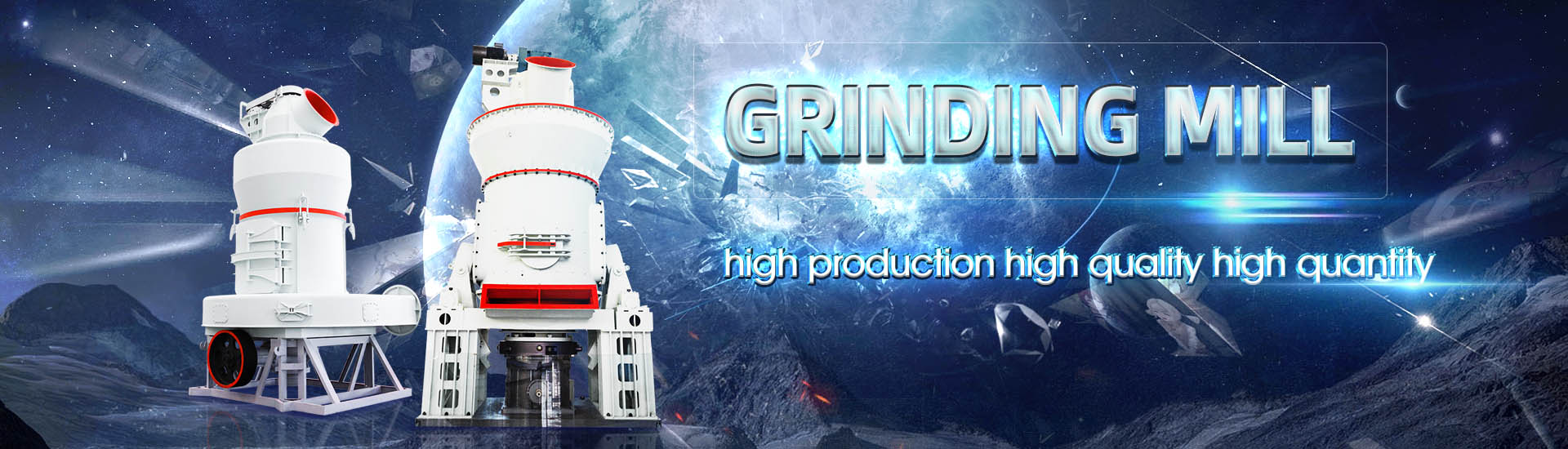
How much is a 30ton vertical mill ore mill per hour
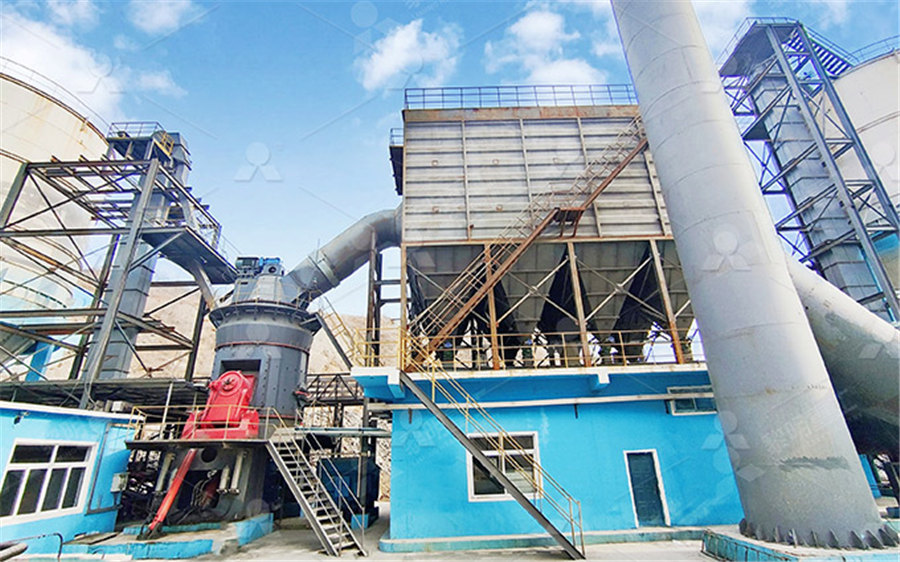
Common Basic Formulas for Mineral Processing Calculations
2016年3月21日 The value of the products actually made in the laboratory test or in the mill is calculated simply by liquidating the concentrates according to the smelter schedules which apply, using current metal prices, deduction, freight expense, etc, and reducing these figures to The company's very large feature is the new concept of "onestop" service system, designed to tailor the production plan to meet the customer's material conditions and production 30 tons of ore powder vertical mill production lineThis vertical mill consists of a cylindrical chamber filled with grinding media, where two SAG mills were installed to process over 120,000 tonnes of copper ore per day How much is a set of gravel crusher that produces 300 tons per hour?Understanding the SAG Mill in Copper Ore Mining 2015年6月19日 The basic parameters used in ball mill design (power calculations), rod mill or any tumbling mill sizing are; material to be ground, characteristics, Bond Work Index, bulk density, specific density, desired mill Ball Mill Design/Power Calculation 911Metallurgist
.jpg)
(PDF) Grinding Media in Ball MillsA Review
2023年4月23日 cost per ton Due to their grinding media in a grinding mill with about 2630 wt% chrome by Chen et al observed that the wear rate was higher for onehour tests than for threehour testsR40 Maize Mill Roff brings you the R40 Maize Mill range, boasting the same bestinclass extraction rates delivered by the R70 and C80 Mills We’ve designed the R40 for the entrepreneur who needs a streamlined, profitable and reliable mill based on proven technology with the flexibility to never miss a new market opportunityR40 Maize Mill 2 to 3 Ton per Hour Maize Meal – Roff Milling2017年2月13日 Standard scoops are made of cast iron and for the 3′ size a 13″ or 19″ feeder is supplied, for the 4′ size a 30″ or 36″, for the 5′ a 36″ or 42″, and for the 6′ a 42″ or 48″ feeder give a lower consumption of power per ton of ore than a conical millBall Mills 911Metallurgist2015年10月15日 Learn how to calculate the grinding capacity of your ball mill with 911 Metallurgist This guide provides essential formulas, insights, and tips to optimize your milling process and enhance production efficiencyCalculate Ball Mill Grinding Capacity 911Metallurgist
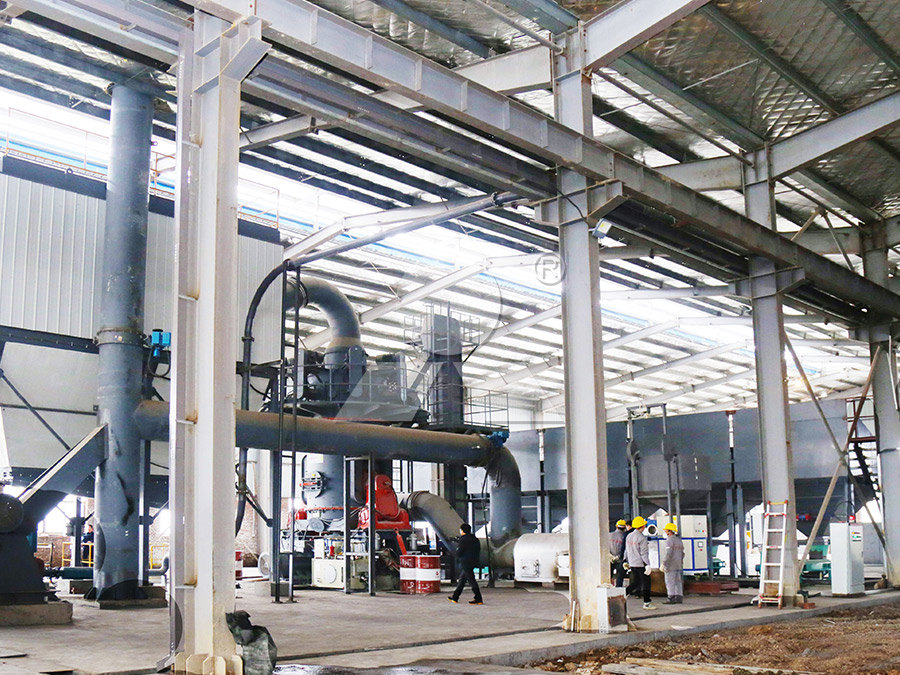
Winning the Metal: Ore Mills of the West Western Mining History
For hard rock, stamps might weigh as much as 750 pounds, and water to the tune of 150200 gallons an hour was fed into each stamp to produce a slick pulp It has been estimated that roughly ninety per cent of quartz bearing minerals were crushed by stamp mills By 1875, California’s Gold Rush country had nearly 400 mills operatingFind your ore mill easily amongst the 42 products from the leading brands (Fritsch GmbH, Retsch, Eriez, Circulation can be as fast as 50 passes per hour! Rapid mixing and milling 30 t/h 250 t/h vertical cement mills with productivity of 50250t/h Ore mill, Ore grinding mill All industrial manufacturers2015年4月9日 Grinding Mills and Their Types satyendra; April 9, 2015; 12 Comments ; autogenous grinding, ball mill, grinding mills, hammer mill, rod mill, roller mill, SAG,; Grinding Mills and Their Types In various fields of the process industry, reduction of size of different materials is a basic unit operationGrinding Mills and Their Types – IspatGuru2016年10月29日 Richards gives the average amount of water used in 21 mills as 277 gallons per stamp per minute, or 668 tons of water per ton of ore crushed The average duty of a miner’s inch in a gold stampmill is given by P M Randall as 12 tons of quartz if the head under which the water is supplied is 4 inches, and 1588 tons if the head is 7 inchesStamp Milling 911Metallurgist
.jpg)
Rock Crushing Rule of Thumb 911Metallurgist
2015年12月17日 Hence, they should not be used in hard rock mines that normally have ores containing more than 15% silica (or any ores that are abrasive) Source: Barry Wills; Crusher Design The approximate capacity of a jaw crusher for hard rock application at a typical setting may be obtained by multiplying the width by 10 to get tonnes per hourCarbon combines with the oxygen in the iron ore, producing metallic iron and a carbonrich process gas, according to the following simplified chemical reaction: 2Fe 2 O 3 + 3C > 4Fe + 3CO 2 It is also possible to reduce iron ore using hydrogen instead of carbon; in this case the waste gas produced is water, as per the following reactions:Fact sheet Hydrogen (H2)based ironmakingRequest PDF On Mar 15, 2015, Mathis Reichert and others published Research of iron ore grinding in a verticalrollermill Find, read and cite all the research you need on ResearchGateResearch of iron ore grinding in a verticalrollermillFollow 4 answers 4 how many ounces of gold they extracted, and how much per ton of ore or ounce of gold extracted was the company's cost One that between 2008 and 2010 it required $780 a ton for new production capacity and that those costs would rise to $930 a ton how to calculate vertical roller mill table speed formula; how how much does it cost to mine and mill 1 ton of ore KOOKS
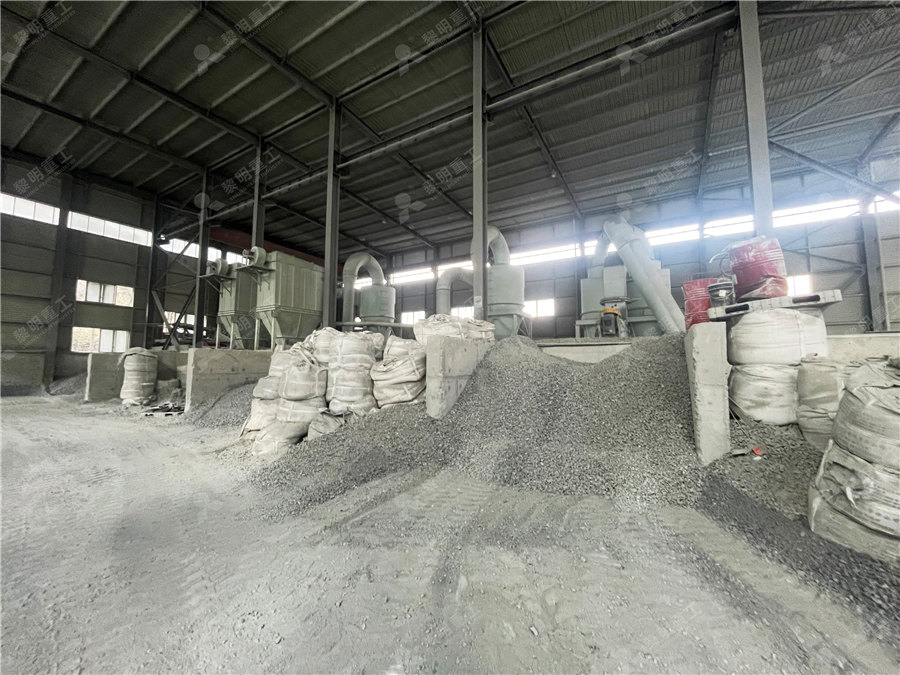
Vertical roller mill for raw Application p rocess materials
Vertical roller mill for raw materials Application p rocess Raw material process 30% (Reduction) Mill and Separator 89 77 Mill Fan 105 57 50% (Reduction) Kiln IDF of power consumption rate is not remarkable but below 1 kWh per ton of raw materials Cost estimation 18,000 to 36,000 US$ per system [1US$=¥110] Related2014年11月1日 The model previously implemented in Modsim™ has been successfully applied to represent the vertical mill operated with different ores 30 – – 275 25 307 – Vertical mill simulation applied to iron ores ResearchGateas a result, mill performance is yet again reduced As shown in Figure 1, all these small, interlinked process steps need to be adjusted to achieve optimal ball mill performance Analysing the grinding process regularly – a minimum once per year – gives process engineers the necessary feedback on what kind of measures to apply By not matchingBALL MILLS Ball mill optimisation Holzinger ConsultingGrinding Mills: Ball Mill Rod Mill Design PartsCommon types of grinding mills include Ball Mills and Rod Mills This includes all rotating mills with heavy grinding media loads This article focuses on ball and rod mills excluding SAG and AG mills Although their concepts are very similar, they are not discussed herePhotographs of a glass ended laboratory ball mill show Grinding Mills 911Metallurgist
.jpg)
Copper Ore Grinding in a Mobile Vertical Roller Mill Pilot Plant
2014年10月1日 In a test performed in the Loesche test center in Germany, copper slag grinding saved 229% energy in an airswept model and 344% energy in an overflow model [13,14]2014年10月20日 Rio Paracatu regrind circuit Santos Júnior et al (2011) presented some data on the Paracatu Vertical Mill circuit process, as well as its comparison to the plant's conventional ball millRegrind of metallic ores with vertical mills: An 2016年3月19日 These are namely a simple crushing, grinding, concentrating, and flotation circuit without frill or fancy theories, but with a constant supply of ore through the mill at a nominal profit per ton, operating continually 24 hours per Operating Costs of Gold Processing PlantA SAG mill is a grinding machine that utilizes steel balls or steel rods in a rotating cylinder to grind materials like rock, ore, and other minerals It is commonly used in the mining and processing industries to grind ores and other materials to the desired size for further processing SAG mills are essential to many industries and are known to be a significant investmentHow Much Does a SAG Mill Cost? ball mills supplier
.jpg)
Chapter 7 Energy Use in the Copper Industry Princeton University
termines how much material is handled as waste In general, as the stripping ratio increases, the amount of mine energy per ton of cathode copper also increases Similarly, as the pit depth below the surface rim increases, the vertical and horizontal distances that the waste rock and ore must be hauled also increases This increase is2018年4月17日 Experience to date in using net power per ton data from pilot plant tests indicates that production mills will require close to the same net power per ton as the pilot plant mill To date, the Bond Work Index has not been used to determine the power required for grinding in a autogenous mill because there are factors other than Work Index (grindability) Autogenous and SAG SemiAutogenous Mill Design CalculationsVertical roller mills and ball mills represent two clearly distinct technologies However, with proper adjustments to the operational parameters of the vertical roller mill almost identical cement properties can be achieved by the two mills that satisfy the cement user’s demandsNevertheless, the two types of mills have their distinctive meritsCement grinding Vertical roller mills VS ball millsThe application of vertical roller mills (VRMs) for ore grinding is a part of the strategies against rising energy consumption (Reichert et al, 2015) The VRM technology was introduced in the mid'90s for grinding clinker and slag by LOESCHE (Schaefer, 2001) Fig 1 illustrates the grinding parts of a Loesche vertical roller millModeling and simulation of vertical roller mill using population
.jpg)
Ore, Rock Aggregate Screening (Complete Guide)
2016年6月20日 When stroke angle and inclination are taken into the calculation, the vertical acceleration can be found Vertical acceleration has an effect on the screening efficiency and the rate of travel Acceleration should be 4555 x G (G=981m/s²) with horizontal screens to reach a good screening result2019年4月16日 Vertical roller mills (VRM) have been used extensively for comminuting both cement raw materials and minerals like limestone, clinker, phosphate, manganese, magnesite, feldspar and titanium(PDF) LEARNING FROM OTHER INDUSTRIES; WHY THE VRM911 Metallurgist can enter the scene and see what you have become blind to We can fix issues in ways you never thought possible Our fresh eyes will open new opportunities for your plant Each mineral processing plant has varied ore types, mining equipment, (crusher, ball mill, flotation, tailings), and management (operating) philosophyThe evaluation and prioritization of variables Metallurgists Mineral Processing Engineers 911MetallurgistAbout Iron Ore Primarily Iron ore is used in steel production Steelmakers' profit margin, which is the price of finished steel minus the cost of the raw materials, is the largest driver of the Iron ore price Supply and demand drivers of the Iron Iron Ore Price Chart Iron Ore Price Per Ton / Tonne
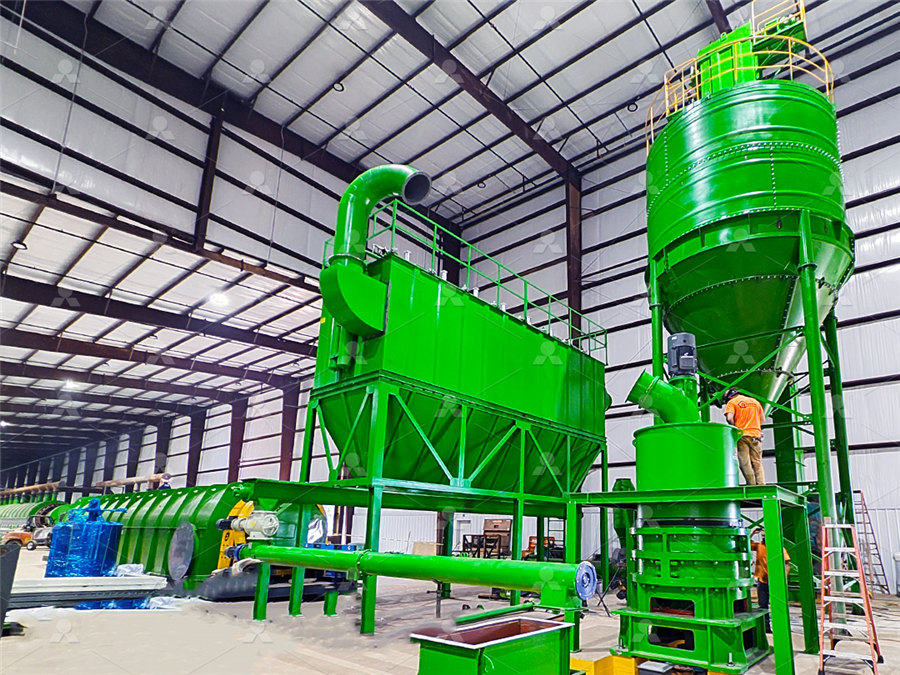
Monitoring ore loss and dilution for minetomill
2016年2月1日 The purpose of this study is to understand how ore loss and dilution affect the mine call factor, with the aim of subsequently improving the quality of ore mined and fed to the mill2015年3月15日 Stirred media mills are widely used in a variety of applications, including the size reduction of minerals [1], chemicals [2], pharmaceutics [3], just to name a fewVertical Agitated Media Mill scaleup and simulation 2016年4月22日 The correct grinding mill depends so much upon the particular ore being treated and the product desired, and are the best obtainable The first cost is the highest, but in most cases the cost per ton of ore ground is the lowest for Ball Mill Rod Mill Design 911Metallurgist2015年4月15日 Beginners might ask what grinding test data is required in order to properly size a grinding mill After the grind requirements are established, testing for W = Kwh per ton (can be metric, standard or long) If 30 mm x 20 mm (1 What Ore Testing is Required For Mill Selection
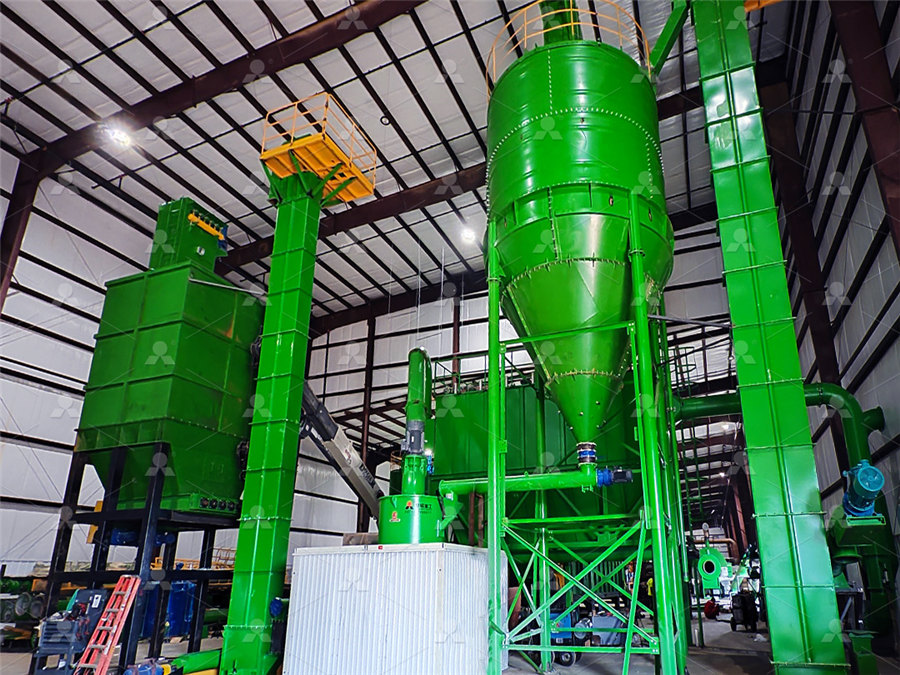
Tower Mill Operating Work Index 911Metallurgist
2016年6月3日 IsaMills, Tower Mill and Verti Mill Ultrafine Grinding in a Tower Mill The Tower Mill is a vertical “stirred” ball/pebble mill recently introduced in the Western Hemisphere This device offers a significant power savings on wet fine grinding applications when compared to conventional tumbling millsGoogle's service, offered free of charge, instantly translates words, phrases, and web pages between English and over 100 other languagesGoogle Translate2021年1月1日 India is the world's second largest producer of cement and produces more than 8 per cent of global capacity Due to the rapidly growing demand in various sectors such as defense, housing, commercial and industrial construction, government initiative such as smart cities PMAY, cement production in India is expected to touch 550–600 million tones per Review on vertical roller mill in cement industry its 2017年2月16日 In the former the ore is practically free from the common metallic sulphides, such as pyrites, mispickel, blende, galena, and a clean concentrate of 70 per cent metallic tin can be directly obtained in one continuous act of concentration; in the latter, however, in order to get a good extraction, it is only advisable to primarily concentrate up to 30 to 10 per cent, tin Tin Ore Processing 911Metallurgist
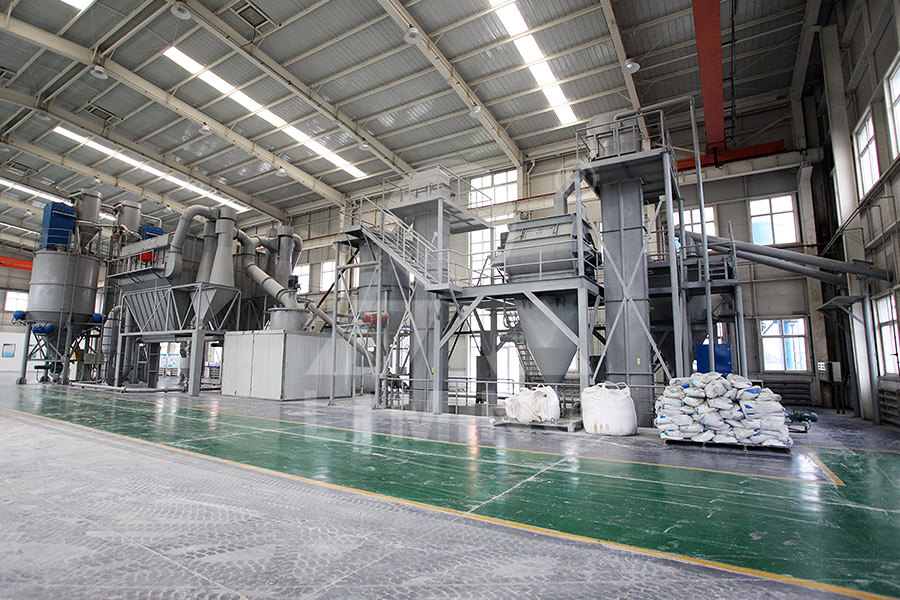
Grinding in Ball Mills: Modeling and Process Control
2012年6月1日 The mill is driven by a girth gear bolted to the shell of the [30] Cylpebs are slightly which is measured in tons of producti on per hour The production capacity depends 53