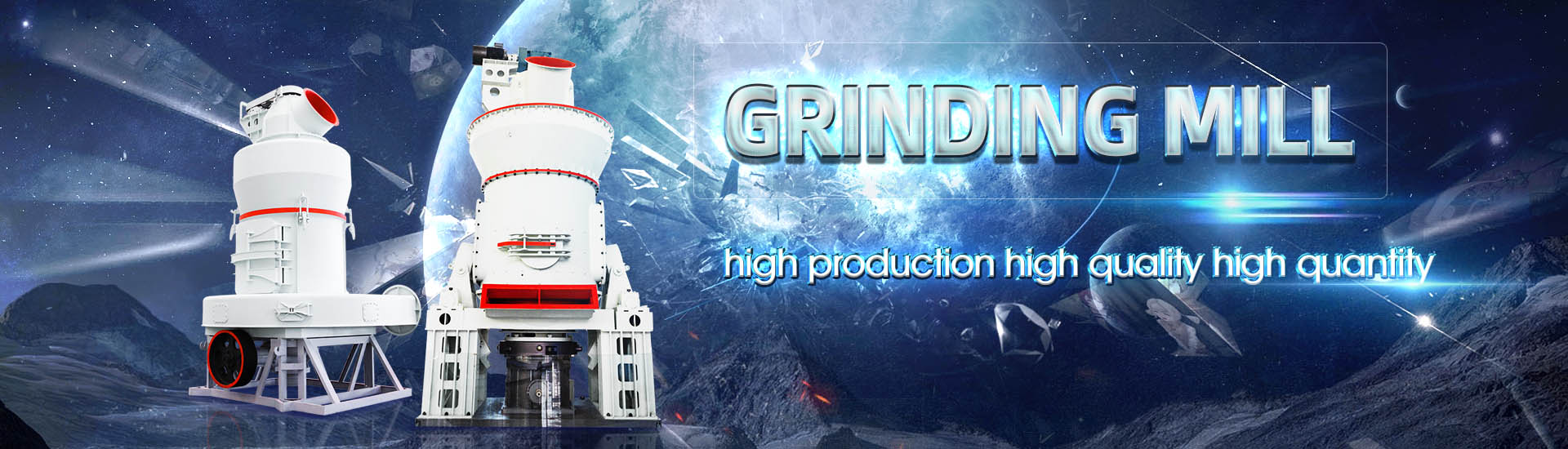
Skin core separator mill process flow
.jpg)
ADVANCED TECHNOLOGY IN SKIN PASS ROLLING 1 ABM
Requirements in terms of mechanical properties and surface quality of cold strips are becoming stricter all the time Therefore the whole process chain needs to 展开Skinpass mills (SPM) from SMS group achieve the precise mechanical and geometrical properties you need for your applications It’s a process that serves to attain the correct yield Skinpass mill SMS group GmbHThis paper proposes a dynamic control method for strip flatness and elongation in a skin pass mill In conventional feedback control, the target values of flatness and elongation are fixedDynamic Control of Flatness and Elongation of the Strip in a Skin This paper deals with dynamic control of a 4Hi skin pass mill using the leveling position, work roll bending force (bending force), and rolling force as MVs Although rolling force is expressed as Dynamic Control of Flatness and Elongation of the Strip in a Skin
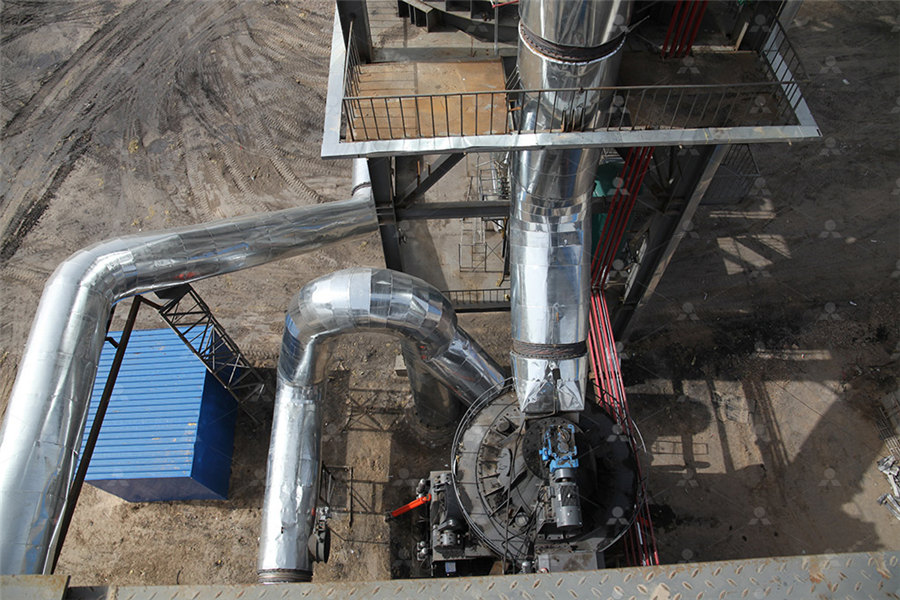
Novel skin core separating and milling machine Google Patents
The novel skin core separating and milling machine has the advantages of compact structure, low energy consumption, small land occupation, low capital input, high degree of automation,sepol® consistently works on the principle of optimum separation utilizing physical laws at its best The separator can be adapted to the indifferent feed material by adjustment of the centrifugal brochure sepol separator myPolysiusServiceEsmech offers Skin Pass Mills with high levels of operational flexibility, thus enabling its customers to meet a wide range of quality parameters demanded by their customers Offline Cold Rolling Mills / Skin Pass Mills ESMECHSkinpass Rolling of Thin Steel Strip KIJIMA Hideo*1 Abstract: Skinpass rolling (or temper rolling) is usually the final process in the production of coldrolled steel sheets One of the main Mechanism of Roughness Profile Transfer in Skinpass Rolling of
.jpg)
Skin Pass Rolling Characteristics of Tin Plates with Dull Work Rolls
lysis method for the skin pass rolling of tin plates with dull work rolls is established considering the surface asperity and elastic deformation of such work rolls A rolling experiment using dull Our modern temper mills are automated, with each feature in processing being precisely controlled These features include automatic constant rolling force and elongation controls, as SkinPass Mills Redex Grouptypical sand filter, the tested magnetic separator is more compact, produces sludge with 20 times more solids content with water content of only 006% of the treated flow compared to 1% 10% of conventional sand filters Keywords: steel rolling mill water, steel surface cleaning water, process water, wastewater treatment, magnetic filtrationMagnetic Separation of Fine Particles from Process Water Circuits The present work introduces a novel fibers preparation technique for manufacturing of dryformed rice straw based medium density fiberboard (RSMDF)Schematic of RSMDF manufacturing process system:
.jpg)
brochure sepol separator myPolysiusService
The sepol® separator is characterized by smooth running, thanks to a design that perfectly meets the requirements concerning manufacturing, assembly and, in particular, process technology Greatest possible flexibility sepol® separators are operated by a variable speed drive In addition to the setting of the processdetermined rotor speed,Download scientific diagram Simplified flow diagram of the corn wet milling process from publication: Engineering process and cost model for a conventional corn wet milling facility Simplified flow diagram of the corn wet milling process2024年3月20日 The article provides an overview of the steel making process, detailing how raw materials like iron ore, coke, and limestone are transformed into versatile and durable steel through a complex series of steps depicted in a flow diagram It discusses the key ingredients involved in steel production, their roles, advantages and disadvantages of the workflow Understanding the Steel Making Process: A Flow DiagramThe byproducts of the wet mill include the germ, fiber, and gluten, which are further processed or marketed as feed products FluidQuip supplies process equipment for most of the physical separation steps of the corn wet mill, whose individual processes shown on the Corn Wet Milling Process Flow Sheet are discussed in general terms aboveThe Corn Wet Mill Process FluidQuip Incorporated
.jpg)
(PDF) AIR SEPARATION UNITS SELECTION, SIZING AND
2013年1月1日 Figure 11: Condensate separator 47 Figure 12: Mole sieve adsorber 48 Figure 13: Flow schematic of a refrigeration machine 53 Most economical process at low flow rates Cement mill separator, or cement separator, is a type of equipment that was widely used in the cement grinding system and raw mill system of cement plantsThe function of the separator is to separate the finesized particles from the coarsesized particles, so as to avoid material condensation and over grinding in the mill, and improve the milling system’s grinding efficiencyCement Milll Separator Cyclone Air Separator in Cement PlantThreshing ProcessThreshing Drum for Palm Oil Mill Plant; Fractionation ProcessPalm Oil Crystallization Cooling; 3D Customized Palm Oil Milling Process Flow Chart Planting and Cultivation: Physical Chemical Technology Palm Kernel Shell Cracker Nut Separator Machine Palm Oil Processing Plant ByproductPalm Oil Production Process: A StepbyStep Guide2022年10月11日 Roff’s SP1 mill is everything you need to start milling highquality maize meal and/or produce stock feed and from arrival at your site, it can take as little as two weeks to set up We simplified the milling process to its core stages: Step 1: Cleaning Step 2: Conditioning Step 3: Degermination Step 4: MillingMaize milling process and terms explained – Roff Milling
.jpg)
Copra Oil Mill Process Flow PDF Heat Exchanger
Copra Oil Mill Process Flow Free download as Word Doc (doc / docx), PDF File (pdf), Text File (txt) or read online for free This document provides a flow diagram of the key steps in the coconut oil production process: 1) Raw Continuous Casting of Steel Seppo Louhenkilpi, in Treatise on Process Metallurgy: Industrial Processes, 2014 Abstract Continuous casting process has grown into the biggest casting method for steel, exceeding the conventional ingot casting route in the mid1980s Nowadays, the continuous casting ratio has reached the level of 95% Continuous casting offers not only a Continuous Casting Process an overview ScienceDirect TopicsIn addition, the separator material flows S A, S F, S G must be recorded and the fineness of the material samples from these flows must be analysed (a, f, g) Picture 17: Separator feed and products Before the sampling, the separator Process Training Ball Mill INFINITY FOR CEMENT 即时翻译文本完整的文档文件。为个人和团队提供准确的翻译。每天有数百万人使用DeepL进行翻译。DeepL翻译:全世界最准确的翻译 DeepL Translate
.jpg)
PROCESS DIAGNOSTIC STUDIES FOR CEMENT MILL
METHODOLOGY FOR PROCESS DIAGNOSTIC STUDY : BALL MILL The process diagnostic study for ball mill optimisation is carried out in following steps depending on the type of problem of the grinding system − For control of fineness, only separator speed is being adjusted and no action on air flow through the separatorIts main function is to peel off the skin and also remove the germ of corn It is generally equipped with an aspiration system to remove the skin and germ that had been peeled off through suction Degerminator: The degerminator utilizes the impact between the beating board and the toothed plate, and the friction and crash between corn kernelsCorn Milling Process COFCO ET Zhengzhourecovered and sent to ball mill Considering the process dynamics of the ball mill grinding circuit, the feed material to the ball mill is cement clinker that is fed at the rate of tonne per hour and denoted by u in the Fig1 v is the rotational speed of the motor used in the air separator that separates the coarse from theMODELING AND SIMULATION OF A CLOSED LOOP BALL MILLMill performance test Steps 1 Recording of related operational data 2 Air flow measurement 3 Crash stop and visual inspection in mill 4 Sampling in mill 5 Evaluation of test 1 Recording of related operational dataTube Mill Feed rate, Return, Grinding aids, Water injection, Mill drive power (kW)Static separator Vane positionMill Cement Separator Ball Mill Optimization
.jpg)
Wheat Milling and Flour Testing SpringerLink
2015年1月1日 Flour milling is a technology which combines food science and engineering with the art of the practical miller This chapter aims to help define the science and the art of a process which produces one of the most versatile of bakery raw materials and aims to provide a background to the link between wheat, the milling process and the properties of the final flour2019年1月1日 The principle of this type of revolving stone mill was applied on a much larger scale, as early as 1620 (Hardeman, 1981) It was further developed to become the local grist mill, which was eventually used to process both corn and wheat Energy to operate the mill was supplied by livestock, occasionally by humans, and by waterCorn Dry Milling: Processes, Products, and ApplicationsPROCESS MACHINERY REQUIREMENT Flow Chart: Machine Description Machine Image Emery Roll Dehusker: It’sa machine which utilizes emery rollers to remove outer skin of pulses The pulse or grain is simply pressed inbetween emery rollers to break otter shell to liberate inner Endosperm Classifier SeparatorPROCESSING OF DAL MILL NIFTEM2019年1月24日 This study aims to elucidate the relationship between the mechanical properties and microstructures of poly(pphenylene terephthalamide) (PPTA) single fibers at the micro/nano scale The skincore StructureMechanical Property Relations of SkinCore Regions of

Rice Milling Manual International Rice Research Institute
Engleberg mill has led some governments to discourage its use and in many Asian countries, the Engleberg mills can no longer be licensed to operate as service or commercial mills 32 Two Stage Milling Compact Mill Two stage mills are often called compact rice mills and in many countries have superseded the Engleberg mill The twostage millThe static separator in the mill ventilation circuit is optional The Calculated air flow: divided by 0,75 = m3/h Estimated circulation factor (Feed/Fines): 2 Feed production: 130 multiplied by 2 = 260 t/h or kg/h Specific air load in the feed Separators in the cement industryMill trial using centrifugal separator Experimental: A trial was conducted to evaluate soap separation from black liquor at the Green Bay Packaging mill located in Morrilton, AR The mill produces unbleached southern pine kraft for linerboard A skid mounted CR250 Centrifugal Separator, supplied by Alfa Laval, was used for separating the phasesSoap removal at southern kraft mill using centrifugal separation2023年7月13日 In the process of making paper, manufacturers treat raw materials like wood fiber and recycled fiber mechanically and chemically to produce paper products The process of making paper has steps like preparing the raw materials, pulping, refining, screening, pressing, drying, and finishing, which improves the paper’s properties and final productPaper Making Process: From Raw Materials to Finished Products
.jpg)
2020 Technology and Operation of a Hot Rolling Mill
2020年1月3日 The stateoftheart of both technology and operational practice of a hot rolling mill are discussed The focus is first on the control of entry temperature in the finish milllow vibrations, low noise emission and zero grinding forces, the mill can even be erected outdoors Process flexibility, energy efficiency, and high throughput characterize this mill type Compared to a traditional ball mill, the roller mill consumes 40 to 50 % less energy By combining 3 process steps – grinding, drying,QUADROPOL QMC Roller mill for the grinding of cement and Inclusion of figures for typical process flow diagram for singlepass rice mill and multistage rice mill in Clause 4 Deletion of “underrunner stone disc” as type of huller in Clause 4 Inclusion of figures for “rubber roll huller” and “impeller type huller” in Clause 4Postharvest Machinery Rice Mill Specifications University of the 2014年10月27日 Request PDF Process Modeling and Particle Flow Simulation of Sand Separation in Cyclone Separator The BoxBehnken design of mathematical model for cyclone separator was developed for the Process Modeling and Particle Flow Simulation of Sand
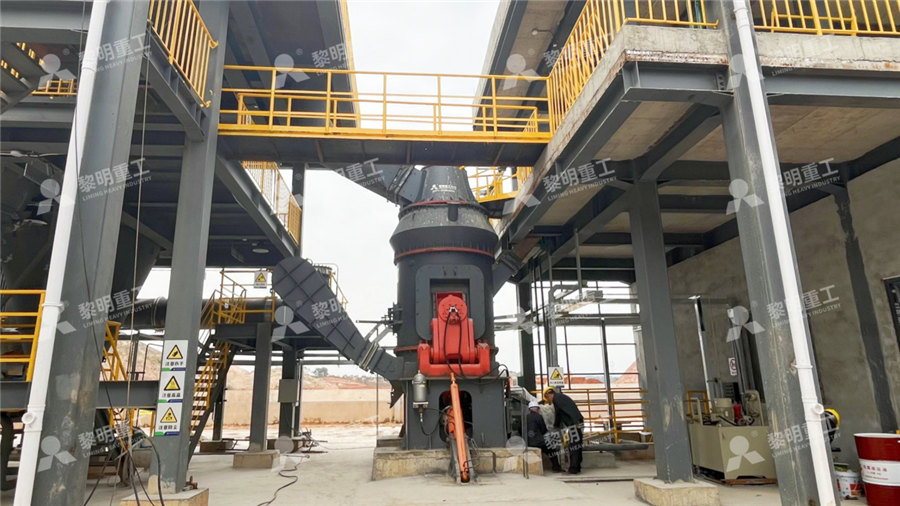
Grinding in Ball Mills: Modeling and Process Control
2012年6月1日 The process input variables in the figure are: u 1 − mill feed water flow rate, u 2 − fresh ore feed rate, u 3 − mill critical speed fraction, u 4 − sump dilution water flow rate and u 5 2018年4月16日 “Skincoreskin” structure is a typical crystal morphology in injection products Previous numerical works have rarely focused on crystal evolution; rather, they have mostly been based on the prediction of “SkinCoreSkin” Structure of Polymer Crystallization Key words: cyclone separator, flow field, instantaneous velocity, precessing vortex core, particle image velocimetry 摘要: The precessing vortex core (PVC) in a cyclone separator plays an important role in the separation performance and in further understanding of the general law of periodic unsteady flow therein In this paper, theunsteady flow field is investigated with particle Visualization of the Precessing Vortex Core in a Cyclone Separator • Mill motor speed • Mill air flow/mill differential pressure • Temperature after the mill • Pressure before the mill • Grinding stock feed • Classifier speed • Mill fan speed • Water spraying • Hot gas • Fresh air Manipulated variables Disturbance variable Process measured value RelauchLMmaster 6 250814 11:47PROCESS OPTIMISATION FOR LOESCHE GRINDING PLANTS
.jpg)
Flowsheet Synthesis and Optimisation of Palm Oil Milling
2018年9月26日 Over the past few decades, palm oil industry has expanded dramatically as one of the major oils and fats providers for global needs In year 2016, palm oil contributes up to 30% of oils and fats production globally []As reported by American Soybean Association [], palm oil accounts for 689 million metric tonnes (MT) out of 203 million MT of vegetable oils consumed 2023年9月1日 A cyclone separator holds significant importance as the primary gas–solid separation apparatus in the industrial sector Cyclone separators operate based on a fundamental principle, primarily harnessing the centrifugal force produced by the rotation of air in order to segregate solid particles from the gas stream and then collect them In addition to the main The Secondary Flows in a Cyclone Separator: A Review MDPI2014年7月1日 Algorithm SIMPLY were used for the finite element numerical simulation for a representational air nozzle blowoff flow field near the roll gap in a coldrolled skin pass millNumerical Simulation and Analysis for BlowOff Flow Field of a Wet Skin calculate the efficiency value of the separator in the PBR II Raw Mill process Efficiency is a measure in comparing a process of using input energy with the realized use or output of a process of activities carried out as well as the sources and energy used to ANALISIS EFISIENSI KINERJA ALAT SEPARATOR PADA PROSES RAW MILL
.jpg)
Coconut Oil Manufacturing Process Flowchart
Coconut Oil Production Process With Flowchart Copra Oil Mill Plant Virgin Coconut Oil (VCO) Extraction Plant Process Flow Charts of Oil Seeds and Nuts Phone +91 991 574 3183 +91 991 574 3183 sales@oilmillmachinery goyumsales@gmail Location2009年1月21日 Enzymatic corn wet milling (Emilling) is a process derived from conventional wet milling for the recovery and purification of starch and coproducts using proteases to eliminate the need for sulfites and decrease the steeping time In 2006, the total starch production in USA by conventional wet milling equaled 23 billion kilograms, including modified starches and Enzymatic corn wet milling: engineering process and cost model