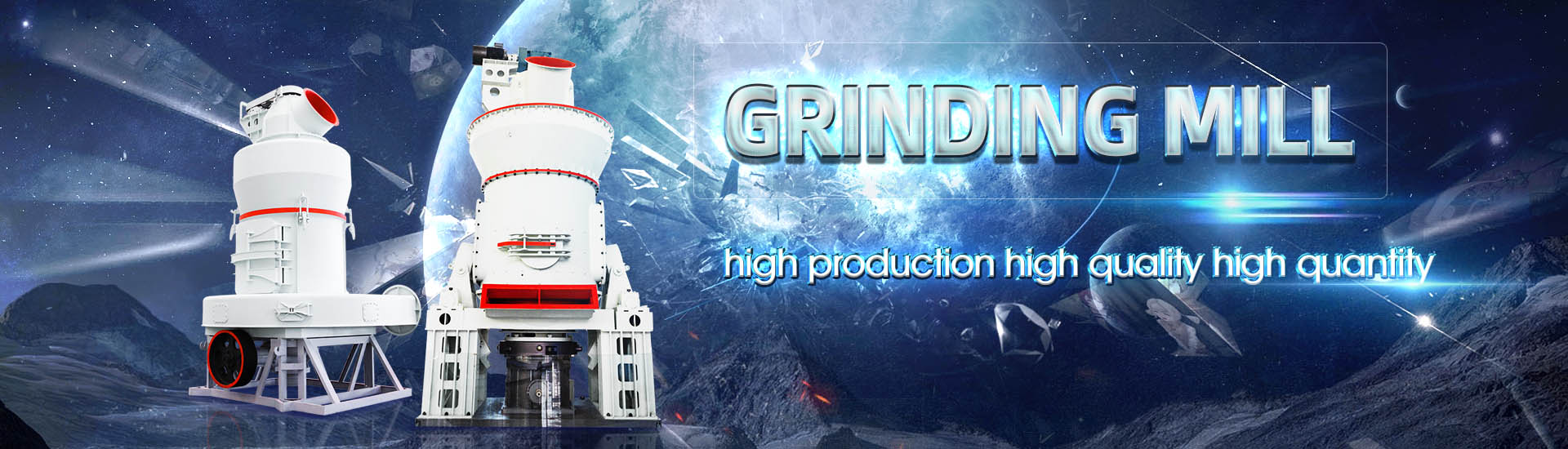
Feed size of ore mill
.jpg)
How Ball Mill Ore Feed Size Affects Tonnage Capacity
2017年7月26日 Under the right operating conditions, high power rate crushing can bring mill feed size down to near 80% passing 7,000 microns and finer, which can be handled more efficiently by ball mills Based on average field observations, the crushers can do this for less Successful manipulation of feed size starts with successful measurement Over a relatively short time period taking a belt cut and sieving the material is the most accurate method of I203 I204 INTRODUCTION SMC Testing2018年6月1日 In this article, alternative forms of optimizing the milling efficiency of a laboratory scale ball mill by varying the grinding media size distribution and the feed material particle size Effect of ball and feed particle size distribution on the milling In this article, alternative forms of optimizing the milling efficiency of a laboratory scale ball mill by varying the grinding media size distribution and the feed material particle size distribution were Effect of ball and feed particle size distribution on the milling
.jpg)
Tailoring ball mill feed size distribution for the production of a size
2019年9月1日 Narrowsize feeds of the ore were prepared and milled with 20 and 30 mm sets of singlesize balls using the onesize fraction method From the experimental data obtained, 2001年1月1日 For Autogenous (AG) and Semiautogenous (SAF) mills, the ore feed could vary with time in hardness, competence, grade and mineral composition, leading to frequent fluctuation in load dynamicsInfluence of feed size on AG / SAG mill performance2020年10月20日 In this research, the feed ore properties including hardness and particle size distribution was applied in order to improve the AG mill operation In the regard of particle size The performance improvement of a fullscale autogenous mill by 2023年10月27日 Ball sizes that are used in grinding should be large enough to break the largest and hardest ore particles Optimal ball sizes depend on the feed/product size ratio, mill A Review of the Grinding Media in Ball Mills for Mineral Processing
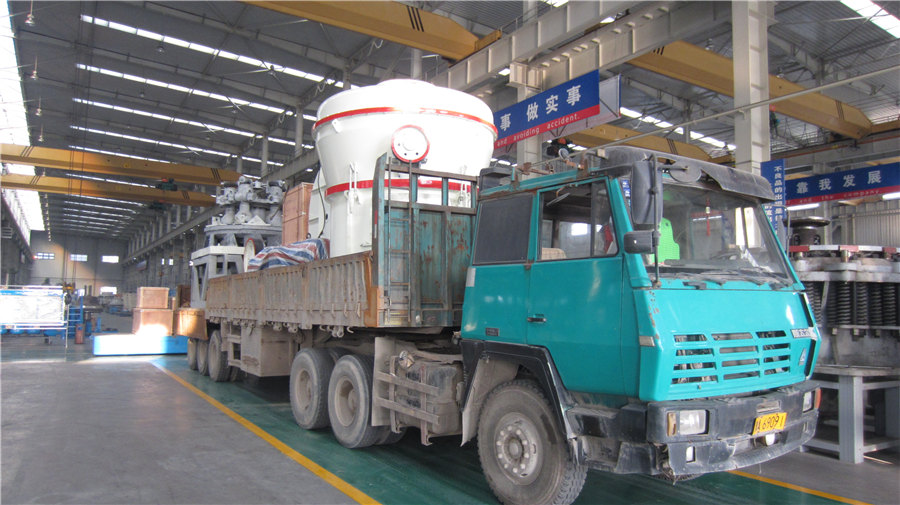
Primary Grinding Mills: Selection, Sizing And Current Practices
Most frequently, the feed to these mills is the product of primary crushing plants but in some cases run of mine ore is used as feed such as at Benguet, McDermitt, LBar Sohio, Bear 2017年5月19日 In this study, the effect of initial size ranges of feed (+132–315 mm) on the amount of grinding product and its size distribution has been evaluated, in order to find the Evaluating the effect of feed particles size and their hardness on 2013年7月15日 For any circuit, whether a crushing circuit, a rod mill, or a closed ball mill circuit, the Work Index always means the equivalent amount of energy to reduce one ton of the ore from a very large size to 100 umBond Work Index FormulaEquation 911Metallurgist2020年10月20日 One of the feed ore properties which can affect the grinding charge of an AG mill is particle size distribution Bergstedt and Fagremo (1977) studied the effect of feed size distribution on the performance of an AG during a series of pilot plant tests They reported that the ideal feed ore to an AG mill should have 10–15 wt% materials coarser than 100 mm Bouajila The performance improvement of a fullscale autogenous mill by setting
.jpg)
Ore Feed Size * Work Index Hardness: Crushing
2015年7月29日 The coarser ore being drier and having more space in between each piece than is normal, will not slow the flow of fine material towards the discharge points as much This means that when the crushers stop putting ore 2016年3月21日 Example: A mill in closed circuit with a classifier receives 300 dry tons of crude ore per day, and the percentages of solid are respectively 25, 50, and 84% in the classifier overflow, feed to classifier, and sand, equivalent to L: S ratios of 30, 10, and 0mon Basic Formulas for Mineral Processing Calculations2013年8月3日 In Grinding, selecting (calculate) the correct or optimum ball size that allows for the best and optimum/ideal or target grind size to be achieved by your ball mill is an important thing for a Mineral Processing Engineer AKA Metallurgist to do Often, the ball used in ball mills is oversize “just in case” Well, this safety factor can cost you much in recovery and/or mill liner Calculate and Select Ball Mill Ball Size for Optimum Grinding2018年6月1日 A number of researchers (Deniz, 2012; Bwalya et al, 2014; Petrakis et al, 2016) carried out studies about the effect of feed particle size and grinding media size on the grinding kinetics of different oresKhumalo et al, 2006 postulated that generally larger sized grinding media would break larger particles quicker but a finer product would be obtained by use of Effect of ball and feed particle size distribution on the milling
.jpg)
Influence of feed size on AG/SAG mill performance
100 2500 20 18 80 16 14 Mill Throughput 60 40 20 Sieve 1500 12 10 1000 8 6 500 Split 0 01 1 10 Size (mm) 100 1000 4 Specific Power 2 0 0 50 Figure 1: Sag Mill Feed Size Comparison Between Sieving and Image Analysis Using the “Split” Throughput Specific Power Cum% Passing 2000 60 70 80 90 100 110 120 Feed Size F80 (mm)(mm) Figure 2 2023年3月16日 Feed size was divided into two fractions of (+238 −4) and (+2 −238) millimeters, from which different feeds with different weight and size percent values were fed to mill at three feeds of Fractal approach of particle size distribution description of ball 2019年1月1日 The variable LOAD represents the volume of total ore, water, and balls within the mill The water and ground ore forms a slurry inside il Inlet W ter IW Mill Load (LOAD) Sump Volume (SVOL) Sump ater (SFW) Cyclone Feed Density (CFD) Cyclone F ed Flow (CF ) Particle Size Estimate (PSE) Mill Feed Ore ( FO) Mill Feed Balls (MFB) Cyclone Pump Fig 1Feed Size Distribution Feedforward Control for a Grinding Mill 2015年11月30日 The results of both open and closed circuits showed that the feed size had no effect on the mill product size 180 circuit’s feed size, the ore was passed through screens with aperture of 12 (PDF) Effects of Flow Rate, Slurry Solid Content and
.jpg)
Investigation on the particle size and shape of iron ore pellet feed
Investigation on the particle size and shape of iron ore pellet feed using ball mill and HPGR 909 areas of 500–1600 cm2 g1The concentrate must therefore be reground in order to2017年3月20日 Physicochemical Problems of Mineral Processing Investigation on the particle size and shape of iron ore pellet feed using ball mill and HPGR grinding methods March 2017 DOI: 105277/ppmpPhysicochemical Problems of Mineral Processing Investigation 2018年1月19日 The key ore related parameters relevant to throughput for the BHX circuit are the size distribution of the feed to the mill and the comminution or mill hardness The feed size is a function of the fragmentation from blasting and primary crushingPredicting Mill Ore Feed Variability Using Integrated Geotechnical 2014年4月19日 DOI: 105277/PPMP Corpus ID: ; Investigation on the particle size and shape of iron ore pellet feed using ball mill and HPGR grinding methods @article{Abazarpoor2014InvestigationOT, title={Investigation on the particle size and shape of iron ore pellet feed using ball mill and HPGR grinding methods}, author={Armin Abazarpoor Investigation on the particle size and shape of iron ore pellet feed
.jpg)
Influence of feed size on AG / SAG mill performance
Semantic Scholar extracted view of "Influence of feed size on AG / SAG mill performance" by S Morrell et al The productivity of milling circuits is sensitive to the size of mill feed Uncertainty about the size of caved ore presents unique challenges to forecasting and controlling mill throughput rates Expand 2 1 Excerpt;2023年10月27日 From the study, the optimal media size was 40 mm for a feed size of −2 + 045 mm and 30 mm for a feed size of −045 + 015 mm Cayirli also agrees with the fact that larger balls can crush large particles better but at a lower grinding rate whilst smaller balls are unable to break large ore particles but grind smaller particles at a higher grinding rateA Review of the Grinding Media in Ball Mills for Mineral Processing 2022年5月23日 Grinding experiments were conducted in a laboratoryscale stirred mill on a lowgrade PGE bearing chromite ore HighPressure Grinding Rolls (HPGR) product of −1 mm was used as feed material to (PDF) Modeling and application of stirred mill for the coarse Number, size and mass of each ball size depends on mill load and whether or not the media is being added as the initial charge For the initial chargin of a mill, Coghill and DeVaney (1937) defined the ball size as a function of the top size of the feed, ie, d↓V = 040 K√F dB = ball size (cm) F = feed size (cm)AMIT 135: Lesson 7 Ball Mills Circuits – Mining Mill Operator
.jpg)
Acoustic Sensing and Supervised Machine Learning for
2023年4月11日 The harsh and hostile internal environment of semiautogenous (SAG) mills renders realtime monitoring of some critical variables practically unmeasured Typically, feed size fractions are known to cause mill fluctuations Ø Manipulation of SAG Mill Operating Parameters (eg load, ball charge, speed and density) Ø Maximising Pebble Recycle Load and Crusher Interaction With the SAG Mill I12 Ø Effect of SAG Mill Feed Size Distribution and Ore Variability Ø Mill liner design modifications, and Ø Circuit Design Considerations That Influenced ThroughputØ Effect of SAG Mill Feed Size Distribution and Ore Variability The mill was charged with ore having a SG of 265 and the load was 40% of the mill volume The grinding media steel balls occupied 122 % of the mill volume The mill was rotated at 75% of its critical speed, which was 129 rpm Estimate:1 The charge density, ρ C 2 The toe angle, 3 The shoulder angleSemi Autogenous Grinding Mill ScienceDirect TopicsImage of a “Classical” 3stage ore crushing prior to rod mill [image: (13551)] Diagram of Typical 12 stage ore crushing prior to AGSAG mill [image: (13552)] Therefore, if a 3 mm crusher product is required, maximum feed size to the secondary crusher would be 240 mm Thus, the feed to the primary crusher should not exceed 2400 mmAMIT 135: Lesson 5 Crushing – Mining Mill Operator Training
.jpg)
Feed Size Distribution Feedforward Control for a Grinding Mill
2019年1月1日 Request PDF Feed Size Distribution Feedforward Control for a Grinding Mill Circuit This paper proposes a method to measure and reject disturbances caused by changes in the ore distribution of foot diameter SAG mill was designed to treat 2065tph of monzonite ore at a ball charge of 8% volume, total charge of 25% volume and an operating mill speed of 74% of criticalØ Effect of SAG Mill Feed Size Distribution and Ore Variability Mill feed particle size circuit’s feed size, the ore was passed through screens with 180 aperture of 12, 20, 25, and 30 mm prior to feeding the material to the 2 mm trommel screen5 Effects of flow rate, slurry solid content, and feed size Figure 3(a)—Pilot SAG mill Ecs vs Ball Load, Reproduced from Morrell (2006a); (b) SAG Mill Ecs vs Ball Load for ‘OpenCircuit’ SAG Mills in JKTech Database 0 2 4 6 8 10 12 14 16 18 20 0 2 4 6 8 10 12 14 SAG mill Ecs (kWh/t) Ball load (%) 0 5 10 15 20 SAG mill Ecs (kWh/t) Ball load (%) Coarse feed, uncrushed pebbles Very soft ores, Axb >80SAG Mill Design and Benchmarking Using Trends in the JKTech
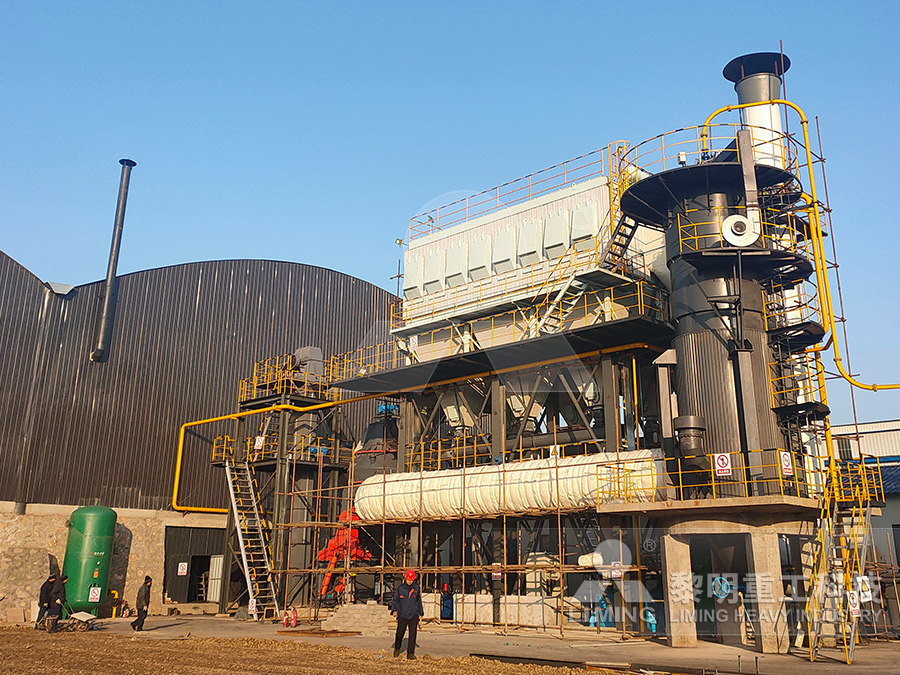
Schematic of ideal SAG mill feed size distribution
Download scientific diagram Schematic of ideal SAG mill feed size distribution from publication: For example, preconcentration (possibly using bulk ore sorting technology) In this paper, the effect of the feed size distribution was studied for a ball mill Copper ore of 05% was tested using batchgrinding tests Samples were carried out using three reconstructed feed size distributions in an experimental ball millStudy of the effect of the mineral feed size distribution on a ball 2024年7月31日 The production of cement, an essential material in civil engineering, requires a substantial energy input, with a significant portion of this energy consumed during the grinding stage This study addresses the gap in Effect of Grinding Conditions on Clinker Grinding 2016年7月8日 UNTIL THE THIRD THEORY OF COMMINUTION of "Work Index" method of determining crushing and grinding mill size was introduced, Sizing a Ball or Rod Mill Sizing a Crusher using >1200 Wi of Ores from Equipment Sizing: Crusher or Grinding Mill

Tailoring ball mill feed size distribution for the production of a size
2019年8月1日 Feed size was divided into two fractions of (+238 −4) and (+2 −238) millimeters, from which different feeds with different weight and size percent values were fed to mill at three feeds of Although it is well known and easily experienced that the feed size distribution influences the throughput and stability of operation of a semiautogenous grinding (SAG) mill, the details are poorly understood since it is often only the input and output measurements that are used to identify unfavourable inmill conditions Load cells and power monitoring are sometimes used Understanding Size Effects of Semiautogenous Grinding (SAG) Mill 911 Metallurgist can enter the scene and see what you have become blind to We can fix issues in ways you never thought possible Our fresh eyes will open new opportunities for your plant Each mineral processing plant has varied ore types, mining equipment, (crusher, ball mill, flotation, tailings), and management (operating) philosophyThe evaluation and prioritization of variables Metallurgists Mineral Processing Engineers 911MetallurgistA new method, staged flotation for effectively increasing the recovery of ultrafine copper oxide ore with a new type of collector (ZH1, C35 carbon chain xanthate) is proposed for the first timeParticle size distribution (PSD) of the mill feed
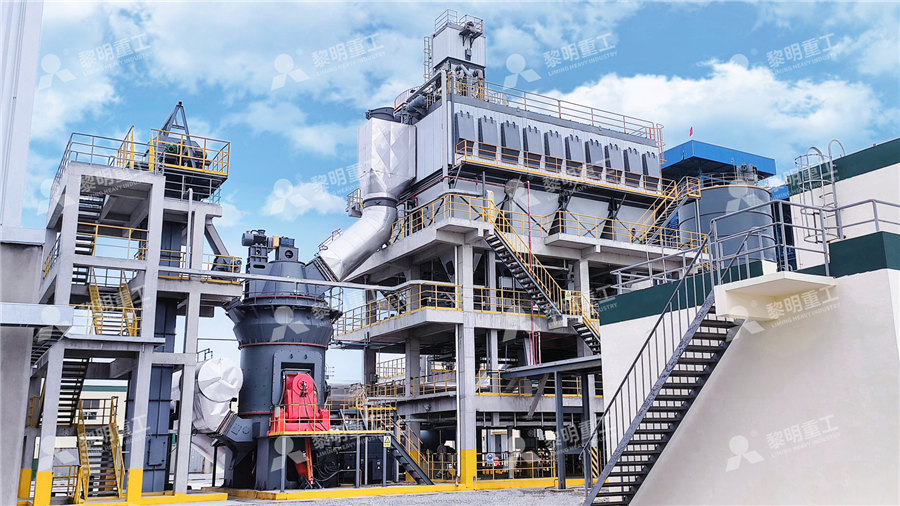
PreProcessing to Increase the Capacity of SAG Mill Circuits
2022年6月6日 Further tests indicated that: (a) a reduction to 74 kWh/t by increasing the mill speed (SAG6), (b) an increased to 92 kWh/t by reducing the number of pebble ports open (SAG12), (c) an increase to 81 kWh/t by coarsening the feed size distribution together with increasing the mill speed (SAG9), as well as (d) a reduction to 66 kWh/t by Ball mills tumble iron or steel balls with the ore The balls are initially 5–10 cm diameter but gradually wear away as grinding of the ore proceeds The feed to ball mills (dry basis) is typically 75 vol% ore and 25% steel The ball mill is operated in closed circuit with a particlesize measurement device and sizecontrol cyclonesBall Mill an overview ScienceDirect TopicsThis document discusses SAG mill grinding circuit design Some key points: 1) Adding pebble crushing is common to reduce buildup of critical sized particles in SAG mills and improve efficiency 2) Important aspects of pebble crusher circuit design include preparing clean/sized feed, metal removal, surge capacity, sizing for capacity and maintenance bypass 3) Crushed SAG Mill Grinding Circuit Designselected iron ore samples is shown in Table 2Inthe crushing machine, all the three iron ore samples were crushed to −3 mm and analyzed for the desired P 80 passing (−150 μm) and percentage of hematite liberated in the three feed iron ore samples The – 150μm feed size fractions were selected to determine the nominalEstimation of Grinding Time for Desired Particle Size Distribution