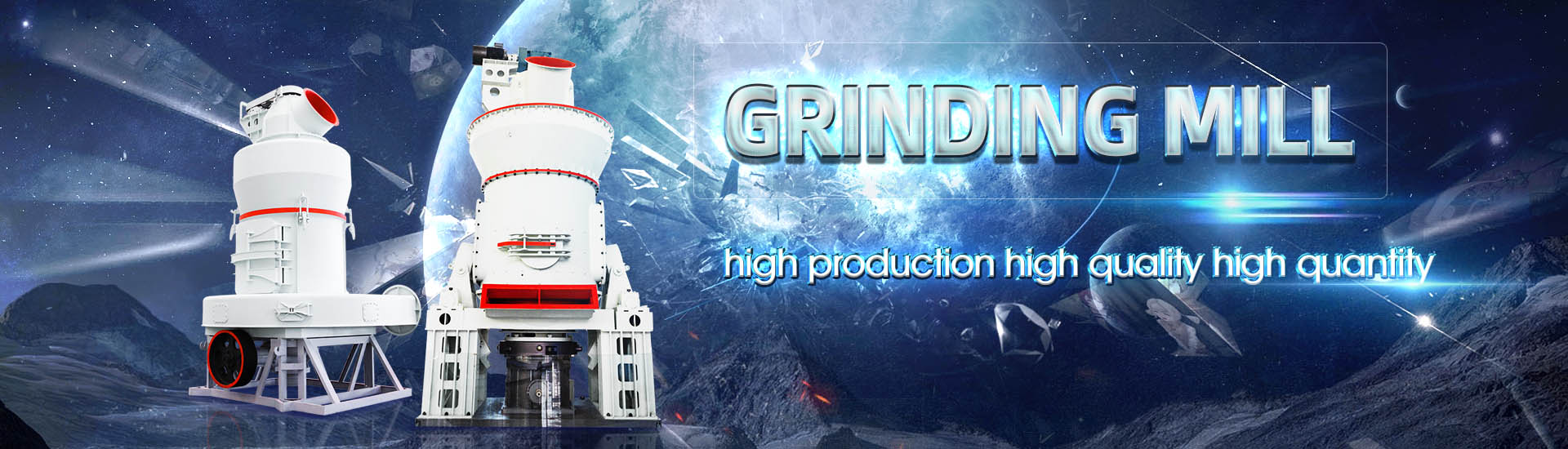
HOME→Determination of the mesh number of the crusher and powder selector, the wind speed at the air inlet is generally
Determination of the mesh number of the crusher and powder selector, the wind speed at the air inlet is generally
.jpg)
Influence of jaw crusher parameters on the quality of primary
2020年6月1日 A parameter study using a jaw crusher is designed to investigate the influence of feed gradation, feed rate, crusher setting and crusher speed on the crusher operation and the quality of the produced aggregatesTo determine and analyze the size distribution of a fixed granular solid by using a Test Sieve Stack To determine and analyze the size distribution of a fixed granular solid by using a MINERAL PROCESSING LABORATORY MANUAL Veer Surendra 2020年10月1日 To study and optimize the gyratory crusher performance, taking the process of crushing iron ore by the gyratory crusher as the specific analysis object in this paper First, the Simulation and optimization of gyratory crusher performance 2024年8月1日 A combination of Taguchi experiments, NN and CFD is used to analyze the effects of characteristic parameters such as inlet air velocity v, rotor cage speed n, number of Parameter optimization of the classifying device of straw micro
.jpg)
(PDF) Evaluation of the Optimum Mesh of Grind for Nchanga
2004年1月1日 The optimum mesh of grind for the openpit ore is 5337% passing 75µm (1341% + 150µm) yielding metal recoveries of 9041% TCo and 9364% AICo This paper discusses 2023年6月30日 This is achieved by studying modelling methods and results, the automation of crushing and grinding processes, and the wear reduction of crusher components On the Modeling and Improving the Efficiency of Crushing Equipment2024年7月18日 To improve the classification performance of the straw microcrusher classifying device, this paper proposes a CFDMLGA (Computational Fluid DynamicsMachine Learning Influence of Rotor Cage Structural Parameters on the Classification 2021年11月9日 Through infrared spectroscopy analysis, it was found that in the phenolic bakelite resin powder of different meshes (80 mesh, 200 mesh, 300 mesh), a peak is observed Numerical and experimental research on the degradation
.jpg)
Design Improvement and Computer Modeling of the Finger Grain
Analyzing the designs of the most common hammer, crushers enabled the determination of the most promising grain crushing scheme, which is its preliminary separation with the 2021年11月6日 The paper concerns investigation of the effect of impact crusher operation on selected qualitative characteristics of mineral aggregate products Qualitative characteristics of Optimization of Aggregate Production Circuit through Modeling 2023年6月30日 Each crusher is a complex unit with a large number of parameters For example, a cone crusher is represented by a system with six degrees of freedom with two symmetryModeling and Improving the Efficiency of Crushing 2020年6月4日 The size reduction process of rocks in cone crushers is one of the most important issues, particularly for the secondary and tertiary stages of crushing operations In this study, 17 different rock types were considered for the evaluation of their size reduction variations that occurred in a laboratoryscale cone crusher Based on several mineralogical, physico Evaluation of size reduction process for rock aggregates in cone crusher
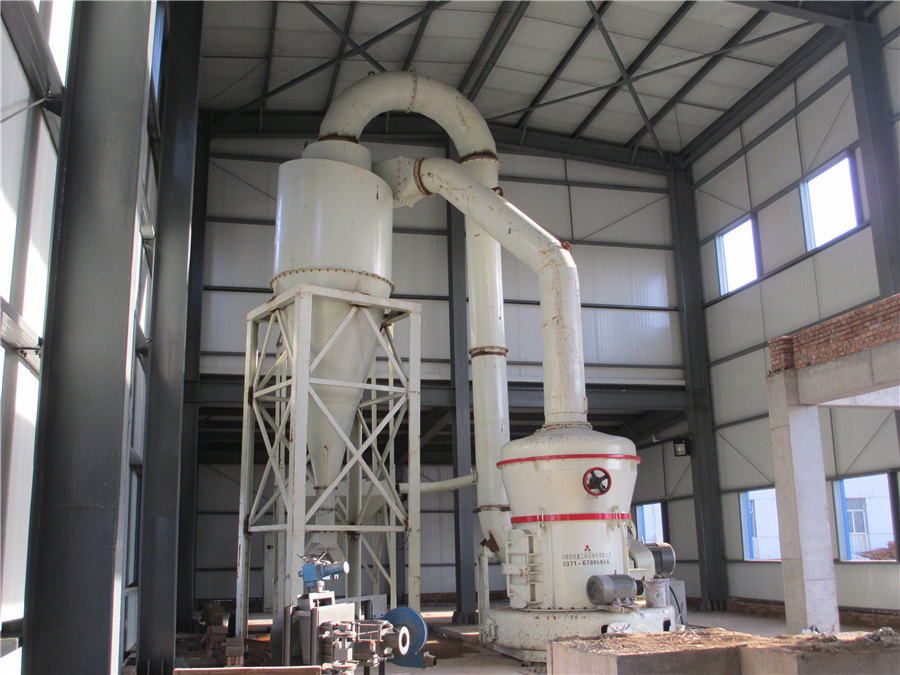
(PDF) New testing methodology for the quantification
2018年11月1日 Under a fixed mechanical drive system and feed size, the product throughput is predominantly determined by the specific energy (kWh/t) of the rock [5,6], the mantle rotational speed and the closed This sieving process for estimating the particle size distribution of a single pharmaceutical powder is generally intended for use where at least 80% of the particles are larger than 75 µm The size parameter involved in determining particle size distribution by analytical sieving is the length of the side of the minimum square aperture through which the particle will pass786 PARTICLE SIZE DISTRIBUTION ESTIMATION BY ANALYTICAL 04005 Determination of the angle and speed of interaction of cotton seed rush with the multifaceted screen drum of the separator Dadakhon Juraev1*, Anvar Djurayev2, Shakhzod Umarov1, Juragul Manglieva3, Nasriddin Obitov3, and Zokhida Eshbaeva3 1Navoi Department of the Academy of Sciences, Navoi, Uzbekistan 2Tashkent Textile and Light Industry Institute, Determination of the angle and speed of interaction of cotton 6th International Conference on Computer Applications in the Minerals Industries, Istanbul, Turkey 57 October 2016 CAMI201634 4 ¦ K kk k minimize q R)3(subjectto ¦ n j j xp (4) ¦ 1 ,k n ijk Istanbul, Turkey Determination of the optimum inpit crusher
.jpg)
Simulation and optimization of gyratory crusher performance
2020年10月1日 To study and optimize the gyratory crusher performance, taking the process of crushing iron ore by the gyratory crusher as the specific analysis object in this paper First, the discrete element method (DEM) analysis model of the iron ore based on the bondedparticle model (BPM) is established On this basis, the impacts of the mantle shaft angle, the concave 2020年10月1日 The gyratory crusher is widely used in primary crushing of metal ore such as iron ore and copper ore due to its high productivity and large feed inlet [[1], [2], [3]]In recent years, with the growth of the world's population, the development of urbanization and the improvement of living standards, the demand for the ore continues to increase, therefore, the Simulation and optimization of gyratory crusher performance 2020年10月31日 The author in study [7] presents the results when using a centrifugal impact crusher of a new design with a hole in the loading neck to supply additional air at a speed of up to 48 ms 1 Studying the operational efficiency of the centrifugalimpact feed 2017年1月1日 crusher and roll crusher in a cl osed cycle with screening to size 100% 3327 mm Composite samples of andesite and lim estone were prepared in ratios: limestone : andesite = 25 : 75,A quick method for bond work index approximate value determination
.jpg)
Influence of jaw crusher parameters on the quality of primary
2020年6月1日 The effect of reduced crusher speed on PSD is seen in Fig 6 When the crusher speed is reduced, the endpoints of the PSD curve – the top size and the amount of material smaller than 1 mm – is not affected On the other hand, the PSD curve is steeper, and there is less material smaller than CSS2019年10月1日 Construction diagram of the laboratory vibratory jaw crusher type KW 40/1: 1jaws, 2kinematic vibrator, 3outlet gap size adjustment mechanism, 4recoil spring system, 5chain transmission, 6 Determination of crushing energy during vibratory crushing2021年3月15日 Analytical expressions were derived to determine the rational rotation speed and productivity of the crusher under consideration Expressions for calculating the kinematic load components acting Chamber Optimization for Comprehensive Lines and plans of grain mixture flow rate in the working crusher chamber at different values of the rotor speed: a) n = 1500 rpm; b) n = 2000 rpm; c) n = 2500 rpm and the visual images differ only in the scale of the speed values Certain zones with different velocity values are clearly distinguished in the chamber cavity The numberDesign Improvement and Computer Modeling of the Finger Grain Crusher
.jpg)
(PDF) Influence of jaw crusher parameters on the quality of
2020年3月19日 A parameter study using a jaw crusher is designed to investigate the influence of feed gradation, feed rate, crusher setting and crusher speed on the crusher operation and the quality of the 2018年11月7日 Because the grinding process of cereal feed is very complex, it is difficult to measure the relevant parameters directly by sensors (Tian et al, 2019;Mugabi et al, 2017)(PDF) The Influence of the Structure of Double Toothed Roller Crusher 3 The mass retained on the smallest mesh no was weighted, and kept aside 4 The sample sieved in this mesh was again sieved with a sieve of higher mesh number (Ex: 16, 22, 72, 85, 100, and 150 respectively) 5 The mass retained on each mesh number was weighted, and sieving is carried out for 15 min 6MINERAL PROCESSING LABORATORY MANUAL Veer Surendra 2018年5月1日 When the vibration motor (1) is operated, it will create a vibrating force that causes the screen frame to oscillate and implements the screening process [2]Determination of capacity of singletoggle jaw crusher, taking
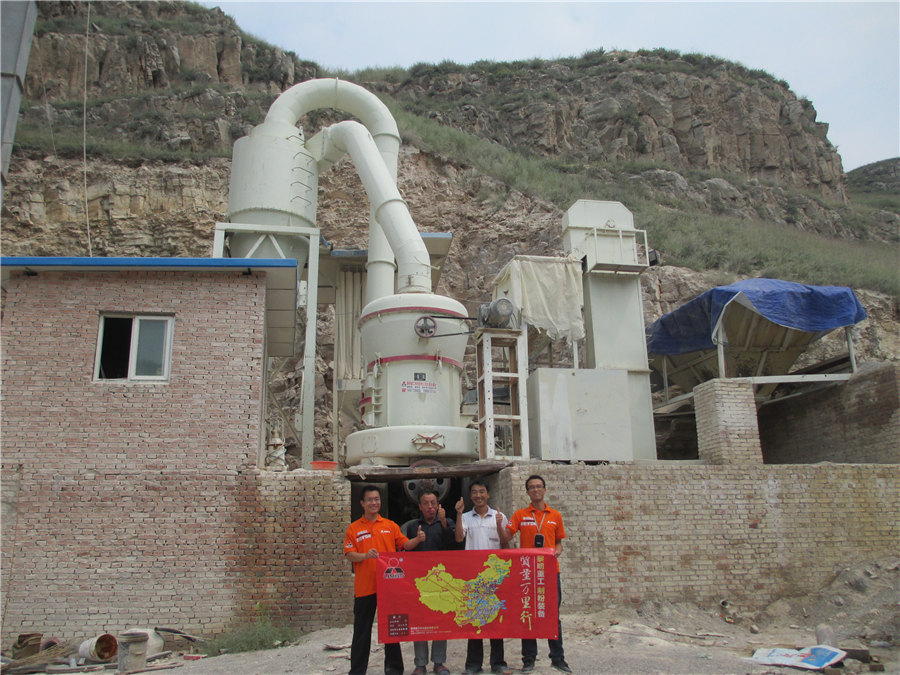
63 Determining Mesh Statistics and Quality
While Fluent Meshing already contains a number of separate mesh diagnostic tools, the Mesh category in the Ribbon includes many useful mesh checking and quality diagnostics from a single access point Figure 613: The Note: Though generally performed automatically when using the meshing diagnostics tools, keep in mind 2023年2月1日 In this paper, a mesh size determination method with strong applicability is proposed According to this method, the mesh size is the product of the scale coefficient and the third root of the (PDF) Study on the mesh size determination method of blast 2017年3月4日 A simplified model (kinematic diagram) of the mechanism of the double buckling jaw crusher is shown in Fig 20 The mechanism in question is a six membered mechanism formed by attaching a binary SIZE REDUCTION BY CRUSHING METHODSIf the speed of the mill is too high the balls are carried over and the mill is said to be centrifuging The minimum speed at which centrifuging occurs is called the critical speed Little or no grinding is done when a mill is centrifuging and operating speed must be less than the critical speed PROCEDURE: About 500g of feed was weighedDEPARTMENT OF OF CHEMICAL ENGINEERING SRMIST
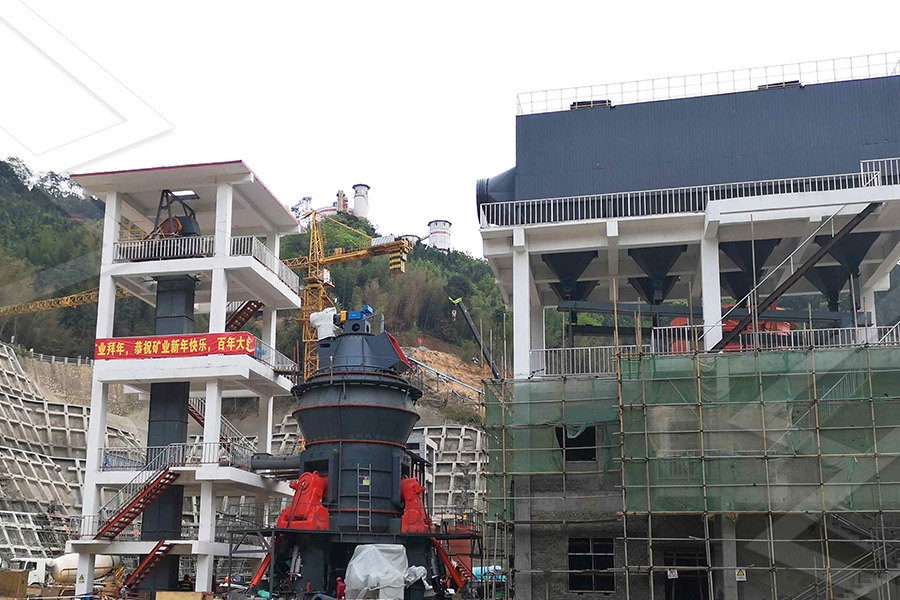
Determination of work index in a common
2005年8月5日 Also the relationship among specific energy consumption and crusher speed and capacity were obtained The most efficient operational regimen corresponded to 1100 rpm of the rotor velocity, 2 2024年6月11日 This measurement, called aperture size, shows the size of the sieve mesh Think of it as a grid of tiny squares over a specific area More squares (or openings) mean a higher mesh number So, a higher mesh number lets smaller particles pass through, and a lower mesh number lets larger particles pass through This might seem counterintuitiveSieve Mesh Sizes: A Guide to Understanding Different Mesh2014年9月16日 A twinroll crusher is selected, like those given in the Roll Crusher capacity Table above, to serve as the reduction crusher The smallest, 24 x 16 roll crusher shown in the Roll Crusher capacity Table above has enough capacity with a setting of 1 in but the maximum size feed will be too large, that is, the stage of reduction is not large enoughCrusher Efficiency Calculations 911Metallurgistdetermined The test gives the weight percentage of powder in each sieve size range This sieving process for estimating the particlesize distribution of a single pharmaceutical powder is generally intended for use where at least 80 per cent of the particles are larger than 75 µm The size parameter involved in2938 PARTICLESIZE DISTRIBUTION ESTIMATION BY
.jpg)
DETERMINATION OF POWDER FINENESS PharmaState Academy
Superfine powder: A powder of which not less than 90% by number of the particles are less than 10mm in size When the fineness of the powder is described by means of a number, it is intended that all the particles of the powder shall pass through a sieve of which the nominal mesh aperture, in mm, is equal to that numberof the standard methods of powder characterization and testing Obtaining reliable powder samples is of vital importance for getting genuine data of chemical composition and the physical and technological properties of a given powder To obtain a representative powder sample for analysis, it is necessary to folPowder Characterization and Testing Elsevier2016年3月11日 Or if 10 g be reduced to exactly 001in from exactly 01in particles, there will be an increase of 10 times 100 minus 10 times 10, or 900 mesh grams Meshpounds, meshounces, meshpercentages, etc, are similarly justified and defined The term “mesh” for a measurement has been objected to, as ambiguous in meaningRock Crushing Theory and Formula using Kick Rittinger’s Law2024年9月4日 Mesh size refers to the number of openings per inch in a screen or sieve For instance, a 100 mesh screen has 100 openings per inch, meaning particles must be smaller than 149 microns to pass throughAchieving 100 Mesh: The Ultimate Guide to Crusher Selection
.jpg)
Review for practical application of CFD for the determination of wind
2019年3月1日 Consequently, a satisfactory numerical simulation is a balance against the mesh resolution, number of mesh cells, the duration and solver time of the simulation/computational resources Therefore, many wind engineers are attempting to decrease the mesh denseness and the number of cells, in order to increase the duration and decrease the solver 2021年7月30日 Powder characterization was done using various conventional and novel powder characterization techniques to measure properties such as, angle of repose, flow index, aerated, tapped and conditioned Techniques to Determine Powder Flow Properties2021年11月6日 The paper concerns investigation of the effect of impact crusher operation on selected qualitative characteristics of mineral aggregate products Qualitative characteristics of crushing products in terms of size reduction ratio Optimization of Aggregate Production Circuit 200 mesh woven wire sieve The ratio of the successive sizes of the sieves in the standard sieve scale is 2 In general, mesh number × mesh size in microns ≈ 15,000 For closer sizing work the sieve ratio of 24 is common The different standards in use are: American Tyler Series American Standards for Testing and Materials, ASTM E1101SIZE REDUCTION AND SEPARATION (4 TH SEM MINERAL ENGG)
.jpg)
Bond Work Index FormulaEquation 911Metallurgist
2013年7月15日 For 150 mesh the average P value is 76 microns, for 200 mesh it is 50, for 270 mesh it is 323, and for 325 mesh it is 267 These average values can be used when P cannot be determined from screen analyses In the AC rod mill grindability test where Grp is the net grams of mesh undersize per revolution of the 12″ x 24″ test rod millNumber : Diameter (mm) Mass of Empty Sieve (g) Mass of Sieve+Soil Retained (g) Soil : Retained (g) Percent Retained : Percent Passing : 4 ; 10 20 40 60 140 200 Pan Total Weight= Qatar University Geotechnical Engineering(CVEN 230) College of Engineering Department of Civil Arch Engineering LABORATORY TEST # 1 GRAIN SIZE ANALYSIS (ASTM D 422) In this study, the effects of three different choke feed level (1/1, 1/2, and 1/4) and four different effective reduction ratios (25, 5, 10, and 20) depend on the capacity of the crusher of the The flowchart of crushing process with onestage and three 2021年6月29日 This article deals with the preparation and laboratory milling of βdicalcium silicate Dicalcium silicate is the second most important calcium silicate of Portland clinker βC 2 S is usually Effects of Mill Speed and Air Classifier Speed on Performance of
)D`ERF`389RMI4.jpg)
Determination of the optimal transition point between a truck
of trucks is required; however, the number of loading machines is the same as for the TS system To avoid increasing the haulage distance, the crusher(s) location may be changed at regular intervals (Rahmanpour et al, 2014) Using this method can save costs and improve the economics of the operationLevel comminution process for brittle materials generally use impact principle with beat and crazy [13] Firstdegree communion process of the crusher, the size of the material is centered between Power draw of the crusher when varying the speed and CSS, not