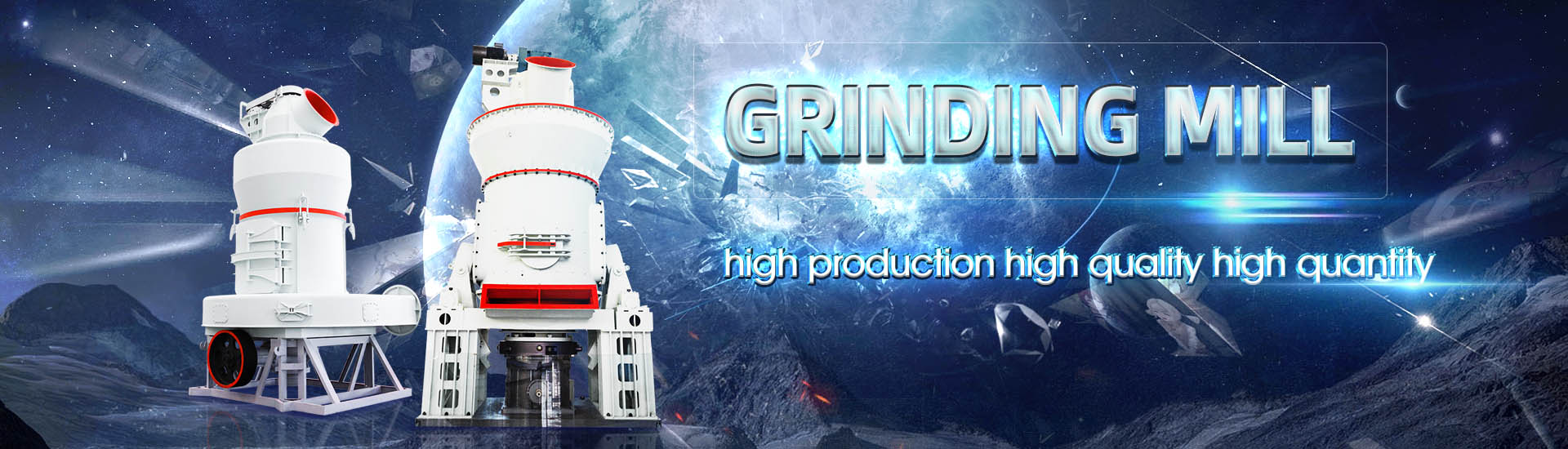
Chengdu coal raw coal mill

A Modeling and Optimizing Method for Electricity Current
Coal mill is an important auxiliary device for coalfired boilers since it directly influences the boiler combustion The coal mill grinds the raw coal to a certain fineness, and then, the coal powder 2023年7月27日 With an area of 500 m2, Chengdu R D Center is one important research platform of Sinoma Int It is outfit with raw material and fuel analysis lab, engineering lab, CDIDCS lab, technology exchange center, Chengdu R D CenterInnovation PlatformR2013年11月20日 Coal mill is an important component of the thermal power plant It is used to grind and dry the moisturized raw coal and transport the pulverized coal – air mixture to the Modeling and Control of Coal Mill NTNU2012年5月1日 The paper presents development and validation of a coal mill model to be used for improved mill control, which may lead to a better load following capability of power plants Derivation and validation of a coal mill model for control
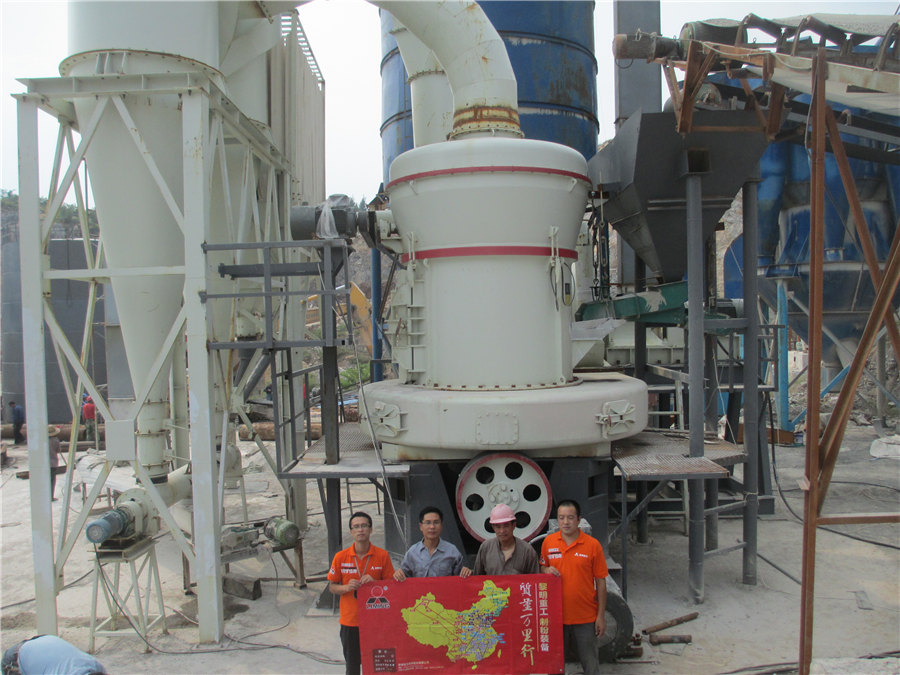
A unified thermomechanical model for coal mill operation
2015年11月1日 Coal mills are bottleneck in coal–fired power generation process due to difficulty in developing efficient controls and faults occurring inside the mills In this paper, a dynamic 2021年8月1日 Raw coal moisture estimation which is connected to coal mass and internal energy in coal mills is included in the model The model has proved to have good predictions Coal mill model considering heat transfer effect on mass 2022年3月25日 The work presented in this paper focuses on modeling Mill Parter Shiptype coal mills that are widely used in the coalfired power plants in China The unknown model parameters are(PDF) A Modeling and Optimizing Method for 2020年8月12日 This study shows the performance of a currently running vertical roller coal mill (VRM) in an existing coalfired power plant In a power plant, the coal mill is the critical An investigation of performance characteristics and
.jpg)
Modeling and Parameter Identification of Coal Mill
2024年1月18日 The coal mills grind and dry the moisturized raw coal and transport the pulverized coal to the boiler burner Their poor dynamic performance causes a slow load take 2023年6月10日 A coal mill is an important component of a steam power plant which grinds precrushed raw coal particles of size 1020 mm to fine particles of size less than 150 µm using Mathematical validation and comparison of ball tube A simple energy balance model of the coal mill is derived in (Odgaard and Mataji 2006), this model is based on a more detailed model found in (Rees and Fan 2003)In this model the coal mill is seen as one body with the mass m mThe following variables are defined: T(t) is the temperature in the coal dust flow in the mill, ṁ PA (t) is the primary air mass flow, T PA (t) is Coal Mill an overview ScienceDirect Topics2013年11月20日 Coal mill is an important component of the thermal power pla nt It is used to grind and dry the moisturized raw coal and transport the pulverized coal ± air mixture to the boiler Poor dynamic performance of coal mill will lead to decrease in the overall efficiency of the power plant, slow load take up rate and fr equent shut downModeling and Control of Coal Mill NTNU
.jpg)
A Study on 500 MW Coal Fired Boiler Unit’s Bowl Mill
15 Mill Wear and Ash Content in Raw Coal The coal is abrasive in nature due to the presence of hard materials like pyrites, α quartz etc, Due to the grinding nature and abrasiveness of coal, the mill parts tend to wear depending on the hours of service and 2024年10月31日 Coal mills, also known as pulverizers, play a critical role in power plants by grinding coal into fine powder, which is then used in various pyroprocesses Be sure about that! Evaluation of a coal grinding system’s fire and explosion protection, including the raw coal storage and the fine coal silo storage normally can be done in one day Coal Mill Safety: A Critical Aspect of Power Plant Operations Coal 2012年11月17日 15 10Bowl Mill Bowl mills are employed to pulverize the precrushed raw coal to the required fineness before it is admitted into the boiler furnace for combustion The mill output can be easily varied, as per the turndown ratio from its minimum to maximum load Crushed raw coal at a controlled rate is fed into the revolving bowl of the Bowl Mill Centrifugal force feeds Coal mill pulverizer in thermal power plants PPT SlideShare2024年10月15日 The raw coal enters the vertical mill bin: The reducer drives the millstone to rotate, and the mixed raw coal and CNS enters the mill through the feed port, scattering on the millstone The controlling of this parameters is required: Mill feed 30 Cashew Nutshell and Raw Coal Cogrinding for Sustainability
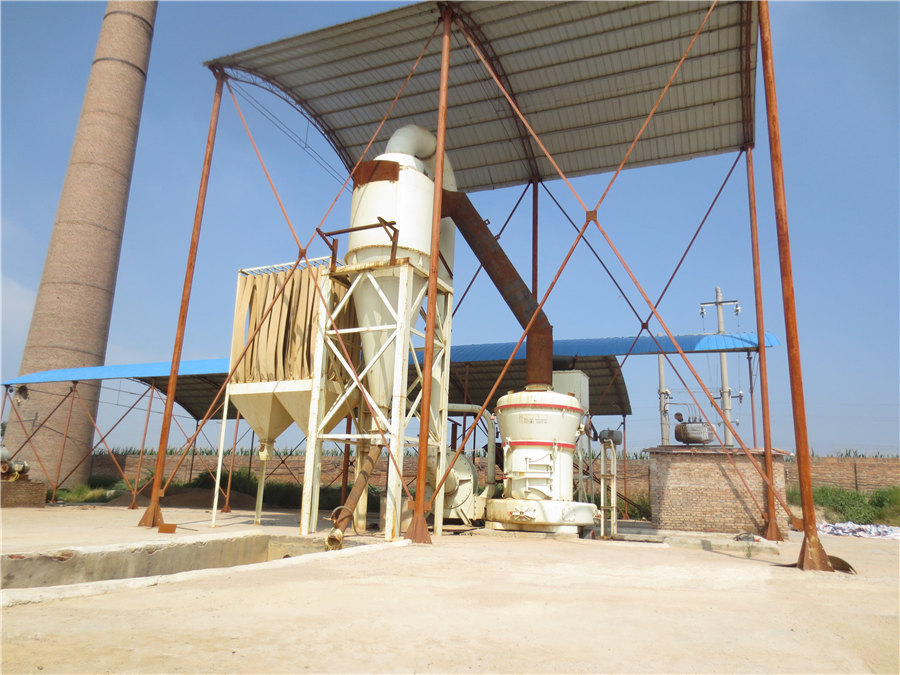
(PDF) Modeling and Parameter Identification of Coal Mill
2009年9月20日 A control oriented model was then developed by Fan (1994) and Fan and Rees (1994) In 2009, coal flow and outlet temperature of mill were modelled using mass and heat balance equations for startup 2021年8月1日 Yukio et al [7] proposed a model consisting of blending, grinding and classifying processes for pulverizer control Agarawal et al [8] differentiated coal powder into ten size groups, divided the bowl mill into four zones, and developed a unified model Palizban et al [9] derived nonlinear differential mass equations of raw coal, recirculation coal and suspension coal in Coal mill model considering heat transfer effect on mass 2014年1月1日 The commissioning was troublefree and no different from grinding plants for cement raw material, limestone or coal coal mill, crushing and cement mill was 0156 clinker g/t, 3914 clinker g (PDF) MPS mills for coal grinding ResearchGate2018年12月21日 This flow sheet and sampling map shows the process flow for a cement plant Key components include: 1) Raw materials like iron sand, silica sand, limestone, clay and gypsum being fed into crushers and mills 2) Processed materials being fed into kiln systems for heating and clinkering 3) Clinker being stored and transported to other cement plants or customers 4) Flow Sheet Kiln, Raw Mill N Coal Mill PDF Cement Concrete
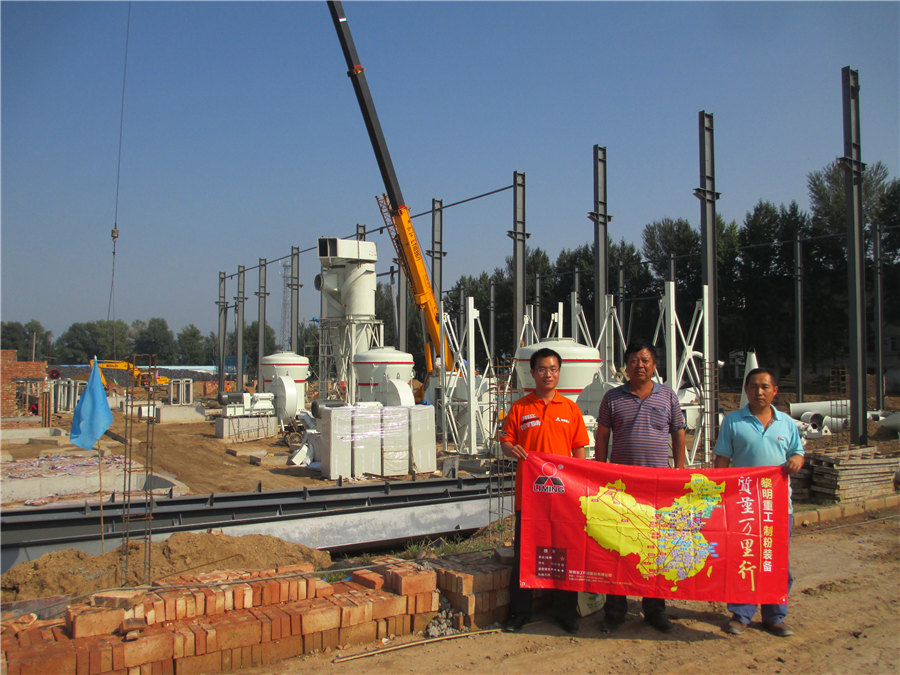
Coal Water Slurry Ball Mill
The raw coal and lump coal are coarsely crushed by the crusher and crushed to 3mm to meet the feed size of the CWS ball mill The cleaned coal obtained by flotation is mixed and stirred in a mixing tank by adding a certain proportion of 2021年4月27日 Coal Mill Temperatures Coal mill hot air inlet temperatures never be more than 600should F and the outlet temperature should not exceed 200°F on Raymond coal mills If the flow of raw coal to the coal mill is interrupted for any reason (for example: plugging, failure of the coal feeder, etc), the outlet temperature of the coal mill can COAL GRINDING SYSTEMS SAFETY CONSIDERATIONSThe coal mill grinds the raw coal to a certain fineness, and then, the coal powder is carried to the burners by first air of boiler combustion During this grinding process, a large quantity of electricity power (generally onethird) is consumed On the other hand, this grinding process also affects the combustion efficiency by coal fineness A Modeling and Optimizing Method for Electricity Current 2020年4月2日 Milling system in coal power plant purposely to process the raw coal to become as pulverise fuel before enter to the boiler furnace Coal mill motor power (kW) 0 4171 4548 4390 Analysis of the Coal Milling Operations to the Boiler Parameters
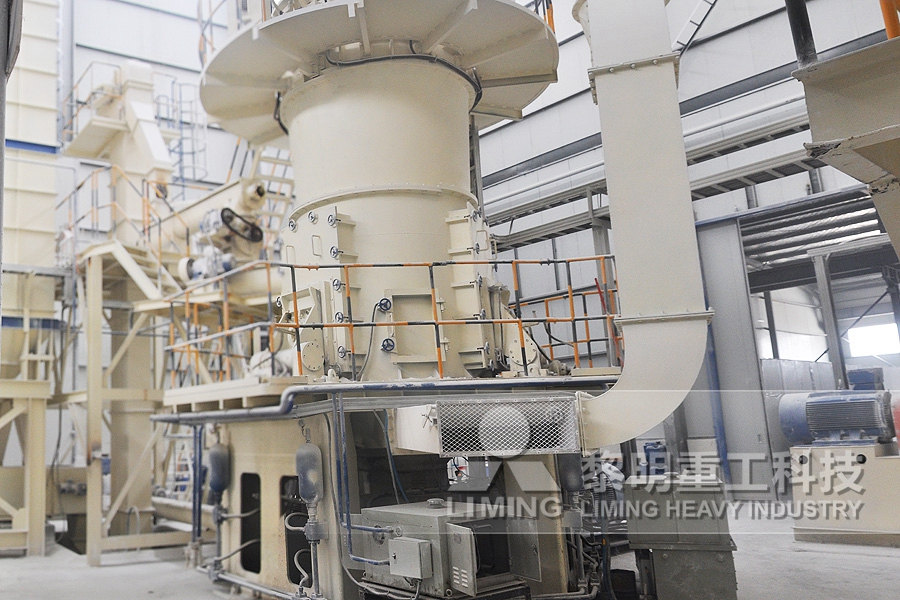
(PDF) Modeling and Control of Coal Mill Academia
The input raw coal flow into the mill is also difficult to be measured Generally, the speed of the conveyor belt will be used for this purpose Additionally, estimation of varying coal quality, type of coal, moisture content present in the inlet raw coal is difficult Due to these problems, control algorithms lead to poor performance when load 2020年8月14日 The coal mill is one of the important auxiliary engines in the coalfired power station Its operation status is directly related to the safe and steady operation of the units(PDF) Application of ModelBased Deep Learning Algorithm in Fault 2024年10月31日 Coal Mill Safety In Cement Production Industries It may come as a surprise, but cement industry is not capturing nearly as many coal dust explosions that actually occur These incidents are often reported as boiler explosions or something else because there is no mention of the fuel involved Raw coal silo protection against fire and Coal Mill Safety In Cement Production Industries2018年6月7日 – Interruptions in raw coal feed – Lower feeder speeds – This occurs because a minimum airflow through the coal mill must be maintained to insure that burner line velocities are not too low to allow settling of coal in the fuel lines or burner components – Not uncommon to achieve air to fuel ratios of 3 to 5 pounds of air per pound Mill Inerting and Pulverizer/Mill Explosion Mitigation
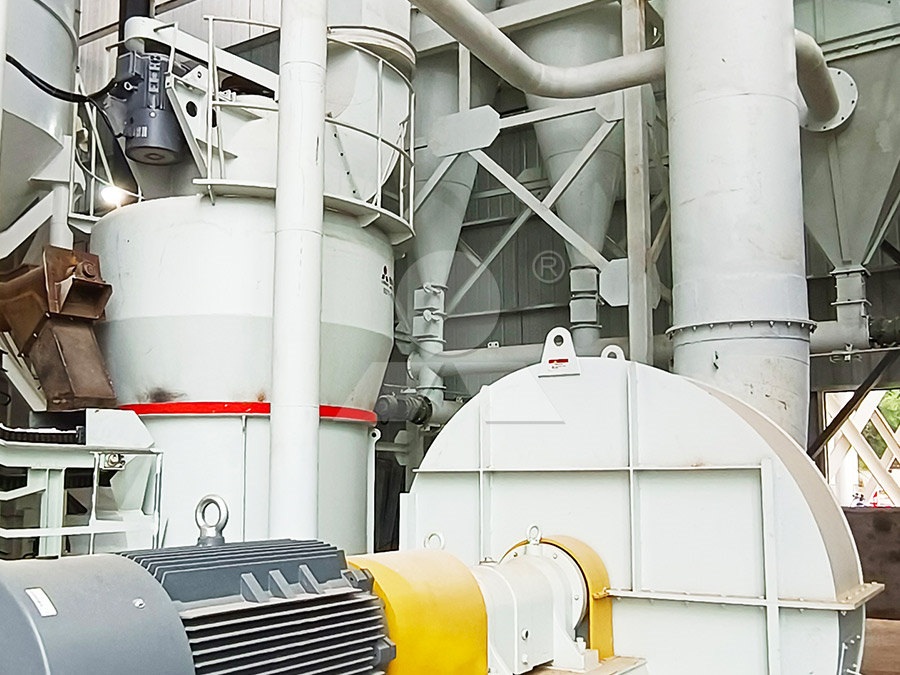
Coal Mill in Cement Plant Vertical Roller Mill AirSwept Ball Mill
A coal mill is also called a coal pulverizer or coal grinder It is a mechanical device used to grind raw coal into pulverized coal powders The most used coal mills in cement plants are airswept ball mills and vertical roller mills At present, most cement plants use coal as the main fuel in the clinker production process2024年9月28日 GC: What led you to establish Coal Mill Safety? VG: I established Coal Mill Safety (CMS) as a consultancy after I ‘retired’ in 2011 If a cement producer wants to install a new coal grinding system, they can commission CMS to look at the supplier’s design and probe it from a safety angle If it has an existingIn discussion: Vincent Grosskopf, Coal Mill Safety2024年10月31日 You will be surprised about what has gone wrong with fire and explosion protection of your system(s) Be sure about that! Evaluation of a coal grinding system’s fire and explosion protection, including the raw coal storage and the fine coal silo storage normally can be done in one day, mostly without having to stop coal grindingSafe operation of coal grinding systems: Raw coal yard 2024年1月11日 With a vertical roller mill (VRM) VRMs consist of a rotating table or bowl and rollers 1 To grind the coal, feed raw or initially crushed coal into the mill which is then ground between the rotating components; 2 Finally, hot air How to Process Coal into Pulverized Coal in 5
.jpg)
Coal Mills for Cement Plants Loesche
2024年11月26日 Coal grinding mills LOESCHE coal grinding mills are distinguished by characteristics that improve efficiency, safety and environmental protection, from the standard version to topoftherange installations Special 4 天之前 Process introduction Vertical coal mill, also known as vertical roller coal mill or vertical coal grinding mill, is a mechanical equipment for crushing and grinding coal into coal powerMainly used for grinding raw coal, bituminous coal, and other fuels into coal powder, which is supplied to rotary kiln and other kilns in the cement plant and thermal power plantcoal grinding machine CHAENG2020年1月1日 Coal mills have a significant influence on the reliability, efficiency, and safe operation of a coalfired power plant Coal blockage is one of the main reasons for coal mill malfunctionEarly Warning of Critical Blockage in Coal Mills Based on 2024年10月31日 proposed a coal mill model that considers the effect of coal moisture on its accuracy, and the model can effectively represent the midhigh process of coal mill dynamics and estimate the key parameters in coal mills Grudziak et al [ 7] monitored the temperature of a dust–air mixture at the outlet of a coal mill an usingOptimization of the pulverized system of the coalfired
.jpg)
Coal Grinding Cement Plant Optimization
Elements of Coal Grinding System: Mill Feeding: Consists of following activities Coal Crusher: Generally, require when ball mill is used for grinding and raw coal size is on higher side(>25mm) Conveying to Hoppers: Covered belt conveyors, horizontal or inclined are most suitable and commonly used for conveying Metal Detector and Magnetic 2022年2月24日 1 – raw coal hopper; 2 – gate of a tape feeder; 3 – belt fuel feeder (BFF); 4 – ball drum mill; a weight load of the mill with coal of 1500 g, equal to 187 g/hImproving the efficiency of the coal grinding process in ball 2024年5月1日 The applicable coal types are bituminous coal, partly poor coal and partly lignite For normal operation of coal mill, the hardgrove grind ability index is between 40 and 80; the particle size of raw coal is smaller than 40 mm Additional specific technical data for the coal mills are listed in Table 1 The working process of this coal mill is Dual fault warning method for coal mill based on2015年11月1日 The coal mill grinds the raw coal into fine powder and hot air entering the mill dries and carries the pulverized coal to the burners of the furnace Maffezzoni (1986) emphasized that coal mills are the primary cause of slow load following capability and regular plant shutdowns A major problem in plant’s load control is the inability of the A unified thermomechanical model for coal mill operation
.jpg)
Coal Mill an overview ScienceDirect Topics
A simple energy balance model of the coal mill is derived in (Odgaard and Mataji 2006), this model is based on a more detailed model found in (Rees and Fan 2003)In this model the coal mill is seen as one body with the mass m mThe following variables are defined: T(t) is the temperature in the coal dust flow in the mill, ṁ PA (t) is the primary air mass flow, T PA (t) is 2013年11月20日 Coal mill is an important component of the thermal power pla nt It is used to grind and dry the moisturized raw coal and transport the pulverized coal ± air mixture to the boiler Poor dynamic performance of coal mill will lead to decrease in the overall efficiency of the power plant, slow load take up rate and fr equent shut downModeling and Control of Coal Mill NTNU15 Mill Wear and Ash Content in Raw Coal The coal is abrasive in nature due to the presence of hard materials like pyrites, α quartz etc, Due to the grinding nature and abrasiveness of coal, the mill parts tend to wear depending on the hours of service and A Study on 500 MW Coal Fired Boiler Unit’s Bowl Mill 2024年10月31日 Coal mills, also known as pulverizers, play a critical role in power plants by grinding coal into fine powder, which is then used in various pyroprocesses Be sure about that! Evaluation of a coal grinding system’s fire and explosion protection, including the raw coal storage and the fine coal silo storage normally can be done in one day Coal Mill Safety: A Critical Aspect of Power Plant Operations Coal

Coal mill pulverizer in thermal power plants PPT SlideShare
2012年11月17日 15 10Bowl Mill Bowl mills are employed to pulverize the precrushed raw coal to the required fineness before it is admitted into the boiler furnace for combustion The mill output can be easily varied, as per the turndown ratio from its minimum to maximum load Crushed raw coal at a controlled rate is fed into the revolving bowl of the Bowl Mill Centrifugal force feeds 2024年10月15日 The raw coal enters the vertical mill bin: The reducer drives the millstone to rotate, and the mixed raw coal and CNS enters the mill through the feed port, scattering on the millstone The controlling of this parameters is required: Mill feed 30 Cashew Nutshell and Raw Coal Cogrinding for Sustainability 2009年9月20日 A control oriented model was then developed by Fan (1994) and Fan and Rees (1994) In 2009, coal flow and outlet temperature of mill were modelled using mass and heat balance equations for startup (PDF) Modeling and Parameter Identification of Coal Mill2021年8月1日 Yukio et al [7] proposed a model consisting of blending, grinding and classifying processes for pulverizer control Agarawal et al [8] differentiated coal powder into ten size groups, divided the bowl mill into four zones, and developed a unified model Palizban et al [9] derived nonlinear differential mass equations of raw coal, recirculation coal and suspension coal in Coal mill model considering heat transfer effect on mass
.jpg)
(PDF) MPS mills for coal grinding ResearchGate
2014年1月1日 The commissioning was troublefree and no different from grinding plants for cement raw material, limestone or coal coal mill, crushing and cement mill was 0156 clinker g/t, 3914 clinker g 2018年12月21日 This flow sheet and sampling map shows the process flow for a cement plant Key components include: 1) Raw materials like iron sand, silica sand, limestone, clay and gypsum being fed into crushers and mills 2) Processed materials being fed into kiln systems for heating and clinkering 3) Clinker being stored and transported to other cement plants or customers 4) Flow Sheet Kiln, Raw Mill N Coal Mill PDF Cement Concrete