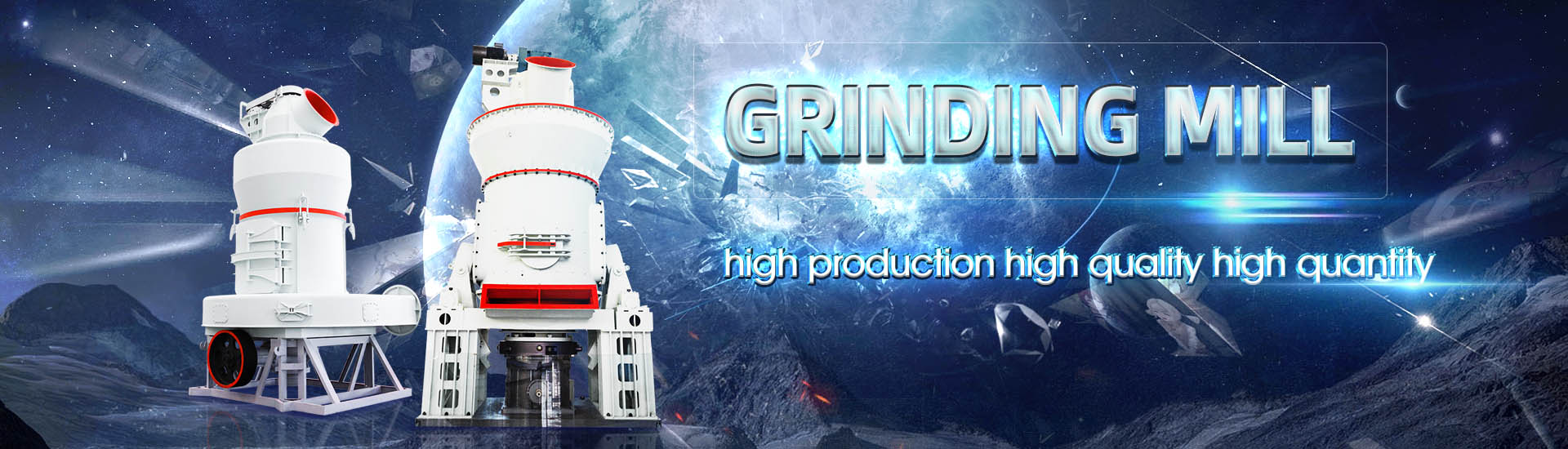
Maoming coal steam pipe processing
.jpg)
Characteristics and kinetics of Maoming oil shale pyrolysis in the
This paper presents an effective numerical simulation method for production prediction of in situ recovery of oil shale reservoirs with steam injection In this method, finite volumebased 2023年4月1日 In this paper, the kinetic analysis and pyrolysis evolution in the transition zone of metal salt catalyzed steam injection insitu Maoming oil shale upgrading were demonstrated Study on the kinetic analysis and pyrolysis evolution in transition 13characteristics and the pyrolysis kinetic of Maoming oil shale heated by transition metal 14salt (CoCl2) assisted steam The experimental results show that compared with 15conventional shale heated by transition metal salt assisted steam2015年7月1日 This approach typically includes the following steps: (1) characterization of feed coal properties to establish particle distributions for size, density, and floatability, (2) simulation A review of stateoftheart processing operations in coal
.jpg)
Current Status and Energy Analysis of Oil Shale’s Retorting Process
2021年2月12日 There are three main ways in which this process provides dry distillation energy to the underground: first, by burning part of the bottom oil shale or semicoke to generate heat 2023年4月1日 We conduct numerical simulations of kerogen pyrolysis by the in situ upgrading process of Steamfrac, which entails the steam or hotwater injection into multistage transverse Characteristics and kinetics of Maoming oil shale pyrolysis in the 2014年11月7日 A novel process of integrated coal pyrolysis with steam reforming of methane (CPSRM) was put forward for improving the tar yield Two Chinese lignites were used to Integrated Process of Coal Pyrolysis with Steam Reforming of 2021年1月3日 This paper proposes a novel operational technique to produce electricity efficiently and environmentally at very low main steam (MS) and hot reheat (HRH) temperature Performance improvement of 500 MW coal power plant at low
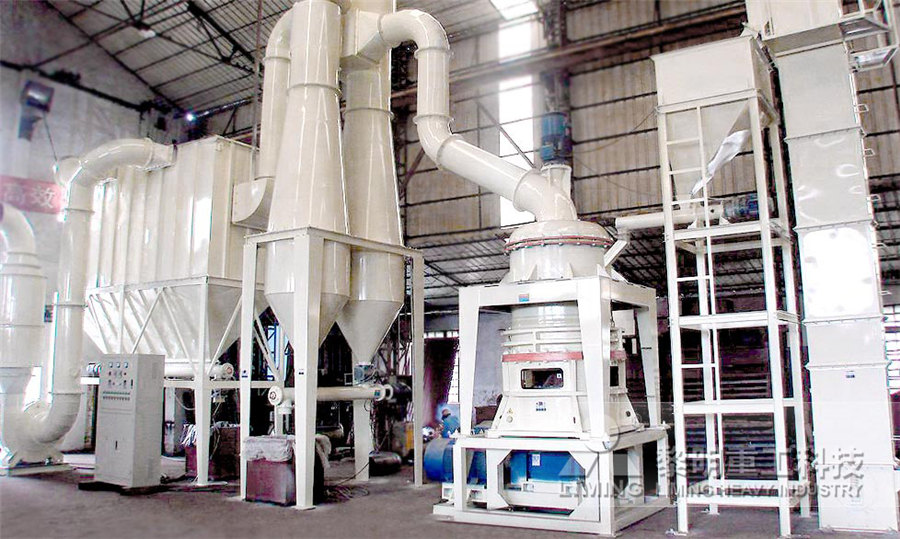
Failure Analysis of Abnormal Bulging and Cracking for High
2022年3月21日 To study the dominant influence factor, the bulging and cracking highpressure steam pipes were investigated with a macro visual inspection, chemical composition analysis, There are 4 crucial steam lines in coalfired power plant: main steam, hot reheat, cold reheat, and feed water piping systems These pipelines are manufactured to ASME B311 ASME BPVC Steam Lines of CoalFired Power Plant and Material SelectionCoalfired power generation plants are most commonly based on pulverised coal combustion (PCC) systems, in which heat from combustion of the coal is used to raise high pressure superheated steam that drives a steam turbine generator Steam turbine plants have been in use for over a hundred years, and have reached supercritical conditions withUnderstanding coalfired power plant cycles ICSC2012年2月11日 The hightemperature components within conventional supercritical coalfired power plants are manufactured from ferritic/martensitic steels To reduce greenhousegas emissions, the efficiency of pulverized coal steam power plants must be increased to as high a temperature and pressure as feasible The proposed steam temperature in the DOE/NETL Processing of Advanced Cast Alloys for AUSC Steam Turbine
.jpg)
Environmental, Health and Safety Guidelines for Coal Processing
COAL PROCESSING APRIL 30, 2007 1 WORLD BANK GROUP Environmental, Health and Safety Guidelines for Coal Processing Introduction such as host country context, assimil The Environmental, Health, and Safety (EHS) Guidelines are technical reference documents with general and industry specific examples of Good International Industry Practice (GIIP)Revolution led to the largescale use of coal, as the steam engine took over from the water wheel as the prime mover in industrial plants Coal is primarily used as a solid fuel to produce electricity and heat through combustion World coal consumption is about 62 billion tons annually, of which about 75% is used for the production of electricityCoal Fired Steam Plants PDHonline2016年12月31日 Kapranos and Priestner [50] reviewed the most common materials used in heat exchangers, summarised as aluminium, coppernickel, stainless steel, and titanium alloysSelection and Analysis of Material for Boiler Pipes in a Steam There are 4 crucial steam lines in coalfired power plant: main steam, hot reheat, cold reheat, and feed water piping systems The welding of ASTM A335 P91 seamless pipes for a main steam line, in a power plant, Peru Power Unit: Main Steam: Hot Reheat: Cold Reheat: Feed Water: MW: T/°C: P/MPa: 200: 540: 137: ASTM A335 P22 OD3555 x 50:Steam Lines of CoalFired Power Plant and Material Selection
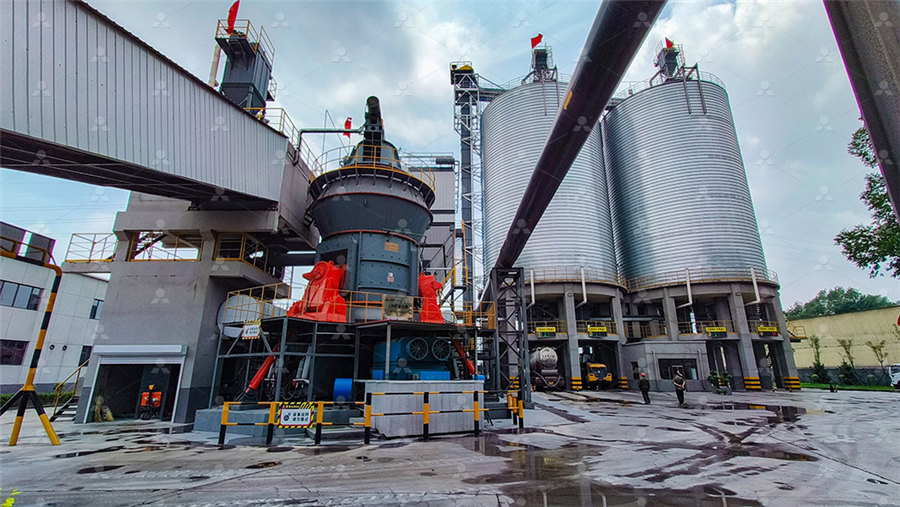
Failure Analysis of Abnormal Bulging and Cracking for High
2022年3月21日 Highpressure steam pipes inevitably suffered from reciprocal interaction of high pressure and temperature during longperiod service, causing deformation and cracking To study the dominant influence factor, the bulging and cracking highpressure steam pipes were investigated with a macro visual inspection, chemical composition analysis, metallographic thermal coal (coal finely ground to generate steam), therefore this document will specifically describe the process of subsurface coal extraction and thermal coal processing Purpose Coal is used for its potential heat energy when burned and since the 1880s has been widely used to generate electricity in power plantsCOAL EXTRACTION AND PROCESSING WordPressManaging a CoalFired Firetube Boiler Workshop PD V al id t on Number : SAIMechE 05 16 2/ 4 Sparge pipe; Soot blower steam supply pipes; Thermal insulation Major Components ID fan; FD fan; Stoker; Grit collector; Feed pumps; Control panel Valves and Fittings14 Managing A Coalfired Firetube Boiler 年10月1日 The coal mining wastes and coal processing byproducts can pollute water in several ways, directly and indirectly In coal mining and processing, a large amount of water is required for suppress dusting, equipment washing and, of course, coal washing [4]Eliminating environmental impact of coal mining wastes and coal
.jpg)
SteamCoal Gasification an overview ScienceDirect Topics
2012年2月2日 Coal steamgasification model in chemical regime to produce hydrogen in a gas–solid moving bed reactor using nuclear heat A Belghit, S El Issami, in International Journal of Hydrogen Energy, 2009 Belghit and Issami (2001) [14] developed a coal steamgasification in the mass transfer regime model in steady state in a moving bed reactor with 2023年4月1日 Location and attribution of functional groups for 700900 cm −1 of Maoming oil shale and semicokes after steam heating to 350, 450, and 550 °C Peak Position, cm −1 Assignment OS 350 °C 450 °C 550 °C; Peak area Percentage, % Peak area A review of the effects of minerals in processing of Australian oil shales Fuel, 73 Study on the kinetic analysis and pyrolysis evolution in transition We developed a healthmonitoring methodology for hightemperature steam pipes that estimated the life prediction of creep–fatigue interaction by directly measuring the displacement of hot parts Three different methods (boiler code, design HealthMonitoring Methodology for High PO Box 4246900100 Nairobi, Kenya +254 700 / +254 735 info@desbroeng Industrial Area, Kampala Road, Nairobi, KenyaProcess/Steam Piping Desbro Engineering

Syngas production by gasification processes ScienceDirect
2023年1月1日 Syngas can be produced by different methods such as gasification of coal, biomass, or waste; steam reforming of natural gas; They can cause a lot of problems such as clogging pipes, It has short processing times, fuel without may specifications, and good thermal performance; however, it produces high content of tars and oils 2015年1月1日 5122 Determination of Active Sites Various methods have been used to study active sites Laine et al [] used the amount of O 2 adsorbed at low temperature to evaluate the number of active sites in the reactionFreund et al [14, 15] used the instantaneous switching reaction gas approach to interrupt the reaction at a given conversion rate, and used the Coal Gasification SpringerLink2004年8月1日 Download Citation Materials technology for coalfired power plants Maintaining coal as an energy source option poses some challenges Among these, the development of ultrasupercritical, high Materials technology for coalfired power plants ResearchGateIn surface mining, the ground covering the coal seam (the overburden) is first removed to expose the coal seam for extraction The elements of a surface mining operation are (1) topsoil removal and storage for later use, (2) drilling and blasting the strata overlying the coal seam, (3) loading and transporting this fragmented overburden material (called spoil), (4) drilling and blasting the Coal Mining and Processing Methods The National Academies
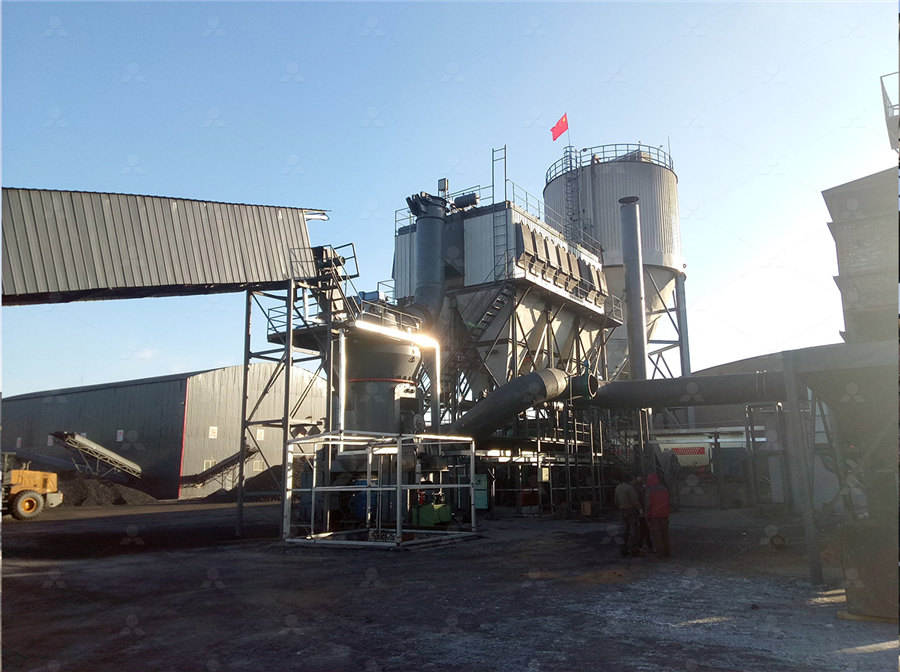
Introduction to Industrial Boilers and Steam Generation Systems
Fundamentally, distillation columns separate fluids into fractions, with lighter fractions moving upwards and heavier fractions at the bottom The bottoms are heated in a reboiler to recover additional lighter fractions for further processing Steam is a common heat source for the reboiler A kettle reboiler is shown in Figure 414COAL PROCESSING APRIL 30, 2007 1 WORLD BANK GROUP Environmental, Health and Safety Guidelines for Coal Processing Introduction such as host country context, assimil The Environmental, Health, and Safety (EHS) Guidelines are technical reference documents with general and industry specific examples of Good International Industry Practice (GIIP)Environmental, Health and Safety Guidelines for Coal Processing2020年7月1日 Improving the energy efficiency of power plants by increasing steam operating temperature up to 700 °C can be achieved using novel engineering design concepts such as coated steam pipe systemsOptimisation and thermomechanical analysis of a coated steam dual pipe A steam boiler is a pressurized vessel that transfers heat to water to lowpressure propane, No 2 oil, coal and other fuels Tubes: In watertube boilers, the metal tubes situated inside the boiler including hospitals, university Steam Boilers 101 — The Definitive Guide to Steam
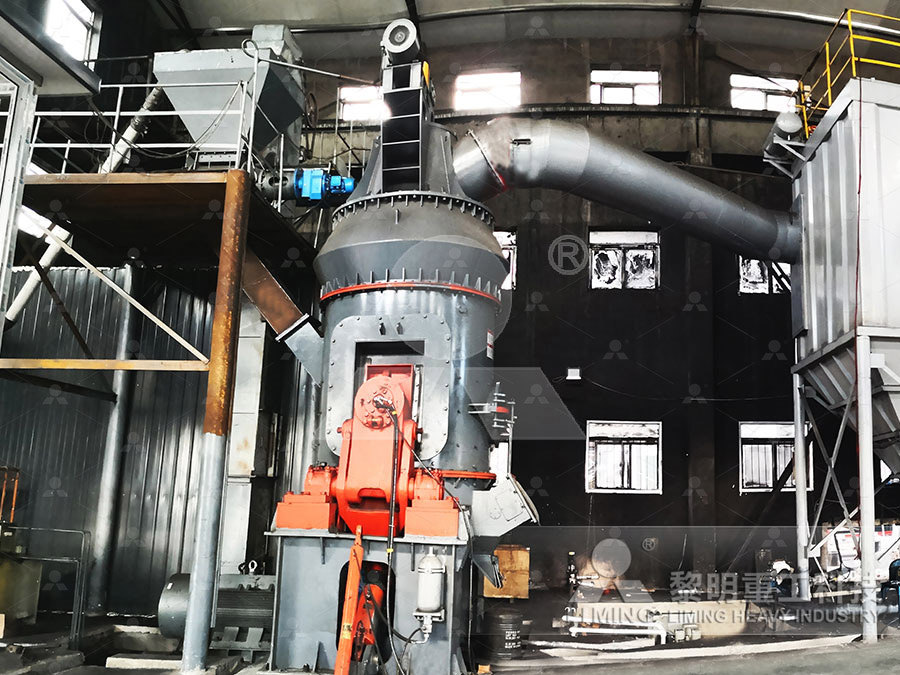
HIGH PRESSURE STEAM PIPES OF A PALM OIL PROCESSING PLANT
Steel pipes are commonly used for transporting high pressure steam from a steam generating unit or boiler to a steam turbine or other processing unit This paper presents a metallurgical examination performed on HP steam pipes of a newly constructed plant for transporting high pressure steam from a boiler to a palm oil processing plant The aim was to assure that the Basic oil processing produces only petroleum gas 0170: Coal liquefaction now produces 90 heavy oil, 20 light oil and 10 petroleum gas, consuming 25 heavy oil, 10 coal and 50 steam 0150: Added coal liquefaction oil processing recipe 091: Added heavy oil cracking and light oil cracking 090: Introduced Basic oil processingOil processing Factorio Wiki2019年7月3日 Around the same time, James Young built a coaloil refinery in Whitburn, Scotland Table 81 summarizes the significant events in petroleum processing from 1860 to 2000 Table 81 Significant events in petroleum refining 1861–2000 Power and SteamPetroleum Processing and Refineries SpringerLink2020年4月2日 Steam boiler belongs to the principal energy sources Its objective is the production of steam for the energy purposes Because of gradual improvements its optimisation potential was almost exhaustedAnalysis of the Coal Milling Operations to the Boiler Parameters
.jpg)
Coal blending and process redesign for a steam generation plant
known as silos, first This is done to draw coal from it if there should be a breakdown underground, or to offload coal just mined if there is a belt malfunction The belt also goes through a bunker which is 194 km away from the silos A bunker is a form of a shoot which stores coal and release it constantly to the conveyor belt before2024年3月1日 Use of hydrogen to mitigate the GHG emission has become a popular alternative to be used as primary fuel for power generation and transportation [14], [15], [16]Hydrogen can also supplement renewable technologies by providing energy during their downtime [17]Although hydrogen is the most abundant element in the universe it is not readily available in pure form Fuel reforming processes for hydrogen production2020年12月27日 2 Environmental, Health, and Safety Guidelines COAL PROCESSING APRIL 30, 2007 2 WORLD BANK GROUP 10 IndustrySpecific Impacts and Management The following section provides a summary of EHS issues associated with coal processing, along with recommendations for their management Recommendations for the management of EHS Coal processing PDF SlideShare2013年12月1日 Steam turbine with a large capacity, operated at high temperature and high pressure Security so the process must be maintained so as not to pose a hazard with a high riskRisk Management and Hazard and Operability Study on Steam
.jpg)
Good practice for industrial coalfired boilers
combustion air supply Coal combustion can be separated into three categories: grate firing, fluidised bed firing and suspension firing The majority of smaller boiler units are stoker or grate fired (Payne and others, 1996) Industrial or utility boilers are designed to burn fuel to produce steam The steam can be used for electricityWhat is the typical pipe material for steam systems? Pipes for steam systems are commonly manufactured from carbon steel to ASME B 169 A106 The same material may be used for condensate lines, although copper tubing is preferred in some industriesPipes and Pipe Sizing Spirax Sarco2009年1月1日 This book details advances in the production of steam and the utilization of all types of fuels Section 1 covers Steam Fundamentals including thermodynamics, fluid mechanics, heat transfer CFD Modeling of MPS Coal Mill for Improved 2023年4月15日 In this work, a series of experiments on pyrolysis of Maoming oil shale were conducted in a custombuilt reactor, in order to investigate the pyrolysis characteristics and the pyrolysis kinetic of Maoming oil shale heated by CoCl 2 assisted steam The experimental results show that compared with conventional and steam heating, the combined physical and Characteristics and kinetics of Maoming oil shale pyrolysis in the
.jpg)
Technology of Producing Petroleum Coking Additives to Replace Coking Coal
2021年12月8日 Coke chemical companies often have a deficit of coals of particularly valuable grades, the coking coals This work studies the opportunity of producing petroleum coking additives using delayed coking during heavy petroleum residue processing Experiments for the production of a carbon material were conducted using three kinds of heavy petroleum residues at given steam conditions, while the maximum allowing capacity is 647MW The high pressure steam (161 MPa) at a temperature of 535ºC, is piped through high pressure steam pipes to the HP turbine The high pressure steam arrives from the boiler in pipes wrapped in thick insulation to prevent thermal energy lossesHOW ELECTRICITY IS PRODUCED AT A COALFIRED POWER 2021年5月11日 The modernday coal processing plants can be categorized into four different circuits, depending upon the size of the coal particles to be treated: (a) coarse coal processing circuit treating particles coarser than 10 mm, (b) small coal circuit for washing particles in the size range of 110 mm, (c) fine coal circuit for cleaning particles in size range of 015–1 mm, and Mineral Beneficiation and Processing of Coal SpringerLink2008年10月17日 These coal fines are disposed and left on either stock piles and slurry ponds near mining sites or added in steam coal regardless of the fact that they constitute a high potential source of energy Cleaner Production in the South African Coal Mining and Processing
43.jpg)
Service systems Dairy Processing Handbook
Stainless steel is used for pipes with a diameter of 25" (65 mm) or larger, galvanized steel is used for smaller pipes The system includes Steam at a temperature of 140 – 150 °C is frequently used as a The boiler is usually fuelled with oil, coal or gas Thermal energy is released by the burning fuel and absorbed by the Maoming FAN, Senior Process Engineer Cited by 1,609 Read 57 publications Contact Maoming FANMaoming FAN Senior Process Engineer ResearchGate