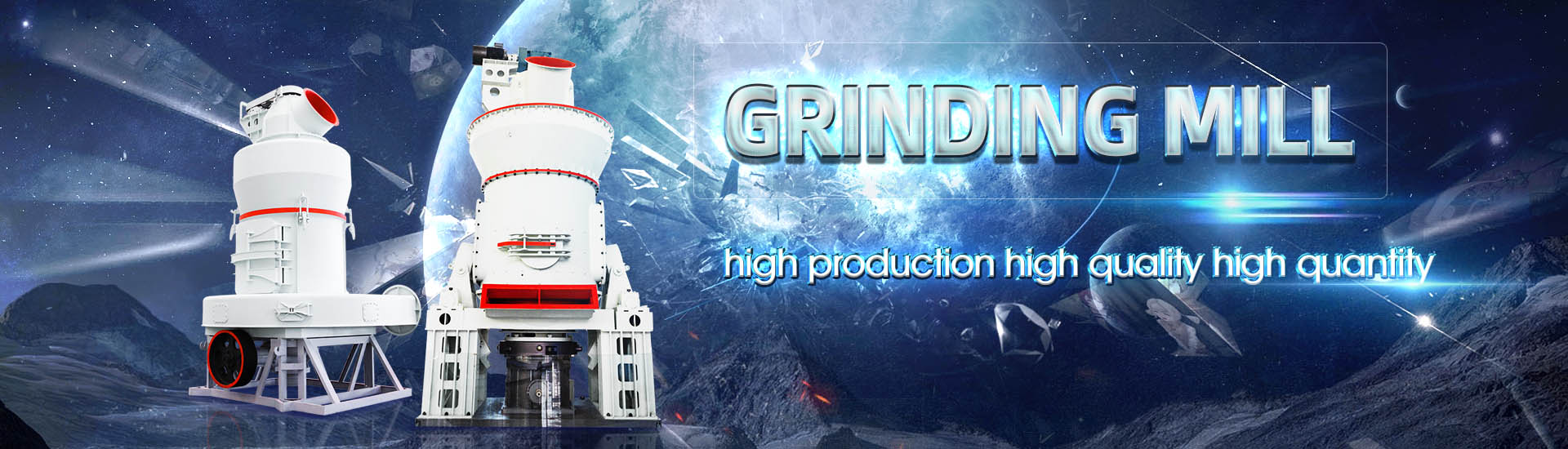
Electrolytic aluminum waste slag mill hydraulic rock mill investment
.jpg)
Research Progress of Electrolytic Aluminum Overhaul Slag Disposal
2023年4月25日 This article analyzes and summarizes the composition and hazards of the overhaul slag and the current development status of domestic and international electrolytic Coal gangue is a byproduct of the production of coalassociated minerals, Review of Research on the Pr2024年5月23日 16 Million metric tons of spent carbon electrodes modify carbonrich solid wastes from aluminum electrolysis are produced annually, threatening ecosystems by cyanide The recycling of carbonrich solid wastes from aluminum 2024年2月1日 The electrolytic aluminum industry generates a large amount lithium (Li)containing electrolytic aluminum slag (EAS) annually, and this can result in severe Efficient lithium recovery from electrolytic aluminum slag via an
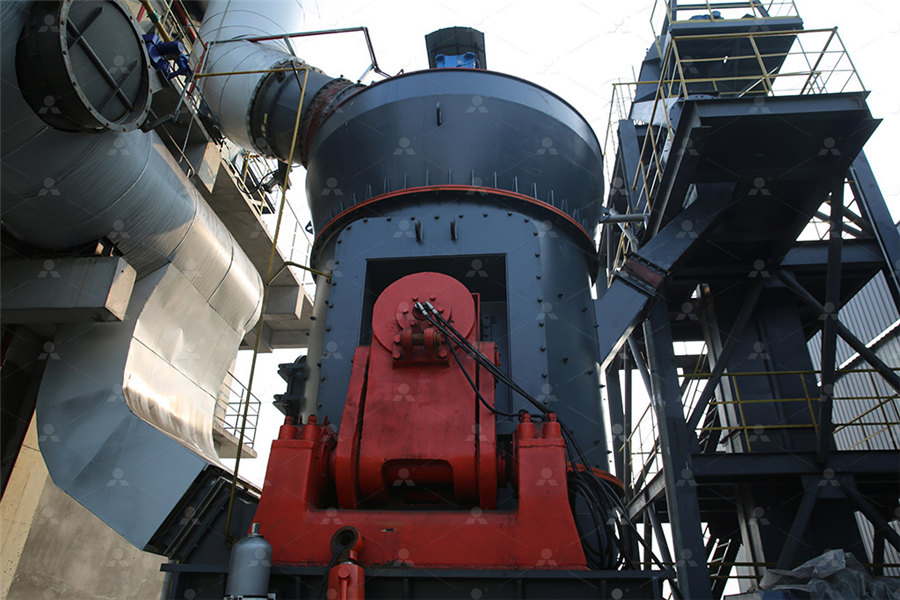
Dissolution behavior of overhaul slag from aluminum reduction
2023年8月1日 The main components of overhaul slag are aluminum and silicon oxides These components could be dissolved in the molten cryolitebased salt system (ie, electrolyte) in the 2020年8月1日 Here, we discuss the influence of different processing parameters on electrolytic refining of aluminum alloy and investigate the mechanism of extracting Al from coarse AlSi Recovery of aluminum from waste aluminum alloy by low 2022年10月9日 In this work, electrolytic aluminum carbon anode slag was separated by flotation Using the selectivity index (SI) as an indicator, the influencing factors of the carbon slag Recovery of carbon and cryolite from spent carbon anode slag of 2023年4月13日 Aluminium is produced by electrolysis using alumina (Al2O3) as raw material and cryolite (Na3AlF6) as electrolyte In this HallHéroult process, the energy consumption is A comprehensive review of aluminium electrolysis and the waste
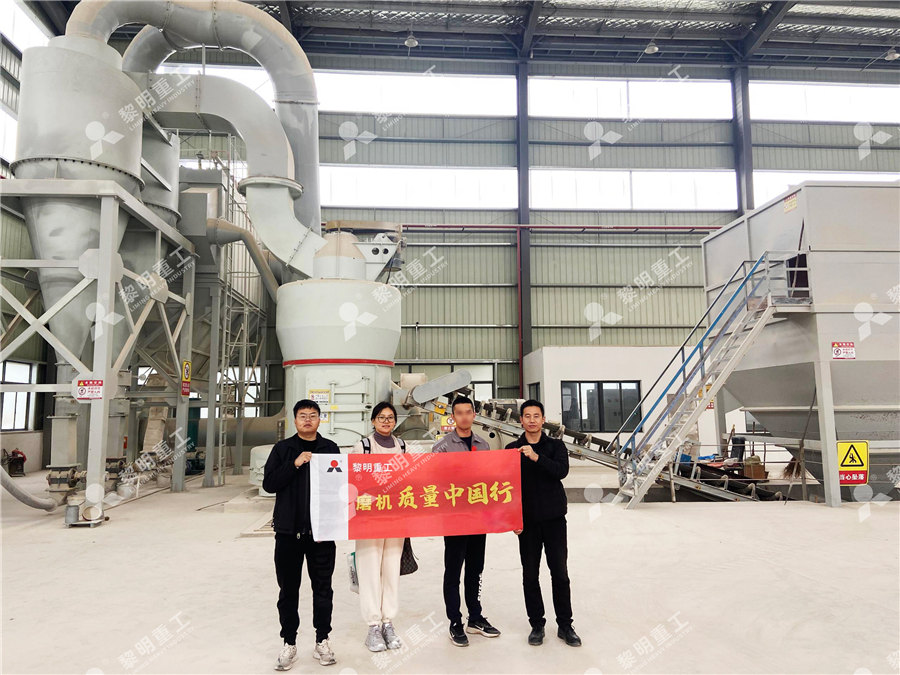
A solidstate electrolysis process for upcycling aluminium scrap
2022年4月13日 Here we propose a solidstate electrolysis (SSE) process using molten salts for upcycling aluminium scrap The SSE produces aluminium with a purity comparable to that of Aluminum ash is a kind of industrial solid waste Original aluminum ash (OAA) can be prepared into original aluminum ash spray powder (OAASP) through hydrolysis treatment, and the Recycling and Utilization of the Electrolytic Aluminium Ash and SlagWith the rapid development of aluminium smelting industry in China, millions of tons of hazardous wastes such as carbon slag, overhaul slag and aluminum ash are generated every yearPresent situation of production, utilization and disposal of This study collected electrolytic aluminum waste cathodes, anodes, limestone and other materials After grinding the materials with an electric mill, 50 grams of electrolytic aluminum waste samples were sieved to 0075 mm The sample was then dried for 2 hours at a temperature of 110 °C in the dryer, then stored in aResearch on the Coprocessing of Mixed Electrolytic Aluminum Waste
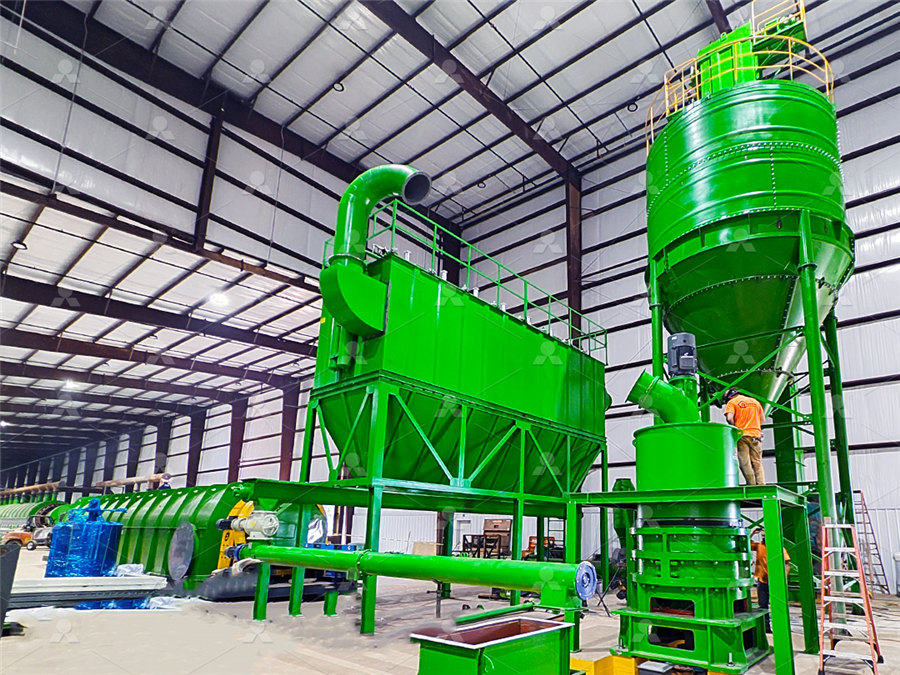
Slag grinding mill micro powder production line
2022年5月12日 Insulation and decorative materials Glassceramic production equipment has less investment and lower cost than cast stone and ceramics It is a promising material (2) Road base or cushion The slag is crushed to form 2021年10月1日 Currently, the HallHeroult method is adopted for industrial aluminum smelting, with alumina as the raw material and cryolite as the solvent (Tarcy et al, 2011)According to statistics, China's primary aluminum output was 3708 million tons in 2020, of which the capacity of using domestic bauxite to produce alumina accounts for approximately 47% (National A novel approach for lithium recovery from waste lithium 2022年2月19日 Recycling waste containing rare earth has always been a research hotspot The molten salt electrolysis process of rareearth metals and alloys generates a large amount of waste slag, which contains high rareearth content and, thus, has very considerable recovery value However, the high content of fluorine in rareearth molten salt slag brings challenges to the Recovery of RareEarth Elements from Molten Salt Electrolytic Slag 2022年10月10日 The comprehensive recovery and utilization of electrolytic aluminum spent carbon anode slag (Hereinafter simplified as “carbon anode slag”) are therefore necessary Flotation is a physical separation method used to separate particles by using the difference in surface property of particles ( Chen et al, 2022 ; Ni et al, 2022 )Recovery of carbon and cryolite from spent carbon anode slag of
.jpg)
What is Blast Furnace Slag and How to Process It?
2022年2月26日 Blast furnace slag can be processed into the following materials by various processes In China, blast furnace slag is usually processed into water slag, slag gravel, expanded slag and slag beadsWater slag is the process of putting the hotmelt blast furnace slag into water for rapid cooling, which mainly includes slag pool water quenching or furnace front 2021年12月1日 Abtract Aluminum slag waste generated from the smelting process of bauxite was used to prepare roof tiles samples Clay was substituted by slag waste in percentages reaching 40% in the basic mix The use of aluminum slag waste in the preparation of roof tiles2022年12月12日 Based on the research on bulk solid waste contact molding technology by our team [49], the comprehensive performance of pressed bricks with different ratios of aluminum ash and calcium carbide slag was investigated, the ratios of aluminum ash and calcium carbide slag are 9:1 ∼ 1:9 and pure aluminum ash and calcium carbide slag, the pressing pressure is 300 Comprehensive performance study of aluminum ash and calcium 2023年3月12日 Recovery of Carbon and Cryolite from Spent Carbon Anode Slag Using a Grinding Flotation Process Based on Mineralogical Characteristics(PDF) Recovery of Carbon and Cryolite from Spent Carbon Anode Slag
.jpg)
Sustainable Approaches for LD Slag Waste Management in Steel
2016年5月16日 Reduce, reuse, and recycle are important techniques for waste management These become significant for improving environmental and economic condition of industries Integrated steel industries are generating huge amounts of steel slag as waste through the blast furnace and Linz–Donawitz (LD) process Presently, these wastes are disposed by dumping in 2023年1月10日 Advantages of Slag Vertical Roller Mill 1 Costeffective, less comprehensive investment Large functions are integrated in one, occupying an area of about 50% of the ball mill system, and can be arranged in the open air, greatly reducing investment costs; the system design is simple and reasonable, saving the total investment in equipment Slag Vertical Roller Mill2021年11月22日 The secondary aluminum ash of electrolytic aluminum is a hazardous waste containing a large amount of toxic and hazardous substances such as fluoride, cyanide, aluminum carbide dies, and aluminum nitride, and The Utilization Technology Analysis Of Secondary 2020年8月1日 Many researchers have studied the refining of aluminum by low temperature aluminium bath system Ali and Yassen (2018) used a different type of dissolvent to recover aluminum from industrial wastes This method was capable of obtaining aluminum of 99% purity by electrorefining of impure aluminum through the use of anhydrous AlCl 3 and NaCl as ionic Recovery of aluminum from waste aluminum alloy by low
.jpg)
Formation mechanism and treatment status of perfluorocarbon in
2024年4月1日 As a high energy consumption and high carbon emission industry, aluminum electrolysis is the global carbon reduction key concern industry From a global perspective, the global carbon emission of aluminum electrolysis in 2022 is more than 1 billion tons, accounting for about 46% of the total global carbon emission [9], [10]In the entire process of electrolytic 2018年12月14日 The studies of fractional, chemical and phase compositions of aluminumcontaining slags of different origin found that slags are multicomponent systems consisting of metal and nonmetal partsTHE USE OF ALUMINUM SLAG RECYCLING PRODUCTS IN INVESTMENT CASTING 2024年2月1日 Aluminum metal was produced using the cryolitealumina molten salt electrolysis method (Ishak et al, 2017) A large amount electrolytic aluminum slag (EAS) is generated during the electrolysis process, as the falling of carbon particles on the anode into the electrolysis cells and the accumulation of lithium fluorine result in energy consumption and electrolyte scrapping Efficient lithium recovery from electrolytic aluminum slag via an 2019年7月8日 In order to recover the waste heat of aluminum dross and carbon resource in carbon residue, the waste heat recovery process of aluminum dross by coupling of physical and chemical method was proposedThermodynamic analysis of waste heat recovery of aluminum
CFB石灰石脱硫剂制备96.jpg)
Utilisation of lead–zinc mill tailings and slag as paste backfill
2020年8月14日 Paste backfilling is an incipient underground mine backfill technology in India It facilitates maximum use of mill tailings with enhanced stability of the underground workings and minimises rehandling of water, as well as provides bulk disposal of mining solid waste Binder type and dosage plays an important role in paste backfill performance This paper highlights Materials 2024, 17, 1431 3 of 16 the preparation of geopolymers Sodium hydroxide (NaOH) particles were purchased from Sinopharm Reagent (Shanghai, China), and sodium silicate (Na2SiO3) powder with a modulus of 314 was purchased from Synthesis of Electrolytic Manganese Slag Solid WasteBased FORT WAYNE, Ind, July 19, 2022 — Steel Dynamics, Inc (NASDAQ/GS: STLD) today announced that its Board of Directors has authorized the company to construct and operate a 650,000tonne lowcarbon, recycled aluminum flat rolled mill, with two supporting satellite recycled aluminum slab centers The capital investment is estimated to be $22 billion for the three Steel Dynamics Announces Investment in New StateoftheArt 2023年10月1日 Cryolitealumina (Na 3 AlF 6Al 2 O 3) molten salt electrolysis is the only modern method for the industrial production of metallic aluminum (Ishak et al, 2017)Under the influence of direct current, Al 2 O 3 dissolved in the molten salt is reduced to monolithic aluminum at the cathode (Haraldsson and Johansson, 2020)As the blood of the electrolytic cell, the electrolyte Efficient extraction and recovery of lithium from waste aluminum

Sustainable Recovery of Fluorine from Waste Aluminum
2023年8月2日 The highvalue, green and harmless purification of aluminum electrolysis comprehensive solid waste can not only reduce its harm to the environment and soil but also separate and recover the highvalue rare elements This study aims to develop a process for recovering and treating waste aluminum electrolytes by sulfuric acid roasting The results of On August 2nd, China Nonferrous Metals Industry Association organized an expert meeting on scientific and technological achievements in Kunming, Yunnan Province, and completed the “electrolytic aluminum overhaul slag” jointly Electrolytic aluminum overhaul slag harmless 2017年3月5日 Normalized CaO (MgO)SiO 2 (Na 2 O,K 2 O)Al 2 O 3 (Fe 2 O 3 ) phase diagram for various types of iron and steel slags Acronyms: blast furnace slag (BFS); basic oxygen furnace slag (BOFS (PDF) Iron and Steel Slags ResearchGate2023年8月1日 The overhaul slag from the aluminum reduction cell is a hazardous waste The annual production of overhaul slag is above one million tons in China [1]The overhaul slag mainly consists of spent impervious materials and refractory bricks [2], [3]A large number of hazardous substances, such as fluorides and cyanides, are included in the overhaul slag [4]Dissolution behavior of overhaul slag from aluminum reduction
.jpg)
Here's what No One tells you about Comprehensive Utilization
2021年2月8日 The aluminum dross skimming from the smelting furnace is called primary aluminum dross, which is graywhite in appearance, mainly composed of a mixture of metallic aluminum and aluminum oxide, and the aluminum content can reach 15%~ 70%, also known as “white aluminum dross”; secondary aluminum dross is the waste after the primary aluminum 2019年9月30日 Electrolytic manganese residue (EMR), red mud (RM) and carbide slag (CS) are three kinds of solid waste which are largely produced and difficult to recycle EMR is a potentially harmful industrial solid waste, its major hazardous substances are heavy metals and ammonia nitrogen, which are harmful to the environment [1] Synergic effects of electrolytic manganese residuered mudcarbide slag The electrolytic aluminum multifunctional crane is the key process equipment for the production of largescale prebaked anode electrolytic aluminum The crane can work in the environment containing HF corrosive gas, alumina powder, fluoride salt, carbon dust powder, asphalt smoke, high molten salt, and strong magnetic fieldElectrolytic Aluminum Multifunctional Crane2024年6月1日 REEs recovery from molten salt electrolytic slag: Therefore, they suggested to fully recover REEs, F and Li by roasting the slag with aluminum sulfate and calcium oxide, as followed by Fig 11 and Eqs (16–18) 69, 70 recovery of waste sulfur slag, 71, 72 recovery of aluminum electrolytic waste residue, 73, 74, 75 etc REEs recovery from molten salt electrolytic slag: Challenges and
.jpg)
电解铝大修渣处置研究进展
2023年4月25日 Research Progress of Electrolytic Aluminum Overhaul Slag Disposal[J] Multipurpose Utilization of Mineral Resources, 2023, 44(2): 159168 doi: 103969/jissn10006532202302025 Citation: Dong Liangmin, Jiao Fen, Liu Wei, Jiang Shanqin, Wang Huanlong As the main solid waste of the electrolytic aluminum industry, 2024年3月21日 manganese slag–solid wastebased geopolymer (SWGP) was evaluated by analyzing the mineral phase, morphology , and leaching concentration of the geopolymer 2Synthesis of Electrolytic Manganese Slag–Solid WasteBased 2024年6月29日 Aluminum electrolyte is a necessity for aluminum reduction cells; however, its stock is rising every year due to several factors, resulting in the accumulation of solid waste Currently, it has become a favorable material for the resources of lithium, potassium, and fluoride In this study, the calcification roasting–twostage leaching process was introduced to extract Stepwise extraction of lithium and potassium and recovery of During a longterm operation of the aluminum electrolysis cell, the molten salts continuously infiltrate and corrode the pot lining, resulting in a huge amount of hazardous waste after the overhaulElectrolytic cell spent lining Fig 2 Overhaul slags of
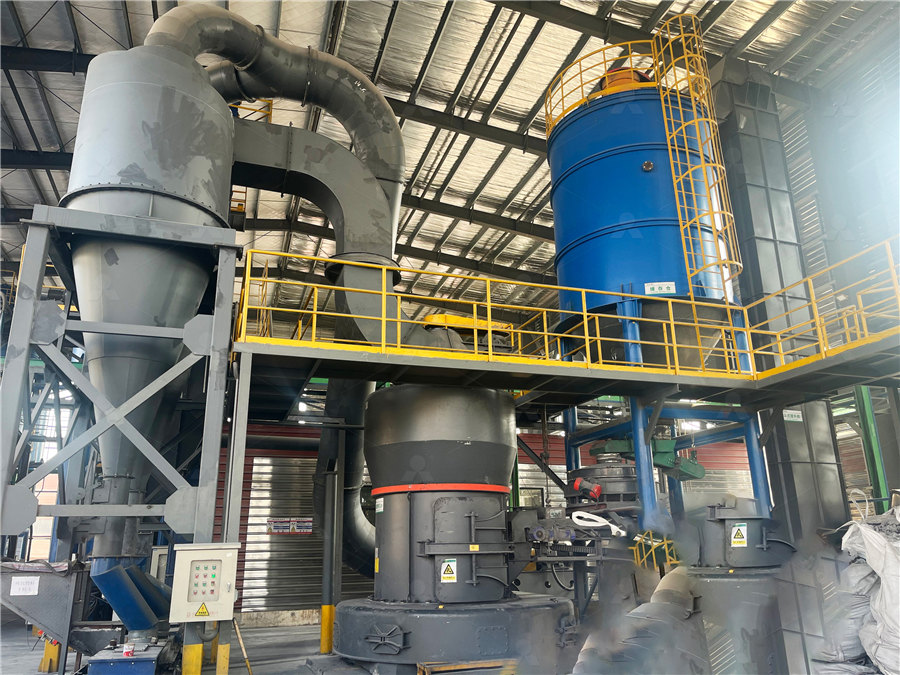
Preparation of electrolytic manganese residue–ground
2013年6月1日 In this research, the electrolytic manganese residue (EMR) based beliteye'elimiteferrite (EBYF) clinker composed of 516 % belite, 256 % iron phase, 158 % ye'elimite and 65 % overburned 2024年2月21日 The electrolytic slag is sent to the jaw crusher and broken into small pieces 2 Grinding The crushed small pieces are sent to the cryolite mill and ground into powder 3 Stir The powdery electrolytic slag is fed into the mixer and stirred evenly 4 FlotationAluminum slag recycled cryolite powder production line2024年2月1日 Efficient lithium recovery from electrolytic aluminum slag via an environmentally friendly process: Leaching behavior and mechanismEfficient lithium recovery from electrolytic aluminum slag via an 2023年12月1日 However, the amount of solid waste generated in electrolysis process continues to accumulate due to the confinements of the process With the growth of solid waste emissions, environmental and ecological issues have ended up one of the major bottlenecks limiting the sustainable development of aluminum enterprises (Liao et al, 2018; Ishak et al, 2017)Harmless recovery and utilization of electrolytic aluminum spent
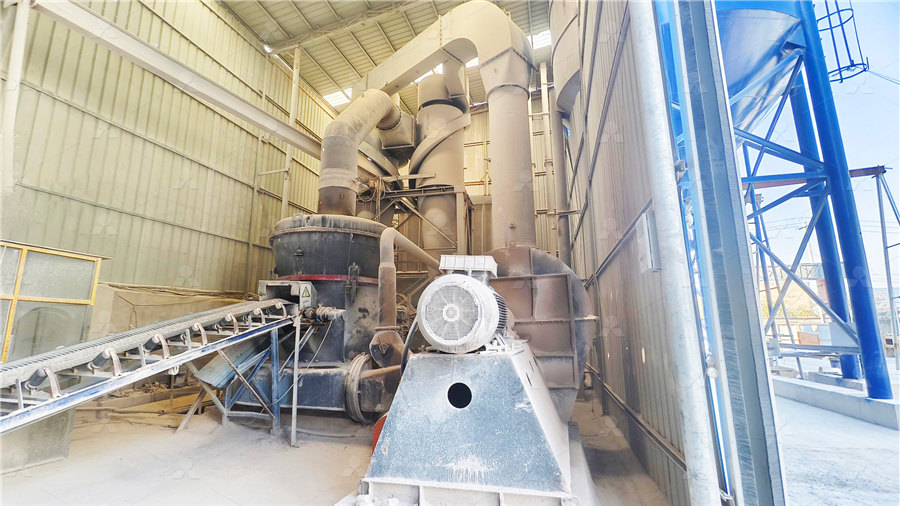
The Utilization Technology Analysis Of Secondary Aluminum Ash
2021年10月27日 The secondary aluminum ash of electrolytic aluminum is a hazardous waste containing a large amount of toxic and hazardous substances such as fluoride, cyanide, aluminum carbide dies, and aluminum nitride, and its treatment has always been a research focus in the electrolytic aluminum industry The traditional landfill and storage methods have been bannedBefesa is currently the European leader in aluminum waste and salt slag recycling plant in the United Kingdom is now a fully operating waste treatment plant for the waste generated from used primary aluminum electrolytic cells (Liberia) Despite the difficulties stemming from the widespread slump in investment, Aluminum Waste Recycling by BEFESA Environmental XPRTa Loesche mill, with a grinding track diameter of only 11 metres, was used as long ago as 1935 However, the breakthrough in grinding this type of material on the vertical roller mill did not take place until the beginning of the 1990’s 1935 The first Loesche mill for grinding cement clinker, an LM 11, was commissioned in Joao Pessao, Brazil2 µm 5 µm Loesche