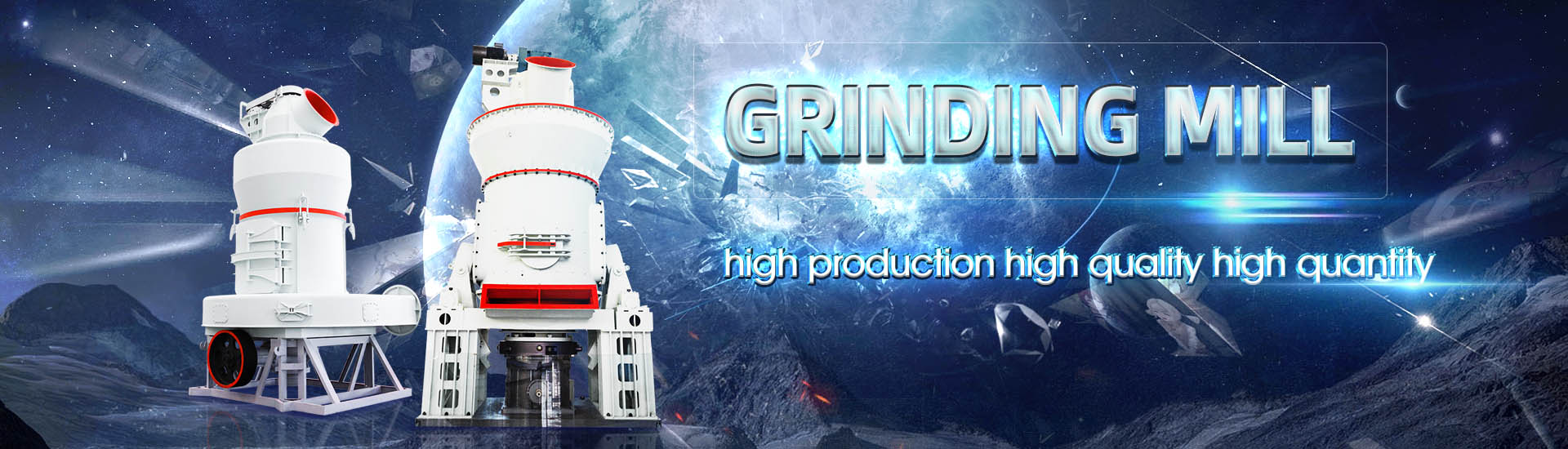
What is the output of a cement mill with a diameter of 33 meters
.jpg)
OPTIMIZATION OF CEMENT GRINDING OPERATION IN BALL MILLS
Optimization of the Cement Ball Mill Operation Optimization addresses the grinding process, maintenance and product quality The objective is to achieve a more efficient operation and Closed circuit ball mill with two compartments for coarse and fine grinding are generally found in cement plants for cement grinding Compartments (filled with grinding media) are divided by a Cement Grinding Cement Plant Optimization2021年1月1日 Vertical roller mill has proved to be a popular choice for finished cement grinding over all other machineries due to advantages like low power consumption, higher capacity, Review on vertical roller mill in cement industry its performance The Cement Plant Operations Handbook is a concise, practical guide to cement manufacturing and is the standard reference used by plant operations personnel worldwide Providing a The Cement Plant Operations Handbook International Cement
.jpg)
Analysis of material flow and consumption in cement
2016年1月20日 The results show that approximately 248 t, 469 t, and 341 t of materials are required to produce a ton of the product in raw material preparation, clinker production, and 2020年5月1日 In this work, the energy and exergy analyses of a cement ball mill (CBM) were performed and some measurements were carried out in an existing CBM in a cement plant to Energy and exergy analyses for a cement ball mill of a new 2 BALL MILLS INTERNATIONAL CEMENT REVIEW FEBRUARY 2021 aim of delivering a target mill discharge size at the end of the chamber, with a maximum residue of five per cent >2mm BALL MILLS Ball mill optimisation Holzinger ConsultingOperation and Elements of a ClosedCircuit Ball Mill System Cement ball mills typically have two grinding chambers The first chamber is filled with larger diameter grinding media and lined with lifting liners The first chamber coarse Optimization of Cement Grinding Operation in Ball

IMPROVING THERMAL AND ELECTRIC ENERGY
2019年3月8日 257 HighEfficiency Fans for Cement Mill V ents (emissions per unit of output) by improving energy efficiency, to eight meters is installed at a three to fourdegree angle that Abstract: The production of cement is rather complex process which includes a high amount of raw materials (eg, limestone, marl, clay, and iron ore), heat, electricity and different fuels The overall input and output of cement productionIn the diagram above of a precalciner kiln, raw meal passes down the preheater tower while hot gases rise up, heating the raw meal At 'A,' the raw meal largely decarbonates; at 'B,' the temperature is 1000 C 1200 C and intermediate Manufacturing the cement kiln Understanding Previous Post Next Post Contents1 Ball charge optimization2 1 How to use the BP21 2 Description of the main indicators used in this BP2101 The residue on 2mm/4mm before partition wall2102 Material filling level and ball charge expansion211 Cement mill specific power 1st compartment 212 Raw mill specific power 1st compartment Ball charge Ball charge optimization INFINITY FOR CEMENT EQUIPMENT

Grinding in Ball Mills: Modeling and Process Control
2012年6月1日 discharging the output product The size of a mill is usually characterized by the sizes of the balls ranging from 10 to 150 mm in diameter Mill – Cement and Concrete Research, V ol and cement Roller presses are used mainly in combination with a ball mill for cement grinding applications and as finished product grinding units, as well as raw ingredient grinding equipment in mineral applications This paper will focus on the ball mill grinding process, its tools and optimisation possibilities (see Figure 1) The ball millBALL MILLS Ball mill optimisation Holzinger Consulting2017年10月20日 1 Introduction Nowadays, cement manufacturing is an energyintensive industry The energy costs of cement industry are about 40% of the product cost that indicates that this sector is one of the biggest CO 2 emitter The global anthropogenic CO 2 emission of cement industry is approximately 5% []The International Energy Agency reported in 2011 that Heat Integration in a Cement Production IntechOpenWide product range: For meeting various requirements from different clients, our cement mill range from cement ball mill, vertical cement mill, Raymond mill, coal mill in cement plant, etc Strong production ability : AGICO CEMENT has a large production capacity and rich experience to produce any cement equipment required in cement plantCement Mill Cement Ball Mill Vertical Cement Mill Factory
.jpg)
How to Improve Cement Ball Mill Performance
The performance of the cement ball mill in cement grinding system directly affects the output capacity and cement quality of the cement plant which can reduce the diameter of the clinker particles to 5 ~ 8mm 2) The pregrinding adds a roller press to What is Cement Mill? A cement mill Ball mills are normally operated at around 75% of critical speed, so a mill with diameter 5 metres will turn at around 14 rpm increasingly commonly, instruments attached directly to the output ducts of the mill In either case, the results can be fed directly into the mill control system, News What is Cement Mill?2022年3月16日 Cement ball mill is a kind of equipment for further fine grinding of materials, with high fineness It is widely used in industry, metallurgy, chemical industry, cement and other industries TheWhat is a Cement Ball Mill? How to Use It? by 2015年2月14日 Costea et al [13] developeda fuzzy logicbased control architecture in which the ball mill grinding process was considered as a single input and single output system (SISO) and the total feed Control System Architecture for a Cement Mill Based on Fuzzy
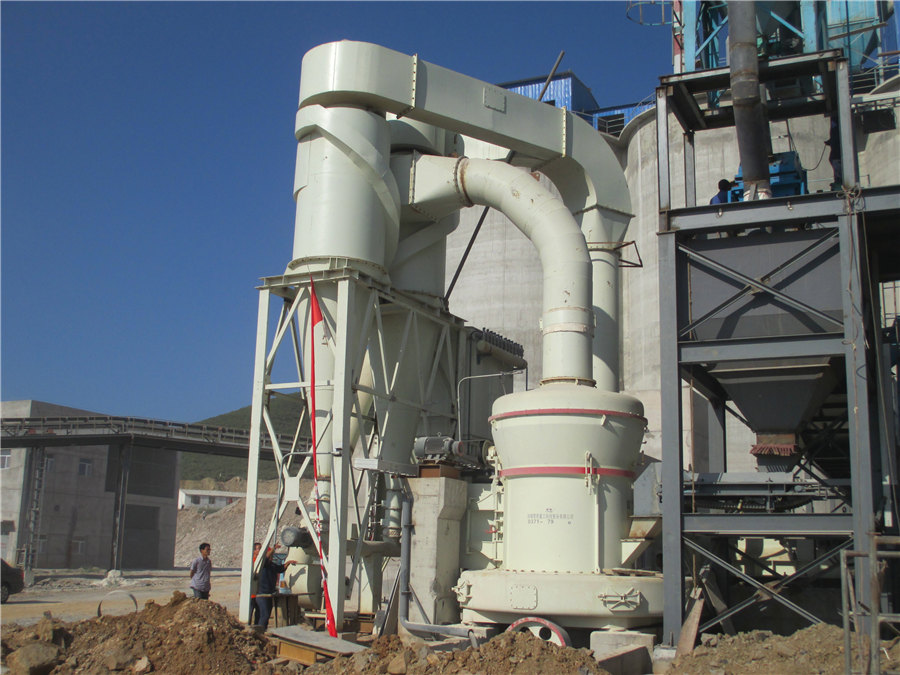
Improvements in New Existing Cement Grinding
3 Factors affecting ball mill performance 4 Ball mill improvements case examples 5 Conclusions question time Introduction Cement manufacture is energy intensive o Cement manufacture consumes typically 3,100 – 3,400 MJ 2023年1月1日 The control objectives of a rotary kiln are to reduce heating fuel consumption, increase clinker output, and improve cement quality However, these goals have more critical interdependencies and rely on unpredictable input parameters, including raw material quality and internal thermal regulation [6]Due to these complexities, a proper tradeoff is needed to A comprehensive review on Advanced Process Control of cement ball mill open and closed circuits [12] with the installation in all cases the dynamic separator When transferring to closedcircuit а mill size 26×13 m at a constant quality cement (3000 cm2pg) capacity grinding unit was increased from 25 to 38 tph while reducing the specific consumption of electricity from 416 to 293 kWhpt The parameterAnalysis of the efficiency of the grinding process in closed circuit In order to improve the output of the cement ball mill grinding system and reduce energy consumption, we have done some researches and analysis and finally, find out effective solutions Adopt Pregrinding Technology The application of pregrinding technology is the main way to greatly increase the output of cement ball mill grinding systemBall Mill For Cement Grinding – Cement Ball Mill Ball Mill
.jpg)
Cement Mill Optimization: Practical Strategies for Enhanced
Adjusting mill parameters: Finetuning mill parameters such as mill speed, ball charge, filling ratio, and grinding media size can have a substantial impact on the grinding efficiency of the mill For example, a 10% increase in mill speed can result in up to 10% higher production rate, while optimizing the ball charge can lead to a 510% reduction in energy consumption2020年2月1日 Nowadays, ball mills are used widely in cement plants to grind clinker and gypsum to produce cement In this work, the energy and exergy analyses of a cement ball mill (CBM) were performed and Energy and exergy analyses for a cement ball mill of a new 2020年7月2日 After determining the model parameters, the mill was simulated in mill fillings of 15, 20, 25, 30, 35 and 40% with ball media of 2 and 25 cm in diameter For every mill filling, the numbers of (PDF) Effects of Ball Size Distribution and Mill Speed and Their 2023年12月20日 The result is called clinker, which are rounded nodules between 1mm and 25mm across The clinker is ground to a fine powder in a cement mill and mixed with gypsum to create cement The powdered cement is then mixed with water and aggregates to form concrete that is used in constructionThe Cement Manufacturing Process Thermo Fisher Scientific

Deep decarbonisation of industry: The cement sector Europa
Cement is the binding agent of concrete, the most widely used construction material in the world The cement sector is a major greenhouse gas emitter, responsible for about 7% of CO 2 emissions globally (1), and about 4% in the EU While Cement Mill The ball charge tendency in the 1 st compartment is to use the coarser of the gradings available When producing high Blaine Cement it is the objective to use less tonnage Achieve nearer 89 kWh/t at the target mill Everything you need to know about clinker/cement Cement manufacturing brief description of a cement mill Cement clinker is usually ground using a ball mill This is essentially a large rotating drum containing grinding media normally steel balls As the drum rotates, the The cement millIt is usually combined with a cement ball mill to form a highefficiency cement grinding system because the practice shows that the we usually adopt the cement roller press to replace the fine crushing and coarse grinding role of the ball mill This increases the output of the ball Roller Diameter(mm) 1000: 1200: 1200: 1200: 1400: 1400 Cement Roller Press Roller Press In Cement Plant Roller Press
.jpg)
Optimization of Cement Grinding Operation in Ball Mills PEC
Feed material is ground in the ball mill, discharged and fed to a classifier with the help of a bucket elevator for classification of the ground cement into two streams – coarse and fines The coarse fraction is sent back to the mill and the fines are collected in cyclones and / or a baghouse as finished productA cement ball mill is ready for transportation There are many kinds of industrial equipment used in a cement plant, including thermal equipment, grinding equipment, dust removal system, transportation system, storage system, and so onWhen placing an order, we may need to order different equipment from multiple manufacturers at the same timeHow to Start a Cement FactoryThe milling process involves the use of a ball mill, a large rotating drum that grinds the clinker and other additives to produce cement powder Importance of Cement Milling Cement milling is a crucial step in cement production that significantly impacts the final product’s quality Here are some reasons why cement milling is essential: 1What is the Importance of Cement Milling ball mills supplier2023年1月29日 What Is The Difference Between Raw Mill And Cement Mill? In terms of output, Raw mill produces fine powder while Cement Mill produces clinker with minor additions of other ingredients depending on type of cement produced What Is Cement Milling? Difference Between Raw Mill And Cement Mill
.jpg)
Ball Mill In Cement Plant Selling Various Types Of Cement Mill
The company’s cement ball mill has 31 specifications and models with a cylinder diameter ranging from 22m to 42m, and the supporting motor is 380KW to 3530KW A single cement ball mill can meet the grinding of 1187t cement products per hour, such as with a roller press Combined use, the production capacity will be greatly improvedVertical roller mills and ball mills represent two clearly distinct technologies However, with proper adjustments to the operational parameters of the vertical roller mill almost identical cement properties can be achieved by the two mills that satisfy the cement user’s demandsNevertheless, the two types of mills have their distinctive meritsCement grinding Vertical roller mills VS ball mills2018年4月1日 The average particle diameter of cement was reduced by 365 μm when 003 wt analyses of a cement ball mill energy saving potential of the cement industry is 1906% and 3369 Energy and cement quality optimization of a cement grinding 1995年10月29日 The control system, based on a 2S4265 CNC unit, allows the milling machine to be operated in universal mode (with manual control), automatic mode (to a set program), copying mode, gauging mode (PDF) Cement mill optimization: Design parameters
.jpg)
Review on vertical roller mill in cement industry its performance
2021年1月1日 India is the world's second largest producer of cement and produces more than 8 per cent of global capacity Due to the rapidly growing demand in various sectors such as defense, housing, commercial and industrial construction, government initiative such as smart cities PMAY, cement production in India is expected to touch 550–600 million tones per 2023年2月25日 The angle of repose is an intrinsic characteristic of a given material; it depends principally on: particle size, rotational speed of the kiln (Fig 2), and surface condition of the kiln wallMore specifically, this angle characterizes the flow properties of “solid particles” in the kiln; it is often assumed to be constant but may vary along the length of the kiln, in correlation with Rotary kiln process: An overview of physical mechanisms, models 2022年5月9日 Cement production is one of the most energyintensive manufacturing industries, and the milling circuit of cement plants consumes around 4% of a year's global electrical energy productionModeling of energy consumption factors for an industrial cement 2013年8月3日 In Grinding, selecting (calculate) the correct or optimum ball size that allows for the best and optimum/ideal or target grind size to be achieved by your ball mill is an important thing for a Mineral Processing Engineer AKA Metallurgist to do Often, the ball used in ball mills is oversize “just in case” Well, this safety factor can cost you much in recovery and/or mill liner Calculate and Select Ball Mill Ball Size for Optimum Grinding

INCREASING OUTPUT OF CEMENT GRINDING IN BALL MILL
Increasing Output Of Cement Grinding In Ball MillCase Study 5 INCREASING OUTPUT OF CEMENT GRINDING IN BALL MILLCASE STUDY 1MOHAN SINGH PANWAR, 2AJAY KUMAR BANSAL, 3HEMANI PALIWAL 1Student, 2Guide, 3External Guide Email: l, 2ajaykumarbansal@poornima, 3hemani8588@gmailWith the increase of cement mill specifications and the requirement of energy saving, high yield, and high quality of cement grinding plant, the closedcircuit grinding is an inevitable trend of cement grinding unitThe essential equipment of a closedcircuit grinding system is a cement classifier, also known as a cement separatorThe function of the cement classifier is to select How To Measure Your Cement Mill And Cement Classifier? AGICO CEMENT2024年1月23日 Cement mill is a crucial equipment in the cement production process, responsible for grinding clinker and other materials to produce the final cement product Skip to content HOME The efficient operation of cement grinding mills directly impacts the quality and output of cement production Beyond cement production, How To Optimize The Operation Of The Cement Mill2023年2月13日 The output of a cement mill is affected by several factors, including the material used in the mill, the size and type of grinding media, the speed of the mill, What are factors that will affect the output of a cement mill?