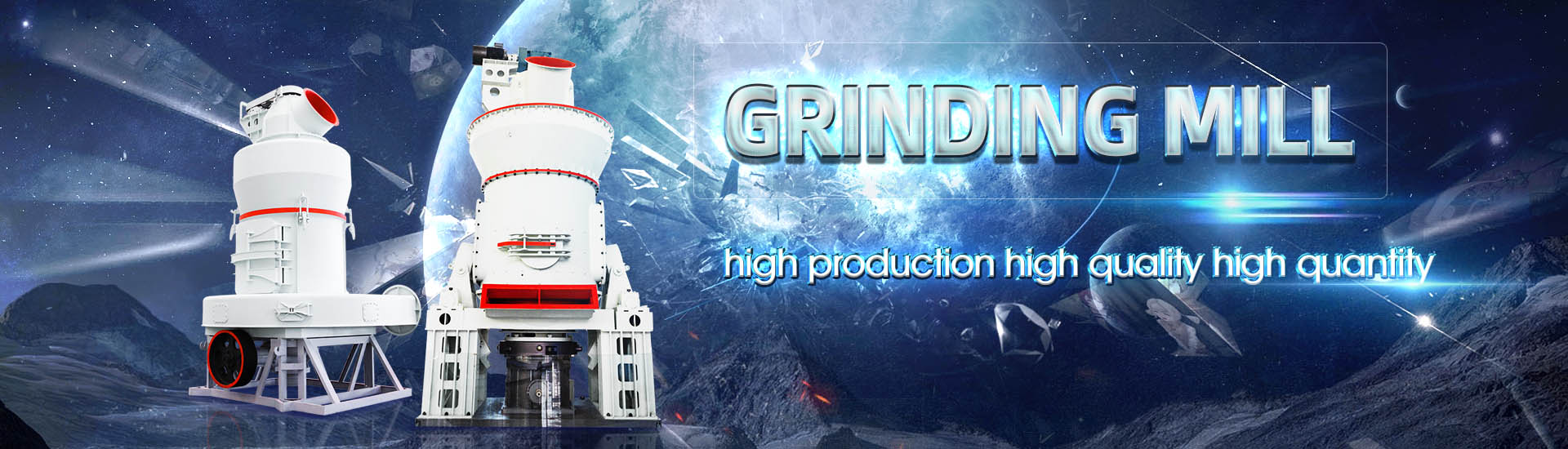
Coal mill force
.jpg)
Coal Mill an overview ScienceDirect Topics
Coal mills or pulverizers play a very essential part in the coalfired power production system Coal mills grind the coal into fine powder, and the primary air entering the mill dries and drives the coal into the power plant furnace for combustion Mills can be a bottleneck for the power generation 2015年11月1日 Coal mills are bottleneck in coal–fired power generation process due to difficulty in developing efficient controls and faults occurring inside the mills In this paper, a dynamic A unified thermomechanical model for coal mill operation2020年8月12日 In a power plant, the coal mill is the critical equipment, whose effectiveness impacts the overall power plant efficiency Uniform coal feeding mass flow rate and required particle size andAn investigation of performance characteristics and Vertical Coal Mill (VCM) is equipment for grinding and pulverizing coal into micron size Rotary kilns then use the powders as fuel burners The VCM has a housing section equipped with aTechnical specifications of vertical roller coal mill
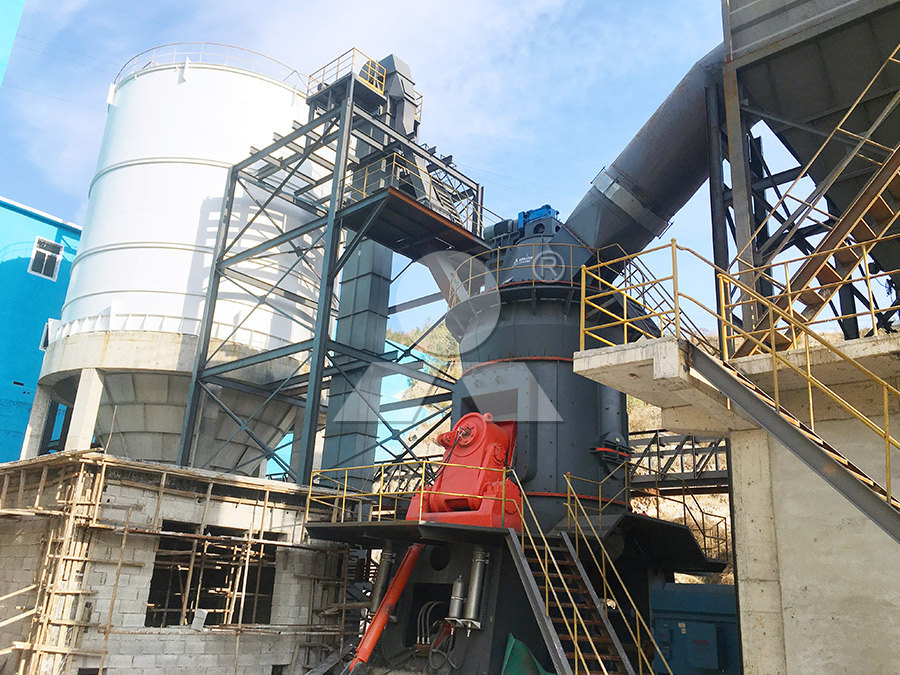
LOESCHEMILLS
The Loesche coal grinding mill range is divided into two serial types: Small twin mills constructed to individual specifications (LM 122 D to LM 202 D), with table diameters from 1,200 to 2,000 2012年5月1日 The paper presents development and validation of a coal mill model to be used for improved mill control, which may lead to a better load following capability of power plants Derivation and validation of a coal mill model for control2023年5月23日 This research proposes to establish a coal mill model considering the joint influence of three major forces on the base of the existing coal mill model and to optimize the partial structures and parameters of the Health indicator construction and application of coal 2009年1月1日 Typically each mill supplies the finely ground coal particles to the boiler through four to six outlet coal pipes It is a common experience that mill outlet pipes have unequal coal flowCFD Modeling of MPS Coal Mill for Improved

Fault Diagnosis of Coal Mill Based on Kernel Extreme
2022年7月26日 Aiming at the typical faults in the coal mills operation process, the kernel extreme learning machine diagnosis model based on variational model feature extraction and kernel principal component analysis is offered2023年5月23日 In this study, a new method of construction of the coal mill health indicator (HI) is proposed, and the operation condition monitoring approaches of the device are designed Health indicator construction and application of coal mill based on Mechanically, the MPS mill is categorized as an applied force mill There are three grinding roller wheel assemblies in the mill grinding section, which are mounted on a loading frame via pivot point The fixedaxis roller in each roller wheel assembly rotates on a COAL PULVERIZER DESIGN UPGRADES TO MEET THE DEMANDS The BTM is a lowspeed mill that primarily grinds coal by impact and attrition The VRM is a medium speed mill that grinds coal by compression and, because of the low coal inventory in the mill and flat grinding surfaces, develops shearing action as well For both mills a constant centrifugal force is maintained The speedA Comparison of Three Types of Coal Pulverizers Babcock Power

Mill Inerting and Pulverizer/Mill Explosion Mitigation
• Coal characteristics profoundly influence risk – Lower rank coals are generally more easily ignited inside the coal mill – High volatile matter and highly reactive coals encourage preignition inside the mill – Higher moisture content requires temperature extremes inside the millA control circuit monitors the coal level in the mill, and controls the speed of the raw coal feeder to maintain it Maintaining the coal level in the mill offers a builtin capacity cushion of pulverized fuel to take care of short interruptions in the raw coal circuit The mill is pressurized and the airtightness is ensured by plenum chambers Pulverizer Wikipedia2020年8月12日 To understand the performance of a vertical roller coal mill, the real operational tests have been performed considering three different coal sources Obtained results indicate that grinding pressure, primary air (PA) temperature and mill motor current have a tendency to rise by increasing coal feeding mass flow rates for all used coalAn investigation of performance characteristics and energetic 2021年3月12日 1 Introduction Two mill systems are employed for most coal grinding applications in the cement industry These are, on the one hand, vertical roller mills (VRM) that have achieved a share of almost 90% and, on the other MPS mills for coal grinding AYS Engineering
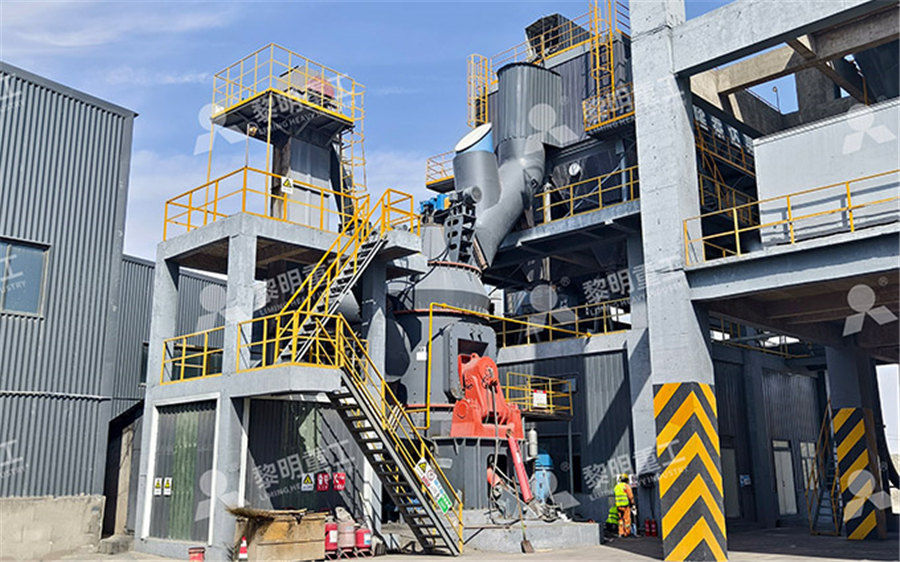
Coal Crushers Coal Pulverizers Mills Williams Crusher
This type of coal pulverizer mill uses centrifugal force to grind solid fuels while maintaining low operating costs Learn More Our Coal Pulverizing Products Williams is one of the world’s leading coal pulverizer manufacturers We have the most advanced directfired coal pulverizing system in the field today2 The hot air is used for transportation of the recirculating coal within the mill and also for transporting the coal from the pulverizer to the furnace As the coal is continuously reduced in size, the smaller/lighter particles are swept from the bowl by the hot air Hot air (and cool tempering air) is provided by the primary air fansBowl Mill Coal Pulverizer COAL HANDLING PLANTSOur ATOX® Coal Mill is a compact vertical roller mill that can grind almost any type of raw coal The coal mill utilises compression and shear force generated between the large rollers and the rotating table to crush and grind raw coal, removing the need for a separate piece of equipment for crushing The coal mill can also grind petroleum ATOX® Coal Mill FLSmidth Cement2011年8月1日 That means using the original design grinding profiles for your mill The majority of coal pulverizers about 20 tons minimum force on the grinding tires A bowl mill spring or hydraulic Pulverizers 101: Part I POWER Magazine
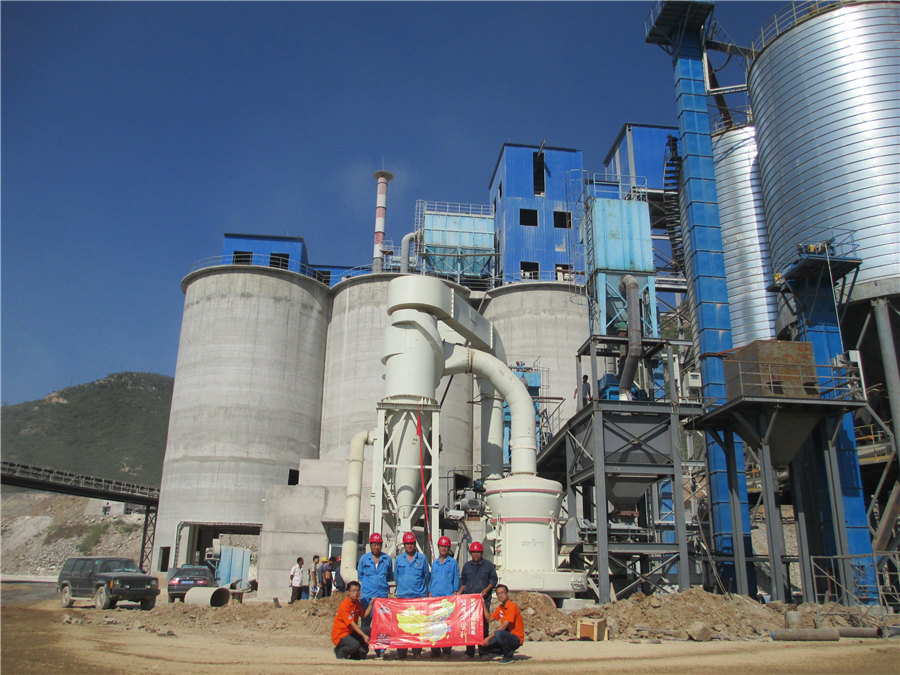
Dual fault warning method for coal mill based on ScienceDirect
2024年5月1日 The coal dust moves outward toward the mill under the action of centrifugal force and the push of the rest of the media, and is thrown out tangentially; the coal dust is dried by the primary air and transported to the separator area in the upper part of the coal mill2015年8月1日 Mill problems originate mainly due to poor controls or faults occurring within the milling system As discussed by GQ Fan and NW Rees [3], the control of mills remains very simple in most of the power plants due to the fact that the mill system is highly nonlinear with strong coupling among the variables and it is very difficult to measure some important Review of control and fault diagnosis methods applied to coal Raw coal enters the top of the pulverizer through the raw coal feed pipe The raw coal is then pulverized between the roll and rotating ring Hot air is forced in through the bottom of the pulverizing chamber to remove unwanted moisture and transport the coal dust up through the top of the pulverizer and out the exhaust pipe directly to the burnerCoal Pulverizer – Power Plant Pall Corporation2022年7月26日 Diagnosis of Coal Mill Based on Kernel Extreme Learning Machine with Variational Model Feature Extraction Energies 2022, 15, 5385 separator, due to centrifugal force and inertial force, the qualified pulverized coal will be sent to the furnace for combustion, while the large particle pulverized coal will fall backFault Diagnosis of Coal Mill Based on Kernel Extreme Learning
.jpg)
HP Bowl type millspower plant equipment
1311 The ventilation resistance of HP coal mill is smaller than that of other medium speed pulverizers, and the air pressure of primary air fan is smaller, which can reduce the investment cost of fan 14 Working principle The function of HP series coal mill is to mill raw coal to achieve the fineness that can be effectively burned in the Section of coal bowl mill Table 1 Guaranteed coal conditions for mill performance evaluation Coal Moisture % 20 Coal HGI 55 Mill Outlet Temperarure °C 80 Mill Air Flow T/hr 102 Coal Fineness (% passing trough 200 mesh) 70% passing through 200 mesh and 90% passing through 50 mesh Differental Pressure 300 mmwc Coal Output from Mill 609 t/hrA Study on 500 MW Coal Fired Boiler Unit’s Bowl Mill Mechanically, the MPS mill is categorized as an applied force mill There are three grinding roller Since the first application using an MPS mill to process pulverized coal in Germany in the mid 1960s, there have been over 2,000 different MPS mill installations operating in Coal Pulverizer Design Upgrades to Meet the Demands of Low 2014年1月1日 Two mill systems are employed for most coal grinding applications in the cement industry These are, on the one hand, vertical roller mills (VRM) that have achieved a share of almost 90% and, on (PDF) MPS mills for coal grinding ResearchGate
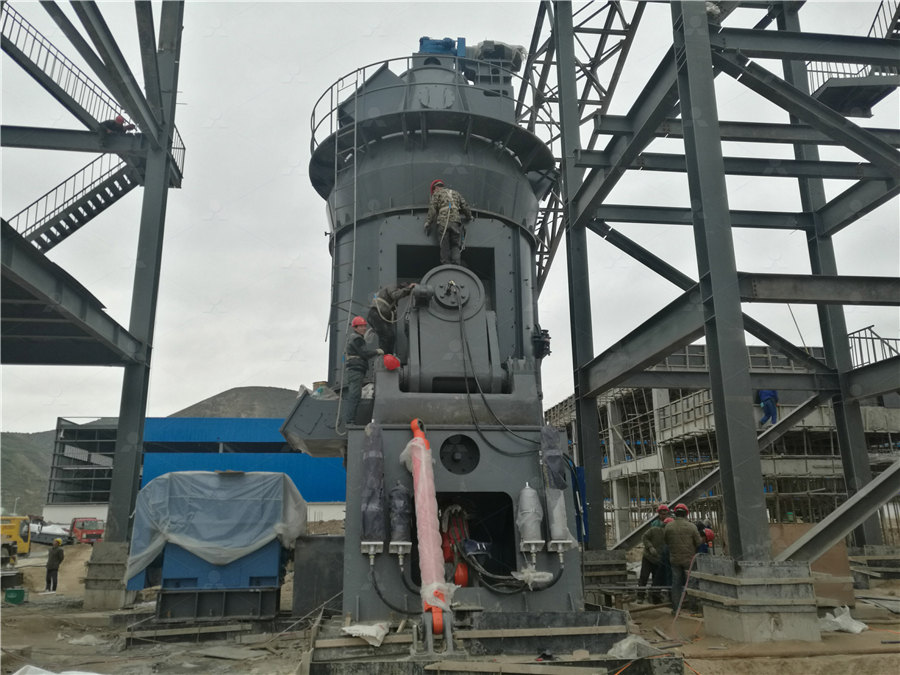
Health indicator construction and application of coal mill based
DOI: 101177/ Corpus ID: ; Health indicator construction and application of coal mill based on the dynamic model @article{Yin2023HealthIC, title={Health indicator construction and application of coal mill based on the dynamic model}, author={Weiming Yin and Yefa Hu and Guoping Ding and Wenbin Xu and Lei Feng and Xueliang Chen and profiles for your mill The majority of coal pulverizers sized around 120,000 pph use three grinding elements, referred to as journals, will be set at about 20 tons minimum force on the grinding tires A bowl mill spring or hydraulic preload for this size of “Blueprint” Your Pulverizer for Improved PerformanceAbstract: The paper presents development and validation of coal mill model (including the action of classifier) to be used for improved coal mill control The model is developed by using the mass and heat balance equations of the coal mill Genetic Algorithm is used to estimate the unknown parameters that are used in the model validationModeling and Control of Coal MillAs one of the three major forces of coal mills, the grinding force exerts a significant impact on the working process of coal mills and parameters like mill current and outlet temperatureTechnical specifications of vertical roller coal mill
.jpg)
Pulveriser in Thermal Power Plant Bowl Mill Ball Mill
In bowl mill pulveriser raw coal coming from feeder gets ground between the grinding rolls and bull ring segments installed on the revolving Bowl Tramp iron pieces which are not required to grind, leave the Bowl due to centrifugal force Coal drying is ensured by controlling the coal mill inlet temperature, to give a target mill exit temperature, usually between 70 and 900C Drying capability varies according to mill circuit design, Table 3 summarises the position The grinding force in both mill types is adjustable using pretensioned springs or hydraulic ramsCOAL PREPARATION AND FIRING INFINITY FOR CEMENT EQUIPMENT2009年1月1日 Coal pulverizers play a critical role in the functioning and performance of a PCfired boiler The main functions of a pulverizer are crushing, drying and separating the fine coal particles CFD Modeling of MPS Coal Mill for Improved Performance and Safety2020年4月7日 Monitoring and diagnosis of coal mill systems are critical to the security operation of power plants The traditional datadriven fault diagnosis methods often result in low fault recognition rate or even misjudgment due to the imbalance between fault data samples and normal data samples In order to obtain massive fault sample data effectively, based on the Modeling of Coal Mill System Used for Fault Simulation MDPI
.jpg)
Modeling of Coal Mill System Used for Fault Simulation
2020年4月7日 PDF Monitoring and diagnosis of coal mill systems are critical to the security operation of power plants Under the action of spring force or liquid pressure, the grinding roller As one of the three major forces of coal mills, the grinding force exerts a significant impact on the working process of coal mills and parameters like mill current and outlet temperatureEffect of mill outlet temperature on the coal moisture content2021年11月4日 In this kind of mill, The redistribution and attrition within the coal bed are forced by movement of the rollers (or by a disc rotation, in the case of the tester)Technique to Investigate Pulverizing and Abrasive Performance of Coals The coal then moves under centrifugal force outwards and under three passive rollers where grinding and crushing takes place Coal mill is an important component of the thermal power plant It is used to grind and dry the moisturized raw coal and transport the pulverized coal (PDF) Modeling and Control of Coal Mill Academia
.jpg)
Industrial Explosion Protection Coal Mill Safety, Explosion and
Safe operation of coal grinding systems: Raw coal silo protection against fire and explosions Safe operation of coal grinding systems: Raw coal yard management The purchasing process for coal grinding systems needs changes Talk at a virtual seminar, November 2023 Accept the probability that the fire and explosion safety of your coal grinding spindle coal pulverising mill’s performance to facilitate optimal plant performance Plant design and mill’s acceptance test data was analysed to understand the design and subsequent changes over the years of the mill’s operation The mill outputs, pulverised coal fineness andPerformance optimisation of vertical spindle coal pulverisers2018年4月6日 An inert system designed for indirect firing is the most common solution at cement plants Equipped with the highefficiency RAKM dynamic separator, the ATOX coal mill will grind any type of coal to the necessary fineness The ATOX mill, if provided with a variable speed motor, will grind petcoke and anthracite down to a fineness below 5% +90 µmATOX Coal Mill Free Download PDFThe ball mill is a traditional coal pulverizer machine, which has been widely used since it was invented In the cement plant, the new dry process cement manufacturing requires the moisture content of coal powder to be 05% ~ 15%, while that of raw coal is 15% ~ 40%Coal Mill in Cement Plant
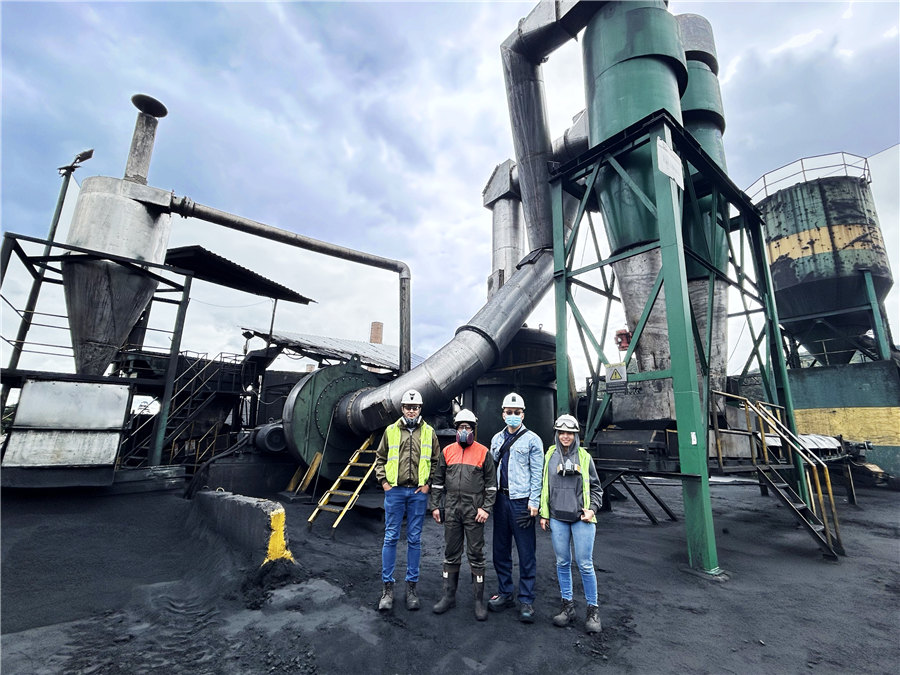
Analysis of the Coal Milling Operations to the Boiler Parameters
2020年4月2日 : Fuel and firing system purposely to deliver light fuel oil or coal as one of the primary elements of fuel in an ideal condition for combustion to take place in the boiler combustion chamberA compact coal mill solution for grinding virtually any type of raw coal Our ATOX® Coal Mill is a compact vertical roller mill that can grind almost any type of raw coal The coal mill utilises compression and shear force generated between the large rollers and the rotating table to crush and grind raw coal, removing the need for a separate Roller mill ATOX® COAL FLSmidth DorrOliver EimcoA coal ball mill works by rotating a cylinder filled with steel balls, crushing and grinding the coal into a fine powder How does a vertical coal mill work? A vertical coal mill works by applying force to the coal particles in the grinding chamber, causing them to break into smaller pieces Which type of coal mill is more energyefficient?How does a Coal Mill Work? ball mills supplier2021年8月1日 Yukio et al [7] proposed a model consisting of blending, grinding and classifying processes for pulverizer control Agarawal et al [8] differentiated coal powder into ten size groups, divided the bowl mill into four zones, and developed a unified model Palizban et al [9] derived nonlinear differential mass equations of raw coal, recirculation coal and suspension coal in Coal mill model considering heat transfer effect on mass
.jpg)
An investigation of performance characteristics and energetic
et al 2017) In a coalfired power plant, one of the main equipment is the coal mill, whose effectiveness influences mainly the whole power plant performance (Shah, Vuthaluru, and2020年6月29日 Grinding takes place by Impact and attrition The primary air is divided into two parts: A Bypass Air: Mixes with the raw coal and dries it before it enters the Mill It also carries the Pulverized fuel by maintaining sufficient velocity in the coal pipes B Air Thru’ Mill: Air that lifts pulverized coal from the Mill shellclassifications and working of mills in a power plant PPT