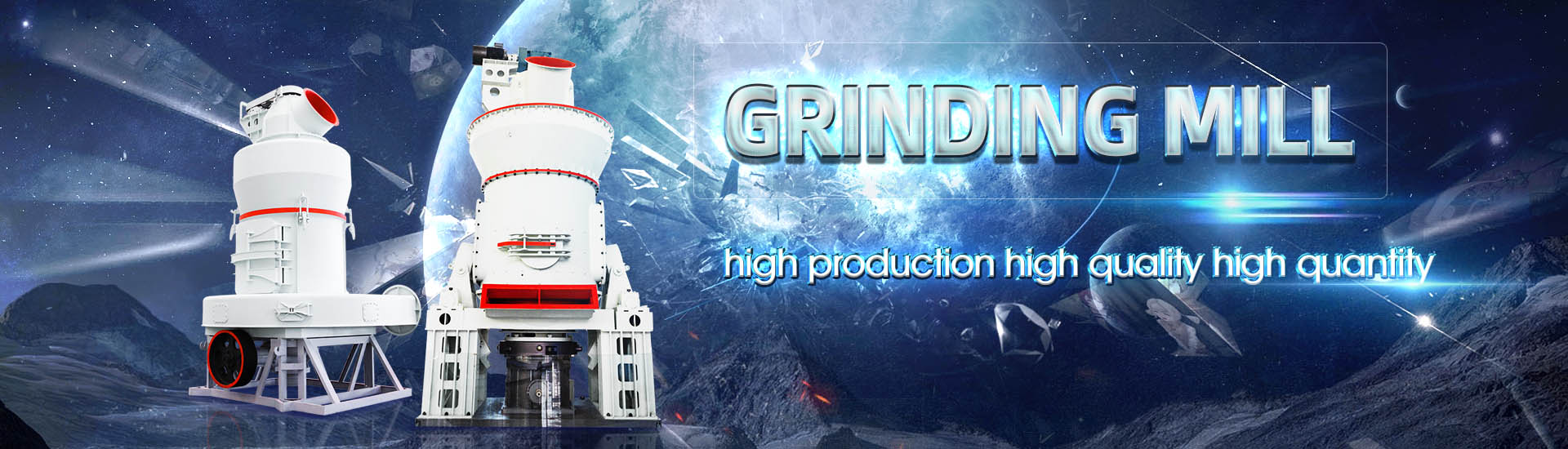
Cement grinding process
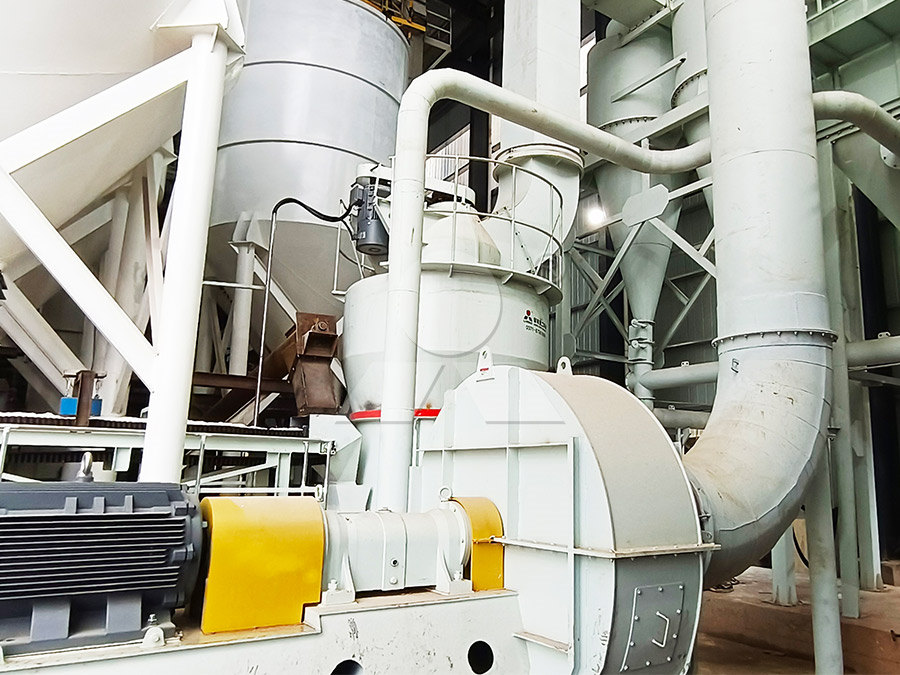
Cement Grinding Unit Process High Quality Cement
Explore Amrit Cement's stateoftheart cement grinding unit Learn about our cement grinding process and plant stages for high quality cementHighly energy intensive unit operation of size reduction in cement industry is intended to provide a homogeneous and super fine (30004000 Blain) cement Grinding operation is monitored for Cement Grinding Cement Plant OptimizationUnderstanding the manufacturing of cement, which intricately involves grinding, crushing, and burning processes, is essential for professionals in construction, engineering, and environmental scienceStepbyStep Guide to the Manufacturing of CementGrinding plays a pivotal role in the cement manufacturing process, transforming raw materials into a fine powder suitable for creating cement It’s a crucial step that directly impacts the physical Grinding in Cement Manufacturing: Key Process, Types of Mills,
.jpg)
Overview of cement grinding: fundamentals, additives,
2017年5月19日 PDF Grinding is an essential operation in cement production given that it permits to obtain fine powder which reacts quickly with water, sets in few Find, read and cite all the researchGrinding with propylene glycol generates approximately 800 Cm 2 /gram cement more surface than grinding without an aid, given the same energy consumption the most popular grinding CEMENT GRINDING SYSTEMS INFINITY FOR CEMENT EQUIPMENTCement grinding and packing process The clinker is ground with an amount of gypsum to a fine powder in order to regulate the setting time of cement and to gain the most important property Cement grinding and packing process Al badia cement2018年8月28日 Proportioning of raw material at cement plant laboratory Now cement plant grind the raw mix with the help of heavy wheel type rollers and rotating table Rotating table rotates continuously under the roller and brought Cement Manufacturing Process The Engineering
.jpg)
CEMENT GRINDING SYSTEMS INFINITY FOR CEMENT EQUIPMENT
The cement grinding process accounts for approx 40% if this energy consumption Further the quality of the final cement is very dependent on the operation mode and product quality as well as consumption of electrical energy it is important that the cement grinding plant is 2018年8月28日 Cement Manufacturing Process Cement is the basic ingredient of construction and the most widely used construction material It is a very critical ingredient, because only cement has the ability of enhancing viscosity of Cement Manufacturing Process The Engineering Nowadays, the dry process is the most popular cement making process which is widely adopted by cement plants all over the world for its great advantages in energy saving and environmental protection Cement Making Process The How Is Cement Produced in Cement Plants Cement 2016年10月5日 Due to the more energyefficient grinding process, Cemex® ground cement will usually have a steeper particlesize distribution curve than corresponding ball mill cements Consequently, when ground to the same specific surface (Blaine), Cemex® cement will have lower residues on a 32 or 45 μm sieve and tend to have a faster strength developmentEnergyEfficient Technologies in Cement Grinding IntechOpen
.jpg)
How Cement is Made Portland Cement Association
While each cement plant may differ in layout, equipment, and appearance, the general process of manufacturing portland cement is the same: crushed limestone and sand are mixed with ground clay, shale, iron while others use a wetgrinding process involving water Quarrying Cement manufacturers quarry raw materials including limestone, clay 2023年7月19日 Grinding aids, primarily amine group chemicals, are used to reduce agglomeration and increase concrete strength in order to ensure an efficient comminution process in the modern cement industryIntensifying the cement grinding process ResearchGatewith essential process calculations Contents Section A – Process summaries 1 Introduction 10 1 The basics of cement manufacture – 2 History of cement manufacture – 3 Portland cement in today’s world 2 Raw materials management system – 22 Concrete problems 16 1 Raw materials – 2 Raw mix – 3 Reserves – 4 Crushing – 5 The Cement Plant Operations Handbook International Cement The grinding process can be done in ball or tube mill or even both Then the slurry is led into collecting basin where composition can be adjusted The slurry contains around 3840% water that is stored in storage tanks and kept ready for the Manufacture of Cement Materials and Manufacturing Process of
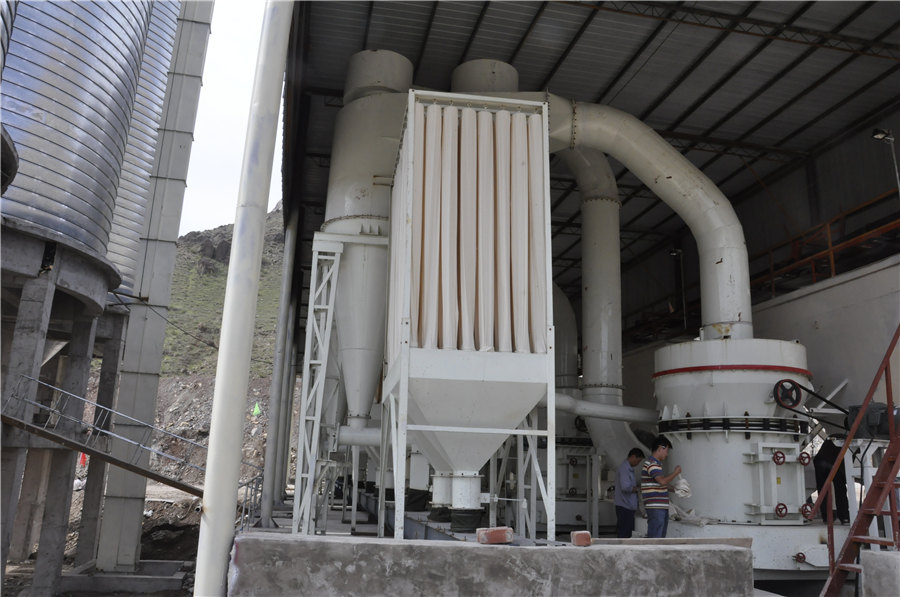
cement grinding Unit
In the cement grinding process, a small amount of admixture is added to eliminate the adhesion and aggregation of the fine powder, accelerate the grinding speed of the material, improve the grinding efficiency, and also increase the content of 330μm by 1020%, which is conducive to the highquality, energysaving and highyield of cement ball millprocess can be divided into the following primary components: raw materials acquisition and handling, kiln feed preparation, pyroprocessing, and finished cement grinding Each of these process components is described briefly below The primary focus of this discussion is on pyroprocessing operations, which116 Portland Cement Manufacturing US Environmental Early hydraulic cements, such as those of James Parker, James Frost and Joseph Aspdin were relatively soft and readily ground by the primitive technology of the day, using flat millstonesThe emergence of Portland cement in the 1840s made grinding considerably more difficult, because the clinker produced by the kiln is often as hard as the millstone materialCement mill Wikipedia2023年10月19日 Therefore, efficient grinding techniques and technologies are employed to minimize energy use and reduce production costs, contributing to the sustainability of the cement industry Types of Clinker Grinding Techniques Clinker Grinding Techniques in Cement
.jpg)
Resistance to Grinding and Cement Paste Performance of Blends
2021年4月19日 Grinding of finished cement is performed in a single stage, intergrinding materials with very different grindabilities This intergrinding process has many different interactions among the different components of the finished cement In a context of developing more sustainable and less energy intensive processes, it is important to understand the 2023年11月28日 Concrete grinding is a crucial process for achieving a smooth and even surface on concrete floors, countertops, or other concrete installations Whether you’re preparing the concrete for a new finish or removing imperfections, follow this stepbystep guide to effectively grind concrete with a concrete grinderHow to Grind Concrete: A StepbyStep Guide to Concrete GrindingEverything you need to know about clinker/cement Grinding if You read and understand this article , you will be ready to be a cement grinding area manager FEED AND FEED SYSTEM Feed Temperature Plants with satellite coolers have high clinker temperatures: eg Cumarebo, Oujda Exit satellite cooler 200250°C Exit grate cooler 100150°CEverything you need to know about clinker/cement GrindingClinker Grinding The cement clinker is ground as finished cement, in a vertical roller mill for cement or in ball mills similar to those normally used for grinding hard raw materials in dry and semidry processes However, the cement clinker is more difficult to grind than raw materials and must also be finer groundAn Introduction to Clinker Grinding and Cement Storage
.jpg)
Cement grinding optimisation ScienceDirect
2004年11月1日 Grinding occurs at the beginning and the end of the cement making process Approximately 15 tonnes of raw materials are required to produce 1 tonne of finished cementThe electrical energy consumed in the cement making process is in order of 110 kWh/tonne and about 30% of which is used for the raw materials preparation and about 40% for the final cement The cement grinding unit manufactured by our company merges drying, grinding, powder classifying, dust collecting and cement packing into a single It can not only grind cement clinker but also process cement admixture, such as gypsum, fly ash, furnace slag, coal gangue, etc, realizing a stable, highquality and automated cement productionCement Grinding Unit Clinker Grinder AGICO Cement6 Cement Production Technology –Cement Grinding –Mechanical Design and Function of Separator Separators –General Classification of Separating Principles •according to flow direction relative to particle track •according to kind of separating field separation by gravitational force separation by centrifugal forceCement Grinding myPolysiusService2024年11月18日 Within the scope of the cement industry, which is characterised by high energy consumption, optimising grinding processes is critical for reducing operational costs and energy usage This paper explores the modernisation of existing cement grinding circuits through the application of Pamir milling technologyOptimising Stirred Milling Technology World Cement
.jpg)
Concrete Grinding: Everything You Need to Know
2023年4月13日 Concrete grinding is a cheap and quick way to even out unlevel concrete slabs, but there's more to know about this concrete repair method What is concrete grinding? Concrete grinding is the process of sanding down 2016年10月5日 In this chapter an introduction of widely applied energyefficient grinding technologies in cement grinding and description of the operating principles of the related equip‐ ments and comparisons over each other in EnergyEfficient Technologies in Cement GrindingPPC is produced by the intergrinding and blending of 65% clinker with 30% fly ash and 5% gypsum to a fineness of 320 m 2 /kg Fineness is a controlled parameter for cement to ensure better hydration and strength development Ground cement is then stored in a waterproof concrete silo for packing More ++Cement Grinding Cement manufacturing process Priya Cement2012年8月30日 Cooling and Final Grinding; Packing Shipping; Cement Manufacturing Process Phase 1: Raw Material Extraction Cement uses raw materials that cover calcium, silicon, iron and aluminum Such raw materials are limestone, clay and sand Limestone is for calcium It is combined with much smaller proportions of sand and clayCement Manufacturing Process Engineering Intro
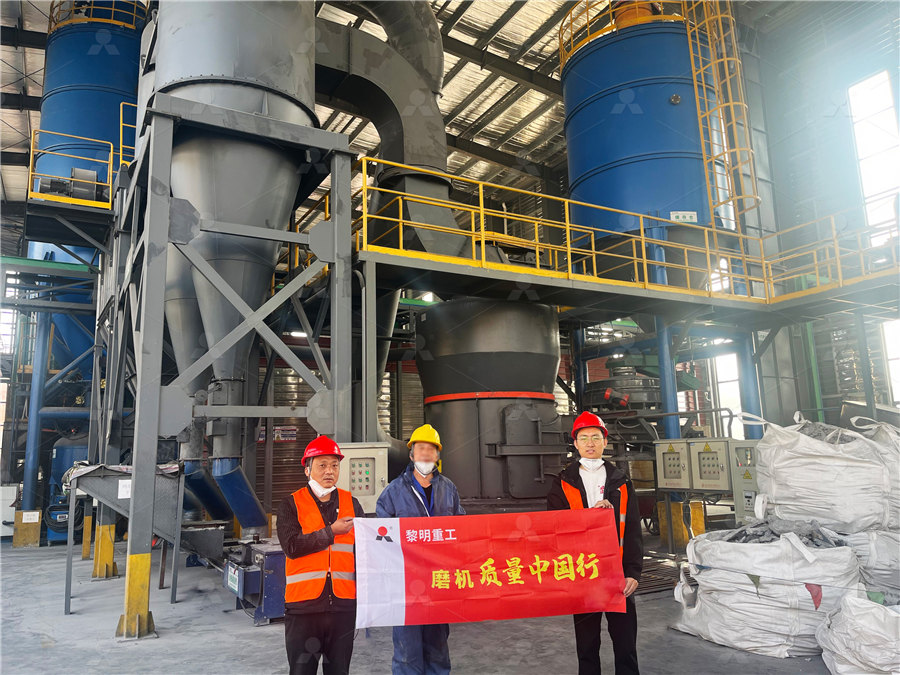
CuttingEdge Grinding Solutions Indian Cement Review
2023年8月21日 ICR looks at the inner workings of grinding mills in the cement industry to understand the technological advancements that are reshaping the landscape against the foreground of sustainability Innovations to enhance the grinding processes are aimed at minimising their environmental footprint while increasing efficiency and performance In 2024年9月10日 Grinding: The cooled Clinker is finely ground with Gypsum and other additives, such as fly ash or slag, in a Cement mill This grinding process produces Cement powder Storage and Packaging: The Cement powder is stored in silos before being packed into bags or delivered in bulk to construction sites for use in various applicationsCement Manufacturing Process: Know Extraction, Processing Cement grinding and packing process The clinker is ground with an amount of gypsum to a fine powder in order to regulate the setting time of cement and to gain the most important property of cement, which is compressive strength To produce different types of cement Cement grinding and packing process Al badia cementGrinding: the material is ground between rollers and grinding table while passing from the center of the table to the nozzle ring The commnation method belongs to the most efficient grinding processes applied in the cement manufacturing Separation: the ground and dried material is lifted up with the drying gasesCement Manufacturing Process
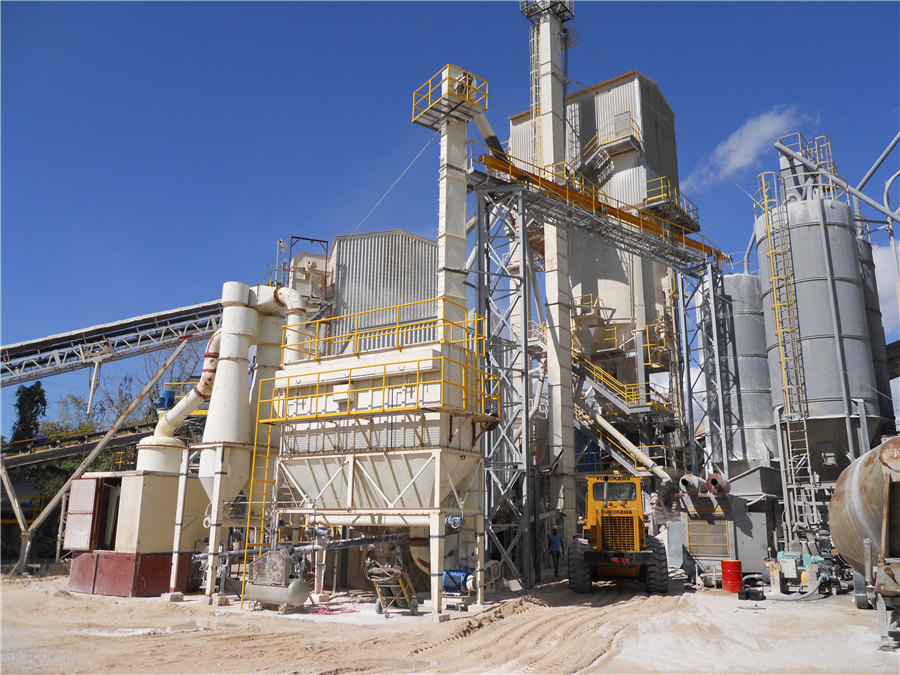
A Comprehensive Guide to the Cement Manufacturing Process
2024年9月5日 The Manufacturing Process of Cement Now, let’s explore the steps involved in the cement production process in more detail: 1 Mining and Crushing The process of making cement begins with mining, where raw materials are extracted from quarries Huge machines called excavators dig the limestone out of the earth2016年10月23日 The principle of Grate Discharge grinding is nearly universally adapted in the cement grinding industry Grate Discharge Ball Mills are the rule rather than 911 Metallurgist is Only close economic study can determine which process should be used CLINKER GRINDING Clinker, the discharge product from the kiln, is partially cooled Cement Grinding 911Metallurgist2017年5月19日 Grinding is an essential operation in cement production given that it permits to obtain fine powder which reacts quickly with water, sets in few hours and hardens over a period of weeks i Overview of cement grinding: fundamentals, 1971年8月17日 116 Portland Cement Manufacturing 1161 Process Description17 Portland cement is a fine powder, gray or white in color, that consists of a mixture of hydraulic cement materials comprising primarily calcium silicates, aluminates and aluminoferrites More than 30 raw materials are known to be used in the manufacture of portland cement, and these116 Portland Cement Manufacturing US EPA

OPTIMIZATION OF CEMENT GRINDING OPERATION IN BALL MILLS
Condition in one of the grinding chambers of the mill Results of Optimization The graphical analysis presented in Figure 2 represents progress of grinding along the length of the mill after optimizing the grinding process rogress of grinding is clearly visible in Desired p the graphs Figure 2: Analysis of longitudinal samplesGas flow, advantage and disadvantage in the Raw mill and Cement mill installations – Grindability concept and the effects of intergrinding materials of different grindability – Ball mill grinding equations and dimensioning – Describe working principles for a separator – Grinding aids and other tools to boost efficiency – Control concepts – Influence of the grinding process on CEMENT GRINDING COURSE The Cement Institute2023年8月21日 Tushar Khandhadia, General Manager – Production, Udaipur Cement Works, discusses the role of grinding in ensuring optimised cement production and a high quality end product How does the grinding process contribute to the production of highquality cement?The quality of cement depends on its reactive properties and particle size grinding helps to reduce Grinding process is a critical stage in cement productionThe cement grinding process is a dynamic system with multiple variables and constraints, and the decisionmaking process is challenging due to the existence of multiple equivalent optimal solutions and the difficulty in finding the global optimal DOUDCGAN: Optimization of cement grinding operational

Energy and cement quality optimization of a cement grinding circuit
2018年7月1日 Among the industries, the nonmetallic industry was reported as the third largest energy user and accounted for about 12% of the global energy use [1]Within this portion, cement industry had the majority of the utilization with 85–12% [1], [2]US Energy Information Administration (EIA) [7] named cement industry as the most energy intensive among the Intensifying the cement grinding process Mas’uda Mukhamedbaeva1, Abdugoffor Khurmamatov1*, and Abduvali Mukhamedbaev2 1Institute of General and Inorganic Chemistry of the Academy of Sciences of the Republic of Uzbekistan, Tashkent, Uzbekistan 2”ANTENNBRANCH” LLC, Tashkent, Uzbekistan Abstract This article deals with the intensification of the Intensifying the cement grinding process e3sconferences2024年10月7日 The course’s first objective is to give an overview of the process chain within the cement industry All the main processes involved during cement production will be discussed, including the extraction and processing of raw materials, the combustion process, cement grinding, quality control and storage, and cement distributionAN INTRODUCTION TO THE CEMENT MANUFACTURINGCement grinding Loading and shipping Quality control and Building on sustainability environmental responsibility HeidelbergCement Headquarters Berliner Strasse 6 69120 Heidelberg Germany Phone: +49 62 21481227 Fax: +49 62 21481217 heidelbergcement How cement is made The finished cement is stored in separate From raw materials to cement