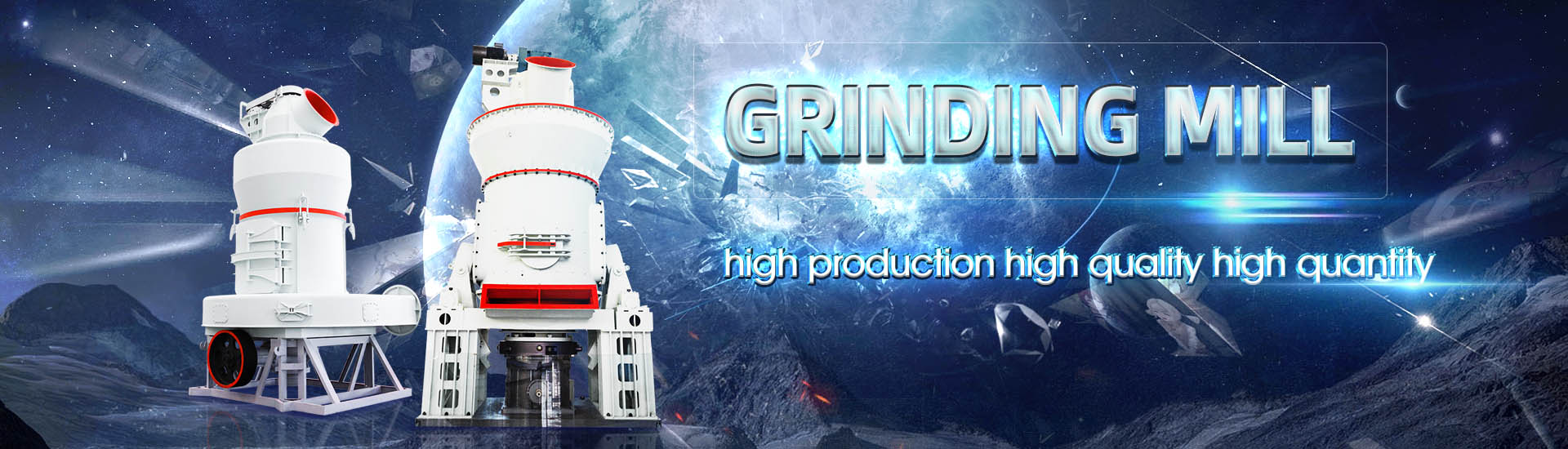
Nickel slag automatic batching nickel slag automatic batching nickel slag automatic batching
.jpg)
Preparation of onepart alkaliactivated nickel slag binder using an
2022年3月7日 Onepart alkaliactivated nickel slag binder (AASB) prepared by mechanical and chemical interaction was studied The effect of balling system on the performance on AASB Alkaliactivated binders can be used in a wide variety of ways, in precasting as View Article2024年1月12日 This article focuses on the preparation of AACM with a large amount of nickel slag Based on this, CTB is prepared using tailings as aggregates The effects of the mass Preparation of alkaliactivated nickel slagbased cemented tailings Granulated nickel slag is essentially an angular, black, glassy slag “sand” with most particles in the size range of −2mm (No 10 sieve) to +0150mm (No 100 sieve) From: The Utilization of Nickel Slag an overview ScienceDirect Topics
.jpg)
Artificial Slags with Modulated Properties for Controlled Nickel
2024年4月15日 Here in this study, we proposed new artificially prepared slag systems with the optimized composition and thereof structure and that are suitable for nickel smelting processes The nickel slag production line has the advantage of saving resources and recovering useful metals The line also includes modern automated equipment and processes that can increase Nickel Slag Production Line Zoomjo GroupNickel slag is a metallurgical solid waste from nickel refineries, which can be recycled as one of excellent secondary sources due to valuable iron contents In this work, the approach of Recycling Nickel Slag by Aluminum Dross: Ironextraction and The potential to treat nickel and cobaltbearing slags and oxide materials using pressure acid oxidative leaching (HPOX) has exhibited variable success in the literature(1)NICKEL SLAG HPOX LEACHING EVALUATION AT LABORATORY
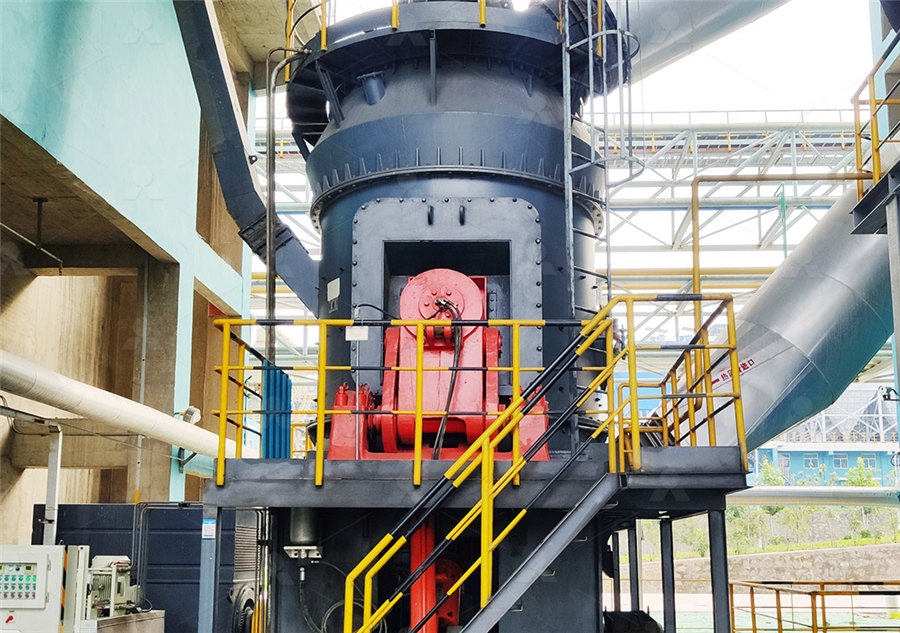
ISASMELT™ TSL – MAKING A SPLASH FOR NICKEL Glencore
equally effective for smelting nickel sulfide concentrates, and converting nickel mattes This paper demonstrates how the features that make ISASMELT™ attractive for copper and lead smelting 2024年10月18日 Nickel slag is the solid waste obtained from the nickel smelting process Based on the magnetic elements in nickel slag, it is a potential ingredient that could be used in Exploration study of nickel slag/modified slag in the ultra 2021年5月11日 We study the structure, chemical composition, and phase composition of slag tailings at the Southern Urals Nickel Plant (SUNP) This information was used to design an Recycling of NickelSlag Tailings into Liquid Products: A Case 2017年11月29日 The results showed that, for nickel smelting slag with 9 wt% MgO, 13–15 wt% CaO and Fe/SiO2 ratio of 12, the melting temperature of nickel slag was lower than 1200 °C, and the viscosity was (PDF) New Slag for Nickel Matte Smelting Process and
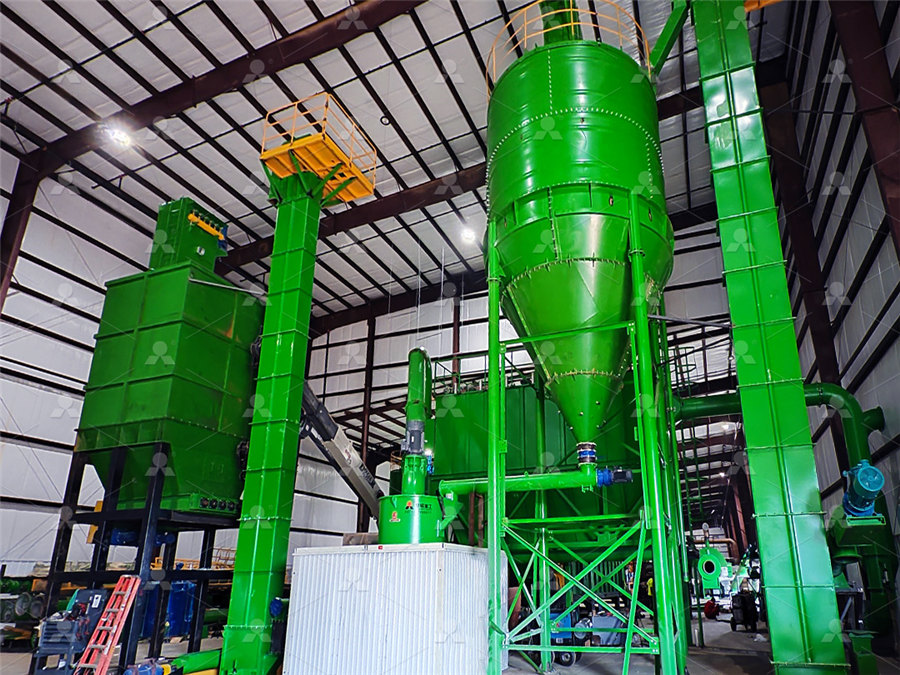
Nickel recovery from electric arc furnace slag by
2017年1月1日 During the pyrometallurgical treatment of the nickelbearing laterite in the plant of GMM SA LARCO, slag is produced after treatment in electricarc furnace (EAF) that contains 010 to 020 % Ni2014年6月1日 A coppernickel slagbased alkaliactivated cementing material (CNSCM) for backfilling was prepared using coppernickel slag as a raw material and sodium silicate (SS) as an activating agentActivating of Nickel Slag and Preparing of Cementitious Materials China Nickel Slag wholesale Select 2024 high quality Nickel Slag products in best price from certified Chinese Plating Nickel manufacturers, Automatic Grade: Automatic 1 / 6 Favorites Slag Conveyor Extractor Conveyor Ash Dredger Machine US$ 5000 / Set 1 Set (MOQ) Nickel Slag MadeinChina2022年11月11日 As a result, the utilization of waste nickel slag has not yet been completely solved and it is an acute environmental problem The building industry is one way of using slags [5,11,12,13,14,15] However, the direct use of slags in the construction industry is complicated by several technological features of this type of materialUtilization of Converter Slag from Nickel Production by
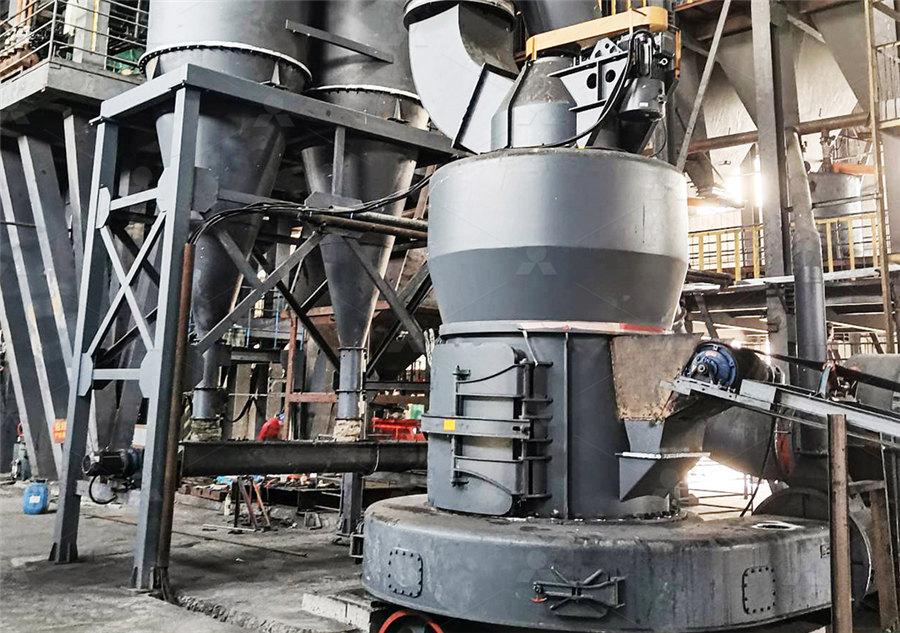
Artificial Slags with Modulated Properties for Controlled Nickel
2024年4月15日 In pyrometallurgy process involving drying, calcination and reductive smelting steps, Saprolite ore is subjected in an electric arc furnace to produce Fe–Ni alloy and Ni matte To optimize the nickel smelting step, the slag consisted of MgO–SiO2–FeO and having a lower viscosity and high fluidity is required In this study, a number of new slag samples with varied 2011年4月1日 Nickel slag contains a notable amount of Co and Ni and is known to be mineralogically and physically stable as it can be used as an aggregate for concrete (Wang et al, 2011)HotMix Asphalt that Contains Nickel Slag Aggregate: Laboratory up to 256 million tons, compared to 13 million tons of nickel slag Nickel slag can be recycled since it contains valuable metals, including nickel, cobalt, and copper The chemical composition of 70% nickel slag is 4147% Silica, 3044% Ferric Oxide, and 258% Alumina An inventive solution to replace components of shotcrete with nickel slagAnalisis Pemanfaatan Limbah Terak Nikel (Slag) sebagai Bahan2009年7月1日 Nickel slag, manganese ore, and desulphurisation slag displayed notable H2selectivity (87 to 104) It can be attributed to the presence of lessactive (lattice) oxygen, High pressure oxidative acid leaching of nickel smelter slag
.jpg)
New Slag for Nickel Matte Smelting Process and Subsequent Fe Extraction
2017年11月29日 Large quantities of residual slag with high Fe content are left behind in pyrometallurgical nickel processing How to separate and recover iron from the high fayalite residue is still a problem because iron mainly exists as ironmagnesium silicate in slag This article suggests that the slag for nickel smelting is adjusted by increasing the amount of lime, partly 2022年9月28日 Xinjiang is rich in coppernickel ore The solution obtained by leaching of coppernickel ore will produce slag containing nickel and cobalt after removing cobalt by adding NiOOH Recovering valuable metals in nickel–cobalt slag after water washing (hereinafter referred to as NCSW) has important environmental and economic significance The purpose of this Optimizing the Leaching Parameters and Studying the Kinetics of Nickel 23 Target Basicity of Modified Slag Compositions of the modified slags (mixture of nickel slag and CaO) with different slag basicities (mass ratio of CaO/SiO 2 in slag system) were plotted in Fig 3 40) As shown in Figs 3(a) and 3(b), CaO–FeO–SiO 2 –MgO and CaO–Al 2 O 3 –SiO 2 –MgO were the corresponding slag systems before and after the reduction process, respectivelyRecycling Nickel Slag by Aluminum Dross: Ironextraction and 2020年12月21日 The global amount of waste electrical and electronic equipment (WEEE) is growing fast Nonferrous metals represent a large portion of this waste, and they can be potentially recovered via black copper smelting Alumina and magnesia, originating from the ewaste or fluxes, can be present in the feed of a secondary copper smelter in varying Slag Chemistry and Behavior of Nickel and Tin in Black Springer
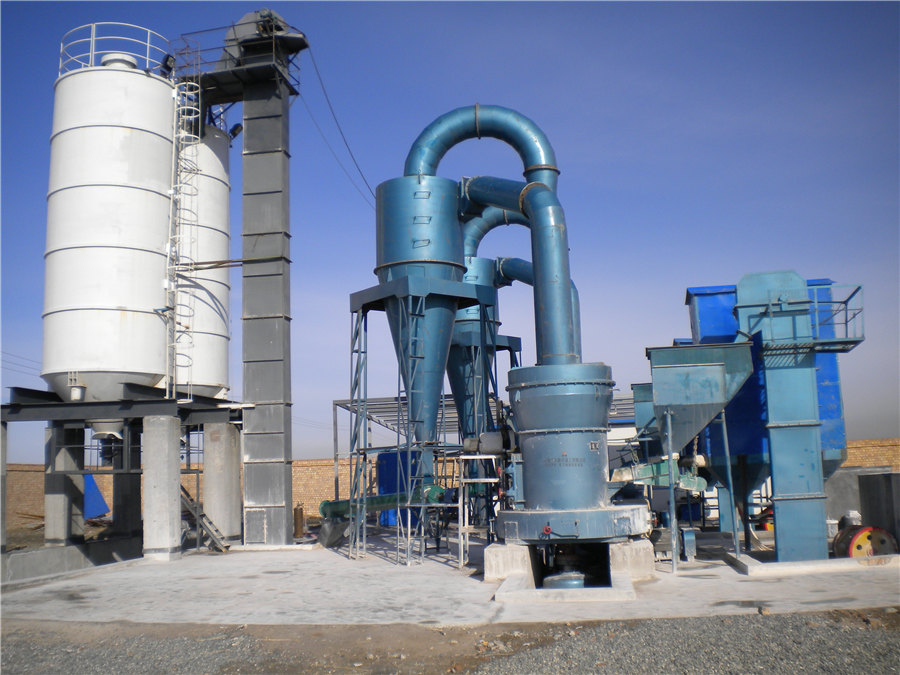
(PDF) Nickel recovery from metallurgical slags ResearchGate
2005年8月21日 Slag from the electric furnaces (E/Fs) contains 016% Ni Nickel recovery was 297% This preconcentrate was then treated in a second (concentration) plantrelative to otation recovery of the raw slag Recovery of iron from nickel ash smelting (FS) slag at a nickel smelter in China, using direct reductionmagnetic separation process, has been investigated by Wang et al [8] In their study, calcium carbide slag was the additive and coke dust was the reductantA Crucial Step Toward Carbon Neutrality in Pyrometallurgical 2003年2月1日 As a fundamental study for the oxygenblowing copper or nickel smelting, the solubility of copper or nickel in the ironsilicate base slag equilibrated with the Cu2SFeS or Ni3S2FeS matte was Nickel, copper, and cobalt slag losses during converting2022年10月10日 Effect of nickel slag on the basic tensile creep of alkaliactivated slag/nickel slag mortars Author links open overlay panel Yu Ma a, Binbin Zhang a, Yiteng Lin a, The size of sample was 40 mm × 40 mm × 40 mm Compressive strength tests were performed using an automatic testing machine (YAW300C, China)Effect of nickel slag on the basic tensile creep of alkaliactivated
.jpg)
Current Situation and Development of Comprehensive Utilization
2017年3月10日 Nickel slag from nickel smelting process is an important secondary metal resource, which contains 40%45% of Fe, 32%36% of SiO2, 1%11% of MgO, 1%3% of CaO (mass fraction) and small amounts of 2022年3月7日 Nickel slag was first milled by high speed (80r/min) for 1 h alone, and then the solid alkali activator was added together with high speed ball milling for 1 h: L30B15T2 + M05: 30: 15: 2: The FBT9 automatic cement Burburne specific surface area tester, Preparation of onepart alkaliactivated nickel slag binder using 2023年8月22日 Firstly, nickel slag sand with a concentrated particle size distribution in the range of 236–060 mm was used to replace the mechanism sand in the ratio of 0%, 25%, a fully automatic mercury pressure instrument with a measurement pore size range of 3 nm1000 μm and a pressure range of 0–414 MPaEffects of incorporating large quantities of nickel slag with various 2017年11月6日 In this study, a new technique was proposed for the economical and environmentally friendly recovery of valuable metals from copper smelting slag while simultaneously upgrading nickel laterite through a coreduction followed by wet magnetic separation process Copper slag with a high FeO content can decrease the liquidus Coreduction of Copper Smelting Slag and Nickel Laterite to
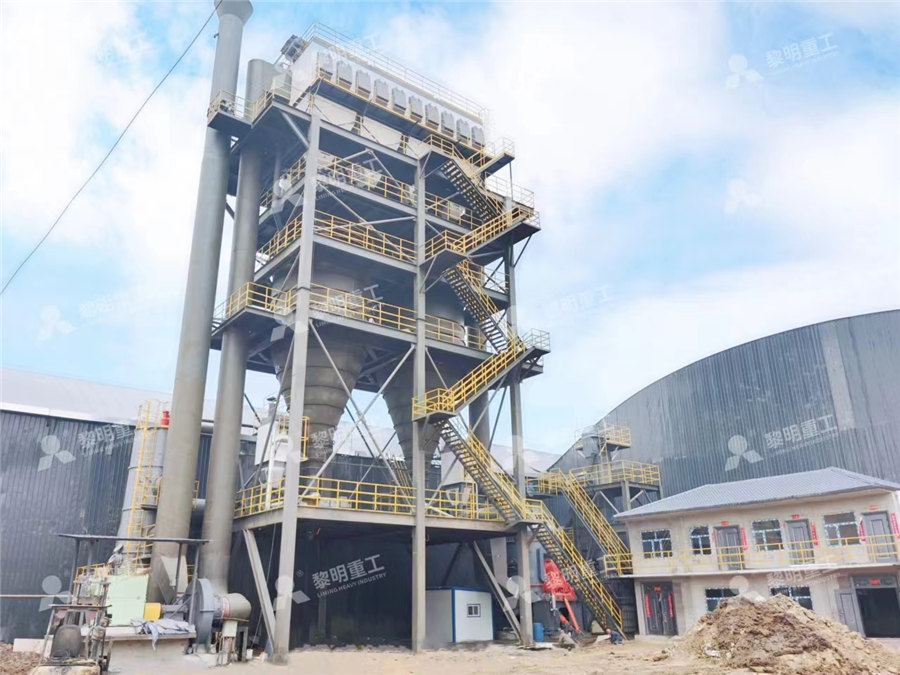
PEMANFAATAN LIMBAH PADAT SLAG NIKEL, ABU
2020年2月13日 15% nickel slag and 15% ply ash with immersio n time for 17 days yielding compressive strength of p aving block 15731 kg /2023年6月9日 This study aimed to increase the recovery efficiency of nickel metal and reduce smelting energy consumption by analyzing the effect of adding B2O3 on the melting characteristics of nickel flash melting slag and the separation of slag and matte In particular, thermodynamic analysis and hightemperature experimental investigations showed that adding Effect of B2O3 on the Melting Characteristics and SlagMatte than 05 Pas, suitable for the nickel matte smelting process C P Cge of the N S To compare the phase change of the new slag system and the original slag of the flash smelting process, CaO was added to the practical original slag to reach the required content with decreasing SiO 2 content At the same time, the MgO content was set at 9 pct New Slag for Nickel Matte Smelting Process and Subsequent Fe In industries where it’s essential to have accurate and efficient batching, automated batching systems have become gamechangers At Cross Company Automation, we’re able to provide stateoftheart automated batching systems that optimize industrial processes, ensure precise ingredient measurements, minimize process errors, and maximize your productivityAutomated Batching Systems Cross Manufacturing Automation
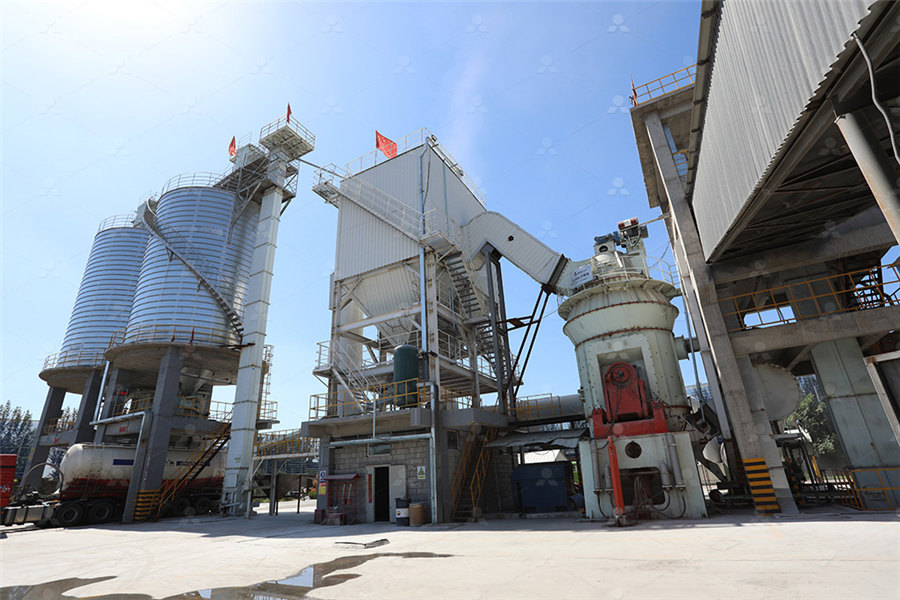
Recycling of NickelSlag Tailings into Liquid Products: A Case
2021年5月1日 This information was used to design an integrated process for reprocessing of nickelslag tailings The first step is to hold the slag/metal melt in a crucible for 15 min at 1300–1400°C, resulting in formation of a nickelrich (15–18%) matte melt at the bottom After this melt cools and hardens, 2023年11月24日 In China, high magnesium nickel oxide ores are predominantly used for nickel production, resulting in the production of nickel slag with a high content of magnesium silicates [30], [31] The chemical compositions of GBFS and HMNS were determined using an ARL9800 Xray fluorescence (XRF) instrument (Thermo Scientific) and are presented in Table 3 Alkalisilica reaction of highmagnesium nickel slag fine Based on above background, recycling nickel slag by aluminum dross with converterslag addition was investigated in this work The modification behavior between nickel slag and converter slag was studied Also, the reduction behavior of nickel slag by aluminum dross with converterslag addition was investigated Element mapping of the modifiedComprehensive Recovery of Multisource Metallurgical Wastes: 2020年7月3日 ASIATODAYID, JAKARTA – Indonesia terus berupaya menciptakan terobosan untuk menghidupkan circular economy (ekonomi berkelanjutan), salah satunya dengan mengolah slag nikel menjadi bahan baku industri “Balaibalai kami telah memiliki teknologi, peralatan dan sumber daya manusia yang memadai dalam kegiatan pengujian, penelitian, penyusunan Indonesia Hasilkan 13 Juta Ton Slag Nikel Per Tahun
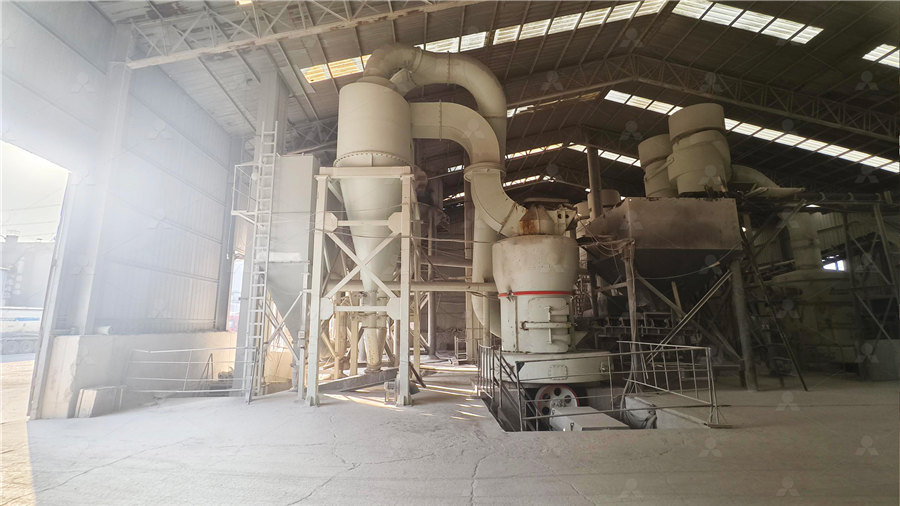
Preparation of nickel slag derived Fe3O4/conductive carbon black
2024年1月17日 First, nickel slag of 80 g was pulverized and sieved and then the slag powder with a particle size of less than 74 μm was obtained Second, some tablets were gotten with a tablet press using the slag powder, the pressed tablets were put into a corundum crucible and warmed up from room temperature at 1450 °C, then held for 1 h, and finally cooled to room 2019年10月24日 Download Citation Recycling Nickel Slag by Aluminum Dross: Ironextraction and Secondary Slag Stabilization Nickel slag is a metallurgical solid waste from nickel refineries, which can be Recycling Nickel Slag by Aluminum Dross: Ironextraction2020年5月13日 in nickel slag cleaning conditions with methane reduction A simplified flowchart of the proce ss can be seen in Figure 1 Minerals 2020, 10, 435 4 of 22 Figure 1Integrated Battery Scrap Recycling and Nickel Slag 2018年8月4日 The slag cleaning (or matte settling) process was experimentally investigated at 1573 K using a fayalitic nickel converter slag containing spinel and matte/alloy particles The addition of various amounts of spent potlining (SPL) was studied in terms of its influence on matte settling and the overall metal recoveries The slags produced were characterized by scanning Enhancement of the nickel converter slagcleaning operation with
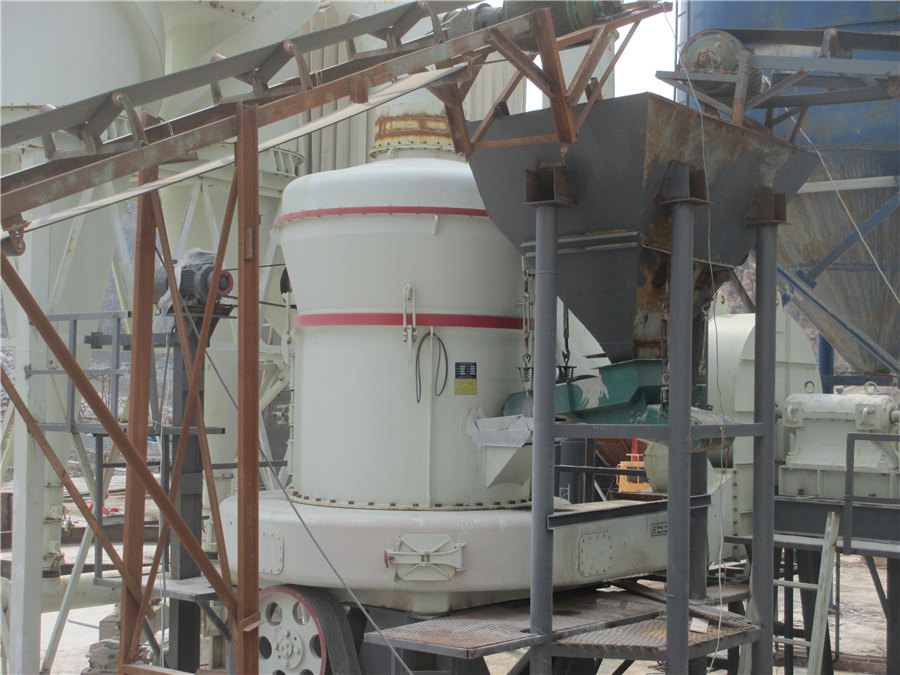
An Ammonia Leaching Process for the Recovery of Value Metals
2024年7月10日 The rapid development of lithiumion batteries has led to a shortage of cobalt and nickel resources Recycling of nickel and cobalt slag can promote sustainable development and environmental protection In this study, a reductive ammonia leaching method is proposed for the recovery of Ni and Co from nickel and cobalt slag (NCS) with high Ni and Co contents The 2017年12月15日 This information was used to design an integrated process for reprocessing of nickelslag tailings The first step is to hold the slag/metal melt in a crucible for 15 min at 1300–1400°C, Processing of nickelcontaining final dump slags with recovery of 2022年12月15日 In order to recover iron from nickel slag, the authors investigated the effect of a water vapor atmosphere on the oxidation process of nickel slag The phase constitution and microstructure of the solid products were characterized using xray diffraction and scanning electron microscopy with an energy dispersive spectrometer The results show that the Recovery of Iron from Nickel Slag in Water Vapor at High 2021年1月1日 The effect of addition of sodi um sulphate (Na2SO4) to nickel slag pyrometallurgical process with temperature and additives ratio as variables in E3S Web of Conferences 2018(PDF) Magnesium Extraction of Ferronickel Slag Processed by

Oxidative Acidic Leaching of Ferronickel Slag for Sustainable
2024年3月25日 Pyrometallurgical processing of lateritic ore produces huge amounts of ferronickel slags, which may contain valuable metals This paper describes a novel hydrometallurgical route to recover metals from ferronickel slag samples and reduce liability matters using oxidative acidic leaching Hydrochloric acid and hydrogen peroxide were 2014年6月1日 The Xray diffraction (XRD) analysis result Table 1 Chemical composition of arseniccontaining cobalt and nickel slag (mass fraction, %) Cu As Zn Pb Co Ni Si Cd 4761 1092 501 233 227 13 041 052 Guolin YU, et al/Trans Nonferrous Met Soc China 24(2014) 1918−1927 1920 Fig 1 XRD pattern of arseniccontaining cobalt and nickel slag Fig 2 SEM Extraction of arsenic from arseniccontaining cobalt and nickel slag 2020年2月26日 To overcome the difficulty in the direct reduction of Fe2SiO4 in nickel slag, the isothermal oxidation of the nickel slag was conducted between 300 and 1000 °C Its morphology and phase composition after oxidation at 300–1000 °C for 5–30 min are analyzed by means of Scanning electron microscopy, Xray diffraction, and thermodynamic calculation The results Structure and Phase Changes of Nickel Slag in Oxidation Treatment