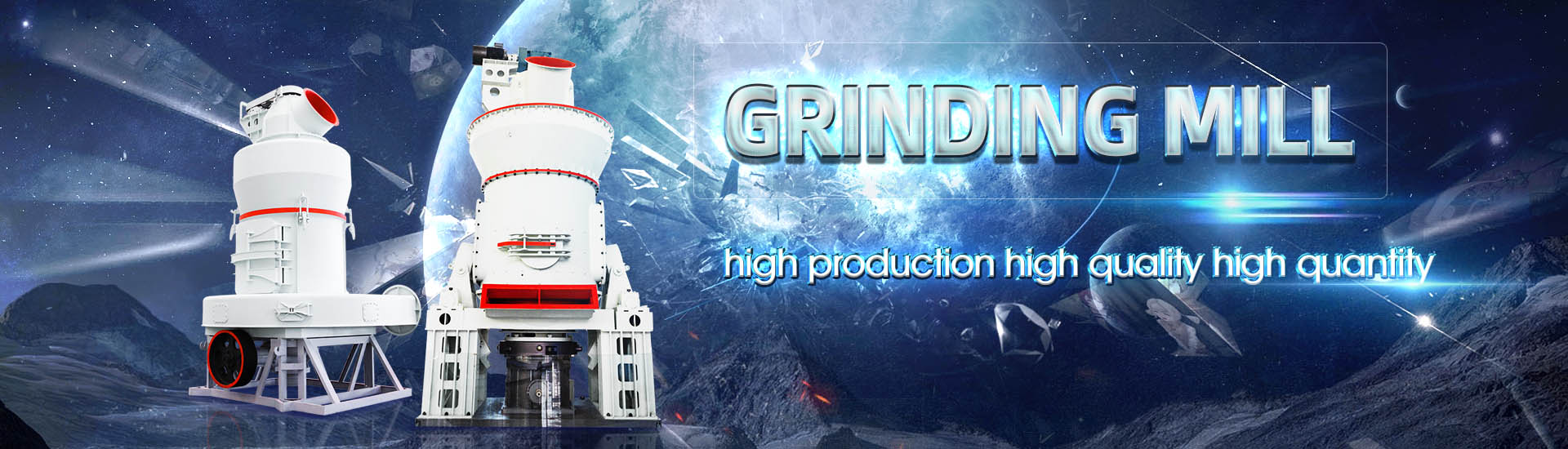
HOME→Grinding mill output Are there any requirements for the crushing method of slag and calcium carbonate
Grinding mill output Are there any requirements for the crushing method of slag and calcium carbonate
.jpg)
2 µm 5 µm Loesche
eat orders As early as 1928, when the first Loesche mill was put on the market, the grinding principle of the vertical roller grinding mill, with a driven grinding track and springloaded rollers 2019年5月23日 Three deironing measures were designed before grinding, and a secondary deironing step was designed between the slag discharging of the grinding mill and the external Comprehensive Utilization Technology of Steel Slag2023年5月15日 water quenching method: The liquid steel slag is crushed into small particles of steel slag using highpressure water during the dumping process Simple process, fast slag Comprehensive utilization of steel slag: A review ScienceDirect2021年9月24日 Based on the analysis, the authors present a holistic approach toward steel slag utilization beyond the conventional application areas like aggregates, landfilling, etc This BOF Steel Slag: Critical Assessment and Integrated Approach for
.jpg)
Current Development of Slag Valorisation in China
2014年2月19日 In addition to the slag granulation process with pollution control and continuously dewatering (INBA™ process), several modified blast furnace (BF) slag 2016年10月28日 In this paper, the grinding characteristics of untreated and pretreated (ie, magnetic separation) steel slag were compared Additionally, the grinding property of (PDF) Comparison of Grinding Characteristics of Converter Steel 2021年10月1日 Three methods have been widely employed to improve the reactivity of steel slag and concurrently reduce its potential harm on cementbased host materials: (i) physical Review Use of steel slag as sustainable construction materials: A 2011年10月26日 A better understanding of the properties of steel slag is required for large volumes of this material to be utilized in a technically sound manner in civil engineering Chemical, Mineralogical, and Morphological Properties of Steel
.jpg)
Comparison of Grinding Characteristics of Converter Steel Slag
2016年10月28日 Currently, the researches on improvement of grinding efficiency for steel slag mainly focus on the optimization of grinding equipment—such as vertical mill and roller mill, The primary types of grinding mills include ball mills, rod mills, autogenous mills, and semiautogenous mills Each mill type has a distinct working mechanism, but they all share common principles of crushing and grinding Ball Mills: Ball mills are Understanding the operation of grinding mills in the mining and 2009年5月1日 A method for predicting the specific energy requirement of comminution Predicting the overall specific energy requirement of crushing, high pressure grinding roll and tumbling mill circuitsPredicting the overall specific energy requirement 2021年12月20日 The Importance of Calcium Carbonate Calcium carbonate (CaCO3) comprises more than 4% of the earth’s crust and is found worldwide Its most common natural forms are chalk, limestone, and marble (produced by Calcium Carbonate Manufacturing Process and
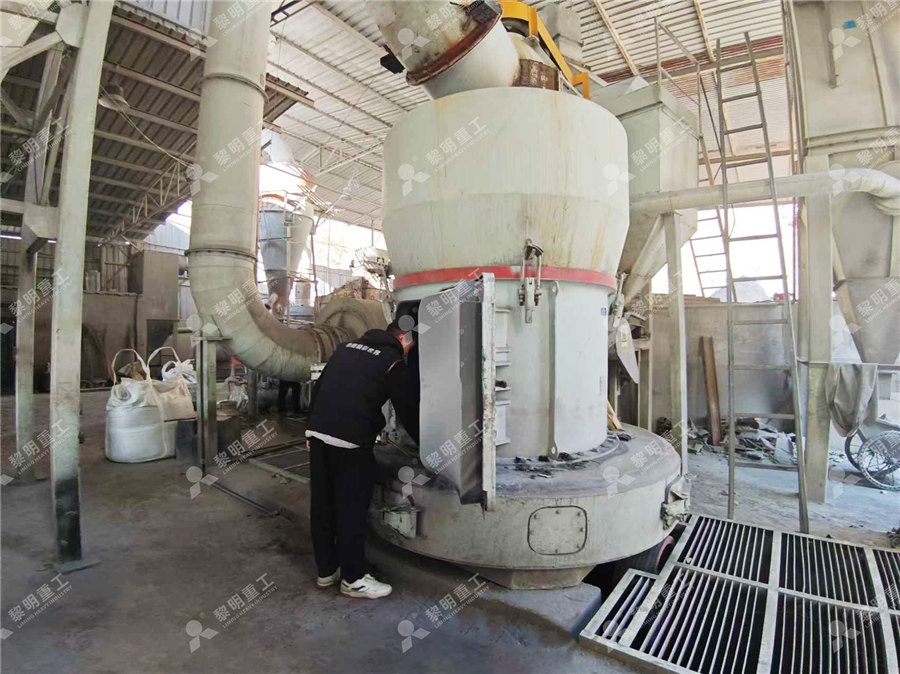
What is the difference between crushing and grinding?
2020年9月7日 There are also several grinding mill machine: Raymond mill, High pressure grinding mill, and Micro powder grinding mill etc However, in most case, a small crusher is needed in the grinding mill machine The crusher is used for crushing the raw material into smaller size, which is more convenient to grinding into super fine size2003年1月1日 There is an increasing body of blasting research indicating significant impacts in crushing and grinding These include increased production through higher output and fewer delays for bridging and (PDF) The Effects of Blasting on Crushing and Grinding2022年1月23日 The crushing area may also include equipment for separation by particle size such as vibrating screens or rollerscreens; both having openings of a known size for proper size separation Preparing the RunofMine (ROM) bauxite for the grinding mill circuit must be completed in order to efficiently size the grinding mill circuitPhysical Bauxite Processing: Crushing and Grinding of BauxiteJune 2022; ARCHIVE Proceedings of the Institution of Mechanical Engineers Part C Journal of Mechanical Engineering Science 19891996 (vols 203210) 236(2):1107(PDF) A comprehensive review on the grinding process:
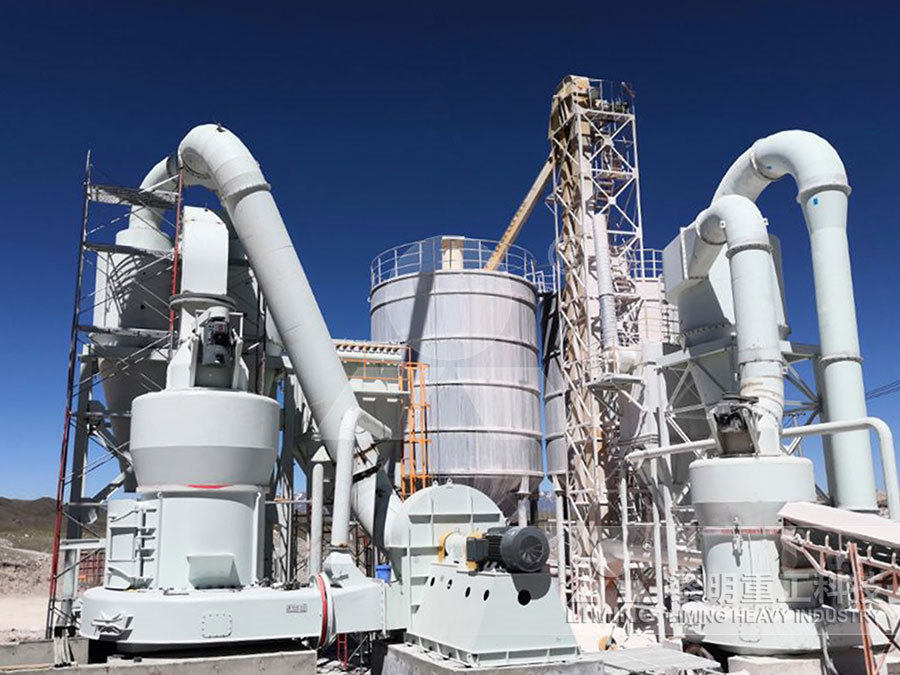
Experimental study on indirect mineral carbonation using five
2024年5月26日 Mineral carbonation is one of the known methods for carbon capture, utilization, and storage (CCUS) Slag from the steel industry is studied as a common source of CaCO3 via mineral carbonation owing to its high Ca content Despite numerous preliminary studies, the optimal factors governing the mineral carbonation of steelmaking slag, such as extraction and 2013年12月1日 Calcination of the limestone is energy intensive as it requires high temperatures (∼1000 °C) the objective of this study is to evaluate the feasibility of production of precipitated calcium carbonate from steel converter slag Calcium was extracted selectively from the slag with an aqueous solution of ammonium salt (NH 4 NO 3, CH 3 COONH 4 Production of precipitated calcium carbonate (PCC) from steelmaking crushing and grinding plants This study helps all the mineral industries to utilize the optimum energy required for comminution units in the mineral processing industries KEYWORDS:Crushing, Grinding, Bond Index, Brittleness, Compressive strength I INTRODUCTION Comminution is the process of crushing and minution Tests Required to Assess the Energy Requirement Combining impact and shearing actions enhances mill efficiency Proper selection of media milling equipment is vital for success in all three areas There are many different types of grinding mills (Table 1) Some devices, such as ball mills, Solids Choose the Right Grinding Mill Chemical
.jpg)
(PDF) Comparison of Grinding Characteristics of
2016年10月28日 The grinding efficiency of steel slag was obviously increased and the particle characteristics were improved after using grinding aids (GA), especially the particle proportions of 332 Mm were 2019年10月8日 1 Crushing and grinding improvement The ore size reduction process involves two steps: crushing and grinding The grinding process is the final operation of making the mineral to dissociate from the monomer and Crushing and Grinding Process JXSC Machine2 GRINDING ICNTERNATIONAL CEMENT REVIEW SEPTEMBER 2022 energy requirements:1 • ball mill: 38kWh/t • HPGR plus ball mill: 3034kWh/t • VRM: 2832kWh/t Grinding is a very energy intensive process that accounts for a significant amount of production costs7 This is why advances in classifier technology have been vital in increasing productionGRINDING Grinding options for slag and pozzolan PEC 2023年12月8日 Limestone Properties The main component of limestone is calcium carbonate (CaCO3), with a Mohs hardness of 3 After limestone is mined from limestone, it is crushed to form limestone particles, that is, stone and sand, or further ground to form limestone powder, which is widely used in industries such as building materials, highways, metallurgy, and Limestone crushing technology and equipment SBM Ultrafine
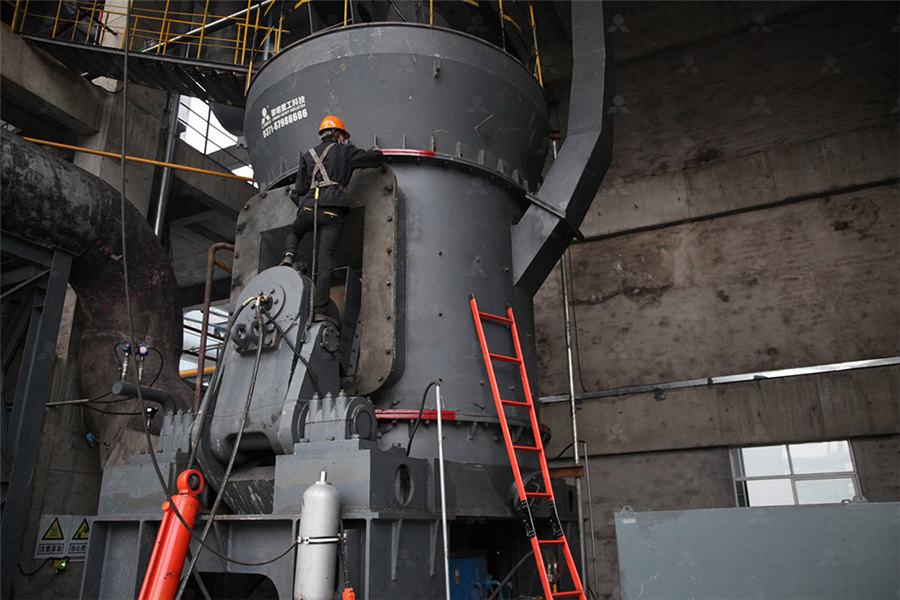
2 µm 5 µm Loesche
Calcium carbonate crystals 20 µm 2 µm 2 µm 5 µm 20 µm 10 µm CEMENTMILL slag in roller grinding mills (vertical airswept grinding mills) is a technology introduced by Loesche The first use of a Loesche mill, with a grinding track diameter of only 11 metres, was used as long ago as 1935 However, the roller grinding mill, 2021年9月24日 During steel production, the impurities in the hot metal react with the fluxes forming the steel slag Chemical constituents of this steel slag (SS) are relevant to iron/steelmaking or blended cement manufacture Harmful impurities present in it, however, limit its recycling to these applications Japan, Europe, and the US consume a significant amount of BOF Steel Slag: Critical Assessment and Integrated Approach for 2007年2月1日 But nowhere in the world have so many roller mills for granulated blast furnace slag grinding been sold as in China during the last 6 years First Polysius slag roller mill in China The first Polysius roller mill for slag grinding in China is in operation since 2002 in Anshan in the province of LiaoningSlag grinding with the Polysius Roller Mill in China2016年6月6日 A variant of this method is to direct pebblecrushing circuit product to the ballmill sump for secondary milling: while convenient, this has the disadvantage of not controlling the top size of feed to the ballmill circuit There have also been pioneer installations that have installed HPGRs as a second stage of pebble crushingSAG Mill Grinding Circuit Design 911Metallurgist
.jpg)
Grinding Mills Common Types 911Metallurgist
2016年11月7日 In Fig 13 is shown a large ball mill, designed for the dry grinding of limestone, dolomite, quartz, refractory and similar materials; this type of mill being made in a series of sizes having diameters ranging from about 26 in to 108 in, with the corresponding lengths of drum ranging from about 15 in to 55 in2008年3月3日 The use of GGBFS as a partial Portland cement replacement takes advantage of the energy invested in the slagmaking process and its corresponding benefits with respect to the enhanced cementitious properties of the slag Grinding slag for cement replacement requires only about 25% of the energy needed to manufacture normal Portland cementEfficient and reliable handling of GBFS and GGBFS at grinding Ball mills have undergone considerable change in the last few decades with trends of increased mill sizes, high efficiency separators and innovative internal designs 7 The efficiency and output are primarily dictated by ball charge for Options for Grinding Slag and Pozzolan for Use as 2017年10月26日 The following are factors that have been investigated and applied in conventional ball milling in order to maximize grinding efficiency: a) Mill Geometry and Speed – Bond (1954) observed grinding efficiency to be a Factors Affecting Ball Mill Grinding Efficiency
.jpg)
Comprehensive utilization of steel slag: A review ScienceDirect
2023年5月15日 Steel slag is the main solid waste generated in the steelmaking process, accounting for 15 to 20% of crude steel output [1]China's crude steel output in 2021 was 1035 billion tons [2], more than half of the global crude steel output (19505 billion tons) [3], and the steel slag output exceeded 120 million tonsIn contrast, the comprehensive utilization rate of Crushing and grinding operations are important for the entire mineral processing process, as well as two operations with huge investment and high energy consumption In terms of metal mines, the equipment investment of crushing and grinding operations accounts for 65% ~ 70% of the total investment in the whole plant, and the power consumption is about 50% ~ 65%3 Principles of Choosing the Crushing and Grinding Process2018年8月1日 Different countries use a variety of steel slag treatment methods In Japan, the most commonly used method to prevent the expansion of steel slag is the aging treatment (Sasaki et al, 1982, Vaverka and Sakurai, 2014) Slag aging also is used to stabilize freeCaO and freeMgO into calcium or magnesia hydroxide (Nishinohara et al, 2013)Steel slag in China: Treatment, recycling, and management2018年4月17日 Mill Sizing: After laboratory and pilot plant testing confirm the feasibility of autogenous or semiautogenous grinding, it can be used to establish the exact grinding circuit and mill sizeIn the pilot plant tests, the tare power of the pilot plant mills should be determined before and after each test run The tare power should be for the empty millAutogenous and SAG SemiAutogenous Mill Design Calculations
.jpg)
Energy and exergy analyses for a cement ball mill of a new
2020年2月1日 Nowadays, ball mills are used widely in cement plants to grind clinker and gypsum to produce cement In this work, the energy and exergy analyses of a cement ball mill (CBM) were performed and A crushing plant delivered ore to a wet grinding mill for further size reduction The size of crushed ore (F 80) was 40 mm and the SG 28 t/m 3 The work index of the ore was determined as 122 kWh/t A wet ball mill 1 m × 1 m was chosen to grind the ore down to 200 micronsGrinding Mill an overview ScienceDirect Topics2016年1月1日 For open circuit grinding [34,35], there is no disagreement with the calculation of the circulating load and classification efficiency, both of which 2 can be characterized relatively accurately(PDF) Analysis of the efficiency of the grinding process in closed In the mill, the mixture of medium, ore, and water, known as the mill charge, is intimately mixed, the medium comminuting the particles by any of the above methods Apart from laboratory testing, grinding in mineral processing is a continuous process, material being fed at a controlled rate into one end of the mill and discharging at the other end after a suitable dwell (residence) timeGrinding Mill an overview ScienceDirect Topics
.jpg)
Operating experience with a vertical roller mill for
2012年3月1日 Vertical roller mills are the mills traditionally used for processing granulated blastfurnace slag and for grinding composite cements From the energy aspect they are superior to grinding plant Factors Influencing Energy Requirements: Material properties, such as hardness and brittleness, along with machinespecific factors, impact the energy and power requirements in comminuting Crushing Efficiency and Rittinger’s Law: Crushing Efficiency: Crushing efficiency is a measure of how well a crushing process converts input32 Principles of comminuting Crushing and Grinding ForcesAGICO is a leading cement industry equipment supplier based in China It can not only supply all kinds of slag powder grinding equipment including ball mill, vertical roller mill, and roller press, but also provide you with a complete turnkey solution for ground granulated blastfurnace slag (GGBS) productionThrough cooperation with Luoyang Design Institue, Tianjin Design GGBS Production Line Slag Mill for Slag Powder Grinding AGICO2021年7月1日 Some surface pretreatment methods borrowed lessons from the treatment of coal, such as mechanical grinding [73], [74], ultrasonic methods [75], [76], microwave methods [77], [78] and heating methods [79], [80], can eliminate oxygencontaining functional groups, reducing the surface oxygen/carbon ratio and improving floatability to a certain extentReview of the characteristics and graded utilisation of coal
.jpg)
How grinding mill design changed over the last 30 years
2020年6月3日 Effect of OEM mergers on grinding mill design A wave of grinding mill OEM mergers took place in the 70’s and 80’s During those years, only a handful of OEM’s were competing with one another, and no more than two or three could bid 2017年9月1日 In this case, the ball mill, which produces more elongated particles, may be preferred over the stirred mill Differences in product shapes are attributed to the different grinding methods used in Fine grinding: How mill type affects particle shape ResearchGate%PDF16 %âãÏÓ 4215 0 obj > endobj 4235 0 obj >/Encrypt 4216 0 R/Filter/FlateDecode/ID[87C03FABF6FB2246BC4F9AB649B4B217>]/Index[4215 26]/Info 4214 0 R/Length 101 AusIMM – Leading the way for people in resources2017年2月17日 When making comparisons of the efficiencies of different grinding and crushing machines it is desirable to be able to estimate the work actually done in crushing the ore from a given size of feed to a given size of product, the screen analysis of both feed and product being determined Messrs Klug and Taylor, in a paper on this subject, published in the monthly Difference between Crushing and Grinding 911Metallurgist
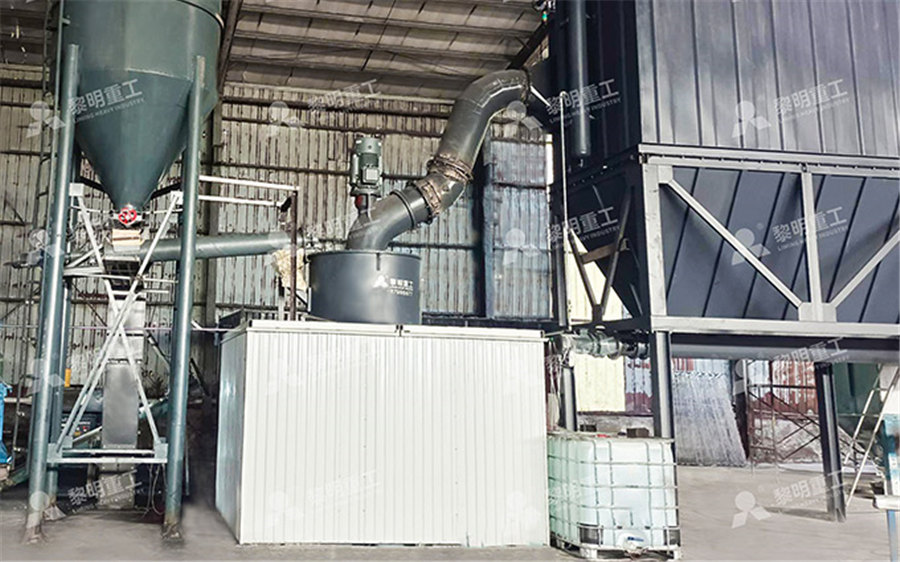
EnergyEfficient Advanced Ultrafine Grinding of Particles Using
2023年7月10日 The present literature review explores the energyefficient ultrafine grinding of particles using stirred mills The review provides an overview of the different techniques for size reduction and the impact of energy requirements on the choice of stirred mills It also discusses the factors, including the design, operating parameters, and feed material properties,