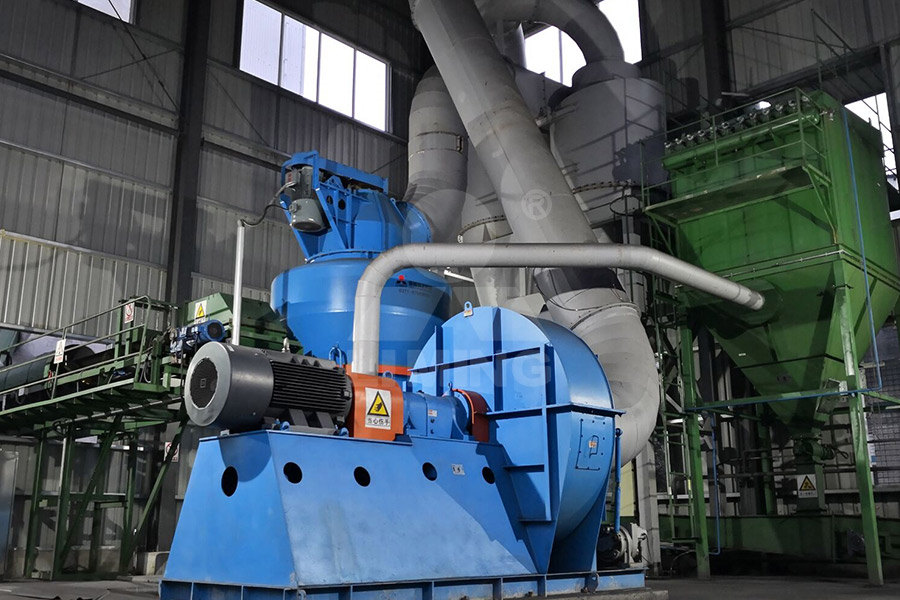
Surface modification of silica micropowder by titanate
2021年11月8日 Silica micropowder (SMP) is a kind of ultrafine quartz powder, prepared from natural quartz ores through crushing, grinding, flotation, was obtained by solid–liquid separation using a filter Place the mSMP in a vacuum drying oven at 60 °C for 1 h, then move it into a drying oven at 130 °C for 3 h Subsequently, 2023年1月1日 The energy consumption for separation and purification processes accounts for 10–15% of the world’s energy consumption [1]The separation of microparticle contaminants is of vital significance for many industries (such as environmental engineering [2], semiconductor industry [3], and aerospace)The use of lubrication is the most important strategy for friction Ultraclean separation of microparticles in lubricant oil based on 2016年5月20日 Separation of microscale particles has been an important issue in industrial, biochemical and clinical applications for identification and analysis of specific particles 1,2,3To achieve the goal Cloggingfree microfluidics for continuous sizebased separation As experts in small particle additives for 50 years, we continue to design specialty waxes and other fine powders that help solve formulation problems and enhance performance in industrial coatings, inks, agricultural, and personal care productsMicro Powders Inc Small Particles, Big Ideas
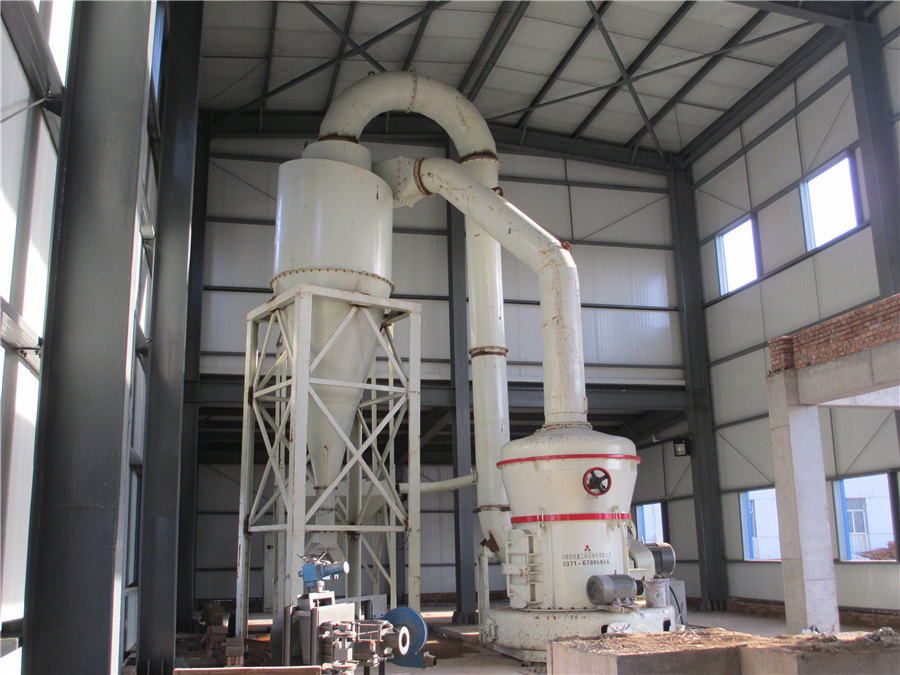
Production process of steel slag micropowder Semantic Scholar
2011年3月17日 The invention relates to a production process of steel slag micropowder, which comprises the following steps: enabling wet steel slag powder with water content of 5% and particle size of 020mm generated after crushing and magnetic separation of steel slag to enter a mill for powder milling, conveying obtained fine powder into a vibration drying and powder 2016年5月1日 Microphase separation technique is the most common method for preparation and production of polymeric membrane [2] The dry cast process, as one of phase separation process, typically needs ternary reaction system including polymeric substance, its goodsolvent with relatively low boiling point, and its nonsolvent with higher boiling point [3]Formation of nanoparticle added functional polymer network 2008年5月1日 In the present work, a numerical model is developed to predict the powder‐binder separation (a common defect in PIM and especially severe in micro‐PIM) during the injection of an alumina ThreeDimensional Numerical Simulation of Segregation in Powder 2015年5月1日 The purity and recovery of SiC powder recovered from the isooctane phase was 900% and 920%, respectively, and those of Si powder recovered from the water phase was 895% and 870%, respectivelyPhase separation of a microsized powder mixture
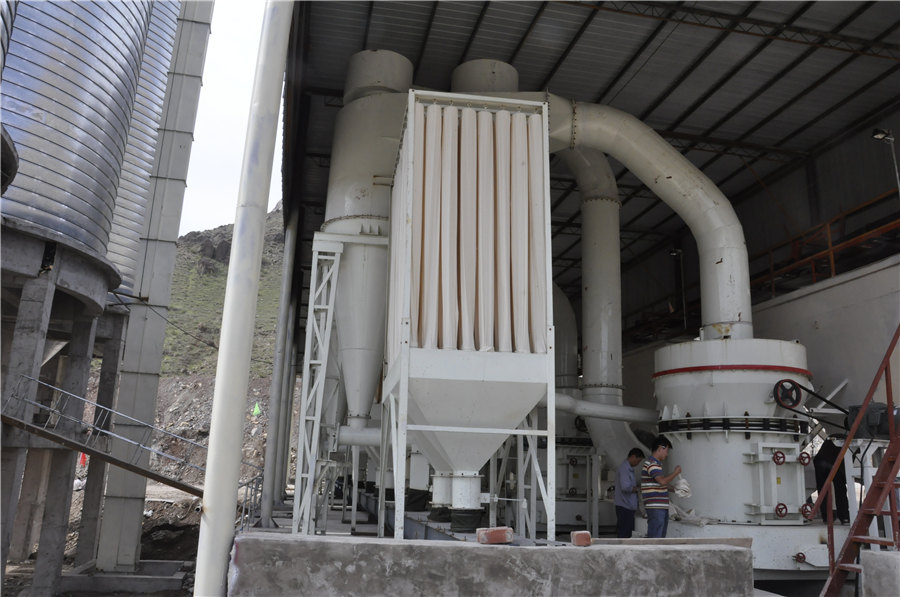
Micro Powder Injection Molding (mu PIM): Review
2011年3月1日 Micro powder injection molding powderbinder separation at high shear rates can lead to the local variation in the melt viscosity which can influence the shrinkage and other mechanical 2011年1月29日 Micropowder injection molding (μPIM) is one of the most promising processes of mass production for the fabrication of small complex shaped ceramic or metallic parts with high sintered density However, dimensional accuracy of finished parts is difficult to achieve because of extremely high shear rates during the injection molding process This promotes the separation Micropowder injection molding: investigation of powderbinder 2021年11月2日 Nano/micro particle composites, as a rule, are obtained by mixing readymade nano and micropowders obtained separately in different processes [23,24,25] However, when mixing powders, the particles of which differ significantly in density, size, and shape, the separation and disturbance of the homogeneity of the mixture are possiblePreparation of Nano/Micro Bimodal Aluminum Powder by Electrical Micropowder injection molding (μPIM) is one of the most promising processes of mass production for the fabrication of small complex shaped ceramic or metallic parts with high sintered density However, dimensional accuracy of finished parts is difficult to achieve because of extremely high shear rates during the injection molding process This promotes the separation Micropowder injection molding: investigation of powderbinder
.jpg)
Progress Report on Phase Separation in Polymer Solutions
2019年3月11日 While in earlier days of engineering materials, the avoidance of porosities was the main objective, 6 in PPM it is explicitly utilized to provoke the aforementioned beneficial capabilities of the polymer materials and to facilitate versatile and momentous applications 1 For instance, PPM shows its extraordinary efficiency in various membrane separation processes 7 The microsize flake silver powders were prepared through wetchemical reduction method by using a microjet reactor Herein ascorbic acid was used as a reducing agent, and sulfuric acid was used as a stabilizer And the lauric acid was used as a dispersing agent to prevent particles’ agglomeration The microjet reactor collides the two solutions together and uniformly mixes Preparation of the microsize flake silver powders by using a micro 2023年6月30日 Abstract Powder injection molding (PIM) is capable of manufacturing complex small components out of metals and ceramics With increasing market demand micropowder injection molding (microPIM) is improving rapidly which calls for improved numerical models of different stages of PIM The injection stage is quite important as different defects may occur Simulation of MicroPowder Injection Molding Using a Dynamic 2024年8月1日 Micronano copper particles tend to be spherical with a size of hundreds of nanometers are successfully prepared using the filtrates of all three leaching systems as precursors for the reduction process The micronano copper particles prepared from reduced copper ammonia solution with copper sulfate solution consisted of cuprous oxide and copperSustainable strategies for recovering metallic copper from waste
.jpg)
Micropowder injection molding: Investigation of powder
1 Micropowder injection molding: Investigation of powderbinder separation using synchrotronbased microtomography and 3D image analysis O Weber 1,*, A Rack 2, C Redenbach 3, M Schulz 1, O Wirjadi 4, 1Karlsruhe Institute of Technology, Institute for Materials Research III, Karlsruhe, Germany 2European Synchrotron Radiation Facility, Grenoble, FranceMicroMesh® sieves are customproduced from electroformed mesh material and assembled in a variety of standard diameter frames to meet your powder or particle separation needs The precise apertures are used to sort, sift, screen MicroMesh Sieves Industrial Netting2024年4月1日 The Ticoated diamond micropowder, with the oxide layer removed, Notably, there was no separation gap between the Ni and Ti layers The weak interfacial bonding force between the diamond and Ni, which lacked a chemical bond, indicated that once the Ni coating wore off, the diamond could easily detachPreparation of the Ni/Ticoated diamond micropowder for 2011年6月1日 Request PDF Preparation and characterization of micro components fabricated by micro powder injection molding Given the dimension of the micro component to be replicated, it is crucial to Preparation and characterization of micro components fabricated
.jpg)
Rapid preparation of micro/nano porous Cu/Cu2O particles
2023年10月1日 Threedimensional (3D) continuous micro/nano porous Cu/Cu 2 O (MNPC) particles that were difficult to obtain before were prepared With the combination of rapid powder sintering and dealloying, when Al element is corroded, the particles can control the corrosion intensity through self shedding, to obtain bimodal pore size micron particlesThe paper describes author's work on the investigation of the molding flow behaviour to determine the defects of green part in metal injection molding (MIM) using powder of carbonyl iron (CIPS Defects in Actual Molding Compared with MOLDFLOW ResultActivated Zeolite Powder Activated Alumina Factory Certified by Products Certified by Cryogenic air separation plays a key role in producing oxygen, This letter is to inform you that we evaluated Molecular Sieve JLOED 3050 MM product from Luoyang Jalon Micronano New Materials Co, Jaloning demand for micro components or micro structures, which are applied in microelectronic systems, microfluidics, and medical tools [13] One such promising process is the micro powder injection molding (μPIM) technology, which is a near net shape production of complex micro components on a large scale [46]Injection molding and debinding of micro gears fabricated by micro
.jpg)
Microalgae Biomolecules: Extraction, Separation and Purification
Several microalgae species have been exploited due to their great biotechnological potential for the production of a range of biomolecules that can be applied in a large variety of industrial sectors However, the major challenge of biotechnological processes is to make them economically viable, through the production of commercially valuable compounds Most of