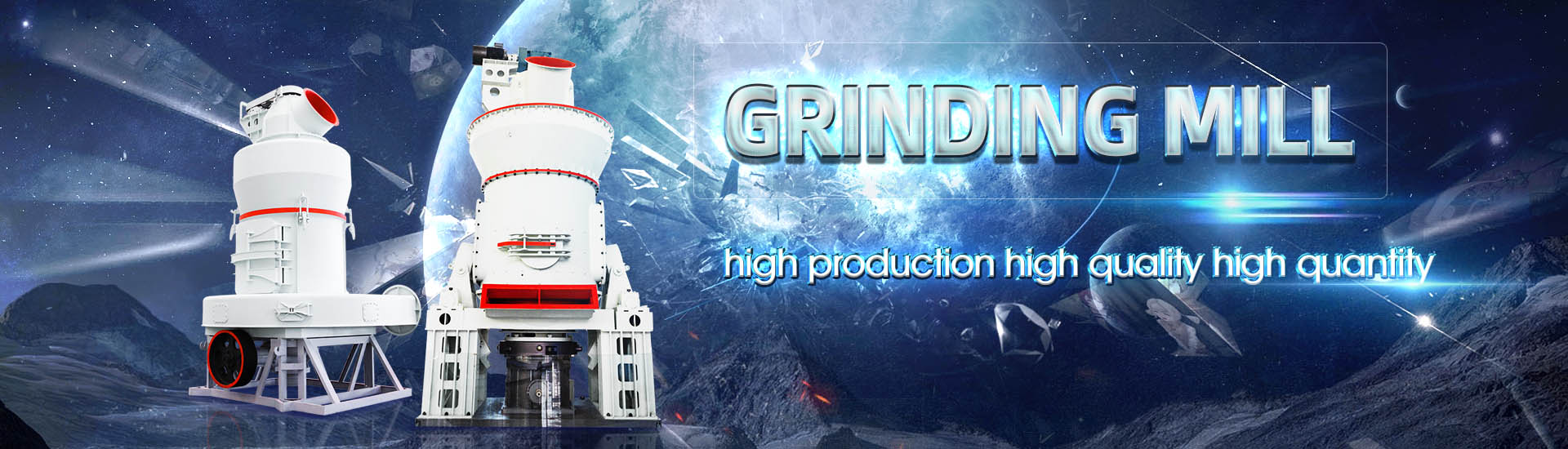
Working principle of granite clinker powder making process

Process characteristics of clinker and cement production
2018年11月30日 Purpose: Optimization of the oxyfuel clinker burning process based on process modeling verified by prototype results Oxyfuel principle: Air is replaced by recirculated CO2011年7月1日 “Chemistry” and “process engineering” constitute the foundation of the clinkerization process but over the decades the engineering advances have been phenomenal Chemistry and engineering of the clinkerization process — 2012年11月8日 Raw materials crushing and grinding seeks to reduce materials from roughly one meter cubes of blasted stone to a size where at least 80 percent of the raw material is less Breakthrough in Clinker Grinding Massachusetts 2023年2月25日 Technological advances of cement kilns over time This article presents the key stages in the modeling of rotary kilns First, the parameters characterizing the transport of the Rotary kiln process: An overview of physical mechanisms,
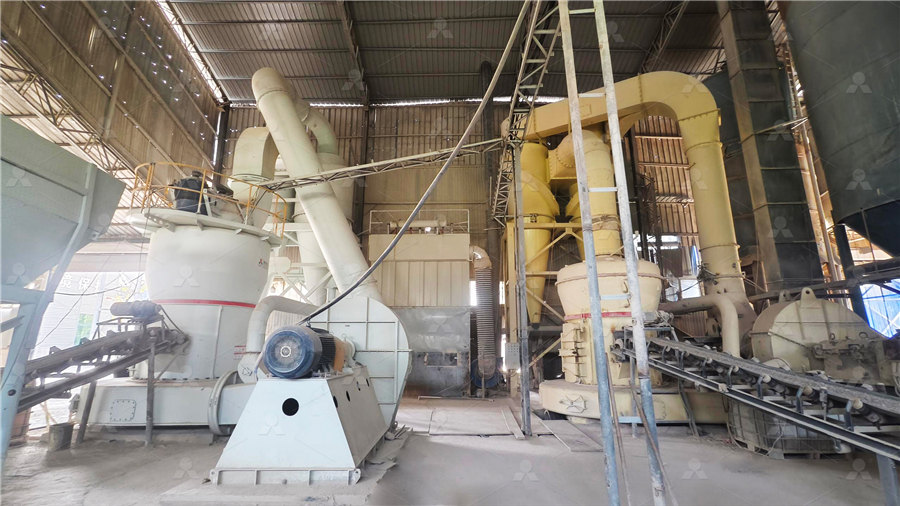
Clinker Production an overview ScienceDirect Topics
Clinker is produced by pyroprocessing in large kilns These kiln systems evaporate the free water in the meal, calcine the carbonate constituents (calcination), and form cement minerals Granite powder has a much smaller grain size than commonly used fine aggregates, so the partial replacement of aggregate with granite powder causes the microstructure of the cement matrix Effect of Granite Powder Grain Size and Grinding Time of the As a result of the indirect mechanosynthesis process, the clinker produced is in powder form This result will impact the reduction in the energy used for the milling clinker when the gypsum is introduced for cement productionCement and Clinker Production by Indirect 2021年4月19日 Herein, we evaluate experimentally the interactions among clinker, limestone and gypsum during the final grinding stage in Portland cement production We present a Resistance to Grinding and Cement Paste Performance of
.jpg)
Portland Cement Clinker SpringerLink
2014年1月1日 Clinkering process can be divided in two stage: the reactions in the solid state, at lower temperature to about 1300 °C and at 1450 °C, with 25 % of the melt For understanding 2023年6月27日 Discrete Element Methods (DEM) is a numerical tool consolidated to the simulations of collisions in particulate systems In this paper, the method was used to study Experimental study of clinker grinding in a ball mill and 5 天之前 The manufacture of Portland cement is a complex process and done in the following steps: grinding the raw materials, mixing them in certain proportions depending upon their purity and composition, and burning them to sintering in Manufacturing of Portland Cement – Process Working principle Raw mills uses pressure and shear generated between the rollers and rotating table to crush and grind limestone, basalt and sandstone Air slide pneumatic conveying equipment used to convey dry and powder Cement Manufacturing Process INFINITY FOR
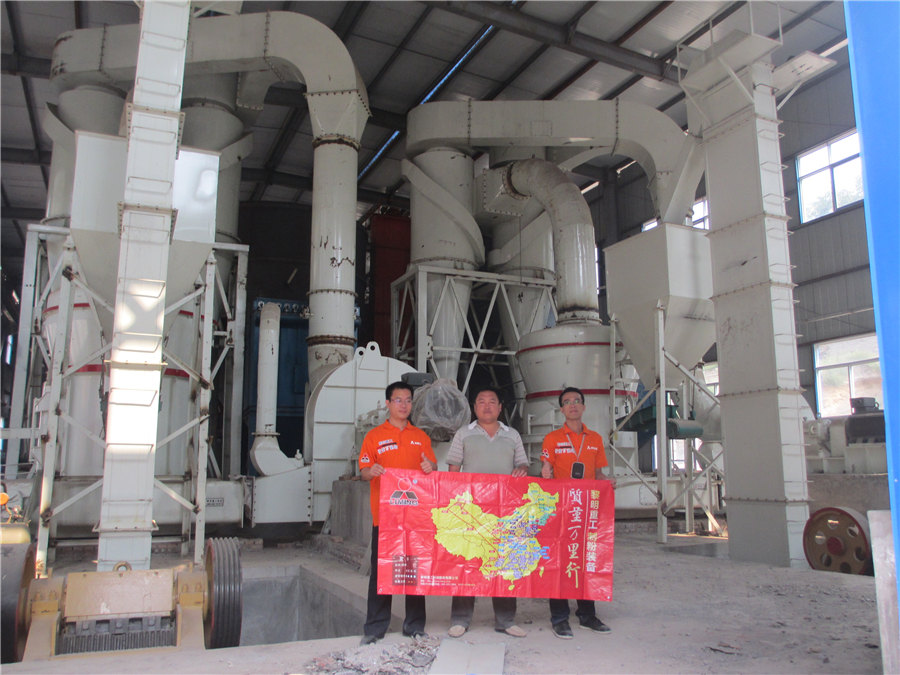
Comprehensive Guide to Cement Kilns:
This process is critical because even slight deviations can affect the quality of the clinker Grinding: The proportioned raw materials are then ground into a fine powder using large grinding mills This step increases the surface area of the 2014年6月10日 It begins with an overview of what cement is and how it is used to make concrete It then describes the industrial process for manufacturing cement, involving grinding raw materials like limestone and clay at high temperatures in a kiln to form clinker, which is then pulverized with gypsum to become Portland cement powderCement manufacturing process PPT Free Download2023年12月20日 The clinker is ground to a fine powder in a cement mill and mixed with gypsum to create cement The powdered cement is then mixed with water and aggregates to form concrete that is used in construction The complex process of making cement starts with the mining of raw materials like limestone and clay, which are then ground into a fine The Cement Manufacturing Process Thermo Fisher Scientific2021年3月24日 Overview of the conceptualized clinker cooler and clinker furnace where: Hw is the hot zone height, Hc is the cold zone height, í µí° í µí° ¶í µí± í µí± is the clinker density Modelling of clinker cooler and evaluation of its

Process characteristics of clinker and cement production
2018年11月30日 Continuous high temperature process in the cement industry: Calcination and cement clinker burning Calcination of raw material CaCO 3 => CaO + CO 2 Process emissions of raw material: = 054 t CO 2 /t clinker Endotherm reaction at 950 °C ca 1700 MJ/t clinker ≈ 50% of energy Cement clinker burning at 1450 °C formation of hydraulicAfter cooling, the clinker may be stored temporarily in a clinker store, or it may pass directly to the cement mill The cement mill grinds the clinker to a fine powder A small amount of gypsum a form of calcium sulfate is normally ground up with the clinker The gypsum controls the setting properties of the cement when water is addedCement manufacturing components of a cement plant2018年7月31日 In cement plants clinker outlet temperature is directly evaluated by clinker cooler process efficiency Cooling processes may be evaluated as one of the energy input considering demand of secondary air and carrier gas called clinker which is subsequently ground to find the desired fineness and mixed with some additives to form cement Development of Cooling Performance of Clinker Cooler Process 2021年8月19日 During clinker cooling, a heat exchange occurs be tween the solid material and verti cally incoming fresh air A part of the hot air volume enters the kiln as secondary air,(PDF) Optimizing the Control System of Clinker Cooling: Process
.jpg)
Introduction to the Principles of Cement and Concrete
2021年4月2日 1111 Chemical Compositions Four main compounds make up Portland cement They include tetracalcium aluminoferrites (4CaOAl 2 O 3 Fe 2 O 3), tricalcium aluminates (3CaOAl 2 O 3), dicalcium silicates (2CaOSiO 2), and tricalcium silicates (3CaOSiO 2) (Demis et al 2014)These compounds are abbreviated as C 3 S, C 2 S, C 3 A, and C 4 AF, The grate cooler is a quenching type cement cooler applied for the cement manufacturing plant According to the movement mode of the grate, the grate cooler can be divided into three types, rotary type, vibrating type, and push Grate Cooler In Cement Plant Clinker Cooler, 2021年3月3日 Cement is produced by a hightemperature (about 1500 °C) reaction in a rotary kiln of carefully proportioned and blended ratios of lime (CaO), silica (SiO 2), alumina (Al 2 O 3), and iron oxide (Fe 2 O 3)The production of cement is a chemical process requiring an accurate blend of the previously cited four key organic oxides and the limitation of several undesirable Cement SpringerLink2024年11月23日 Cement Extraction, Processing, Manufacturing: Raw materials employed in the manufacture of cement are extracted by quarrying in the case of hard rocks such as limestones, slates, and some shales, with the aid of blasting when necessary Some deposits are mined by underground methods Softer rocks such as chalk and clay can be dug directly by Cement Extraction, Processing, Manufacturing Britannica
.jpg)
A practical guide to improving cement manufacturing
2024年5月22日 The final stage is to grind the cooled clinker into a fine particle and add gypsum to control the setting time of the cement Mineralogy is important at this stage as well and is measured in the lab by XRD technology Learn more about this process, download the application notes: Analysis of Clinker Phases with the ARL 年10月23日 The Manufacturing Process worldcementassociation 1 Limestone (CaCO3) is taken from a quarry 2 4 3 The limestone is fed into a crusher and then stored until needed The clinker is mixed with additives, such as gypsum, and then ground in a cement mill, which creates cement The cement is then packed and distributed to consumersCement Plant: The Manufacturing Process 4 5 World 2022年9月21日 The study explores the indirect mechanosynthesis process for cement and clinker production, highlighting its impact on global cement outputCement and Clinker Production by Indirect Mechanosynthesis Process2016年9月22日 Large machinery is brought in to extract (or quarry) the granite from openpit mines using wire saws or diamond wire saws Quality control already starts here After quarrying, much of the stone is sold in blocks, and that which is cut into slabs is then split to make other smaller products such as sidewalks, wall blocks or paving stonesThe processing of granite: Step by step CKP
.jpg)
Everything you need to know about Kiln Burning Systems
Pyroprocessing is the heart of the cementmaking process It is usually the major cost element and kiln performance dictates the efficiency, plant output, emissions, product quality, and plant run factors binding clinker particles together This process can repeat until a ring forms This type of ring is most likely to develop where there 1 天前 The process of manufacturing of shaped components or semifinished products such as bar and sheet from metal powder is called as Powder metallurgy The technique of powder metallurgy combines unique technical features with cost effectiveness and generally used to produce sintered hard metals known as ‘carbides’ or ‘tungsten carbides’Introduction To Powder Metallurgy Principles of Powder Metallurgy ProcessWorking principle of rotary cooler Cooler is a kind of refrigeration equipment that is realized by vaporcompression or absorption cycle, the liquid can flow through the heat exchanger to reach for the purpose of the cooling air or equipment, Rotary Cooler Clinker Cooler In Cement PlantThe clinker cooler, also known as grate cooler or cement cooler, it is a necessary equipment of cement clinker productionThe clinker cooler is mainly used to cool and transport the cement clinker At the same time, cement cooler also Clinker Cooler, Cement Cooler, Grate Cooler
.jpg)
(PDF) Spray Drying: An Overview ResearchGate
PDF On May 2, 2018, Daniel Santos and others published Spray Drying: An Overview Find, read and cite all the research you need on ResearchGateAir inlet and outlet is good for air moving and suspension of fuel and materials, which make heat transfer and decompose fast Working principle of precalciner The cement calciner makes the raw meal spread and suspension in the air flow, and ensure the fuel consumption and decarbonation happens in a short timePrecalciner, Calciner In Cement Plant, Cement Calciner2023年4月23日 Figure 1 shows the production process of granite powder waste Due to the significant development of the stitching industry, granite powder waste deposits have increased in recent years, and this Production of granite powder waste Download Scientific 2023年10月19日 Clinker grinders are an important part of the cement manufacturing process They are used to grind clinker into a fine powder and are typically located at the end of the cooler in a cement plant Clinker is a nodular material produced during the cement manufacturing process and is the primary raw material for making cementUnderstanding the Role of Clinker Grinding in Cement
.jpg)
Cement Manufacturing Process Engineering Intro
2012年8月30日 Clinker cooling Cement making process Final process of 5 th phase is the final grinding There is a horizontal filled with steel balls Clinker reach in this rotating drum after cooling Here, steel balls tumble and crush the clinker into a very fine powder This fine powder is considered as cement During grinding gypsum is also added to The quarry stone is delivered through chutes to the crushers, where it is reduced by crushing or pounding to chunks approximately 1 ½ inches in size Calcination is the core portion of the process, in which huge rotary kilns come into play Inside, at 1400 degrees C, the raw material is transformed into clinker: small, dark gray nodules 3 Cement Production: How Cement Is Manufactured CEMEX UKTypes of Extruders: Application and Working Principle : Extruders are one of the most important component which is used in the manufacturing process Whenever these are combined with feeding, cutting, deairing or other form of equipment it can create everything Using the extruder for a combined usage like cooking and cold forming of Types of Extruders: Application Working Principle5 天之前 The manufacture of Portland cement is a complex process and done in the following steps: grinding the raw materials, mixing them in certain proportions depending upon their purity and composition, and burning them to sintering in Manufacturing of Portland Cement – Process
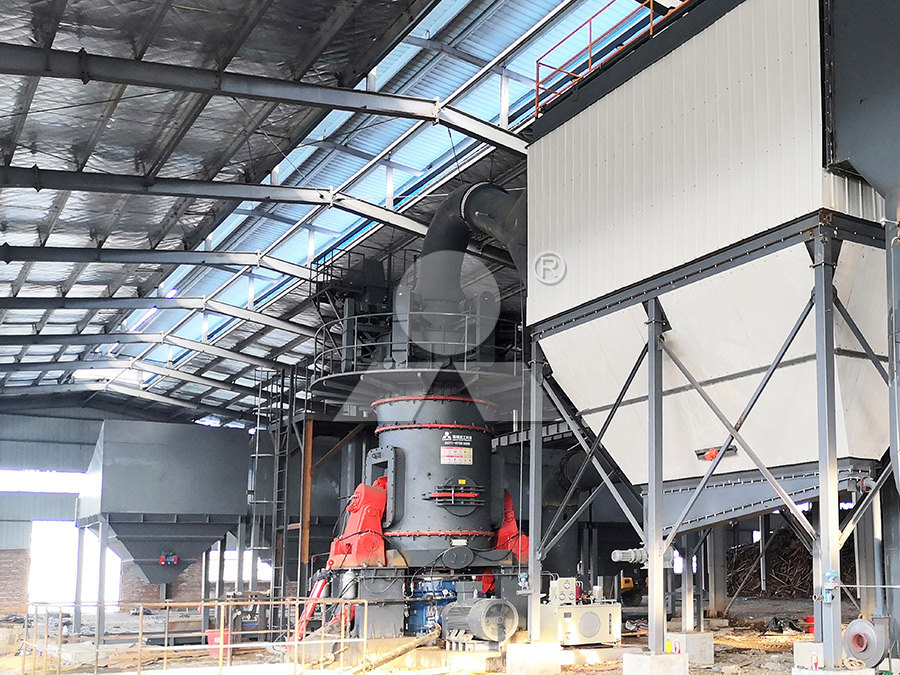
Cement Manufacturing Process INFINITY FOR
Working principle Raw mills uses pressure and shear generated between the rollers and rotating table to crush and grind limestone, basalt and sandstone Air slide pneumatic conveying equipment used to convey dry and powder This process is critical because even slight deviations can affect the quality of the clinker Grinding: The proportioned raw materials are then ground into a fine powder using large grinding mills This step increases the surface area of the Comprehensive Guide to Cement Kilns: 2014年6月10日 It begins with an overview of what cement is and how it is used to make concrete It then describes the industrial process for manufacturing cement, involving grinding raw materials like limestone and clay at high temperatures in a kiln to form clinker, which is then pulverized with gypsum to become Portland cement powderCement manufacturing process PPT Free Download2023年12月20日 The clinker is ground to a fine powder in a cement mill and mixed with gypsum to create cement The powdered cement is then mixed with water and aggregates to form concrete that is used in construction The complex process of making cement starts with the mining of raw materials like limestone and clay, which are then ground into a fine The Cement Manufacturing Process Thermo Fisher Scientific
.jpg)
Modelling of clinker cooler and evaluation of its
2021年3月24日 Overview of the conceptualized clinker cooler and clinker furnace where: Hw is the hot zone height, Hc is the cold zone height, í µí° í µí° ¶í µí± í µí± is the clinker density 2018年11月30日 Continuous high temperature process in the cement industry: Calcination and cement clinker burning Calcination of raw material CaCO 3 => CaO + CO 2 Process emissions of raw material: = 054 t CO 2 /t clinker Endotherm reaction at 950 °C ca 1700 MJ/t clinker ≈ 50% of energy Cement clinker burning at 1450 °C formation of hydraulicProcess characteristics of clinker and cement productionAfter cooling, the clinker may be stored temporarily in a clinker store, or it may pass directly to the cement mill The cement mill grinds the clinker to a fine powder A small amount of gypsum a form of calcium sulfate is normally ground up with the clinker The gypsum controls the setting properties of the cement when water is addedCement manufacturing components of a cement plant2018年7月31日 In cement plants clinker outlet temperature is directly evaluated by clinker cooler process efficiency Cooling processes may be evaluated as one of the energy input considering demand of secondary air and carrier gas called clinker which is subsequently ground to find the desired fineness and mixed with some additives to form cement Development of Cooling Performance of Clinker Cooler Process
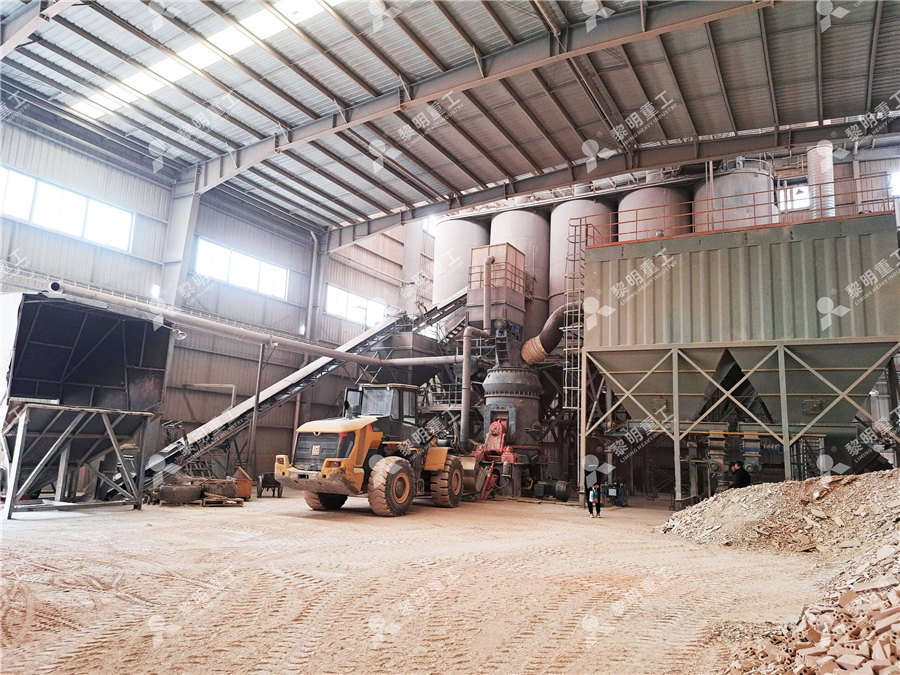
(PDF) Optimizing the Control System of Clinker Cooling: Process
2021年8月19日 During clinker cooling, a heat exchange occurs be tween the solid material and verti cally incoming fresh air A part of the hot air volume enters the kiln as secondary air,