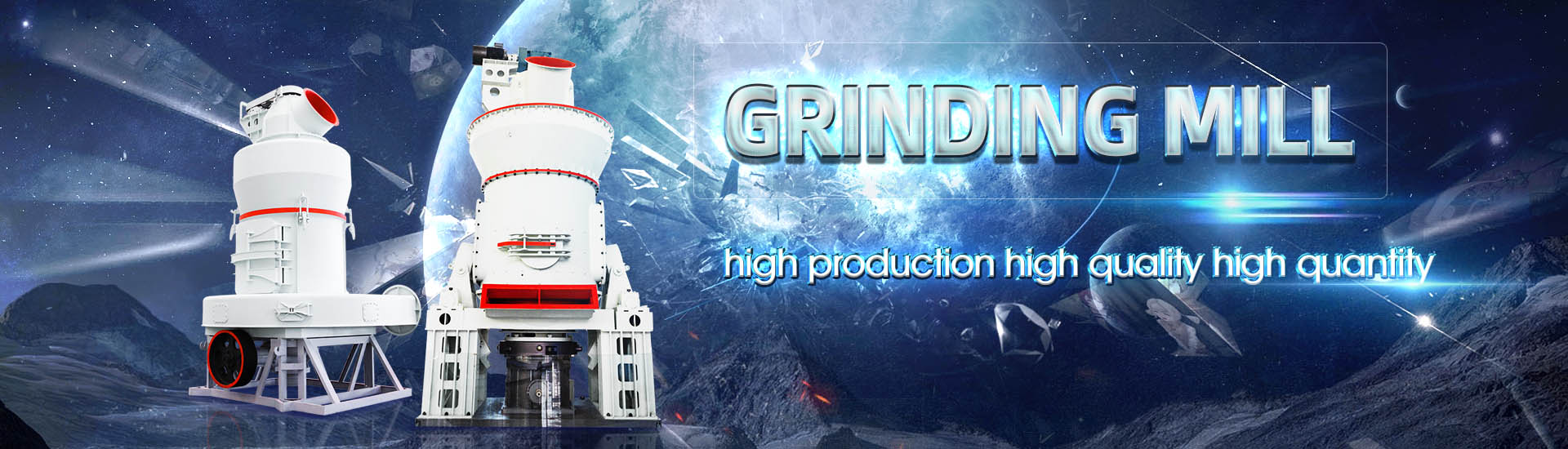
NPF1416 ore mill liner 18
2FD{P}PC]854]XQ.jpg)
Semiautogenous grinding (SAG) mill liner design and development
SAG mill liner development draws primarily on practical experience from SAG milling operations supported by computerbased modeling of charge motion in SAG mills and on established predicting mill trajectory > Optimise speeds, liner height, bar spacing, etc > For large SAG mills the new liners can be 73% critical whilst worn liners require 80% criticalThe Selection Design and Application of Mill Liners for Large Wet highlighted the significance of correct mill liner selection Liners protect the mill shell from wear and transfer energy to the grinding charge, and a careful balance is required to optimise these The Selection and Design of Mill Liners 911 MetallurgistOptimal mill lining solution for your specific mill Promote safety, improve grinding efficiency, reduce downtime and enhance profitability Metallic, PolyMet™, Megaliner™, Rubber and Mill liners Metso
.jpg)
Semiautogenous mill liners Designs, alloys, and maintenance
Fig 1 Semiautogenous mill rail liner Whether the mill is to be fully autogenous (FAG) or semiautogenous (SAG), there are some basic design concepts to remember Abrasive slurry Orebed is a mill liner with totally unique properties If you have a Vertimill or a pebble mill with magnetic ore, Orebed is the superior solution for you offered only by Metso Selecting Orebed, Orebed™ mill liners Metso2006年1月1日 PDF Dramatic shortcomings of mill liner designs, especially of large semiautogenous grinding (SAG) millssuch as rapid failure, mill shell damage Find, read (PDF) Selection and design of mill liners ResearchGateIn spite of initial difficulties, large autogenous and semiautogenous mills have reached an acceptable level of technology that provides the mineral engineer with a reliable, low cost Semiautogenous mill liners: Designs, alloys, and maintenance
.jpg)
Key considerations when selecting a mill lining system
2020年1月27日 Rubber and composite mill liners are increasing in popularity, with several advantages when compared to metal mill liners: Ease and speed of manufacture, with shorter primary mill for grinding coarse ore directly from the crushed stockpile Such application requires a more aggressive liner profile with high lifter bars and relatively thin intermediate plates This Three factors that determine the wear life and performance of mill Extend mill life and improve grinding efficiency with our durable mill liners Designed for optimal wear resistance and customized to your needs size reduction ratio, and feed grain size As long as no crushed ore larger than 25 mm is fed to the rod mill and no crushed ore larger than 10 mm is fed to the 18 34 2475 15 21 38 31 Mill Liners for Enhanced Performance2015年9月20日 Volume proposed shell liners (m^3) 183 Mass proposed the mill charge included both coarse ore fragments and and hence its potential as a tool for design optimisation of mill linersImproving liner design for efficiency and life
.jpg)
Prediction of tumbling mill liner wear: Abrasion and impact effects
In tumbling mills, liners raise grinding media and ore to transfer energy from mill to load During the course of mill operation, the lifters wear and thus affect the mill performance through Rubber steel alloy composite mill liners can protect the metal or other parts inside the mill from erosion Mill Compared with the metal lining of the mill, the harder the ore is, 18: 14: Elongation at break, % >= 400: 500: 350:Ball Mill LinerTega DynaPrime range has been designed specifically for the bigger size of the mills where modern liner handlers are available Tega DynaPrime has been engineered to reduce the number of pieces being installed inside the mill, substantially reducing the installation downtime for maximum mill operation uptimeTega DynaWear Rubber Mill Liner Manufacturer and Supplier2006年1月1日 The relining time also reduced by 375% with the new liners Powell et al, 2006; Rajamani, 2006;Yahyaei et al, 2009;MalekiMoghaddam et al, 2013;MalekiMoghaddam et al, 2015;Cleary and Owen (PDF) Selection and design of mill liners ResearchGate
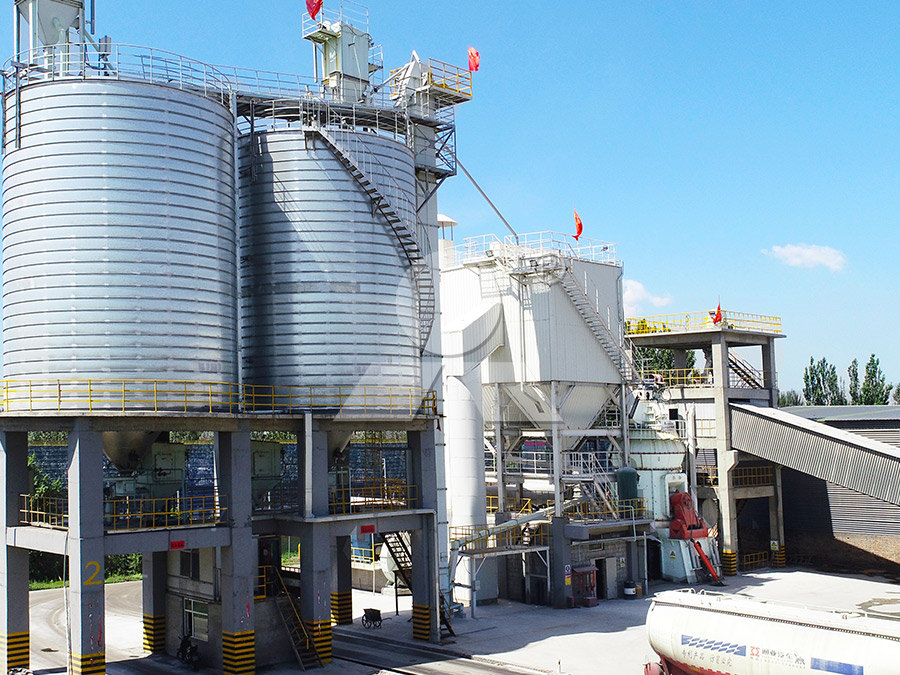
Recommended Ball Mill Speed Liner Configuration
2017年10月25日 For fine grinding (normal rod mill product) mill efficiency and rotational speed are less interdependent (Gow et al, 1934), and therefore slightly reduced speeds may be desirable in order to provide a suitable balance between maximum power rating for a given size of equipment, and provision for future speed up to accomodate a capacity increase or longrange 2011年9月19日 Survey data from three sites treating different ores were used to fit the data to models in JKSimMet The breakage rates obtained from the survey data were extrapolated according to Toor et al QUANTIFYING THE INFLUENCE OF LINER SHAPE AND MILL 2023年6月7日 A trojan horse directs ore into a mill from a conveyor The liners protect the structure of the trojan horse and can be made to the exact geometry that is most advantageous for flow rate and maximum lifespan Possible alloys/materials: 201 (ASTM A532 Class II Different Mill Liners and Alloys to Use Penticton Foundry2020年11月5日 At 1143 cm rib height, the test mill outperformed the mill with conventional full deflector liners with softer ore, but did not perform as well on harder ore By increasing the rib height to 1651 cm, the mill not only drew the required power but also consistently outperformed the mill with the original full deflector liners (Figure 9)Aerofall Mill Liner Design 911Metallurgist
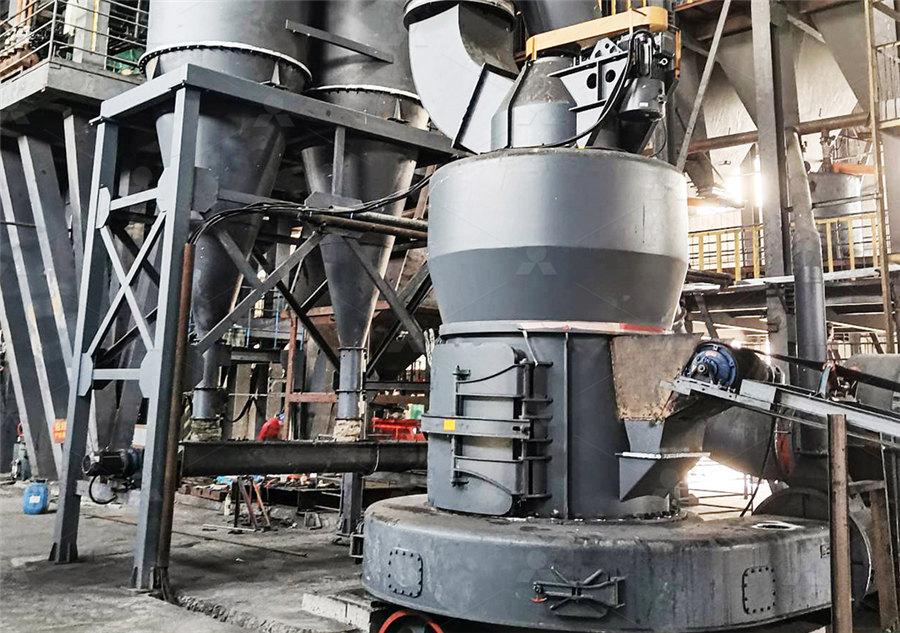
The Selection and Design of Mill Liners ResearchGate
Mines (WA) 36ft SAG mill the number of Outer Head Liners was reduced from 36 to 18 pieces and in doing so reduced the time to replace them by 9 hours at a cost downtime saving of about U$25,000 percycle of mill liners The liner wear reading can be used to calculate available volume inside the mill as the inside mill volume for ore grinding is a function of volume of mill liners The measurement of liners can also be used to estimate the grinding performance and the monetary output of the mill 23 TerminologyEvaluation of Abrasive Wear Measurement Devices of Mill LinersM S POWELL et al 96 11TH MILL OPERATORS’ CONFERENCE 2012 / HOBART, TAS, 29 31 OCTOBER 2012 with optimum mass and life characteristics and enhanced costlife bene ts DEM simulation outputs Powell A more holistic view of mill liner management2021年6月17日 Moreover, the proportion of crushing energy dissipated between steel ball and liner, ore and liner are 188 and 018 %, respectively, and the proportion is small, so the wear of liner is small However, the ratio of crushing energy between the steel ball and the steel ball is 2355 %, which shows that the steel wear is relatively high under this conditionPARAMETER OPTIMIZATION OF LARGE SAG MILL LINER
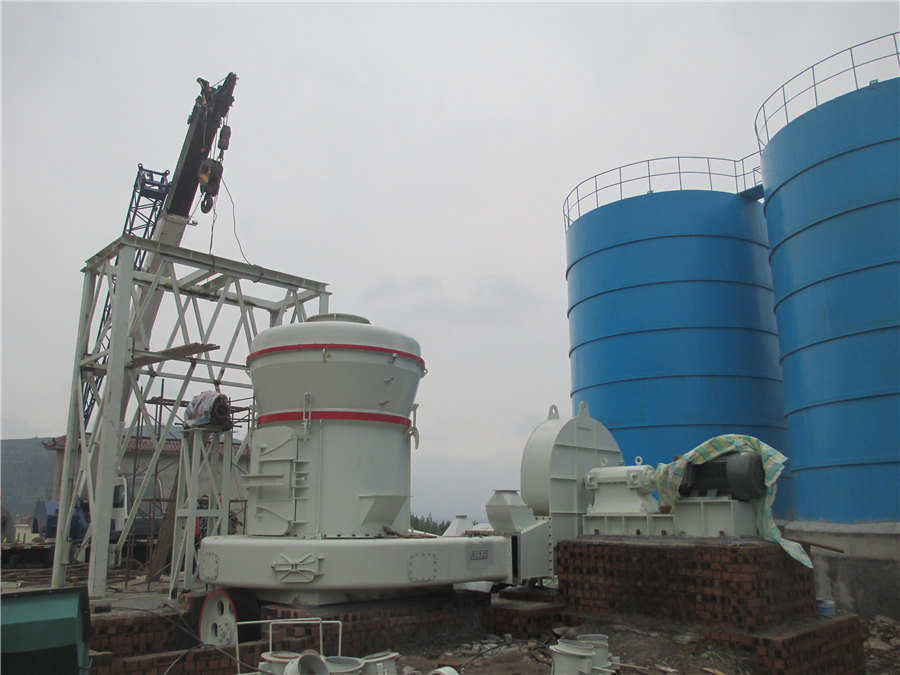
MILL LINER OPTIMISATION
2021 Mill Liner Optimisation Waldo Verster Slide: 2 Introduction Mill Liner Optimisation Grind •Mill Speed •Ore Characteristics •Total volumetric filling •Grinding media type, size and 2021 Mill Liner Optimisation Waldo Verster Slide: 年6月4日 The Metal Magnetic Mill Liner Difference one set of magnetic mill liners was brought to the US for installation into a secondary ball mill used for the grinding of iron ore at Cleveland Metal Magnetic Mill Liner Designed for Secondary and Regrind 5 Table 3 – Ore size distribution Size, mm mean size, mm % retained No of Ore particles in DEM slice 1500 1060 1261 018 2 760 898 033 7 530 635 386 212INTEGRATING LINER PROFILE EVOLUTION AND MILL Mill Liner Market Outlook (2023 to 2033) According to a recently published report by FactMR, the global mill liner market stands at US$ 970 million in 2023 Worldwide demand for mill liners is predicted to rise at a CAGR of 58% and reach a market valuation of US$ 171 billion by 2033end Increasing demand for mill liners is attributed to their advantages, including their use as Mill Liner Market Size, Demand Growth Analysis Report 2033
.jpg)
What Does Mill Liner Do? ball mills supplier
Mill liners are an essential component in grinding mills, providing a protective surface to minimize wear and extend the lifespan of the mill In this article, we will explore what mill liners do, their importance, and the different types available Mill liners are protective components that shield the interior of a grinding mill from the abrasive forces generated by grinding media and oreunique, and so is the equipment it relies on Our mill liners are designed with this reality in mind Every ARMOUR mill liner solution is optimised to your unique equipment needs Using state of the art simulation technology and industry leading expertise, rest assure ARMOUR mill liners are going to protect your mill and perform as they areARMOURTM Mill liner solutions Augmenting grinding excellence 2007年8月1日 SAG mill liner development draws primarily on practical experience from SAG milling operations supported by computerbased modeling of charge motion in SAG mills and on established good design practice Liner design needs to respond to the process aspects of mill liner action that are critical to good SAG mill performance, ie, the impact of shell liners on the Semiautogenous grinding (SAG) mill liner design and developmentcycle of mill liners The liner wear reading can be used to calculate available volume inside the mill as the inside mill volume for ore grinding is a function of volume of mill liners The measurement of liners can also be used to estimate the grinding performance and the monetary output of the mill 23 TerminologyEvaluation of Abrasive Wear Measurement Devices of Mill Liners
.jpg)
Types And Applications Of Mill Liners FC Mill Liners
Discover the diverse types of mill liners and their applications Get highquality mill liners at FC Mill Liners Explore our products now! Skip to content English Menu Toggle English; Español; Contact Us Contact Us 8776603265 877 Ideal for SAG mill (Diameter below 34 ft) and Ball Mill (Diameter between 15ft and 18 ft) DynaSteel® Composite Mill Liners DynaSteel® is tailormade for each mill in question, Increase Mill availability to process more ore; Increase Mill operation time as a result of faster relining; Increase Life as per plant requirement;Tega Dyna Steel Mill Liners for Ball SAG Mills Tega Industries2020年10月1日 When the purchasing of a ball mill is done successfully, it is important to take the stem in which you are carrying out the maintenance on a daily basis and servicing of the ball mill liners is also provided to it, and along with that, the replacement of the ball mill liner is one of the essential work of the maintenance The ball mill liners are nothing but indispensable Ball Mill Liner Replacement2021年2月20日 Iron Ore Mining; ZincLead Mining; Others; By Sales Channel: Direct; Distributors; 1218 Europe Mining Mill Liner Market Size Forecast By Sales Channel 12181 Direct 12182 Distributors 1219 Basis Point Share (BPS) Analysis By Sales Channel 12 Mining Mill Liner Market Report Global Forecast From
.jpg)
Global Mill Liner Market AnalysisSize Forecasts
2024年11月18日 Mill Liner Market Global Mill Liner Industry, Share, Size This report was recently updated on November 18 2024 with the latest and most recent market numbers Report Weir Group announced that they have been awarded with Euros 100 million order for “Australian magnetite iron ore project – Bridge Magnetite Superior design compounds Longer liner life/less liner cost per ton Reduced installation time compared to steel Reduced weight makes it safe to install liners by hand, eliminating the need for a mill liner handler Reduction in noise Reduce noise levels for improved working conditions, and overall noise pollutionRubber Mill Liner Andes Mining2021年4月10日 Dimensions and operation parameters of VTM1500 and its scaleddown version considered in the discrete element method (DEM) simulations (PDF) Industrial Vertical Stirred Mills Screw Liner Wear Profile 2020年2月10日 The shell liner type, rotation speed, and ball filling percent are the key factors influencing the charge behavior inside the SAG mills, and consequently, their performanceAn investigation on effect of shell liner type on performance of
.jpg)
SAG Mill Liner Design
SAG mill liner design and configuration can significantly impact mill performance Key considerations for liner design include lifter spacing and angle, grate open area and aperture size, and pulp lifter design and capacity As mills increase 98 S Kolahi et al / Int J Min GeoEng (IJMGE), 551 (2021) 97107 was conducted through consideration of the total energy dissipation andInvestigation of the effect of industrial ball mill liner type on their Finding the right mill liner will increase the lifespan of your mills and decrease downtime Check out the different types of mill liners you should know Skip to content (780) 4764226 Parts Our Pallet Car component parts are each The Different Types of Mill Liners You Should Know 2011年4月1日 Measurement of the liner wear in the mill of an ore dressing plant is one of the critical parameters in the context of mill downtime and production seconds/revolution on the mill With 18 large Evaluation of Abrasive Wear Measurement Devices of Mill Liners
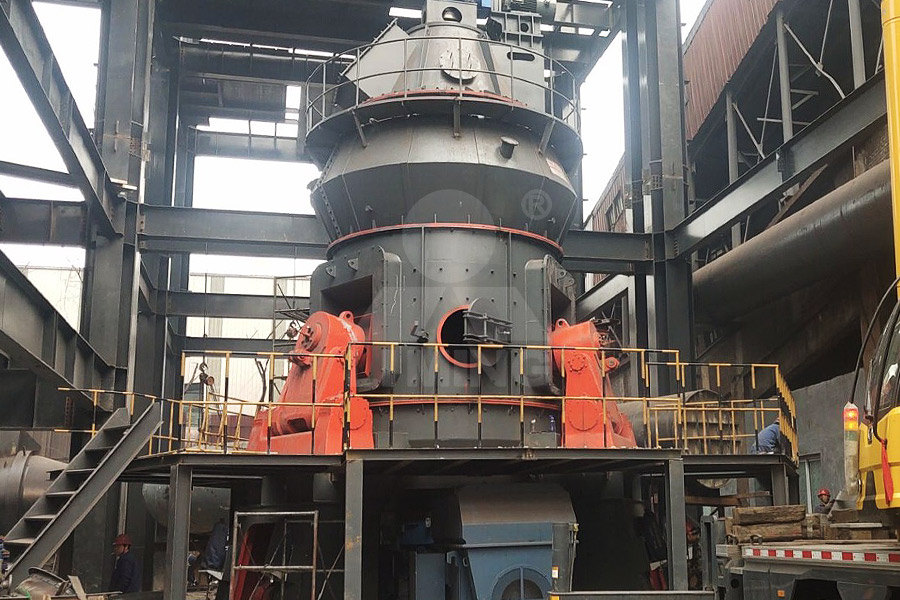
Ball mill liner Wear Parts For Industry Qiming Casting
When the ball grinder works, the lining plate is subject to the dropping the impact of steel balls and materials as well as the sliding wear of steel balls Therefore, the friction between mill liners and material, as well as between mill liners and steel balls, is also an important reason for serious damage to the mill liners Unqualified linerof the mill A new liner design was then designed by increasing the width of the lifter top from 125 to 15 cm and increasing the lifter height from 16 to 26 cm to enhance the liner life Keywords: AG/SAG Mill, Shell Liner, GolEGohar Iron Ore, Wear Profile, NonUniform Design 1 Introduction Mill liner design influences the grindingEvolution of AG mill shell liner design at GolEGohar There are several types of mill liners available, each with its unique properties and benefits The most common types of mill liners include: Steel Liners Steel mill liners are the most widely used type of mill liner, and they are typically made of highstrength steel alloys such as manganese steel, chrome steel, or NihardWhat Are Mill Liners? ball mills supplierRubber mill liners from Multotec extend the lifespan of your mineral processing equipment by protecting the inner shell from impacts and abrasions caused by processing different types of minerals Multotec, a leader in wear solutions, has developed optimised rubber mill liner designs that result in less wear than standard linersRubber Mill Liners Multotec
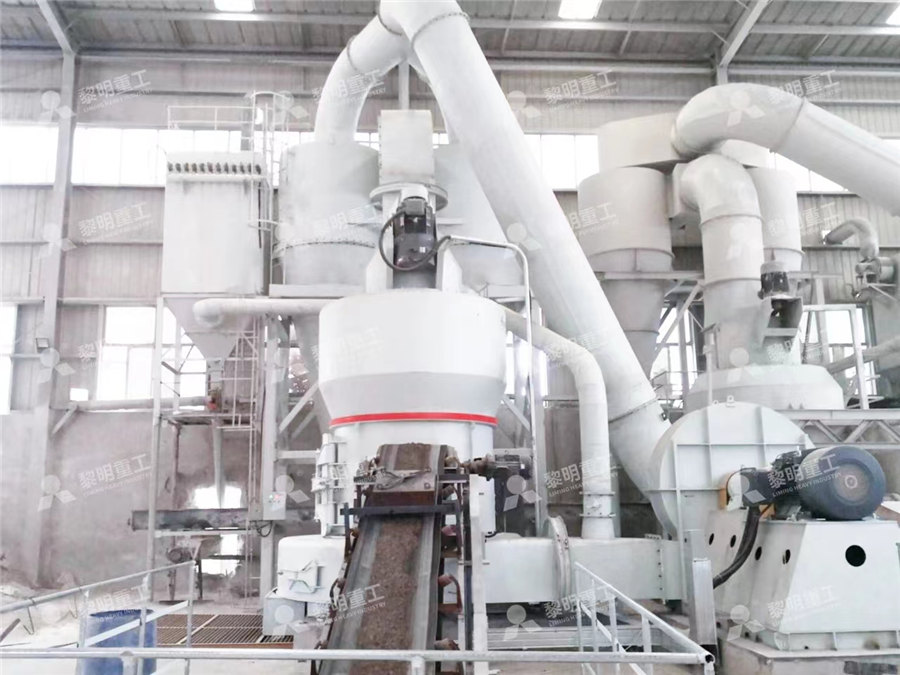
Evaluation of abrasive wear measurement devices of mill liners
Measurement of the liner wear in the mill of an ore dressing plant is one of the critical parameters in the context of mill downtime and production performance 18 1 Excerpt; Save Experimental analysis of charge dynamics in tumbling mills by vibration signature technique B Behera BK Mishra CVR Murty Engineering2016年11月12日 This curve is seen to be, very roughly, of the same form as that of Fig 518, relation to the total surface produced The agreement with the general form of Fig 35 relating the power input to the mill, is not so good for the higher mill fillings; the rate of metal wear being much higher than the power inputGrinding Media Lining Media Liner Wear Rate Modelling