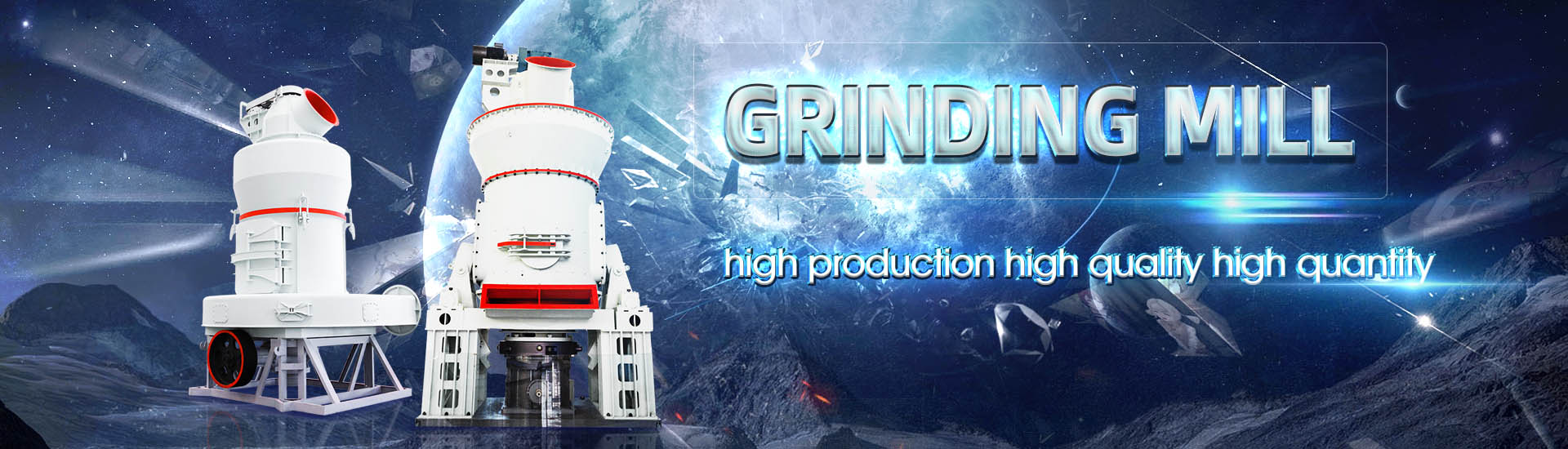
Raw material crushing and grinding system drying process
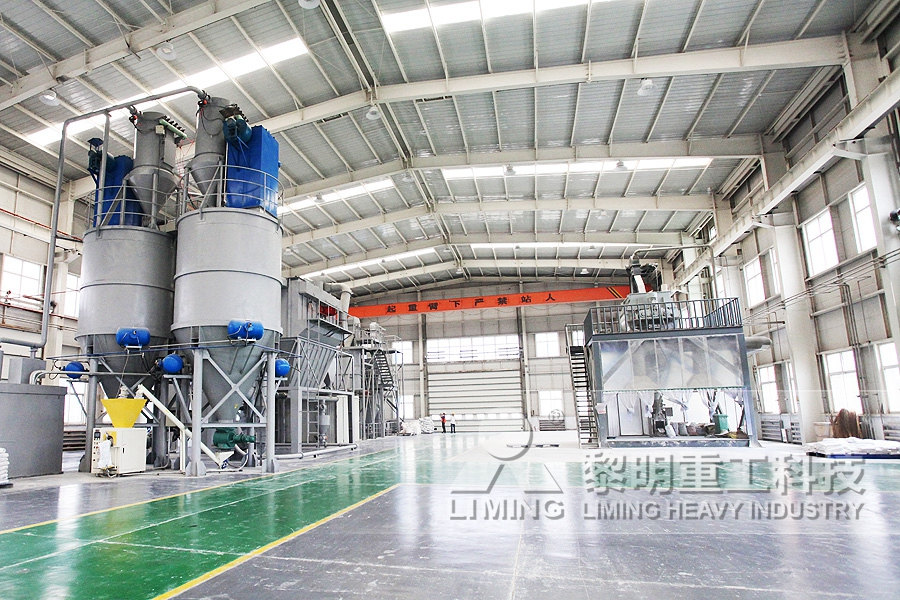
Raw Material DryingGrinding Cement Plant Optimization
Drying of moisture in raw materials is required for effective grinding and subsequent handling of raw meal This is achieved normally by ducting part of the kiln exhaust gas through the mill with inlet temperatures of up to 320°CManufacture of raw materials The raw materials for the dry process are reduced to the fineness needed to feed the kiln through a combination of crushing and grinding Where hard materials Raw Grinding Systems The Cement InstituteDry milling is commonly used in the manufacturing, food processing and chemical industries to grind and crush materials into a powder form without using any liquid The Atritor Cell Mill and the Pulveriser are dry milling machines that are Dry Milling Processes Solutions Atritor2022年2月28日 Conventionally, many mineral processing plants conduct ore comminution stage by dry crushing, followed by wet grinding and classification steps to achieve target size Grinding SpringerLink
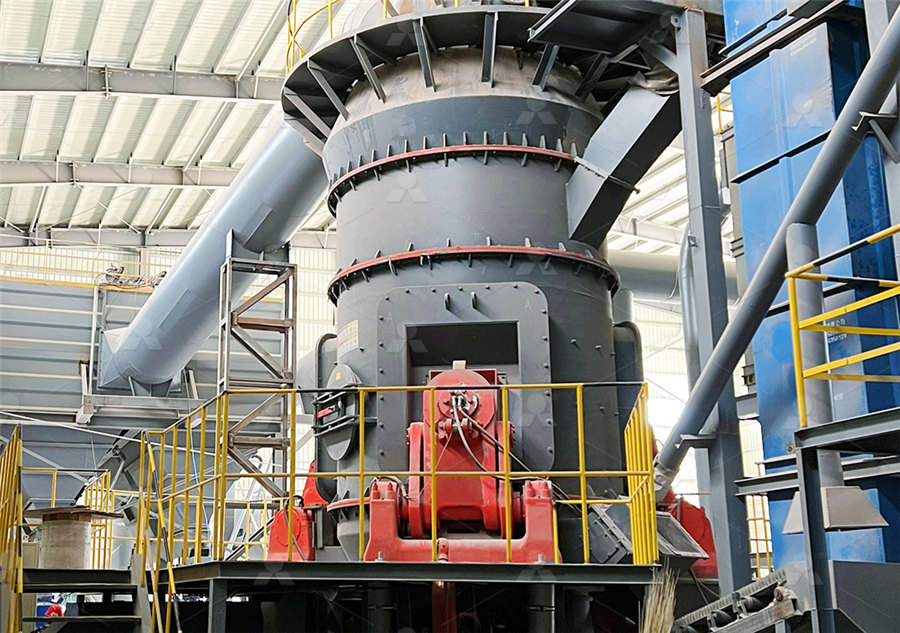
From raw materials Extracting raw materials Raw material
The desired raw mix of crushed raw material and the additional components required for the type of cement, eg silica sand and iron ore, is prepared using metering devices2016年1月20日 The preparation of raw material involves primary and secondary crushing of the quarried material, drying of the material, further raw grinding, and blending of the material The Analysis of material flow and consumption in cement production The preparation of cement involves mining; crushing, and grinding of raw materials (princi pally limestone and clay); calcining the materi als in a rotary kiln; cooling the resulting clinker; Cement Manufacturing International Finance Corporationdrying and grinding of mineral raw materials up to 40 mm particle size and moisture content of not more than 15% DMU has an autonomous operating principle, but the overall system of AUTOMATION OF THE DRYING AND MILLING UNIT FOR THE

Dry Process an overview ScienceDirect Topics
In raw meal preparation for dry process cement manufacture, the raw materials are subjected to crushing in an appropriate plant, dried and ground to a fine powder In the wet process, hard Fig 49 shows a grinding system with predrying and precrushing of the SKET/ZAB, A dryinggrinding process often encountered in America, Fig 425 shows a longitudinal section through a Dou ble Rotator dryinggrinding Drying of raw materials INFINITY FOR CEMENT 2012年6月1日 The feed material is typically composed of the BFRs and the catalyst, both in powder form As the cylinder starts to rotate, the grinding balls inside the cylinder crush and grind the feed Grinding in Ball Mills: Modeling and Process Control2019年10月31日 In friction grinding, this surface grinding is dominant(*3)(*4)。 In the case of volume grinding, crushing occurs not at the particle surface but in the whole part The particle is broken up into several pieces, and this process Pulverization 1: Definition and purpose THINKY
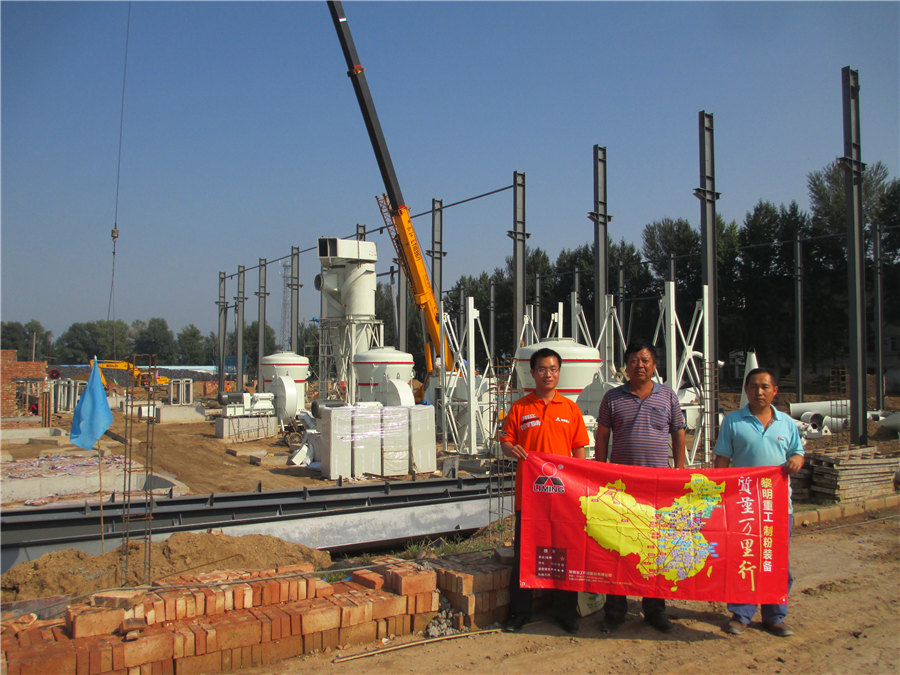
The Cement Plant Operations Handbook International Cement
2 Raw materials management system – 22 Concrete problems 16 1 Raw materials – 2 Raw mix – 3 Reserves – 4 Crushing – 5 Drying – 6 Preblending – 7 Storage and handling 3 Raw milling and blending 3 Computerised Maintenance Management Systems 30 1 Raw milling – 2 Blending – 3 Kiln feed 4 Flames and fuels 38 12020年8月25日 A full cement production process includes the cement crushing process, raw mill process There are three steps of the hightemperature system: Drying or making raw meal block, and then calcining in the kiln can also be classified as wetprocess cement production Drying and grinding dehydrated raw materials and send Cement Production Process Cement Manufacturing Process2024年3月12日 The size of raw materials; Match according to the size of the raw materials, and if necessary, add crushing equipment The requirements for final product fineness (1) If it requires grinding fineness between 80425 mesh, it is recommended to use Raymond grinding mill Raymond grinding mill has a low purchasing costDolomite Crushing Process And Grinding EquipmentJune 2022; ARCHIVE Proceedings of the Institution of Mechanical Engineers Part C Journal of Mechanical Engineering Science 19891996 (vols 203210) 236(2):1107(PDF) A comprehensive review on the grinding process:
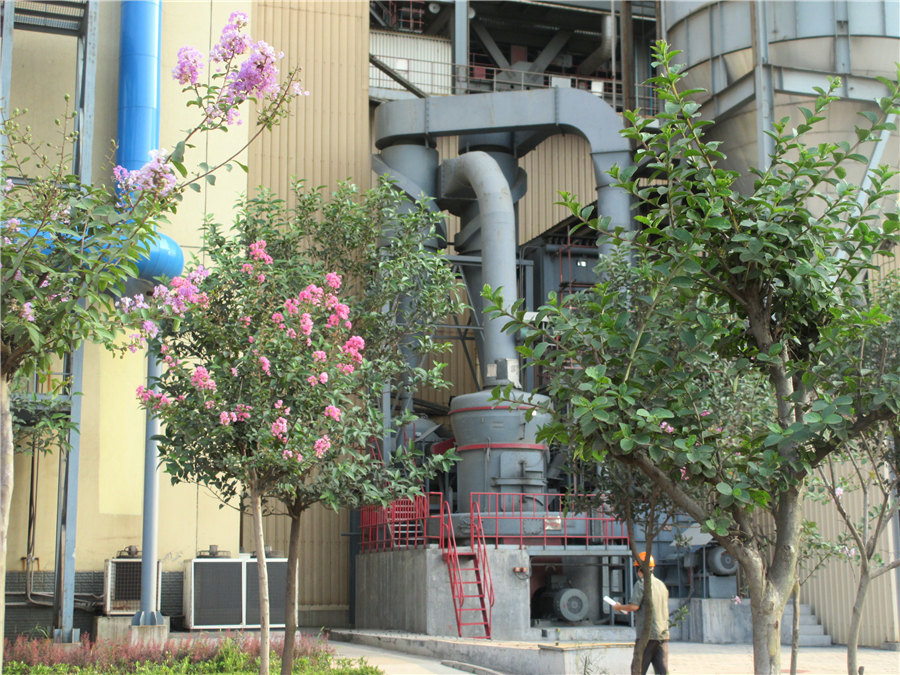
Cement Manufacturing Process: Know Extraction, Processing
2024年9月10日 Steps of Cement Manufacturing The steps involved in cement manufacturing are as follows: Quarrying: Raw materials such as limestone and clay are extracted from quarries or mines; Crushing and Grinding: The extracted raw materials are crushed and ground into a fine powder; Blending: The crushed and ground raw materials are blended in specific proportions Each of the processes shown above uses electricity to drive the motors that drive the grinding and crushing plant, mixing equipment, conveyors, fans, rotate the kiln, and grates Finish grinding or milling (the process of grinding clinker) has different requirements to raw grinding or milling (the process of milling the raw material)The Cement Production ProcessThe initial step in producing brick is crushing and grinding the raw materials in a separator and a jaw crusher Next, the blend of ingredients desired for each particular batch is selected and filtered before being sent on to one of three brick shaping processes—extrusion, molding, or pressing, the first of which is the most adaptable and thus the most commonHow brick is made material, production process, manufacture, Quarrying of raw materials involves (Process of Raw Material Extracting) Mining and removal of Overburden; Haulage comprises the transport of the fragmented rock pile material from the loading point to the crushing plant The Cement Manufacturing Process INFINITY FOR
.jpg)
Analysis of material flow and consumption in cement production process
2016年1月20日 For the current study, eight primary units are defined: crushing materials into a crusher, grinding the raw materials in a raw mill, preheating and calcining the raw meal in a preprocessing tower, burning the calcined raw meal in a rotary kiln, grinding coal, cooling the hot clinker in a cooler, grinding the clinker and additive in a cement mill, and blending and storing diagram of the process is presented This process also enables the alternate grinding of different raw materials, such as granulated blast furnace slag, clinker and concrete in a single plant 2 Introduction, state of technology Currently, sustainability, careful use of resources and critical consideration of the specific CO 2 emis1 SummarySelective comminution of concrete waste and recovery of the A Dry Process Kiln 06 B Raw material unloading 07 C Raw material piles 08 D Primary crushing 09 E Secondary crushing 10 F Screening 11 G Raw material transfer 12 H Raw material grinding/drying 13 I Clinker cooler 14 J Clinker piles 15 K Clinker transfer 16 L Clinker grinding 17 M Cement silos 18116 Portland Cement Manufacturing US Environmental 2022年5月22日 from the mining of raw material through pregrinding to the main wet grinding The LCA includes the determination of the functional unit (FU), the system boundaries, and the(PDF) EnergyModel and Life CycleModel for Grinding Processes
.jpg)
GRINDING TECHNOLOGY COURSE The Cement Institute
2024年11月4日 A 6week modular course is designed to give the course attendee a solid understanding of the grinding system and its auxiliary equipment The purpose of the training is to Identify and understands necessary known and unknown information towards the completed cycle of the grinding system, whether it is a ball mill, vertical mill, or crushing process2024年9月20日 2 Impact crusher The impact crusher can process materials with a side length of 100500 millimeters or less, with a maximum pressure resistance of 350 MPA It has the advantages of a large crushing ratio and with cubic material particles This machine is widely used in building materials, ore crushing, railways, highways, energy, transportation, cement, mining, How Does The Graphite Grinding Plant Process?Raw material blending is an important process affecting cement quality The aim of this process is to mix a variety of materials such as limestone, shale (clay), sandstone and iron to produce The cement raw material blending process and its control system Size reduction process begins with usage of explosives at the area for production of ore In later stages, the size reduction process performed with crushers before grinding in mills is called "crushing" Although there is no limit set, the downsizing process over 3 mm is considered as "crushing" and the ones below 3 mm are considered "grinding"What Is The Crushing Process MEKA
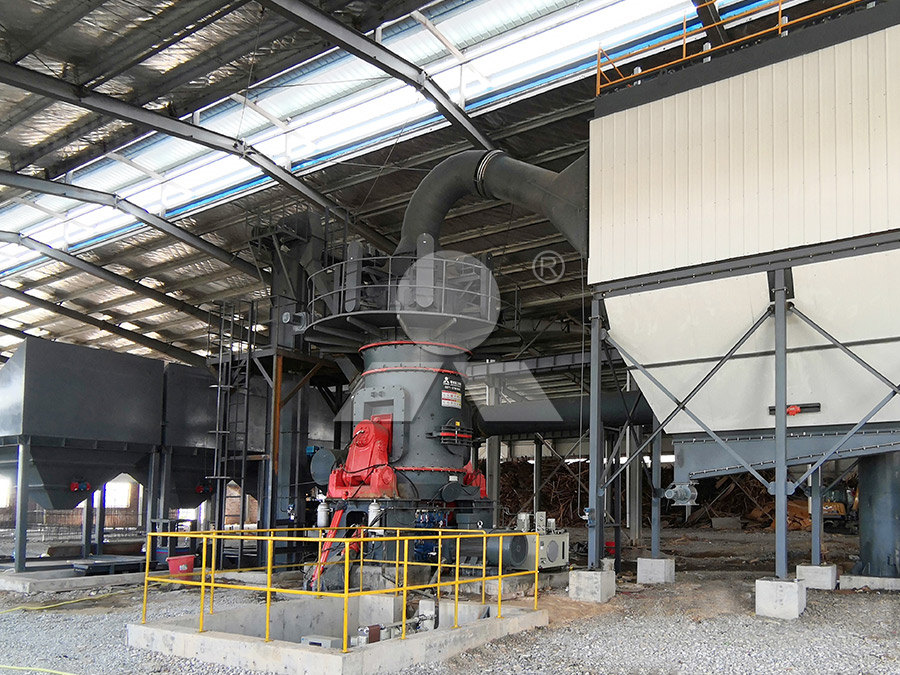
CEMENT MANUFACTURING PROCESS: RAW GRINDING PLANT
VRM offers simplicity by combining the functions of secondary / tertiary crushing, drying, grinding and classifying in one compact machine In VRM, the entire amount of hot kiln gas can be taken in Broadly, there are two systemsThis process of size reduction is called comminution The crushing and grinding process will produce a range of particles with varying degrees of liberation (Figure 2) Any particles that exceed a target size required for physical separation or Introduction to Mineral Processing or Beneficiation2021年1月22日 In the whole process of cement production, the electricity consumption of a raw material mill accounts for about 24% of the total Based on the statistics of the electricity consumption of the raw A Survey and Analysis on Electricity Consumption of Raw Material Raw meal homogenization is the most important process link of the four, accounting for 40% of the homogenization task It is an important factor to support the balanced and stable working performance of preheaters and kilns, and Cement Raw Meal Homogenization Process in The
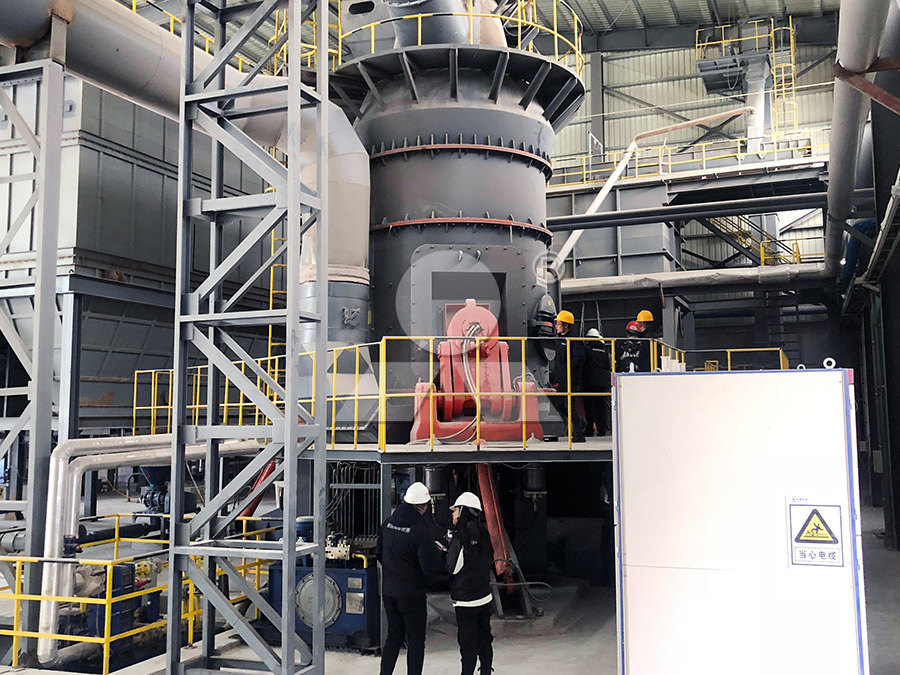
Review on vertical roller mill in cement industry its performance
2021年1月1日 Raw mix, high grade limestone, sand and iron ore are transported from their bins to raw mills for drying and further fine grinding The raw mill is either a Ball mill with two chambers or Vertical roller mill with inbuilt classifier The hot gases from the pre heater enter the mill and are used for drying material in the mills2023年7月10日 The cement manufacturing process involves the extraction and processing of raw materials, such as limestone, clay, and shale, which are then heated in a kiln at high temperatures to form clinkerCement Manufacturing Process and Its Environmental Impact2017年8月24日 In contrast to crushing, which takes place between fairly rigid surfaces, grinding is a random process because the level of grinding of a mineralization particle is based on the probability of the particle entering a zone between the grinding medium (eg, balls) and the probability of some breakage event occurrence after entryMineral Processing SpringerLinkNew material combinations and structures can be created by crushing and grinding materials at low temperaturesOverall, cold grinding is an important process in various industries, enabling the production of fine powders and particles and contributing to improved product quality and Cold grinding crushing materials at low temperatures
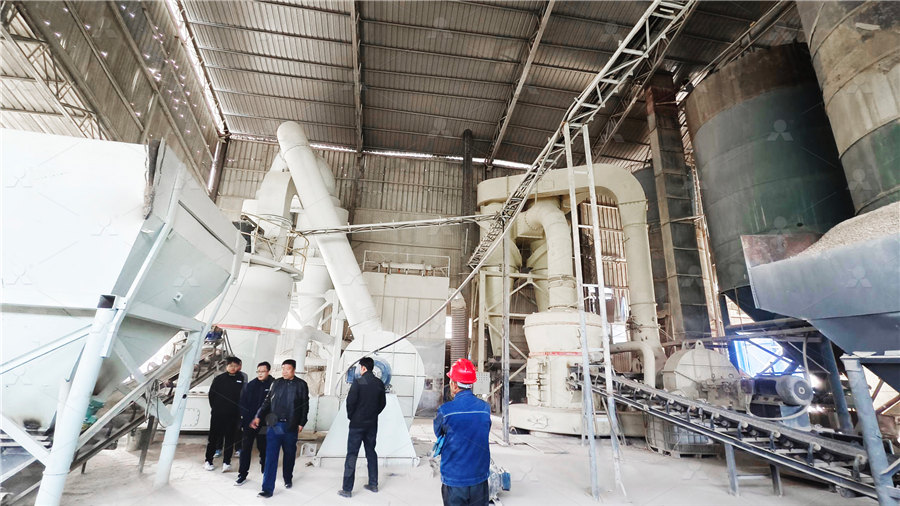
Grinding Shaping System Anode Material
It can crush needleshaped materials to achieve a lengthtodiameter ratio of 15: 1; No temperature rises in the crushing process, suitable for the crushing of heatsensitive materials It can disperse the sintered agglomerated ultrafine materials with a MINERAL ENGINEERING FUEL TECHNOLOGY (MME203) 4th Semester B Tech Dept of Metallurgical and Materials Engineering VSSuniversity of Technology , Burla Sambalpur , odisha Person Name Designation Department involved And id Course Gautam Assistant MME coordinator Behera professor [ protected] Course Co Dinesh Assistant MME Unit Processes in Pyrometallurgy: Drying, Calcination, Roasting crushing equipment do not make contact with each other during size reduction CrushabililY may be defined as the ease of crushing a sample under standard conditions Various test ing procedures may be used to measure crushability" (Horst 1985, p 3A5) "The reasons for comminution of raw materials and mineral products are numerous, howeverCHAPTER 5 GENERAL PRINCIPLES OF MINERAL PROCESSING Machines and systems for the pulverization of thermoplastic raw materials in order to produce freeflowing powders for extrusion, coating, the textile industry and rotomoulding Pulverizing systems at ambient temperature, systems with Machines for crushing, grinding, washing and
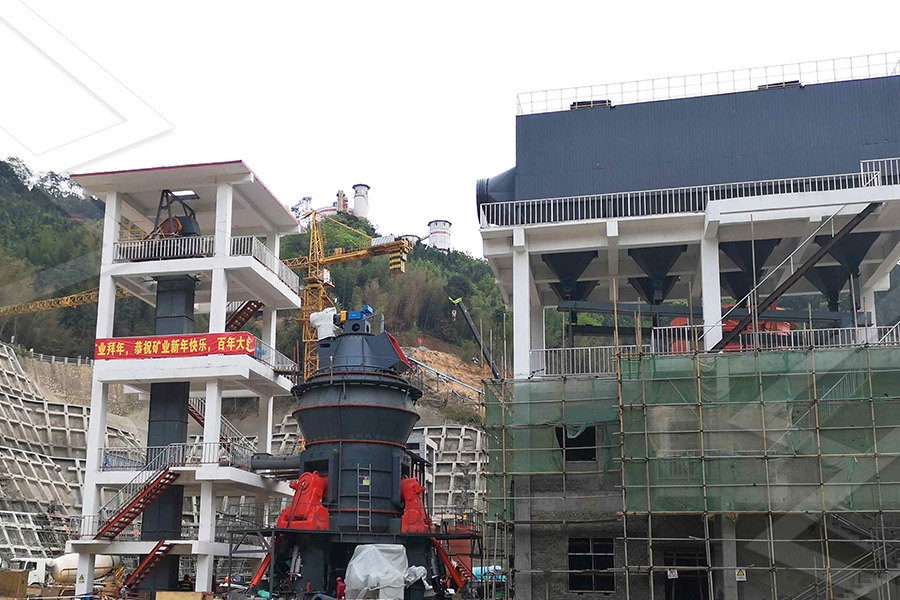
MeasurementControl for Crushing and Screening Process
2023年6月3日 It mainly includes crushing process control, crushing appliance fault diagnosis, and automatic distributing control Crushing Process Control To ensure the continuous, stable, and safe operation of the ore crushing production process, it is necessary to monitor the running state and parameters of key equipment (such as crusher and belt conveyor) in real time for 2024年4月26日 In the BOF process, hot metal is combined with scrap steel and oxygen, which removes impurities and adjusts the carbon content to produce the desired steel grade The EAF process uses electricity to melt scrap steel and Iron Ore Processing: From Extraction to Manufacturing2024年2月1日 1 Crushing/grinding First off, the dry, raw clay material is crushed and ground in what's called a jaw crusher This turns the material into smaller particles and it's at this stage that the other materials are added Different size pieces are separated, and larger pieces are set aside for pummelling so they can be used in another batch 2 FormingHow Do Bricks Get Made? Brickhunter4 天之前 Best system briquetting, granulating, crushing, grinding, drying Friday, November Choosing the suitable crushing and grinding process and equipment can significantly increase Drying Drying is a critical aspect of materials processing, throughout the journey from raw material to end product, the ability to control Best system briquetting, granulating, crushing, grinding, drying
)D`ERF`389RMI4.jpg)
Cement Manufacturing—Technology, Practice, and Development
2021年11月17日 A raw mix is prepared based on the raw materials chemistry, process design, and process considerations, but will also be dependent upon product specifications and on environmental considerations To achieve good quality clinker, a welldesigned raw mix, adequately ground raw meal, and uniform composition are essential requirements together The raw materials, now known as kiln feed, enter a raw mill that consists of a drying chamber and a grinding chamber The kiln feed is then fed into a rotary kiln, a large chemical reaction chamber with temperature reaching approximately 1400 degrees C This forms the clinker (dark grey nodular material) components C3A, C4AF, C2S, and C3SA practical guide to improving cement manufacturing processes The raw material production of cement plant can be classified into four steps: crushing, grinding, mixing and homogenizing Crushing: the limestone and other materials are crushed into small pieces by cement crusher, such as hammer crusher, cone crusher, jaw crusher, impact crusher, etc Mixing: according to the requirement of clinker, compound Preparation Of Cement Raw Material Cement Mill, Cement 2024年6月26日 The material is subjected to grinding process in between two surfaces moving towards each other at varying speeds, thereby creating fine, even product Each has its own purpose for which it is meant when it comes to the reduction of material size through crushing or grinding Prochem Milling Systems Suppliers Delumpers Understanding the Difference Between Crushing Grinding in Material
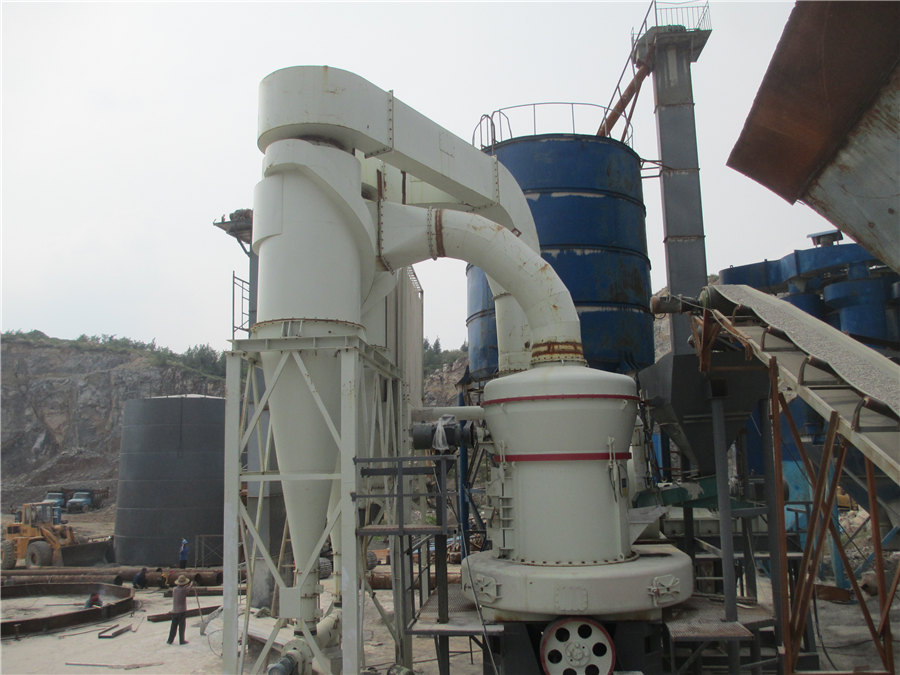
(PDF) Impact of the Drying Temperature and Grinding Technique on
2020年7月2日 The energy demand for the grinding process was determined and it was shown that drying temperature, grinding system, and mainly type of biomass affects the grindability Raw material specific